
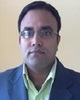
- Open Access
- Authors : Prasenjit Talukdar , Romsha Singh , Sharahnan Puzari , Azharul Fardin Sattar, Tapan Baruah
- Paper ID : IJERTV10IS070194
- Volume & Issue : Volume 10, Issue 07 (July 2021)
- Published (First Online): 23-07-2021
- ISSN (Online) : 2278-0181
- Publisher Name : IJERT
- License:
This work is licensed under a Creative Commons Attribution 4.0 International License
Effect of Fe2O3 Nanoparticle on Viscoelastic Property of Crude Oil: From a Flow Assurance Perspective
Prasenjit Talukdar*1, Romsha Singp Sharahnan Puzari1, Azharul Fardin Sattar1, Tapan Baruap
1Department of Petroleum Engineering, DUIET, Dibrugarh University, India
2University of Petroleum and Energy Studies (UPES), Dehradun, India
Abstract:-The transportation of hydrocarbons in Oil and Gas Industry is one of the selective important aspects as it helps in facilitating the smooth conduct of the surface operation activities and thereby maintaining a growth in market strategy. However due to the complex nature of crude oil, it is generally difficult in certain areas to assure its smooth flow through pipelines. This paper primarily studies the effectiveness of using Ferric oxide nanoparticle in crude oil which seemingly helps to assure transportation through pipelines. The paper describes experimental investigations for amplitude sweep, frequency sweep, pour point, shearing rate and viscosity of the prepared compositions for 0.5%, 1% and 1.5% of Fe2O3 Nanoparticle composition with respect to formation crude wherein the variation of the stated parameter profiles suggested for the use of Fe based nanoparticle. The novelty of the paper is governed by the attempt of the author to study viscoelastic analysis from the flow assurance perspective of crude oil which is a first of a kind of experimental investigation.
Keywords: Ferric oxide, Nanoparticle, Amplitude Sweep, Frequency Sweep, Flow Assurance, Viscoelastic Analysis
-
INTRODUCTION
The origin of the term Flow Assurance dates back to 1990s coined by Petrobras which refers to Guarantee of Flow [1]. In line with the advancement of exploration and production activities, the Oil Industry is gradually paving its way forward to increase recovery from complex oilfields and unconventional reservoirs as well which produces highly viscous crude. In this context, it is of prime importance to deal with the rheological parameters of the crude so that it can be transported easily from one place to another. For crude flow in pipelines a viscosity less than 200-300 mPa.s is generally desirable at the pumping temperature [2]. Successively, the heavy crudes are not acceptable by downstream industries and hence viscosity reduction is important to provide a seamless transportation through pipelines for the purpose of further processing at different oil and gas facilities. The viscoelastic profile study provides a means to better determine the ability of a composite mixture to assure flow through pipelines or conduits. The industrial treatment of produced heavy crude in India generally revolves around heating of crude and consequent heating of pipelines [3], use of pour point depressants [4], use of drag reducing additives [5], emulsification of crude oil in water [6], implementation of
core annular flow [7], dilution or blending of crude oil with lighter alcohols [8,9]. However, these conventional methods lag behind in the deliverability of the desired results in the transportation of heavy crude with asphaltene or wax context. Additionally, some studies have made also been made in the field of use of suitable oil in water emulsions which showed significant results in reduction of pour point and viscosity and thereby facilitating the transportation process [10-14] which were prepared by mechanical homogenization method [15]. Furthermore, recent research also studies the significant use of ultrasonic waves to reduce the chances of the wax precipitation inside the pipelines which is achieved by achieved by the disintegration of large carbon compounds to smaller ones by the high frequency ultrasonic waves [12]. The researchers have also suggested that the surfactants are easily separable at surface facilities with no leftover residues which serves to be beneficial for further processing of the crude [16] but the area of alteration of viscoelastic property of crude oil still leaves a window for assuring the flow of crude seamlessly. This paper aims at synthesis of a novel Fe based nanoparticle which will play an important role in affecting the viscoelastic property of crude oil from the deeper perspective of flow assurance. The nanoparticles study on dynamic rheological properties of crude oils have been analysed by researches in recent studies which provided fruitful outcomes [17]. The present study focuses on the experimental investigation of various areas which includes amplitude sweep, frequency sweep, viscosity profile subjected to shear rate alongwith the comparison drawn with conventional heavy crude sample collected from Barmer, Rajasthan, India. The experiments performed therein suggested the novelty of the use of Fe based nanoparticle for the effective seamless transportation and movement of crude from the origin to the destination.
-
MATERIALS AND METHODS
The crude oil sample was collected from an oilfield in Barmer, Rajasthan. The kerosene was bought from local shop which was double distillated before using in the experiment. The Anton Paar MCR 102 Rheometer was used for rheological property analysis. The rotational static test was carried out using Concentric Cylinder (CC) for the measurement of viscosity with respect to shearing rate of
the samples taken into consideration. Oscillation test for determination of frequency sweep was carried out in the Plate Plate (PP) configuration. The samples are listed in Table I. FeO3 nanoparticles were procured from Nanolab private Limited which had an average size of 50 60 nm.
Table I. Description of Sample and their composition of crude and nanoparticle
Sample
Composition
A
Crude
B
70/30 (Crude/Kerosene)
C
0.5% Fe2O3 Nanoparticle 70/30 (C/K)
D
1% Fe2O3 Nanoparticle 70/30 (C/K)
E
1.5% Fe2O3 Nanoparticle 70/30 (C/K)
-
RESULTS AND DISCUSSION
-
Steady state rotational test
Figure 1. Viscosity vs. Shearing Rate
The experiment is conducted for five fluids, viz.: Crude, 30% kerosene in 70% crude (70/30, C/K), 0.5% Fe2O3 NP in C/K (70/30), 1% Fe2O3 NP in C/K (70/30) and 1.5% Fe2O3 NP in
C/K (70/30). The loss in viscosity in each fluid with addition of nanoparticles is compared with respect to crude.
The shearing rate for each type of crude is increased and the viscosity is compared at three points, viz.: 1 sec-1, 300 sec-1 and 800 sec-1. It is observed from Figure 1. that for raw crude the values of viscosity are 120252 mPa-s at 1 sec-1, 819 mPa- s at 300 sec-1 and 350.1 mPa-s at 800 sec-1. Now, the viscosities of other fluids for the same shearing rates are observed as follows:
Table II. Viscosity of fluids
FLUID TYPES
at 1s-1
at 300 s-1
at 800 s-1
C/K (70/30)
40084
273
113.5
0.5% Fe2O3 NP in C/K (70/30)
4923.1
61.2
40
1% Fe2O3 NP in C/K (70/30)
1901.6
29.5
19.45
1857.05
28.55
18.25
From the above data in Table II., it can be clearly inferred that on addition of Fe2O3 NP to raw crude, the viscosity of the crude can be significantly reduced. It is also observed that the largest drop in viscosity occurs between C/K(70/30) and 0.5% Fe2O3 NP in C/K(70/30).This decrease in viscosity largely reduces the production of paraffins in pipelines and helps in a seamless flow of fluid through pipelines.
Experimental analysis is conducted to determine the change of Storage Modulus (Pa) with respect to Shear Strain (%). The experiment conducted is called Oscillation test. Here, the fluid (in this case, Crude) is kept in between two plates residing above and below the fluid. The upper plate is the allowed to oscillate to produce a certain degree of shear strain in the fluid. For each shear strain (%) there is a change in amplitude, but the frequency is kept constant.
After the test, a graph is obtained which is shown in Figure
2. It is observed that during the initial phase, the storage modulus of the fluid remains constant and then after a certain point a dip occurs and the graph tends to move downward. This happens when the fluid has deformed, which implies that storage modulus has reduced.
The experiment is conducted for five types of fluids- Crude, 30% Kerosene in 70% crude (70/30, C/K), 0.5% Fe2O3 NP in C/K (70/30), 1% Fe2O3 NP in C/K (70/30), 1.5% Fe2O3 NP in C/K (70/30).
The following observations were made:
-
In crude, for about 1000000 Pa of storage modulus, the shear strain is about 0.0309%.
-
In crude containing 30% kerosene, for about 20000 Pa of storage modulus, the shear train is about 0.214%.
-
In 0.5% ferric oxide in C/K (70/30), for about 10000 Pa of storage modulus, the shear strain is about 0.0664%.
-
In 1% ferric oxide in C/K (70/30), for about 3000 Pa of storage modulus, the shear strain is 0.143%.
-
In 1.5% ferric oxide in C/K (70/30), for about of 2500 Pa of storage Modulus, the shear strain is 0.996%.
-
-
Amplitude sweep measurements from oscillation test
Figure 2. Storage Modulus vs Shear Strain
Comparing the values of storage modulus with respect to the value of storage modulus in case of unmixed crude in terms of percentage, it is observed that:
-
For 30% kerosene in crude oil, we have 0.059% deviation of shear strain
-
For 0.5% ferric oxide in C/K (70/30), we have 0.011% deviation of shear strain.
-
For 1% ferric oxide in C/k (70/30), we have 0.036% of deviation in shear strain.
-
For 1.5% ferric oxide in C/K (70/30), we have 0.312% of deviation in shear strain.
Hence, we can conclude that addition Fe based nanoparticles hugely tends to lower the viscosity of crude oil.
The detailed analysis of viscoelastic property of the crude oil is studied using the oscillation test and plots of storage and loss modulus and loss factor versus angular frequency (rad/s) are shown in Figure 3. The test is conducted for five types of crude raw Crude, 70% Crude and 30% kerosene, 0.5%, 1% and 1.5% Fe2O3 NP in 70/30 C/K respectively.
-
-
Frequency Sweep data from Oscillaion Test
Figure 3. Storage and Loss Modulus and Loss Factor vs. Angular Frequency
On plotting the storage modulus (G) and Loss Modulus (G) vs Angular frequency graph, it is observed that for raw crude oil, the storage modulus is around 75000 Pa and loss modulus is around 15000 Pa at low frequency; and even at high frequency the difference in values does not alter much, which signifies the elastic property is dominant over viscous property and the crude behaves as viscoelastic solid. Now, when the mixture of 30% kerosene and 70% crude is taken into account, the values of both moduli decrease but their difference is not much less than raw crude, at all frequencies, which signifies that adding of kerosene moderately decreases it viscoelastic solid property.
Again when 0.5% Fe2O3 NP is added the values of both moduli decreases but their difference does not change much than raw crude and 70/30 C/K and thus its again shows that viscoelastic solid property decreases very moderately. Surprisingly, when 1% Fe2O3 NP was added, the difference significantly reduces as can be observed in the graph, the point came too closer. Thus, viscoelastic solid property reduces greatly. Finally, when 1.5% was added, the points almost collided which shows viscous property gets dominant over elastic property. Let us see what happens when Loss Factor (G/G) verses Angular frequency graph is plotted. For raw crude, 70/30 C/K and 0.5% Fe-NP 70/30 C/K the values of loss factor at low frequencies are same around 0.30 rad/s. But at high frequencies the values of crude and 0.5% Fe2O3 NP 70/30 C/K increases to 0.40 but 70/30 C/K decreases to around 0.22.
But for 1% and 1.5% Fe2O3 NP in 70/30 C/K shows a significant better result. The value of loss factor for 1% Fe2O3 NP in 70/30 C/K at range 0.15- 6.13 rad/s is around 0.73 and
at high frequency the values cross 1 reaching up to 1.3. And similarly, for 1.5 Fe2O3 NP in 70/30 C/K crosses the loss factor of 1 at around 0.94 rad/s. At low frequency 1.5 % Fe2O3 NP in 70/30 C/K shows higher loss factor than 1% Fe2O3 NP in 70/30 C/K but crossing loss factor of 1 it shows alternate result.
The point at which loss factor crosses 1 is called as crossover point and subsequently, the fluids convert into viscoelastic liquid from viscoelastic solid. Thus, it concludes that by adding 1% or 1.5% Fe2O3 NP in 70/30 C/K makes it significant for pipeline transportation.
-
Viscosity vs. Temperature measurement for pour point approximation
Figure 4. Viscosity vs. Temperature for pour point approximation
The effect of Fe2O3 NP on 70/30 Crude/Kerosene has been studied and a plot of Viscosity vs Temperature with pour points is presented in Figure 3. It was observed that the pour point of raw crude is found to be 24.5o C. But when 30% kerosene is added to the crude, the pour point decreases to 21o C. Surprisingly, with addition of 0.5% Fe2O3 NP the pour point decreases to 20.5o C. Further when 1 % and 1.5% Fe2O3 NP were added the pour point decreases to 19o C and 18.5o C respectively as evident from Figure 4. Although adding more than 1.5% Fe2O3 NP does not alter the pour point anymore. Thus, reducing the pour point from 24.5o C to 18.5o C makes it suitable for pipeline transportation.
IV.CONCLUSION
The results of the experimental investigation carried out using Fe2O3 NP based nanoparticle suggested that there is a drastic change in the viscoelastic properties of crude oil. With the addition of Fe2O3 NP, the storage capacity of base crude oil decreases. This decrease prevents back-pressure that frequently arises from pump start up issues. Moreover, the nature of crude turns from viscoelastic solid to liquid as the loss factor approaches unity, especially at higher frequencies.The results of the shearing rate vs. viscosity profile referred to the fact that upon addition of 1.5% of Fe2O3 NP, there is a decrease in viscosity. Moreover, it acted as pour point depressing agent which is truly beneficial from the aspect of transportation of the crude. Thus, overall perspective suggests that Fe2O3 NP proved to be beneficial for crude transportation through pipelines.
REFERENCES
-
Gupta, Anand & Sircar, Anirbid & Pdpu, India. (2015). Need of Flow Assurance for Crude Oil Pipelines: A Review. International Journal of Computational Science and Engineering. 6. 2015-2045.
-
Kessick, M. A.; Denis, C. E. S. Pipeline transportation of heavy crude oil. U.S. Pat
-
Al-Besharah, J. M.; Salman, O. A.; Akashah, S. A. Ind. Eng. Chem. Res. 1987, 26 (12), 24452449.
-
Deshmukh, S.; Bharambe, D. P. Fuel Process. Technol. 2008, 89 (3), 27233.
-
Chen, Q.; Wang, M.; Pan, N.; Guo, Z.-Y. Energy Fuels 2009, 23 (9), 44704478.
1982.
-
Bensakhria, A.; Peysson, Y.; Antonini, G. Oil Gas Sci. Technol. 2004, 59 (5), 523533.
-
Gateau, P.; Henaut, I.; Barre , L.; Argillier, J. F. Oil Gas Sci. Technol. 2004, 59 (5), 503509.
-
Ghannam, M. T.; Hasan, S. W.; Abu-Jdayil, B.; Esmail, N. J. Pet. Sci. Eng. 2012, 81, 122128.
-
Ashrafizadeh, S. N.; Kamran, M. J. Pet. Sci. Eng. 2010, 71 (34), 205211.
-
Kumar, S.; Mahto, V. Chem. Eng. Res. Des. 2016, 115, 3443. [12] Kumar, S.; Mahto, V. Pet. Sci. 2017, 14 (2), 372382.
-
Al-Roomi, Y.; George, R.; Elgibaly, A.; Elkamel, A. J. Pet. Sci. Eng. 2004, 42 (24), 235243.
-
Anto, R., Deshmukh, S., Sanyal, S., & Bhui, U. K. (2020). Nanoparticles as flow improver of petroleum crudes: study on temperature-dependent steady-state and dynamic rheological behavior of crude oils. Fuel, 275,