
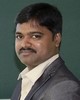
- Open Access
- Authors : Gurushanth B Vaggar , Viresh B Sirimani , Devaraj P Sataraddi , Nandeesh M Hiremath, Fakkiresh Bhajantri
- Paper ID : IJERTV10IS080008
- Volume & Issue : Volume 10, Issue 08 (August 2021)
- Published (First Online): 07-08-2021
- ISSN (Online) : 2278-0181
- Publisher Name : IJERT
- License:
This work is licensed under a Creative Commons Attribution 4.0 International License
Effect of Filler Materials on Thermal Properties of Polymer Composite Materials: A Review
Gurushanth B Vaggar1*
1*Associate Professor Department of Mechanical Engineering
Alvas Institute of Engineering and Technology Moodbidri, Karnataka State, India.
Viresh B Sirimani2, Devaraj P Sataraddi3, Nandeesh M Hiremath4, Fakkiresh Bhajantri5 2, 3, 4, 5Undergraduate Students
Alvas Institute of Engineering and Technology
Moodbidri, Karnataka State, India.
Abstract The thermal property variations are nonlinear in polymer composites, it is very difficult to identify and predict the temperature behavior of these materials with unknown thermal conductivity. However, thermal property measurement of composite materials is not an easy task due to temperature variations complexity. Thermal conductivity and thermal stability of polymers composites enriched by making them hybrid polymer composites by adding fillers such as CNT, graphene, silicon carbide, copper powder, copper mesh in carbon fibre reinforced polymer (CFRP) and glass fibre reinforced polymer (GFRP). The potential use of polymer composites in the structural application areas of aerospace, automotive, pressure vessels and wind energy are estimated about 47% of the total glass fibre market. The worldwide demand of glass fibre is 45.35 tons/year and demand of glass fibre increasing every year at the rate of 10.6%. Various filler materials and percentage adding to polymer composites was the key factor in deciding the thermal properties of polymer composites.
Keywords Thermal conductivity (K); Coefficient of Thermal Expansion (CTE); Thermal Gravimetric Analysis (TGA); Silicon; Wear.
-
INTRODUCTION
Manufacturing of polymer matrix composites are the reason for high strength low density in nature as compared to that of metals and their alloys. More temperature variable conditions polymer composites are failed to exhibit good thermal properties in a different fields like automobile sectors, military weapons, aerospace parts and medical instruments etc. The solution to this kind of problems, try to use micro or nano sized filler particles in the polymer composites, to make them hybrid and are called hybrid polymer composites (HPC). Adding filler materials in a small percentage to regular polymer composites vary the thermal properties overall and hybrid polymer matrix composites much stable under varied temperature conditions without changing the base strength of polymer matrix composite materials.
For different applications a predefined desired properties and novel kind of materials are manufactured using fillers in polymer composites and are known as hybrid composites. By varying the volume fraction proportion of fillers in epoxy resin glass fibres will improve the mechanical, physical and thermal properties of composites. Without effecting the strength, stiffness and physical properties of base constituents hybrid composite materials give much improved and enhanced thermal properties. Due to high strength low
density and economic compared to metals and metal alloys, hybrid polymer composites are used in various fields of applications like aerospace, marine, military weapons, automotive parts and wind mill turbine blades. Requirement and use of hybrid composites has increased in many fields, communication sectors and electronics devices where high thermal resistance low density factors are predominant [1].
Today, most suitable and promising materials for structural work in a competing engineering world are FRPCs (fibre reinforced polymer composites) for their cost effectiveness, high strength-weight ratio and high stiffness. Fibre reinforced polymer composites are made with high strength fibres and low modulus continuous matrix, fibres may be natural fibres (sisal fibre, jute fibre, bamboo fibre, areca fibre and banana fibre etc.) or synthetic fibres (carbon fibre, glass fibre and aramid fibre etc.) and bio polymers, thermoplastic or thermoset matrix materials. Strength of FRPCs lies in amount of adhesion occurs between polymeric matrices and fibres, orientation of fibre, size of fibres and loading of fibres.
For many application fields like military, aerospace, wind power mills, automotive and construction, glass fibres are the most used fibres because of easy processing technique, low density, good resistant to corrosion, high strength sustainability, toughness and recyclable. E-Glass fibres are most widely used fibres in polymer composites, Zirconium content present in glass fibre prevents the corrosion effect on glass fibre. S-Glass fibre are not used much due to high modulus tensile strength and expensive as compared to E- glass fibres [2].
Epoxy resin glass fibre composites are have both organic and inorganic combination of materials, coating of glass fibres controls the matrix and fibre interface contact properties. From several study approaches it is noticed that the toughness and strength of polymer composites are closely associated with interface property improvement [3].
For electrical and electronics applications, regular polymers used are thermally and electrically insulated. As the electrically insulating polymer materials are poor thermal conductivity, the dissipation of heat becomes major problem, to overcome that, extra heat dissipating additional attachments needs to provide in terms heat sinks, extended fins and fans. To develop composite materials to meet electrically and thermally acceptable properties for electrical and electronics applications, we need to use reinforcing elements such as fibres and filler particles in regular polymers. Silicon carbide, silicon oxide, aluminium oxide,
aluminium nitride and ceramic particles fillers are most frequently used reinforcing elements in regular polymers [4]. Major percentage of polymer matrix composites are used almost in every field of engineering applications, Hence it is essential to improve the thermal and mechanical properties of polymer composites [5]. Plane polymer materials have certain disadvantages like, poor thermal stability, low-grade environmental and chemical stability, and low thermal conductivity. To overcome such problems, composites need to be redesigned with various filler particles [6]. Additive materials are primarily used to modify and tailor material properties of the composite. By introducing additives into resin system it enhances the processability or durability of the composite. Additives help in increasing the performance or a specific property as well it increases the overall cost of the product. Various additives widely used to boost the thermal and electrical conductivity of the resin are graphite powder, chopped carbon fibre, carbon nano-tubes, SiC nanoparticles, Cu nanoparticles etc.
-
EFFECT OF FILLER PARTICLES ON THERMAL CONDUCTIVITY
Addition of Silicon carbide filler particles to the neat epoxy polymer composites increases thermal conductivity as the volume fraction percentage increases; 20% and 30% SiC filler particles have shown 0.41 and 0.51 W/m K thermal conductivity respectively [7]. The addition of graphene nano- plates (1% weight) increased thermal conductivity and the enhancement was significant due to homogenous dispersion of graphene nano-plates in the epoxy polymer matrix and internal bonding. Thermal conductivity improvement is 33.3% for 1% graphene nano-plates compared to plain epoxy resin [8]. Thermal conductivity of 1.86 W/m K attained higher value with 30% volume fraction carbon Fibre and silicon carbide hybrid fillers, which is higher than that of neat epoxy resin 0.202 W/m K by 9 times [4].
Use of natural fibre, orientation f fibre, in polymer hybrid composites and study of their thermal properties reveals that the thermal conductivity of composites increases with the increase in fibre angle and the maximum value attained is 0.215W/mK at 90° Fibre orientation. The thermal conductivity values are explored in the range of 40°C-70°C temperature variation and the highest value is attained is
0.214 W/mK [9]. The use aluminium and red mud particles in polymer matrix composites to find thermal conductivity, results demonstrates that, there is an improvement in thermal conductivity of about 262% for 25 Vol% of aluminium particle filler in epoxy resin filled composites. For red mud particles it is 203%. Indeed, even there is a huge distinction in thermal conductivity of an aluminium and red mud powder, it is seen slight distinction of thermal conductivity of their composites [10].
There is an improvement of thermal conductivity of epoxy resin aluminium nitride composites, which are developed with a 0 to 35% volume fraction range 100 micron A1N particle size, theoretical and experimental results of polymer composites shown, thermal conductivity increase is very fast for higher fraction by volume (>35%) compared with lower fraction volume (<35%). Experimental & theoretical results of thermal conductivity found very closure [11]. The polymers thermal conductivity using carbon nanotubes with various proportionate which gives increase in
thermal conductivity after introducing SWCNT & MWCNT in polymers composites [12]. Thermal properties of composites shows high density polyethylene silicon particles filler composites thermal conductivity increases with increasing silicon fillers volume fraction, and at 20% volume fraction of silicon effective thermal conductivity reaches to double compared to pure high density polyethylene [13].
The effective study of thermal conductivity of high- density polyethylene composites filled aluminium powder particles numerically with filler content variation on comparing theoretical empirical models result and experimental results, at less particle content experimental, theoretical model and numerical results are very close to each other, greater than 10% filler particles exhibit effective thermal conductivity exponentially. For greater than 10% aluminium powder filled composites failed to predict the behavior of thermal conductivity of theoretical model equations [14].
Polypropylene Boron nitride & talc fillers are used separately in proportions 10, 20, 30 & 40% to find the thermal conductivity of polypropylene composites and noticed increase in thermal conductivity of BN filler composites as compared to talc filler composite and neat polypropylene. Thermal conductivity of polypropylene hybrid composite (PP + BN + Talc) increases marginally 10 V% talc and 20 V% BN gives higher (1.22 W/mK) thermal conductivity [15].
-
EFFECT OF FILLER PARTICLES ON TGA
The improvisation of thermal properties of Kevlar fibre hybrid composites shows Kevlar fibres are better one with 472.0°C, 511.9°C and 536.0°C endothermic peak temperatures. Weight loss of 68.8% observed at 800.0°C, glass transition temperature increases up to 122.5°C with improved thermal stability [16]. Hybrid composites with cardanol, kenaf and recycled carbon have a good thermal stability with their fraction fillers. The melting temperature of hybrid composites increased up to 152.2°C for 50C50K concentration [17]. Thermal analysis of an epoxy resin and carbon black composites provides improvement in glass transition temperature (90°C), the initial decomposition temperature of neat epoxy (from 302°C to 310°C). The addition up to 4% carbon black in epoxy resin shown better results [18].
Thermal property study of TGA test shows decomposition temperature of 1% & 3% titanium nanoparticles found increases and for 5% & 7% titanium nanoparticles decreases as compared to pure polypropylene [19]. Epoxy resin silica composites are exhibited more stable thermally than pure epoxy resin. The interaction of silica particles and epoxy resin brakes the polymer chain. Low thermal stability found in nano sized silica blended composites, due to lower dispersity of nano silica particles. Increase in degradation temperature for epoxy resin hybrid nano silica composites [20]. The use fillers cause increase in thermal conductivity of polymer composites. CNT filler polymer composites exhibited good thermal properties compared with other fillers. TGA test shows that up to 350°C composites are stable with 0.5% weight reduction [21].
Graphite nanoparticles (GNPs) epoxy resin nanocomposites thermal conduction ability increases with the increase in GNPs fraction addition. High thermal conductivity GNPs added to epoxy resin (E-51) causes to develop a lower interfacial thermal resistance in epoxy resin, which influence the transport of phonon intern increases the thermal conductivity of GNPs epoxy resin nanocomposites. Also the GNPs/E-51 composites exhibits high glass transition temperature, due to GNPs surface molecules react with epoxy resin which increases the strength of interface bonding between GNPs and epoxy resin (E-51). The thermal stability of epoxy resin graphite nanoparticle composites improves with the addition of GNPs, the properties like high thermal conductivity, good interfacial compatibility, good mixing of GNPs with epoxy resin are the main reason for thermal stability increase of Graphite nanoparticles (GNPs) epoxy resin nanocomposites [22].
By introducing the carbon nanotubes (CNTs) in glass fibre woven composites causes increase in the thermal degradation temperature about 5°C more than that of plane epoxy resin glass fibre composites. In thermal degradation process CNTs glass fibre composites sustains high temperature as compared to epoxy resin glass fibre composites [3].
-
EFFECT OF FILLER PARTICLES ON CTE Thermal characterization property of polyurethane multi
walled carbon nanotube (PU-MWCNT) composites, adding small composition of multi walled carbon nanotubes in polyurethane polymer matrix thermal degradation temperature of polyurethane composites was improved from 409°C to 421°C. Under the similar temperature range conditions, the coefficient of thermal expansion (CTE) values of polyurethane multi walled carbon nanotube composites reduced in comparison to only polyurethane matrix. A maximum 58.31% reduction in the CTE of PU-MWCNT composites were observed at 5wt% of multi walled nanotubes [23]. Hybrid composites are prepared with epoxy resin, glass fibre, fly ash, stone powder and silicon carbide in a 50:50 matrix fibre and 5% & 20% fillers in weight proportionate. From thermal experiments it is observed that glass fibre epoxy resin (GFER), GFER + silicon carbide 5% and GFER
+ silicon carbide 20% shows high thermal conductivities compared to other composites, but GFER + fly ash 5%, GFER + silicon carbide 20% and GFER + stone powder 20% exhibits low CTE when compared with other composites [24].
Use of hybrid fillers (Aluminium nitride, Silicon carbide, Boron nitride) in polymer composites was found more effective in thermal conductivity increase of HPCs, because of structure filled with high percentage filler material which enhances the connectivity of fibres. In comparing thermal conductivities silicon carbide composites are higher than others. CTE decreases with the increase of filler volume fractions [25]. The reduction in coefficient of thermal expansion, enhancement in effective thermal conductivity and thermal stability, leads to wide scope of high density polyethylene silicon particles filler composites in the electronic field applications [13].
Matrix and Fibre
Filler Material %
Thermal Conductivity (W/m °C)
Thermal Expansion Coefficient
(/ °C)
Reference
50% GF,
50% Epoxy
Nil
2.89
1.96×10-5
[1] 50% GF,
40% Epoxy
10% Fly Ash
1.69
1.85×10-5
50% GF,
35% Epoxy
15% Fly ash
1.23
1.48×10-5
50% GF,
40% Epoxy
10% Stone powder
2.34
1.85×10-5
50% GF,
35% Epoxy
15% Stone powder
1.58
2.59×10-5
50% GF,
40% Epoxy
10% Al2O3
1.32
2.40×10-5
50% GF,
35% Epoxy
15% Al2O3
1.72
1.66×10-5
50% GF,
40% Epoxy
10% Mg(OH)2
1.56
2.44×10-5
50% GF,
35% Epoxy
15% Mg(OH)2
2.38
1.11×10-5
50% GF,
40% Epoxy
10% SiC
3.51
7.40×10-6
50% GF,
35% Epoxy
15% SiC
2.76
3.70×10-6
50% GF,
40% Epoxy
10%
Hematite
2.45
1.85×10-5
50% GF,
35% Epoxy
15%
Hematite
3.06
1.85×10-5
100% Epoxy
Nil
0.30
—–
[7] 90% Epoxy
10% Gr
0.32
—–
90% Epoxy
10% SiC
0.33
—–
90% Epoxy
5%Gr, 5%
SiC
0.33
—–
80% Epoxy
20% Gr
0.46
—–
80% Epoxy
20% SiC
0.41
—–
80% Epoxy
15%Gr, 5%
SiC
0.46
—–
80% Epoxy
5%Gr, 15%
SiC
0.46
—–
80% Epoxy
10% Gr,
10% SiC
0.51
—–
70% Epoxy
30% Gr
0.54
—–
70% Epoxy
30% SiC
0.51
—–
70% Epoxy
25% Gr,
5% SiC
0.52
—–
70% Epoxy
5% Gr,
25% SiC
0.52
—–
70% Epoxy
20% Gr,
10% SiC
0.56
—–
70% Epoxy
10% Gr,
20% SiC
0.54
—–
70% Epoxy
15% Gr,
15% SiC
0.58
—–
60% Epoxy
40% Gr
0.64
—–
60% Epoxy
40% SiC
0.68
—–
60% Epoxy
35% Gr,
5% SiC
0.64
—–
60% Epoxy
5% Gr,
35% SiC
0.62
—–
Matrix and Fibre
Filler Material %
Thermal Conductivity (W/m °C)
Thermal Expansion Coefficient
(/ °C)
Reference
50% GF,
50% Epoxy
Nil
2.89
1.96×10-5
[1] 50% GF,
40% Epoxy
10% Fly Ash
1.69
1.85×10-5
50% GF,
35% Epoxy
15% Fly ash
1.23
1.48×10-5
50% GF,
40% Epoxy
10% Stone powder
2.34
1.85×10-5
50% GF,
35% Epoxy
15% Stone powder
1.58
2.59×10-5
50% GF,
40% Epoxy
10% Al2O3
1.32
2.40×10-5
50% GF,
35% Epoxy
15% Al2O3
1.72
1.66×10-5
50% GF,
40% Epoxy
10% Mg(OH)2
1.56
2.44×10-5
50% GF,
35% Epoxy
15% Mg(OH)2
2.38
1.11×10-5
50% GF,
40% Epoxy
10% SiC
3.51
7.40×10-6
50% GF,
35% Epoxy
15% SiC
2.76
3.70×10-6
50% GF,
40% Epoxy
10%
Hematite
2.45
1.85×10-5
50% GF,
35% Epoxy
15%
Hematite
3.06
1.85×10-5
100% Epoxy
Nil
0.30
—–
[7] 90% Epoxy
10% Gr
0.32
—–
90% Epoxy
10% SiC
0.33
—–
90% Epoxy
5%Gr, 5%
SiC
0.33
—–
80% Epoxy
20% Gr
0.46
—–
80% Epoxy
20% SiC
0.41
—–
80% Epoxy
15%Gr, 5%
SiC
0.46
—–
80% Epoxy
5%Gr, 15%
SiC
0.46
—–
80% Epoxy
10% Gr,
10% SiC
0.51
—–
70% Epoxy
30% Gr
0.54
—–
70% Epoxy
30% SiC
0.51
—–
70% Epoxy
25% Gr,
5% SiC
0.52
—–
70% Epoxy
5% Gr,
25% SiC
0.52
—–
70% Epoxy
20% Gr,
10% SiC
0.56
—–
70% Epoxy
10% Gr,
20% SiC
0.54
—–
70% Epoxy
15% Gr,
15% SiC
0.58
—–
60% Epoxy
40% Gr
0.64
—–
60% Epoxy
40% SiC
0.68
—–
60% Epoxy
35% Gr,
5% SiC
0.64
—–
60% Epoxy
5% Gr,
35% SiC
0.62
—–
TABLE I. VARIOUS FILLER COMPOSITE MATERIAL THERMAL PROPERTIES.
60% Epoxy
30% Gr,
10% SiC
0.62
—–
75% Vol.
Epoxy
25% Vol.
Red Mud particles
1.102
—–
60% Epoxy
10% Gr,
30% SiC
0.61
—–
97.5% Vol.
Epoxy
2.5% Vol.
AlN
0.418
—–
[11] 60% Epoxy
20% Gr,
20% SiC
0.71
—–
95% Vol.
Epoxy
5% Vol. AlN
0.492
—–
100%
Epoxy/Polye ster
Nil
0.12
—–
[8] 92.5% Vol.
Epoxy
7.5% Vol.
AlN
0.561
—–
99.8%
Epoxy/Polye ster
0.2% Wt.
of GNPs
0.09
—–
90% Vol.
Epoxy
10% Vol.
AlN
0.611
—–
87.5% Vol.
Epoxy
12.5% Vol.
AlN
0.661
—–
99.5%
Epoxy/Polye ster
0.5% Wt.
of GNPs
0.1
—–
85% Vol.
Epoxy
15% Vol.
AlN
0.712
—–
99%
Epoxy/Polye ster
1% Wt. of GNPs
0.16
—–
100% Vol. H145 F PP
Nil
0.24
—–
[15] 90% Vol. H145 F PP
10% Vol. BN
0.54
—–
98.5%
Epoxy/Polye ster
1.5% Wt.
of GNPs
0.14
—–
80% Vol. H145 F PP
20% Vol. BN
0.78
—–
83.5% Vol.
Polyester & cobalt naphthenate.
16.5% Vol.
Areca Fibre
0.199
—–
[9] 70% Vol. H145 F PP
30% Vol. BN
1.10
—–
90% Vol. H145 F PP
10% Vol.
Talc
0.28
—–
78.7% Vol.
Polyester & cobalt naphthenate.
21.3% Vol.
Areca Fibre
0.196
—–
80% Vol. H145 F PP
20% Vol.
Talc
0.47
—–
70% Vol. H145 F PP
30% Vol.
Talc
0.59
—–
72.1% Vol.
Polyester & cobalt naphthenate.
27.9% Vol.
Areca Fibre
0.184
—–
70% Vol. H145 F PP
10% Vol.
BN, 20%
Vol. Talc
0.90
—–
70% Vol. H145 F PP
20% Vol.
BN, 10%
Vol. Talc
1.20
—–
65.2% Vol.
Polyester & cobalt naphthenate.
34.8% Vol.
Areca Fibre
0.175
—–
100%
Polyurethane
Nil
128.74×10-6
[23] 95% Vol.
Epoxy
5% Vol. Aluminium particles
0.525
—–
[10] 99%
Polyurethane
1% Wt. MWCNTs
108.54×10-6
90% Vol.
Epoxy
10% Vol.
Aluminium particles
0.648
—–
97%
Polyurethane
3% Wt. MWCNTs
103.56×10-6
95%
Polyurethane
51% Wt. MWCNTs
53.67×10-6
85% Vol.
Epoxy
15% Vol.
Aluminium particles
0.732
—–
50% GF,
45% Epoxy
5% Fly Ash
0.6
18.1×10-5
[24] 80% Vol.
Epoxy
20% Vol.
Aluminium particles
1.232
—–
50% GF,
30% Epoxy
20% Fly ash
0.4
23.5×10-5
75% Vol.
Epoxy
25% Vol.
Aluminium particles
1.317
—–
50% GF,
45% Epoxy
5% Stone powder
1.3
34.8×10-5
95% Vol.
Epoxy
5% Vol. Red Mud particles
0.493
—–
50% GF,
30% Epoxy
20% Stone powder
3.1
16.5×10-5
90% Vol.
Epoxy
10% Vol.
Red Mud particles
0.578
—–
50% GF,
45% Epoxy
5% SiC
5.0
23.8×10-5
50% GF,
30% Epoxy
20% SiC
7.5
16.8×10-5
85% Vol.
Epoxy
15% Vol.
Red Mud particles
0.643
—–
80% Vol.
Epoxy
20% Vol.
Red Mud particles
0.738
—–
-
CONCLUSIONS
The following conclusions are inferred from this study.
-
As the current polymer fibre composites are having very low thermal properties and low thermal resistance against high temperature applications, hence after improvising the thermal properties the polymer fibre reinforced composite materials can be effectively usable in wide applications. The use of polymer composites are distinguished based on type of fibres and fillers content.
-
The current work is focused to study the thermal properties of polymer matrix composites, a specific fillers or additives are used and they play a major role in defining the thermal, mechanical and fire resistance behaviour of polymer matrix composites. The polymer composites abundant use and wide applications, likely to replace or alternate for the metals in future.
-
From the above review study (Table I), it reveals that the thermal properties of polymer matrix composites are depending on the filler materials thermal properties. High thermal conductivity filler materials increases the thermal properties of polymer matrix composites and low thermal conductivity fillers decreases the thermal properties of polymer matrix composites. So based on thermal property requirement the type filler can be used in polymer matrix composites.
ACKNOWLEDGMENT
The Authors are very much grateful to Dr. S. C. Kamate, Principal, HIT, Nidasoshi, Karnataka, India. Dr. Basava T, Dept. of Mechanical Engineering, SDMIT, Ujire, Karnataka, India for their valuable suggestions, guidance and support. I Thank GOD almighty for his grace throughout the work.
REFERENCES
-
K. Devendra and T. Rangaswamy. Thermal Conductivity and Thermal Expansion Coefficient of GFRP Composite Laminates with Fillers. ISSN: 2320-2491 (2013).
-
M. K. Gupta, Investigations on Properties of Glass Fibre Reinforced Polymer Composite, American Journal of Polymer Science & Engineering, (2018) ISSN 2572-5734, Volume 6, Issue 1.
-
Akm Samsur Rahman, Vijaya Rangari, Shaik Jeelani, Thermal and mechanical properties of woven glass fiber reinforced epoxy composites with carbon nanotubes grown in-situ, The International Journal of Engineering And Science (IJES), Volume 4, Issue 12, PP – 54-61, 2015.
-
Aseel A Kareem, Enhanced thermal and electrical properties of epoxy/carbon fibersilicon carbide composites, Advanced Composites Letters Volume 29: 16, 2020, DOI: 10.1177/2633366X19894598.
-
Bhasker Bommara, Dr. M. Devaiah*, P. Laxmi Reddy, M. Ravindra Gandhi, Thermal characterization of fibre reinforced polymer composites and hybrid composites, International Journal of Mechanical Engineering and Technology, Volume 10, Issue 03, March 2019, pp. 10551066.
-
Garima Mittal, Kyong Y. Rhee, Vesna Mikovi-Stankovi, David Hui, Reinforcements in multi-scale polymer composites: Processing, properties, and applications, Composites Part B 138 (2018) 122-139. Science direct, Elsevier.
-
Krishnamachar Srinivas, Mysore Siddalingappa Bhagyashekar. Thermal Conductivity Enhancement of Epoxy by Hybrid Particulate Fillers of Graphite and Silicon Carbide. Journal of Minerals and Materials Characterization and Engineering, 2015, 3, 76-84.
-
Minh-Tai Le and Shyh-Chour Huang, Thermal and mechanical behaviour of hybrid polymer nanocomposite reinforced with graphene nano platelets, Materials 2015, 8, 5526-5536.
-
S. P. Kumar Gudapati, K. Supraja, A.V. Ratna Prasad, Thermal Conductivity Characterization of Areca Palm Fiber Reinforced Polymer Composites, International Journal of Pure and Applied Mathematics, Volume 119 No. 17 2018, 1871-1880, ISSN: 1314-3395.
-
Johan Banjare, Alok Agrawal, Yagya Kumar Sahu, Alok Satapathy, Analytical and experimental investigation of particulate filled polymer composites with enhanced thermal conductivity, Indian Journal of Engineering and Materials Sciences, Vol. 23, December 2016, pp. 389- 398.
-
Alok Agrawal, and Alok Satapathy. Development of a Heat Conduction Model and Investigation onThermal Conductivity Enhancement of AlN/Epoxy Composites. Elsevier Procedia Engineering 51 (2013) 573 578.
-
Manel Haddadi, Boudjemaa Agoudjil, Abderrahim Boudenne, Thermal conductivity of polymer/carbon nanotube composites, Materials Science Forum Vol 714 (2012) pp 99-113.
-
T.K. Dey, M. Tripathi, Thermal properties of silicon powder filled high-density polyethylene composites, Thermochimica Acta 502 (2010) 3542, Elsevier.
-
Dilek Kumlutas, Ismail H, Tavaman, M. Turhan Coban. Thermal conductivity of particle filled polyethylene composite materials. Elsevier Composites Science and Technology 63 (2003) 113 117.
-
A. Suplicz, J.G. Kovacs, Development of thermal conductive hybrid composites, ECCM15 – 15th European Conference on Composite Materials, Venice, Italy, 24-28 June 2012.
-
Vivekanandhan Chinnasamy, Sampath Pavayee Subramani, Sathish Kumar Palaniappan, Bhuvaneshwaran Mylsamy, Karthik Aruchamy, Characterization on thermal properties of glass fiber and kevlar fiber with modified epoxy hybrid composites, Journal of materials research and technology, 2020; 9(3): 31583167.
-
Zahra Dashtizadeh, K. Abdan, M. Jawaid, and Masoud Dashtizadeh, Thermal and flammability properties of kenaf/recycled carbon filled with cardanol hybrid composites, Hindawi International Journal of Polymer Science, Volume 2019, Article ID 9168342, 7 pages.
-
Tanusree Bera, S.K. Acharya, Punyapriya Mishra, Synthesis, mechanical and thermal properties of carbon black/epoxy composites, International Journal of Engineering, Science and Technology Vol. 10, No. 4, 2018, pp. 12-20.
-
A. M. Maharramov, M. A. Ramazanov, A. B. Ahmadova, F. V. Hajiyeva, U. A. Hasanova, Thermal and mechanical properties of polymer-based nanocomposites of isotactic polypropylene and titanium nanoparticles, Digest Journal of Nanomaterials and Biostructures, Vol. 11, No. 2, April – June 2016, p. 365 372.
-
Dongho Kim, Ildoo Chung and Guni Kim, Study on Mechanical and thermal properties of fiber-reinforced epoxy/hybrid-silica composite, Fibers and Polymers 2013, Vol.14, No.12, 2141-2147.
-
M S Nurul and M Mariatti, Effect of thermal conductive fillers on the properties of polypropylene composites, Journal of Thermoplastic Composite Materials, 26(5) 627639. (2011).
-
Junwei Gu, Xutong Yang, Zhaoyuan Lv, Nan Li, Chaobo Liang, Qiuyu Zhang, Functionalized graphite nanoplatelets/epoxy resin nanocomposites with high thermal conductivity, International journal of heat and mass transfer 92 (2016) 1522, Elsevier.
-
Dinesh Kumar, Prashant Jindal, Effect of multi-walled carbon nanotubes on thermal stability of polyurethane nanocomposites, Materials Research Express 6 (2019) 105336.
-
Ravi Kumar B N, Ananda.G.K, Shivaappa.D, Mahesh.H.R. Effect of Fillers on Thermal and Fire Resistance Properties of E-Glass Epoxy Composites. International Journal of Mechanical Engineering Research & Applications (IJMERA) Vol. 1 Issue 4, September 2013.
-
Geon-Woong Lee, Min Park, Junkyung Kim, Jae Ik Lee, Ho Gyu Yoon, Enhanced thermal conductivity of polymer composites filled with hybrid filler, Composites: Part A 37 (2006) 727734, Applied Science & Manufacturing, Elsevier.