
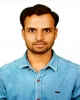
- Open Access
- Authors : Aslamjaved I K , Manjunath B D , Basappa N K
- Paper ID : IJERTV10IS090228
- Volume & Issue : Volume 10, Issue 09 (September 2021)
- Published (First Online): 05-10-2021
- ISSN (Online) : 2278-0181
- Publisher Name : IJERT
- License:
This work is licensed under a Creative Commons Attribution 4.0 International License
Effect of Fillers on Wear Properties of E-Glass/Jute Fiber Epoxy Composites and Analysys of the Results Through Annova Tool
Aslamjaved I K
Lead Engineer,
HCL Technologies, Bangalore, India
Manjunath B D
CAE Engineer,
Basappa N K
Senior Quality Engineer,
Tefabo Product Pvt Ltd,, Bangalore, India
Xitadel technologies, Bangalore, India
Abstract In this research work, the tribological behavior of glass fiber reinforced epoxy composites filled with AL2O3 and Granite. Particulates were studied using a pin-on- disc wear apparatus under dry sliding conditions. The influences of wear parameters like Sliding Speed, Load and Percentage of filler content, on the sliding wear rate were investigated. A plan of experiments based on the Taguchi technique, was performed to acquire data in a controlled way. An orthogonal array and analysis of variance (ANOVA) were applied to investigate the influence of process parameters on the sliding wear behavior of these composites. The Taguchi design of experiment approach eliminates the need for repeated experiments and thus saves time, material and cost. Taguchi approach identifies not only the significant control factors but also their interactions influencing the specific wear rate predominantly. The results shows that the wear parameter Sliding Speed have major impact on wear rate.
Keywords Composites, Fillers, Mechanical, Properties, Strength
-
INTRODUCTION
Composite materials are new generation materials developed to meet the demands of rapid growth of technological changes of the industry. Composite materials are engineering materials made from two or more constituents materials that remain separate and distinct on macroscopic level while forming a single component. It consists of short and soft collagen fibers embedded in a mineral matrix called apatite. A composite material is defined as a structural material created synthetically or artificially by combining two or more materials having dissimilar characteristic. One constituent is called matrix phase and other is called reinforcing phase. Reinforcing phase is embedded in the matrix to give desired characteristic.
Now-a-days, in the field of composite materials all the research showing interest in using the waste material as a filler material. All shows interest in developing the new natural fiber instead of traditional fibers because of their low cost, combustibility, lightweight, low density, high specific strength, renewability, non-abrasively, non-toxicity, low cost and bio-degradability. Still yet many challenges to overcome in order to become largely used as reliable engineering materials for structural elements. However, their use is steadily increasing, and many large industrial corporations are planning to use, or commencing to use, these materials in
their products. Natural fibers are renewable and biodegradable material and are largely available in the nature in worldwide. Pineapple leaf, oil palm fiber Hemp, sisal, jute, kapok, jute, rice husk, bamboo and wood are the fibers most commonly used as reinforcing natural fibers in polymer matrix. Filler materials are used to reduce the material costs, to improve mechanical properties to some extent and in some cases to improve process ability. Besides, it also increases properties like abrasion resistance, hardness and reduce shrinkage. Adding of ceramic micro fillers into the continuous material drastically increases the wear resistance and the properties also changes rapidly due to the varying of the filler percentage.
Properties of composites are strongly dependent on the properties of their constituent materials, their distribution and the interaction among them. The geometry of the reinforcement (shape, size and size distribution) influences the properties of the composite to a great extent. Natural fillers and fibers reinforced thermoplastic composite have successfully proven their high qualities in various fields of technical application. As replacements for conventional synthetic fibers like aramid and glass fibers are increasingly used for reinforcement in the thermoplastic due to their low density, good thermal insulation and mechanical properties, reduced tool wear, unlimited availability, low price, and problem free disposal. Composite materials have successfully substituted the traditional materials in several light weight and high strength applications. The reasons why composites are selected for such applications are mainly their high strength-to weight ratio, high tensile strength at elevated temperatures, high creep resistance and high toughness. Typically, in a composite, the reinforcing materials are strong with low densities while the matrix is usually a ductile or tough material. If the composite is designed and fabricated correctly it combines the strength of the reinforcement with the toughness of the matrix to achieve a combination of desirable properties not available in any single conventional material. The strength of the composites depends primarily on the amount, arrangement and type of fiber and /or particle reinforcement in the resin.
-
EXPERIMENTATION AND METHODOLOGY Two types of Fiber materials are used for reinforcing the
epoxy filled composites in the ratio of volume of jute and
Glass Fiber and rest volume is Epoxy and fillers.
GLASS FIBER
Glass Fiber is a material consisting of numerous extremely fine Fibers of glass. Glass Fiber in its various forms has been the most common reinforcement for polymer matrices. It forms a very strong and light Fiber reinforced polymer (FRP) composite material called Glass reinforced plastic (GRP). Glass Fiber has roughly comparable properties to other Fibers such as polymers and carbon Fiber. Although not as strong or as rigid as carbon Fiber, It is much cheaper and significantly less brittle. A variety of different chemical compositions is commercially available.
The types of Glass Fiber available are
-
A-glass
-
C-glass
-
E-glass
-
For this work E-Glass (7mill) selected as reinforcement material.
JUTE FIBER
Jute is a long, soft, shiny vegetable Fiber that can be spun into coarse, strong threads. Jute is replaced by synthetic materials in many of these , some uses take advantage of jute biodegradable nature, where synthetics would be unsuitable. It is also strong, durable and light fast Fiber.
MATRIX MATERIAL (EPOXY)
Unsaturated polyester, resin L-12 (3202), manufactured by Atul LTD is used as matrix material. Epoxy resins are most commonly used resins. It is the most popular polymer composite matrix (PCM). More than 2/3rd of polymer matrix used in aerospace applications is epoxy based. The main reasons for epoxy being the most used polymer matrix material are high strength, low viscosity and low flow rates, which allow good wetting of Fibers and prevent misalignment Fiber during processing, available in more than 20 grades to meet specific property and producing requirements.
FILLERS
Fillers are ingredients added to enhance the properties such as strength, surface texture, hardness and to enhance wear properties and lower the cost of polymers.
Aluminum oxide is an amphoteric oxide with the chemical formula Al2o3.Aluminium oxide particles is a ceramic powder commonly used filler. It is commonly referred to as Alumina, or in its crystalline form, as well as many other names, reflecting its widespread occurrence in nature and industry. Its most significant use in the production of aluminum metal, although it is also used as abrasive due to its hardnes and as a refractory material due to its high melting point . Low reactivity and low cost make this reinforcement very attractive that require moderate strength, and stiffness improvement while retaining good wear resistance.
Granite powder, a by-product obtained during the sizing of granite stones by processing granite slabs has no end use. In the present study, granite powder is used as the reinforcement to the matrix system to prepare composites.
Granite powder is always massive, hard and tough so it has gained widespread use. It is the by-product material generated by cutting and shaping of building stones in stone cutting plants. The water used for cooling up the cutting saw flows out carrying very fine suspended particles as high viscous liquid known as stone slurry. The stone slurry was oven dried ground and sieved. The average density of stone powder is between 2.65 and 2075g/cm3, its compressive strength usually lies above 200MPa, and its viscosity near STP is 3-6×1019 pa-s. Melting temperature is 1215-12600c.
2.1 FABRICATION OF COMPOSITES
The E-glass-Jute/Epoxy based composites filled with varying concentrations (0, 10 and 15 Vol %) of aluminum oxide (Al2O3), sieved stone powder were prepared. The volume fraction of Fiber, epoxy and filler materials were determined by considering the density, specific gravity and mass. The required ingredients of resin, hardener, and fillers are mixed thoroughly in a basin and the mixture is subsequently stirred constantly. The glass Fiber positioned manually. Mixture is made of brushed uniformly, over the glass plies and Jute plies. Entrapped air is removed manually with squeezes or rollers to complete the laminates structure and the composite is cured at room temperature.
Hybrid laminates of woven jute and glass mat were prepared by hand lay-up technique. For quick and easy removal of the composite sheet a mould release sheet was put over the glass plate. Mould release spray (Biolene) was also applied at the inner surface of the mould wall after it was set on the glass plate. Stacking was made in the order of 11G+1J+9G+1J+9G+1J+9G+1J+9G+1J+11G for 10mm
thickness specimen and 5G+1J+5G+1J+5G for 3mm thickness specimen. Jute and glass fabrics were pre- impregnated with the matrix material consisting of epoxy resin and hardener in the ratio of 10:1. Care was taken to avoid formation of air bubbles during pouring. Pressure was then applied from the top and the mould was allowed to cure at room temperature for 72 hrs. During the application of pressure some polymer squeezes out from the mould. For this, care has already been taken during pouring. After 72 hrs the samples were taken out of the mould, after curing the laminate was cut into required size of erosion and other mechanical tests by Zig-zag cutter machine.
Table 2.1 Composition of Materials
DESIGNATION |
COMPOSITION |
GJE |
Jute Fiber(10%)+Glass Fiber(40%)+Epoxy(50%)+ Filler(0%) |
GJEA1 |
Jute Fiber(10%)+Glass Fiber(40%)+Epoxy(50%)+ Al2o3 Filler(10%) |
GJEA2 |
Jute Fiber(10%)+Glass Fiber(40%)+Epoxy(50%)+ Al2o3 Filler(15%) |
GJEG1 |
Jute Fiber(10%)+Glass Fiber(40%)+Epoxy(50%)+ Granite powder Filler(10%) |
GJEG2 |
Jute Fiber(10%)+Glass Fiber(40%)+Epoxy(50%)+ Granite powder Filler(15%) |
SPECIMEN PREPARATION
The prepared slabs of the composite materials were taken from the mould and then specimens were prepared from composite slabs for wear tests according to standards ASTM-G99-05. The test specimens were cut by laminate by using Zig-Zag board cutter machine. Three identical test specimens were prepared for different tests.
EXPERIMENTATION
Introduction
This chapter describes the details of processing of the HFR composites and the experimental procedures followed for their Mechanical and Wear properties evaluation. Tensile, Flexural, impact and hardness tests were carried out using Universal testing machine, impact machine and hardness testing machine respectively. Three identical samples were tested for tensile strength, Flexural, impact strength and hardness.
Density
Density is also a major factor influencing the selection of a material for any application. Density is defined as the mass per unit volume. It is observed that the composite density values are calculated theoretically from weight fractions by Eq.(1) are not equal to the experimentally measured values [4]. This difference is due to the presence of voids and pores in the composites. The observation shows that more voids are found in the composites with the addition of Fiber as well as filler material.
. (1)
WEAR PROPERTY TESTING
DUCOM pin on disc test apparatus was used to investigate the dry sliding wear characteristics of composite specimens. Dry sliding wear tests were conducted as per ASTM G99 standards [27]. Specimen with size of 10mm x 10mm x 30mm is subjected vertically to the counter face where the contact area is constant. During experiment the specimens remain fixed and disc rotates. Wear test was carried out at sliding velocities of 1.4m/sec, 2m/sec and 2.6m/sec against normal loads of 20N, 40N, and 60N and wear rate was calculated after 23.8 16.7 and 12.8 minutes respectively. Care has been taken that the specimen was continuously cleaned with woolen cloth to avoid the entrapment of wear debris and to achieve uniform experimental procedure. After each test the disc was cleaned using acetone solution. The wear testing machine is microprocessor controlled in which height loss and frictional force can be monitored simultaneously by a PC based data logging system. The height loss of pin specimen was measured using a Linear Variable Differential Transducer (LVDT) and frictional force was measured using a load cell.
Specific Wear is given by
Where,
m = Mass loss in gms
= Density of specimen in g/cc
T = Test duration in sec
v = sliding velocity in m/s
F = Applied load in N
Where,
W and represent the weight fraction and density correspondingly. The suffix f, m and ct stand on behalf of the fiber, matrix and the composite materials respectively. The composites under this investigation consists of three components namely matrix, fiber and particulate filler and the suffix p indicates the particulate filler materials.
The actual density (ce) of the composite can be obtained experimentally by simple water immersion technique. The volume fraction percentage of voids (Vv) in the composites is calculated by the following equation (2)
——— (2)
Designation |
Theoretical Density |
Measured Density |
Void fraction |
GJE |
1.6183 |
1.5621 |
3.472780078 |
GJE A1 |
1.5363 |
1.4816 |
3.560502506 |
GJE A2 |
1.4984 |
1.3884 |
7.341163908 |
GJE G1 |
1.7315 |
1.4358 |
17.07767831 |
GJE G2 |
1.7942 |
1.5093 |
15.87894326 |
15.87894326
Designation |
Theoretical Density |
Measured Density |
Void fraction |
GJE |
1.6183 |
1.5621 |
3.472780078 |
GJE A1 |
1.5363 |
1.4816 |
3.560502506 |
GJE A2 |
1.4984 |
1.3884 |
7.341163908 |
GJE G1 |
1.7315 |
1.4358 |
17.07767831 |
GJE G2 |
1.7942 |
1.5093 |
Table 2.2 Density and void content of different composites
Fig 2.2 Wear test specimen
Table 5.2 Specifications of Wear Testing Machine
Test parameter |
Values |
Remarks |
Specimen pin size |
3 to 12 mm dia in steps of 2mm, 20 to 30mm long |
Independent holders for clamping pin sizes 3,4,6,8,10 & 12 mm & Ball O10 & 12.7 |
Wear disc size |
O165 x 8mm |
En31 hardened to 62HRc-2Nos |
Wear track dia |
Min: 50mm, max:100mm |
Continuously variable |
Disc rotation |
Min: 200 rpm, max:2000 rpm |
Continuously variable in steps of 1rpm |
Normal load |
Min: 5 N, Max: 200N |
Manual loading In steps of 0.5 kg by dead weights |
Frictional force |
Min: 0N, Max: 200N |
Least count 0.1N |
Wear |
± 2000 micrometer |
Least count 1micrometer |
Test ball dia |
10 mm |
Individual ball holder for 10mm |
-
RESULTS AND DISCUSSION
The ultimate tensile strength, impact strength, flexural strength and brinell hardness number for different composition of composite materials are presented in tables
-
and their variations shown in figures 5 to 8 respectively.
Fig. 3.1 Effect of Control factors on Specific wear rate
Fig 3.2 Effect of Control factors on Specific wear rate
Fig 3.3 Effect of Control factors on Specific wear rate
Fig. 3.4 Tested Specimen of Wear Test
The specific wear rate of GJE composite is influenced by applied load value and counter face material. Increase in wear rate is associated with the surface layer reaching the softening point of the polymer consequent to high wear rates. The softening of GJEA1 composite is different from GJE composite due to the difference in heat deformation temperature, which also explains the effectiveness of the formed transfer film. In case of rubbing polymer on polymer, the effectiveness of this film becomes less or disappears due to removal by rubbing fiber. As wear
process in polymers involves adhesive and plastic flow, transitions between regions dominated by each of these, commonly lead to changes in wear rate. Furthermore, the results are closely related to structuring characteristics and transfer film formation on the counterpart material. It is also clear that GFR fibers result in some abrasives besides the adhesive wear mechanism [28].
-
-
Analysis of Wear by ANOVA Taguchi experiments:
Taguchi technique is a powerful tool for the design
of high quality systems. The Taguchi approach to experimentation provides an orderly way to collect, analyze, and interpret data to satisfy the objectives of the study. By using these methods, in the design of experiments, one can obtain the maximum amount of information for the amount of experimentation used. Taguchi parameter design can optimize the performance characteristics through the setting of design parameters and reduce the sensitivity of the system performance to the source of variation. This is accomplished by the efficient use of experimental runs to the combinations of variables studied. This technique is a powerful tool for acquiring the data in a controlled way and to analyze the influence of process variable over some specific variable, which is unknown function of these process variables. The most important stage in the plan of experiments is selection of factors. Taguchi technique creates a standard orthogonal array to accommodate the effect of several factors on the target value and defines the plan of experiments. The experimental results are analyzed using analysis of means and variance to study the influence of factors.
Table 7.1 Process Parameters with their values at three levels.
Levels
Sliding Speed, S in m/s
Load, L in N
Filler Content, F in %
1
1.4
20
0
2
2.6
40
10
3
2.6
60
15
The wear test is carried out with variable sliding speed, load and percentage of filler. The levels of these process variables are as shown in the Table 7.1. The experimentations were conducted as per standard L27 orthogonal array, so as to investigate which design parameter significantly affects the dry sliding wear for the selected combinations of load, sliding speed and percentage of Filler.
Plan of Experiments
The Experiments were conducted as per the standard orthogonal array. The selection of the orthogonal array was based on the condition that the degree of freedom for the orthogonal array should be greater than or equal to sum of those wear parameters. In the present investigation an L27 orthogonal array was chosen, this has 27 rows and 13 columns as shown in the Table 7.2. The wear parameters chosen were (1) sliding speed (2) Load and (3) percentage of Filler and their levels indicated in Table 7.1. The experiments consist of 27 tests (each row in the L27 orthogonal array) and
were assigned with parameters. The first column in table was assigned to sliding speed (S), second column was assigned to load (L), fifth column was assigned to percentage of Filler (F) and remaining columns were assigned to their interactions. The sliding wear tests results were subjected to the analysis of variance.
Standard Orthogonal L27 (313) Array of Taguchi for Wear
td>
2
L27(313)
Test
1
2
3
4
5
6
7
8
9
10
11
12
13
1
1
1
1
1
1
1
1
1
1
1
1
1
1
2
1
1
1
1
2
2
2
2
2
2
2
2
2
3
1
1
1
1
3
3
3
3
3
3
3
3
3
4
1
2
2
2
1
1
1
2
2
2
3
3
3
5
1
2
2
2
2
2
2
3
3
3
1
1
1
6
1
2
2
2
3
3
3
1
1
1
2
2
2
7
1
3
3
3
1
1
1
3
3
3
2
2
2
8
1
3
3
3
2
2
1
1
1
3
3
3
9
1
3
3
3
3
3
3
2
2
2
1
1
1
10
2
1
2
3
1
2
3
1
2
3
1
2
3
11
2
1
2
3
2
3
1
2
3
1
2
3
1
12
2
1
2
3
3
1
2
3
1
2
3
1
2
13
2
2
3
1
1
2
3
2
3
1
3
1
2
14
2
2
3
1
2
3
1
3
1
2
1
2
3
15
2
2
3
1
3
1
2
1
2
3
2
3
1
16
2
3
1
2
1
2
3
3
1
2
2
3
1
17
2
3
1
2
2
3
1
1
2
3
3
1
2
18
2
3
1
2
3
1
2
2
3
1
1
2
3
19
3
1
3
2
1
3
2
1
3
2
1
3
2
20
3
1
3
2
2
1
3
2
1
3
2
1
3
21
3
1
3
2
3
2
1
3
2
1
3
2
1
22
3
2
1
3
1
3
2
2
1
3
3
2
1
23
3
2
1
3
2
1
3
3
2
1
1
3
2
24
3
2
1
3
3
2
1
1
3
2
2
1
3
25
3
3
2
1
1
3
2
3
2
1
2
1
3
26
3
3
2
1
2
1
3
1
3
2
3
2
1
27
3
3
2
1
3
2
1
2
1
3
1
3
2
L27(313)
Test
Sliding Speed, S in m/s
Load, L in N
Filler content, F in %
Specific wear rate mm3/Nm (GJE+Al)
Specific wear rate mm3/Nm (GJE+Gr)
1
1.4
20
0
8.01E-05
8.01E-05
2
1.4
20
10
5.06E-05
5.23E-05
3
1.4
20
15
0.000108
6.63E-05
4
1.4
40
0
7.2E-05
7.2E-05
5
1.4
40
10
7.6E-05
2.61E-05
6
1.4
40
15
2.7E-05
4.14E-05
7
1.4
60
0
4.27E-05
4.27E-05
8
1.4
60
10
1.13E-05
2.32E-05
9
1.4
60
15
3.6E-05
4.42E-05
10
2
20
0
7.99E-05
7.99E-05
11
2
20
10
5.05E-05
0.000156
12
2
20
15
7.19E-05
9.92E-05
13
2
40
0
3.99E-05
3.99E-05
14
2
40
10
8.42E-06
5.21E-05
15
2
40
15
4.49E-05
4.96E-05
16
2
60
0
3.73E-05
3.73E-05
17
2
60
10
1.12E-05
5.21E-05
18
2
60
15
4.19E-05
3.86E-05
19
2.6
20
0
6.41E-05
6.41E-05
20
2.6
20
10
1.69E-05
5.23E-05
21
2.6
20
15
5.41E-05
6.64E-05
22
2.6
40
0
4.81E-05
4.81E-05
23
2.6
40
10
2.54E-05
6.1E-05
24
2.6
40
15
2.71E-05
1.66E-05
25
2.6
60
0
2.67E-05
2.67E-05
26
2.6
60
10
1.69E-05
6.98E-05
27
2.6
60
15
1.8E-05
2.21E-05
L27(313)
Test
Sliding Speed, S in m/s
Load, L in N
Filler content, F in %
Specific wear rate mm3/Nm (GJE+Al)
Specific wear rate mm3/Nm (GJE+Gr)
1
1.4
20
0
8.01E-05
8.01E-05
2
1.4
20
10
5.06E-05
5.23E-05
3
1.4
20
15
0.000108
6.63E-05
4
1.4
40
0
7.2E-05
7.2E-05
5
1.4
40
10
7.6E-05
2.61E-05
6
1.4
40
15
2.7E-05
4.14E-05
7
1.4
60
0
4.27E-05
4.27E-05
8
1.4
60
10
1.13E-05
2.32E-05
9
1.4
60
15
3.6E-05
4.42E-05
10
2
20
0
7.99E-05
7.99E-05
11
2
20
10
5.05E-05
0.000156
12
2
20
15
7.19E-05
9.92E-05
13
2
40
0
3.99E-05
3.99E-05
14
2
40
10
8.42E-06
5.21E-05
15
2
40
15
4.49E-05
4.96E-05
16
2
60
0
3.73E-05
3.73E-05
17
2
60
10
1.12E-05
5.21E-05
18
2
60
15
4.19E-05
3.86E-05
19
2.6
20
0
6.41E-05
6.41E-05
20
2.6
20
10
1.69E-05
5.23E-05
21
2.6
20
15
5.41E-05
6.64E-05
22
2.6
40
0
4.81E-05
4.81E-05
23
2.6
40
10
2.54E-05
6.1E-05
24
2.6
40
15
2.71E-05
1.66E-05
25
2.6
60
0
2.67E-05
2.67E-05
26
2.6
60
10
1.69E-05
6.98E-05
27
2.6
60
15
1.8E-05
2.21E-05
-
Results and Discussion
The experiments were conducted with an aim of relating the influence of sliding speed (S), applied load (L) and percentage of filler (F) with dry sliding wear of both the composites under study. On conducting the experiments as per the orthogonal array, the dry sliding wear results for various combinations of parameters were obtained and shown in Table 7.3. The ANOVA allows analyzing the influence of each variable on the total variance of the results. Table 7.4 shows the results of ANOVA for the wear of the test samples. This analysis was performed with a level of significance of 1% and 10% i.e. for a level of confidence of 99%. The last column of the table shows the contribution % (P) of each variable in the total variation indicating the influence degree on the wear of contact pair. If the Test F value is greater than the F (1%) column value, then the assigned variable is statistically significant.
At the medium values of the wear parameters matrix gets powdered and retains at the site of the fibers, consequently the breakage of the fibers also takes place at certain areas of the sample. Simultaneous accumulation of all the wear parameters at medium level contributes the overall weight loss. However, there is a reduction in the weight loss as compared to the higher values of applied load as mentioned in Table 7.4.
Sources of variance |
SS |
DOF |
Adjacent SS |
F |
P |
S |
2981.81 |
1 |
93.66 |
39.164 |
93.9 |
L |
90.70 |
1 |
39.80 |
16.643 |
2.85 |
F |
14.29 |
1 |
1.24 |
0.517 |
0.45 |
SL |
36.86 |
1 |
15.34 |
6.143 |
1.16 |
LF |
.01 |
1 |
0 |
0.001 |
– |
SF |
.42 |
1 |
.42 |
0.177 |
– |
Error |
50.22 |
21 |
50.22 |
1.58 |
|
Total |
3174.31 |
27 |
100 |
Sources of variance |
SS |
DOF |
Adjacent SS |
F |
P |
S |
2981.81 |
1 |
93.66 |
39.164 |
93.9 |
L |
90.70 |
1 |
39.80 |
16.643 |
2.85 |
F |
14.29 |
1 |
1.24 |
0.517 |
0.45 |
SL |
36.86 |
1 |
15.34 |
6.143 |
1.16 |
LF |
.01 |
1 |
0 |
0.001 |
– |
SF |
.42 |
1 |
.42 |
0.177 |
– |
Error |
50.22 |
21 |
50.22 |
1.58 |
|
Total |
3174.31 |
27 |
100 |
ANOVA for GJE+ Aluminium Powder
S=1.54644 R seq=98.42 % R seq (adj)=97.97%
Box-Cox transformation of the response with the rounded lambda =-0.230791
The 95% CI for Lambda is (-0.437291,-0.108291)
From the ANOVA Table 7.4 for the specific wear rate it is observed that the speed (=83.27%), Filler content (P=93.9%), Load (P=2.85%), interaction (LxF) between Load and Filler content (P=1.16%) have great influence on the specific wear rate and hence these are physically and statistically highly significant. However interactions (SxL) between Speed and Load, interaction between Speed x filler content have lesser effect on specific wear rate as error value ( P=1.58) is higher side hence less significant . From the analysis of ANOVA for specific wear rate, it is observed that the speed(S) has major impact on specific wear rate followed by filler content, load and interaction of (L x F).
Sources of variance |
SS |
DOF |
Adjacent SS |
F |
P |
S |
558908 |
1 |
10346 |
8.7748 |
89.90 |
L |
30372 |
1 |
8668 |
7.3517 |
4.88 |
F |
2534 |
1 |
484 |
0.4102 |
0.4 |
Sources of variance |
SS |
DOF |
Adjacent SS |
F |
P |
S |
558908 |
1 |
10346 |
8.7748 |
89.90 |
L |
30372 |
1 |
8668 |
7.3517 |
4.88 |
F |
2534 |
1 |
484 |
0.4102 |
0.4 |
ANNOVA for GJE+ Granite Powder
SL |
4854 |
1 |
1556 |
1.32 |
0.78 |
LF |
86 |
1 |
60 |
0.051 |
– |
SF |
134 |
1 |
134 |
0.1133 |
– |
Error |
24760 |
21 |
24760 |
3.98 |
|
Total |
621648 |
27 |
100 |
S=34.3372 R seq=96.20 % R seq (adj)=94.88%
Box-Cox transformation of the response with the rounded lambda =-0.5
The 95% CI for Lambda is (-0.778195,-0.230195)
From the ANOVA Table7.5 for the specific wear rate it is observed that the speed (P=89.90%), Filler content (P=0.4%), Load (P=4.88%), interaction (SxL) between Speed and Load (P=1.16%) have great influence on the specific wear rate and hence these are physically and statistically highly significant. However interactions (SxL) between Speed and Load, interaction between Speed x filler content have lesser effect on specific wear rate as error value (P=3.98) is higher side hence less significant. From the analysis of ANOVA for specific wear rate, it is observed that the speed(S) has major impact on specific wear rate followed by load, filler content and interaction of (S x L).
CONCLUSIONS:
The experimental study on the effect of fiber and filler loading on wear behavior of GJE, Aluminum oxide and Granite filled GJE composites leads to the following conclusions:
-
The Specific Wear rate of the GJE composites are influenced by applied load and counter face material
-
From the ANOVA both the fillers Al2O3 and Granite powder it is observed that the control factor sliding speed has major impact on the specific wear rate. GJEA1 shows maximum wear resistance.
REFERENCES:
-
A study on the potential of sugarcane fibers/polyester composite for tribological applications, by N.S.M. El-Tayeb. Wear 265 (2008) 223235.
-
Dry Sliding Wear Behavior of Garnet Particles Reinforced Zinc- Aluminum Alloy Metal Matrix Composites, by Mukundadas Prasanna Kumar et al., ISSN 13921320. Materials Science.Vol.12, No. 3. 2006.
-
Effect Of Load And Speed On Wear Properties Of Al 7075-Fly Ash Composite Material, by DeepakSingla, S.R. Mediratta. ISSN: 2319- 8753 . International Journal of Innovative Research in Science, Engineering and Technology Vol. 2, Issue 5, May 2013.
-
Modeling and Analysis for Wear Performance in Dry Sliding of Epoxy/Glass/PTW Composites Using Full Factorial Techniques, by
M. Sudheer, Ravikantha Prabhu, K. Raju, and Thirumaleshwara Bhat Hindawi Publishing Corporation .ISRN Tribology Volume 2013, Article ID 624813, 11 pages.
-
Studies on dry sliding wear behaviour of Graphite filled glassepoxy composites, by S. Basavarajappa , S. Ellangovan , K.V. Arun. Materials and Design 30 (2009) 26702675.
-
The Role of Fillers on Friction and Slide Wear Characteristics in Glass-Epoxy Composite Systems, by B. Suresha, G. Chandramohan,
J. N. Prakash, V. BalusamyandK Sankaranarayanasamy. Journal of Minerals & Materials Characterization & Engineering, Vol. 5, No.1, pp 87-101, 2006.