
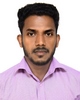
- Open Access
- Authors : Ramdas E R , Rajesh M , Dr. Lalu P P
- Paper ID : IJERTV10IS090102
- Volume & Issue : Volume 10, Issue 09 (September 2021)
- Published (First Online): 22-09-2021
- ISSN (Online) : 2278-0181
- Publisher Name : IJERT
- License:
This work is licensed under a Creative Commons Attribution 4.0 International License
Effect of Fly Ash and Magnesium on Mechanical Properties of Friction Stir Weld Joint in Al6063 Composites
Ramdas E R
Assistant Professor
Kelappaji College of Agricultural Engineering and Technology
Tavanur, Malappuram, India
Rajesh M
Dr. Lalu P P
Assistant Professor
Government Engineering College Thrissur, India
Assistant Professor
SNMIMT Maliankara, Ernakulam, India
Abstract- In the recent past, another class of material, namely the metal matrix composites (MMCs), is becoming increasingly important and drawing attention of engineers. The aim of this study is to investigate the feasibility of joining Flyash, Mg reinforced aluminium alloy (Al6063) composite by friction stir welding. The aluminum-based metal Matrix composite (MMC) material containing 5wt%', 10wt%,15wt% fly ash and 1 wt%, 2 wt%, 3 wt% Mg were fabricated by liquid metallurgy (stir cast) method. The new aspects in the experimental studies of mechanical properties of friction stir weld joint in Al6063 MMC composites were emphasized in this paper. The mechanical properties assessment included tensile and hardness tests. It has been observed that addition of Flyash significantly improves the hardness and tensile properties as compared with that of unreinforced matrix. The results obtained reveal that 10 wt% Flyash in aluminium composite (A16063) improved the ultimate tensile strength to
-
MPa.
Keywords-Stir Casting; Friction Stir Welding; A16063; Fly Ash
-
INTRODUCTION Particulate reinforced metal matrix
composites remain interesting field of materials, such as high specific modulus, high specific strength, low density and easy fabrication. Therefore, these materials are used not only in the field where the working costs are mainly influenced by weight, such as aerospace and aircraft, but also in other industrial fields, like the automotive industry [7]. Along with a great deal of research about the fabricating processes and properties estimation for this kind of materials continuing, the further investigation on practical applications of secondary processing technologies such as machining, joining, plastic forging, joining and so forth are also becoming considerably important and urgent. With regard to the joining of discontinuously reinforced aluminium alloy matrix composites, it is generally referred to the metallurgical joining processes. Extensive efforts have been devoted to investigating the appropriate processes to join the similar or dissimilar composites [5]. There are still many problems on the joining of discontinuously reinforced aluminum matrix composite materials by the generally used fusion welding processes, in the melting state, the liquid welding pool of
composite had a great viscosity with poor flowability, and it is difficult for composite itself to mix with the filler materials.
Consequently, the formation of weld and the quality of welded joint are not satisfactory. When the molten welding pool was cooled down, the reinforcement phases were rejected by the solidification front, and the normal solidification processes of the welding pool had been broken down, and this would lead to micro segregation or inhomogeneous distribution of the reinforcement phases. Finally, there would be many defects in the weld until now, however, it can be said that joining of metal matrix composites is an area still full of open questions. There are still many fundamental research works that should be done to investigate the joining performance of this kind of composite materials in detail [4]. Friction welding finds widespread industrial use as a mass- production process for the joining of materials. In the welding process, the joining surface of the samples is heated to the desired temperature through frictional heat and then a forging pressure is introduced to weld the parts. Friction welding can be used to join metals of widely differing thermal and mechanical properties. Often, combinations that can be friction welded cannot be joined by other welding techniques because of the formation of brittle phases, which make the joint poor in mechanical properties. The sub-melting temperatures and short weld times of friction welding allow many combinations of work metals to be joined [5]. Thus, friction welding technology appears to be the most promising for joining of discontinuously reinforced aluminum alloy matrix composites. As mentioned above, friction welding might be successfully applied in case of a metal matrix composite (MMC) containing short fibers or oxide particles as the strengthening phase.
-
EXPERIMENTAL PROCEDURE
Flyash reinforced Aluminium alloy (A16063) composites, processed by stir casting [1] route was used in this work. The required quantities of fly ash (5, 10, 15
wt. %) and Mg (1, 2, 3 wt%) were taken in powder containers. Then the Fly ash was heated to 450°C and maintained at that temperature for about 1 hr. Then weighed quantity of Al (6063) alloy was melted in a crucible at 750°C which is more than 100°C above liquids temperature of the matrix alloy. The molten metal was stirred to create a vortex and the weighed quantity of preheated fly ash particles were slowly added to the molten alloy. Also corresponding weighed quantity of Mg was added to ensure good wettability of particles with molten metal. After mixing the melt was poured into a prepared mould for the preparation of specimen. After solidification of the composites it will be machined to make it suitable for welding.
TABLE I. CHEMICAL COMPOSITIONS OF AL (6063) ALLOY (WEIGHTPERCENTAGE)
TABLE II. CHEMICAL COMPOSITION OF FLY ASH (WEIGHT PERCENTAGE)
From each composition of A16063-Flyash-Mg composite, 6 mm thick plates were machined to the required dimensions (I 50 x I 50 mm).
A. FSW Tool Geometry
From the literature survey it was found FSW welding has been carried out by using complicated tool geometries [6], which are extremely difficult to manufacture. But it was observed that the complicated tool pin profiles tend to wear out after few numbers of runs leading to a conical form. This has been occurred specially while working with comparatively higher tensile strength materials, e.g. 2xxx or 7xxx series aluminium alloys. Hence in the present study SS304 have been used to fabricate the FSW tools. The material composition and the thermo mechanical properties of SS304 are shown in table 3 and table 4 respectively. The chosen tool geometry and fabricated tool for FSW of 6mm thick aluminum alloy are shown in figure 1 and figure 2 respectively.
TABLE III. COMPOSITION OF SS304 BY PERCENTAGE
Ni
Cr
C
Si
Mn
P
S
Fe
8-11
18-20
0.08
0.75
2max
0.04
0.03
Bal
TABLE IV. PHYSICAL PROPERTIES OF SS304
Density
8.0 g/cm3
Melting point
14000C (25500F)
Tensile strength
Psi-75000, Mpa-515
Yield strength
Psi-30000, Mpa-205
Elongation
35%
Fig.1. FSW Tool Geometry
Fig. 2. Fabricated FSW Tool
To carry out the FSW experiment a vertical milling machine with 7.5 hp motor capacities was used. The tool was mounted in the vertical arbor using a suitable collates. The plates to be joined were clamped to the horizontal bed with zero root gaps. The clamping of the test pieces was done such that the movement of the plates was totally restricted under both plunging and translational forces of the FSW tool. The tool rpm and translational speed of the bed were set prior to each run of welding. After plunging the rotating tool at the plate butt and visually ensuring full contact of the tool shoulder with the plate surface, the bed movement was done. From the literature survey conducted the optimum tool rotational speed and tool traverse speed selected as 1400 rpm and 110 mm/min respectively [3]. A typical experimental FSW setup is shown in figure 3.
Fig.3. FSW Experimental Setup
-
SPECIMEN PREPARATION AND TESTING
The tensile test specimens were prepared by machining from the weld plate. Each specimen having 150 mm length 25 mm breadth and 6 mm thickness. Test specimen for hardness testing was also machined from various composition of weld joint.
-
Tensile Test
Test specimens were prepared according to ASTM E8M-04 standards, each specimen having 150mm length 25 mm breadth and 6 mm thickness, as shown in figure 4. Tensile specimen was loaded in
Universal Testing Machine until the failure of the specimen occurs. Tests were conducted on composites of different combinations of reinforcing materials and ultimate tensile strength was measured.
Fig.4. Joint Configuration and Dimension of Tensile
Specimen
For conducting a standard tensile test, a specimen that has been measured for its cross-sectional area. Uniaxial tensile test is conducted on the fabricated specimen to obtain information regarding the behavior of a given material under gradually increasing stress strain conditions.
-
Hardness Test
Bulk hardness measurements were carried out on the base metal and composite samples by using standard Brinnel hardness test. Brinnel hardness measurements were carried out in order to investigate the influence of particulate weight fraction on the matrix hardness. Load applied was 1000 kgs and indenter was a steel ball of 10 mm diameter. Hardness represents the resistance of material surface to abrasion, scratching and cutting, hardness after gives clear identification of strength. In all hardness tests, a define force is mechanically applied on the test piece for about 15 seconds. The hardness was determined by recording the diameter lengths of indentation produced. The test was carried out at three different locations and the average value was taken as the hardness of the composite weld specimens. Common indenters are made of hardened steel or diamond.
-
-
RESULT AND DISCUSSION
-
Tensile Strength
Figure 5 shows the effect of fly content and Mg on ultimate tensile strength of composite material weld joints. Similarly figure 6 shows the variation of ultimate strength between various composite joint and base metal joint (A16063). In both the cases the addition of fly ash up to 10% with A16063 matrix is increasing the tensile strength of the composite material. By increasing the wt% of fly in the A16063 alloy matrix, dispersion of fly ash particles in a soft ductile A16063 alloy matrix results in improvement in strength. And improvement in UTS may be due to the matrix strengthening that might have occurred following a reduction in composite grain size and the generation of a high dislocation density in the matrix as
a result.
Fig.5. Ultimate Tensile Strength of Reinforced Weld Joints
Figure 6 shows the tensile strength of FSW joints increases gradually up to 10% Fly ash after that it decreases. The decrease in the tensile strength of the joints with fly ash weight fraction beyond 10 % is due to the poor wettability of the reinforcement with the matrix.
Fig.6: Tensile strength of fly ash reinforced and base metal joint
-
Hardness Test
Hardness tests were performed on base metal weld and various composites joints to know the effect of fly ash in matrix material. A load of 1000 kg for a period of 15 seconds was applied on specimens. The hardness was determined by recording the diameter of indentation produced by the ball. The test was carried out across the weld joint at three different locations and the average value was taken as the hardness of specimens. Figure 6 shows effect of Fly ash in hardness of various FSW joints.
Fig.7. Hardness Value of Composite Weld
Figure 7 shows the results of hardness test on base metal (A16063) joint and weld joint containing different wt % of fly ash in it. From the figure 7 it is evident that the hardness of the composite weld joint is much higher than that of its parent metal joint.
Fig.8. Hardness in parent and composite weld
It is also shown that the hardness of the composite material increases with wt% of fly ash content. This may be because of addition of fly ash makes the ductile A16063 alloy into more brittle in nature with increase in the fly ash content. And also the dispersion of fly ash particles enhances the hardness, as particles are harder than A16063 alloy, and render their inherent property of hardness to soft matrix.
REFERENCES
-
P. Shanmughasundaram(2011) Some Studies on Aluminium Fly Ash Composites Fabricated by Two Step Stir Casting Method, European Journal of Scientific Research ISSN 1450- 216X Vol.63 No.2 (2011), pp.204-218, Euro Journals Publishing, Inc. 2011.
-
Parminder Singh (2012) Evaluation of Strength Degradation and Microstructure in Friction Stir Welded Aluminium 6063-T6. International Journal of Engineering Research & Technology (IJERT) Vol. 1 Issue 7, September 2012 ISSN: 2278-0181.
-
Ajay Singh Verma (2012)Effect of Process parameter of AL- 6063 based fly ash composites using Taguchi International Journal of Applied Engineering Research, ISSN 0973-4562 Vol.7 No.11 (2012).
-
Biswajit Parida, (2012), Study of Mechanical and Micro- structural Properties of Friction Stir Welded Al-Alloy. International Journal of Emerging Technology and Advanced Engineering (ISSN 2250-2459, Volume 2, Issue 10, October 2012)
-
R.Madhusudhan (2013) An experimental study on mechanical and microstructural properties of dissimilar aluminium alloy friction stir welds. International Journal of Mechanical and Production Engineering, ISSN (PRINT): 2320-2092, Volume 1, Issue 1, 2013.
-
Rohatgi P.K., Applications of fly ash in synthesizing low-cost MMCs for automotive and other applications, JOM (2006): pp71-76.
-
-
CONCLUSION
-
Based on the study conducted on Al 6063 composite material contain Fly ash and Mg, the following conclusions canbe made:
-
Fly ash upto 15% by weight was successfully added to Al by stir casting route to produce composite.
-
The Friction stir welding was successful to join various wt % of Al6063 Fly Ash alloy.
-
Better mechanical properties (hardness, tensile strength) were obtained with the FSW joint fabricatedwith 10% Fly Ash.
-
An initial stage of a tunnel defect was found at the intersection of weld nugget and thermo- mechanically affected zone.