
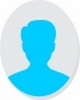
- Open Access
- Authors : Junling Zhao, Lanrong Cai, Min Li
- Paper ID : IJERTV9IS090084
- Volume & Issue : Volume 09, Issue 09 (September 2020)
- Published (First Online): 19-09-2020
- ISSN (Online) : 2278-0181
- Publisher Name : IJERT
- License:
This work is licensed under a Creative Commons Attribution 4.0 International License
Effect of Powder Kinds on Microstructure and Properties of TC4 Layer Strengthened by Powder-Mixed Near-Dry EDM
Junling Zhao1,2, lanrong Cai1,2, Min Li1,2
(1. Tianjin University of Technology and Education, Tianjin 300222;
2. Tianjin High Speed Cutting and Key Processing Laboratory, Tianjin 300222;)
Abstract: A layer of strengthening layer was machined on the surface of TC4 titanium alloy by powder-mixed near-dry EDM surface strengthening technology. The surface observation and wear resistance measurement were carried out, and the changes of surface morphology and wear amount were recorded. The results show that different kinds of mixed powder have significant influence on the surface morphology and wear resistance of the strengthened layer. When Ni and B4C powder are mixed, the wear resistance of the strengthened layer is the best; with the addition of Al powder, the wear resistance of the surface of the strengthened layer decreases, and the thickness of the strengthening layer also decreases, but the strengthening time is shortened, but the wear resistance of the strengthened layer is always higher than that of the substrate surface.
Keywords: Powder; petal structure; strengthening layer; wear resistance
1 INTRODUCTION
After the powder-mixed near-dry EDM technology was proposed, it has always been the focus of the field of EDM surface strengthening, and many new processing technologies have been proposed, especially in the field of the influence of discharge parameters and tool electrodes on the strengthening layer, and many research results have been achieved [1-5]. At present, in the field of powder-mixed near-dry EDM, most of them focus on improving the hardness, friction properties and fatigue resistance of the alloy surface [6,7]. However, there is not much research on the effect of powder kind on the wear resistance of surface modified. Therefore, it is necessary to study the properties of the electrospark strengthened layer under different kinds of powder processing conditions, which can provide more basis for different kinds of powder to strengthen the substrate surface, and also provide more reference indexes for the wear resistance of the strengthened layer.
The kind of powder plays a key role in the process of surface modification. Chen Hongyu et al. Found that the content of Ni powder affects the bending strength of WC Ni Composites [8]. Cai Zhihai and others found that Ni based amorphous coatings with high content were prepared by flame spraying in the form of crystal [9]. Xu Feng et al. Found that adding appropriate amount of Ni can accelerate the mechanical alloying process and shorten the time for producing cermet powder [10]. Yang Jian et al. Found that with pure Ni powder as cladding material, under the condition of laser cladding, the surface of the coating is smooth, the microstructure is dense, and it is well bonded with the substrate [11]. However, there are few studies on the preparation of strengthening layer by adding various strengthening powders together, especially in the field of multiple powder mixing.
In this paper, the effect of Ni powder, Al and B4C powder particles on the microstructure and properties of TC4 titanium alloy surface strengthened by near-dry EDM with mixed powders was verified. Finally, the surface quality and wear resistance of the strengthened layer processed by different kinds of powder were studied and analyzed by observing the surface morphology and measuring the wear loss of the strengthened layer with different powder kinds.
2 TEST MATERIALS AND METHODS
In this paper, different kinds of strengthening powder are used as the main factors in this experiment. In this experiment, powder-mixed near-dry EDM technology was applied on af1100 EDM machine tool to strengthen the surface of TC4 titanium alloy. The size of TC4 titanium alloy matrix was 10mmx10mmx10mm. Using B4C, Al and Ni powder particles with average size of 7m, 0.3g/l solution of Ni + Al, Ni + B4C and Ni + Al + B4C mixed with deionized water as strengthening medium, graphite as tool electrode, peak current of 8.2A, pulse width of 100 s, pulse gap of 100 s, pulse voltage of 120 V and processing depth of 0.1 mm were selected.
In this experiment, the surface morphology and microstructure of the strengthened layer were observed by tescan Vega TS 5136xM scanning electron microscope and super field depth microscope, and the effects of different kinds of mixed powder on the microstructure of the strengthened layer were analyzed. The wear loss of different samples was tested by MM-200 wear tester. The rotation speed was set at 200R / min, the load was 100N, and the test time was 7min. The wear amount in the test process was recorded and analyzed.
3 RESULTS AND ANALYSIS
-
Effect of different kinds of powder on the surface structure of strengthening layer
fragment
fragment
100m
100m
-
Ni+Al, low power (b) Ni+Al, local amplification
crack
crack
100m
petal
100m
petal
(c)Ni+B4C, low power (d)Ni+B4C, local amplification
crack
crack
Small fragment
Small fragment
20m
20m
20m
20m
100
100
(e)Ni+Al+B4C, low power (f)Ni+Al+B4C, local amplification
Fig. 1 Surface morphology of strengthening layer under different kinds of mixed powder
In Fig. 1, it can be found that the structure of strengthening phase is formed on the strong flower layer, and the surface of the strengthening layer is uneven. However, under the condition of different kinds of powder mixing, the surface morphology of the strengthening layer is slightly different, and the shape of the strengthening phase is different. This is due to the different characteristics of Al powder and B4C powder added in the process of EDM strengthening. When the strengthening powder Ni, Al powder and B4C powder are mixed as strengthening medium, the high temperature melting and rapid solidification rate between graphite electrode material and matrix material are different, resulting in different morphology of strengthening layer and microstructure growth of strengthening phase.
From (a) and (b) of Fig. 1, it can be found that there are more short and thick petal like strengthening phases on the strengthening layer, which are dense and uniform. In the local enlarged view, we can see that the petal like strengthening phases are scattered and piled up, but there are microcracks; in (c) and (d), it is found that there are more and evenly distributed long petal shaped strengthening phases on the strengthening layer, and there are lamellar structures around the petals, and there are few cracks; in (E) and (d), there are many long petal shaped strengthening phases (f) In the figure, it can be clearly seen that the end of petal like tissue is mostly spherical, with poor overall roughness. There are a large number of small pieces of tissue on the petal like structure, and cracks are generated on the petal like strengthening phase.
-
-
Effect of different powder kinds on the thickness of strengthening layer
Table1. Section thickness of strengthened layer(m)
Samples
position1
position2
position3
position4
position5
average value
Ni+Al
18.11
17.54
16.73
19.12
18.32
17.96
Ni+B4C
19.66
18.97
20.14
19.73
19.53
Ni+Al+B4C
17.64
18.83
17.63
19.89
18.39
18.47
Fig. 2 Thickness of strengthening layer under different powder mixing kinds
It can be seen from table 1 that the average thickness of the strengthened layer obtained by the mixed processing of Ni and B4C is the largest, which is 19.53 m; when the processing of Ni and Al is mixed, the average thickness of the strengthened layer is the smallest, which is 17.96 M. This is because the melting point of Al is relatively low. Under the same processing conditions, the melting energy of Al powder is small and the melting rate is fast. In addition, due to the light weight of Al powder, it is easy to float in the solution and is not easy to be melted to the processing surface. In Figure 2, it can be clearly seen that with the addition of Al powder, the thickness of strengthening layer decreases; when Ni and B4C are mixed, the thickness of each position is the largest.
-
Effect of different powder kinds on strengthening time
Table2. Strengthened time under different powder-mixed conditions
Samples
time1
time2
time3
average time
Ni+Al
121
133
127
127
Ni+B4C
139
154
133
142
Ni+Al+B4C
129
156
126
137
It can be found from table 2 that among the three test schemes, the strengthening time is the shortest when Ni and Al powders are mixed. Compared with the traditional EDM process, powder-mixed near-dry EDM surface strengthening has improved the efficiency. With the increase of powder mixing kinds, the strengthening time is also different. Because the melting point of Al powder is low and the ionization energy is low, the machining efficiency is improved and the surface strengthening time is reduced in the mixed powder strengthening medium containing Al powder.
-
Effect of different powder kinds on wear resistance of strengthened layer
Table3. Wear mass losses of different strengthened samples and TC4 base material
Samples
Mass before experimental/g
Mass after experimental/g
Mass loss/g
TC4 base material
4.314
4.272
0.042
Ni+Al
4.273
4.250
0.023
Ni+B4C
4.354
4.337
0.017
Ni+Al+B4C
4.269
4.248
0.021
It can be found in Table 3 that the wear loss decreases after the powder-mixed near-dry EDM strengthening. When Ni and B4C are mixed strengthened, the wear loss decreases most, which is due to the presence of strengthening phases such as TiC in the strengthened layer[12], which can improve the wear resistance of the surface. When Al powder is added into the strengthening powder, the petal structure on the strengthening layer grows in a slender shape, and small flake tissue blocks appear in the surrounding tissue. The morphology of these structures is not conducive to the improvement of wear resistance. The reason is that Al powder needs low energy and can melt and solidify fully and rapidly. The remaining energy released by EDM will make the machined surface continue to bombard again, and the microstructure is unstable in the growth process. Therefore, there are more debris like structures on the surface of the strengthened layer. When Ni and B4C powders were mixed, petal like tissues on the surface of the strengthening layer grew well, and most of them were short and thick petals with dense and uniform distribution. This is due to the high melting point of B4C, which requires a large amount of energy in the process of discharge breakdown strengthening, and there is no large residual discharge energy, which makes the microstructure growth stable.
-
CONCLUSION
-
The results show that petal like strengthening phase can be obtained in all kinds of mixed powder processing conditions, but the surface morphology is different. When Ni and B4C powder are mixed, the wear resistance of the strengthened layer is the best.
-
When Al powder is added, the thickness of strengthening layer is reduced. When Ni and B4C powder are mixed, the thickness of strengthened layer is the largest.
-
The time required to strengthen the surface is affected by the kind of mixed powder, but there is no significant difference in the processing time. When Al powder is mixed, the strengthening time is reduced.
REFERENCE:
-
Santosh KS and Saurav D. Experimental studies on graphite powder-mixed electro-discharge machining of Inconel 718 super alloys: Comparison with conventional electro-discharge machining. Proc IMechE Part E: J Process Mechanical Engineering 2019; 233(2): 384-402.
-
Li Min, Wang Hongwei, Cai lanrong, et al. Microstructure and properties of surface strengthened TC4 titanium alloy by EDM [J]. Aerospace materials technology, 2013, 3:95-99.
-
Li Min, Wang Hongwei, Cai lanrong, et al. Study on surface strengthening of TC4 titanium alloy by EDM in different media [J]. Special casting and nonferrous alloy, 2013, 33 (6): 499-502.
-
Liu Shijie, Cai lanrong, Li Min, et al. Study on micro crack of TC4 strengthened layer by near-dry EDM [J]. Manufacturing technology and machine tool, 2019, 3:100-103.
-
Liu Shijie, Cai lanrong, Li Min, et al. Effect of electrode near-dry EDM surface strengthening on Microstructure and properties of TC4 strengthening layer [J]. Machine tool and hydraulic, 2019, 47 (9): 32-35.
-
Santosh KS and Saurav D. Experimental studies on graphite powder-mixed electro-discharge machining of Inconel 718 super alloys: Comparison with conventional electro-discharge machining[J]. Proc IMechE Part E: J Process Mechanical Engineering 2019; 233(2): 384-402.
-
Kumar S, Batish A, Singh R, et al. A mathematical model to predict material removal rate during electric discharge machining of cryogenically treated titanium alloys[J]. Proc IMechE, Part B: J Engineering Manufacture Manuf 2015; 229(2): 214-228.
-
Carlos MR and Patricio F. Comparison between different methods for experimental analysis of surface integrity in die-sinking electro-discharge machining processes[J]. Proc IMechE Part B: J Engineering Manufacture 2020; 234(3): 479-488.
-
Chen Hongyu, Wang Zhaocheng, Luo Laima, Zhu Liu, Tu Zhibiao,Wu Yucheng.Effect of Ni Content on Microstructure and Properties of WC-Ni Composites Prepared by Electroless Plating and Powder Metallurgy[J].Rare Metal Materials and Engineering,2017,46102820-2824.
-
Cai Zhihai, you Jiayu, Shang Junchao, Du Xiaokun, Qin hang, Liu Jian. Preparation and characterization of Ni based alloy powder and amorphous coating [J]. Material protection, 2019,52 (3): 64-67.
-
Xu Feng, Zhou Xiaoping, Fang kaize. Acceleration effect of Ni in mechanical alloying of al-tio2-b2o3 powder [J]. Acta materia heat treatment, 2016,37 (3): 181-187.
-
Li Min, Cai lanrong. Microstructure and properties of TC4 titanium alloy strengthened by powder mixed near-dry EDM [J]. Special casting and nonferrous alloy, 2017,37 (9): 1014-1017.