
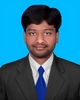
- Open Access
- Authors : Manjunath N K , Annapurna B P , Prakash T B , Shashi Shekhar Singh
- Paper ID : IJERTV10IS010205
- Volume & Issue : Volume 10, Issue 01 (January 2021)
- Published (First Online): 30-01-2021
- ISSN (Online) : 2278-0181
- Publisher Name : IJERT
- License:
This work is licensed under a Creative Commons Attribution 4.0 International License
Effect of Sulphate Attack on Rice Husk Ash-Filtered Sand Self-Compacting Concrete
Manjunath N K[1], Dr. Annapurna B P[2], Prakash T B[3], Shashi Shekhar Singh[4]
Assistant Professor, Professor, BMS Evening College of Engineering, Department of Civil Engineering, Bangalore [1], [3] Professor, University Visvesvaraya College of Engineering, Faculty of Engineering – Civil, Bangalore [2] Associate Professor, Madda Walabu University, Department of Civil Engineering, Bale Robe, Ethiopia [4]
Abstract:- Experiments were conducted to study the effect of rice husk ash and filtered sand on the durability property sulphate attack. In this study M70 grade concrete with rice husk ash, filtered sand and superplasticizer were used. Cement and sand was replaced at the levels of 5%, 10%, 15%, 20% and 25%, 50%, 75%, 100% respectively. From the test results, it was observed that rice husk ash SCC and rice husk ash filtered sand SCC has shown better performance than conventional concrete.
Keywords:- Fresh Properties, Durability Properties, Self- Compacting Concrete (SCC), Rice Husk Ash (RHA), Filtered Sand (FS), Sulphate Resistance, Sodium Sulphate (Na2So4).
INTRODUCTION
Concrete is a widely used construction material for various types of structures due to structural stability and strength. All the materials required producing such huge quantities of concrete come from the earths crust. Thus, it deflects its resources every year creating ecological strains. On the other hand, human activities on earth produce solid wastes in considerable quantities of over 2500/MT per year, including industrial wastes, agricultural wastes and wastes from rural and urban societies. Recent technological development has shown that these materials are valuable as inorganic and organic resources and can produce various useful products. Amongst the solid wastes, the most prominent ones are fly ash, blast furnace slag, rice husk ash, silica fume and demolished construction materials.
From the middle of 20th century, there had been an increase in the consumption of mineral admixtures by the cement and concrete industries. This increasing demand for cement and concrete is met by partial cement replacement. Substantial energy and cost savings can result when industrial by-products are used as a partial replacement for the energy intense Portland cement. The use of by-products is an environmentalfriendly method of disposal of large quantities of materials that would otherwise pollute land, water and air. The current cement production rate of the world, which is approximately 1.2 billion tones/year, is expected to grow exponentially to about 2 billion tones/year by 2015. Most of the increase in demand will be met by the use of supplementary cementing materials. Prior to 1970, RHA was usually produced by uncontrolled combustion and the ash so produced was crystalline and possessed poor pozzolanic properties. In 1973, Mehta
published the first of several papers describing the effect of pyro processing parameters on the pozzolanic reactivity of RHA. Based on his research, Pitt designed a fluidized bed furnace for controlled burning of rice husks. By burning the rice husks under a controlled temperature and atmosphere, a highly reactive RHA was obtained. The utilization of RHA as a pozzolanic material in cement and concrete provides several advantages, such as improved strength and durability properties, reduced materials cost due to cement savings and environmental benefits related to the disposal of waste materials.
The main components of concrete are cement, sand & coarse aggregate. The production of cement adds pollution to the environment is a well-known fact to civil engineers. River sand which is used as fine aggregate is becoming very scarce, sand mining is discouraged to save the rivers of our country. Because of these environmental and economic reasons it requires thinking about the use of industrial wastes as alternative materials in concrete production, which not only reduce the cost of production of concrete but also controls the pollution relatively.
Rice plant is one of the plants that absorbs silica from the soil and assimilates it into its structure during the growth (Smith et al., 1986). Rice husk is the outer covering of the grain of rice plant with a high concentration of silica, generally more than 80-85%. Surface soils from tank beds, agricultural fields and village common lands have been excavated and washed to produce a kind of artificial sand in order to meet the enormous demand known as filtered sand. Only source materials with suitable strength, durability and shape characteristics should be considered. Production generally involves screening and possible washing. Separating into discrete fractions, recombining and blending may be necessary.
Therefore the utilization of Rice Husk Ash (RHA) & Filtered Sand (FS) in concrete for the replacement of cement & sand, environmentally and economically advantageous.
In the present study Portland cement and sand was replaced by RHA and FS at various percentages to study strength and durability property sulphate attack.
EXPERIMENTAL PROGRAMME
MATERIALS USED
Cement: ordinary Portland cement of 53 grade confirming to IS: 12269-1987 was used for the present experimental investigation. The cement was tested as per the Indian standards IS: 4031-1988. The test results are given in Table 1.
Fine Aggregates: Natural river sand as per IS: 383-1987 was used. The physical properties and sieve analysis of fine aggregate are presented in Table 2.
Filtered Sand: IS: 383-1987 was used. The physical properties obtained on conducting sieve analysis and specific gravity tests for Filter Sand and for different replacement levels of sand by Filter Sand is presented in Table 3. The amount of silt content in sand to be used in concrete should be less than 5% according to codal provisions (IS 383). If the amount of silt content is higher than 5% affects the strength of concrete. Hence the amount of silt content in the present filtered sand is investigated by using Hydrometer test and results shown in Table 4.
Coarse Aggregates: Crushed Granite jelly of size 12.5mm down confirming to IS: 383-1987 was used as shown in Table 5.
Rice Husk Ash: The rice husk ash obtained from Maddur (Mandya District.). RHA used for investigation have tested in the Civil Aid and the chemical characteristics are given in Table 6.
Superplasticizer: Polycarboxylic ether based super plasticizer Glenium 6100 has been used in present research work.
MIX PROPORTIONING
For the present investigation, High strength self- compacting concrete of grade M70 was aimed. To achieve this grade of concrete, OKAMURA (JAPANESE) METHOD of mix design was used.
NOTE: [C.SCC – Convention Self Compacting Concrete with only Cement & Natural Sand without RHA & FS].
The mix proportions obtained for C.SCC of M70 grade is 1:1.12:1.17 is been replaced by RHA & FS in place of cement & natural sand by different percentages, which is tabulated in Table 7.
Note: C.SCC-Conventional Concrete (0%RHA, 0%FS);
A Series-5% RHA; B Series-10% RHA; C Series-15% RHA; D Series-20% RHA;
Ao A1 A2 A3 A4 5% RHA, (100%NS+0%FS, 75%NS+25%FS, 50%NS+50%FS, 25%NS+75%FS,
0%NS+100%FS);
Bo B1 B2 B3 B4 10% RHA, (100%NS+0%FS, 75%NS+25%FS, 50%NS+50%FS, 25%NS+75%FS,
0%NS+100%FS);
Co C1 C2 C3 C4 15% RHA, (100%NS+0%FS, 75%NS+25%FS, 50%NS+50%FS, 25%NS+75%FS,
0%NS+100%FS);
Do D1 D2 D3 D4 20% RHA, (100%NS+0%FS, 75%NS+25%FS, 50%NS+50%FS, 25%NS+75%FS,
0%NS+100%FS).
TESTING OF SCC
It is important to mention that none of the test methods for SCC have yet been standardized and included in Indian Standard Code for the present.
The following are some of the features of SCC mentioned in Indian standard code IS: 456-2000.
-
Slump flow: Minimum 600mm.
-
Sufficient amount of fines (<12.5mm) preferably in the range of 400kg/m3 to 600kg/m3.This can be achieved by having sand content more than 38% and using mineral admixture to the order of 25% to 50% by mass of cementitious materials.
-
Use of high range water reducing (HRWR) admixture and viscosity modifying agent (VMA) in appropriate dosages are permitted.
European guidelines for testing, covers number of parameters ranging from material selection, mixture design and testing methods like slump flow test, L-box test and V- funnel test as recommended by EFNARC for determining properties of SCC in fresh state. Most of Indian researchers are following these guidelines to determine the rheological properties of SCC mixes.
TESTING METHODS OF SCC
Different methods have been developed to characterize the rheological properties of SCC. No single method has been found until date, which characterizes all the relevant workability aspects. Each mix has been tested by more than one test method for the different workability parameters.
Following are the tests recommended by European guidelines.
-
Slump flow test- The slump flow test is used to assess the horizontal flow of SCC in the absence of obstructions. The test also indicates resistance to segregation. On lifting the slump cone, filled with concrete the average diameter of spread of the concrete is measured. It indicates the filling ability of the concrete.
-
V-funnel test- The flowability test of the fresh concrete can be tested with the V-funnel test, where by the flow time is measured. The funnel is filled with about 22kgs of concrete and the time taken for it to flow through the apparatus is measured. Shorter flow time indicate greater flowability.
-
L-Box test- This is a widely used test, suitable for laboratory and site use. It accesses filling and passing ability of SCC and serious lack of suitability can be detected visually. The vertical section of the L-box is filled with concrete, and then the gate is lifted to let the concrete flow into the horizontal section. Blocking ratio, it indicates passing ability of concrete or the dosage to which the passage of concrete through the bars is restricted.
TESTS CONDUCTED
Sulphate Attack Test
This test was carried out on the specimens of total number of 126 cubes of 100 mm size after 28 and 56 days curing period. The specimens were taken from the curing tank and initial weight was taken. 5% of sodium sulphate (Na2So4) by weight of water was added with water as per earlier investigators and a set of specimens were immersed continuously for a period of 28 days to determine the sulphate attack of the concrete with and without RHA along with FS.
The concentration of the solution was maintained throughout this period by changing the solution periodically. The specimens were taken out from the sulphate solution after 28 days of continuous soaking. The surface of the cubes were cleaned, weighed and then tested in the compression testing machine under the uniform rate of loading of 140 kg/cm2/min. The changes in strength of concrete cubes were calculated as per IS: 516-1959.
RESULTS AND DISCUSSIONS
The slump flow characteristics, V-funnel & L-box of the mixtures satisfies the EFNARC requirement. Slump flow decreases with increase in RHA content along with FS. The RHA indicates the increase in the viscosity of concrete. The blocking ratio in L-box test were as per requirement of SCC mixes as laid down by EFNARC guidelines. The results are presented in Table 8.
The fresh concrete properties compared to EFNARC specifications, the slump obtained from RHA-FS SCC is between 768 mm to 653mm. The V-Funnel time obtained from RHA-FS SCC is between 2.95 sec to 5.12 sec. The H2/H1 ratio obtained from RHAFS SCC is between 0.945 to 0.862.The fresh concrete properties of RHA-FS SCC obtained are within the EFNARC specifications.
Compressive Strength:
From the Table and Fig following observations are made: The partial replacement of cement by RHA alone in C.SCC (RHA-FS SCC) reduces the weight of C.SCC, with increase in percentage of RHA the reduction in weight also increases. The weight of RHA-FS SCC with RHA of 5%, 10%, 15% and 20% and FS of 0% (A0, B0, C0 and D0) is 2.34, 2.11, 2.00 and 1.99 kgs respectively, whereas weight of C.SCC is 2.4 kg.
In addition to the replacement of cement by RHA, the natural sand partially replaced by FS in SCC (A1, A2, A3, A4 series), reduces the weight of RHA-FS SCC specimen further, for a typical case of RHA-FS SCC with 10% RHA and FS of 25%, 50%, 75% and 100% (B1, B2, B3, B4 series)
the weights are 2.00, 2.10, 1.99 and 1.98 kgs respectively, whereas the weight of RHA-FS SCC of B0 (10% RHA and 0% FS) is of 2.11 kg.
Hence from the above observations the replacement of cement and natural sand by RHA and FS respectively in SCC (RHA-FS SCC) reduces the weight of SCC in comparison to C.SCC.
From Table and Fig the following observations are made:
The SCC with RHA attains significant strength only after 28 days of curing unlike Conventional Self Compacting Concrete (0% RHA, 0% FS) which attains its strength at 28 days of curing.
The compressive strength of RHA-FS SCC for different replacement level of FS from 0% to 100% with 5%, 10%, 15% and 20% of RHA varies between 73.18 N/mm2 to
58.36 N/mm2; 67.54 N/mm2 to 50.36 N/mm2; 53.77 N/mm2
to 42.07 N/mm2 and 45.75 N/mm2 to 37.03 N/mm2 respectively. Whereas compressive strength of Conventional SCC is 79.69 N/mm2.
The compressive strength of RHA-FS SCC of A-series SCC i.e. 5% RHA and FS of 0%, 25%, 50%, 75% and
100% are 73.18 N/mm2, 68.44 N/mm2, 70.81 N/mm2, 64.88
N/mm2 and 58.36 N/mm2. Similar variations are observed for RHA of 10%, 15% and 20% i.e. B, C and D-series.
The RHA-FS SCC with replacement of 5%, 10%, 15% & 20% of RHA and replacement of FS of 50% (A2, B2, C2 & D2) the Compressive strength compared to 0% FS (A0, B0, C0 & D0) reduces, it reduces by 3.24%, 2.62%, 14.60% & 0.60% respectively. And when compared to 25% of FS (A3, B3, C3 & D3) the compressive strength increases, it increases by 3.47%, 3.74%, 9.34% & 3.75% respectively.
The replacement of sand by FS in RHA-FS SCC influences in reduction of the compressive strength. However the replacement level of FS of 50% (A2, B2, C2 & D2) gives higher strength when compared to other replacement levels of FS.
Hence from the above observations replacement of cement partially by RHA reduces the compressive strength compared to C.SCC. The compressive strength of RHA-FS SCC is reduced further when natural sand is replaced partially by FS.
Sulphate Resistance:
-
From the Table, it is observed that C.SCC and RHA-FS- SCC (A0, B0, C0 and D0) specimens when immersed in 5% Na2so4 solution doesnt lose its compressive strength instead it shows a marginal gain in weight.
-
The gain/loss in weights of C.SCC and RHA-FS- SCC when immersed in 5% Na2so4 solution are similar in 28 and 56 days curing period. However, the effect of variation in compressive strengths is higher in the specimens with 56 days of curing period.
-
The percentage gain in strength in RHA-FS SCC of A0, B0, C0 and D0 SCC specimens were found to be 2.68%, 5.20%, 1.91%, and 0.44%, at 28 days curing period and 4.16%, 1.37%, 6.97% and 4.68% at 56 days curing period respectively.
-
It is also observed that as the natural sand replaced by FS in RHA-FS SCC (A1-A4, B1-B4, C1-C4, D1-D4) immersed in 5% Na2so4 the strength decreases, and the reduction in strength increases with increase in % of FS. The strength reduces by 0.35%-5.15%; 0.7%-9.48%, 5.21%- 12.97%; 4.38%-2.52% respectively.
-
The reduction in compressive strength increases considerably when the % of FS is greater than or equal to 50%. The % reduction in compressive strengths of A3, A4; B3, B4; C3, C4; and D3, D4 are 6.01%, 5.15%; 7.47%, 9.48%; 8.10, 12.97%: and 1.99%, 2.52% respectively.
-
From all the observations, it can be seen that the resistance to sulphate attack of RHA-FS SCC specimens with partial replacement of cement with RHA and 0% FS (A0, B0, C0, D0) has more resistance than the C.SCC.
However, the partial replacement of natural sand by FS reduces the resistance of sulphate attack.
CONCLUSIONS
Fresh properties:
RHA contributes in the reduction of agricultural waste that is the main cause of environmental problems in agricultural countries. On the other hand, it is an approach to improve the quality of concrete without using costly additives such as silica fume, GGBFS etc.
Due to the presence of RHA in SCC along with FS, the required strength of SCC is obtained to actual values, after 56 days of curing unlike normal concrete which attains the strength at 28days.
The presence of RHA reduces the slump, with the increase in quantity of RHA in SCCs the reduction in slump also increases. The addition of FS along with RHA further reduces the slump. For D4-Mix (20% RHA+100% FS) the slump reduced frrom768 mm (Conventional SCC mix) to 653 mm.
The T500 time increases with the increase in percentage of RHA. The presence of FS further increases the T500 time i.e., 2.95 sec to 5.12 sec.
The increase of RHA affects the consistency of flow of SCC. The presence of FS along with RHA, add to the increase in reduction of consistency of flow.
The V Funnel time increases with the increase in percentage of RHA. The presence of FS further increases the V Funnel time.
Durability properties:
-
The RHA-FS SCC of (A0 B0 C0 D0) when immersed in sulphate solution gains weight, the
% gain in weight is higher than the C.SCC. With partial replacement of natural sand by FS of 25% to 100% shows marginal loss in weight for all series of specimens (A, B, C, D).
-
The resistance to sulphate attack of RHA-FS SCC specimens with replacement level of RHA of 5%, 10%, 15% and 20% and FS of 0% (A0, B0, C0 and D0) has more resistance than the C.SCC. However, the partial replacement of natural sand by FS reduces the resistance of sulphate attack.
-
Hence the RHA-FS SCC with replacement of cement by RHA is more durable than the RHA-FS SCC with replacement of natural sand by filter sand.
REFERENCES
-
V.Ramasamy* Dr.S.Biswas, Durability Properties of Rice Husk Ash Concrete ICI Journal, October-December 2009.
-
Salas*, 1, M. A. Ospina1, S. Delvasto2 and R. MejÃa de Gutierrez2, Study on the Pozzolanic Properties of Silica Obtained from Rice Husk by Chemical and Thermal Process 1 Materials Engineer, Ph.D Student, Composites Materials Group, CENM, Universidad del Valle, Cali, Colombia, 2 Titular Professor, Composites Materials Group, CENM, Universidad del Valle, Cali, Colombia, Received zzz, revised zzz, accepted zzz, Published online zzz.
-
Alireza Naji Givi 1, Suraya Abdul Rashid 2, Farah Nora A. Aziz 3, Mohamad Amran Mohd Salleh 2, Contribution of Rice Husk Ash to the Properties of Mortar and Concrete: A Review Journal of American Science, 2010;6(3).
-
A.A.Ramezanianpour1, P.Pourbeik2, F.Moodi3, Sulfate Resistance of Concretes Containing Rice Husk Ash 5th National Congress on Civil Engineering, May 4-6, 2010, Ferdowsi University of Mashhad, Mashhad, Iran.
-
P. Chindaprasirt a, C. Jaturapitakkul b, U. Rattanasak c,*, Influence of fineness of rice husk ash and additives on the properties of lightweight aggregate Fuel 88 (2009) 158162.
-
Paratibha Aggarwal*, Yogesh Aggarwal, S M Gupta, R Siddique, Properties of Self-Compacting Concrete An Overview 30th Conference on Our World in Concrete & Structures: 23 24 August 2005, Singapore.
-
S. D. Nagrale1, Dr. Hemant Hajare2, Pankaj R. Modak3, Utilization Of Rice Husk Ash International Journal of Engineering Research and Applications (IJERA) ISSN: 2248- 9622, Vol. 2, Issue 4, July-August 2012, pp.001-005.
-
Kartini, K.1,*, Mahmud, H.B.2, Hamidah, M.S.3, Absorption And Permeability Performance Of Selangor Rice Husk Ash Blended Grade 30 Concrete Journal of Engineering Science and Technology,Vol. 5, No. 1 (2010) 1 16 © School of Engineering, Taylors University College.
-
Sumrerng Rukzon1, Prinya Chindaprasirt2, and Rattana Mahachai3, Effect of grinding on chemical and physical properties of rice husk ash International Journal of Minerals, Metallurgy and Materials Volume 16, Number 2, April 2009, Page 242.
-
Maurice E. Ephraim, Godwin A. Akeke and Joseph O. Ukpata, Compressive strength of concrete with rice husk ash as partial replacement of ordinary Portland cement Scholarly Journal of Engineering Research Vol. 1(2), pp. 32-36, May 2012.
-
A. Ramezanianpour1,*, M. Mahdi khani2, Gh. Ahmadibeni3, The Effect of Rice Husk Ash on Mechanical Properties and Durability of Sustainable Concretes International Journal of Civil Engineerng. Vol. 7, No. 2, June 2009.
-
B. Chatveera a,*, P. Lertwattanaruk b, Evaluation of sulfate resistance of cement mortars containing black rice husk ash Journal of Environmental Management 90 (2009) 14351441.
-
Md. Harunur Rashid, Md. Keramat Ali Molla, Tarif Uddin Ahmed, Durability of Mortar in Presence of Rice Husk Ash World Academy of Science, Engineering and Technology 43 2010.
-
Dr. Hemant Sood1, Incorporating European Standards for Testing Self Compacting Concrete in Indian Conditions International Journal of Recent Trends in Engineering, Vol. 1, No. 6, (May 2009).
-
Akindehinde Ayotunde Akindahunsi1) and Oluwotosin Alade, Exploiting the Potentials of Rice Husk Ash as Supplement in Cement for Construction in Nigeria International Journal of Concrete Structures and Materials, Vol.4, No.1, pp. 3~8, (June 2010).
-
Mixture proportioning procedure for Self-compacting concrete, The Indian concrete journal, Aug 2004.
-
OKAMURA, H., Ozawa, Kand Ouchi, M. self-compacting concrete, structural concrete, March 2001, No.1, pp.5.17.
-
OKAMURA,H., Ozawa, K. Mix design for self-compacting concrete, concrete library of JSCE, June 1995, No.25, pp.107- 120.
-
M.S. Shetty, Concrete Technology (Theory and practice), S.Chand and Company Ltd. New Delhi.
-
IS 10262-2009, Indian standards, Recommended Guidelines for Concrete mix Design.
-
IS 12269-1987, Specifications for 53 grade Ordinary Portland Cement.
-
SP 23-1982, Hand Book on concrete mixes (Based on Indian Standards).
-
IS 383-1970,Specifications for Coarse and Fine aggregates From Natural sources from concrete.
-
IS 516-1959, Indian Standards, Methods of tests for strength of concrete.
-
-