
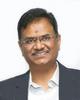
- Open Access
- Authors : Prahallad B S, Jaya R Shinganmakki, Swathi J, Karthik K N, Mohan M
- Paper ID : IJERTV12IS080033
- Volume & Issue : Volume 12, Issue 08 (August 2023)
- Published (First Online): 26-08-2023
- ISSN (Online) : 2278-0181
- Publisher Name : IJERT
- License:
This work is licensed under a Creative Commons Attribution 4.0 International License
Effect of Variation of the Gradation in the Bituminous Mixes
Prahallad B S, Jaya R Shinganmakki, Swathi J, Karthik K N, Mohan M Department of Highway Technology,
RASTA Center for Road Technology, Bengaluru, India 560058.
Abstract – This study analyzes the effect of gradation differences within bituminous mixes on mechanical and performance aspects. The study investigates how variations in aggregate particle sizes affect the mix's stability, durability, and resistance to distress mechanisms using extensive laboratory testing and analysis. The results show that appropriate gradation improves load-bearing capacity and resistance to rutting and cracking. The study underlines the importance of accurate gradation control in creating bituminous mixes that provide improved long-term performance and structural integrity.
Keywords – gradation; bituminous mixes; durability; load- bearing capacity.
-
INTRODUCTION
Bituminous mixtures, which include aggregates, bitumen, and fillers, are critical components of road building. Aggregate gradation, which determines particle size distribution, significantly impacts mechanical properties and overall mix performance. Grading promotes proper interlocking, compaction, and durability, which is critical for pavement longevity and structural integrity. Understanding the impact of gradation variations on bituminous mixtures is critical in civil engineering. The distribution of aggregate size influences void content, density, and permeability, which in turn influences load resistance, deformation, and durability. Engineers improve mix designs for targeted performance and long-term road infrastructure by methodically examining various gradation patterns. This research delves into the intricate correlation between alterations in gradation and the technical characteristics of bituminous mixtures. Extensive testing will indicate how gradation variations affect stability, rutting, cracking resistance, and pavement lifespan. The study increases mixed design understanding, promoting efficient and robust road construction procedures.
A. Role of Gradation in the Bituminous Mix
Gradation in bituminous mixtures significantly impacts mechanical qualities and overall road performance. A balanced particle size distribution improves stability by facilitating interlocking and resisting deformation. Effective compaction is enabled by well-graded aggregates, which increase pavement density and load-bearing capacity. Gradation affects durability by regulating void content and
moisture susceptibility, as well as water drainage and crack resistance. During construction, optimum gradation promotes bitumen-aggregate adhesion and workability. Furthermore, improved gradation can eliminate voids, improving pavement durability and cost-effectiveness. Gradation, in the end, plays a role in producing a well- engineered mix that enhances mechanical characteristics, durability, and pavement performance, resulting in safer and longer-lasting roads.
-
LITERATURE REVIEW
This section examines prior studies on bituminous mix filler materials and gradation effects, highlighting the importance of these factors in mix design and durability. It analyzes the effects of adding fillers and different gradations on bituminous pavement performance and sustainability and highlights significant studies in this area.
-
Arjit Kumar Banerji [1]
The Marshall technique was used in the study to evaluate different HMA aggregate gradations for Indian flexible pavements. While mid-point gradations displayed greater stability, finer gradations required more binder. Introducing the Gradation Ratio (GR), which is important for durable and reliable road construction in India. It connects aggregate gradingwith mix design.
-
Afaf A. H. M. [2]
The study looks into how variations in aggregate gradation affect the properties of asphalt concrete. Notably, modifications in the ratio of coarse to fine and fine to coarse have a big impact on the mix, with a coarse grading (max size 25 mm) producing the best stability, stiffness, and void characteristics. According to test results, coarse gradation can successfully produce bituminous concrete when combined with WCA, producing results that are satisfactory.
-
Rajendra Maharjan, Gautam Bir Singh Tamrakar [3]
Mineral aggregate makes up a sizeable percentage of the asphalt concrete mix, protecting from outside influences. The effect of grade on permanent deformation was investigated, and it was discovered that as grades got finer, the optimal bitumen concentration increased. For
strength, it is advisable to stay within the middle-upper gradation range. Upper grading yielded maximum stability (1550 kg) and density (2407 kg/m3) with 5.37% OBC, highlighting the importance of correct optimization for long-lasting bituminous mixtures.
-
Siyu Chen, Sanjeev Adhikari and Zhanping You. [4]
The study analyzes the permeability, porosity, and voids of two fine-graded HMA mixtures with various aggregate sizes. Permeability was raised by increased air spaces and porosity, whereas moisture cycles affected results. The 12.5- mm gradation performed better in terms of rusting. For creating asphalt mixes that can withstand pore pressure, useful insights are provided.
-
-
MATERIALS
Bituminous mixtures, necessary for building roads, include fillers for cohesion, aggregates for strength, and bitumen as a binder. Elasticity and durability are improved by warm mix additives, fibers, anti-stripping agents, and polymer modifiers. Asphalt pavements are stable, long- lasting, and function well when the aggregate is graded properly and the mix is well designed. The aggregates used in this study ranged from coarser fractions through mid- gradation to finer fractions.
-
LABORATORY STUDIES AND DATA ANALYSIS The Marshall stability test and performance tests were
conducted on the various bituminous mixes, and the resulting results are listed below. The different gradations are designated as MIX 1, MIX 2, and MIX 3.
TABLE I. GRADATION VARIATION OF THE MIXES
Sieve Size (mm) |
Lower Limit |
Upper Limit |
% passing Fine Gradation MIX 1 |
% passing Mid Gradation MIX 2 |
% passing Coarser Gradation MIX 3 |
19 |
100 |
100 |
100 |
100 |
100 |
13.2 |
90 |
100 |
91.64 |
95.45 |
100 |
9.5 |
70 |
88 |
72.17 |
78.79 |
86.95 |
4.75 |
53 |
71 |
56.09 |
64.66 |
70.43 |
2.36 |
42 |
58 |
44.42 |
51.17 |
57.83 |
1.18 |
34 |
48 |
37.33 |
40.73 |
46.34 |
0.6 |
26 |
38 |
29.07 |
30.44 |
37.38 |
0.3 |
18 |
28 |
20.95 |
23.93 |
26.19 |
0.15 |
12 |
20 |
12.43 |
16.21 |
18.53 |
0.075 |
4 |
10 |
3.77 |
5.73 |
7.49 |
-
MIX: 1 (BC GRADE II- Course) Sample A = 13.2 mm down. Sample B = 4.75 mm down. Sample C = FILLER (CEMENT) Type of binder= VG-30.
A: B: C:44%:54%:2%
-
MIX: 2 (BC GRADE II- Medium) Sample A = 13.2 mm down Sample B = 6.3 mm down Sample C = 4.75 mm down Sample D = FILLER (CEMENT) Type of Binder = VG-30
A: B:C:D: E:8%:13%:19%:57%:2%
-
MIX: 3 (BC GRADE II- Fine) Sample A = 19 mm down Sample B = 12 mm down Sample C = 6.3 mm down Sample D = 2.36 mm down Sample E = FILLER (CEMENT) Type of Binder = VG-30
A: B:C:D: 35%:18%:45%:2%
Fig. 1. Gradation of Various Mixes
TABLE II. SUMMARY OF THE MARSHALL TEST RESULTS
Binder Type
Filler
Gradation
OBC %
Air Voids (Va)
%
Voids Filled with Bitumen (VFB)
%
Bulk Density (Gb) g/cc
Flow value in mm
Stability (Kg)
SurfaceArea in M2/Kg
VG-30
Cement
MIX-1
5.5
5.20
51.53
2.36
3.3
1200.00
7.18
MIX-2
6.16
3.69
79.89
2.36
3.77
1213.39
8.69
MIX-3
6.73
2.83
85.00
2.41
3.88
1245.57
10.11
Fig. 2. Surface Area due to variation in Gradation
Bitumen content vs Stability
1400.00
1300.00
1200.00
1100.00
MIX 1
MIX 2
MIX 3
1000.00
4.5
5.5
6.5
7.5
BITUMEN %
Fig. 3. Bitumen content vs. Stability at varying gradation mix
Bitumen Content vs Air voids
5.50
5.00
4.50
4.00
3.50
3.00
2.50
2.00
MIX 1
MIX 2
MIX 3
4.5 5.5 6.5 7.5
BITUMEN %
Fig. 4. Bitumen content vs. Air voids at varying gradation mix
Bitumen content vs Flow
5.00
4.00
MIX 1
3.00
MIX 2
MIX 3
2.00
4.5
5.5
6.5
7.5
BITUMEN %
Fig. 5. Bitumen content vs. Flow at varying gradation mix
Bitumen content vs VFB%
90.00
80.00
70.00
60.00
MIX 1
MIX 2
MIX 3
50.00
4.5
5.5
6.5
7.5
BITUMEN %
Fig. 6. Bitumen content vs. VFB% at varying gradation mix
Bitumen content vs VMA%
20.00
15.00
10.00
MIX 1
MIX 2
MIX 3
5.00
4.5
5.5
6.5
7.5
BITUMEN %
Fig. 7. Bitumen content vs. VMA% at varying gradation mix
Bitumen content vs Density
2.56
2.54
2.52
2.50
2.48
2.46
2.44
2.42
2.40
MIX 1
MIX 2
MIX 3
4.5 5.5 6.5 7.5
BITUMEN %
Fig. 8. Bitumen content vs. Density at varying gradation mix
TABLE III. SUMMARY OF THE PERFORMANCE TEST
Type of Binder
Filler
Gradation
Rut Depth
Static Indirect Tensile Strength (Unconditioned)
Static Indirect Tensile Strength (Conditioned)
Tensile Strength Ratio
No. of Cycles taken in Fatigue Test
20%
Stress
30%
Stress
VG-30
Cement
MIX 1
5.72
835.8
762.57
91.23
3687
1876
MIX 2
4.46
882.9
797.28
93.72
2569
1034
MIX 3
7.3
891.6
835.66
90.3
3798
1896
Fig. 9. Tensile strength vs. Varied mixes
MIX 3
1896
3798
MIX 2
1034
2569
MIX 1
1876
3687
0
500 1000 1500 2000 2500 3000 3500 4000
Number of Cycle
No. of cycles 30% stress No. of cycles 20% stress
Fig. 10. No. of Cycle vs Mixes at 20% stress and 30% Stress
-
Discussion And Conclusion
It has been proven that the variation in gradation within bituminous mixes has a significant impact on the performance characteristics of the mixtures. Strength, rutting resistance, drainage, and compactness are all greatly impacted by the precise distribution of coarse, mid, and fine fractions.
Different gradation patterns in mixes, including Mix 1's coarser fraction and Mix 3's finer fraction, displayed specific benefits and drawbacks. Due to its finer fraction, Mix 3 performed better overall because it allowed for better interlocking, a well-graded composition, and efficient void filling with fine aggregates. This led to greater strength, resistance to rutting, and general stability.
On the other hand, Mix 1 had loose packing concerns, which would have compromised its overall durability and stability, despite the enhanced drainage brought on by its coarser fraction.
A finer fraction (Mix-3) beats all other examined gradations in terms of stability, hardness, and distress resistance because fine particles fill in gaps and increase interlocking.
Mix-3 reduces water-related deterioration due to the advantageous effects of fine particles, which boost binding to the bituminous binder and improve moisture resistance. It is suited for areas with significant rainfall and moderate traffic.
REFERENCES
[1] Arijit Kumar Banerji 1, Antu Das 2, Arobinda Mondal 3, Rahul Biswas 4, Md. Obaidullah 5 A comparative evaluation on the properties of HMA with variations in aggregate gradation of laboratory and field producedmixes.
[2] Afaf A. H. M Effect of aggregate gradation and type on hot asphalt concrete mix properties. [3] Rajendra Maharjan 1, Gautam Bir Singh Tamrakar 2 Effect of Aggregate Gradation Variation on the Marshall Mix Properties of Asphalt Concrete. [4] Abhijith B.S 1 and Suresha S.N 2 Effect of Aggregate Gradation and Bitumen Contenton Workability of HMA Mixtures. [5] Siyu Chen, S.M. ASCE 1; Sanjeev Adhikari 2 and Zhanping You, M. ASCE 3 Relationship of Coefficient of Permeability, Porosity, and Air Voids in Fine-Graded HMA. [6] ASTM D 6927-15. (2015). Standard Test Method for Marshall Stability and Flow of Bituminous Mixtures. Annual Book of American Society for Testing materials ASTMStandards, 17. [7] ASTM D6931-17. (2017). Standard Test Method for Indirect Tensile (IDT) Strength ofBituminous Mixtures 1. 37. [8] ASTM: D 2041-03a. (2003). Standard Test Method for Theoretical Maximum SpecificGravity and Density of Bituminous Paving Mixtures. ASTM International, 17.