
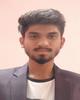
- Open Access
- Authors : Ganesh D. Thombre , Deepak R. Sharma , Raj P. Anchalkar , Amit C. Gunge
- Paper ID : IJERTV10IS060078
- Volume & Issue : Volume 10, Issue 06 (June 2021)
- Published (First Online): 12-06-2021
- ISSN (Online) : 2278-0181
- Publisher Name : IJERT
- License:
This work is licensed under a Creative Commons Attribution 4.0 International License
Electric Vehicle Model To Improve Efficient Utilization of Energy
1stGanesh D. Thombre
Student, Dept. of Electrical-Electronics And Power Engineering, JNEC College, Aurangabad, Maharashtra, INDIA
3rdRaj P. Anchalkar
Student, Dept. of Mechanical Engineering, PES College, Aurangabad, Maharashtra, INDIA
2ndDeepak R. Sharma
Student, Dept. of Mechanical Engineering, PES College, Aurangabad, Maharashtra, INDIA
4thAmit C. Gunge
Professor, Dept. of Mechanical Engineering, JNEC College, Aurangabad, Maharashtra, INDIA
Abstract – The power industry word-wide has seen aggressive power demand growth in the pursuit of economic development of the countries. power management plays a vital role in reducing consumption and efficient utilization of the resource. Due to restriction of vehicle emission and high demand for fossil fuels nowadays, car manufacturers around the world are looking into alternative ways in introducing new car model that would vastly capture the market. Electric vehicle is widely regarded as a promising solution to reduce air pollution in cities and key to a low carbon mobility future. However, their environmental benefits depend on the temporal and spatial context of actual usage (journey energy efficiency) and the rolling out of electric vehicles is complicated by issues such as limited range. Since car battery plays the crucial role on the overall performance of electric vehicle, many researchers have been working on improving the component. This paper is focused on reducing the power consumption in electric vehicle which involves modification in electric vehicle design. By modifying the electric vehicle design, as proposed in this paper, power consumption will get reduced and as a result the battery range will be prolonged.
Key Words – Electric vehicle, energy consumption, battery, wheels, motor.
-
INTRODUCTION
In recent past, electric vehicles [EVs] received a great attention from scholars and manufacturing companies due to several reasons. One of the most eminent reason is the need for reducing the environmental pollution caused by vehicles with internal combustion engine which use fossil fuels [1]. Carbon monoxide and carbon dioxide are harmful gases produced by the internal combustion engine of the conventional vehicles due to burning fuels. Another reason is that electric vehicles are more economic than conventional vehicles regarding the cost of the propulsion [3]. Electric motors considered as the heart of propulsion system of EVs. They receive the electrical energy from the batteries and convert it into traction torque to move the vehicle. According to the foregoing discussion, a lot of researches have been conducted on electric vehicle.
With traditional vehicles, especially cars, the internal combustion engines [ICE] were mostly located in the front of vehicles. thus, the centre of gravity of vehicles was also prejudice forward, so it affected stability of vehicles when moving at high speed and the operation of the brake system [5-6]. The ICE is difficult to place in the middle or in the
back of cars, due to the specific structure of cars. Therefore, the anti-lock brake system [ABS] had been used to increase the movement safety of vehicles when traveling with the high velocity [7]. With the EV using electric batteries, the advantage of electric batteries compared to the ICE is the small weight and size, thus, the electric battery can be installed in the front, middle, or rear locations of the EV to improve the vehicles space. However, the installation location of the electric battery can affect the dynamic load distribution of the wheels and vibration of the EV body which directly affects the EVs stability and movement safety. Therefore, it should be studied.
In EVs battery has occupy around 20-25 percent of the gross vehicle weight. Because of this heavy weight of battery, electric vehicle consumes a lot of energy just to carry the energy source which reduce the range of battery. Similar situation demands for an advanced electric vehicle model to reduce the energy consumption. This paper aims for the efficient energy utilisation in EVs by using unique car model having two chassis which uniformly distribute the total weight of car throughout both chassis and reduce the power consumption to improve battery range.
-
ELECTRIC VEHICLE SETUP
An electric vehicle is quite flexible as compared to ICE [4]. Reason behind EVs flexibility is the absence of intricate mechanical arrangements that are required to run a conventional vehicle. In EV, there is only one moving part, the motor. This motor can be controlled by different control arrangements and techniques. The motor needs a power supply to run which can be from an assembly of sources [battery source]. These two components can be placed at different position on the vehicle and as long as they are connected through electrical wires, the vehicle will work. Then again, an EV can run solely on electricity, but an ICE and electric motor can also work in combination to turn the wheels. Because of such flexibility, different configurations emerged which are adopted according to the type of vehicle. An EV can be considered as a system incorporating three different subsystems [4]: energy source, propulsion and auxiliary. The energy source subsystem includes the source, its energy management system as well
as refuelling system. The propulsion subsystem has the electric motor, power converter, controller, transmission, and the driving wheels as its components. The auxiliary subsystem is comprised of auxiliary power supply, temperature control system and the power steering unit. These subsystems are shown in Figure [1].
Figure 1 – EV subsystems
The arrows indicate the flow of the entities in question. A backward flow of power can be created by regenerative actions like regenerative braking. The energy source must be receptive to store the energy sent back by regenerative actions. Most of the EV batteries along with capacitors are compatible with such energy regeneration techniques [4]. (Chan, 2002)
EVs can have different configurations as shown in Figure [2a] shows a front-engine front wheel drive vehicle with just the ICE replaced by an electric motor. It has a gearbox and clutch that allows high torque at low speeds and low torque at high speeds. There is a differential as well that allows the wheels to rotate at different speeds. Figure [2b] shows a configuration with the clutch omitted. It has a fixed gear in place of the gearbox which removes the chance of getting the desired torque-speed characteristics. The configuration of Figure [2c] has the motor, gear and differential as a single unit that drives both the wheels. Some EVs uses an electric motor mounted at the front to drive the front axle. In Figure [2d] and [2e], configurations to obtain differential action by using two motors for the two wheels are shown. To produce an in-wheel drive, Mechanical interaction can be further reduced by placing the motors inside the wheels. A planetary gear system is employed here because advantages like high speed reduction ratio and inline arrangement of input and output shafts. Mechanical gear system is totally removed in the last configuration [2f] by mounting a low-speed motor with an outer rotor configuration on the wheel rim. Controlling the motor speed consequently controls the wheel speed and the vehicle speed. EVs can also built with rear wheel drive configuration as well.
Where, C: Clutch; D: Differential; FG: Fixed Gearing; GB: Gear Box; M: Electric Motor
Figure 2 – Different EVs configuration
-
ront wheel drive vehicle with the ICE replaced by an electric motor, [b] Vehicle configuration with the clutch omitted, [c] Configuration with motor, gear and differential combined as a single unit to drive the front wheels, [d] Configuration with individual motors with fixed fearing for the front wheels to obtain differential action, [e] Modified configuration of Figure [2d] with the fixed gearing arrangement placed within the wheels, [f] Configuration with the mechanical gear system removed by mounting a low-speed motor on the wheel rim [4]. (Chan, 2002)
From above discussion, we understand the general EVs configuration and design. We also understand that by making possible arrangements for installation of EV components, gives satisfactory results in power consumption.
-
-
ENERGY SOURCE
EVs can get the energy required to run from different sources. The criteria such sources have to satisfy are mentioned in [4], high energy density and high-power density being two of the most important ones. There are other characteristics that are sought after to make a perfect energy source, long service, fast charging, cycle life, less cost and maintenance being a few of them. High specific energy is required from a source to provide a long driving range whereas high specific power helps to increase the acceleration. Because of the diverse characteristics that are required for the perfect source, quite a few sources or energy storage systems come into discussion; they are also used in different conjunction to provide desired power and energy requirements [4]. Batteries have been the crucial
energy source for EVs for a long time, though of course, was time has gone by, different battery technologies have been invented and adopted and this process is still going on to attain the desired performance goals. If the electric automobile is arrayed with a greater number of batteries and its weight increases to 3,500 kg, the travel range increases to 170 km. If equipping electric automobiles with NiMH batteries, a medium class electric automobile with a weight of 1,500 kg can achieve a travel range of 100 km per charge.
First hybrid technology automobiles were introduced at the beginning of the 21st century, and later electric automobiles appeared as well. However, the key disadvantage of electric automobiles, just like it was 110 years ago, was the relatively heavy battery packs that did not allow considerably increasing the travel range of the electric automobiles. A lot of funds were invested in the fields of science related to the development of battery technologies for electric automobiles; however, at present, Number of very light and cheap batteries that, in terms of the weight and energy capacity, are equivalent to the fuel tank of internal combustion automobiles have been designed. For this reason, the buyers of electric automobiles need to choose the automobiles meeting the necessary operational conditions, one of which is the travel range per charge. An essential aspect in purchasing an electric automobile is the price of it [8] (M., 2011). Research on the effects of the weight of batteries of an electric automobile and of the total weight of the electric automobile on its performance parameters is very urgent. In designing a greater capacity fuel tank for an internal combustion engine automobile, auto manufacturers only risk decreasing the free space of the automobile. When operating such an automobile, the user has a free choice to operate it with a full or a half-empty tank, especially in a situation where daily kilometrage is small. In the case of an electric automobile, the battery pack installed on the electric automobile has to be transported all the time, regardless of the average daily kilometrage. One of the parameters to be easily calculated based on the technical characteristics of an electric automobile is energy consumption per km travelled. For modern electric automobiles, this parameter is in a very broad range of 67.8- 216.7 Wh·km-1, which indicates that, in terms of economical fuel consumption, electric automobiles of various models may differ more than threefold [9]. Modern electric automobiles are equipped with lithium-ion batteries. The most popular battery capacity is 20-22 kWh. The weight of batteries is increased by extra elements, e.g., the battery management system, the cooling and safety system as well as the assembly box for battery modules. The travel range of modern electric automobiles is in the range of 60-450 km, according to the NEDC test cycle [9]. The volume occupied by batteries is also large [11]. (C.E., 2009).
Using lithium-ion batteries in electric automobiles the weight of the battery system necessary for traveling 100 km can exceed 150 kg. For limousine-class electric automobiles, the travel range of which is more than 300 km, the weight of batteries could exceed 500 kg [11].
(C.E., 2009). This is one of the reasons why auto manufacturers are not eager to considerably increase the capacity of battery packs to above 30 kWh. A medium- class electric automobile equipped with 1.1 kWh batteries can cover, on average, a distance of 8 km [12]. A number of researchers suggest using the plug-in technology, as the cost of the battery system for such vehicles could be considerably decreased, as well as there is no need to worry about energy exhaustion after the battery has been fully discharged [13]. Optimum parameters may be chosen by performing a simulation for hybrid automobiles equipped with battery packs and electric motors of various capacities [13]. Compact-class electric automobiles are usually intended for urban driving, and they are not equipped with high-capacity battery packs. If compared with internal combustion automobiles of the same class, electric automobiles are usually heavier by 10-15 % [9, 14].
Figure 3 Effect of weight of an automobile on its performance parameter
-
PROPOSED METHODOLOGY
By Studying about electric vehicle configuration and battery specification, we identify the role of electric vehicle design and how it affects the performance and power consumption in EV. Therefore, we are proposing a new model of EV which will reduce the power consumption and improve the efficient utilization of energy. We know that it takes less force to drag/pull any load than carrying it on our head. Because, when a person is carrying some load on his/her head than the total weight of that load is directly projected on that persons body. While pulling, we only have to override the friction of the object against the ground. Because the coefficient of friction between a box and the ground is usually less than one(<1). When we drag/push, we can use our body weight to help by leaning into it. we push or leaning away from it when we drag. Also, we don't have to combat gravity and only have to worry about moving the load laterally. Straker et al. (1996) found the physical limits for pushing and pulling to be more than double the limits for lifting, lowering and carrying. As well as being subjectively rated as being less strenuous than lifting. For example, A 70 kg person can easily pull/drag 50kg of bag up too long distance but, hardly carry it on the head. To overcome this problem, we introduce wheel bags. As we have discussed before, in case of pulling we only have to override the friction of the object against the ground so we dont have to combat
gravity, therefore using wheel bags improved the working range of a person.
The Same concept can be applicable for electric vehicle. In an electric vehicle there is only one moving part, the motor. It can be controlled by different control arrangements and techniques. The motor needs a power supply to run, which can be from an array of sources. These two components can be placed in different position on the vehicle and as long as they are connected through electrical wires, the vehicle will work. As we discussed the electric vehicle configuration and battery setup. It shows us that, in the ongoing electric vehicle, the total weight of lectric motor, power inverter, controls, transmission, battery is projected on the wheels. The total weight projected on wheels is around 2100kg 3200kg. Because of this massive weigh, very high torque and power is required to rotate the wheels and to achieve high velocity.
We are proposing a unique model of electric vehicle in which 2 chassis will install in a single vehicle. These chassis will have four wheels attached to both of them. These two chassis will manufacture in a manner such that, they will have such mechanical arrangements which will allow both chassis to install in-between one another. This leads us to manufacture a unique EV model with 8 wheels, as shown in figure [4],[5]. So one chassis will be the outer chassis and another chassis will be inner chassis of the vehicle. Outer chassis will have electric motor, power invertor, controllers and transmission etc. mounted on it and inner chassis will only have battery unit mounted on it. Basically, both chassis are separate from one another and exerts their weight on ground separately. But we have to couple these chassis with mechanical structure to provide stability and co-ordination in between the wheels. We also have to consider the moments of wheels which will happen when a driver turn the vehicle. And we have to provide such controller and synchronism in between all the wheels which will endow co-ordination in wheels for a perfect and smooth ride.
Figure 4 Isometric view of Proposed EV model
Coupling of these chassis should be in a manner that, outer chassis should only bear the weight of equipment mounted on it which involves electric motor, power inverter, controllers, transmission etc. And inner chassis
should only bear the weight of battery unit which will mounted on it. An electric wire keeps inverter and battery in contact through which inverter get power supply. As we mount inverter and motor to outer chassis, therefore torque and power is actually provided to the wheels attached to outer chassis. Therefore, wheels attached to outer chassis are the one who actually drives the vehicle. And because of the proposed design, The weight of battery unit will directly exert on the ground and not on the wheels who is driving the vehicle. So its like outer chassis is only dragging the battery unit. This reduce the load acting on motor to drive the vehicle and as a result Power consumption will reduces and range of battery will increase significantly. Side view, front view, top view and back view of the proposed vehicle model is shown in figure [5]. This unique EV model will not only save energy but also endow vehicle with a different, attractive and muscular look.
Figure 5 Views of proposed EV model
From above approach we understand that the proposed model of EV requires a different manufacturing method and this EV setup will be complicated and also upsurge the manufacturing cost of the vehicle as it have 2 chassis and 8 wheels installed in it. But improving the efficient power consumption and saving energy was always being our primary aim in the field of engineering and technology.
-
CONCLUSION
Electric vehicles have great potential of becoming the future of transport while saving this planet from imminent calamities caused by global warming. They are a viable alternative to conventional vehicles that depend directly on the diminishing fossil fuel reserves. This paper first describes general structure and discusses the energy storage in electric vehicle and how the weight of battery influences the electric automobile performance. We also discusses, how energy can be saved if we use pulling action instead of carrying load.
Therefore, by understanding these concepts we proposed a unique electric vehicle model with two chassis. This unique electric vehicle model will reduce the weight acting on wheels who drives the vehicle. As weight acting on wheels of the vehicle get reduced, therefore power requires to rotate wheels will decreases and as a result power consumption will get dwindles significantly. The main purpose of this study is to understand the electric
vehicle set up and propose a modern electric vehicle model to improve efficient utilization of power and improve battery range in electric vehicle.
-
REFERANCE
-
J.Y. Yong, V.K. Ramachandaramurthy, K.M. Tan, N. Mithulanan than, A review on the state-of-the-art technologies of electric vehicle, its impacts and prospects Renew. Sustain. Energy Rev., 49 (2015), pp. 365-385
-
F. UnNoor, S. Padmanaban, L. MihetPopa, M.N. Mollah, E. Hoss ain, A Comprehensive study of key electric vehicle components technologies, challenges, impacts, and future direction of development Energies, (2017), pp. 2-82
-
C.C. Wang, S.Y. Cheng, T. Hsiao, W.Y. Chou, Application of optimum tire force distribution to vehicle motion control Int. J.
Hydrogen Energy, 34 (15) (2009), pp. 6005-6020
-
Chan, C.C. The state of the art of electric and hybrid vehicles. Proc. IEEE 2002, 90, 247275.
-
Arya K., Soheil R., et al. An intelligent cooling system and control model for improved engine thermal management. Applied Thermal Engineering, Vol. 128, 2018, p. 253-263.
-
Chiong M., Rajoo S., et al. Engine turbocharger performance prediction: One-dimensional modeling of a twin entry turbine. Energy Conversion and Management, Vol. 57, 2012, p. 68-78.
-
Mohamed H., Musa M., Pakharuddin M., et al. Performance comparison between sliding mode control and active force control for a nonlinear anti-lock brake system (ABS). WSEAS Transactions on Systems and Control,
-
Abdul-Hak M., Al-Holou N., Mohammad U. Predictive Intelligent battery Management System to Enhance the Performance of Electric Vehicle. In Electric Vehicles
Modelling and Simulations. Intech, 2011, pp.365-384
-
Berjoza D., Jurgena I. Effects of Change in the Weight of Electric Vehicles on their Performance Characteristics. Proceedings of International conference Agronomy Research 15, 2017.
-
Huh J., Lee W., Cho G.-H.,Lee B., Rim C.-T. 2011.Characterizationof novel inductive power transfer systems for on-line electric vehicles. Daejeon, Korea, 978-1-4244-8085- 2/11.2011 IEEE pp.1975-1979.
-
Thomas C.E. Fuel cell and battery electric vehicles compared. International Journal of Hydrogen Energy. 34 (15), 2009, pp. 6005-6020.
-
van Vliet O., Brouwer A.S., Kuramochi T., van den Broek M., Faaij A. Energy use, cost and CO2 emissions of electric cars. Journal of Power Sources. International Journal of the Science Technology of Battery, Fuel Cell and other Electrochemical Systems. Elsevier, 169 (4) ISSN 0378-7753, 2011, pp. 2298- 2310.
-
Hauffe R., Samaras C., Michalek J. J. 2008. Plug-in hybrid vehicle simulation: how battery weight and charging patterns impact cost, fuel consumption, and CO2emissions. In Proceedings of the 2008 Design Engineering Technical Conferences & Computer and Informationin Engineering Conferences, New York City, NY, USA, IDETC2008-50027, pp.1-7.
-
Faria R., Moura P., Delgado J., A. T. de Almeida 2012. A sustainability assessment of electric vehicles as a personal mobility system. Energy Conversiona nd Management 61, pp.19- 30.