
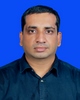
- Open Access
- Authors : D K Karthik , Dr. Srikanth Salyan
- Paper ID : IJERTV10IS070232
- Volume & Issue : Volume 10, Issue 07 (July 2021)
- Published (First Online): 27-07-2021
- ISSN (Online) : 2278-0181
- Publisher Name : IJERT
- License:
This work is licensed under a Creative Commons Attribution 4.0 International License
Enhancement in Thermal Hydraulic Performance by Employing Detached Ribs Inside A Gas Turbine Blade Internal Cooling Passage (AR = 1:5)
D K Karthik,
Research Scholar, Department of Mechanical Engineering,
National Institute of Technology, Tiruchirappalli, India
Dr. Srikanth Salyan,
Assistant Professor, Department of Aeronautical Engineering, Dayananda Sagar College of Engineering,
Bangalore, India
Abstract:- Degree of pressure loss and heat transfer due to rib turbulators inside a turbine blade cooling passage determines the overall performance of a gas turbine engine. Therefore, the focus of this experimental work is to determine the impact of detached ribs on pressure loss and heat transfer inside a passage which resembles an actual passage inside a turbine blade airfoil. The passage used for performing experiments has a rectangular cross-section with aspect ratio (AR) 1:5 and hydraulic diameter (Dh) 0.05 m. Detached V and W-ribs under study were mounted on opposite walls pointing upstream. Rib height (e) and angle-of-attack () for both ribs were 3 mm and 30° respectively. Thermal Hydraulic Performance (THP) for both detached ribs were assessed for four Reynolds numbers 30000, 45000, 60000 and 75000 at height-to-hydraulic diameter ratio (e/Dh) 0.06 and pitch-to-height ratio (P/e) 9. Experimental results indicated better heat transfer capabilities for detached V-ribs, with highest heat transfer enhancement of 3.4 at Reynolds number 30000. For all the Reynolds numbers investigated, Nusselt number ratios of both the ribs were comparable with maximum variation of 8.3% at Reynolds number 75000. Pressure losses for detached W-ribs were 25% and 13.6% higher than detached V-ribs at Reynolds numbers 30000 and 75000 respectively. Thermal hydraulic performance of detached V-ribs at Reynolds number 30000 and 75000 were 7.4% and 14.4% higher than detached W-ribs. Best thermal hydraulic performances shown by detached V-ribs for the lowest and highest Reynolds number tested were 2.9 and 1.7.
Keywords:- Reynolds number, Detached Ribs, Heat Transfer coefficient, Nusselt number ratio, Friction factor ratio, Thermal Hydraulic Performance
-
INTRODUCTION
Combusted gases having temperatures above 1000° C impinge turbine blades which result in thermal stresses. To improve engine life and performance, these thermal stresses have to be managed rightfully by employing efficient cooling techniques. Depending on the level of blade surface temperatures different techniques are used for cooling different sections of the turbine blade. In the mid-section, rib turbulators having different shapes are used. Rib turbulators are fixed to the internal walls and as the coolant flows over it secondary flows are generated leading to improvement in heat transfer. Heat transfer improvement is proportional to pressure drop penalty and hence the target is to achieve increment in heat transfer for a low pressure drop penalty. Rib geometry influences the thermal hydraulic performance and hence researchers have focused their studies on understanding the effects of rib geometry on thermal hydraulic performance. Published work relevant to the current study have been highlighted in table 1 and discussed subsequently.
Table 1: Findings of few important studies
Configuration
AR
e/Dh
P/e
Re
Maximum Area Averaged Nusselt number ratio
Han and Zhang [1]
Continuous V-shaped ribs, Broken V-shaped ribs
1:1
0.0625
10
60°/
45°
15000 –
90000
3.6
Ekkad and Han [3]
Orthogonal, Continuous V-shaped ribs, Broken V-shaped ribs
1:1
0.125
10
60°
6000-60000
3.2
Tzeng and Mao [5]
Half V-shaped ribs
1:1
0.125
10
60°
20000-
40000
2-3
Wright et al. [7]
Angled ribs, Discrete W-ribs, Discrete V- ribs
4:1
0.078
10
45°
10000-
40000
3.8
Maurer et al. [10]
Continuous V-ribs
2:1
0.0625/
0.02
10
45°
95000-
500000
2.5
Sriharsha et al. [12]
Orthogonal ribs, V-broken ribs
1:1
0.15/0.2/0.25
10
60°
10000-
30000
4.3
Alkhamis et al. [13]
Continuous V-ribs
1:1
0.1 to 0.18
5 to 10
45°
30000 –
400000
3.9
Baraskar et al. [14]
Continuous V-ribs
8:1
0.03
10
60°
5000-14000
2.57
Smith et al. [17]
Angled ribs
1:1/
1:2/
1:6
0.1-0.058
10
45°
4000-
130000
2.5
Kumar and Amano [18]
Continuous V-ribs, Broken V-ribs
1:1
0.125
10
60°
21000/
56000/
85000
3-5
Prashant et al. [20]
Angled ribs and Continuous V-ribs
1:1
0.125
16
45°
19500-
69000
2.5 – 3
Abraham and Vedula [21]
Continuous V and W- ribs in converging channel
–
0.08
6/10/17.5
45°
5000 –
35000
3
Prashant et al. [22]
Continuous V-ribs
1:2
0.125
9.625
45°
25000 –
75000
3.5
DENG Honghu et al. [24]
Orthogonal ribs
1:1
0.1/0.2/ 0.3
–
90°
20000 –
40000
3-4
Han and Zhang [1] using square cross-section cooling channel assessed the performance of detached and continuous ribs (P/e=10). They presented that increment in heat transfer for 60° ribs is better than 45° ribs and broken ribs exhibited better performance. Taslim and Li [2] experimented different ribs for Reynolds numbers up to 30000 and concluded that continuous V-ribs (e/Dh=0.083) produced maximum pressure drop and heat transfer. The authors also concluded that 45° angled and detached ribs produced best thermal performance. Ekkad and Han [3] by way of experiments in two-pass square cooling passage using orthogonal, 60° continuous, and broken ribs confirmed that broken V-ribs and parallel ribs for P/e=10 and e/Dh =
0.125 produced greater enhnacements with intensity of flows observed to be stronger in the bend region. Gao and Sunden [4] compared thermal performances of 60° parallel and continuous V-ribs with apex pointing upstreamand downstream in a very narrow cooling passage (AR=1:8) and presented that for Reynolds numbers up to 6000, continuous V-ribs with apex pointing downstream provided best performance for P/e=10. Tzeng and Mao [5] using pressurized coolant evaluated the effects of staggered half V-ribs in multi-pass cooling passage for Reynolds numbers between 20000 and 40000 and showed that the heat transfer was better with pressurized coolant and the influence of ribs were noticeable in all the passes.
Hadhrami et al. [6] by using a rectangular duct of AR = 2 examined different types of V-shaped ribs (P/e=10) and established that enhancement in heat transfer was highest for 45° V-ribs pointing upstream. Wright et al. [7] investigated continuous and detached 45° V and W-ribs (P/e=10) in a wide entrance rectangular cooling channel (AR=4) for Reynolds numbers 10000 to 40000 and confirmed that detached ribs showed better performance and W-ribs generated highest frictional loss and heat transfer. Gao and Sunden [8] presented that the upstream facing V-ribs produced greater enhancements for Reynolds numbers up to 5800 in a rectangular passage (AR-1:8). Akhanda M.A.R et al [9] by employing square ribs conducted experiments in a square channel for Reynolds number range 46000 to 52000 and established that the heat transfer and pressure drop because of ribs were 15% and 6% higher than duct with smooth wall. Maurer et al. [10] by using Thermochromic Liquid Crystal Technique studied the performances of V-ribs for Reynolds numbers between 95000 500000 and P/e=10 in a rectangular channel (AR=2) and concluded that the ribs with lower height fixed on one wall exhibited highest performances.
Gupta et al. [11] established that 60° broken V-ribs (e/Dh = 0.0625) provided maximum enhancement in comparison to orthogonal and saw-tooth ribs in a channel (AR=1) for tested Reynolds numbers up to 30000. Sriharsha et al. [12] through experimental studies confirmed that 60° broken V-ribs (P/e=10) exhibited better heat transfer enhancement capabilities in a channel (AR=1) for Reynolds numbers tested up to 30000. Alkhamis et al. [13] compared the thermal performances of angled and continuous V-ribs and confirmed that 45° continuous V-ribs fixed in a square channel delivered better performance than angled ribs for Reynolds numbers between 30000 to 400000 and P/e ratio between 5-10. Baraskar et al. [14] evaluated the performance characteristics of 60° V-ribs in a wide rectangular cross-section channel (AR=8) for Reynolds numbers upto 14000. They concluded that with increase in velocity, the heat transfer increased and friction reduced. Lamont and Christopher
[15] by using Transient Liquid Crystal technique studied three rib profiles in a diverging channel upto Reynolds number 28000 and concluded that 45° V-ribs provided uniform and higher levels of heat transfer than 60° and 90° ribs.Xie et al. [16] studied 45° mid-truncated ribs (P/e=10) up to Reynolds number 50000 in square cross-section passage and presented that upstream pointing 45° mid-truncated V-ribs produced maximum heat transfer enhancement and mid-truncated angled ribs showed highest performance. Smith et al. [17] studied three different aspect ratio rectangular channels with angled ribs (P/e=10). They confirmed that channel with AR=1:6 produced highest enhancement for Reynolds number ranging from 4000 -130000 because of superior and stronger secondary flows. Kumar and Amano [18] presented the performance of continuous V- ribs and broken ribs in a channel (AR=1) for Reynolds numbers 21000, 56000 and 85000. They established that
broken ribs delivered better augmentation than continuous ribs and ribs facing downstream showed best performance. Ghodake et al. [19] examined the heat transfer augmentation for different rib profiles in a rectangular channel for geometric parameters (P/e=8.3 and e/Dh =0.035) and confirmed that 45° broken V-ribs exhibited superior augmentation.
Prashant et al. [20] compared thermal performances of four different rib turbulators in a square cross-section serpentine passage for Reynolds numbers 19500 to 69000 and showed that for P/e =16 and e/Dh =0.125 performance of angled ribs and continuous V-ribs were better than continuous W-ribs. Abraham and Vedula [21] compared the performances of continuous 45° V and W- ribs inside a converging duct for Reynolds numbers 5000 to 35000 and P/e values 6, 10 and 17.5. They reported that for e/Dh=
0.08 and P/e=10, the performances were optimum and within uncertainty limits. Prashant et al. [22, 23] presented the effects on heat transfer with 45° contiuous V-ribs in a serpentine rectangular cross-section channel (AR=1:2) for Reynolds numbers between 25000 to 75000 and reported that the augmentations increased along the flow view strengthening of secondary flows and was maximum at the 180° turn region due to superior turbulent mixing. Authors by way of numerical investigation showed that 45° angled and V-ribs exhibited best thermal performance inside a square channel for Reynolds numbers 20000 to 70000. DENG Honghu et al. [24] by using 90° ribs studied the influence of three different blockage ratios (e/Dh) on friction and heat transfer inside a rotating square channel. For Reynolds number range 20000 to 40000, the authors concluded that the thermal performance was optimum for blockage ratio 0.1.
Due to the shape of airfoil, the height difference between the leading and trailing walls of a turbine blade reduces towards the trailing edge and increases towards the leading edge from the mid-chord. Increase in height difference results to very narrow ribbed cooling passages adjoining the leading edge with aspect ratios upto 1:6 [17]. From literature studies it has been established that most of the ribbed cooling studies have been limited to cooling passages with aspect ratios ranging from 8:1 to 1:4 and therefore there is a need to study the heat transfer and friction in narrow rectangular cooling passages adjoining the leading edge with aspect ratio lessor than 1:4. Another important aspect is the heat load management in airfoil leading edge. The wall temperatures near the leading edge are relatively higher than other regions of airfoil and hence it is very important to achieve maximum heat transfer at reduced pressure drop and coolant consumption. Since the coolant is also utilized for impingement and film cooling after exiting the ribbed passages, an effort to increase heat transfer by reducing the rib pitch or by increasing the rib height will result in increased pressure drop thereby reducing the thermohydraulic performance inside the ribbed channels and also affecting the effectiveness of impingement cooling and film cooling which will decrease the reliability and durability of turbine blade.
With due consideration to above factors, the current experimental work has been conducted with an objective to identify suitable rib turbulators which can minimize the pressure drop and maximize the heat transfer inside a cooling passage (AR=1:5) close to the leading edge for the Reynolds number range 30000 75000. In order to achieve the aim, detached upstream pointing W and V-ribs were chosen and vital geometric parameters such as rib angle-of-attack, rib height and rib pitch were optimized. To the authors understanding, the rib geometry mentioned at table 2 has been used for the first time in a ribbed cooling passage with aspect ratio 1:5 and the selected geometric parameters have provided encouraging results. The maximum and minimum THP achieved was 2.9 and 1.67. The current work helps to understand the influence of detached upstream pointing W and V-ribs on heat transfer and pressure drop inside narrow ribbed cooling passages and also establishes that the ribs and geometric parameters selected are ideal for cooling passages located near the leading edge.
Table 2: Rib Geometry
Ribs
e
P/e
e/Dh
ecommended range in literature
P/e
e/Dh
Detached V
3
9
0.06
30°
5-15
0.05-0.1
30° – 60°
DetachedW
-
EXPERIMENTAL SETUP
1. Blower
6. Developing section
11. Laptop
2. Bypass valve
7. Ribbed section
12. Differential Pressure Transmitter
3. Inlet valve
8. Exit section
13. Thermal Infrared camera
4. Venturimeter
9. DC Source
14. Inlet Thermocouple
5. Water manometer
10. Data logger
15. Exit Thermocouple
Fig. 1 Schematic layout of experimental setup
Schematic layout of experimental setup is depicted at figure 1. Coolant used for experimental purpose is air which is supplied from a blower and regulated using valves. A calibrated venturimeter connected to a water manometer is fitted in coolant flow path to estimate the mass flow rate. Downstream end of venturimeter is connected to the test section using a pipe on which calibrated thermocouples are fitted for measuring inlet bulk temperature of coolant. Test section shown in figure 2 consists of three distinct sections namely developing section, ribbed wall section and exit section. Full length of the test section is 1.5 m and all the sections are made of Plexiglas. The ribbed wall section is 600 mm (12 Dh) long and located in between the 600 mm long developing section and 300 mm long exit section. Developing and exit sections are located at the upstream and downstream ends of ribbed wall section. These sections are provided to ensure that coolant velocity in the ribbed wall section is steady and uniform. Ribbed wall section has two smooth walls and two ribbed walls. Pressure drop in the ribbed section is captured by using a Differential Pressure Transmitter. Calibrated thermocouples are fitted to the exit section for measurement of outlet bulk temperature of coolant.
(a) Developing section (b) Ribbed wall (c) Exit section (d) Copper Blocks (e) Pressure tapping
(a) Developing section (b) Ribbed wall (c) Exit section (d) Copper Blocks (e) Pressure tapping
Fig. 2 Schematic of Test Section
3-D image of detached V-ribs and W-ribs studied in the present work are shown in figures 3. Ribs are made from balsa wood similar to Abraham and Vedula [21] and fixed to the inner surface of 0.2 mm stainless steel foil by applying anabond silicone sealant. Detached V-rib has two arms and detached W-rib has four arms prepared in two V shapes. Rib arms having a square cross-sectional area (3 mm x 3 mm) are symmetrically fixed on the foil with a gap of 3 mm between the rib arms along the centreline. To the outer surface of stainless steel foil, copper blocks are soldered on either end which in-turn are connected to 1200 W (150 A, 8 V) Direct Current (DC) power source. Calculated electrical resistance of each foil is lower than 0.05 . Lateral conduction through the foil is not considered view negligible foil thickness. Effective rib surface area of 400 mm x 30 mm between the copper blocks which is exposed to camera is painted with matt black paint to achieve high emissivity. A thermal infrared camera has been used to record the surface temperatures of ribbed walls. The camera readings have been verified against a calibrated thermocouple. A maximum temperature difference of 3.5° C was observed for the measurement range of 35°C – 80°C. Table 3 gives the details of measuring instruments used in the current experimental work.
Fig. 3 3D image of Detached V-ribs and Detached W-ribs
Table 3: Details of measuring instrument
Instrument
Make and Model
Range
Accuracy
Thermocouple
K-Type
0°C – 600°C
± 0.25%
Differential Pressure Transmitter (DPT)
KIMO, CP 100
0-100 Pa
± 1.5%
Thermal Imaging Camera
Fluke, Ti 9
-20°C – 250°C
± 5°C
Digital Multimeter
Mastech, M 3900
200 mV 1000 V
± 0.5%
Hot wire Anemometer
Testo 425
0-20 m/s
± 0.03 m/s
-
EXPERIMENTAL PROCEDURE AND DATA REDUCTION
After starting the constant speed centrifugal blower, the flow rate is adjusted to achieve the differential pressure corresponding to the Reynolds number to be tested. After the flow stabilises, power is supplied to the ribbed walls from the DC power source. After running the experiment for 30 minutes, the flow and thermal parameters were found steady and hence parameters such as inlet and exit bulk air temperatures, voltage drop between the copper blocks, and pressure drop in the ribbed wall section were logged. Subsequently, by using the thermal camera the images of the ribbed walls were recorded and the same was processed
using the Fluke software to get the local wall temperatures and in-turn heat transfer coefficients. Methodology adopted to derive Thermal Hydraulic Performances for both ribs has been discussed below:-
The energy balance for the bulk air is expressed as
= ( ) (1)
Net heat input () to the ribbed walls is determined after deducting heat losses () in view of radiation and natural convention from heat input ( = ). In the present work, the maximum heat loss is observed to be 9.5% of heat input at Reynolds number 30000. Bulk coolant temperature at a particular point in the ribbed wall is obtained by linear interpolation of inlet and outlet bulk coolant temperatures recorded by calibrated thermocouples and same verified using the enthalpy balance equation. The local bulk air temperature in the cross-stream direction is assumed to be constant. Heat transfer coefficient at a point in the ribbed wall is determined using below expression
=
()
(2)
Heat transfer coefficient is substituted in equation (3) to obtain Nusselt number distribution for the ribbed walls
=
(3)
Nusselt numbers obtained from equation (3) is normalised with Dittus-Boelter correlation for fully developed turbulent flow in smooth circular duct
= 0.0230.80.4 (4)
Frictional loss is determined by substituting the pressure drop measured across the ribbed walls in equation (5). The friction value is then normalised with friction for fully developed turbulent flow in smooth circular duct given by Blasius equation [7] and the same mentioned at equation (6)
=
22
(5)
= 0.079 1/4 (6)
Thermal hydraulic performance [23] at constant pumping power is determined for both ribs by using the expression below
THP () =
( )
1
(7)
(
(
)
)
3
Uncertainties have been calculated using Kline and McClintock [25] method. Maximum uncertainty estimated in heat transfer and friction calculations were 9% and 6.5% corresponding to Reynolds number 30000.
-
EXPERIMENTAL RESULTS AND DISCUSSION
Fig. 4 Averaged Heat transfer coefficient
Span Averaged Heat Transfer Coefficient. Averaged heat transfer coefficient calculated along two axiss located at 0.25 w and 0.5 w are depicted in figure 4. In case of detached V-ribs, the averaged heat transfer coefficient measured along the centerline (0.5 w) were higher than 0.25 w, wth an average variation of 7% and a maximum variation of 10% at Reynolds number 30000. For detached W-ribs, the averaged heat transfer coefficient measured along 0.25 w was marginally higher than
0.5 w, with a maximum variation of 1.5%. Analysis of heat transfer coefficient between two successive Reynolds number showed a maximum variation of 18.5% between Reynolds numbers 60000 and 75000 for detached V-ribs along the centerline and 11% between Reynolds numbers 45000 and 60000 for detached W-ribs along 0.25 w. Further, the averaged heat transfer coefficient at Reynolds number 75000 was 35% higher than Reynolds number 30000 for detached V-ribs and for detached W- ribs, heat transfer coefficient at Reynolds number 75000 was 21.5% higher than Reynolds number 30000. Average variation for the experimented range of Reynolds number was 10.5% and 6.5% for detached V and W-ribs respectively. From the above results, it has been concluded that the magnitude of secondary flows generated by detached W-ribs were stronger and relatively uniform along the cross-stream direction in comparison to the secondary flows generated by detached V-ribs. Further, the intensity of turbulent mixing or the vortices generated by detached W-ribs are better than detached V-ribs which resulted to lower variations in cross-stream direction.
Fig. 5 Nusselt number ratio along 0.5 w for Detached V-ribs
Fig. 6 Nusselt number ratio along 0.25 w for Detached V-ribs
Fig. 7 Nusselt number ratio along 0.5 w for Detached W-ribs
Fig. 8 Nusselt number ratio along 0.25 w for Detached W-ribs
Local Nusselt number ratio. Local Nusselt number ratio along 0.25 w and 0.5 w span lengths for detached V-ribs and detached W-ribs are shown in figures 5-8. It is inferred from the graphs that, the Nusselt number ratio for detached V and W ribs were highest at Reynolds number 30000 and decreased thereafter as the Reynolds number increased. The variations along
the stream showed a saw-tooth profile and is mainly because of rib induced coolant flow separation and re-attachment in the passage. As the coolant air flows inside the channel, velocity boundary layer builds up in the direction of flow. Due to the presence of ribs in the passage, the growth of velocity boundary layer is prevented thereby leading to a phenomenon of repeated detachment and attachment of velocity boundary layer within the cooling passage. This cyclic phenomenon of detachment at the rib and attachment between the ribs resulted to variation in wall temperatures which in-turn changed the magnitude of Nusselt number. Further analysis of Nusselt number obtained indicated that the intensity of heat transfer was high at the re-attachment point as the thickness of the velocity boundary layer is the lowest and mixing of coolant is better. After the point of re- attachment, the velocity boundary layer starts to grow leading to a gradual increase in wall temperatures. At very high coolant velocities the variations in heat transfer between the ribs reduced due to lower boundary layer thickness and better coolant mixing.
For detached V-ribs, extent of variation of Nusselt number ratio in the stream direction was low, with maximum variation calculated between two successive re-attachment points being 5% at Reynolds number 30000. In case of detached W-ribs, the level of variation in local Nusselt number ratio is found to be highest along the axis 0.25 w. The variation in the direction of flow is observed to be 29% at Reynolds number 30000 and 24% at Reynolds number 75000. At Reynolds number 45000, the variation is observed to be highest at 37%. The difference in local Nusselt number ratio between the span lengths were also analysed for both the rib shapes separately. For detached V and W-ribs the variations were 9.5% and 7% respectively at Reynolds number 30000 and 5% and 2.5% respectively at Reynolds number 75000.
Even though the rib height and angle of attack were same for both the ribs, detached W-ribs showed higher streamwise variation because the effects of ribs due to additional rib arms and reduced rib length were stronger in comparison to detached V-ribs. Further, variation in cross-stream direction is lessor for detached W-ribs because, the stronger counter-rotating vortices along the rib arms resulted in enhanced mixing and thin boundary layer in the cross-stream direction.
Fig. 9 Averaged Nusselt number ratio
Area Averaged Nusselt number ratio. Area averaged Nusselt number ratio achieved for different Reynolds numbers is shown in figure 9. For the investigated Reynolds numbers, maximum variation observed between the area averaged Nusselt number ratio of detached V-ribs and detached W-ribs is 8.3% at Reynolds number 75000. The values obtained for detached V-ribs and detached W-ribs at Reynolds number 30000 were 1.57 and 1.76 times higher than Reynolds number 75000 respectively. The Nusselt number ratio between two successive Reynolds number were analysed independently for both the ribs shapes and it was seen that maximum variation for detached V and W-ribs were 26% and 35% respectively, between Reynolds numbers 30000 and 45000, which shows that the rib effects were dominant for this range of Reynolds number. Between Reynolds numbers 60000 and 75000, the variation is 3% and 17% for detached V and W-ribs respectively, which shows that the influence on heat transfer due to detached V-ribs diminished beyond Reynolds number 60000.
Normalized Friction Factor. Normalized Friction factor for investigated Reynolds number are given in figure 10. For the same geometric parameters, the detached W-ribs generated greater friction due to increased contact area. The variation between the friction factor ratios of detached V-ribs and detached W-ribs is highest at Reynolds number 30000, which is 25%. For an increase in Reynolds number, the difference between the friction factor ratios of both ribs reduced with minimum difference of 13.6% observed at Reynolds number 75000. Decline in variation between the friction factor ratio of both ribs indicates that the rib effects were prominent at lower Reynolds number and the effects gradually reduced as the coolant velocity increased. The magnitude of friction factor ratios were also analysed for both the rib shapes separately. For detached V and W-ribs, the difference between friction factor ratios for two successive Reynolds numbers showed a decreasing trend. The maximum difference has been observed between Reynolds numbers 30000 and 45000, which were 12.5% and 10% for detached V and W- ribs respectively. The minimum differences were between Reynolds numbers 60000 and 75000, which were 10% and 8.5% corresponding to detached V and W-ribs. Marginal drop in percentage variation between the friction factor ratios can be because of reduction in rib effects at higher stream velocities. Average variation for the experimented Reynolds numbers is 11.5% and 7.5% corresponding to detached V-ribs and detached W-ribs.
Fig. 10: Friction factor ratio for studied Reynolds number
Thermal Hydraulic Performance. Thermal hydraulic performance achieved for different Reynolds number is depicted in figure 11. Detached V-ribs showed higher thermal hydraulic performance than detached W-ribs for the verified Reynolds numbers. The maximum difference in performance between two rib shapes is 14.4% at Reynolds number 75000. Further, the thermal hydraulic performance of detached V-ribs and detached W-ribs at Reynolds number 30000 were 1.74 and 1.85 times higher than Reynolds number 75000. From the above results it can be concluded that, at higher coolant velocity, the rib effects declined more for detached V-ribs which resulted in maximum difference in thermal hydraulic performance at Reynolds number 75000.
Fig. 11: Thermal Hydraulic Performance for investigated Reynolds number
Comparison with Published data. The results of the current work have been compared with published work. Table 4 and figure 12 shows the comparison of normalized Nusselt number and table 5 and figure 13 highlights the Thermal Hydraulic Performance. It can be seen that, detached V and W-ribs studied in the present work resulted in higher heat transfer enhancement and thermal performance in comparison to other rib configurations, which can be attributed to stronger rib induced secondary flows and low frictional losses induced by the ribs as a result of discontinuity, low height-to-hydraulic diameter ratio and angle of attack. As the results have been encouraging, it can be concluded that the present rib geometry can be utilized in narrow rectangular cooling channels adjoining the leading edge of airfoil for effective thermal management.
Table 4: Comparison of Nusselt number ratio
Configuration
AR
e/Dh
P/e
Re
Nu/Nuo
Present Study
Detached V-ribs
1:5
0.06
9
30°
30000/
60000
3.44/2.24
Detached W-ribs
3.5/2.3
Ekkad and Han [3]
Angled ribs
1:1
0.125
10
60°
30000/
60000
2.0/1.8
V-broken ribs
2.9/2.1
Wright et al. [7]
Discrete V-ribs
4:1
0.078
10
45°
30000
3.15
Discrete W- ribs
4:1
0.078
10
45°
30000
3.4
Smith et al. [17]
Angled ribs
1:6
0.058
10
45°
30000/
60000
1.9/2.0
Prashant et al. [20]
Angled ribs
1:1
0.125
16
45°
30000/
60000
2.4/2.2
Continuous V-ribs
3.0/2.5
Continuous W-ribs
2.5/2.0
Fig. 12: Averaged Nusselt number ratio
Table 5: Comparison of Thermal Hydraulic Performance
Configuration
AR
e/Dh
P/e
Re
THP
Present Study
Detached V-ribs
1:5
0.06
9
30°
30000/
45000/
60000/
75000
2.9/2.18/1.78/1.67
Detached W-ribs
2.7/2.03/1.75/1.46
Wright et al. [7]
Angled
4:1
0.078
10
45°
20000/
40000
1.55/1.35
Discrete V-ribs
1.65/1.4
Discrete W- ribs
1.7/1.45
Smith et al. [17]
Angled ribs
1:6
0.058
10
45°
25000/
50000/
75000
1.5/1.2/1
Prashant et al. [20]
Angled ribs
1.1
0.125
16
45°
19500/
35500/
52000/
69000
1.4/1.37/1.2/1.18
Continuous V-ribs
1.65/1.5/1.4/1.15
Continuous W-ribs
1.45/1.3/1.15/0.95
DENG Honghu et al. [24]
Orthogonal ribs
1:1
0.1
–
90°
20000
3
Fig. 13: Thermal Hydraulic Performance
-
CONCLUSION
-
For both the rib shapes, the level of pressure drop and heat transfer increased for an increase in Reynolds number. Further, the Nusselt number ratio decreased and friction factor ratio increased for an increase in Reynolds number.
-
Maximum difference between area averaged Nusselt number ratios of both rib profiles is 8.3% at Reynolds number 75000. The area averaged Nusselt number ratios obtained for detached V and W-ribs at Reynolds number 30000 were 1.57 and 1.76 times higher than Reynolds number 75000 respectively.
-
Detached W-ribs showed maximum variation in wall temperatures along the stream. Maximum and minimum variations in Nusselt number ratios of detached W-ribs were 37% and 24% corresponding to Reynolds numbers 45000 and 75000. For detached V-ribs the maximum variation in Nusselt number ratios along the stream was 5%.
-
Detached V-ribs showed greater variation in wall temperatures in cross-stream direction. Variation in Nusselt number ratios between the two span lengths were 9.5% and 7% for detached V-ribs and detached W-ribs at Reynolds number 30000 respectively.
-
Pressure drop was highest for detached W-ribs. Maximum and minimum differences between the friction factor ratios of both ribs were 25% and 13.6% corresponding to Reynolds numbers 30000 and 75000.
-
Friction factor ratio at Reynolds number 75000 was 1.37 times higher than Reynolds number 30000 for detached V-ribs. For detached W-ribs the friction factor ratio at Reynolds number 75000 was 1.25 times higher than Reynolds number 30000.
7 Detached V-ribs showed higher thermal hydraulic performance than detached W-ribs for the tested Reynolds numbers. Maximum thermal hydraulic performances were 2.9 and 2.7 for detached V-ribs and detached W-ribs at Reynolds number 30000.
-
The maximum difference between the thermal hydraulic performance of two rib shapes is 14.4% at Reynolds number 75000.
-
Gas turbines blades are exposed to high temperatures during operation. Due to high and large variations in temperatures during operation, thermal stresses are induced which is required to be managed efficiently. It is evident from the results of present study that the heat transfer enhancement and thermal performance achieved due to detached V-ribs and W-ribs are encouraging however, considering the key factors like uniformity in heat transfer and lower frictional losses, detached V-ribs is recommended over detached W-ribs for effective thermal management.
NOMENCLATURE
Angle of attack
P Rib pitch, mm
e Height of the rib, mm
Dh Hydraulic diameter of test section, m
W Width of the test section, mm
H Height of the test section, mm
-
Velocity of air, m/s
-
Width of the ribbed wall, mm
mass flow rate, Kg/s
-
Heat transfer coefficient, W/m2-K
Re Reynolds number
Nu Nusselt number
Nuo Nusselt number for smooth circular pipes (Dittus- Boelter correlation)
Pr Prandtl number
-
Streamwise air velocity, m/s
Density if air, Kg/m3
µ Dynamic viscosity of air, N s/m2
k Thermal Conductivity of air, W/m-K
Qinput Heat input, W
Qnet Net heat input, W
A Effective rib surface area of the foil, m2
L Length between the pressure taps of ribbed section, m
Tbulk Bulk air temperature, K
Tbin Bulk air inlet temperature, K
Tbout Bulk air outlet temperature, K
Twall Wall temperature, K
cp Specifc heat of air, J/Kg K
I Current
V Voltage
f Friction factor
fo Friction factor in smooth circular pipe (Blasius friction factor)
Thermal hydraulic performance
P Pressure drop across the ribbed section, N/m2
A Ampere
-
Volt
Ohms
-
Watt
CONFLICTS OF INTEREST STATEMENT
Manuscript title: Enhancement in Thermal Hydraulic Performance by Employing Detached Ribs inside a Gas Turbine Blade Internal Cooling Passage (AR = 1:5)
The authors D K Karthik and Dr. Srikanth Salyan certify that they have NO affiliations with or involvement in any organization or entity with any financial interest (such as honoraria; educational grants; participation in speakers bureaus; membership, employment, consultancies, stock ownership, or other equity interest; and expert testimony or patent-licensing arrangements), or non-financial interest (such as personal or professional relationships, affiliations, knowledge or beliefs) in the subject matter or materials discussed in this manuscript.
REFERENCES
-
Han JC, Zhang YM (1992) High Performance Heat Transfer Ducts with Parallel Broken and V-Shaped Broken Ribs. International Journal of Heat and Mass Transfer 35 (2): 513523. https://doi.org/10.1016/0017-9310(92)90286-2
-
Taslim ME, Li T (1994) Experimental Heat Transfer and Friction in Channels Roughened With Angled, V-Shaped, and Discrete Ribs on Two Opposite Walls. International Gas Turbine and Aeroengine Congress and Exposition, 94-GT-163. https://doi.org/10.1115/1.2836602
-
Ekkad SV, Han JC (1997) Detailed Heat Transfer Distributions in Two-Pass Square Channels with Rib Turbulators. International Journal of Heat and Mass Transfer 40 (11):2525-2537. PI1: S0017-9310(96)00318-3.
-
Gao X, Sunden B (2001) Heat Transfer and Pressure Drop Measurements in Rib-Roughened Rectangular Ducts. Experimental Thermal and Fluid Science 24: 2534. https://doi.org/10.1016/S0894-1777(00)00054-6.
-
Tzeng SC, Mao CP (2001) Heat Transfer in a Radially Rotating Four-Pass Serpentine Channel with Staggered Half-V Rib Turbulators. Journal of Heat Transfer 123:39-50. https://doi.org/10.1115/1.1338130.
-
Al-Hadhrami L, Griffith T, Han JC (2003) Heat Transfer in Two-Pass Rotating Rectangular Channels (AR=2) with Five Different Orientations of 45 Deg V-Shaped Rib Turbulators. Journal of Heat Transfer 125 (2): 232242. https://doi.org/10.1115/1.1561455
-
Wright LM, Wen-lung F, Han JC (2004) Thermal Performance of Angled, V-Shaped, and W-Shaped Rib Turbulators in Rotating Rectangular Cooling Channels (AR 4: 1). Journal of Turbomachinery 126: 604-614. https://doi.org/10.1115/1.1791286
-
Gao X, Sunden B (2004) PIV Measurement of the Flow Field in Rectangular Ducts with 60 ° Parallel, Crossed and V-Shaped Ribs. Experimental Thermal and Fluid Science 28 (2004): 639653. https://doi.org/10.1016/j.expthermflusci.2003.10.005
-
Khan RK, Ali MAT, Akhanda MAR (2006) Heat Transfer Augmentation in Developing Flow through a Ribbed Square Duct. Journal of Thermal Science 15 (3): 251256. https://doi.org/10.1007/s11630-006-0251-z.
-
Maurer M, Wolfersdorf JV (2007) An Experimental and Numerical Study of Heat Transfer and Pressure Loss in a Rectangular Channel With V-
Shaped Ribs. Journal of Turbomachinery 129: 800-806, https://doi.org/10.1115/1.2720507
-
Gupta A, Sriharsha V, Prabhu SV, Vedula RP (2008) Local Heat Transfer Distribution in a Square Channel with 90 ° Continuous , 90 ° Saw Tooth Profiled and 60 ° Broken Ribs. Experimental Thermal and Fluid Science 32: 9971010. https://doi.org/10.1016/j.expthermflusci.2007.11.015
-
Sriharsha V, Prabhu SV, Vedula RP (2009) Influence of Rib Height on the Local Heat Transfer Distribution and Pressure Drop in a Square Channel with 90 ° Continuous and 60 ° V-Broken Ribs. Applied Thermal Engineering 29 (1112): 24442459. https://doi.org/10.1016/j.applthermaleng.2008.12.015
-
Alkhamis NY, Rallabandi AP, Han JC (2011) Heat Transfer and Pressure Drop Correlations for Square Channels With V-Shaped Ribs at High Reynolds numbers. Journal of Heat Transfer 133 (11): 111901 (8 pages). https://doi.org/10.1115/1.4004207
-
Baraskar S, Aharwal KR, Lanjewar A (2012) Experimental Investigation of Heat Transfer and Friction Factor of V-Shaped Rib Roughed Duct with and without Gap. International Journal of Engineering Research and Applications 2 (6): 102431. ISSN: 2248-9622
-
Lamont J, Christopher K (2013) Heat Transfer Enhancement in Narrow Diverging Channels. Journal of Turbomachinery 135: 17. https://doi.org/10.1115/1.4007740
-
Xie G, Liu J, Ligrani PM, Sunden B (2014) Flow Structure and Heat Transfer in a Square Passage with Offset Mid-Truncated Ribs. International Journal of Heat and Mass Transfer 71: 4456. https://doi.org/10.1016/j.ijheatmasstransfer.2013.12.005
-
Smith MA, Mathison RM, Dunn MG (2014) Heat Transfer for High Aspect Ratio Rectangular Channels in a Stationary Serpentine Passage with Turbulated and Smooth Surfaces. Journal of Turbomachinery 136: 111. https://doi.org/10.1115/1.4025307
-
Kumar S, Amano RS (2015) Experimental Investigation of Heat Transfer and Flow Using V and Broken V Ribs within Gas Turbine Blade Cooling Passage. Heat and Mass Transfer 51 (5): 631647. https://doi.org/10.1007/s00231-014-1436-8
-
Ghodake NG, Rao C, Arakerimath RR (2016) Flow and Heat Transfer Analysis of Various Ribs for Forced Convection Heat Transfer. Journal of Emerging Technologies and Innovative Research 3 (7): 4247. JETIR1607010
-
Prashant S, Ravi BV, Ekkad SV (2016) Experimental and Numerical Study of Heat Transfer Due to Developing Flow in a Two-Pass Rib Roughened Square Duct. International Journal of Heat and Mass Transfer 102: 12451256. https://doi.org/10.1016/j.ijheatmasstransfer.2016.07.015
-
Abraham S, Vedula RP (2016) Heat Transfer and Pressure Drop Measurements in a Square Cross-Section Converging Channel with V and W Rib Turbulators. Experimental Thermal and Fluid Science 70: 208219. https://doi.org/10.1016/j.expthermflusci.2015.09.003
-
Prashant S, Li W, Ekkad SV, Ren J (2017) Experimental and Numerical Investigation of Heat Transfer inside Two-Pass Rib Roughened Duct (AR = 1:
2) under Rotating and Stationary Conditions. International Journal of Heat and Mass Transfer 113: 384398. https://doi.org/10.1016/j.ijheatmasstransfer.2017.05.085
-
Ravi BV, Prashant S, Ekkad SV (2017) Numerical Investigation of Turbulent Flow and Heat Transfer in Two-Pass Ribbed Channels. International Journal of Thermal Sciences 112: 3143. https://doi.org/10.1016/j.ijthermalsci.2016.09.034
-
Deng H, Li H, Tao Z, Qiu L, Zhu J (2020) Effect of Blockage Ratio on Heat Transfer and Pressure Drop in Rotating Ribbed Channels at High Rotation Numbers. Journal of Thermal Science 29. https://doi.org/10.1007/s11630-020-1275-5
-
Kline SJ, McClintock FA (1953) Describing uncertainties in single sample experiments, Mechanical Engineering 75(3-8)