
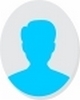
- Open Access
- Authors : Osama S. Alghamdi, Abdulrahman M. Basahal
- Paper ID : IJERTV13IS100004
- Volume & Issue : Volume 13, Issue 10 (October 2024)
- Published (First Online): 16-10-2024
- ISSN (Online) : 2278-0181
- Publisher Name : IJERT
- License:
This work is licensed under a Creative Commons Attribution 4.0 International License
Enhancement of Production Performance and Ergonomics Safety Conditions in R&D Aviation Manufacturing Sector by using 5S and Time and Motion Study Techniques
Osama S. Alghamdi Department of Industrial Engineering
King Abdulaziz University Jeddah, Saudi Arabia
Abdulrahman M. Basahal
Professor, Department of Industrial Engineering King Abdulaziz University
Jeddah, Saudi Arabia
AbstractThe research and development (R&D) unit is a crucial determinant unit that reflects company growth and performance. In particular, the R&D manufacturing units activities depend on specific requirements such as changeable design features, inconstant timeline, high failure rate, etc. So, time is usually a critical factor in this type of unit and is significantly impacted by skilled workers performance. Additionally, many workers perform their tasks interfaced with machine and manual activities for a prolonged period. Therefore, assessing time and protecting workers from ergonomic safety hazards will contribute to enhancing overall unit performance. The current study aimed to apply two lean manufacturing tools: the time and motion study and 5S methods. One computer numerical control workstation in the milling department in the R&D unit was selected to apply these methods. Firstly, the time and motion study was conducted for three products pre-5S to assess the current state of the milling department. Then, 5S was implemented. After that, a time and motion study was conducted for the same three products after the 5S method, including workstation redesign. The NASA-TLX and Nordic Musculoskeletal Questionnaire tools were applied before and after the 5S methods implementation. The main findings post-5S were reducing the standard time, movement, and subtasks to manufacture the three products. In addition, significant improvements were observed in the operators post-5S NASA TLX and Nordic Musculoskeletal Questionnaire scores. Finally, the time and motion study and 5S methods, as tools of lean manufacturing, tend to improve and measure the manufacturing process and reduce operators ergonomics risks and workload demand.
Keywords: R&D Unit, Lean Manufacturing, Time and Motion Study, 5S, Ergonomic Risks, NASA-TLX, Nordic Musculoskeletal Questionnaire
-
INTRODUCTION
The R&D unit is a specialized department within a company, organization, or institution that focuses on the research, innovation, and development of new products, technologies, or processes. The R&D units main function is to drive growth and competitive advantage by creating new knowledge, improving existing products, or developing entirely new offerings that align with the companys long-term strategy. Lean manufacturing is centered on five key principles: value, value stream, flow, pull, and perfection. These principles guide the elimination of waste and enhancement of value in production processes. In R&D workshops, where production is
characterized by high variability, these principles must be adapted to manage this environments unique challenges. The study will explore how each principle can be applied, particularly in improving workflow efficiency and reducing ergonomic risks.
Lean manufacturing has become a cornerstone for enhancing operational efficiency and reducing waste across various industries. In R&D mechanical workshops, where high variability and low-volume production are common, the integration of lean principles offers a strategic approach to address unique operational challenges.
R&D units, particularly in Saudi Arabia, face significant challenges due to the high complexity and unpredictability of tasks. Inefficiencies in scheduling, safety risks, and ergonomic hazards are prevalent, demanding tailored interventions. In R&D units, there are a variety of demand levels for manufacturing products as well as the specifications of these products, which can delay their production. That will be an obstacle to performance. Safety hazardsin particular, ergonomicsare considered an obstacle, since most staff and workers perform either sitting or standing tasks with a machine interface for a prolonged period. Therefore, the current research study aimed to evaluate lean manufacturings impact on performance metrics and health and safety risks in R&D workshops, with a focus on implementing and assessing the effectiveness of 5S, time and motion studies, NASA-TLX, and ergonomic interventions. Additionally, lean manufacturing tools, namely the time and motion study and 5S, were applied to minimize these obstacles.
Integrating safety management systems (SMS) with lean manufacturing, particularly through the 6S approach (which adds safety to the traditional 5S), can significantly enhance both safety and productivity. The study will explore how this integration can be effectively implemented in R&D environments, focusing on the reduction of ergonomic hazards and the promotion of a safety culture (Clarke et al., 2019; Kleindorfer et al., 2020).
Ergonomic hazards, such as repetitive motions, forceful exertion, and awkward postures, are prevalent in manufacturing environments and pose significant risks to workers. The study assessed these risks using the Nordic Musculoskeletal Questionnaire (NMQ) and explored how lean techniques can mitigate these hazards, improving worker safety
and comfort (Punnett & Wegman, 2019; Silverstein et al., 2018).
This research is significant as it bridges the gap between lean manufacturing theory and its practical application in R&D settings, a relatively underexplored area. By focusing on R&D workshops in Saudi Arabia, the study provides insights that are particularly relevant to industries in developing economies undergoing rapid industrialization. The findings are expected to contribute to the broader discourse on operational efficiency and safety management in the context of advanced manufacturing environments.
-
METHODOLOGY
-
Research Design
This study utilizes a case study approach to explore the application of lean manufacturing principles in an R&D mechanical manufacturing workshop in Saudi Arabia. The case study design allows for an in-depth examination of the challenges faced by the workshopsuch as meeting the clients requested deadlines to manufacture the products needed, poor housekeeping, and a weak safety culture in the R&D unitand lean interventions effectiveness in addressing these challenges. The research is divided into two phases: pre- implementation assessment and post-implementation evaluation.
To perform this study, one computer numerical control workstation from the milling department in the R&D unit was chosen. The study had 21 participants, who comprised everyone related to this workstation. Historical data showed lateness in delivering the products to the clients. Therefore, given the time made available by the management to perform this study, three similar products were chosen to manufacture before and after 5S implementation. The products were Part 1, Part 2 and Part 3 which is requested parts from clients asked to be manufactured in CNC machine using the raw material requested by the client. The request comes with 2D and 3D drawing to manufacture these Products.
This study measured production performance, worker movement, and the number of subtasks needed to accomplish the manufacturing process using the time and motion study method, safety ergonomic hazards assessment through the NMQ (Legault et al., 2014), and NASA TLX to evaluate overall taskworkloads in the R&D workshop (Dias et al., 2018). All of these measurement methods were performed pre and post 5S implementation.
-
Pre-Implementation Assessment: The initial phase involved a comprehensive assessment of the workshops current state, including safety practices, productivity levels, and ergonomic conditions. Data were collected through time and motion studies, NASA-TLX workload assessments, and the NMQ.
-
Post-Implementation Evaluation: The final phase involved a reassessment of the workshops performance to evaluate the impact of the lean interventions. The same data collection methods used in the pre-implementation phase were employed to ensure consistency and comparability of results.
-
-
Data Collection
The study employs a combination of quantitative and qualitative data collection methods to provide a comprehensive understanding of the workshops performance before and after lean implementation (Al-Ghamdi, 2020; Hignett & McAtamney, 2017).
-
Time and Motion Studies: Time and motion studies were conducted on three products, with one piece of each product requested, since the study was done in an R&D workshop running on the same workstation to obtain the standard time for each product and to analyze the time required to complete tasks and the movements involved in performing these tasks. The time and motion study method was applied from the orders delivery to the operator until the operator delivered the product to the quality control department, measuring every step with a stopwatch. This method helps identify inefficiencies in the workflow and areas where time can be saved. Such studies are conducted by observing workers as they perform their tasks and recording the time taken for each step in the process. The data are collected and then analyzed to identify patterns and areas for improvement.
-
NASA-TLX Workload Assessment: The NASA-TLX (Task Load Index) is a widely used tool for assessing perceived workload. It measures six dimensions of workload: mental demand, physical demand, temporal demand, performance, effort, and frustration level. Twenty-one workers were asked to rate each dimension on a scale after completing their tasks, providing insights into the six demands of their work. The results were used to calculate the adjusted rating for each participant in this study to identify tasks that placed excessive demands on workers and develop strategies for reducing these demands (Aktas Potur et al., 2022).
-
Nordic Musculoskeletal Questionnaire (NMQ): The NMQ is a validated tool for assessing musculoskeletal symptoms among workers. It focuses on identifying the prevalence of discomfort, pain, and other symptoms in different body regions, such as the neck, shoulders, knees, and lower back. The questionnaire was administered to the 21 workers before and after lean implementation to assess the impact of ergonomic interventions on worker health and comfort.
-
-
Lean Techniques Implementation
The study implemented two lean techniques to improve safety, productivity, and ergonomic conditions in the R&D workshop (Grier, 2015).
-
5S Methodology: The 5S methodology is implemented to organize the workspace, reduce waste, and improve efficiency. The five steps of 5S (sort, set in order, shine, standardize, and sustain) were applied to the one workstation under study, with the goal of creating a clean, organized, and efficient working environment (Hamelin, 2019). The implementation process involves engaging workers in sorting through their tools and materials, arranging them in an orderly manner, cleaning their workstations, establishing standard procedures for maintaining order, and sustaining these practices over time.
-
Workstation Redesign: Workstations are redesigned to improve ergonomic conditions and reduce the risk of musculoskeletal disorders. This involves adjusting the height and layout of workstations to reduce awkward postures, providing adjustable seating and equipment, and ensuring that
tools and materials are within easy reach. The redesign process is informed by the results of the NMQ and NASA-TLX assessments, which identify specific ergonomic issues that need to be addressed.
-
-
Data Analysis
The data collected from the time and motion studies, NASA- TLX assessments, and NMQ were analyzed using a descriptive statistical method.
-
Descriptive Statistics: Descriptive statistics, such Pie Charts and another types of charts, are used to summarize the data and provide an overview of the workshop's performance before and after Lean implementation.
-
-
-
RESULTS
-
Pre Implementation Analysis
The initial assessment revealed several areas of concern in the R&D workshop. The time and motion studies identified inefficiencies in the workflow, including excessive movement between workstations, frequent interruptions, and delays caused by disorganized workspaces. The below points show examples of unnecessary steps observed:
-
Move to request material and move back to workstation.
-
Move to request tools for the machine and move back to workstation.
-
Move to search for tools and move back to workstation.
-
Move to collect material and tools and move back to workstation.
The NASA-TLX assessment indicated that workers were experiencing high levels of demand, particularly in tasks that required precision and sustained attention. The NMQ results highlighted a high prevalence of musculoskeletal discomfort, particularly in the lower back, shoulders, knees, and neck (Kuorinka et al., 1987).
-
-
Post-Implementation Findings
The post-implementation assessment showed significant improvements across all key performance indicators.
-
Time and Motion Studies: The time and motion studies revealed reductions in the standard time, distance covered, and number of subtasks required to complete manufacturing the products. The standard time taken to complete Part 1 decreased by 6%, that of Part 2 decreased by 31%, and that of Part 3 decreased by 40%. The movement was reduced by 66% for Part 1, 59% for Part 2, and 88% for Part 3. The number of
subtasks was reduced by 50% for Part 1, 22% for Part 2, and
59% for Part 3.
-
NASA-TLX Workload Assessment: The NASA-TLX assessment showed a 44% decrease in perceived workload after calculating the adjusted rating workload for the 21 participants. Additionally, for the subscales, there was a significant decrease in the workload demands and an increase in performance, as shown in Figure 5, indicating that the lean interventions had successfully reduced the strain and workload associated with the tasks.
-
Nordic Musculoskeletal Questionnaire (NMQ): The NMQ results showed a significant reduction in musculoskeletal discomfort, particularly in the lower back, neck, knees, and shoulders. The prevalence of lower back discomfort decreased by 63%, neck discomfort decreased by 54%, knee discomfort decreased by 67%, and shoulder discomfort decreased by 69%, suggesting that the ergonomic interventions effectively addressed the issues identified in the initial assessment.
-
-
Comparative Analysis
The comparative analysis of pre- and post-implementation data demonstrated that the lean interventions positively impacted the workshops performance and safety.
-
Productivity: The reduction in task copletion standard times and interruptions led to reduced time to complete the tasks. The standard time taken to complete Part 1 decreased by 6%, that for Part 2 decreased by 31%, and that for Part 3 decreased by 40%. The streamlined workflow and organized workspaces allowed workers to complete their tasks more efficiently, leading to a significant improvement in output.
-
Ergonomics Safety and health hazards: The integration of SMS with lean practices minimized the opportunities for workers injuries and discomfort. The 5S approach, combined with regular safety audits and ergonomic assessments, created a safer working environment and fostered a culture of safety among workers.
The improvements in ergonomic conditions, as indicated by the NMQ results, led to a reduction in musculoskeletal discomfort and a decrease in absenteeism due to work-related injuries. The ergonomic interventions, such as workstation redesign, contributed to a more comfortable and sustainable working environment.
-
-
DISCUSSION
-
Interpretation of Results
This studys findings demonstrate that lean manufacturing principles, when tailored to the specific needs of R&D workshops, can significantly enhance productivity, safety, and ergonomic conditions. The reduction in task completion times and interruptions as well as the reduction in ergonomic risks and improved workload management are particularly noteworthy, highlighting the effectiveness of the 5S methodology and workstation redesign. The integration of SMS with lean practices further reinforced the positive impact on safety, creating a safer and more efficient working environment.
-
Impact on Productivity and Safety
The successful implementation of lean techniques in the R&D workshop led to substantial improvements in both productivity and safety. The reduction in task completion times and interruptions, combined with the decrease in adjusted workload rating, allowed workers to perform their tasks more efficiently and with less strain. The ergonomic interventions, particularly the workstation redesign, significantly reduced the prevalence of musculoskeletal discomfort, contributing to a healthier and more productive workforce.
Karvounis (2021) found that the implementation of 5S showed statistically significant improvements in both product quality and cost reduction for the facility. However, he also revealed that 5S led to a statistically significant decline in performance and an increase in maintenance costs. The common factor between that study and the present one is the focus on performance. However, contrary to Karvounis (2021), the performance in this paper increased. This may be because the 5S studies were conducted in different industries. This shows that 5S is not always the right lean manufacturing tool to apply depending on the type of industry.
-
Implications for Industry
This studys findings have broader implications for the R&D sector in Saudi Arabia and similar industrial contexts. By demonstrating lean manufacturings feasibility and benefits in R&D environments, this research provides a framework for other organizations seeking to enhance their innovation processes through lean methodologies. The study also highlights the importance of integrating safety and ergonomic considerations into lean initiatives, particularly in environments where tasks are complex and variable.
-
-
CONCLUSION AND RECOMMENDATIONS
-
Summary of Key Findings
The study found that the application of lean manufacturing principles in R&D mechanical manufacturing workshops led to significant improvements in productivity for the products considered in the current study, since the standard time to accomplish the tasks decreased for all the products under study. Moreover, the applied lean manufacturing toolsthe time and motion study and 5Salso led to significant positive impacts on the overall task workload and improved musculoskeletal suffering among the present studys participants. The 5S methodology and workstation redesign proved particularly effective in reducing ergonomic risks and enhancing workspace organization.
-
Conclusions
The research concludes that tailored lean strategies are essential for addressing the unique challenges of R&D environments. These strategies not only improve operational performance but also contribute to a safer and more sustainable working environment.
-
Practical Recommendations
For R&D workshops looking to implement Lean Manufacturing:
-
Adopt the 5S Methodology: Focus on workspace organization to reduce waste and improve efficiency.
-
Integrate SMS with Lean: Ensure safety practices are embedded within lean initiatives to mitigate risks.
-
Promote Continuous Improvement: Foster a culture of ongoing evaluation and refinement of processes.
-
Redesign Workstations: Improve ergonomic conditions by adjusting workstation layouts to reduce awkward postures and forceful exertions.
-
-
Future Research
Future research should explore the long-term sustainability of lean practices in R&D settings and investigate the potential for integrating advanced technologies, such as Industry 4.0, with lean manufacturing to further enhance safety and productivity (Hines et al., 2004).
REFERENCES
-
Aktas Potur, E., Toptanc, ., Kabak, M. (2022). Mental workload
assessment in construction industry with fuzzy NASA-TLX method. In
J. Xu, F. Altiparmak, M. H. A. Hassan, F. P. GarcÃa Márquez, & A. Hajiyev (Eds.), Proceedings of the Sixteenth International Conference on Management Science and Engineering Management Volume 2 (pp. 729742). Springer. https://doi.org/10.1007/978-3-031-10385-8_52
-
Al-Ghamdi, S. G., Al Rashid, A., Khan, S. A., & Koç, M. (2021). Additive manufacturing of polymer nanocomposites: Needs and challenges in materials, processes, and applications. Journal of Materials Research and Technology, 14, 910941. https://doi.org/10.1016/j.jmrt.2021.07.016
-
Clarke, S., Probst, T., Guldenmund, F., & Passmore, J. (2019). The Wiley Blackwell handbook of the psychology of occupational safety and workplace health. Wiley.
-
Dias, R. D., Ngo-Howard, M. C., Boskovski, M. T., Zenati, M. A., & Yule, S. J. (2018). Systematic review of measurement tools to assess surgeons intraoperative cognitive workload. British Journal of Surgery, 105(5), 491501. https://doi.org/10.1002/bjs.10795
-
Grier, R. A. (2015). How high is high? A meta-analysis of NASA-TLX global workload scores. Proceedings of the Human Factors and Ergonomics Society Annual Meeting, 59(1), 17271731.
-
Hignett, S., & McAtamney, L. (2017). Rapid Entire Body Assessment (REBA). Applied Ergonomics, 31(2), 201205.
-
Hines, P., Holweg, M., & Rich, N. (2004). Learning to evolve: A review of contemporary lean thinking. International Journal of Operations & Production Management, 24(10), 9941011.
-
Karvounis, N. D. (2021). Lean application: An assessment of 5S on employee attitudes and productivity [Doctoral dissertation, Old Dominion University]. STEMPS Theses & Dissertations. https://doi.org/10.25777/n2nv-wp9
-
Kuorinka, I., Jonsson, B., Kilbom, Å., Vinterberg, H., Biering-Sørensen, F., Andersson, G., & Jørgensen, K. (1987). Standardised Nordic questionnaires for the analysis of musculoseletal symptoms. Applied Ergonomics, 18(3), 233237.
-
Legault, É. P., Cantin, V., & Descarreaux, M. (2014). Assessment of musculoskeletal symptoms and their impacts in the adolescent population: Adaptation and validation of a questionnaire. BMC Pediatrics, 14, 173. https://doi.org/10.1186/1471-2431-14-173
-
Punnett, L., & Wegman, D. H. (2019). Work-related musculoskeletal disorders: The epidemiologic evidence and the debate. Journal of Electromyography and Kinesiology, 14(1), 1323.
-
Shah, R., & Ward, P. T. (2007). Defining and developing measures of lean production. Journal of Operations Management, 25(4), 785805.
-
Silverstein, B. A., Fine, L. J., & Armstrong, T. J. (1998). Occupational factors and carpal tunnel syndrome. American Journal of Industrial Medicine, 11(3), 343358.