
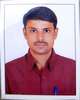
- Open Access
- Authors : Merugu Ajay Babu, Mohd. Mohinoddin, Narsimhulu Sanke
- Paper ID : IJERTV12IS070086
- Volume & Issue : Volume 12, Issue 07 (July 2023)
- Published (First Online): 07-08-2023
- ISSN (Online) : 2278-0181
- Publisher Name : IJERT
- License:
This work is licensed under a Creative Commons Attribution 4.0 International License
Enhancing Efficiency of Double Pipe Heat Exchangers with Nanofluids: A Comprehensive Review of Strategies
Merugu Ajay Babu Research Scholar University College
of Engineering Osmania University, Hyderabad.
Mohd. Mohinoddin Professor Mechanical Engineering Department Muffakham Jah College
of Engineering & Technology, Hyderabad.
Narsimhulu Sanke Professor Mechanical Engineering Department University College of Engineering Osmania University,
Hyderabad.
Abstract
The heat exchanger is an essential component in various systems and applications, and researchers have been dedicated to improving its thermal conductivity to enhance efficiency. Several strategies have been employed to achieve this goal, including the insertion of tapes with different shapes and numbers, the use of rings with varying shapes and spacing, and the transformation of a basic liquid into a nano liquid by incorporating nanomaterials with high conductivity and ultra-small particle sizes. Various types of nanomaterials have been added in different concentrations to explore their impact. Previous studies have shown that increasing heat transfer is often accompanied by a pressure drop at both ends of the exchanger. Numerous factors influence the amount of heat transferred and the resulting pressure drop. These factors include the torsion tape ratio, the pitch of the ring, and whether the pitch faces the direction of flow or not. The heat transfer rates can also be influenced by the length and angle of the wings, the number of rings and tapes, and whether they contain holes or wings. Additionally, the Reynolds number, the type, conductivity, and size of the nanomaterials, as well as the base fluid used in the nanofluid, have an impact. Furthermore, variations in the shape of the exchanger tube and the rates of rise can introduce additional effects. In this study, the factors, costs, and benefits of employing different technologies to enhance the efficiency of the Double pipe heat exchangers with nano fluids are reviewed. The aim is to provide with comprehensive information so they can make informed decisions regarding the technology to utilize. It is crucial to consider these factors to ensure the most suitable and cost-effective approach is chosen for improving heat exchanger performance.
Key words: Heat Exchangers, Nano fluids, CFD, Twisted coil, Thermal conductivity and DPHE
-
INTRODUCTION
Several researchers tried to study the consequence are some experimental and numerical studies that have been completed in recent years. Heat transfer is a correction of thermal engineering that concerns the generation, use, transformation, and interchange of thermal energy and heat between physical systems. As such heat transfer is involved in every sector of the economy. Heat transfer is divided into various mechanisms, such as, conduction, convection, radiation, and transfer of energy one place to another. Engineers also study the transfer of mass of differing chemical species, either cold or hot, to achieve heat transfer. While these mechanisms have different characteristics, they often occur instantaneously in the same system. Heat conduction, also called diffusion, is the direct microscopic exchange of kinetic energy of particles through the boundary between two systems. When an object is at a different temperature from another body or its surroundings, heat flows so that the body and the surroundings reach the same temperature, at which point they are in thermal equilibrium. Such spontaneous heat transfer always flows high temperature region to low temperature region, as described by the second law of thermodynamics. Heat convection occurs in this heat is flows two ways one is natural convection another one is forced convection, when bulk flow of a fluid (gas or liquid) carries heat along with the flow of matter in the fluid. The flow of fluid may be forced by external processes and natural convection its own transfer. All convective processes also move heat partly by diffusion, as well. In forced convection heat is forced to flow by use of a pump, fan or other mechanical means. Thermal radiation occurs through a vacuum or any transparent medium (solid or fluid) It is the transfer of energy by means of photons in electromagnetic waves governed by the same laws.
Heat exchangers are widely used in various engineering and industrial applications, including factories,
power plants, heating and cooling equipment, and industries such as electricity, chemical, energy-saving, and petroleum. They serve important roles in these industries and play a vital role in processes involving heating, cooling, and thermal energy transfer. Chemical evaporators, which are a type of heat exchanger, can be classified based on the area, shape, and function of the process, as well as the liquid-to-vapor phase-change exchanger classification. The classification of heat exchangers can also be based on their construction type and the method of energy supply. This categorization allows for a better understanding of the tasks performed by heat exchangers in different projects and systems. Heat exchangers operate by transferring internal thermal energy between fluids of different temperatures or between a liquid and a solid surface in thermal contact. They facilitate the exchange of heat and are primarily used for heating and cooling purposes. Heat exchangers are vital components in a wide range of thermal applications in our daily lives, including food preservation, cooling and heating systems, and various devices that require heat absorption or rejection. Given the significance of heat exchangers, engineers are continually seeking ways to enhance heat transfer rates and improve the overall efficiency of these systems. The objective is to maximize the effectiveness and quality of heat exchangers in order to optimize their performance and meet the demands of different applications. This pursuit of efficiency and effectiveness is driven by the crucial role heat exchangers play in numerous aspects of our daily lives.
Heat Exchangers Applications
external power makes them less practical and limited in some applications.
On the other hand, passive techniques do not require external power for heat transfer enhancement. They utilize the existing energy within the system. Examples of passive techniques include using enhanced surfaces like fins or extended surfaces to increase the available surface area for heat transfer. Additionally, turbulence promoters like twisted tapes or vortex generators can be used to enhance fluid mixing and heat transfer. However, passive techniques may lead to increased fluid pressure drop, which can impact overall system efficiency.
Compound techniques combine elements of both active and passive techniques to achieve heat transfer enhancement. By leveraging the benefits of both approaches, compound techniques aim to mitigate their respective limitations. For instance, these techniques may involve combining passive heat transfer enhancement elements with controlled fluid flow or periodic activation of active techniques.
In summary, the field of heat transfer enhancement involves a diverse range of techniques tailored to specific industrial needs. By understanding the advantages and limitations of active, passive, and compound techniques, engineers can select the most suitable approach to optimize heat transfer efficiency while meeting application requirements.
Heat exchangers may be classified they are shown in
below
-
Recuperators or regenerators
-
Transfer Process (Direct contact and indirect
Process industry Power industry Air conditioning Electronic cooling Heat storage
contact)
-
Type of construction (tubes, plates and extended
Reboilers Fossil boilers Evaporators Micro coolers Direct contact
condensers
surfaces)
-
Heat transfer mechanism (single phase and two
Evaporators Nuclear steam generators
Condensers Heat sinks Steam accumulators
phase)
-
Flow arrangement (Parallel flow, counter flow or
Condensers Condensers Cold plates Phase change
materials
Freezers Cooling Towers Heat pipes
cross flow)
Figure 2 shows the classification of heat exchanger
Micro structured Heat Exchangers
Micro structured Heat Exchangers
many applications require the space to be occupied by the
MEMS Heat pumps
Fig. 1 Few applications of heat Exchangers
Heat transfer enhancement is a critical aspect in various industrial applications, and there are three main categories of techniques used to achieve it: active techniques, passive techniques, and compound techniques.
Active techniques involve the application of external power to enhance heat transfer. Methods like mechanical agitation, vibration, or electric fields are utilized to improve heat transfer rates. Although effective, these techniques can be complex to implement and design, and their reliance on
exchanger to be kept as low as possible. The compact heat
exchangers supply this purpose along with the necessary amount of energy exchange and low fluid inventory.
Fig.2 Classifications of heat Exchangers
Overall, the choice of heat transfer enhancement technique depends on the specific application and the balance between the desired heat transfer improvement, power requirements, and other system considerations. Engineers and researchers continue to explore and develop new techniques in order to enhance heat transfer efficiency in industrial applications.
Younus Hamoudi Assaf et al. [1] The paper reviewed factors, costs, and benefits of using nano additives in heat exchangers with twisted tapes and rings to enhance efficiency. The goal was to help users make informed decisions about the technology to use.
Mehta et al. [2] The researchers tested the
performance of compact heat exchangers using 23
nanofluid. They used the Number of Transfer Units (NTU)
method to study the nanofluid's effect on heat exchanger performance. A heat exchanger was designed and developed using the nanofluid.
Poudel et al. [3] This study investigated the thermal conductivity and viscosity of copper nanoparticles in ethylene glycol to create a nanofluid. Copper nanoparticles were synthesized using a chemical reduction method and dispersed in ethylene glycol with water as the solvent. The measured increase in thermal conductivity was twice the value predicted by the Maxwell effective medium theory. The increase in viscosity was about four times of that predicted by the Einstein law of viscosity. Analytical calculations suggested that using this nanofluid as a coolant in heat exchangers without changing the tube diameter would not be beneficial. However, increasing the tube diameter could exploit the nanofluid's increased thermal conductivity for better performance.
Hasanuzzaman et al. [4] The researchers conducted an experimental analysis of heat exchanger effectiveness
enhancement using various nanofluids (CuO-water, 23 – water, and Ti2-water) with 2% nanoparticle concentration
in counter flow heat exchangers. They compared the thermal
efficiency of the heat exchanger using water as the working fluid. CuO-water nanofluid showed a significantly higher convective heat transfer coefficient (81% higher) and overall heat transfer coefficient (23% higher) compared to water and other nanofluids.
Hejazi et al. [5] Conducted experiments on condensation of HFC-134a in a horizontal double-tube counter-flow heat exchanger with different twisted tape inserts. Found that a twisted tape with a twist ratio of 6 provided the highest enhancement in heat transfer coefficient and maximum pressure drop compared to the plain tube. Heat transfer and pressure drop increased by 40% and 240%, respectively, compared to the plain tube. The twisted tape with a twist ratio of 9 showed the best performance in enhancing heat transfer with the minimum pressure drop.
Developed empirical correlations for predicting smooth tube and swirl flow pressure drop.
Anil Singh Yadav [6] Investigated heat transfer and pressure drop characteristics in a double pipe heat exchanger with half-length twisted tape tabulators. Swirling flow was generated using twisted half-length tape mounted inside the inner tube heat exchanger. The experimental results showed that the swirl or vortex motion created by the twisted tape significantly increased the heat transfer rate. The thermal performance of the smooth tube was better than that of the half-length twisted tape.
Anil Yadav [7] Studied the impact of half-length twisted tape insertion on heat transfer and pressure drop characteristics in a U-bend double pipe heat exchanger. The half-length twisted tape inserts increased the heat transfer rate significantly due to the tape-induced swirl or vortex motion. Heat transfer coefficient increased by 40% compared to the plain heat exchanger. On the basis of equal mass flow rate, the heat transfer performance of half-length twisted tape was better than the plain heat exchanger, while the smooth tube had better performance on the basis of unit pressure drop. The thermal performance of the plain heat exchanger was better than the half-length twisted tape by 1.3-1.5 times.
Smith Eiamsa-ard et al. [8] Investigated a double pipe heat exchanger with regularly spaced twisted tape inserts and compared the findings with a heat exchanger without a twisted tape insert. Found that the heat transfer coefficient increased with the twist ratio of the twisted tape.
PV Durga Prasad et al. [9] Analyzed trapezoidal tape inserts in a double pipe heat exchanger to increase heat transfer efficiency. The heat transfer coefficient and friction factor characteristics were calculated to carry out performance analysis. The performance results showed that as the Reynolds number increased, the Nusselt number also increased. Trapezoidal tape inserts with a specific H/D ratio enhanced the heat transfer efficiency by 34.24% compared to a plain tube with water.
Azad and Moztarzadeh [10] Conducted a theoretical study using the NTU approach for co-axial heat pipe heat exchangers. Investigated the effect of the number of rows of co-axial heat pipes on the thermal efficiency of the heat exchanger.
Hsieh and Huang [11] Studied the numerical calculation of thermal efficiency and pressure drop of heat- pipe heat exchangers with aligned tube rows. Found that counterflow exhibited better heat transfer rates and lower pressure drop compared to the parallel flow method.
Tan and Liu [12] Established an NTU model to predict the thermal performance of heat pipe heat exchangers. Compared their results with previous investigations and found good agreement. Concluded that the NTU approach is
a convenient method for predicting heat exchanger performance.
Madhu Shree Kole, T.K. Dey [13] Used water as the base fluid and CuO as nanoparticles to prepare surfactant-free nanofluids using long-duration sonication. Investigated the thermal conductivity, viscosity, and pool boiling performance of the nanofluids as a function of particle volume fraction and temperature. Reported significant enhancements in boiling heat transfer coefficient and marginal viscosity enhancement due to the use of nanofluids.
Y. Raja Sekhar et al. [14] Conducted experimental analysis and observed that the Nusselt number and friction factor increase with an increase in nanoparticle concentration. The friction factor decreases with an increase in Reynolds number, while the Nusselt number increases. Using nanofluids and twisted apes in pipe flows showed advantages in terms of heat transfer enhancement and energy efficiency.
Layth W. Ismael et al. [15] Conducted experimental analysis and emphasized the development of thermal conductivity due to the presence of nanoparticles in the fluid, showing greater enhancement than micro fluids. Found that the addition of highly conductive nanoparticles significantly increases the thermal conductivity of heat-transfer fluids.
Faris Mohammed Ali et al. [16] Through numerical simulations, it was found that the thermal conductivity and thermal diffusivity of nanofluids increase with increasing particle size. The thermal conductivity and thermal diffusivity
of 23 nanofluids also increase with higher volume fraction
concentrations. This enhancement is attributed to various
factors, including ballistic energy, the nature of heat transport in nanoparticles, and the interfacial layer between solid and fluids.
Masuda et al. [17] Investigated the thermal transport properties of nanofluids containing metallic oxide nanoparticles (Aluminum oxide and Titanium oxide) in water. Using the hot wire transient technique, they calculated
the thermal conductivity of 2O -based nanofluids and found approximately 30% and 12% enhancements in 2O-23 and 2O – Ti2 nanofluids, respectively.
Murshed et al. [18] Conducted experimental
measurements of thermal conductivity in Titanium oxide nanoparticle-based nanofluids in de-ionized water using a transient hot wire system. Their experimental results showed an increase in nanofluid thermal conductivity with an increase in nanoparticle volume concentration. Attempted to compare experimental values with predictions from different models (Bruggeman, Hamilton & Crosser, and Wasp), but the models failed to accurately predict the augmentation of thermal conductivity.
Rohit et al. [19] Utilized Ti2/water nanofluid as a
coolant medium in a concentric heat exchanger. Observed
that the addition of more nanoparticles increased heat transfer
at the same Reynolds number. Proposed a new correlation to
predict the Nusselt number and friction factor of Ti2/water nanofluid, with good agreement between experimental and
theoretical values.
Shyam Sundar et al. [20] Focused on investigating the thermophysical properties and convective heat transfer
characteristics of 23 nanofluid. Conducted experimental
measurements of thermal conductivity and viscosity at
various volume concentrations and temperatures, validating the properties through experiments.
Nagasarada et al. [21] Conducted experimental analysis on enhancing heat transfer using twisted tape inserts of different widths in a circular horizontal tube under turbulent flow conditions.
The study aimed to investigate the effect of reduced twisted tape widths on heat transfer coefficients and pressure drops compared to a standard tube width.
Yue Cao et al. [22] Investigated the optimum design for a plate-fin heat exchanger (PFHE) of a gas and supercritical carbon dioxide combined cycle using thermal oil as an intermediate heat-transfer fluid.
Used a multi-objective genetic algorithm (NSGA-II) to optimize the number of fin layers, plate width, and geometrical parameters of fins on both sides of the PFHE based on conflicting objectives: heat transfer area and pressure drop on the exhaust side. Applied the TOPSIS approach to choose the best solution from the Pareto frontier obtained by NSGA-II, and further simulations confirmed the rationality of the optimization results.
Mladen Bonjakovi and Simon Muhi [23] Presented numerical analysis of a tube heat exchanger with trimmed star-shaped fins. Found that trimming the rear part of the fin to Ø28 mm led to the best results, with up to 8.12% increase in heat transfer and a reduction in pressure drop of up to 0.92% compared to star-shaped fins without trimming. Compared trimmed fins with perforated star-shaped fins and observed that trimmed fins increased the heat transfer coefficient by up to 5.75% and reduced pressure drop by up to 0.76% compared to perforated fins.
Raman Bedi et al. [24] Conducted experimental investigation on augmenting heat transfer in a shell and tube heat exchanger using twisted tape with baffles and hiTrain Wire Matrix inserts.
The study revealed that the inserts efficiently disturb the tube-side fluid flow, resulting in increased pressure drop, wall shear, and substantial enhancement in tube-side heat transfer rate.
Twisted tape with baffles showed higher heat transfer coefficient at lower Reynolds numbers, while hiTrain wire had higher heat transfer coefficient at higher Reynolds numbers.
Ali K. Abdul Razzaq et al. [25] Conducted a numerical study on a double twisted tube heat exchanger and found that it exhibited higher heat transfer compared to a plain tube heat exchanger.
The twist ratio was found to affect the cold outlet temperature, pressure drop, and effectiveness, with increasing twist ratio leading to increased values of these parameters.
Dr. Hisham Assi Hoshi [26] Conducted experimental investigation on enhancing heat transfer using a combined insert of twisted tape with circular cut and wire coil in a double pipe heat exchanger. The combined wire coil with twisted tape showed 1.268 times higher enhancement efficiency compared to using each device alone and the plain tube, outperforming the twisted tape and wire coil alone.
Based on the literature review, the following key points and research gaps have been identified:
Nanofluids for heat transfer enhancement: Nanofluids have been widely applied in various engineering applications such as food processing, chemical industries, and power plant engineering to enhance heat transfer with lower heat exchanger costs and reduced power consumption.
Heat transfer improvement techniques: Many heat transfer enhancement techniques, including active, passive, and compound methods, have been used to improve the performance of heat exchangers for industrial applications with a focus on minimizing operating costs.
Surface modifications for increased heat transfer: The literature indicates that an increase in heat transfer can be achieved through surface modifications of heat exchangers, such as using plain twisted tape inserts and helical coil inserts, especially when nanofluids are used under different flow conditions.
Limited attention to fractal geometries: Despite various heat transfer enhancement techniques, the use of fractal geometries in the design of heat exchangers has received little attention and exploration. Further research in this area could lead to novel and efficient heat exchanger designs.
Low heat transfer augmentation in plain tube flow: Traditional plain tube designs with straight-line fluid flow and no swirl motion result in relatively low heat transfer augmentation in the tube side. This highlights the need for innovative approaches to enhance heat transfer in plain tube configurations.
Based on the exhaustive literature study, the following research gaps have been identified as listed below:
-
Little researchers have used water, 2OTi2water nanofluids, 23 water nanofluids as working and heat
transport fluid.
-
Few researchers have investigated the implementation of DPHE with U bend and V bend and twisted tape with minimum influencing parameters.
-
There is no such work was carried on perforated twist tape and perforated Circling twisted tape on inner tube of DPHE.
-
Comparative study on working and heat transport fluid has not been reported based on various length of the pipe, length of the twist and twist angle of Circling twisted tape.
-
-
OBJECTIVES
Based up on previous studies and literature gaps The present work will concentrates on different types of inserts such as the twisted tape, Circling twisted tape on the inner tube, perforated twist tape with various profile cuts and perorated Circling twisted tape on inner tube in Double Pipe Heat Exchanger (DPHE) with different nanofluid such as
23 and Ti2 along with 2O which gives better thermal
enhancement than the conventional fluids with this fallowing
objectives have been made for my work.
The objectives you mentioned involve the computational and experimental investigation of different configurations of double-pipe heat exchangers (DPHE) and the optimization of various process parameters. Here is a summary of the objectives:
Experimental Investigation: The second objective is to conduct experimental studies to compare and validate the results obtained from the CFD analysis. Experimental investigations will involve measuring heat transfer coefficients, pressure drops, and overall performance of the DPHE configurations under different operating conditions.
Computational Fluid Dynamics (CFD) Analysis: The first objective is to perform a CFD analysis using ANSYS FLUENT software on three different configurations of DPHE: traditional (without inserts), DPHE with twisted tape inserts, and DPHE with circling twisted tape inserts along with perforated profiles. This analysis aims to simulate and analyze the fluid flow, heat transfer, and pressure drop characteristics of these configurations.
Optimization of Process Parameters: The third objective is to improve the effectiveness of the DPHE by optimizing various process parameters. This could include parameters such as flow rates, tube dimensions, insert geometries, and operating temperatures. The goal is to enhance the heat transfer performance and efficiency of the DPHE.
Nanofluid Utilization: The fourth objective involves
using nanofluids, specifically Ti2 and 23 nanoparticles dispersed in water ( 2O), to examine their effectiveness in
enhancing the heat transfer performance of the DPHE. The
nanofluids will be evaluated for their thermophysical properties and their impact on heat transfer and pressure drop in the heat exchanger.
Modified Twisted Tape Geometries: The fifth objective is to explore and evaluate geometric modifications of the twisted tape inserts. This includes using various types
of twisted tapes, such as different twist ratios or profiles, as well as incorporating perforations in the twisted tape design. The goal is to assess the impact of these modified geometries on heat transfer and pressure drop characteristics.
Performance Comparison: The final objective is to compare the performance of the modified heat exchanger geometries (twisted tape with different modifications, circling twisted tape with perforations) with that of the traditional DPHE configuration. This comparison will help assess the effectiveness and efficiency improvements achieved with the modified geometries.
Overall, these objectives aim to enhance the understanding of DPHE performance, optimize process parameters, explore nanofluid utilization, and evaluate modified geometries to improve the heat transfer efficiency of the heat exchanger.
-
CONCLUSIONS
Heat exchangers with nanoparticles offer a promising avenue for extracting energy efficiently. The incorporation of nanoparticles in heat transfer fluids significantly enhances heat transfer performance and improves overall system efficiency. With further advancements in nanoparticle synthesis, heat exchanger design, and long-term reliability assessment, nanoparticle-enhanced heat exchangers hold great potential for a wide range of energy conversion applications, contributing to a sustainable and energy- efficient future.
-
The use of twisted tape inserts and circling twisted
tape inserts with perforated profiles in DPHE significantly enhances heat transfer performance compared to the traditional configuration.
-
CFD simulations provide valuable insights into fluid
flow patterns, heat transfer characteristics, and pressure drop distribution within the DPHE.
-
Heat transfer coefficients and pressure drops will
measured experimentally confirm the enhancement achieved with twisted tape inserts and circling twisted tape inserts with perforated profiles.
-
The experimental studies highlight the importance
of considering practical limitations, such as manufacturing constraints and flow maldistribution, when optimizing process parameters.
-
The optimization of various process parameters,
including flow rates, tube dimensions, and operating temperatures, leads to improved heat transfer performance and efficiency of the DPHE.
-
Optimal parameter combinations are identified that
maximize heat transfer while minimizing pressure drop, resulting in enhanced overall heat exchanger performance.
-
The optimized DPHE design ensures effective utilization of available resources and provides cost- effective solutions for specific heat transfer requirements.
-
The utilization of nanofluids, specifically Ti2 and
23 nanoparticles dispersed in water ( 2O),
demonstrates their potential for enhancing heat
transfer in DPHE.
-
Nanofluids exhibit improved thermophysical properties, such as increased thermal conductivity, which contribute to enhanced heat transfer coefficients.
-
The experimental results validate the potential of
nanofluids to enhance heat transfer performance in DPHE, providing insights into their suitability for practical applications.
-
Geometric modifications of twisted tape inserts,
including variations in twist ratio, profiles, and perforations, offer opportunities to enhance heat transfer performance in DPHE.
-
The experimental investigation will show that
modified twisted tape geometries can further improve heat transfer coefficients while minimizing pressure drop penalties.
-
The selection of an optimal twisted tape geometry
depends on specific heat transfer requirements, fluid properties, and practical considerations.
REFERENCES
[1]. Younus Hamoudi Assaf, Impact of Nano Additives in Heat Exchangers with Twisted Tapes and Rings to Increase Efficiency: A Review, Advanced Technologies Applied to Renewable Energy,Sustainability 2023
[2]. Mehta, K.T. Dinesh, M.J. Nilesh, and M.P. Nimit, Heat Exchanger using Nanofluid, International Journal of Advanced Engineering Technology, 3 , 49 – 54. [3]. J.G. Poudel, M. Chiesa, J.B. Gordon, J.J. Ma, J.B. Wang, Z.F. Ron,Y.T. Kang, H. Ohtani, J. Nanda, G.H. Mcklnley and G. Chen, Enhancement Thermal Conductivity and Viscosity of Copper Nano Particles in Ethylene Glycol Nanofluid, Journal of Applied Physics, 103, 074301.
[4]. M. Hasanuzzaman, R. Saidu, and N.A. Rahim, Effectiveness Enhancement of Heat Exchanger by using Nanofluids, IEEE First Conference on Clean Energy and Technology, 11, 98 – 103. [5]. Hejazi V, M A Akhavan- Behabadi and Afshari, experimental investigation of twisted tape inserts performance on condensation heat transfer enhancement and pressure drop, International communications in heat and mass transfer, Vol. 37, pp.1376-1387. [6]. Anil Singh Yadav, Effect of Half-length Twisted tape tabulators on heat transfer and pressure drop characteristics inside a double pipe U bend heat exchanger, Jordan Journal of Mechanical and Industrial Engineering, Vol. 3, No. 1, pp. 17-22. [7]. Anil Yadav Effect of half-length twisted tape tabulator on heat transfer and pressure drop characteristics inside a double pipe U bend heat exchanger, Jordan journal of mechanical & Industrial engg, Vol.3, pp.17-22. (2009) [8]. Smith Eiamsa Ard, Chinark Thianpong, and Pongjet Promvonge , Experimental Investigation of heat transfer and flow friction in acircular tube fitted with regularly spaced twisted tape element, International communication in Heat and Mass Transfer, Vol. 33, pp.1225-1233. (2006)
[9]. Durga Prasad P V, Gupta A V S S K S and DeepakK, Investigation of Trapezodial cut twisted tape insert in a double pipe U tube heatexchanger using 23/ water nanofluid, 2nd International
Conference on Nanomaterials and Technologies, Procedia Materials
Science, Vol. 10, pp. 50-63. (2014)
[10]. E. Azad, and F. Moztarzadeh, Design of Air to Water Co-Axial Heat Pipe Heat Exchanger, Heat Recovery System, 5 (3) , 217 – 224. [11]. S.S. Hsieh, and D.C. Huang, Thermal Performance and Pressure Drop of Counter Flow and Parallel Flow Heat Pipe Heat Exchangers with Aligned Tube Rows, Heat Recovery System and CHP, 8 (4), 343 – 354. (1988) [12]. J.O. Tan, and C.Y. Liu, Predicting the Performance of a Heat Pipe Heat Exchanger using the Effectiveness NTU Method, International Journal of Heat and Fluid Flow, 11 (4), 376 – 379. (1990) [13]. Madhusree Kole, TK Dey, Role of interfacial layer and clustering on the effective thermal conductivity of CuOgear oil nanofluids [14]. Y. Raja Sekhar, Experimental investigation the nanofluids heat transfer characteristics in horizontal spirally coiled tubes, [15]. Experimental investigation of thermal conductivity and pressure drop for water nanofluid mixture, Layth W. Ismael & Khalid F. Sultan Iraqi journal of mechanical and material engineering, 2013, Volume 13, Issue 3, Pages 570-585 [16]. The effect of volume fraction concentration on the thermal conductivity and thermal diffusivity of nanofluids: Numerical and experimental, Faris Mohammed. [17]. Masuda, H, Ebata, A, Teramae, K & Hishinuma, N, Alternation of Thermal Conductivity and Viscosity of Liquid by Dispersing Ultra-Fine Particles (dispersions of 23, SiO2, and TiO2 Ultra-fine
particles Netsu Bussei (Japan), Vol. 4, pp. 227-233.
[18]. Murshed, SMS, Leong, KC & Yang, C, Enhanced thermal conductivity of TiO2 Water based nanofluids, International Journal of Thermal Sciences, Vol. 44, pp. 367 373. [19]. Rohit S Khedkar, Sriram S Sonawane, Kailas L Wasewar, Influence of CuO nanoparticles in enhancing the thermal conductivity of water and mono ethylene glycol based nanofluid, International communication in Heat and Mass Transfer, Vol. 39, pp. 665-669. [20]. Shyam Sundar and K V Sharma, Turbulent heat transfer and frictionfactor of 23 nanofluid in circular tube with twisted tape inserts, International Journal of Heat and Mass transfer, Vol. 53, pp. 1409-
1416.
[21]. Naga Sarada. S, Sita Rama Raju.A.V, Kalyani Radha.K, and Shyam Sundar.L , Enhancement of Heat transfer using varying width twisted tape inserts, International Journal of Engineering, Science and Technology, Vol.2, No. 6, pp. 107-118. (2010) [22]. Yue Cao, Jun Zhan, Jianxin Zhou and Fengqi Si Design Optimization of Plate-Fin Heat Exchanger in a Gas Turbine and Supercritical Carbon Dioxide Combined Cycle with Thermal Oil Loop, Appl. Sci. 2022, 12, 42 [23]. Numerical Analysis of Tube Heat Exchanger with Trimmed Star- Shaped Fins , Mladen Bonjakovi´c and Simon Muhic Appl. Sci. 2022, 12, 4857. https://doi.org/10.3390/ app12104857 [24]. Raman Bedi, K Kiran, A M Mulla, Manoj and Gurumoorthy S Hebbar, Experimental Augmentation of Heat Transfer in a Shell and Tube Heat Exchanger using Twisted Tape with baffles and hiTrain Wire Matrix Inserts A Comparative Study, Volume 376, International Conference on Advances in Manufacturing, Materials and Energy Engineering (ICon MMEE 2018) 23 March 2018,
[25]. A Numerical Study for a Double Twisted Tube Heat Exchanger, AliK. Abdul Razzaq, Khudheyer S. Mushatet , Page: 1583-1589, International Journal of Heat and Technology, Vol. 39, No. 5,
October, 2021
[26]. Dr. Hisham Assi Hoshi, Experimental investigation of enhancement heat transfer of insert twisted tape of circlar cut with wire coil in thedouble pipe heat exchanger , Vol. 22, No.03, May 2018 ISSN 2520- 0917