
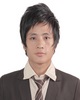
- Open Access
- Authors : Param Tamin , Purnachandra Bramhankar, Vishal Gajghate
- Paper ID : IJERTV11IS030141
- Volume & Issue : Volume 11, Issue 03 (March 2022)
- Published (First Online): 29-03-2022
- ISSN (Online) : 2278-0181
- Publisher Name : IJERT
- License:
This work is licensed under a Creative Commons Attribution 4.0 International License
Enhancing The Strength of Pervious Concrete using Polypropylene Fibre
Param Tamin1
Persuing M. Teech in Transportation Engineering G H Raisoni University, Saikheda M.P India
Purnachandra Bramhankar2
Assistant Professor, Department of Civil Engineering
G H Raisoni University, Saikheda M.P India
Vishal Gajghate 3
HOD
Department of Civil Engineering G H Raisoni University,
Saikheda M.P India
Abstract: Pervious concrete pavement is an effective means to address important environmental issues and support green and sustainable growth. By capturing storm water and allowing it to seep into the ground, pervious concrete is instrumental in recharging groundwater, reducing storm water runoff, and Meeting U.S. Environmental Protection Agency(EPA) storm water regulations. In fact, the use of pervious concrete is among the Best Management Practices recommended by the EPA. This report provides the information obtained from a literature search, site visits, and a laboratory study of polypropylene fibers in Pervious concrete. The literature search yielded information from numerous laboratory studies of the material properties of polypropylene fiber reinforced concrete (PFRC). The literature showed that, for the low fiber volumes (0.15% and 0.2%) recommended by most manufacturers, there was marginal improvement in toughness, fatigue, impact resistance, permeability, shrinkage, and wear resistance. Limited construction has taken place on PFRC suitable for airport construction. Most construction has been of slabs-on-grade and structural slabs. The laboratory study showed that, at 0.2% percent by volume offibers, the reinforced concrete enhances the strength of pervious concrete.
Keywords: Pervious concrete, Polypropylene fibres, Compressive strength, Ground water recharge.
- INTRODUCTION
Pervious concrete is a special concrete that contains continuous voids which are intentionally incorporated into concrete, allows water from precipitation and other sources to pass through, which in turn reduces the runoff from a site and recharging ground water levels. Porous concrete also called pervious concrete, no-fine concrete, gap graded concrete, enhanced porosity concrete is a macro- porous concrete. Urbanization and the resulting increase in urban storm water led to an increase in runoff and pollution. The natural process of rainfall infiltration has been diverted and decreased. Decreasing the infiltration rate causes deduction in recharging groundwater which has led to a number of environmental concerns, decreasing the base flow in streams and drying up of small streams. Pervious concrete is made by omitting the fine aggregate from the concrete mixture. Porous concrete can be used in numerous applications such as permeable concrete for pavement, base course, concrete bed for vegetation or living organism, noise absorbing concrete, thermal insulated concrete and other civil engineering and architectural applications. Porous concrete is made of attached single-size aggregate by Portland cement. Aggregate is the main part of the concrete volume. Chemical properties of porous concrete are similar to the dense concrete. In porous concrete sufficient paste, which is created by controlled amounts of water and cementation materials, coats and binds the aggregate particles and create a highly permeable and well drained system. Since the aggregate strength is usually high, the strength of the thin paste around the aggregate particles and the strength of the interface between the aggregate and the paste are relatively weak. The pervious concrete strength therefore depends primarily on the properties of the paste and the interface between the paste and the aggregate. Optimum range of water cement ratio for both strength and permeability point of view ranges from 0.28 to 0.40. High range Water reducer and thickening agent are introduced in the concrete to improve its strength and workability. Addition of styrene butadiene latex is found to improve the compressive strength but reduce permeability. Pervious concrete, three components must be improved, the strength of the paste, the paste thickness around the aggregate, and the interface between the aggregate and the paste.
-
- POLYPROPYLENE FIBRE:
-
- FIBRE USED IN CONCRETE
The raw material of polypropylene is derived from monomeric C3H6 which is purely hydrocarbon. Its mode of polymerization, its high molecular weight and the way it is processed into fibers combine to give polypropylene fibers very useful properties as explained below:
-
-
- There is a sterically regular atomic arrangement in the polymer molecule and high crystalline. Due to regular structure, it is known as isotactic polypropylene.
- Chemical inertness makes the fibers resistant to most chemicals. Any chemical that will not attack the concrete constituents will have no effect on the fiber either. On contact with more aggressive chemicals, the concrete will always deteriorate first.
- The hydrophobic surface not being wet by cement paste helps to prevent chopped fibers from balling effect during mixing like other fibers.
- The orientation leaves the film weak in the lateral direction which facilitates fibrillations. The cement matrix can therefore penetrate in the mesh structure between the individual fibrils and create a mechanical bond between matrix and fiber.
-
The polypropylene fibre that will be used for test: Type = polypropylene Length = 40 mm
Diameter = 2 mm Aspect ratio = 20
Properties Polypropylene fibre
Density (g/cub.m) Fibre cut length (mm) Diameter (mm) Aspect ratio (L /D) Dosage
Tensile strength (kg
/cub. m) Elongation (%)
0.905
40
2
20
0.1 -0.3 % by volume of concrete
330
12
Flexural modulus (Kg 13,500 /cub. m) Permeability Good
Durability Excellent
-
- SPECIFICATION OF MATERIAL USED:
- CEMENT
- SPECIFICATION OF MATERIAL USED:
-
- MATERIAL USED
Cement is a fine grey powder. It is mixed with water and material such aggregates. The cement and water form a paste that binds other materials together as concrete hardens. In the present work 53 grade cement was used for casting of cubes for all concrete mixes. The cement was uniform colour i.e. grey with a light greenish shade and was free lumps. Ordinary Portland cement ULTRA TECH 53 GRADE was used.
-
-
- COARSE AGGREGATE
-
Crushed granite stones from local queries were used as aggregate. The maximum size of aggregate used was 20 mm retained to the 12.5 mm. The broken stones are generally used as aggregate. The aggregate where washed to removed dirt and dust and were dried to surface dry condition.
3.1.2.1 Test for Aggregate:
3.1.2.1.1 Water Absorption: Water absorption test value = 1.3 %. 3.1.2.1.2Specific Gravity:
Specific gravity of the sample is = 2.63.
3.1.2.1.3 Aggregate Impact Test:
Aggregate Impact Value of the sample is = 13.
Aggregate impact values are used to classify the stone aggregate with respect to toughness property, as indicated below:
Aggregate impact value, %
Toughness property Less than 10 Exceptionally tough / strong 10 to 20 Very tough / strong 20 to 30 Good for pavement surface course Above 35 Weak for pavement surface Table no.1 Criteria of Aggregate Impact Value
According to these criteria our aggregate sample is very tough and strong, so we can use this aggregate in our construction.
3.1.3 WATER
Portable water free from salts was used for casting and curing of concrete as per IS 456-2000 recommendation. Water quality used in pervious concrete should be the same as that used in conventional concrete: potable water, recycled water, or tap water. Due to the sensitivity of pervious concrete, water quality control is very important.
4.1 METHOD:
-
- MIX DESIGN
While pervious concrete contains the same basic ingredients as the more common conventional concrete [i.e. Aggregate, Portland cement, water, and a variety of admixtures], the proportioning of ingredients is quite different. One major difference is the requirement of ingredients is quite different. One major difference is the requirement of increased void space within the pervious concrete. The amount void space is directly correlated to the permeability of the pavement. With low water to cement ratio, the need for void space within the mix design, and little to no fine aggregates, the conventional design of concrete needs
to be adjusted accordingly. Ranges of materials associated with pervious concrete are listed below. These ranges are based on previous research.
Design void content: 15% to 25% Water to cement ratio: 0.27 to 0.33
The goal for the final mix design was to provide a strong, durable pervious concrete design which allowed for adequate drainage of rainwater. Reviewing the literature and past research, a 15% design void content would have allowed for higher strength and durability in the previous concrete samples but not allowed adequate drainage based on Maryland peak storm events. A 25% void content would have allowed more than enough void space in the samples to accommodate a peak storm even in Maryland but have provided the strength and durability that was required for the research project.
ACI mix design method. NRMCA Mix design method. ASTM Mix design method.
IS recommended mix design method.
These all are very useful method to mix design of pervious concrete.
- METHODOLOGY We will prepare several cubes for testing the compressive strength.
-
- BATCHING:
Batching is the process of measuring and combining the ingredients of concrete. Careful procedure was adopted in the batching, mixing and casting operations.
For compressive strength with water cement ratio 0.36% and different percentage of admixtures by volume of concrete.
5.1.1 Dosage of fibres and their calculation:
- Calculation for volume of cube:
Volume of one cube = [0.15 X 0.15 X 0.15] m3= 0.003375 m3 Weight of one cube = 0.003375 X 2362(concrete density) = 7.972 kg
- Calculation of volume of concrete for M20 grade:
Cement to aggregate ratio = 1:4
- Volume of cement for one meter cube = 1/ (1+4)= 0.2 m3 Weight of cement per meter cube = 0.2 X 1440(bulk density)= 288 kg Volume of cement for one cube = 0.003375/(1+4) = 0.000675 m3
Weight of cement for one cube = volume X bulk density = 0.000675 X 1440 = 0.972 kg b.Volume of aggregate for one meter cube =4/ (1+4)= 0.8 m3
Weight of aggregate per meter cube = 0.8 X 1450(bulk density) =1160 kg Volume of aggregate for one cube = 0.003375 X 4/(1+4) = 0.0027 m3 Weight of aggregate for one cube = 0.0027 X 1450 = 3.915 kg
Water cement ratio = 0.36 c. Weight of water = 288 X [1/0.36] = 800 kg Weight of water in one cube = 0.972 X (1/0.36) = 2.7kg
Density of concrete = [weight of [cement +sand +aggregate +water]] per meter cube
=[288+1160+800] = 2248 kg/m3
Weight of concrete for one cube = 2248 X 0.003375 = 7.980 kg
- 0.15% of polypropylene fibre =7.980X 0.0015 = 0.01197 kg
- Volume of cement for one meter cube = 1/ (1+4)= 0.2 m3 Weight of cement per meter cube = 0.2 X 1440(bulk density)= 288 kg Volume of cement for one cube = 0.003375/(1+4) = 0.000675 m3
- Weight of polypropylene fibre:
-
- 0.2% of polypropylene fibre =7.980X 0.002= 0.01596 kg
- 0.25% of polypropylene fibre =7.980 X 0.0025 = 0.01995 kg
- Calculation for volume of cube:
- CURING:
- BATCHING:
The specimens were allowed to remain in iron mould for 24 hours under ambient condition. After that, these were remoulded with care so that no edges were broken and were placed in curing tank at the ambient temperature for curing. The ambient temperature for curing was 27+2 degree calicoes or 27-2 degree calicoes.
-
- SLUMP CONE TEST:
6. TESTING OF SPECIMEN
Fill the cone with concrete in three layer and tamper 25 blows evenly in each layer with 5/8 diameter and 24 long hemisphere steel rod. Remove the excess concrete from top of the cone, using tampering rod, clean overflow from base of cone. Lift the cone vertically with slow and even motion. Lay a straight edge across the top of the slump cone. Measure the amount of slump in the inches from the bottom of straight edges to top of slump concrete at a point over original centre of base. Discrete concrete and do not use in any other tests.
- COMPRESSIVE TEST:
Compressive strength or compression strength is the capacity of a material or structure to withstand loads tending to reduce size, as opposed to tensile strength, which withstands loads tending to elongate. In other words, compressive strength resists compression (being pushed together), whereas tensile strength resists tension (being pulled apart). In the study of strength of materials, tensile strength, compressive strength, and shear strength can be analyzed independently. Some materials fracture at their compressive strength limit; others deform irreversibly, so a given amount of deformation may be considered as the limit for compressive load. Compressive strength is a key value for design of structures.
The specimen after a fixed curing period of 7 days, 14 days and 28 days were tested for compressive strength
2000 KN compressive testing machine (UTM). The specimen is placed on bearing surface of the testing machine and compressive load was applied on opposite face axially and slowly
- PERMEABILITY TEST:
- SLUMP CONE TEST:
The property of the concrete which permits water (fluids) to percolate through its continuously connected voids is called its permeability.
- We check the permeability of plain pervious concrete cube. 1000 ml water which is passed through the voids of the plain pervious concrete cube and the water is retained to another pan that stored water measures it is 860 ml.
- The permeability of 0.15% of polypropylene fibre mixed pervious concrete cube. 1000 ml water which is passed through the voids of the polypropylene fibre mixed pervious concrete cube and the water is retained to another pan that stored water measure it is 900 ml.
- The permeability of 0.2% of polypropylene fibre mixed pervious concrete cube. 1000 ml water which is passed through the voids of the polypropylene fibre mixed pervious concrete cube and the water is retained to another pan that stored water measure it is 920 ml.
- The permeability of 0.25% of polypropylene fibre mixed pervious concrete cube. 1000 ml water which is passed through the voids of the polypropylene fibre mixed pervious concrete cube and the water is retained to another pan that stored water measure it is 940 ml.
- RESULTS Results for M20 Grade Pervious Concrete in Compressive Test
-
- PORTLAND CEMENT CONCRETE:
For 7 days:
Cubes Loads (KN) Load (N) S tr e ss = ^^(N/mm2) Areav 1 255 255000 10.79 N/mm2 2 250 250000 3 260 260000 For 14 days:
Table no.5
Cubes Loads (KN) Load (N) S tre ss = ^^(N/mm2) Arav 7
1 310 310000 11.57 N/mm2 2 300 300000 3 305 305000 For 28 days:
Table no.6
Cubes Loads (KN) Load (N) S tr e ss = i^(N/mm2) Areav
1 315 315000 13.97 N/mm2 2 310 310000 3 318 318000 Table no.7
- USING POLYPROPYLENE FIBRE IN CONCRETE (0.2%):
- PORTLAND CEMENT CONCRETE:
For 7 days:
Cubes Loads (KN) Load (N) S tr e ss = ^^(N/mm2) Areav 1 240 240000 10.85 N/mm2 2 249 249000 3 244 244000 For 28 days:
Table no. 8
Cubes Loads (KN) Load(N) S t r e s s = ^|^(N/mm2) 1 283 283000 12.34 N/mm2 2 275 275000 3 279 279000 Table no. 13
7.1. RATE ANALYSIS
-
- FOR 1 CUBE OF PERVIOUS CONCRETE:
Weight of cement for one cube = volume X bulk density = 0.000675 X 1440 = 0.972 kg. Volume of aggregate for one cube = 0.003375 X 4/(1+4) = 0.0027 m3.
Sr.No MATERIALS QTY. UNIT RATE AMOUNT 1 CEMENT 0.972 KG 6.6/KG 6.5 Rs 2 AGGREGATE 0.0027 M3 660M3 2 Rs TOTAL 8.5 Rs Table No. 14
- FOR 1 CUBE WITH POLYPROPYLENE FIBRE 0.15%:
- FOR 1 CUBE OF PERVIOUS CONCRETE:
0.15% of polypropylene fibre = 7.980X 0.0015 = 0.01197 kg.
Sr.No MATERIALS QTY. UNIT RATE AMOUNT 1 CEMENT 0.972 KG 6.6/KG 6.5 Rs 2 AGGREGATE 0.0027 M3 660M3 2 Rs 3 FIBRE 0.01197 KG 380 Rs 4.5 Rs TOTAL 13 Rs Table No. 15
7.3 FOR 1 CUBE WITH POLYPROPYLENE FIBRE 0.2%:
0.2% of polypropylene fibre = 7.980X 0.002= 0.01596 kg
Sr.No MATERIALS QTY. UNIT RATE AMOUNT 1 CEMENT 0.972 KG 6.6/KG 6.5 Rs 2 AGGREGATE 0.0027 M3 660M3 2 Rs 3 FIBRE 0.01596 KG 380 Rs 6 Rs TOTAL 14 Rs
Table No. 16
7.4 FOR 1 CUBE WITH POLYPROPYLENE FIBRE 0.25%:
0.25% of polypropylene fibre = 7.980 X 0.0025 = 0.01995 kg
Sr.No MATERIALS QTY. UNIT RATE AMOUNT 1 CEMENT 0.972 KG 6.6/KG 6.5 Rs 2 AGGREGATE 0.0027 M3 660M3 2 Rs 3 FIBRE 0.01995 KG 380 Rs 7.5 Rs TOTAL 16 Rs Table No. 17
-
- COMPRESSIVE TEST (CUBE) OF M20:
-
- CONCLUSIONS
The test carried out at 7 days, 14 days and 28 day, the comparison is made between the plain pervious concrete and polypropylene fibre mixed pervious concrete.
- The compressive strength of polypropylene fibre mixed pervious concrete is increased as comparison to the plain pervious concrete.
- When we used the polypropylene fibre in pervious concrete in various proportion 0.15%, 0.2% and 0.25% of volume of concrete the result obtained by the compressive strength of polypropylene fibre up to 0.2% of used result get increased.
-
- PERMEABILITY TEST OF M20:
- PLAIN PERVIOUS CONCRETE:
1000 ml water which is passed through the voids of the plain pervious concrete cube and the water is retained to another pan that stored water measures it is 860 ml.
- POLYPROPYLENE FIBRE MIXED PERVIOUS CONCRETE:
1000 ml water which is passed through the voids of the polypropylene fibre mixed plain pervious concrete cube and the water is retained to another pan that stored water measures it is 970 ml.
- The permeability of polypropylene fibre mixed pervious concrete is increased as compared to the plain pervious concrete.
- The 0.25% polypropylene fibre mixed pervious concrete is compressive strength is less but the permeability is more than 0.2% polypropylene fibre mixed pervious concrete.
- The strength of pervious concrete is increased when fibre used in 0.2% more than of its used the strength decreased. So, we conclude that the ratio of fibre used as less than 0.2%.
- PLAIN PERVIOUS CONCRETE:
- PERMEABILITY TEST OF M20:
-
- REFERENCES
- RESULTS Results for M20 Grade Pervious Concrete in Compressive Test
K. R, Julius Walter. A.G, M. Murugalingam (Department Of Civil Engineering, Loyola Institute Of Technology).