
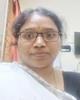
- Open Access
- [post-views]
- Authors : J. Jhansi , P.V.S. Lakshmi Narayana , S Shanti , Bhomik
- Paper ID : IJERTV10IS050475
- Volume & Issue : Volume 10, Issue 05 (May 2021)
- Published (First Online): 19-06-2021
- ISSN (Online) : 2278-0181
- Publisher Name : IJERT
- License:
This work is licensed under a Creative Commons Attribution 4.0 International License
Erosion Resistant Coatings on Martensitic Stainless Steels
-
Jhansi, Bhomik, P.V.S. Lakshmi Narayana, S. Santh
Mahatma Gandhi Institute of Technology, Hyderabad, India
Abstract.:- Solid particle erosion has been recognized as a serious problem in various engineering applications including pipelines, valves handling gases, hydraulic systems, aerospace components and liquid impellers. Power station boiler valves and other parts of coal fired plants are subjected to frequent degradation by erosion. The presence of such erosive environments suggests the application of harder and wear resistant coatings that protects the base material. Thermal spray processes are now widely used to protect against wear and corrosion but also against heat (thermal barrier coating) and for functional purposes. In the present study, the Plasma spray process and Detonation Gun Spray process are used for coating 86WC-10Co-4Cr and Detonation Gun Spray process for coating 75Cr3C2-25NiCr on Martensitic Stainless Steel substrate (0.07C-0.79Si-0.67Mn-13.95Cr-3.79Ni-0.42Mo-80.11Fe). Air-jet erosion tester is used to carry out the erosion test at a velocity of 60m/s at 90° impact angle using silica as an erodent. In this study the detonation gun spray process has exhibited higher erosion resistance compared to that of plasma spray process on martensitic stainless steel. It is observed that hard phases provide protection against low angle impact and metallic phases act tough, for high angle erosion.
Keywords: Solid Particle Erosion, Wear Resistant Coatings, Martensitic Stainless Steel, Plasma Spray Process, Detonation Gun Spray Process.
-
INTRODUCTION
Erosive wear is the removal of material from a surface due to mechanical interaction between the surface and a fluid, or impinging liquid or solid particles or liquid + solid particles is a serious problem in many engineering applications [1]. Although it is only a surface phenomenon, it can cause structural failure directly or as a part of combined effects (for example erosive wear with corrosion or fatigue etc). Erosion is generally seen in subsea gate valves and steam bath surfaces (steam turbine blades) in thermal power plants. Power station boiler valves and other variety parts of coal-fired plants are subjected to frequent degradation by erosion problems [2]. The presence of such erosive environments suggests the application of harder and wear resistant coatings that protects the base material [3]. In the case of hydro- turbines, cavitation erosion promotes formation of cavities or pits at the surface and modifies the hydraulic profile of the components [4].
Research studies have generated knowledge for the improvement of new structural materials and coatings capable of withstanding erosive conditions. However the presence of erosive environments suggests that the application of harder, wear- resistant coatings will perform better [5]. Martensitic Stainless Steels are commonly adopted for regular ends, such as in the automotive industry [6], but may also be used in the cutting-edge design of complex structures, such as nuclear reactors [7] and power plants [8]. Cermet coatings, mainly carbide type coatings (WC-Co-Cr and Cr3C2-NiCr) have shown excellent performance in different industrial areas. These coatings are composed of carbide particles reinforcing a metal matrix, combining the properties of ceramic-carbide type materials of high hardness and toughness and ductility of metals. Cermets based on WC are used in applications working at a relatively low temperatures (<500oC) and in non-corrosive environments. The Cr3C2- NiCr formulations are used in aggressive atmospheres and/or high temperature (~900oC) conditions. These coatings are industrially produced by using thermal spray processes such as detonation and plasma coating technologies. These methods are now widely used to spray coatings against, wear and corrosion but also against heat (thermal barrier coatings) and for functional purposes [9]. The choice of the deposition process depends strongly on the expected coating properties for the application and coating deposition cost. Coating properties are determined by the type of coating material, the deposition process and the set of parameters used [10].
The basic objective of this current work is to study the erosion resistant coatings behavior on Martensitic Stainless Steel using detonation gun spray and plasma spray processes. The thickness of coating materials (WC-Co-Cr and Cr3C2-NiCr) obtained is 200 to 400µm. Application of above materials for surface coatings on the Martensitic Stainless Steel substrate, gives very different, complex microstructures composed of carbides, metallic phases and oxides, which will increase the hardness and performance of these coated substrates under erosive environments.
-
MATERIALS AND METHODS
-
-
Initial microstructure:
The chemical composition of the substrate is determined by Spectroscopic Analysis and is given in Table I.
Table 1: Chemical composition, %Wt of substrate material
Elements
Chemical composition, %Wt
C
0.075
Si
0.79
Mn
0.67
P
0.009
S
0.012
Cr
13.95
Ni
3.79
B
0.00012
Cu
0.156
Mo
0.42
Fe
80.11
The Martensitic Stainless Steel (MSS) samples of dimensions 30x30x12 mm thick are prepared by cutting and machining. To examine the metal surface properly, the surface should be polished to high degree of reflectivity. After polishing, etching is done with picral (picric acid 5g, ethanol-100cc). The morphology of martensite observed through optical microscope is lathe martensite, which has a shape of a strip. A number of lathes a parallel fashion more or less completely filling austenite are shown in the Fig. 1.
Fig. 1: Optical Microstructure of Substrate Material at 100X magnification
-
Coating Materials
The two coating materials used on MSS substrate are WC-Co-Cr and Cr3C2-NiCr and the coating powder characteristics are given in Table 2. The microstructures of the coatings are characterized using the Metallurgical Microscope and are shown in Fig.
-
The microstructure of DG spray WC-Co-Cr consists of WC grains exhibiting straight edges and sharp angles embedded in a cobalt matrix.
Table 2: Coating Powder Characteristics
Powder Characteristics
Particle Size [µm]
4.5 µm
Particle Shape
Spherical
The white area in the images (Fig. 2a) consists of WC particles and the dark gray area consists of pure (Co-Cr) binder[11]. The microstructure of DG spray Cr3C2-NiCr coating shows a dense skeletal network of fine chromium carbide (Cr3C2) and chromium oxide (Cr2O3) bound within the ductile matrix [12]. The white phases correspond to metallic bonding matrix, dark phases correspond to oxides and gray phases correspond to carbides of rounded and flattened aspect.
Fig. 2: Optical Microstructures of (a) 86WC-10Co-4Cr coating (b) 75Cr3C2- 25NiCr coating
Spectroscopic Analysis is done in order to find out the chemical composition of coatings along with substrate material and is shown in Table 3.
Table 3: Chemical composition of Coating Materials
Coating Material
Composition
WC-Co-Cr
86WC-10Co-4Cr
Cr3C2-NiCr
75Cr3C2-25NiCr
-
-
Coating Processes
The two coating methods used in the current research work are Detonation Gun Spray Process and Plasma Spray Process for coating 86WC-10Co-4Cr and 75Cr3C2-25NiCr coating materials on Martensitic Stainless Steel substrate.
-
Detonation Gun Spray Process
The Martensitic Stainless Steel samples are grit blasted with Al2O3 grits of size 150 mm at a pressure of 3 to 3.5 bars at room temperature before coating. In Detonation Gun spray (DG) process, the reaction gases (acetylene and oxygen), a carrier gas and powdered coating material (86WC-10Co-4Cr and 75Cr3C2-25NiCr) are introduced into the combustion chamber, mixed and ignited by a spark from a spark plug as shown in Fig.3. The powder material is heated by detonation energy release, forming high-pressure ultra sonic wave, which propagates hot gas stream and accelerates the powder particles up to 900 m/s and hits the surface of the substrate. After each combustion process (detonation) a flushing gas (Ar, N2) cleans the combustion chamber before a new cycle starts. There are about 4 to 8 detonations per second. The impact of high kinetic energy of the hot powder particles, with the substrate result in a buildup of a very dense and strong coating [13,14].
Fig. 3: Detonation Gun Spray Process
The spraying conditions adopted in this present work are given in Table 4.
Table 4: Spraying Parameters adopted for DG Process
Parameters
Values
Spraying Atmosphere
Air
Spray Spot Diameter
25 mm
Spraying Distance
(Al2O3)
(Carbides)
200 mm
165 mm
Thickness/Shot
5-6 µm
Shots/sec
3 shots
During the coating process, feed rate of both gaseous and powder material, will alter the coating properties such as hardness, thickness, porosity, bond strength etc. The feed rate of gases adopted, are given in Table 5.
Table 5: Feed Rate of gases adopted
Materials
Pressure bar (C2H2, O2, N2)
Feed rate of gases [SLPH] (C2H2, O2, N2)
Cr3C2-NiCr
1, 2, 3
2640, 2320, 800
WC-Co-Cr
1, 2, 3
2960, 2400, 720
-
Plasma Spray Process
Air plasma spray process (APS) is used for coating 86WC-10Co-4Cr on Martensitic Stainless Steel substrate. Before spraying WC-Co-Cr powder with plasma spray process on the substrate (Martensitic stainless steel), is sand blasted at 5.17 bars. The plasma generated for plasma spraying usually incorporates one or more mixture of Ar, He, N2 and H2 gases. The start of an electric arc, with high frequency spark, is the energy source for plasma spraying. The arc burns between a cylindrical tungsten cathode and radial, concentric copper anode, which is also nozzle. Into this nozzle the arc gases Ar, He or N2 mixtures are fed. When these gases pass through the arc, the interaction between electrons from cathodic source and gas molecules/atoms, causing dissociation or ionization of the gas, is creating plasma state. As the unstable plasma recombines back to the gaseous state and gets cooled, thermal energy is released. Point of recombination temperature can be 6600oC to 15000oC. The coating material (86WC-10Co-4Cr) is injected into the gas, is melted and sprayed towards the substrate. The schematic diagram of the APS process is shown in Fig. 4 and the spray parameters are given in Table 6.
Fig. 4: Schematic view of plasma spray process [15]
-
-
Characterization Techniques
In the present work, micro hardness and Porosity are employed to evaluate both strength and porosity details of substrate and coating.
Table 6: Spraying conditions adopted for plasma spray process
Parameter
Value
Spraying Atmosphere
Air
Coating Thickness
275-300 µm
Feed Rate (powder)
44 g/min
Passes
4
Power (kW)max
80
Spraying Distance
135-165 mm
-
Hardness and Porosity
-
The hardness of the substrate and the coating materials is determined with Vickers Hardness Tester. In this test, the instrument has a square-based diamond pyramid indenter with an included angle of 136° between opposite faces. 300 gm load for 10 sec is applied to know the micro hardness of the coatings. Macro hardness of the substrate is evaluated with Vickers Hardness Tester, at a load of 30 kgf for 10 sec, then unloaded. Porosity measurements of coated substances are carried out, using optical microscope, fitted with image analyzer, on the sectioned and polished surface of coatings.
2.5 Erosion Test
An Air Jet Erosion Tester (Fig. 5) is used for testing the coated and uncoated samples. In this the erodent is fed by particle feeder, at a controlled rate, into mixing chamber and constant flow rate of air with particles are maintained by connecting the compressor to the mixing chamber. The particles further accelerated with air stream through a stainless steel converging nozzle and then finally hit the sample kept fixed at sample holder. 10 cm distance is kept between the sample to be tested and nozzle,
where nozzle outlet diameter is 10 mm. The feed rate is maintained at 45 g/min. The erosion test is carried out as in the steps given below.
Fig. 5: Schematic diagram of Air Jet Erosion Test (a) Sand Injection System (b) Details of Erosion Chamber
The sample is first cleaned in acetone, dried and then weighed using an electron balance having a resolution of 0.01 mg. Sample is fixed to the sample holder and eroded with SiO2 particles, at the pre determined particle feed rate, impact velocity and impact angle for about 10 minutes. The sample is then removed, cleaned in acetone and dried, weighed to determine the weight loss. The time allowed for each sample to erode is two hours in this present work. Erosion rate is determined by weight loss to that of mass of erodent. The erosion test conditions used for the present study are given in table 7.
Table 7: Erosion Test Conditions
Erosion Conditions |
|
Erodent Material |
Silica |
Particle Velocity [m/s] |
60 |
Feed Rate [g/min] |
45.33 |
Impact Angle [°] |
90 |
Particle Shape |
Round and Angular |
Nozzle distance [mm] |
10 |
Particle Size [µm] |
250-350 |
-
RESULTS AND DISCUSSION
-
Hardness and Porosity
The macro hardness value of substrate is 315 HV30kg and the micro hardness values of coating materials are given in Table 8.
Table 8: Hardness of coatings
Coating Material
Micro hardness [HV0.3kg]
86WC-10Co-4Cr
1075
75Cr3C2-25NiCr
961
The porosity values o coated samples are found out using microprobe analyzer fitted to optical microscope. It is observed from the Table 9 and Figure 6 that the porosity is low (<1%) for 86WC-10Co-4Cr and Cr3C2-NiCr coated samples, using DG technique and high (>4.8%) using APS technique. The porosity is low using DG technique because the kinetic energy of the powder particles is high enough to get deformed, so as to join with one another without pores left between them. The comparison of DG technique with APS technique is done based on temperature and velocity. Porosity of APS coatings is more. As, more time is allowed for the reaction of O2 contained at the droplet surface in APS process compared to DG technique.
Table 9: Porosity of coatings on the substrate
Substrate
Coating process
Coating Material
Porosity (%)
Martensitic stainless steel
Detonation Gun Spray Process
86WC-10Co-4Cr
0.41
75Cr3C2-25NiCr
0.46
Plasma Spray Process
86WC-10Co-4Cr
4.80
Fig. 6: Porosity of Coated Substrates
-
Erosion Test
-
Step Wise Erosion
Air-sand erosion tester at normal impact carries out erosion test for the coated and uncoated substrates for one hour each at an interval of 10 minutes. As shown in Fig. 9(a), in first four intervals the weight loss for Martensitic Stainless Steel is less and almost uniform. Because initiation and crack propagation has been delayed due to its toughness, is due to its low carbon percentage. Then stepwise increment of weight loss and in the last interval, drastic increase of it is observed, where crack propagation is faster and material removal takes place by formation of a lip or platelet and its subsequent fracture.
In Fig. 9(b), comparison of 86WC-10Co-4Cr coating on Martensitic Stainless Steel using both DG and APS processes is done. It is observed that for DG process, there is a drastic increase in erosion from first interval to second interval, due to the dominant nature of brittle erosion. It is due to fast initiation and crack propagation, the WC particles were pulled out from Co-Cr binder phase where the bonding between the splats is weak. Then in the next interval it is observed that very less erosion has taken place due to good mechanical bonding of coating with the substrate. Whereas in Plasma sprayed WC on Martensitic Stainless Steel, the erosion increases steadily up to third interval is due to subsurface damage of plasma sprayed splats. At fourth and fifth interval, erosion decreases and at sixth interval, it increases drastically due to uprooting of WC particles, more amount of porosity (Table 9). And further decrease in erosion in last intervals.
The comparison of 86WC-10Co-4Cr and 75Cr3C2-25NiCr coatings on Martensitic Stainless Steel using DG process is shown in Fig. 9(c).It is observed that erosion increases drastically in the second interval for 75Cr3C2-25NiCr coating, due to dominant brittle erosion by fracturing of metal carbide particles or pullout of them from the distorted binder. At third and fourth intervals, the erosion decreases, due to ductile erosion of Ni-Cr binder phase. The sudden increase in the erosion at the fifth interval is due to pullout of particles and voids formation. Then there is slight increase in the erosion at sixth interval is may be due to better adhesion between the splats.
-
Cumulative Weight Loss
The cumulative weight loss of all the samples with time is given in Table 10. The erosion behavior of Detonation gun sprayed and plasma sprayed WC-Co-Cr material on martensitic stainless steel, are shown in the fig. 7(a). DG coating shows much more erosion resistance when compared to plasma spraying because DG gun coating is sprayed at high velocity. The coating
has low porosity, good bond strength and adhesion when compared to plasma spray coating.
Table 10 Cumulative weight loss of coated and uncoated samples for test duration of one hour.
Substrate
Tech niqu e
Coating material
Cumulative Weight Loss [gm]
10min
20min
30min
40 min
50 min
60 min
Martensitic stainless steel
–
Uncoated
0.0013
0.0018
0.0022
0.0026
0.0030
0.0042
DG
86WC-
10Co-4Cr
0.0196
0.0897
0.0911
0.0952
0.0958
0.0987
75Cr3C2-
25NiCr
0.0019
0.0240
0.0275
0.0283
0.0416
0.0428
APS
86WC-
10Co-4Cr
0.0016
0.0037
0.0192
0.0242
0.0322
0.1222
Fig. 7(a) Cumulative weight loss of 86WC-10Co-4Cr coating on martensitic stainless steel specimen using APS and DG processes
Fig. 7 (b) Cumulative weight loss of different coating materials using DG spray process on martensitic stainless steel specimen
Even the hot corrosion studies of Cr3C2NiCr coating with DG spray process on Ni and Fe based superalloys have shown better erosion resistance due to low porosity, flat splat microstructures and uniform fine grains[16]. In Fig. 7(b) it is observed that, erosion rate is more for brittle coating material (86WC-10Co-4Cr) and less for comparatively ductile coating material (75Cr3C2-25NiCr) because, the effect of impact angle at 90° is different for ductile and brittle materials [17&18]. At this angle, erosion is maximum for brittle materials and minimum for ductile materials and the same results are justified with 75Cr3C2-25NiCr. The Fig. 7(b) shows that Cr3C2-NiCr coating is more erosion resistant compared to that of WC-Co-Cr coating and so is the reason Cr3C2-NiCr coating is preferable on Martensitic Stainless Steel. It is observed, from the graph, that there is almost sudden increase at second interval of each graph, because both the coating materials, including the substrate are brittle in nature. A brittle fracture in metals is characterized by a fast rate of crack propagation with very little of plastic deformation. Here the crack is unstable, that is once the crack nucleates the propagation continues spontaneously without an increase in magnitude of the applied stress.
-
-
-
. CONCLUSIONS
On Martensitic Stainless Steel, 86WC-10Co-4Cr material is coated using both DG and APS processes, 75Cr3C2-25NiCr material is coated using DG process and the following conclusions are drawn.
-
DG process has shown better erosion resistance compared to the APS process. This is due to high velocity of the powder particles resulted in good mechanical bonding of the coated material with the substrate and has shown low porosity when compared to APS process.
-
75Cr3C2-25NiCr coating using DG process exhibit improved erosion resistant behavior compared to 86WC-10Co-4Cr coating on martensitic steel substrate.
REFERENCES
-
Friction, Lubrication, Wear Technology, ASM Handbook, Vol. 18.
-
P.Basu, C.Kefa, L.Jestin. (2000) Erosion Prevention in Boilers. In: Boilers and Burners. Mechanical Engineering Series. Springer, Newyork, NY
-
Thermal Spray Coating Processes, ASM Handbook, Vol. 5, urface Engineering
-
Fauchais, Pierre & Vardelle, Armelle. (2012). Thermal Sprayed Coatings Used Against Corrosion and Corrosive Wear. 10.5772/34448
-
J.F. Santaa, J.A. Blanco, J.E. Giraldo , A. Toroa, Cavitation erosion of martensitic and austenitic stainless steel welded coatings, Wear 271 (2011),pp 14451453.
-
I. Fagoaga, J.L. Viviente, P. Gavin, J.M. Bronte, J. Garcia and J.A. Tagle, Multilayer coatings by continuous detonation system spray technique, Thin Solid Films, Vol.317, pp. 259-265, 1998.
-
H. Mohrbacher, Martensitic automotive steel sheet-fundamentals and metallurgical optimization strategies. Advanced Materials Research. Trans. Tech. Publ. 2015, 1063, 130142.
-
R. Klueh, AT Nelson, Ferritic/martensitic steels for next-generation reactors. J. Nucl. Mater. 2007, 371, 3752.
-
F.Abe, Precipitate design for creep strengthening of 9% Cr tempered martensitic steel for ultra-supercritical power plants. Sci. Technol. Adv. Mater. 2008, 9, 013002.
-
P.P. Psyllaki, M. Jeandin and D.L. Pantelis, Microstructure and wear mechanism of thermal sprayed alumina coatings, Materials Letters, vol. 47, pp. 77-82, 2001.
-
Varol Özkavak, H. ahin, Saraç, M. F. Alkan, Z.
-
Comparison of wear properties of HVOF sprayed WC-Co and WC-CoCr coatings on Al alloys , 2019, Materials Research Express, Vol-6,Issue- 9, pp096554, 2019/07/12 , ISSN: 2053-1591
-
Subhash Kamal, R. Jayaganthan, S. Prakash,High temperature oxidation studies of detonation-gun-sprayed Cr3C2NiCr coating on Fe- and Ni-based superalloys in air under cyclic condition at 900°C,Journal of Alloys and Compounds, Volume 472, Issues 12,2009, pp 378-389, ISSN 0925-8388.
-
P. Fauchais and A. Vardelle, Thermal Sprayed Coatings Used Against Corrosionand Corrosive Wear , SPCTS, UMR 7315, University of Limoges,
France, March 2012
-
Rointan and F. Bunshah, Deposition technologies, properties and applications, Noyes Publications, pp. 77-81 and 92-102, 2001
-
Detonation thermal spray coating process, available at www.gordonengland.co.uk/xds.html.
-
Subhash Kamal, R. Jayaganthan, S. Prakash, Sanjay Kumar,Hot corrosion behavior of detonation gun sprayed Cr3C2NiCr coatings on Ni and Fe- based superalloys in Na2SO460% V2O5 environment at 900°C, Journal of Alloys and Compounds,Vol 463, Issues 12,2008,pp 358-372,ISSN 0925-8388.
-
M Hutchings, Tribology: Friction and Wear of Engineering Materials, London, Edward Arnold; 1992
-
A.P. Harsha, Deepak Kumar Bhaskar, Solid Particle Erosion Behavior of Ferrous and Non-ferrous Materials and Correlation of Erosion Data with Erosion Models, Materials and Design 2008; 29, pp1745-1754,2008.
-