
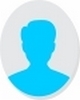
- Open Access
- Authors : Bala Krishna Mudavath, G Praveen Kumar
- Paper ID : IJERTV14IS020048
- Volume & Issue : Volume 14, Issue 2 (February 2025)
- Published (First Online): 22-02-2025
- ISSN (Online) : 2278-0181
- Publisher Name : IJERT
- License:
This work is licensed under a Creative Commons Attribution 4.0 International License
Evaluating the Effects of High Hydrogen Stick Welding on Weld Integrity and Joint Efficiency
Bala Krishna Mudavath
Cyient Hyderabad, Telangana, India
G Praveen Kumar
Cyient Hyderabad, Telangana, India
Abstract -Shielded Metal Arc Welding (SMAW) is a popular welding method in small-scale industries and for repair tasks, appreciated for its affordability, flexibility, portability, and versatility. This technique utilizes a consumable electrode encased in flux coating, which, upon burning, produces slag and shield gases to protect the weld from atmospheric contamination. Various parameters influence the quality, productivity, and cost of SMAW, and the correct selection of these parameters enhances weld strength. This paper investigates the implications of using high hydrogen electrodes, achieved by exposing the electrodes to the atmosphere to increase hydrogen levels. Hydrogen atoms, being very small and mobile, can easily escape the weld zone and collect along microstructural discontinuities, eventually causing stresses that lead to cracks and other defects. By conducting welds with both high hydrogen and normal/dry electrodes, and subjecting the resulting joints to non-destructive (NDT) and destructive testing (DT), the outcomes are analyzed and compared.
Keywords SMAW; electrode; NDT; DT; welding (key words)
-
INTRODUCTION
Shielded Metal Arc Welding (SMAW) is a type of arc welding that utilizes a consumable metal electrode with a flux coating to protect the weld. As the electrode melts during welding, the flux releases vapors that safeguard the weld from contamination by the surrounding atmosphere. This welding process is commonly referred to as "stick welding" due to the use of the metal electrode. SMAW offers a range of electrodes in different sizes and types, which are selected based on the specific application and other variables. The size and type of the electrode influence the arc voltage, which typically ranges from 16 to 40 volts. Additionally, the amperage required can range from 20 amps to 550 amps. Depending on the electrode, either alternating current or direct current can be used. Generally, larger electrodes are preferred for higher deposition rates and require higher currents.
SMAW Welding Techniques For a clean and smooth weld, its essential to choose the right type of steel that suits SMAW welding. Steel within the AISI-SAE 1015 to 1025 range is ideal, as it has less than 0.1% silica and less than 0.035% sulfur content. Steels with alloy compositions exceeding these limits may be prone to cracking. After selecting the appropriate steel, ensure the edges are properly cleaned to achieve a neat weld. This includes removing rust, paint, moisture, oils, and scale. If
cleaning the joint is not possible, use an E6010 or E6011 electrode with a slower travel speed to ensure gas bubbles escape before the puddle solidifies.
Basic SMAW Welding Quality Tips Several quality issues can occur during the SMAW welding process. These include porosity, which results from trapped gas in the weld that doesn't escape before the metal solidifies, weakening the weld due to gas bubbles. Splatter can happen from low voltage or high amperage, while poor fusion may occur from dirty metal or insufficient power. Shallow penetration can be caused by fast travel speed, low current, or an excessively large electrode. Cracking can result from any of these issues, as well as from improper weld movement and using unsuitable metals. For metals that are not ideal, use a slower travel speed to keep the puddle molten, allowing gases to escape and creating a strong weld. When welding thinner stock (10-18 gauge), position the work at a 45-75-degree angle for faster travel, ensuring the joint doesnt become too wide to avoid burn-through. For thicker plates (3/16 or heavier), weld flat to achieve optimal electrode placement.
The Industrial Applications of SMAW SMAW is widely used across various industries due to its versatility and portability. One of the key advantages is its ability to be applied in diverse environments with minimal setup time and effort. The simplicity of SMAW equipment, compared to other welding methods, means there are fewer chances for malfunction or breakdown. For instance, the tubular electrode in FCAW can become kinked and fail to feed properly, leading to welding defects. Additionally, many welders are trained in SMAW, making it easier to find skilled professionals. STI Group proudly provides high-quality SMAW services alongside many other welding techniques.
-
Selection of Material
-
Selection of Welding process
-
Edge preparation
-
Welding process
-
Testing
-
-
METHODOLOGY
Selection of Material – Mild steel (MS) Plates of Dimensions 150mmx100mmx6mm of 4 pieces.
Electrode: An electrode is a conductive material, either metal or composite, that facilitates the flow of electric current and generates the arc required for welding. It also acts as the filler material, melting and merging with the workpieces to form a strong connection once it cools and solidifies. Electrodes are classified into two categories: consumable and non- consumable.
Factors for selecting electrode:
-
Base metal properties
-
Tensile Strength
-
Welding Current
-
Base metal thickness Shape and Joint fit up
-
Welding position
-
Specification and service condition
-
Environmental Job Conditions.
In this process we have selected Flux coated electrode of
E7018 (Consumable electrode)
Consumable Electrode: A consumable electrode is an electrode used in welding that melts and integrates into the weld joint during the process. As it melts, it generates the heat required to create the weld and supplies the filler material that joins the workpieces. This melting action allows the electrode to release molten metal into the joint, which solidifies as it cools, forming the weld bead.
Electrode of E7018:
E – Electrode
60 – Load (Pound-force per square inch) 1 – Position Capabilities
3 – Electro Flux
For this research process again, electrodes are classified into two types:
-
Dry or Normal Electrode
-
High Hydrogen Electrode
Dry or Normal Electrode: To make electrode as dry, keep the electrode in laboratory oven for 10 to 15 minutes until the temperature of oven Reaches more than 100 degree Celsius. This electrode is considered a dry electrode.
Initially temperature of laboratory oven is 31 degree Celsius and final temperature is 104 degree Celsius.
High Hydrogen Electrode: An Electrode is placed in Atmosphere for 1 hour and hydrogen gas is sprayed throughout the electrode and it is considered as High Hydrogen electrode.
In this project we are performing weld joints by using E7018 Electrodes of different sizes 2.5mm, 3.15mm, 4mm. As the Electrode size varies the current supply also varies.
E7018 electrode
Layer
Diameter
Range
Root Layer
2.5mm
50 Range
Second Layer
3.15mm
90 Range
Top Layer
4mm
110Range
SELECTION OF WELDING PROCESS:
Shielded Metal Arc Welding (SMAW) is a popular welding process that uses a consumable electrode coated with flux. As the electrode melts, the flux generates gases that protect the weld from atmospheric contamination. SMAW is valued for its versatility, portability, and low cost, making it ideal for small-scale industries and repair work. The process can be used on a variety of metals, and the electrodes type and size influence the heat and amperage required. While simple to use, it requires skill to avoid issues like porosity, cracking, or improper fusion. SMAW is widely used due to its effectiveness and ease of learning.
EDGE PREPARATION:
Before welding have to perform a groove operation on work pieces by using grinding process. A groove is a specially shaped cut or channel made in the edges of the base materials that are to be welded together. This groove is designed to provide room for the filler material, which comes from the electrode or welding wire, to be added during the welding process. This helps to ensure a strong bond between the two metal pieces. The angle of the "V" typically ranges from 30°
to 60°, with 45° being the most common. Performing V- groove operation on work pieces.
WELDING PROCESS:
It's crucial to make sure that the surfaces you plan to weld are clean and devoid of contaminants like rust, oil, dirt, or paint. Such contaminants can significantly impact the weld quality, leading to weaker bonds and potential defects. By properly preparing the surfaces, you enhance the effectiveness and durability of the weld. Ensure the welding machine is set up correctly by adjusting the output current to match the materials and electrode size being used. Select an electrode with a 2.5 mm diameter and place it in the electrode holder to begin welding the root layer of the workpieces. Secure the workpieces in a butt joint, positioned side by side and aligned for optimal access during welding. Connect one lead from the welding machine (the negative lead for DC welding) to the workpiece to complete the electrical circuit.
While maintaining the arc, guide the electrode along the joint. As the electrode and the workpiece melt, a weld pool will form, with the electrode supplying the filler metal necessary for the weld. The welder needs to keep the electrode at an angle of 15°-20° to the workpiece, while maintaining the right speed and arc length, to ensure good material penetration and fusion. The flux coating on the electrode burns off during welding, creating a gas shield that protects the molten pool from atmospheric contamination and oxidation. As the weld pool cools, it solidifies, forming a metal bond between the base materials. The flux residue, or slag, forms on top of the weld pool.
Once root layer is welded, then select the 3.15mm and 4mm diameter electrode to weld second layer and Top layer respectively. Repeat the above welding operation with both sizes of electrodes. Same welding operation to be performed individually on different work pieces with both Dry or normal electrode and High hydrogen electrode.
TESTING
We have conducted Both Non-destructive testing (NDT) and Destructive testing (DT) to evaluate the results of both joints (Joint welded with dry electrode and high hydrogen electrode)
NON-DESTRUCTIVE TESTING (NDT)
Non-destructive testing (NDT) refers to the techniques used to inspect, test, or evaluate materials, components, or assemblies for any discontinuities or variations in properties without impairing their functionality. After the inspection or test, the part remains usable. In this research, we are conducting several types of non-destructive tests on welding.
-
-
Dye Penetrant NDT (PT)
-
Magnetic Particle NDT (MT) DESTRUCTIVE TESTING (DT)
Destructive testing (DT) involves applying stress to materials, components, or machines to identify their failure point. Throughout the test, the item is subjected to forces that eventually lead to deformation or destruction of the material.
-
Tensile Test
-
Leeb Hardness Test
-
-
DYE PENETRANT TEST:
Definition: Dye penetrant testing (DPT) is a non-destructive method used to identify surface-breaking defects like hairline cracks, surface porosity, leaks in new products, and fatigue cracks. By using a liquid dye, it reveals defects that are otherwise invisible, making them detectable.
Dye Penetrant Test Procedure:
Pre-Cleaning: In this method, the test surface is cleaned to eliminate any dirt particles.
Application of Penetrant: The penetrant is subsequently applied to the surface of the workpieces for testing.
Dwell Time: Penetrant dwell time refers to the duration during which the penetrant remains in contact with the surface of the part being tested.
Excess removal of Penetrant: Use cotton waste to wipe away any excess penetrant from the surface.
Application of Developer: Once the excess penetrant has been removed, a white developer is applied to the sample.
Inspection: Defects are inspected using the Magnifying glass.
Post Cleaning: After the inspection is done, the developer is removed from the surface.
RESULTS OF DYE PENETRANT TEST:
Results of Dry or Normal electrode weld joint NO SIGNNIFICANT DEFECT (NSD) FOUND.
Results of High hydrogen electrode weld joint:
Defects found:
-
LACK OF PENETRATION
-
ROOT POROSITY
-
-
MAGNETIC PARTICLE TEST (NDT):
Definition: Magnetic Particle Inspection (MPI) is an efficient technique used to detect surface and near-surface defects, such as cracks, pores, cold laps, and incomplete sidewall fusion in welds, in magnetic materials. This method employs various techniques to locate these imperfections effectively.
Defects:
-
SPATTERS
Results of High hydrogen electrode weld joint:
Magnetic Particle Test Procedure:
Calibration: It is process to check weather equipment is working properly or not with the help of a bar of rectangular cross section with small holes in it. Now place the Permanent Magnetic Yoke on the rectangular bar for testing and the spray the ferrous powder on it then you can find few defects due to internal holes in rectangular bar.
Pre-Cleaning: The test surface is cleaned to eliminate any dirt particles.
Magnetization: By placing a permanent magnetic yoke on work piece Magnetization is created.
Application of Developer: After the magnetization process, a white developer is applied to the workpieces.
Application of Magnetic powder: Apply the magnetic powder on workpieces.
Defects found:
-
Under cuts
-
-
TENSILE TEST:
Inspection: Defects are examined using a permanent magnetic yoke.
Recording: Record the defects found in the experiment and identify what are the defects found in normal electrode weld joint and high hydrogen weld joint.
Post Cleaning: After the inspection is completed Clean the work pieces.
RESULTS OF MAGNETIC PARTICLE TEST (NDT):
Results of Dry or Normal electrode weld joint
Definition: Secure a material piece at both ends and pull it until it breaks. This test assesses its tensile strength (how strong it is), elongation (how much it can stretch), and tensile modulus (how stiff it is). A universal testing machine is used to perform the tensile test to determine these properties.
Universal Testing Machine (UTM): A UTM is utilized to evaluate the tensile stress and compressive strength of various materials. It derives its name from its capability to conduct numerous standard tests for both ensile and compression properties on materials, components, and structures.
Load Frame: Tensile testing machines can be equipped with load frames that have either single or dual column
configurations, which vary based on their force capacity.
Software: The test software allows operators to set up test methods and generate output results.
Load Cell: A load cell is a type of transducer used to measure the force exerted on a test specimen. Instron load cells are known for their precision, being accurate to within 1/1000 of their capacity.
Grips and Fixtures: There is a variety of specimen grips and fixtures available to securely hold test specimens of various materials, shapes, and sizes.
Strain Measurement: Certain test methods necessitate measuring a specimen's elongation under load. Instron's AVE2 device is capable of detecting changes in specimen length with an accuracy of up to ±1 µm or 0.5% of the reading.
TENSILE TEST PROCEDURE:
-
Position the sample between two fixtures known as "grips" that hold the material securely.
-
Ensure the material has known dimensions, including length and cross-sectional area.
-
Begin to apply weight to the material, with one end gripped and the other end fixed.
-
Gradually increase the weight (referred to as the load or force) while simultaneously measuring the change in length of the sample.
-
Note the readings when the material reaches its breaking point or fails under the load.
Work piece after tensile test:
CALCULATIONS:
Specimen:
Length 185mm Thickness 6mm
DRY/NORMAL ELECTRODE:
Load = 49KN Length = 185mm Thickness = 6 mm Deflection = 21mm Elongation = 198mm
STRESS = Load/Area
= 49x 103 / 185×6
= 44.14 N/mm2 Ans
STRAIN = Change in length – Original Length Original Length
= 198-185 x 100% = 7.02
185
HIGH HYDROGEN ELECTRODE:
Load = 35KN Length = 185mm Thickness = 6 mm Deflection = 11mm Elongation = 190mm
STRESS = Load/Area
= 35x 103 / 185×6
= 31.53 N/mm2 Ans
STRAIN = Change in length – Original Length
Original Length
= 190-185 x 100% = 2.7
185
OBSERVATIONS:
ELONGATION
DEFLECTION
DBREAKING POINT
DRY ELECTRODE
198mm
21mm
49KN
HIGH HYDROGEN
ELECTRODE
190mm
11mm
35KN
-
-
LEEB HARDNESS TEST :
Definition: The Leeb hardness test measures the hardness of materials, usually metals, by assessing the rebound velocity of a small, hard impactor (typically a tungsten carbide ball) when it strikes the material's surface. The hardness value is determined by comparing the impact velocity with the rebound velocity, providing an indication of the material's resistance to deformation.
Hardness: Hardness is a material property that indicates its resistance to deformation, scratching, abrasion, or indentation. This characteristic is crucial in materials science, engineering, and geology to assess how durable or resistant a material is to mechanical wear.
There are two types of method in Leeb Hardness Tester
-
Ultrasonic Contact Impedance
-
Rebound
Rebounded Hardness Tester Procedure:
Firstly, set up the rebounded hardness testers properly. Ensure the test surface is clean and free from contaminants.
Setup of Impact Body: Prepare the impact body, typically a mass with a spherical tungsten carbide tip, and ensure it is properly positioned in the tester.
Acceleration: Accelerate the impact body towards the test surface using spring force, reaching a specified speed.
Impact and Indentation: The impact with the surface creates an indentation due to plastic deformation, resulting in a loss of some of the impact body's initial velocity.
Measuring Velocity: Measure the velocities of the impact body before and after it strikes the surface without physical contact.
Analysis: Compare the impact and rebound velocities to calculate the hardness value, indicating the material's resistance to deformation.
Results of Leeb Hardness test for High hydrogen electrode:
VIII. CONCLUSION:
In this research paper, Shielded Metal Arc Welding (SMAW) was successfully performed on mild steel (MS) plates using both dry electrodes and high hydrogen electrodes (E7018).
Various non-destructive (NDT) and destructive (DT) tests were conducted on weld joints made with normal electrodes and high hydrogen electrodes. The results revealed that weld joints created with high hydrogen electrodes exhibited more defects compared to those made with normal electrodes.
Additionally, the strength of the weld joints using high hydrogen electrodes was found to be weaker than that of the weld joints made with normal electrodes.
. REFERENCES
-
Kumar A and Sundarajan S, Selection of Welding Process Parameters for the 3Process, Vol. 21, No. 8, 2006, pp. 789-793.
-
S. C. Juang and Y. S. Tarng, Process parameter selection for optimizing the weld pool geometry in the ARC welding of stainless steel, Journal of Material Process Technology, Vol. 122, No. 1, 2002, pp. 33-37.
-
Balasubramanian M and Balasubramanain V, Process Parameter Optimization of the Pulsed GTAW of Titanium Alloy, Journal of Material Science and Technology, Vol. 24, No. 3, 2008, pp. 423-426.
-
Senthilkumar, V. Balasubramanian and M. Y. S. Babu, Effect of Pulsed Current GTAW Parameters on Fusion Zone Microstructure of AA6061, International Journal of Metals & Materials, Vol. 13, No. 4, 2007, pp. 345-
351.
-
American Welding Society (AWS) Welding Research Supplement: This supplement presents peer-reviewed research papers on welding procedures, metallurgy, equipment, processes, testing, and quality control
-
K. Shanmugam, A.K. Lakshminarayanan, V. Balasubramanian, Tensile and Impact Properties of Shielded Metal Arc Welded AISI 409M Ferritic Stainless Steel Joints, J. Mater. Sci. Technol, 25 (2009) 181.
-
Y. Liao et al. Effect of rivet arrangement on fatigue performance of electromagnetic riveted joint with 10 mm diameter rivet.
-
Interface characteristics and performance of magnetic pulse welded copper-steel tubes.
-
Effect of continuous high temperature exposure on the adhesive strength of epoxy adhesive, CFRP and adhesively bonded CFRP-aluminum alloy joints.
-
Numerical simulation and experimental study on electromagnetic crimping of aluminum terminal to copper wire strands.