
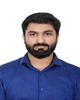
- Open Access
- Authors : Abdul Rahman , T. Malleswari Devi , Mohammed Khaja Moinuddin
- Paper ID : IJERTV11IS050183
- Volume & Issue : Volume 11, Issue 05 (May 2022)
- Published (First Online): 23-05-2022
- ISSN (Online) : 2278-0181
- Publisher Name : IJERT
- License:
This work is licensed under a Creative Commons Attribution 4.0 International License
Evaluation of RC, Composite and RC + Composite Structure under the Seismic Loading – A Comparative Study
1Abdul Rahman, 2T. Malleswari Devi, 3Mohammed Khaja Moinuddin
1M. E student, Department of Civil Engineering, CBIT(A) college, Telangana, Hyderabad, 2Asst.Prof, Department of Civil Engineering, CBIT(A) college, Telangana, Hyderabad, 3PhD Research Scholar, Department of Civil Engineering, IIT-H, Telangana, Hyderabad
Abstract – Constructing high-rise structures in vulnerable land is always a major concern for structural engineers. The failure of many multi-storied and low-rise reinforced cement concrete and masonry buildings due to seismic forces has put structural engineers to look into different methods of construction practices to adopt, coming out from traditional methods to the new evolutionary designs. Since the RCC structure is bulky and has huge weight, composite structure could be the alternative solution to overcome these problems.
To understand the behaviour of composite structure and its response during earthquakes, comparative study is done between conventional special moment resisting frame (SMRF) structure and composite structure. And for the better comparison, five different models of conventional SMRF frame, composite and semi rigid or semi composite structure were modelled and analysed. Further two more models were added in order to come out of different problems in the proposed models.
Modelling and analysis is carried out in ETABS-16. To know at what height composite structures are effective, analysis was done on 3 different storey levels i.e 7, 15 and 30 storeys. The building is presumed to be in critical seismic prone zone i.e Zone IV and soil type as medium soil Type-II. For the dynamic analysis, Response Spectrum Method is used.
Comparative study of all the different Models of same storey level in terms of storey drift, base shear, storey stiffness, maximum displacement, shear force & time period is discussed and shown.
Key Words: Composite structure, RC structure, RC + Composite, Dynamic response, Dynamic Analysis, Comparative study
-
INTRODUCTION
Over the past thirty-forty years, composite construction has been used in the US, UK, Australia and Japan as a cost-effective alternative to traditional structural steel or RC Structures and has become the most common form of floor system for steel framed office buildings.
Compared to high-rise steel structures, composite systems offer more effective and efficient use of materials, a reduction in overall construction time and many other advantages. The use of steel in construction industry is very low in India compared to many developing countries and limiting the use of steel as an alternative construction material where it can be economical is a heavy loss for the Nation.
Nowadays, composite construction is dominating the multi-storey building sector. Its due to the strength & stiffness as well as ductility that can be achieved with the minimum use of construction materials. Compressive and Tensile strengths can be utilised in a highly efficient and light weight design when steel and concrete materials are combined together effectively, as concrete is efficient in compression and the steel in tension. Also the reduction in self-weight reduces the forces in those structural elements which are supported on them, including foundations and also benefits in terms of speedy construction time.
Composite construction was first used in both buildings and bridges in U.S. over a century ago. Steelconcrete composite beams was the earliest form of method in composite construction. A composite tubular column was adopted as they provide permanent and integral formwork for compression member & also reduces construction time and cost.
The application of profiled steel deck slab (Steel sheet & RC slab) was adopted as it works for dual purposes i.e permanent formwork and reinforcement to concrete slab.
1.1 RESEARCH SIGNIFICANCE
-
The Indian Standard Codal provision IS 3935-1966 says Though composite construction is not a very new technique, its importance in structural construction is of recent realization in this country. Thus researchers should also realise the research work on this topic.
-
This research is carried out to know the structural behaviour of the steel-concrete composite structure under seismic loadings.
-
Comparing different models i.e reinforced concrete cement & steel concrete composite structure will give a better idea between two different structural configurations.
-
-
METHODOLOGY
-
In the design of high rise structures, reinforced cement concrete structure is found to be bulky and has huge weight whereas composite structure has less self-weight compared to rcc structure
-
As in steel sections, ductility and high tensile strength are key properties, while stiffness and high compressive strength is the best property of concrete members. Thus combining the duo steel-concrete composite structures, strength and stiffness can be achieved with minimum use of materials.
-
In view of incorporating the above observations, the present study was carried out focusing on RC + Composite structures which can be constructed where the lower half stories will be of RCC and the remaining above half stories will be constructed as composite. With this overall reduction in self-weight of structure, stiffness on bottom floors and flexibility on top floors can be attained.
-
It is presumed that when seismic forces hit the RC + Composite structure, vibrations due to seismic energy will dissipate properly from the structure without any structural damage.
-
Also when the wind hits the structure, the top stories will dissipate the wind energy easily as the top stories is more flexible due to composite structure.
-
Fig -2.1: Architectural plan
2.1 Description of Structural Model
Analysis was carried out considering seismic zone-IV and soil type was considered as Medium i.e. soil type-II. Response reduction factor, R=5 & Importance factor, I=1.
This project is analyzed considering different storey levels G+7, G+15, G+30 and each storey level has five different models i.e. M-1, M-2, M-3, M-4, M-5 with architectural plan dimensions 28 m x 35 m has seven bays in X and Y direction regular building. Total height of the building is 25m, 53m & 105.5m for G+7, G+15 & G+30 respectively. Keeping height of ground floor 4 m and typical storey height 3.5m which is maintained throughout the building. All the modelling and analysis was done in Etabs 16.
Following are the models considered for the analysis. Details of each model is described below:
Model no.1 (M-1): An RCC bare frame structure in which all the beams and columns are modelled as line elements, including core shear wall for lift at the centre of building having weight of masonry walls of 230mm thick on all the beams. Core wall or shear wall and floor slabs are modelled as thin Shell element.
Model no.2 (M-2): Model same as model no.1(M1) including L-shaped shear walls at extreme corners of building.
Model no.3 (M-3): Model same as model no.1(M1) but
-
All the reinforced concrete columns are encased with ishb and iswb section with minimum percentage of steel in column (composite columns).
-
All the slabs are made as Deck slab and all the beams are made ISHB sections (Composite floor).
Model no.4 (M-4): Model same as Model no.3(M-3) including L- shaped shear alls at extreme corners of building.
Model no.5 (M-5): This Model has two parts, 1st part is lower portion of the structure and the above remaining half of the structure is 2nd part. i.e for (i) G+30 Storey Building, till G+16 is 1st half and 2nd half is above 16th storey to top storey (ii) G+15 Storey Building, till G+8 is 1st half and 2nd half is above 8th storey to Top storey (iii) G+7 Storey, till G+4 is 1st half and 2nd half is above 4th Storey to the Top storey.
-
1st Half part consists of RC beams and RC slabs.
-
2nd Half portion consists of composite floor i.e All the slabs are made as Deck slab and all the beams as ISHB steel sections.
-
All the RC columns are encased with ISHB and ISWB section with min percentage of steel in column (composite columns) throughout the structure.
-
Shear walls are considered at core and exterior corner edges as L-shaped
Note: Column sizes in composite Models kept same to the RC column. The main reason was to increase ductility in composite columns keeping stiffness and rigidity same as RC column where we can reduce lateral displacement upto some extent in Composite structure.
MODEL 1 MODEL 2 MODEL 3 MODEL 4 MODEL 5
Fig -2.2: Top view and Rendered View of different Models
Fig -2.3: Different Column sizes considered for RC and Composite Structure
Fig – 2.4: Representative image of Profiled Decking Floors system
Table -2.1: Building Details Table -2.2: Column and Beam Details
-
-
RESULTS AND DISCUSSIONS
Study was carried out considering different parameters like lateral displacements, storey drifts, storey shear force, storey stiffness and time period for the different building models with graphical representation.
Note: (i) Results are shown only for 30 stories but conclusions will be given for other story level (G+15 & G+7) also.
-
For the values of Displacement, Drift, Storey Shear Force and Storey Stiffness, refer Table 3.13.4 at the end.
-
Result Values are shown in Appendix Tables.
-
LATERAL DISPLCEMENT
30
28
26
24
22
Storey No's
20
18
16
14
12
10
8
6
4
2
0
0 3 6 9 12 15 18 21 24 27 30 33 36
Storey Displacement in "mm"
M-1-30
M-2-30
M-3-30
M-4-30
M-5-30
Chart -3.1: Displacements in X-direction
30
28
26
24
22
20
Storey No's
18
16
14
12
10
8
6
4
2
0
0 3 6 9 12 15 18 21 24 27 30 33 36 39 42 45 48
Storey Displacement in "mm"
Chart -3.2: Displacements in Y-direction
M-1-30
M-2-30
M-3-30
M-4-30
M-5-30
-
From table 3.1 and chart 3.1 & 3.2, Model 3 i.e composite structure with shear wall at core only, shows the highest displacement value at top floor level when compared with all the other building model, it shows that, this model is more flexible among all other building models in both longitudinal and transverse directions.
-
Semi rigid or semi composite i.e Model 5 is showing similar results when compared with Model 1 & 2 in both the directions.
-
Percentage differences when Model 3 is compared with Model 1, 2, 4 & 5 are 16.3%, 30.2%, 6% & 17.4% respt in Transverse direction.
-
-
STOREY DRIFT
30
28
26
24
22
Storey No's
20
18
16
14
12
10
8
6
4
2
0
0 0.0002 0.0004 0.0006
Storey Drift
Chart -3.3: Drift in X-direction
M-1-30
M-2-30
M-3-30
M-4-30
M-5-30
30
28
26
24
22
Storey No's
20
18
16
14
12
10
8
6
4
2
0
0 0.0002 0.0004 0.0006
Storey Drift
Chart -3.4: Drift in Y-direction
M-1-30
M-2-30
M-3-30
M-4-30
M-5-30
-
All the drift ratios are within the permissible limit specified by the IS-1893-2002.
-
Model 2 shows the least and Model 3 shows the highest amount of drift ratio when compared with all other models.
-
Combination of RCC and composite building i.e Model 5, the drift initially was very much low in transition zone (16th and 17th storey) and then the drift drastically increased due to the flexibility in upper stories.
-
Model 5 must be given due concentration during designing and construction in transition zone
-
-
STOREY SHEAR FORCE
30
28
26
24
22
Storey No's
20
18
16
14
12
10
8
6
4
2
0
0 1000 2000 3000 4000 5000 6000
Storey Shear in KN
Chart -3.5: Storey Shear in X-direction
M-1-30
M-2-30
M-3-30
M-4-30
M-5-30
30
28
26
24
22
Storey No's
20
18
16
14
12
10
8
6
4
2
0
0 1000 2000 3000 4000 5000 6000
Storey Shear in KN
Chart -3.6: Storey Shear in Y-direction
M-1-30
M-2-30
M-3-30
M-4-30
M-5-30
-
Max storey shear is seen in Model 2, since it has higher seismic weight when compared to other Models.
-
Composite structure shows minimum storey shear, as its self-weight is lesser then RC structures.
-
Model 5 is showing closer values to Model 2.
-
Percentage differences when Model 4 is compared with Model 1, 2, 3 & 5 in X-direction are 14.5%, 25.4%, 7.4% & 11.86%
respectively. And in Y-direction when Model 3 is compared with Model 1, 2, 4 & 5 are 23.2%, 40.15%, 16.32% & 30.11%
respectively.
-
-
STOREY STIFFNESS
30
28
26
24
22
Storey no.
20
18
16
14
12
10
8
6
4
2
0
0 4000000 8000000 12000000 16000000 20000000
Storey Stiffness in Kn/m
Chart -3.7: Storey Stiffness in X-direction
M-1-30
M-2-30
M-3-30
M-4-30
M-5-30
30
28
26
24
22
Storey no.
20
18
16
14
12
10
8
6
4
2
0
0 3500000 7000000 10500000 14000000 17500000 21000000
Storey Stiffness in Kn/m
Chart -3.8: Storey Stiffness in Y-direction
M-1-30
M-2-30
M-3-30
M-4-30
M-5-30
-
No soft storey found at any level storey even at Transition of RCC and composite Structure of Model 5.
-
Models with shear walls at periphery and core are showing highest amount of Stiffness values.
-
Stiffness differences when Model 3 is compared to Model 1, 2, 4 & 5 are 10%, 30%, 20% & 27% in X-direction and 18%,
52%, 37% & 49% in Y-direction.
-
Stiffness attained in RC + Composite structure i.e Model 5 is almost similar to Model 2 which is complete RC model with shear wall at core and periphery.
-
-
TIME PERIOD
5.5
5
Time Period in Secs
4.5
4
3.5
3
2.5
2
1.5
1
0.5
0
1 2 3 4 5 6 7 8 9 10 11 12
Mode No's
Chart -3.9: Time Period for 30 Storey Models
M-1-30
M-2-30
M-3-30
M-4-30
M-5-30
-
Model 3 shows the highest time period among all the Models in all storey level.
-
The time period of Model 2 & 5 is nearly same and showing least time period in comparison with other Models.
-
In 30 storey, composite Models showing max time period even after incorporation with shear wall at core and periphery but in 15 sorey it was showing somewhat reduction after incorporation of Shear wall.
-
For 7 Storey level, models with shear wall at core and periphery was showing least and same time period compared to models with shear wall at core only.
-
-
JOINT REACTIONS
40000.0
Joint Reactions in kN
Maximum reaction by gravity loads (D. L+L.L+SIDL) were only considered. Maximum value in every Model was occurring near the Center of the building and it was on Shear wall which is shown in the Fig.3.1 for all the models of different storey level.
60000.0
G+7
G+15
G+30
M-1
M-2 M-3 M-4
M-5
20000.0
0.0
Storey Levels
Chart -3.12: Maximum Joint Reactions
-
Minimum reaction was seen in Model 3 and maximum reaction in Model 2
Fig -3.1: Max. Loads acting on shear wall
-
In 30 storey models, the percentage difference when Model 3 is compared with Model 1, 2, 4 & 5 are 19%, 25%, 1% & 4% respt.
-
More than 21% reduction in self weight is attained when Model 5 is compared with Model 2.
-
Model 5 which has half of the structure RC and half of the structure composite then also the self-weight of the building can be reduced drastically.
-
Time Period
-
-
-
CONCLUSIONS
-
Maximum time period is observed in models with shear wall at core only which is Model 1 & 3. Least time period was seen in models with shear wall at core and periphery edges irrespective of RC and composite structure. Thus it can be said that additional shear walls at periphery edges is playing vital role in reducing time period.
-
In 7 storey building, Model 2, 4 & 5 were showing similar and the minimum time period over Model 1 & 3. With this it can be said that going for low rise structure, providing Shear wall at periphery edges will effectively work irrespective of its structural configuration.
-
Displacement
-
For 30 Storey building, In RC Structure Model 2, 15% of reduction was seen compared to Model 1. But in composite models, only 6% reduction was seen between Model 3 & 4. This shows that shear wall is not effectively working in G+30 storey for composite structures. Thus, it need some additional lateral resisting frame like bracings or outriggers etc. [see sec 4.2-a]
-
For 15 Storey, providing shear wall at periphery edges in composite Model is showing considerable reduction in storey displacement i.e about 15%. Thus it shows that shear wall effectively working till 15 Storey level in composite structure.
-
By going half RC half composite model, the displacement was similar to the Model with complete RC structure for all the storey levels.
-
DRIFT RATIO
-
-
Model 2 shows the minimum amount of drift ratio and Model 3 maximum. Thus it can be said that Model 2 is stiffer than all other models and in Model 3 flexibility prevails.
-
Although, in composite models, drift ratios where fallen within the specified limit of IS-Codal provisions. Deflections must be limited during earthquakes for many different reasons, and hence provision of adequate stiffness is important, peculiarly in composite models.
-
In Model 5, average drift at transitional zones are quite high in comparison with other storey levels. Thus greater concentration must be given during analysis and design of two different structural configurations when combined together. [see sec 4.2-a]
-
SHEAR FORCE
-
-
Maximum shear force was seen in RC Model with shear wall at core and periphery (Model 2) and the minimum was found in Model 3 i.e composite model with shear wall at core only. This shows that Model 2 has higher capacity to resist lateral loads during seismic events.
-
For Model 5, base shear is similar to Model 2, with this it can be concluded that even going for half of the structure as composite, we can get shear force similar to fully RC structure.
-
STIFFNESS
-
Stiffness is higher in RC models compared to composite models. This shows that Composite models has a lesser storey stiffness compared to RC structure despite of keeping same column sizes as of RC columns in composite models and even inducing with I-Sections. Thus it can be said that storey stiffness will not only depend on column properties and sizes but the floor system considered in the models will also matter.
-
Percentage differences when Model 4 & 5 is compared was 10 % and between Model 2 and 5, only 3% is seen. This shows that stiffness similar to RC structure can be attained by making half of the building as RC and other half as Composite
-
In 7 Storey, stiffness is same in the models with shear wall at periphery and core as well. Thus any one of the structure configuration Model can be adopted for 7 storey building.
-
Concluding Remarks:
-
Its seen that RC + Composite structure is showing overall best results compared to complete RC or composite Models.
As in bottom stories of Model 5, stiffness is similar to RC structure and ductility is similar to composite structure.
-
During seismic excitation, building should be stiffer at bottom as well as ductile to transfer the seismic vibrations safely and at the same time when the upper stories get displaced, there will be P-delta effects. Thus, P i.e Gravity loads should be minimized to reduce P-Delta effects. This can be achieved by adopting composite or steel structure which will reduce self-weight.
-
Both the parameters, that is ductility & stiffness at bottom stories and reducing self-weight in upper stories can be achieved by combining duo structural configuration together which is Model 5 RC + Composite Structure.
-
-
Further Additional work 4.2-a: Observations
-
In 30 storey models, when the shear walls were introduced to the composite structure i.e Model 3 at periphery edges, result shows that it was not effective in reducing displacement and drift.
-
In RC + Composite model (model 5), average drift at transitional zones is quite high in comparison with other storey levels.
4.2-b: Alternate Solution
-
Instead of providing shear walls at periphery edges, bracings found to be more effective compared to shear walls in composite structure. [see 4.2-d Results]
-
Near the transition zone in Model 5, providing bracings will reduce the sudden drift change. [see 4.2-d Results]
4.2-c: Models Descriptions
Model 6 Same as RC + Composite structure (Model 5) with additional X-bracings from transition zone (15 Storey) to the top storey.
Model 7 Composite Structure (Model 3) with additional X-bracings at periphery of the Model.
Note: Angle Bracings are adopted with dimensions 150x150x25 in mm.
Fig-4.1: Model 6 Fig-4.2: Model 7
4.2-d: Results
30
28
26
24
22
Storey No's
20
18
16
14
12
10
8
6
4
2
0
0 2 4 6 8 10 12 14 16 18 20 22 24 26 28 30 32 34 36 38 40 42 44 46 48
Storey Displacement in "mm"
Chart – 4.1: Storey displacement of 30 Storey Models
M-1-30
M-2-30
M-3-30
M-4-30
M-5-30
M-6-30
M-7-30
From the Chart 4.1, it can be said that for 30 storey composite model, Bracings are the better option when compared to shear walls. As when Model 3 is compared with Model 4 (shear wall at periphery edges) only 6% of reduction is seen. And when Model 3 is compared with Model7 (Bracings at periphery) around 17% of reduction was seen. Hence we can conclude that dual resisting frames (core shear walls with external bracings) are better option instead of core Shear wall in additin to shear wall at edges.
30
28
26
24
22
Storey No's
20
18
16
14
12
10
8
6
4
2
0
0 0.0001 0.0002 0.0003 0.0004 0.0005 0.0006
Storey Drift
M-1-30
M-2-30
M-3-30
M-4-30
M-5-30
M-6-30
M-7-30
Chart – 4.2: Storey Drift of 30 Storey Models
From chart 4.2, it can be observed that Drift was drastically reduced when bracings were introduced at transition zone in Model 5 RC + composite structure which is Model 6. And its showing similar results when compared with model 2.
Drift in composite Model 3 reduced more when bracings (Model 7) were provided at periphery instead of shear walls (Model 4).
-
-
-
REFERENCES
APPENDIX
Table: A.1 Displacement values for 30 Storey Models
Storey no. |
Model 1-30 |
Model 2-30 |
Model 3-30 |
Model 4-30 |
Model 5-30 |
|||||
Ux |
Uy |
Ux |
Uy |
Ux |
Uy |
Ux |
Uy |
Ux |
Uy |
|
30 |
29.4 |
39.0 |
29.4 |
32.5 |
34.3 |
46.6 |
29.8 |
43.8 |
29.8 |
38.5 |
29 |
28.3 |
38.2 |
28.4 |
31.8 |
33.0 |
45.4 |
28.7 |
42.5 |
28.6 |
37.2 |
28 |
27.3 |
37.3 |
27.5 |
31.0 |
31.7 |
44.2 |
27.6 |
41.2 |
27.5 |
35.9 |
27 |
26.2 |
36.4 |
26.6 |
30.1 |
30.5 |
43.0 |
26.4 |
39.8 |
26.4 |
34.6 |
26 |
25.1 |
35.4 |
25.6 |
29.3 |
29.2 |
41.7 |
25.3 |
38.4 |
25.2 |
33.2 |
25 |
24.0 |
34.3 |
24.6 |
28.3 |
27.9 |
40.4 |
24.1 |
37.0 |
24.0 |
31.8 |
24 |
22.9 |
33.2 |
23.5 |
27.4 |
26.5 |
39.0 |
23.0 |
35.5 |
22.8 |
30.4 |
23 |
21.8 |
32.1 |
22.5 |
26.4 |
25.2 |
37.5 |
21.8 |
34.0 |
21.6 |
29.0 |
22 |
20.7 |
30.9 |
21.4 |
25.3 |
23.9 |
36.0 |
20.7 |
32.4 |
20.4 |
27.5 |
21 |
19.6 |
29.6 |
20.3 |
24.2 |
22.5 |
34.4 |
19.5 |
30.8 |
19.2 |
26.0 |
20 |
18.5 |
28.2 |
19.2 |
23.0 |
21.2 |
32.8 |
18.3 |
29.1 |
18.0 |
24.5 |
19 |
17.3 |
26.8 |
18.1 |
21.9 |
19.9 |
31.1 |
17.1 |
27.5 |
16.8 |
22.9 |
18 |
16.2 |
25.4 |
17.0 |
20.6 |
18.5 |
29.3 |
16.0 |
25.8 |
15.6 |
21.4 |
17 |
15.1 |
23.9 |
15.8 |
19.4 |
17.2 |
27.5 |
14.8 |
24.1 |
14.5 |
19.9 |
16 |
13.9 |
22.4 |
14.7 |
18.1 |
15.9 |
25.7 |
13.7 |
22.3 |
13.3 |
18.4 |
15 |
12.8 |
20.9 |
13.5 |
16.8 |
14.6 |
23.8 |
12.5 |
20.5 |
12.2 |
16.9 |
14 |
11.7 |
19.3 |
12.4 |
15.5 |
13.3 |
21.9 |
11.4 |
18.8 |
11.1 |
15.5 |
13 |
10.6 |
17.7 |
11.2 |
14.2 |
12.0 |
20.0 |
10.3 |
17.0 |
10.0 |
14.1 |
12 |
9.6 |
16.1 |
10.1 |
12.8 |
10.8 |
18.1 |
9.2 |
15.3 |
9.0 |
12.7 |
11 |
8.5 |
14.5 |
9.0 |
11.5 |
9.6 |
16.1 |
8.1 |
13.5 |
8.0 |
11.3 |
10 |
7.5 |
12.8 |
7.9 |
10.1 |
8.4 |
14.2 |
7.0 |
11.8 |
7.0 |
10.0 |
9 |
6.5 |
11.2 |
6.8 |
8.8 /td> |
7.2 |
12.3 |
6.0 |
10.1 |
6.0 |
8.6 |
8 |
5.5 |
9.5 |
5.8 |
7.5 |
6.1 |
10.4 |
5.1 |
8.5 |
5.1 |
7.3 |
7 |
4.6 |
7.9 |
4.8 |
6.2 |
5.1 |
8.5 |
4.1 |
6.9 |
4.2 |
6.0 |
6 |
3.7 |
6.4 |
3.8 |
4.9 |
4.1 |
6.8 |
3.3 |
5.4 |
3.3 |
4.8 |
5 |
2.9 |
4.9 |
2.9 |
3.7 |
3.1 |
5.1 |
2.5 |
4.0 |
2.5 |
3.6 |
4 |
2.1 |
3.5 |
2.1 |
2.6 |
2.3 |
3.6 |
1.8 |
2.8 |
1.8 |
2.5 |
3 |
1.4 |
2.2 |
1.4 |
1.7 |
1.5 |
2.2 |
1.1 |
1.7 |
1.2 |
1.6 |
2 |
0.8 |
1.2 |
0.8 |
0.9 |
0.8 |
1.1 |
0.6 |
0.9 |
0.7 |
0.8 |
1 |
0.3 |
0.4 |
0.3 |
0.3 |
0.3 |
0.4 |
0.2 |
0.3 |
0.3 |
0.3 |
Table: A.2 Drift Ratios for 30 Storey Models
Storey No. |
Model 1-30 |
Model 2-30 |
Model 3-30 |
Model 4-30 |
Model 5-30 |
|||||
RSA-x |
RSA-y |
RSA-x |
RSA-y |
RSA-x |
RSA-y |
RSA-x |
RSA-y |
RSA-x |
RSA-y |
|
30 |
0.000344 |
0.000289 |
0.000338 |
0.00026 |
0.000448 |
0.000389 |
0.00049 |
0.000432 |
0.000476 |
0.000418 |
29 |
0.000402 |
0.000305 |
0.000359 |
0.000269 |
0.000514 |
0.000405 |
0.000504 |
0.00044 |
0.000497 |
0.000427 |
28 |
0.000426 |
0.000324 |
0.000376 |
0.000282 |
0.000538 |
0.000423 |
0.00051 |
0.000449 |
0.00051 |
0.000437 |
27 |
0.000445 |
0.000343 |
0.000394 |
0.000297 |
0.000553 |
0.00044 |
0.000518 |
0.000461 |
0.000524 |
0.00045 |
26 |
0.000462 |
0.000362 |
0.000411 |
0.000312 |
0.000566 |
0.000458 |
0.000525 |
0.000473 |
0.000537 |
0.000462 |
25 |
0.000476 |
0.00038 |
0.000425 |
0.000326 |
0.000578 |
0.000475 |
0.000531 |
0.000484 |
0.000547 |
0.000472 |
24 |
0.000487 |
0.000396 |
0.000438 |
0.000339 |
0.000588 |
0.00049 |
0.000534 |
0.000494 |
0.000556 |
0.000481 |
23 |
0.000495 |
0.000411 |
0.000449 |
0.000351 |
0.000595 |
0.000504 |
0.000536 |
0.000503 |
0.000562 |
0.000487 |
22 |
0.000499 |
0.000425 |
0.000458 |
0.000362 |
0.0006 |
0.000517 |
0.000535 |
0.000511 |
0.000566 |
0.000491 |
21 |
0.000501 |
0.000439 |
0.000465 |
0.000372 |
0.000601 |
0.00053 |
0.000533 |
0.000518 |
0.000568 |
0.000493 |
20 |
0.0005 |
0.000449 |
0.000469 |
0.000379 |
0.000599 |
0.000541 |
0.000529 |
0.000523 |
0.000566 |
0.000492 |
19 |
0.0005 |
0.000459 |
0.000472 |
0.000386 |
0.000597 |
0.000552 |
0.000524 |
0.000528 |
0.000563 |
0.000489 |
18 |
0.000501 |
0.000468 |
0.000474 |
0.000391 |
0.000595 |
0.000561 |
0.000519 |
0.000531 |
0.000557 |
0.000482 |
17 |
0.000502 |
0.000474 |
0.000475 |
0.000395 |
0.000593 |
0.000569 |
0.000512 |
0.000533 |
0.000559 |
0.000482 |
16 |
0.000509 |
0.000486 |
0.000481 |
0.000403 |
0.000594 |
0.000579 |
0.000507 |
0.000535 |
0.000524 |
0.000456 |
15 |
0.000483 |
0.00048 |
0.000469 |
0.000398 |
0.000577 |
0.000578 |
0.000499 |
0.000531 |
0.000503 |
0.00044 |
14 |
0.000487 |
0.000484 |
0.000467 |
0.0004 |
0.000577 |
0.00058 |
0.000493 |
0.000528 |
0.00049 |
0.000429 |
13 |
0.000484 |
0.000485 |
0.000463 |
0.000399 |
0.000572 |
0.000579 |
0.000485 |
0.000523 |
0.000479 |
0.00042 |
12 |
0.00048 |
0.000486 |
0.000459 |
0.000399 |
0.000566 |
0.000576 |
0.000474 |
0.000516 |
0.000467 |
0.000412 |
11 |
0.000473 |
0.000485 |
0.000454 |
0.000396 |
0.000556 |
0.00057 |
0.000461 |
0.000505 |
0.000455 |
0.000404 |
10 |
0.000465 |
0.000482 |
0.000445 |
0.000392 |
0.000544 |
0.000561 |
0.000445 |
0.000491 |
0.000441 |
0.000395 |
9 |
0.000456 |
0.000476 |
0.000435 |
0.000385 |
0.00053 |
0.000549 |
0.000428 |
0.000475 |
0.000426 |
0.000386 |
8 |
0.000447 |
0.000467 |
0.000422 |
0.000375 |
0.000518 |
0.000533 |
0.000406 |
0.000454 |
0.000409 |
0.000373 |
7 |
0.000434 |
0.000453 |
0.000405 |
0.000361 |
0.000515 |
0.00051 |
0.000381 |
0.000428 |
0.000387 |
0.000357 |
6 |
0.000418 |
0.000432 |
0.000382 |
0.000341 |
0.000505 |
0.000479 |
0.00035 |
0.000395 |
0.000361 |
0.000335 |
5 |
0.000405 |
0.000402 |
0.000352 |
0.000314 |
0.000486 |
0.000438 |
0.000313 |
0.000355 |
0.000328 |
0.000306 |
4 |
0.000394 |
0.00036 |
0.000314 |
0.000277 |
0.000456 |
0.000383 |
0.00027 |
0.000305 |
0.000288 |
0.000269 |
3 |
0.00037 |
0.0003 |
0.000265 |
0.000229 |
0.000407 |
0.000312 |
0.000217 |
0.000244 |
0.000238 |
0.00022 |
2 |
0.000326 |
0.000222 |
0.0002 |
0.000167 |
0.000328 |
0.000225 |
0.000155 |
0.000171 |
0.000176 |
0.000158 |
1 |
0.000197 |
0.000107 |
0.000103 |
0.000079 |
0.000162 |
0.000101 |
0.000074 |
0.000075 |
0.000086 |
0.000073 |
Table: A.3 Storey Shear Force for 30 Storey Models
Storey no. |
Model 1-30 |
Model 2-30 |
Model 3-30 |
Model 4-30 |
Model 5-30 |
|||||
Vx |
Vy |
Vx |
Vy |
Vx |
Vy |
Vx |
Vy |
Vx |
Vy |
|
30 |
593.8 |
567.8 |
622.7 |
678.9 |
531.7 |
442.8 |
501.3 |
561.3 |
525.2 |
605.1 |
29 |
593.8 |
567.8 |
622.7 |
678.9 |
531.7 |
442.8 |
501.3 |
561.3 |
525.2 |
605.1 |
28 |
1602.3 |
1473.6 |
1703.9 |
1804.5 |
1454.2 |
1174.9 |
1351.4 |
1433.4 |
1424.8 |
1567.8 |
27 |
1951.2 |
1765.4 |
2094.3 |
2187.3 |
1778.8 |
1417.4 |
1635.9 |
1686.9 |
1731.7 |
1862.8 |
26 |
2203.7 |
1970.3 |
2396.9 |
2472.8 |
2015.5 |
1585.0 |
1838.8 |
1846.7 |
1956.6 |
2061.9 |
25 |
2372.9 |
2113.5 |
2628.1 |
2686.9 |
2172.6 |
1689.8 |
1975.3 |
1943.3 |
2115.4 |
2195.3 |
24 |
2372.9 |
2113.5 |
2628.1 |
2686.9 |
2172.6 |
1689.8 |
1975.3 |
1943.3 |
2115.4 |
2195.3 |
23 |
2536.0 |
2322.1 |
2949.8 |
3004.8 |
2307.4 |
1785.2 |
2119.2 |
2069.2 |
2307.5 |
2383.2 |
22 |
2570.4 |
2424.8 |
3069.7 |
3143.4 |
2325.2 |
1819.5 |
2156.5 |
2138.0 |
2370.6 |
2475.4 |
21 |
2597.1 |
2532.9 |
3173.7 |
3275.9 |
2337.6 |
1869.5 |
2183.4 |
2215.9 |
2423.3 |
2571.6 |
20 |
2628.3 |
2641.8 |
3266.3 |
3400.8 |
2359.8 |
1943.6 |
2205.3 |
2296.6 |
2469.9 |
2667.2 |
19 |
2670.5 |
2745.8 |
3351.6 |
3516.2 |
2398.6 |
2038.9 |
2226.6 |
2373.7 |
2513.7 |
2756.6 |
18 |
2725.0 |
2842.3 |
3433.6 |
3622.0 |
2452.8 |
2144.0 |
2252.2 |
2443.9 |
2558.0 |
2837.8 |
17 |
2790.6 |
2932.9 |
3518.7 |
3723.0 |
2517.2 |
2245.5 |
2288.2 |
2509.6 |
2608.2 |
2913.9 |
16 |
2864.8 |
3021.5 |
3613.9 |
3825.7 |
2587.2 |
2332.1 |
2341.1 |
2575.5 |
2670.8 |
2991.1 |
15 |
2864.8 |
3021.5 |
3613.9 |
3825.7 |
2587.2 |
2332.1 |
2341.1 |
2575.5 |
2670.8 |
2991.1 |
14 |
3039.9 |
3203.3 |
3854.1 |
4054.0 |
2748.6 |
2445.1 |
2515.1 |
2721.0 |
2887.4 |
3200.1 |
13 |
3145.2 |
3293.0 |
3999.1 |
4178.5 |
2848.4 |
2477.9 |
2634.2 |
2797.9 |
3031.5 |
3319.3 |
12 |
3145.2 |
3293.0 |
3999.1 |
4178.5 |
2848.4 |
2477.9 |
2634.2 |
2797.9 |
3031.5 |
3319.3 |
11 |
3267.4 |
3377.3 |
4155.5 |
4305.4 |
2968.1 |
2508.6 |
2768.3 |
2874.6 |
3190.7 |
3441.0 |
10 |
3580.3 |
3538.2 |
4491.6 |
4568.7 |
3281.3 |
2617.7 |
3069.5 |
3042.0 |
3536.5 |
3693.0 |
9 |
3580.3 |
3538.2 |
4491.6 |
4568.7 |
3281.3 |
2617.7 |
3069.5 |
3042.0 |
3536.5 |
3693.0 |
8 |
3989.2 |
3743.1 |
4861.3 |
4879.2 |
3681.7 |
2833.7 |
3417.3 |
3286.6 |
3919.7 |
4002.3 |
7 |
4213.2 |
3877.7 |
5055.4 |
5057.6 |
3894.9 |
2969.8 |
3604.0 |
3447.0 |
4122.1 |
4187.0 |
6 |
4213.2 |
3877.7 |
5055.4 |
5057.6 |
3894.9 |
2969.8 |
3604.0 |
3447.0 |
4122.1 |
4187.0 |
5 |
4638.0 |
4180.3 |
5429.3 |
5420.1 |
4290.1 |
3232.0 |
3966.0 |
3791.4 |
4513.5 |
4569.8 |
4 |
4811.5 |
4315.4 |
5585.6 |
5572.0 |
4448.9 |
3332.9 |
4116.7 |
3937.9 |
4677.2 |
4731.2 |
3 |
4944.5 |
4417.9 |
5705.2 |
5684.5 |
4569.3 |
3403.5 |
4231.1 |
4045.6 |
4802.5 |
4850.3 |
2 |
4944.5 |
4417.9 |
5705.2 |
5684.5 |
4569.3 |
3403.5 |
4231.1 |
4045.6 |
4802.5 |
4850.3 |
1 |
5031.5 |
4479.8 |
5780.9 |
5751.2 |
4646.4 |
3443.2 |
4302.7 |
4108.5 |
4881.7 |
4920.4 |
Table: A.4 Storey Stiffness Values for 30 Storey Models
Storey no. |
Model 1-30 |
Model 2-30 |
Model 3-30 |
Model 4-30 |
Model 5-30 |
|||||
Kx |
Ky |
Kx |
Ky |
Kx |
Ky |
Kx |
Ky |
Kx |
Ky |
|
30 |
569357 |
664906 |
661004 |
881687 |
417037 |
380426 |
444834 |
426200 |
460289 |
477967 |
29 |
1101175 |
1218581 |
1306180 |
1637746 |
821903 |
715615 |
874314 |
793206 |
904133 |
894817 |
28 |
1510140 |
1589625 |
1789853 |
2163662 |
1136968 |
956777 |
1200169 |
1045481 |
1245429 |
1188601 |
27 |
1813389 |
1797770 |
2143625 |
2494050 |
1375693 |
1108184 |
1440041 |
1199782 |
1495465 |
1375769 |
26 |
2025432 |
1892715 |
2394472 |
2682020 |
1543231 |
1186360 |
1605928 |
1278022 |
1668001 |
1485547 |
25 |
2153287 |
1917861 |
2559000 |
2775768 |
1649644 |
1210472 |
1708778 |
1309528 |
1786673 |
1543838 |
24 |
2227414 |
1911318 |
2670532 |
2817414 |
1705894 |
1199855 |
1774043 |
1318984 |
1861814 |
1579996 |
23 |
2260232 |
1895622 |
2746557 |
2832018 |
1728413 |
1173718 |
1811277 |
1323855 |
1919753 |
1611353 |
22 |
2278700 |
1888460 |
2803405 |
2844714 |
1735244 |
1147926 |
1836854 |
1334611 |
1965673 |
1649156 |
21 |
2290220 |
1885979 |
2848918 |
2851053 |
1741905 |
1134429 |
1856669 |
1350329 |
2004415 |
1691865 |
20 |
2325890 |
1895109 |
2905995 |
2869912 |
1767620 |
1141304 |
1884861 |
1373584 |
2061699 |
1746677 |
19 |
2365342 |
1910812 |
2958207 |
2884495 |
1799384 |
1163750 |
1906362 |
1397111 |
2114093 |
1805260 |
18 |
2417966 |
1921738 |
3009321 |
2902208 |
1849747 |
1192435 |
1936551 |
1417569 |
2178848 |
1869402 |
17 |
2489346 |
1935884 |
3067784 |
2919971 |
1911288 |
1222381 |
1977715 |
1439836 |
2258208 |
1941276 |
16 |
2573965 |
1951878 |
3142489 |
2945083 |
1987101 |
1245131 |
2042807 |
1464211 |
2380419 |
2048711 |
15 |
2686450 |
1988044 |
3258637 |
3008563 |
2069128 |
1265697 |
2130573 |
1499844 |
2529996 |
2167583 |
14 |
2801770 |
2015928 |
3383781 |
3057344 |
2171109 |
1275495 |
2249675 |
1539005 |
2698473 |
2279243 |
13 |
2939439 |
2045340 |
3529684 |
3120606 |
2287864 |
1283196 |
2394753 |
1587002 |
2892688 |
2384539 |
12 |
3102901 |
2074530 |
3706958 |
3193888 |
2434858 |
1293776 |
2572785 |
1643564 |
3109858 |
2493446 |
11 |
3311765 |
2106629 |
3912705 |
3281958 |
2615003 |
1317147 |
2782583 |
1713020 |
3359255 |
2605018 |
10 |
3601917 |
2156133 |
4193813 |
3404375 |
2870820 |
1363363 |
3060331 |
1804285 |
3664741 |
2737574 |
9 |
3911881 |
2222030 |
4488494 |
3553823 |
3140944 |
1433912 |
3355462 |
1924982 |
3995323 |
2898351 |
8 |
4289423 |
2322009 |
4841908 |
3758999 |
3473296 |
1535896 |
3722499 |
2090741 |
4389319 |
3104932 |
7 |
4744583 |
2468319 |
5288066 |
4036397 |
3871628 |
1675006 |
4176117 |
2319657 |
4872416 |
3384800 |
6 |
5304036 |
2676636 |
5864020 |
4413167 |
4358899 |
1860618 |
4762208 |
2629841 |
5487079 |
3758075 |
5 |
5999984 |
2979546 |
6629214 |
4949833 |
4965430 |
2113812 |
5531406 |
3062561 |
6294921 |
4274859 |
4 |
6893215 |
3433110 |
7704266 |
5750303 |
5792820 |
2487261 |
6597300 |
3690660 |
7388979 |
5033175 |
3 |
8213451 |
4203548 |
9383510 |
7079105 |
7029679 |
3119660 |
8231786 |
4731745 |
9095625 |
6290891 |
2 |
10417199 |
5833051 |
12352249 |
9898726 |
9292780 |
4454379 |
11263662 |
6916623 |
12358739 |
8897661 |
1 |
15558846 |
11790339 |
20048652 |
20199197 |
13971262 |
9657903 |
17473163 |
15417718 |
19204879 |
18810740 |
Note: What we Justified at the time was, we wanted to increase the ductility of the structure keeping stiffness of the structure same as RC.
If we were concerned about reducing self wt, then equivalent section method would have been adopted to select the composite element sizes. But this could lead to reduction of stiffness and increase in displacement.