
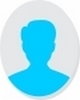
- Open Access
- Authors : Behzad Shokati Beyrag , Amir Hossein Farshidfar , Rashid Hajivand Dastgerdi , Mohammad Almasi
- Paper ID : IJERTV11IS100079
- Volume & Issue : Volume 11, Issue 10 (October 2022)
- Published (First Online): 02-11-2022
- ISSN (Online) : 2278-0181
- Publisher Name : IJERT
- License:
This work is licensed under a Creative Commons Attribution 4.0 International License
Evaluation of the Wall Deflections of an Urban Excavation Supported by Truss Structures using Three-Dimensional Modeling
Behzad Shokati Beyrag 1, Amir Hossein Farshidfar 2, Rashid Hajivand Dastgerdi 3 , Mohammad Almasi 4
1 Graduate Student, Azad university of Marand, Marand, Iran
Graduate Student, Shahid Beheshti University, Tehran, Iran
3 Graduate Student, Amirkabir University of Technology, Tehran, Iran
4 Graduate Student, Yazd University , Yazd, Iran
Abstract nowadays, excavation is considered as one of the most sensitive and important stages of urban construction, and because of the high sensitivity of this stage, engineers always try to choose the appropriate stabilization systems and analyze, design and implement them with different methods. Many buildings that are in the vicinity of deep excavation are damaged due to wall displacements during construction, therefore limiting the deformations, that are the result of deep excavations, is one of the most important design issues, especially in urban areas. in addition to excavation stability analysis, engineers evaluate and predict deformations and displacements around the excavation by using the geotechnical information of the construction, excavation geometry, surcharges around them, and simulation of the excavation stages. In this research, a numerical simulation, utilizing the Plaxis software, have been developed for a real project and the results obtained from two methods of modeling and monitoring have been compared with each other. Due to the complexities in 3D modeling using finite element software, most geotechnical engineers rely solely on the results obtained from analytical methods. In this article, it has been tried to make the process of 3D modeling of excavation in urban areas easier by considering some simplified assumptions.
Keywords Finite Element Modelling, Excavation, Settlement, Truss Structures
- INTRODUCTION
In recent decades, with the development of urbanization and population growth, the need to design high-rise buildings is inevitable. On the other hand, the height restriction in construction in some historical places and cities and the increasing value of lands in recent years have forced many owners to build buildings with several floors. Increasing the excavation depth is especially important in urban areas near buildings and roads, and ensuring the stability and control of displacements of the excavation wall and the ground surface behind the wall must be carefully examined. In this situation, some excavation stabilization methods lose their efficiency. Therefore, the discussion of deep excavation with proper stabilization method has become very important. The proper method of stabilizing the excavation according to the conditions and type of soil, the depth of excavation, and etc. are selected. The general methods of stabilizing excavation operations are: slope stabilization, improving and modifying the soil characteristics like the injection method, and Excavation with the implementation of support structures like truss structure, restrained piles, nailing, and etc. One of the most common and oldest ways to stabilize the excavations near to substantial structures is to restraint them by using truss support system or diaphragm walls due their rigidity and safety level.
Numerous researches have been conducted in order to determine behavior of the excavation walls and the forces applied by the lateral earth pressure to the support systems. Many achievements were obtained in the process of analysis and design of the system to provide the safety. Khosravi et al.. [1] used 4 geotechnical centrifuge models, to examine the effects of distance of the surcharge on the deformation of the the walls. A series of FEM analysis were also carried out applying different constitutive soil models, to compare the results obtained from the physical and numerical modeling of the nailed wall. Based on the comparison of the results of centrifuge models and the results obtained from different constitutive models, the most agreement is evident in the hardening soil with small strain model. Nejjar et al.. [2] presents a numerical back analysis of a recent fully monitored 32 m deep excavation of Fort dIssy-Vanves-Clamart (FIVC) metro station in Paris. Both FEM-2D and FEM-3D models were compared to the simplified proposed model by the engineer called subgrade reaction method (SRM) and the consistency between these modellings were investigated. The results could be used for an optimization purpose in future designs of deep excavations in similar ground conditions. Costa and Borges [3] conducted their researches through the geotechnical behavior of a braced excavation in the soft soils of San Francisco (USA), both during and after the construction period. Three months after the end of excavation, the values of earth pressure on both wall faces in the partial drained analysis were slightly larger than values at the end of construction, particularly on the lower part of the wall; this effect is linked to the volumetric strain (swelling effect) that arises from the partial dissipation of negative excess pore pressure. Numerical results are compared with field results, considering the construction period improves the results obtained from the behavior of the excavation in soft soils.
In the present study, a monitored restrained excavation by truss support system were simulated. The lateral displacement of the excavation walls and the forces applied to the truss system members were investigated by the Plaxis software and the results were compared to the monitored field data. As most geotechnical engineers avoid 3D-modelling and only rely on analytical methods because of the complications of it, here in we have offered some simplification ways to reduce the runtime and errors to make the results more realistic.
- MATERIALS AND METHODS
-
- General characteristics of the excavation
In this study a constructed monitored project were investigated around the north urban area of Tehran city, which has been stabilized by the use of a truss support structure system, due to its proximity to the surrounding buildings and the shallow depth of the excavation. The depth of the excavation is 5.78 meter. According to the figure 1, there is a six-story building on the south side of the excavation and a five-story building on the northwest corner, there are courtyard in the western and northern sides, and there is a courtyard in the eastern side of excavation.
Fig. 1. Excavation plan and surrounding buildings
The truss support structure system method is one of the most appropriate and common methods among the support structures in urban areas. Its implementation is simple and does not require high equipment and expertise, and at the same time, it has great flexibility in terms of implementation in different conditions. To implement this type of support structure, first dig holes in the place of the vertical members of the truss, which are located near the wall of the excavation. The depth of these holes is equal to the depth of the excavation plus an extra amount for the implementation of the pile at the lower end of the truss member. Then reinforce the pile and place the vertical member inside the pile and then pour concrete into the pile. After the concrete hardens, the lower end of the vertical member will be placed inside the pile with a rigid connection. Then remove the soil along the wall of the excavation with a stabilized slope, after that implement the foundation of the diagonal member. After that, connect the diagonal member from one side to the vertial member and from the other side to the base plate above the foundation. Now, remove the soil enclosed between the brace members of the trusses throughout the length of the wall step by step to integrate the horizontal function of the truss along the wall, and in each step, install the horizontal and diagonal members of the truss gradually until the truss is completed. Although Utilizing this method is suitable for most excavation located in urban area, has a lot of flexibility and simple with no need to special expertise and equipment, but there are obvious disadvantages compared to other methods such as lower constructing speed and the restriction created by the truss members in the excavation. It should also be mentioned that this system have some limitations for depth of the excavation and is proper for supporting excavations with depth more than 7-8 meter [4].
Fig. 2. truss support structure implementing stages in deep excavations [5]
- Numerical Modelling
- General characteristics of the excavation
The numerical study have been done by using Finite element Method (FEM) and with the help of Plaxis software, which has additional advantages and options for geotechnical projects compared to other software and codes. During the initial analysis, the range of boundaries was determined in such a way that their effects on the results could be ignored. The simulating process has progressed before the construction stage of the foundations, which includes three consecutive phases, and it includes, respectively, establishment of initial stresses in the zone, excavation, installation of support structures and activate them step by step, until getting to the lowest depth of the excavation. And finally to calculate the factor of safety for the mentioned excavation. The method of implementing the intermediate phases is described in the material and method section [5]. The vertical boundaries of the excavation are considered to be fixed only in the directions perpendicular to the planes but the bottom of the excavation assumed to be fixed in each direction. 47,630 6-node triangular elements with an average size of 1.5 (m) are used for analysis and meshing, the size becomes smaller by approaching to the excavation. Since the main goal of the present research is to investigate the displacement of the excavation walls and the forces acting on the support structure, the displacements related to the walls of the adjacent buildings are ignored and the buildings are simulated as a rigid body. The equivalent load of each floor of the building is considered equal to 10 kpa, which according to the number of floors of the mentioned building, this load is applied directly on the level of the foundation of the building. Also, the equivalent load of the street near the excavation is equal to 10 Kpa, and in order to simulate the gravity body forces, the acceleration is considered 9.8 m/s2 downwards.
According to the difference in the loads applied to the excavation wall in different directions, the height differences in the area and the geometry of the excavation, three types of truss structures have been used to stabilize the mentioned excavation, the truss structure related to the north and west walls are the same and for other walls the structures are different.
The behavior of support structures was modeled as linear elastic. In table 1 and 2, the truss support system and shotcrete wall parameters are presented [8]. It should also be noted that hardening soil (HS) was chosen for soil modeling.
Table. 1. Truss support system properties
Poisson ratio () Elasticity modulus (E) Unit weight () 0.3 210E6 (KN/m2) 78 (KN/m3) Table. 2. Concrete properties used for shotcrete
Poisson ratio () Elasticity modulus (E) Unit weight () thickness (d) 0.2 25E6 (KN/m2) 24 (KN/m3) 0.1 (m) Table. 3. Concrete properties used for truss foundation
Poisson ratio () Elasticity modulus (E) Unit weight () thickness (d) 0.2 28E6 (KN/m2) 25 (KN/m3) 0.4 (m) Hardening soil model is an advanced model for simulating the behavior of both soft and hard soils. Similar to the Mohr-Columb model, soil behavior in limited stress states (elastic range) is defined by the angle of internal friction, cohesion and dilation angle. This model is completely different from the Mohr-Coulomb method in defining the stiffness parameter. In this model, three types of stiffness are defined as triaxial loading stiffness E50, triaxial un-loading stiffness Eur, and oedometer loading stiffness Eoed. The basic difference between the Mohr-Columb model and the hardening soil is that in the hardening soil model, the stiffness is a function of the stress level, and with the increase of the stress, all the stiffness parameters increase. In the Mohr-Columb model, the loading and unloading stiffness are equal, while in the hardening soil model, the un-loading stiffness is three to five times the loading soil stiffness. This problem has caused the hardening soil model to have very good accuracy and performance in simulation surface excavations [5, 6, 7]. The soil parameters are listed in table 3.
Table. 4. Hardening Soil model parameters
E50 Eoed Eur Cohesion Coefficient (C) Internal friction angle () Poisson ratio () Rint 30E3 (KN/m2) 30E3 (KN/m2) 90E3 (KN/m2) 18 (KN/m3) 15(KN/m2) 25 0.3 0.9 -
- Displacements
-
- RESULTS AND DISCUSSIONS
the total displacements of the whole model and all walls have been calculated. As it is shown, the maximum displacements occurred along the western wall. (Fig. 3-5)
Fig. 3. Total deformation of the soil around the excavation
Fig. 4. Deformation of the excavation walls after the final phase
Fig. 5. Deformation of the western wall
In figure 5 the maximum displacement, which happened in western wall is shown. It is seen that 14 mm displacement happened on the 2/3 height of the excavation wall. Figure 6, 7 shows the deformation of the entire truss support structure. As it is known, the deformations are more intense in the middle and bottom of the structure due to the increase in the lateral pressure of the soil. Considering that, the maximum displacements are related to the western and northern wall. The truss structure tends to be compressed to the inside due to the displacements of behind walls, and this pressure has caused changes in the shapes in this direction. It is rational to expect more axial forces along the members of the support system for the walls with the maximum displacement.
Fig. 6. Deformation of the guardian structure (scaled 100 times)
Fig. 7. Deformation of the truss structure after the completion of the excavation process (scaled 75 times)
Based on the results obtained from the numerical simulation, the displacements of both northern and western wall were compared to the field in figure 8 and 9. It is noticed that, the monitoring data are collected for two points on top edge of both west and northern walls. The deformation of the northern and western wall for the specified points are 6 (mm) and for the field data is 4 (mm).
Fig. 8. Western wall displacement diagram for numerical model output and field data for the middle of the wall
-
- Axial force
Fig. 9. Northern wall displacement diagram for numerical model output and field data fr the middle of the wall
The maximum compressive axial force occurred in the main diagonal members of the north wall with a value of 558 (KN), which is the result of the surcharge of the building in its side and the differences in the soil height beside it, and the maximum tensile force has been created along the inner inclined member of the western wall with a value of 325 (KN), because the maximum displacements have occurred in the middle of the western wall. Moreover, these displacements have causes a compressive force along the horizontal member of the trusses (Fig.10). The only difference between the northern and western wall is locating a 6- story building near to the western in addition to the effects of a 5-story building. It applies more lateral earth pressure, displacement and axial forces to its side.
Fig. 10. Axial force distribution along the truss structure elements
As mentioned before the maximum deformation along the western side is slightly more than the northern wall and their structure is subjected to more axial forces. In figure 11 and 12 the maximum axial forces along the northern and western walls are illustrated respectively
Fig. 11. The maximum and minimum axial force of the northern wall truss structure
Fig. 12. The maximum and minimum axial force of the western wall truss structure
- Factor of safety
- Axial force
To evaluate the support structure performance here we did a safety factor calculation using Plaxis software. The results obtained from the numerical study showed that the factor of safety for the system is 2.5. The truss structure elements and the shotcrete walls behavior were considered to be linear elastic during the procedure, which causes an increase in FOS compared to the reality.
-
- CONCLUSIONS
In this study an urban surface excavation supported with truss structure for a case study have been investigated. Some simplifying assumptions were introduced and the modelling procedure were optimized to reduce run time and increase the accuracy. Here after the validation we started to examine the structural and geotechnical performance of the excavation and the guardian structure. The maximum displacement occurred through the western wall, and generally it is obvious that the more deformation causes the more forces along the members. Walls with higher elevation caused more pressure on the structure. To evaluate the guardian structure efficiency we calculated the safety factor. Safety factor for the excavation is 2.5, but this number can be in a lower grade if we apply a nonlinear behavior to the structure properties. However this action will increase run time dramatically. It is advised that for more accuracy nonlinear material behavior for structural elements should be considered.
REFERENCES
[1] Khosravi, F., Soorani, S. R., & Ahimoghadam, F. (2020). Evaluation of Constitutive Soil Models in Soil Nail Wall Using Centrifuge Model. Amirkabir Journal of Civil Engineering, 52(1), 171-186. [2] Nejjar K, Dias D, Cuira F, Chapron G, Le Bissonnais H. Numerical modelling of a 32 m deep excavation in the suburbs of Paris. Eng Struct.2022;268(March). doi:10.1016/j.engstruct.2022.114727
[3] Costa PA, Borges JL, Fernandes MM. Analysis of a braced excavation in soft soils considering the consolidation effect. Geotech Geol Eng.2007;25(6):617-629. doi:10.1007/s10706-007-9134-7
[4] Usefi, Saeed and Azizi peste bagloo, Hamid Reza and Salehi Alamdari, Negar,1400,Three-dimensional analysis of improving the reliability and serviceability of truss guard structures in terms of side bracing effects,8th National Conference on Applied Research in Civil Engineering, Architecture and Urban Management,Tehran,https://civilica.com/doc/1395304 [5] Maleki M, Nabizadeh A. Seismic performance of deep excavation restrained by guardian truss structures system using quasi-static approach. SN Appl Sci. 2021;3(4):1-17. doi:10.1007/s42452-021-04415-9 [6] Taylor P, Teo PL, Wong KS. The IES Journal Part A: Civil & Structural Engineering Application of the Hardening Soil model in deep excavation analysis. 2012;(August 2014):37-41. doi:10.1080/19373260.2012.696445 [7] Schanz T, Vermeer PA, Bonnier PG. The hardening soil model: formulation and verification. In: Beyond 2000 in Computational Geotechnics. Routledge; 2019:281-296. [8] Ammar Jalil Almosawi , Anis A. Mohamad-Ali , David A. M Jawad, 2019, Behaviour of Waler Retaining System on Sheet Piles using Finite Element Method, INTERNATIONAL JOURNAL OF ENGINEERING RESEARCH & TECHNOLOGY (IJERT) Volume 08, Issue 06 (June 2019),