
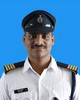
- Open Access
- Authors : Gyan Ranjan, Onam Uikey, Abhishek Kumar, Aditya Kumar Sharma, Deepak Sharma, Suresh Lade
- Paper ID : IJERTV13IS110037
- Volume & Issue : Volume 13, Issue 11 (November 2024)
- Published (First Online): 22-11-2024
- ISSN (Online) : 2278-0181
- Publisher Name : IJERT
- License:
This work is licensed under a Creative Commons Attribution 4.0 International License
Experimental Analysis of Flame-Retardant Materials with a 45-Degree Flammability Apparatus
Gyan Ranjan, Onam Uikey, Abhishek Kumar, Aditya Kumar Sharma, Deepak Sharma
B-tech ( Fire Engineering ) Student at NFSC, Nagpur , MINISTRY OF HOME AFFAIRS GOVT.OF INDIA.
Suresh Lade
M- tech ( Petrochemical Technology ) Laxminarayan Institute of Technology, Nagpur, Maharashtra
Abstract : This research paper explores the flammability characteristics of various flame-retardant textile materials using the 45-degree flammability apparatus, focusing on their potential applications in consumer apparel outside of sleepwear or protective clothing. The study adheres to ASTM D1230 standards to measure the materials’ responses to heat and flame under controlled conditions. Although this method does not directly correlate with real-world fire hazard assessments, it offers a systematic approach to examining how textiles react to ignition and burn propagation. We assessed a range of flame-retardant fabrics, evaluating parameters such as ignition time, charring, melting, and fusion behaviors. The samples were preconditioned through a cycle of dry cleaning and laundering to simulate typical wear-and-care cycles before testing, which was conducted by applying a flame to each sample in a 45-degree frame. Our results categorize the tested textiles into three flammability classes, providing insight into their potential risks and suitability for apparel use. This study underscores the need for rigorous textile testing to ensure consumer safety and highlights the efficacy of the 45-degree flammability apparatus as a cost-effective alternative to 16 CFR Part 1610 compliance testing for exploratory research on flame-retardant properties.
Keywords: Thermal Insulation, Heat Flux, Fire Retardant, 45 degrees flaminility apparatus, Nomex, Kevlar fiber..
- INTRODUCTION
The increasing demand for safer, flame-retardant materials in various industries has driven significant research into the flammability properties of fabrics. Flammability testing plays a critical role in assessing the behavior of materials when exposed to fire, providing vital information that informs the development of safer, more resilient products. Among the array of flammability tests, the 45-Degree Flammability Test Method stands out as a standardized procedure widely used to evaluate the ease with which fabrics ignite and sustain burning. This method, applied across a range of materials (excluding specific items like childrens sleepwear or certain protective garments), assesses how fabrics respond to controlled heat and flame exposure. The insights gained from this test aid manufacturers, safety experts, and regulatory agencies in identifying potential fire hazards associated with different textile materials.
The 45-Degree Flammability Test provides a consistent framework for fabric evaluation, ensuring accurate and repeatable results across different testing environments. Using SI units as the primary measurement standard, the test also
incorporates inch-pound units for international applicability, enhancing uniformity and precision. Conducted within a stainless steel chamber with a glass observation panel, the test includes safety features like an automatic ignition system and a brushing device to simulate real-life conditions and improve reliability. Although the test offers critical data on fabric flammability, it does not encompass all real-world fire risks, as various factors affect material behavior during actual fires.
In this research, we tested a range of flame-retardant materials using the 45-Degree Flammability Tester. Our objective was to compare these materials’ flammability characteristics, including ignition resistance and flame spread rates, to evaluate their suitability for different applications. This analysis aims to support advancements in fabric safety standards and promote more informed material selection in industries such as medical textiles, protective clothing, and consumer goods. The findings from this study contribute to a growing body of knowledge that can enhance fire safety in material design and application.
- MECHANISM
The 45-degree flammability test is a useful, low-cost method to understand the flammability of fabrics. However, its not meant for official testing of fabrics sold in bulk, as regulations require fabrics to meet stricter standards (16 CFR Part 1610). This test gives an early indication of fabric safety, but it doesnt replace the need for more comprehensive tests required by law.
If two labs have different results when testing the same fabric, both the buyer and the supplier need to work together to find out if their equipment or methods have biases. They should test a group of similar samples and compare results statistically. If any bias is found, they need to adjust their approach or make a mutual agreement on how to interpret future results.
Many fabrics, including those made from natural and synthetic fibers, can catch fire easily. Some can even be dangerous when used in clothing, depending on how quickly they ignite, how fast flames spread, the heat produced, and how the clothing is designed. This test measures two important factors: how easily the fabric catches fire and how fast the flames spread.
To classify fabrics into one of three flammability classes, limits are set based on experience. However, these classes dont guarantee safety under all conditions, as many factors can affect flammability, including the weather, how the fabric is prepared, and natural differences in the fabric itself.
Because finishes (like fabric treatments) and fabric surfaces can affect flammability, testing is done both before and after
cleaning. This method, though, is not used to test hats, gloves, shoes, or lining materials.
- SPECIMEN FOR TESTING
- Glass Fibre Fabric:-
Fiberglass Fabric made out of high quality E Glass Fiberglass have excellent properties like heat & flame resistant, Non- Corrosive, Continuous temperature rating upto 540 deg C. The main application for this include Expansion Joints, Pipe Lagging, Flange & Valve Covers, Safety Clothing, Hear Shields, Insulation Pads, Navy Board Facing fabrics, Welding Blankets, Insulation covers or shields.
- Silicone Rubber coated fiberglass fabric:-
Silicone rubber compounded in special formula is applied to coat or impregnate on one side or both sides of fiberglass fabrics, for use in applications which require heat resistance, spark safety, chemical resistance, or abrasion resistance. The operating temperature is from-50°C to +250°C normally. Due to its good performance on heat resistance, weatherproof, moisture proof, and chemical resistance to acid, alkali, and also good flexibility with abrasion resistance.
- Aluminum Foil Laminated Fiberglass Fabric:- Aluminized Fiberglass Cloth Series is ideal thermal insulation material combining aluminum and fiberglass. The insulation material combines many types of fiberglass, Kevlar, flame- retardant cotton, aluminosilicate ceramic cloth, silicone rubber coated fiberglass fabric and other component materials. It can be used for piping protection, engine components, construction
materials, and other uses. The excellent thermal insulation materials are great for steam heating pipelines, sound-proof materials in construction and provide a protective layer for glass wool blankets. They offer fire-resistance, anticorrosion, heat isulation, and sound absorbency. For packing materials they offer moisture resistance, mildew proof properties, fire- resistance, and anticorrosive properties.
- Graphite Coated Fiberglass Fabric:-
Graphite coated glass cloth is constructed with a glass fibre fabric which is coated on both sides with a graphite solution. The graphite coating will increase the fabric’s resistance to temperature and abrasion and can improve performance where flexing is required. It is commonly used in the manufacture of welding curtains/covers, heat shields, sleeves, connectors and insulation jackets. Graphite coated fiberglass fabric are treated with a Graphite & Silicone impregnation. A specially formulated, non shedding, lubricating graphite finish that improves resistance to both temperature and abrasion.
- Silica Fabrics:-
Silica materials are a superb high temperature insulation and can be used for a long time without changing of properties at the temperature higher than 1000 deg C for a short period of time.
We manufactures a wide range of silica fabrics with the weight from 120 to 1400 Gram/SQM with different types of finish improving their properties. One of the considerable sectors of silica fabric application – production of welding blankets, fire protective blankets, screens and curtains, casing as a thermal barrier for protection of the equipment, high temperature insulation of furnaces, turbines, screens for protection from molten metal splashes, sparks, thermal insulation.
Applications:-
As a means of high temperature insulation at up to 1200 deg C
- Thermal protection for different industries,
For refractory base, gaskets and blankets,
Protecting from flame, splashes of molten metal,
Excessive heat, as a filler for composite materials,
For the production of thermal insulation mats with basalt.
- Thermal protection for different industries,
- Ceramic Fabrics:-
Ceramic Fabrics are made from an alumino-silicate based refractory fiber. This ceramic fabric is suitable for the most extreme high temperature environments due to its low thermal conductivity and good resistance to corrosive chemicals. Because ceramic fabric with stands temperatures up to 1260°C, they are commonly used as high temperature insulation or lining in and around furnaces, boilers, and kilns.
Applications:-
Welding spark protection blankets/curtains,
Insulation Pads for Fire protection,
insulation mattress/jocket cover material,
High temperature fabric seals.
Automotive Insulation
Aerospace & Marine
- Rexine:-
Rexine is made by applying a coating of PVC on the cotton cloth. The fabric is used in airproof and waterproof packing and decoration. The fabric is being used for making seat covers and railway interiors for years. This artificial leather cloth fabric is a durable, soft, and long-lasting.
Application:-
Rexines versatility makes it a popular choice for various
applications:
- Furniture Upholstery: Sofas, chairs, and ottomans in homes and offices
- Automotive Interiors: Car seat covers and door panels
- Fashion Accessories: Bags, wallets, and shoes
- Bookbinding: Covers for notebooks and diaries
- Home Decor: Cushion covers, bed headboards, and wall panels
- Nomex:-
Unlike flame-retardant treated (FRT) materials, Nomex fibers are inherently flame resistant: the flame resistance is an inherent property of the polymer chemistry. It will not diminish during the life of the fiber, and it cannot be washed out or worn away.
The fibers low stiffness and high elongation give it textile-like characteristics that allow processing on conventional textile equipment.
Nomex meta-aramid, poly(meta-phenyleneisophthalamide), is prepared from meta-phenylenediamine and isophthaloyl chloride in an amide solvent. It is a long chain polyamide where at least 85% of the amide linkages are attached directly to two aromatic rings. The meta-oriented phenylene forms bends in the polymer chain, reducing chain rigidity as compared to the para orientation in the chemically similar Kevlar para-aramid chain. This flexible polymer chain gives Nomex more textile-like qualities while retaining high-temperature properties similar to Kevlar.
Application:-
- protect against flash fire and electric arc exposure;
- firefighter garments;
- fabrics and spun yarns for filtration applications;
- insulation in flame-resistant (FR) thermal protective apparel;
- rubber reinforcement;
- transportation textiles such as aircraft carpeting.
- Some uses for the paper products include insulation in electric motors and transformers, wire wrapping and honeycombed strength members in many aircraft.
Figure-4
- Glass Fibre Fabric:-
- PREPARATION OF SPECIMENS:-
Perform tests on the fabric as it will reach the consumer. Accomplish exploratory testing to determine the proper orientation of specimens, face of fabric and part of pattern to be tested by marking and cutting a single 50 by 150 mm (2 by 6 in.) specimen for each fabric surface, direction, and pattern and testing according to standard test procedure.
Marking and Cutting:-
Mark out the required number of specimens each 50 by 150 mm (2 by 6 in.) on the surface opposite that to be tested, with the long dimension in the direction in which burning is most rapid as established in the preliminary trials (See 8.1). Long dimension is the longer length of test specimen for purposes of this method. In cases where it is dicult to determine the direction of the lay of the nap, it is possible to identify it Laboratory Test Manual for 16 CFR Part 1610. Identify the end of each specimen toward which, and on the surface of which ame spread is most rapid by attaching a staple to it. Then cut specimens from the fabric. Place any identication markings on the side and end opposite of that to be tested.
Refurbished Fabric:-Cut a swatch large enough to provide ve or ten specimens, as indicated in , with allowance for shrinkage in dry cleaning and washing, and subject the swatch to dry cleaning and washing procedures as per sop. Specimen is a section of sample to be tested having specic dimension. Five or ten specimens are required to be tested for a complete test.
Solvent: Perchloroethylene,
commercial grade Detergent class: Cationic. Extraction time: 3 min.
Drying Temperature: 60 to 66°C (140 to 150°F). Drying Time: 18 to 20 min.
Cool Down/Deodorization time: 5 min.
Perchloroethylene is toxic and a suspected carcinogen, and the usual precautions for handling chlorinated solvents need to be taken. Perchloroethylene is to be used only under well- ventilated conditions. The solvent is nonammable. 9.2.1.3 Samples shall be dry cleaned in a load that is 80 % of the machines capacity. If necessary, ballast of clean textile pieces or garments, white or light in color, and consisting of approximately 80 % of wool fabric pieces and 20 % cotton pieces shall be used.
Specimen Mounting:-
Clamp the specimens individually in the specimen holders of the ammability tester. Insert the specimen in the frame so that the bottom edge of the specimen coincides exactly with the lower edge of the longest (top) frame. This can be accomplished by laying the specimen on the bottom (shorter) frame so that the top edge of the specimen coincides exactly with the top of the cut out portion of the frame. The stapled or marked end is placed in the uppr position during test. Bull Dog clips are usually used to hold the two halves of the specimen holder together, but other methods are acceptable. Double-faced tape is often used on the bottom half of the specimen holder to help hold the specimen taut and in place.
Brushing:-
Brush each specimen having a raised ber surface with the specimen mounted in a specimen holder. The purpose of the metal plate or template on the carriage of the brushing device is to support the specimen above the level of the top surface of the specimen holder during the brushing operation.
5 .TESTING PROCEDURE:-
-
- Steps
- Prepare the Flammability Tester:
- Ensure that the flammability tester is set up on a stable surface and is ready for use. Check that all components are clean and functional.
- Position the Specimen:
- Insert the Trial Specimen: Place the trial specimen (not a prepared one) into the specimen holder. Make sure it is securely fastened.
- Set the Holder: Adjust the specimen holder so that the longest frame or side is facing upwards. This is important for ensuring proper flame exposure.
- Adjust the Indicator:
- Position the Rack: Adjust the position of the rack on the tester so that the tip of the indicator touches the face of the specimen. This ensures that you have the correct starting point for measuring the flame’s impact.
- Set the Flame Position:
- Align the Burner: Adjust the burner and the specimen holder so that the flame will hit the vertical center of the specimen.
- Distance from the Bottom: Measure 19 mm (or 0.75 inches) up from the bottom of the specimen. Ensure that the flame is positioned at this height, keeping the indicator still touching the specimen.
- Adjust the Burner Distance:
- Set Burner Face Position: Measure the distance from the face of the specimen to the burner. It should be set at 86 mm (or about 3.4 inches). Ensure this distance is maintained while confirming the burner is correctly aligned with the specimen.
- Final observation:
- Recheck Measurements: Double-check both the 19 mm height from the bottom of the specimen to the flame and the 86 mm distance from the specimen to the burner face. Ensure everything is in place and stable.
- Valve operation:-
- Open the Fuel Control Valve: Turn on the control valve for the fuel supply.
- Remove Air from the Line: Allow about 5 minutes for any air in the fuel line to be pushed out. This helps ensure a steady gas flow.
- Ignition;-
- Ignite the Gas: Carefully light the gas once youve
allowed time for the air to clear.
- Adjust the Flame Length: Set the flame so that it measures 16 mm (about 5/8 inch) from the tip of the flame to the opening of the gas nozzle. Make sure the flame is stable and the length is correct.
- Ignite the Gas: Carefully light the gas once youve
- Remove the Specimen from the Desiccator:
- Open the desiccator carefully to avoid disturbing the environment inside.
- Using clean, dry gloves or tweezers, gently remove the mounted specimen. Be careful not to touch the specimen with your bare hands, as moisture or oils can affect the results.
- Place the Specimen in the Testing Apparatus:
- Position the specimen on the rack inside the chamber of the testing apparatus. Ensure it is securely placed and stable, as any movement could impact the test results.
- Set Up the Stop Cord:
- Take the stop cord and measure 9.5 mm (approximately 3/8 inch) from the lower surface of the top plate of the specimen holder.
- Adjust the stop cord so that it is parallel to this surface and positioned at the correct height. Make sure it is straight and secure.
- Attach the Stop Weight:
- Locate the stop weight thread guide on the apparatus.
- Hook the stop weight in place close to the guide, ensuring it is positioned just below it. This setup will allow the stop weight to function correctly during the test.
- Timing the Exposure to the Flame:
- Be ready to expose the specimen to the flame.
- Start a timer as soon as you remove the specimen from the desiccator. You have 45 seconds to complete this step.
- Within this time frame, ensure that the specimen is correctly positioned for the flame exposure as per your testing protocol.
- Final Checks:
- Before exposing the specimen to the flame, double- check that everything is correctly set up: the specimen is secure, the stop cord is at the right height, and the stop weight is properly attached.
- Ensure that any safety measures are in place, including wearing protective equipment and having a fire extinguisher nearby.
- Expose the Specimen:
- Once you are within the 45-second window, proceed to expose the test specimen to the flame according to your testing protocol.
- Close the Door of the Apparatus:
- Gently close the door of the testing apparatus. Ensure it seals properly to prevent any drafts or air leaks, which could affect the test results.
- Prepare the Timer:
- Locate the timer that you will use for the test.
- Set the timer to zero. This prepares it for timing the duration of the test accurately.
- Check the Environment:
- Make sure that the testing area is draft-free. This means there should be no open windows, fans, or other sources of airflow that could influence the test.
- Confirm that the temperature in the testing area is at room temperature. Ideally, this should be around 20- 25°C (68-77°F). If necessary, allow the apparatus to acclimate to the room temperature before proceeding.
a)
- Confirm that the temperature in the testing area is at room temperature. Ideally, this should be around 20- 25°C (68-77°F). If necessary, allow the apparatus to acclimate to the room temperature before proceeding.
- Make sure that the testing area is draft-free. This means there should be no open windows, fans, or other sources of airflow that could influence the test.
- Finalize Setup:
- Double-check that all components of the apparatus, including the specimen and flame setup, are ready for testing.
- Ensure that any safety equipment is in place, such as protective eyewear and a fire extinguisher.
- Conduct the Test:
- Once everything is confirmed and the environment is stable, you are ready to start the test. Begin the test according to your specific protocol, keeping the environment and apparatus conditions consistent.
- Activate the Starting Mechanism:
- Press the starting lever or button to begin the test.
- Start the Timer:
- When you activate the starting mechanism, the timing mechanism begins automatically. This meas you dont need to start the timer manually.
- Apply the Flame:
- The flame is applied to the specimen for exactly 1 second. This is part of the test to measure flammability.
- Automatic Timing:
- The timing will continue until the stop cord burns through and releases the weight. This action will signal the end of the timing.
- Observations:-
- Record the time of ame spread for each specimen, and note whether the base of each specimen having a raised ber surface is ignited, charred, melted, or fused to a point where the damage is apparent on the reverse side of the specimen.
Calculate the arithmetic mean of the burn times for each direction of the material. If the burn time is less than 3.5s or if some specimens do not burn, test 5 additional samples. Average the 5 or 10 test times. Test before and after refurbishing.
Classify the results used by 16 CFR 1610 as follows: Class 1 material do not have raised surface and flame spread is 7 sec and are usually acceptable for use; Class 2 material fall between Class 1 and 3; Class 3 materials are considered unsuitable for the trade and have a flame spread of < 4s for raised surface material.
Result Table for 45 Degree Flammability Test
Average
Burn Time (s) |
Classification (Class 1, 2, 3) | Surface Type | Additional Notes |
6.7 | Class 1 | Flat | No issues |
3.1 | Class 3 | Raised | Raised surface |
5.6 | Class 1 | Flat | No issues |
2.9 | Class 3 | Raised | Raised surface |
- RESULTS AND INTERPRETATION:-
- Ignition Behaviour:-
- Ignition or Non-Ignition: The material may ignite when exposed to the flame, or it may not. Materials that ignite are classified as flammable, while those that do not are considered to have higher resistance to ignition. In some cases, the material may exhibit a delayed ignition, which could suggest a degree of fire resistance, but it still classifies as flammable.
- Flame Spread:
- Self-Extinguishing or Sustained Flame: Some materials may catch fire and then extinguish themselves quickly after the removal of the flame, which suggests low fire propagation potential. On the other hand, materials that continue to burn or spread the flame are more hazardous, as they pose an ongoing risk of fire.
- Time to Ignition and Burn Duration:
- The time it takes for the material to ignite, and the duration for
which it burns, are critical factors. Materials that take a long time to ignite and self-extinguish quickly after ignition are considered safer from a fire hazard perspective. Materials that ignite rapidly and burn for extended periods are more hazardous and may require further treatment or modification to meet fire safety standards.
- Post-Burn Damage:
- After the test, the extent of damage to the sample is assessed. This includes the presence of charring, melting, or other structural alterations. Materials that undergo significant physical degradation may be deemed unsuitable for applications requiring high fire resistance.
Team Members
- CONCLUSION:-
45-degree flammability test is a fundamental tool for evaluating the fire safety characteristics of materials, providing critical insights into their ignition potential, flame spread behavior, and burn duration. These factors collectively inform the fire- resistance classification of materials and support their safe application in fire-sensitive environments, such as construction, textiles, and transportation. By assessing how a material behaves when exposed to an angled flame, this test aids in identifying flammable versus flame-resistant materials, helping to mitigate fire risks effectively. The test’s results contribute to developing safer materials that align with industry standards and enhance safety measures across various sectors. Ultimately, the 45- degree flammability test is instrumental in advancing fire safety, as it supports the selection and use of materials that minimize fire hazards and ensure greater protection in environments where fire prevention is paramount.
ACKNOWLEDGEMENT :-
This research did not receive any specific grant from funding agencies in the public, commercial, or not-for-profit sectors.
- Developments in Science and Engineering. In Interior Finishing Materials, 1st ed.;Koca, G., Ed.; St. Kliment Ohridski University Press: Soa, Bulgaria, 2016; pp. 606618.6.Taylor, C.
- The Design, Production and Reception of Eighteenth-Century Wallpaper in Britain, 1st ed.; Routledge: London, UK, 2018;pp. 45100.7.Choi, Y.; Joe, I.; Lee, S.; Oh, K.
- An experimental study on the ignition and emissions characteristics of wallpapers. J. Mech. Sci.Technol. 2009,23, 28392847. [CrossRef]8. Al- Baldawi, M.T.
- Application of smart materials in the interior design of smart houses. Civ. Environ. Res. 2015,7, 115.9.Li, W.; Zhao, L.; Zhang, Q.; Zhao, G.
- Flame retardance and antibacterial performance of wooden wallpaper treated with compositemodied agent. Wood Res. 2016,61, 423 432.10.Tian, N.; Delichatsios, M.A.; Zhang, J.; Fateh, T.
- A methodology and a simple engineering re performance model for intumescentre retardant coatings. Fire Saf. J. 2018,98, 120129. [CrossRef]11.Popescu, C.; Pfriem,
- A. Treatment and modication to improve the reaction to re of wood and wood based productsAnoverview. Fire Mater. 2020,44, 100111. [CrossRef]12.Chen, F.; Zhu, Y.; Chen, F.; Dong, L.; Yang, R.; Xiong, Z.
- Fire alarm wallpaper based on re-resistant hydroxyapatite nanowireinorganic paper and graphene oxide thermosensitive sensor. ACS Nano 2018,12, 31593171. [CrossRef]13. Weil, E.D.
- Fire-protective and ame-retardant coatings- A state of the art review. J. Fire Sci. 2011,29, 259296. [CrossRef]14.Salasinska, K.; Mizera, K.; Celi
´nski, M.; Kozikowski, P.; Borucka, M.; Gajek,
- A. Thermal properties and re behavior ofpolyethylene with a mixture of copper phosphate and melamine phosphate as a novel ame retardant. Fire Saf. J.2020,115, 103137. [CrossRef]15.Cho, S.O.; Kim, Y.S.
- A study on data research for re regulations and re retardant in interior
architecture. Korean Inst. Inter. Des.J. 2010,19, 95102.16.Law Viewer,
- Fireghting System Installation Business Act. Available online: https://elaw.klri.re.kr/eng_mobile/viewer.do?hseq=54812&type=part&ke y=12 (accessed on 3 May 2023).17.Sabee, M.M.S.M.; Itam, Z.; Beddu, S.; Zahari, N.M.; Kamal, N.L.M.; Mohamad, D.; Zulkepli, N.A.; Shaq, M.D.; Hamid, Z.A.A.
- Flame retardant coatings: Additives, binders, and llers. Polymers 2022,14,
2911. [CrossRef] [PubMed]18.Boonmee, N.; Quintiere, J.G.
- Glowing ignition of wood: The onset of surface combustion. Proc. Combust. Inst.2005,30, 23032310.[CrossRef]19.Wang, S.; Wang, X.; Wang, X.; Li, H.; Sun, J.; Sun, W.; Yo, Y.; Gu, X.; Zhang, S. S
- Surface coated rigid polyurethane foam withdurable ame retardancy and improved mechanical property. J. Chem. Eng. 2020,385, 123755. [CrossRef]20.Huang, Y.; Jiang, S.; Liang, R.; Liao, Z.; You, G.
- A green highly-effective surface ame-retardant strategy for rigid polyurethanefoam: Transforming UV-Cured coating into intumescent self- extinguishing layer. Compos. Part A Appl. Sci. Manuf.2019,125, 105534. [CrossRef]21.Dro´zdziel-Jurkiewicz, M.; Bienia´s, J.
- Evaluation of surface treatment for enhancing adhesion at the metal- composite interface inbre metal-laminates. Materials 2022,15, 6118. [CrossRef]22.Yang, H.; Yu, B.; Song, P.; Maluk, C.; Wang, H.
- Surface-coating engineering for ame retardant exible polyurethane
foams: Acritical review. Compos. Part B Eng. 2019,176, 107185
- ASTM ( D1230 10 )
- REFERENCES:
- Pile, J. Interior Design, 4th ed.; Prentice Hall: Hoboken, NJ, USA, 2007;
pp. 1156.2. Liu, C.; Deng, T.; Zhou, S.; Yan, R.; Huang, L.
- Experimental investigation on re assessment for typical interior wallpapers. FireTechnol. 2022,58, 9911009. [CrossRef]3.Yang, H.; Kim, D.; Kim, H.
- Combustion and mechanical properties of re retardant treated waste paper board for interior nishingmaterial. J. Fire Sci. 2002,20, 505517. [CrossRef]4.Konecki, M.; Galaj, J.
- Flame transfer through the external walls insulation of the building during a re. Procedia Eng.2017,172,529535. [CrossRef]5.Efe, R.; Matchavariani, L.; Yaldir, A.; Levai, L.