
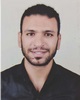
- Open Access
- Authors : Mohamed Ibrahim Hussien , Tarek Abdel Moneim Sharaf , Ibrahim Hassan El Kerch
- Paper ID : IJERTV11IS100021
- Volume & Issue : Volume 11, Issue 10 (October 2022)
- Published (First Online): 13-10-2022
- ISSN (Online) : 2278-0181
- Publisher Name : IJERT
- License:
This work is licensed under a Creative Commons Attribution 4.0 International License
Experimental Behaviour of Circular Filled Tube Long Steel Columns with and Without Shear Connectors Due to Axial Load
Mohamed Ibrahim Hussein
Teacher assistant of steel structures, Faculty of Engineering, Suez Canal University, Egypt.
Tarek Abdel Moneim Sharaf
Associate professor at, Faculty of Engineering, Port Said University, Egypt.
Ibrahim Hassan El Kerch
Prof of steel structures, Faculty of Engineering, Suez Canal University, Egypt.
Abstract:- Experiment tests were conducted to study the effect of in-fill concrete and shear connectors on long-filled steel tubes subjected to axial load. Nine experiment tests were conducted to study the maximum carrying load, stress-strain curves, load-deformation curves, and failure shape. The results were studied and compared to prove that in-fill concrete improved the axial load capacity of steel tubes and placing shear connectors improved the filled tube steel columns and their failure modes. The experiment results were compared with the calculation from design codes namely, ECP [1], EC4[2], AISC[3], and ACI[4] The comparison of results showed that EC4 closely expected the load-carrying capacity.
Keywords: Long-filled steel tube, shear connectors, axial load.
-
INTRODUCTION
In modern construction performance, engineers need to use all of the available advantages of the various materials so they use composite construction because of the structural and constructional advantages of both concrete and steel. Presently composite floor systems are widely utilized in a steel buildings in the form of composite beams. Several composite steel-concrete structural systems have been used during the last few decades in the construction of high-rise buildings; the composite columns are the most important. As compared to composite floor systems, composite columns are still not very popular in Egypt, although they are extensively used in Japan and the Fareast. In Japan and China, they were used in buildings of all heights primarily because of their seismic resistance; in the rest of Asia, they are often used in tall buildings to reduce drift due to typhoon (hurricane) winds. Until the middle of the nineteenth century, engineers were usually encasing steel columns with low-strength concrete primarily to protect them from fire. To construct a more economical structure, the strength of both steel and concrete must be used. Composite sections and especially composite columns have a very important advantage, due to their high normal and bending stiffness due to steel resistance in tension and its ductility as well as buckling resistance of concrete. Composite columns allow structural engineers to achieve
less column cross-section compared with reinforced concrete columns and bare steel columns due to less vertical. In the past, structural engineers had used closed- form solution analysis to obtain the full column capacity, but widely using numerical computer analysis especially using finite element programs allows the engineers to solve complicated problems with high analysis accuracy.
-
OBJECTIVE
The main objective of this experiment is to find the performance of composite columns filled with concrete and unfilled, also study the effect of the presence of shear connector and absence, and study the maximum axial load- bearing capacity, ductility, and different deformation shape.
-
LITERATURE REVIEW
G Sunil Reddy and G N Sreekanth[5] present experimental work on 2 circular specimens of concrete-filled steel tube (CFST) filled with high-strength concrete M-40 they used the filled tube with concrete because it can decrease the local buckling of the steel tube and the concrete core itself also added admixture (superplasticizer) to increasing the workability, with shear connector and without subjected to axial load the results of investigation observed the bond strength between concrete core and steel tube is more critical for high strength concrete otherwise Baskar et al (2012) used fly ash or silica fume as light aggregate and the results of the experiment with light aggregate offer high bond strength and compressive strength than normal concrete but the reduction on the axial load capacity of normal concrete with the losing of the bond between steel tube and concrete is negligible so EUROCODE 4[1] gives the best estimation for both (CFST) with normal and high strength concrete.
Tian-Yi Song; Zhong Tao Han [6] present experimental work of 12 specimens (circular and square) at room temperature they used stainless, carbon steel, normal, expansive concrete, studs, and, internal rings They found that the best process to increase the bond strength is welding internal rings, the second and the third process using studs or expansive concrete, but a static analysis
indicates that the bond strength decreases with increasing concrete strength and the peak bond strength was touched when the shear studs were sheared off from steel tube. Also, because of the friction distribution of section shape, they found that it t was easy to form bond strength in the circular column compared with the square column. They observed that no local buckling happened with the specimens of the normal interface. With shear studs, just the concrete was pushed down through the steel tube. Outward local buckling occurred with the specimens of internal rings and especially happened near the rings. They concluded that the concrete type, steel type, and temperature level did not affect the failure mode.
Mohamed Ghannam; Zhong Tao; and Tian Yi Song [7] conferred six specimens of concrete-filled stainless-steel columns (CFST) with entirely different cross-sectional (circular and square), with axial load, with steel reinforcement, and without exposed to the fireplace. They complete that stainless steel is far higher in value than steel; however, stainless steel had additional advantages reminiscent of high corrosion resistance, maintained, and extraordinarily durable. The circular column failed due to the overall buckling, and the local buckling occurred only near the mid-height. For the square column, local bulking happened on the steel tube, and the reinforcement bars had no noticeable effect on the failure mode.
-
MATERIALS AND SPECIMENS TABLE
4.1Cement
The cement used in the experimental study was ordinary Portland cement that complied with the
Egyptian Standard Specifications No. 203-2003, and the water-cement ratio is 40%.
4.2Aggregate
The aggregate used for the concrete mix was dolomite stone parts and sand.
-
Fine aggregates
Natural sand was used in the construction of concrete specimens. It was clean, graded, and free from deleterious materials.
-
Coarse aggregates
The coarse aggregate is dolomite stone particles with a nominal maximum size of 25 mm. it was clean and free from silt, clay, and loam. Two sizes of coarse aggregate were used size 1, and size 2. The two sizes were mixed by 60:40 to give good grading.
4.3Water
Potable water was used for mixing concrete and curing.
-
Steel Tube
Cold-formed section of mild steel with a yield strength of 242 MPa and ultimate strength of 372 MPa as shown in a stress-strain curve in Fig (1), mild steel characterized by its malleability, ductility, and high tensile strength also is commonly used in construction.
Fig(1) stress-strain curve for mild steel.
-
4.4.1. Steel tube cross-section
There were nine circular columns with a diameter of 100
mm steel wall thickness of 2 mm and high of 1500mm.
-
4.4.2. Shear connectors
-
Three filled tube circular columns were placed with shear connectors. Shear connector diameter is 3 mm with length
30 mm and grade 4.6 distributed at 50 mm staggered around column surface.
Table 1: Number of specimens.
series. no
circular(C) specimens without fire
filled (f)
hollow (h)
with shear connector(s)
1
Cp
1
2
Cp
1
3
Cp
1
4
Cs1
1
5
Cs2
1
6
Cs3
1
7
Cf1
1
8
Cf2
1
9
Cf3
1
-
-
EXPERIMENTAL STUDY
The author experiment with nine Specimens (Cf1) (Cf2) (Cf3) (Cp) (Cp) (Cp) (Cs1) (Cs2) (Cs3) with strain- gauge at four completely different locations gauge no (1, 2) at 18 cm from top and gauge no (3, 4) at 75 cm from the top as Fig(2), creating a chart with the results of every strain gauge and therefore the axial load of each strain gauge as figures (2)and chart of the global deformation and therefore the axial load as figures (3).
Figure (1) location of strain gauge (1, 2, 3, and 4)
150
AXIAL LOAD (KN)
300
AXIAL LOAD (KN)
100
200
50 Cp
(Ch)strain gauge 1 Cp
100
Cf1
(Cf)strain gauge 1 Cf2
Cf3
MICRO-STRAIN
0
Cp
MICRO-STRAIN
0
0 5000 10000 15000 20000 25000
0 5000 10000
Figure (2. A) chart of strain gauge no 1 of three circular hollow tubes (Ch) specimen.
Figure (2. E) chart of strain gauge no 1 of three circular filled tubes with concrete (Cf) specimen.
150
AXIAL LOAD (KN)
100
50
Cp
(Ch)strain gauge 2 Cp
AXIAL LOAD (KN)
300
200
100
(Cf)strain gauge 2 Cf1 Cf2
MICRO-STRAIN
0
0 2000 4000
Cp
MICRO-STRAIN Cf3
0
0 1000 2000 3000 4000 5000
Figure (2. B) chart of strain gauge no 2 of three circular hollow tubes (Ch) specimens.
Figure (2 .F) chart of strain gauge no 2 of three circular filled tubes with concrete (Cf) specimens.
150
AXIAL LOAD (KN)
100
50
0
Cp Cp Cp
(Ch)strain gauge 3
MICRO-STRAIN
350
AXIAL LOAD (KN)
300
250
200
150
100
50
(Cf)strain gauge 3
MICRO-STRAIN
Cf1 Cf2 Cf3
0 1000 2000 3000 4000 5000
0
0 2000 4000 6000 8000 10000
Figure (2. C) chart of strain gauge no 3 of three circular hollow tubes (Ch) specimens.
150
Figure (2 .G) chart of strain gauge no 3 of three circular filled tubes with concrete (Cf) specimens.
AXIAL LOAD (KN)
100
50
0
Cp
(Ch)strain gauge 4 Cp
Cp
MICRO-STRAIN
0 1000 2000 3000
AXIAL LOAD (KN)
300
200
100
0
Cf1
(Cf)strain gauge 4 Cf2
Cf3
MICRO-STRAIN
0 2000 4000 6000
Figure (2.D) chart of strain gauge no 4 of three circular hollow tubes (Ch) specimens.
Figure (2 .H) chart of strain gauge no 4 of three circular filled tubes with concrete (Cf) specimens.
250
AXIAL LOAD (KN)
200
150
100
50
0
(Cs)strain gauge 1
MICRO-STRAIN
Cs1 Cs2 Cs3
Cp
Cp Cp FEM
160
140
AXIAL LOAD (KN)
120
100
80
60
40
20
0
0 10000 20000 30000
Figure (2 .I) chart of strain gauge no 1 of 3 circular filled tubes with shear connectors (Cs) specimens.
0 5 10 15 20 25 30
DEFORMATION(mm)
Figure (3 .A) chart of global deformation of three circular hollow tubes) Ch( specimens.
250
AXIAL LOAD (KN)
200
150
100
50
0
(Cs)strain gauge 2 Cs1 Cs2
MICRO-STRAIN Cs3
0 2000 4000 6000 8000 10000
400
AXIAL LOAD (KN)
300
200
100
0
Cf1
Cf2
Cf3 FEM
0 5 10 15 20 25
DEFORMATION(mm)
Figure (2 .J) chart of strain gauge no 2 of 3 circular filled tubes with shear connectors (Cs) specimens.
250
Figure (3.B) chart of global deformation of three circular filled tubes with concrete) Cf (specimens.
AXIAL LOAD (KN)
200
150
100
50
0
Cs1
(Cs)strain gauge 3 Cs2
MICRO-STRAIN Cs3
0 5000 10000 15000 20000 25000
350
300
AXIAL LOAD (KN)
250
200
150
100
50
0
Cs1 Cs2 Cs3 FEM
0 5 10 15 20 25 30 35 40
DEFORMATION(mm)
Figure (2 .K) chart of strain gauge no 3 of 3 circular filed tubes with shear
connectors (Cs) specimens.
250
Figure (3.C) chart of global deformation of three circular filled tubes with shear connectors) Cs( specimens.
AXIAL LOAD (KN)
200
150
100
50
0
(Cs)strain gauge 4
MICRO-STRAIN
Cs1
Cs2 Cs3
-
Casting and Preparation of the Specimen
First, the square steel specimens were disaggregated to 1500 mm lengths, liner weld of size 2 mm to weld internal stiffeners at the head of the specimen at the top and bottom as shown in Fig (5) internal vertical to prevent the local buckling in the loading area as a result of the concentration of stresses.
0 5000 10000 15000 20000 25000
Figure (2 .L) chart of strain gauge no 4 of 3 circular filled tubes with shear connectors (Cs) specimens.
Figure (5) int. stiffeners
When pouring concrete on steel columns we put foam at the top and bottom to prevent the descent of concrete to the end of the column at the casting we leave 20 mm empty to prevent direct contact of the loads with concrete because concrete is considered an element to prevent the occurrence of local buckling of steel tube and the loads are transferred to it by friction with steel in a specimen without shear connector and in the specimen with shear connector the load is transmitted by friction with steel tube and bond by the shear connector.
The concrete is poured every 300 mm and then it is shocked with an electric vibrator, all the specimens filled with concrete were poured into the same concrete mixture, 6 standard cubes of the mixture were taken for testing in the lab, and the average result of the stress of the concrete was 21.89Mpa as Fig (6). The concrete grade is 25 MPa as shown in the stress-strain curve of concrete in Fig (7).
Figure (6) cubes tested in the lab
Figure (7) stress-strain curve of concrete
-
Curing
The presence of a steel tube around the concrete as a casing made it retain its moisture content and the difficulty of evaporation of water from it, so we will not put the sample in the water so that the steel is not exposed to corrosion, it is possible to paint the sample with a waterproof material, which is not economical, but the standard test cubes because they are exposed to direct air and the speed of evaporation of water from them was flooded until it reached the required compressive strength of concrete after 28 days.
-
The Method of Loading and Adjusting the Alignment
The loading is done using the head of the loading frame with a height from the ground 2 meters allowed for the main movement up or down +-250 mm and therefore there is a base of steel with a height of 0.5 meters to put the column with high 1.5 meters on it to reach the head of the loading frame and was confirmed to place the column in the middle of the base to prevent the occurrence of eccentricity and then the height of the column was weighed by the water balance to make sure that it is stable . The loading frame was down and the column loaded with an initial 1kn load and then the 4 top corner of columns was connected to 4 strings and their function to maintain the column from the occurrence of horizontal displacement to simulate the reality as in Fig(8). The column was loaded in a controlled column method with a constant displacement of 0.25 mm per second and continued loading to the time the column reached the collapse and during the experiment, the column was monitored by 2 cameras in different places, 4 strain- gauge placed at the places described as mentioned and (LVDT) was placed at the head of the loading frame another at the middle of the column as Fig (9) to measure the horizontal displacement.
Figure (8) method of fixing cylinder column
Figure (9) the locations of (LVDT)
-
-
RESULTS AND DISCUSSION
Figure (6.A) chart of global deformation of three circular tubes, hollow, filled, filled with shear connectors.
For hollow circular steel columns (Ch), it has been noted that the failure load was about 14 tons. For filled circular tube with concrete (Cf), the specimens started with lightly global buckling; then the steel tube began to have a local buckling. The unfiled concrete-made specimens of filled tube columns failed due to global buckling because concrete restrained steel walls from local buckling. It has been noted that the failure load was about 30 tons for (Cf). The presence of infill concrete did not change column failure behavior where the failure of both hollow and filled specimens was due to global buckling, not local buckling. It has been noted that the failure load of filled tube circular columns with shear connectors was about 310 tons which indicated that shear connectors presence did not affect failure load or failure mode shape.
As shown in Fig (10), Cylinder steel columns failure mode indicates that the shape of failure in cylinder hollow tubes (Ch) specimens occurred as global buckling in-between half and upper third of column height. Due to the cross- section shape, there was no failure starting due to local buckling. As for cylinder tubes filled with concrete (Cf), the concrete infill began to slip within the outer steel case; then there was local buckling or distortion occurred and spirited over the entire column height then global buckling occurred at the middle of column height to form half-sin curve deformed shape as shown at the Fig (11). For cylinder tubes filled with concrete that had shear connectors (Cs), there was no slipping between steel case and infill concrete due to shear connectors presence. (Cs) columns resisted axial loading up to global buckling occurrence with s-failure mode shape; then, there was local buckling at narrow spaces at the upper third of specimen height. Also, in the opposite direction at the lower third of specimen height, as shown in Fig (12).
Figure (10) failure shape of (Ch)
Figure (11) failure shape of (Cf)
Figure (12) failure shape of (Cs)
-
CONCLUSION
The presence of concrete improves the performance of steel columns even in the absence of direct transmission of loads on concrete. Since the concrete inside the specimens filled with concrete did not transmit any loads on it except through friction.
-
Concrete in the circular tubes filled with concrete (Cf) prevents the early failure of steel columns by global buckling. This postpones the failure process where a load of failure increases by 150%, and failure occurs as a result of global buckling outward in the first stage of failure and does not
occur suddenly where the concrete increases the period of post-failure.
-
Shear connectors have a slight effect in the circular tubes filled with concrete with shear connector (Cs)
-
Shear connectors have no significant effect on axial load capacity where the failure load of columns Cs increases by 130% than (Ch) and the failure load increases by 5% than (Cf).
-
Shear connectors presence changed failure mode shape from half sin curve to S-curve.
-
-
ACKNOWLEDGMENT
The author wishes to express his sincere thanks of Prof. Tarek Abdel Moneim Sharaf for his guidance and support throughout this investigation. The encouragement of Prof. Ibrahim ELKersh was nothing less than inspiration.
Special thanks to faculty of engineering, Port Said the concrete research laboratory for supporting the
8. REFERENCES
[1] ECP. Egyptian Code of Practice for Steel Construction and Bridges (Load and Resistance Factor Design). ECP-205 LRFD. Egypt: HBRC; 2012. [2] EC4. 1996. Design of steel and concrete structures, Part 1.1, general rules and rules doe building. Eurocode 4 DD ENV 1994-1-1:1996, British Standards Institution, London. [3] AISC (2005). Specification for Structural Steel Buildings,American Institute of Steel Construction, Chicago, IL
[4] ACI Committee 318 standard building code for structural concrete (ACI318-99). [5] G Sunil Reddy G N Sreekanth, Nandyal RGM, Nandyal Dr. S Balamuragan (load Bearing Capability of CFST Columns with and without Shear Connectors) | July 2017. [6] Tian-Yi Song1, Zhong Tao, M.ASCE2; Lin-Hai Han, M.ASCE3; and Brian Uy, M.ASCE4, Bond Behavior of concrete-filled Steel Tubes at Elevated Temperatures, DOI: 10.1061/(ASCE)ST.1943-541X.0001890. © 2017 AmericanSociety of Civil Engineers.
[7] Mohamed Ghannam1, Zhong Tao, and Tian Yi Song, Fire Resistance Tests of Concrete-filled stainless Steel Tubular Columns, Composite Construction in Steel and Concrete VII.