
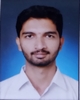
- Open Access
- [post-views]
- Authors : Akshay Zende , Akshay Nathgosavi , Rushikesh Gawade , Shrikant Patil, Vinayak Nikam, Rahul Gaji
- Paper ID : IJERTV9IS090330
- Volume & Issue : Volume 09, Issue 09 (September 2020)
- Published (First Online): 25-09-2020
- ISSN (Online) : 2278-0181
- Publisher Name : IJERT
- License:
This work is licensed under a Creative Commons Attribution 4.0 International License
Experimental Investigation of a Centrifugal Pump Working Under Gas-Liquid Two Phase Flow Condition
Akshay Zende, Akshay Nathgosavi, Rushikesh Gawade, Shrikant Patil, Vinayak Nikam
Dept. Of Mechanical Engineering
Aannasaheb Dange College of Engineering and Technology, Ashta.
Rahul Gaji (Asst. Prof.) Dept. of Mechanical Engineering
Aannasaheb Dange College of Engineering and Technology, Ashta.
Abstract The centrifugal pump operation under gas-liquid two phase flow condition is a common problem in the oil and gas industry. Same problem is encountered in electrical submersible pumps. Moreover in the loss of coolant accidents (LOCA) the water in the pressurized water reactor flashes into steam and pump is operated in steam-water two phase flow condition. The performance of the centrifugal pump is found to be decreased under gas-liquid two phase flow condition. However, the limited literatures are available for the study. In this scenario, this paper presents the experimental work to investigate the performance of centrifugal pump operated in gas-liquid two phase flow condition. The performance of pump working in water phase flow condition is analyzed at different rotational speed to validate the result with standard performance characteristics. Then experiments are performed by introducing the air at inlet of a pump. The performance of a pump working under air-water flow condition is found to be deteriorated continuously from part load to overload operating condition.
KeywordsCentrifugal pump; single phase flow; two phase flow; performance.
-
INTRODUCTION
In the nuclear industries, the coolant (water) is pumped under high pressure to a reactor core to remove the heat. The nuclear reactors have proven to be safe; however, there is always a chance of accidents leading to radioactive leakage. The emphasis in the nuclear industries and research organizations is on the understanding of the reliability and safety mechanism and accident situation. There are several hypothetical accident situations, which may give rise to core disruption and radioactive leakage. One of the most severe is LOCA, which may occur due to leakage of coolant in the rector system components.
The centrifugal pumps are normally used to force the water in the coolant circuit. During the normal operation of the pump, there is only liquid flow through the pump passages and single phase analysis is used to study the performance of the pump. However, during operational transients or LOCA condition, the recirculating coolant of Pressurized Water Reactor (PWR) may flash into steam due to loss of line pressure [1]. The pressurized water now contains vapor, the amount of which will depend upon the extent of the transient or accident condition. Centrifugal pump become unable to generate the same head in gas-liquid two phase flow condition as that of the single phase flow case [1,2, 4]. Moreover, head is almost lost in the accident situation [1, 2]. From a PWRs safety point of view, it is therefore essential to understand such
phenomena and develop the capability for accurately predicting and improving the performance of PWRs Centrifugal Cooling Pump under the gas-liquid two phase flow conditions.
Similar situations also encountered in the process industry, production and transport of oil, which often is accompanied by natural gas. An important application of high economic significance is the pumping and transport of oil-gas mixture with the electric submersible pumps.
Over the period of time various researchers investigated the performance of a centrifugal pump under gas- liquid two phase operating condition. A numerical model of radial flow pump working with gas-liquid was developed by considering the air compressibility and fluid viscosity [3]. The video recording with high speed camera was employed to understand the physical phenomenon of gas-liquid interaction in the impeller [5]. In addition to this various flow pattern inside the multiphase (water-air) centrifugal pump was observed [9]. The numerical analysis was carried by various authors to understand the influence of gas void fraction on the performance of electric submersible pumps and flow physics in the flow domain of the pump [6,7,8].
In spite of the availability of good literatures, the lack of understanding of the flow dynamics of the centrifugal pump has been identified due to complex nature of gas-liquid two phase interactions. Moreover it is very important to investigate the characteristics of a Centrifugal Pump operated under gas- liquid two phase flow condition which is not commonly provided by the manufacturers. Therefore objective of this paper is to investigate the characteristics of the centrifugal pump working under gas-liquid two phase flow condition.
-
EXPERIMENTAL SETUP
For the present study, end suction centrifugal pump with head, discharge and speed of 5 m, 1.3 lps and 1650 rpm respectively is selected. The Pump consists of closed impeller with five numbers of blades. The photographic view of the test rig is shown in Fig. 1. The test rig consists of hydraulic and pneumatic circuit.
-
Hydraulic Circuit
A Hydraulic circuit consists of Booster pump, Centrifugal pump to be tested equipped with dimmer and energy meter, Sump and flow measuring tank. The discharge is measured by Rota meter connected at the outlet of Centrifugal pump which is calibrated with the flow measured by the measuring tank. The flow rate of water is controlled by the flow control valve.
A separate flow control valve is fitted at the outlet of booster pump. Booster pump is used to maintain the pressure at the inlet of centrifugal pump to be tested. The centrifugal pump is connected with the DC prime mover with the belt drive. The speed of the centrifugal pump is controlled by supplying variable voltage from dimmer.
-
Test Rig
-
Introducing Air in The Hydraulic Circuit
Fig.1. Photographic view of the Test rig
The electric power provided to prime mover is measured by the energy meter. The head developed by the centrifugal pump is evaluated from the pressure measuring devices connected at inlet and outlet of the centrifugal pump and total losses occurred. The speed of the pump is measured by the contact type of tachometer. The specifications of various measuring devices are listed in Table 1.
Table I. General Specification of Various Instruments
Parameters
Measuring Device
Range
Accuracy
Inlet Pressure
Vacuum gauge
0-760 mm of Hg
+/- 1 mm of Hg
Outlet Pressure
Pressure Gauge
0-1.06 kg/cm2
+/- 0.1 kg/cm2
Speed
Tachometer
0-5000 rpm
+/- 1 rpm
Discharge
Rotameter
0-12 lps
—
-
-
Pneumatic Circuit
The pneumatic circuit of test rig consists of a Reciprocating compressor, Flow control valve, Venturimeter and Air entrainment system. The reciprocating compressor supplies the compressed air to the pneumatic circuit. The flow rate of air is controlled by flow control valve. The flow rate of air is measurd by the venturimeter. The air entrainment system consists of a pipe whose outer peripheri is drilled in such a way that it can create the air bubble diameter from 0.5 mm to 4 mm. The entrained air is mixed with the water at the inlet duct of a centriugal pump.
The specification of venturimeter is as follows: The inlet diameter of venturimeter: 25 mm
The throat diameter of venturimeter: 12.5 mm The coefficient of discharge: 0.98
-
-
RESULT AND DISCUSSION
The performance of a Centrifugal pump is obtained for single phase (water) and air-water two phase flow operating condition.
Finally, complete content and organizational editing before formatting. Please take note of the following items when proofreading spelling and grammar:
-
Performance under single phase (water) operating condition
The performance of a centrifugal pump is obtained at different rotational speed i.e. 1350, 1500, 1650 and 1800 rpm.
Fig.2. Performance of a centrifugal pump at different rotational speed
The discharge from the pump is altered by adjusting flow control valve and evaluated the performance parameters i.e. head, output power, input power and efficiency. The performance curve of a pump operated under water medium is shown in Fig. 2. All the curves follow the trends of standard centrifugal pump.
-
Performance under air-water two phase flow condition
The air is introduced in the hydraulic circuit of a centrifugal pump to analyze its performance. The flow control valve of an air is adjusted to keep the mass flow rate constant. By keeping the same mass flow rate of air i.e 2.45 kg/s, the discharge of water is varied and performance parameters of the pump are evaluated. The performance of a pump is analyzed for 1600 rpm rotational speed. The performance curve for both water phase and air-water phase is shown in Fig. 3.
Fig.3. Performance of a centrifugal pump at air-water flow medium
The result showed that the head curve is continuously below to the curve obtained for water phase flow from part load to overload condition. The output power and efficiency of the pump for air-water is also below of the water phase flow from part load to overload condition. The drop in the efficiency of pump is due to increase of the hydraulic losses and accumulation of air pockets in the pump flow domain. The Best efficiency point (BEP) is shifted towards lower flow rates.
-
-
CONCLUSION
In the present study, the operating characteristics of end suction centrifugal pump are carried out by experimental approach. The experiments are performed at water phase and air-water two phase flow operating condition. The performance of the pump is deteriorated by introducing the air. The head delivered by the pump is less in two phase flow condition as compared with water phase. The efficiency of the pump is decreased from
59.63 % to 39.95%. So it is highly recommended to optimize the centrifugal pump to increase its performance under air- water two phase flow condition.
ACKNOWLEDGMENT
The authors are sincerely acknowledge the department of mechanical engineering (ADCET, Ashta) for providing the experimental facility and supported this work.
REFERENCES
-
M. Murakami and K. Minemura, Effects of entrained air on the performance of centrifugal pump (First report, Performance and flow conditions), Bull., JSME. 17 (1974) 1047-1055.
-
M. Murakami and K. Minemura, Effects of entrained air on the performance of centrifugal pump (Second report, Effects of number of blades), Bull., JSME. 17(1974) 1286-1295.
-
K. Minemura, T. Uchiyama, S. Shoda and K. Egashira, Prediction of air water two phase pump performance of a centrifugal pump based on one dimensional two fluid model, ASME Journal of fluids engineering. 120 (1998) 327-334
-
G. Noghrehkar, M. Kawaji, A. Chan, H. Nakamura and Y. Kukita, Investigation of centrifugal pump performance under two phase flow conditions, ASME Journal of fluids engineering. 117 (1995) 129-137.
-
A. Poullikkas, Effects of two-phase liquid-gas flow on the performance of nuclear reactor cooling pump, Progress in nuclear energy. 42 (2003) 3-10.
-
J. Caridad and F. Kenyery, CFD analysis of electrical submersible pumps (ESP) handling two phase mixture, Journal of energy resources technology. 126 (2004) 99-104.
-
J. Caridad and F. Kenyeri, Slip factor for centrifugal impellers under single and two phase flow conditions, ASME Journal of fluids engineering. 127 (2005) 317-321.
-
J. Caridad, M. Asuaje, F. Kenyery, A. Tremante and O. Aguillon, Characterization of a centrifugal pump impeller under two phase flow condition, Journal of petroleum science and engineering.63(2008) 18- 22.