
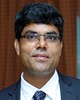
- Open Access
- Authors : D. K. Shinde , Ketan Ghorpade , Pramod A Naik , D N Raut
- Paper ID : IJERTV10IS050218
- Volume & Issue : Volume 10, Issue 05 (May 2021)
- Published (First Online): 21-05-2021
- ISSN (Online) : 2278-0181
- Publisher Name : IJERT
- License:
This work is licensed under a Creative Commons Attribution 4.0 International License
Experimental Investigation of Grit Blasting Parameters on Alpha Case Removal of Forged Alloy Part Ti-6Al-4V used in Aviation Industry
Ketan Ghorpade1
1, PG Student,
Department Production Engineering, Veermata Jijabai Technological Institute Mumbai
India 400019
Pramod A. Naik2
3,Ph D Scholar,
Department Production Engineering, Veermata Jijabai Technological Institute Mumbai
India 400019
D. K. Shinde3
3Associate Professor,
Department Production Engineering, Veermata Jijabai Technological Institute Mumbai
India 400019
D. N. Raut4
4Professor,
Department Production Engineering, Veermata Jijabai Technological Institute Mumbai
India 400019
Abstract Titanium and its alloys are attractive engineering materials used in aerospace industry because of their superior mechanical properties such as high specific strength and excellent corrosion resistance. Ti6Al4V alloy commonly used for manufacturing components in jet engines, such as fan blades, disks, wheels and sections of the compressor where the maximum temperature is in the range of 300450 °C. Titanium forged parts are heated above 900°C during forging undergoes reduce roll, blocker, flattener, finisher, trimming etc. processes for producing final forging. During this process when surface of forged part gets contact with oxygen from environment and producing oxide layer. This oxide layer is commonly known as alpha case. The alphacase layer has adverse effect on mechanical properties such as ductility, fracture toughness and especially the fatigue life when an engine component is subjected to dynamic loading. The effect of grit blasting parameters on the alpha case removal and surface roughness of Ti6Al4V alloy was examined using the Taguchi designs of experiments and Grey relational analysis.
KeywordsAlphacase, Taguchi design, Grey relational analysis, Surface Roughness, ANOVA, Grit Blasting Parameters
-
INTRODUCTION
During titanium forging when heated parts are in contact with atmospheric oxygen forms oxide layer on surface called as alpha case[1]. Failure of titanium forged parts may be causes due to crack propagation on alpha case layer present on the surface. Etching is the process which removes the alpha case layer and avoids formation of cracks on the surface. This process involves use of hazardous chemicals like concentrated hydrofluoric acid (HF) and nitric (HNO3) acid with required proportion, which makes this process dangerous and required proper attention and safety measures to carry out process. Chemical etching also have adverse effect on part surface by introducing pitting and/or intergranular corrosion and thus affects the fatigue strength[2]. Grit blasting can be used as alternate process for
etching and can be used for removing alpha case layer by applying proper process parameters. Grit blasting process involves various process parameters like grit selection, exposure time, blasting pressure, blasting angle, distance of nozzle from the part surface. Hence it is required to develop scientific method to have both economic and damage free grit blasting surface in case of titanium forged parts.
Grit Blast cleaning with abrasive media removes old coatings, rust, and other unwanted material from a surface, and creates an anchor pattern to allow new coatings to adhere better. Manufacturers who turn to grit blast cleaning as an environmentally responsible alternative to chemical stripping processes often realize substantial cost savings as well.
-
EXPERTIMENTAL PROCEDURE
-
Material
Titanium forged flaptrack Prolongations of material Ti6Al4V is used in experiment. The flaptrack is used in wings of Boeing 737 for aviation purpose. For experimental trails, the extracted prolongations are taken having dimensions height 48mm; width 77mm; length 120mm. The flaptrack material is given in table 1.
Table 1: Chemical composition of Ti6Al4V flaptrack
El e m en t
Al
V
Fe
O
C
N
H
Y
Oth er
Ti
%
w ei gh t
6.
75
4
. 5
0
0.
30
0
.2
0
0
. 0
8
0.05
(500
ppm
)
0.01
25
(125
ppm
)
0.00
5
(50
ppm
)
0.5
0
remai ning
-
Prolongation and Bracket Preparation
Bracket preparation is carried out for experimental work. Total 8 Prolongation are used to make 16 trials and for that it is required to mask half portion of prolongation. To mask that portion bracket preparation is done having dimensions 200mm×200mm×100mm as shown in figure 1 A). dia. 16mm and dia. 13mm rods are taken out from bracket which will further used for locating of prolongation while experimental trails.
Figure 1: Shows A) Flaptrack Prolongation; B) Bracket
-
Trail Setup
asted s
asted s
Fig 2a-e shows the trial setup for the experimentation of grit blasting of the flaptrack prolongation and bracket component. This experiment consists of air receiver tank, air drier unit, hopper, and nozzle (L9 mm). For measuring alpha case hardness Clemex micro-hardness tester is used and Mitutoyo surface roughness tester is used for
Table 2 Grit blasting parameters and their levels
Process Parameter
Symbol
Level 1
Level 2
Level 3
Level 4
Nozzle Distance (mm)
A
300
350
400
450
Blasting Angle (Degree)
B
30
45
60
75
Blasting Time (Second)
C
60
90
120
150
Blasting Pressure (Bar)
D
4.5
5.0
5.5
6
-
-
DESIGN OF EXPERIMENT AND TAHUCHI METHOD
The Taguchi method is an optimization technique which is widely used in engineering analysis. This method reduces the no. of experimental runs and cost associates with it. The Taguchi method uses a loss function to calculate the deviation between the experimental values and the desired values. The design of experiment (DOE) was based on Taguchi design considering four factors each at four levels. In the present analysis total number of runs = L16 have been taken. The experimental results for alpha case depth (ACD) and surface roughness (Ra) are depicted in Table 3 for 16 runs. Both alpha case depth is measured on transverse section of mounting and surface roughness were measured at surface of grit blasted prolongation of flaptrack as shown in Fig. 1
checking surface roughness of grit bl
-
urface.
-
B).
The effective use of Taguchis Orthogonal Array
a Approach for predicting the effects of individual process parameters on thickness of deposited layer in powder coating process. An orthogonal array approach and the signal to noise ratio have been used to understand the factor effects in powder coating of EN8 Steel Shaft. Experimental results are also provided to confirm the effctiveness of this
d e approach [4].
The body component traceability throughout the manufacturing process has the potential to change the way we approach the quality assurance and control issue. Thus, there is huge scope for data collection and analysis. This will assist
Figure 2. a) Air receiver tank, b) Air Drier, c) Hoper Unit, d) Surface roughness testing and e) Clemex Microhardness tester.
-
Experimental Parameters and levels
Grit mix, grit flow rate, intensity, Grit blasting angle, grit velocity, distance between nozzle to work piece, coverage area, grit blasting pressure and exposure time are the input parameters. Since some parameters such as velocity, intensity, and coverage are difficult to control, controllable influential parameters such as grit mix selection, grit blasting angle, grit blasting angle and exposure time factors were considered in the present investigation. Pilot experiments are carried among GH050 and GH025 nominal size are in mm from which GH050 gives promising results to remove maximum material. Other controllable factors levels are determined from literature base. These shot peening parameters along with their levels are shown in Table 2.
to achieve the extremely ambitious goal of Zero Defect i. e. the title of World Class Manufacturer[5].
Sr.
Nozzle Distance mm
Blasting Angle Degree
Blasting Time Second
Blasting Pressure Bar
ACR (HV)
Ra (µm)
1
300
30
60
4.5
1
6.470
2
300
45
90
5.0
8
8.288
.3
300
60
120
5.5
6
5.816
4
300
75
150
6.0
11
6.659
5
350
30
90
5.5
18
5.505
6
350
45
60
6.0
4
7.586
7
350
60
150
4.5
19
5.877
8
350
75
120
5.0
26
7.654
9
400
30
120
6.0
24
4.629
10
400
45
150
5.5
16
6.794
11
400
60
60
5.0
9
4.536
12
400
75
90
4.5
19
6.285
13
450
30
150
5.0
17
3.674
14
450
45
120
4.5
3
7.245
15
450
60
90
6.0
18
6.333
16
450
75
60
5.5
31
7.461
Sr.
Nozzle Distance mm
Blasting Angle Degree
Blasting Time Second
Blasting Pressure Bar
ACR (HV)
Ra (µm)
1
300
30
60
4.5
1
6.470
2
300
45
90
5.0
8
8.288
.3
300
60
120
5.5
6
5.816
4
300
75
150
6.0
11
6.659
5
350
30
90
5.5
18
5.505
6
350
45
60
6.0
4
7.586
7
350
60
150
4.5
19
5.877
8
350
75
120
5.0
26
7.654
9
400
30
120
6.0
24
4.629
10
400
45
150
5.5
16
6.794
11
400
60
60
5.0
9
4.536
12
400
75
90
4.5
19
6.285
13
450
30
150
5.0
17
3.674
14
450
45
120
4.5
3
7.245
15
450
60
90
6.0
18
6.333
16
450
75
60
5.5
31
7.461
Table 3 Taguchi L16 factorial design and Experimental Observation
-
S/N RAITO ANALYSIS
The analysis of variance is done to investigate which of the following process parameters has more influence on response value. ANOVA table can be generated from Minitab software or manual calculations. This is accomplished by separating the total variability of the S/N ratios, which is measured by the sum of squared deviations from the total mean of the S/N ratio, into contributions by each of the process parameters and the error [5]. The overall mean of S/N ratios can be calculated using the equations 1-3.
Lower the best type (LB) (1)
Higher the better type (HB) (2)
Nominal the better type (NB) ..(3)
In the Taguchi method the term signal represents the desirable value (mean) for the output characteristic and the term noise represents the undesirable value (S.D) for the output characteristic. Therefore, the S/N ratio is the ratio of the mean to the standard deviation. Taguchi uses the S/N ratio to measure the quality characteristic deviating from the desired value. Loss function obtained from Taguchi analysis is further converted into a signalnoise (S/N) ratio[3]. Generally, there are three kinds of quality characteristics in the analysis of the S/N ratio, such as the higher the- better, lower-the-better and the nominal-the-best. [6].
The objective of this project is to reduce alpha case depth and surface roughness. Therefore, smaller the better characteristic is used shown in equation. Table 4 shows the experimental results for alpha case depth and the corresponding S/N Ratios using the equations mentioned above. The response table and S/N response graph for alpha case depth are shown below. Regardless of the lower-the- better or the higher-the-better quality charcteristic, the greater the S/N ratio corresponds to the smaller variance of the output characteristic around the desired value[5].
The manufacturing, assembly process and powder coating process. There was a problem during assembly of parts of Manual Squeezer. By conducting experiments as per Taguchis Orthogonal array, following results have been obtained after the Statistical analysis using descriptive method. The study showed influencing parameter in powder coating process is the spraying voltage. Because it shows large variation in response value if its level is changed from 1 to 2. One can say that as Voltage increases, the thickness of deposited layer increases. Also its has no effect on outcome even if its level is changed from 1 to 2. The bake time and Curing Medium showed less variation when their levels are changed from 1 to 2. The Amount of layer deposited on smooth part is less in comparison with that of Rough part if all other parameter settings remain unchanged [8].
The DOE trials conducted using Taguchi OAs L4 (2^3) experimental setup suggests optimum Laser engraving DMC parameters is 8×8 mm2 (DMC Size) and 3 Laser passes. The DMC code engraved by Laser has performed successful scanning within required time constraint in the various manufacturing environment. So, it implements for the mass production applications [9].
Table 4 Response Table for S/N Ratios
Level
A, [D(mm)]
B,
[A(degree)]C,
[T(sec.)]D,
[P(bar)]1
-13.61
-17.20
-13.66
-15.17
2
-21.25
-15.93
-23.46
-21.01
3
-21.96
-21.33
-16.62
-22.07
4
-20.69
-23.05
-23.77
-19.26
Delta
8.34
7.12
10.11
6.90
Rank
2
3
1
4
Fig. 3. Main effects ploy for S/N ratios Table 5 Response Table For Means
Level
Nozzle distance
Blasting angle
Blasting time
Blasting pressure
1
6.500
11.250
7.250
10.500
2
13.500
7.750
15.750
11.750
3
13.250
13.000
7.750
13.750
4
13.250
14.500
15.750
10.500
Delta
7.000
6.750
8.500
3.250
Rank
2
3
1
4
Fog. 4. Main Effects plot for Means
-
ANALYSIS OF VARIANCE
ANOVA is a statistical method which is used to determine the interaction of individual for all the control factors in the test design. ANOVA is performed by using statistical software MINITAB 14 to determine the significant process parameter. It helps in predicting the best combination of process parameters for optimal performance characteristics.[4] In this study, ANOVA was used to analyze the effects of grit blasting distance, grit blasting time, grit blasting angle and grit blasting pressure on alpha case removal and surface roughness. This analysis was carried out a 5% significance level and a 95% confidence level. The
significance of control factors in ANOVA is determined by comparing the F value of each control factor.
The last column of the Table 6 shows the percentage value of each parameter contribution which indicates the degree of influence on the process performance. According to Table 6, the percent contributions of the A, B, C and D factors on the surface roughness were found to be 25.23%, 18.22%, 49.08% and 5.08% respectively. Thus, the most important factor affecting the parameter on alpha case removal was blasting time (Factor C, 49.08%).
Table 6 Results of ANOVA for alpha case depth
Process param eter
Degree of free Dom DOF
Sum of squares (SS)
Mean square (MS)
F ratio
Contribution Rate (%)
ACD
A
3
140.25
46.750
10.58
25.23
B
3
101.25
33.750
7.64
18.22
C
3
272.75
90.917
20.58
49.08
D
3
28.25
9.417
2.13
5.08
ERROR
3
13.25
4.417
–
2.39
TOTAL
15
555.75
–
–
100
-
-
CONCLUSION
Grit Blast cleaning with abrasive media removes old coatings, rust, and other unwanted material from a surface, and creates an anchor pattern to allow new coatings to adhere better. Manufacturers who turn to grit blast cleaning as an environmentally responsible alternative to chemical stripping processes often realize substantial cost savings as well. Experimental work of removal of alpha case using grit blasting parameters based on Taguchi analysis has shown following important findings.
Taguchis robust orthogonal array design method is suitable to analyze the alpha case depth problem. The parameter design of the Taguchi method provides a simple, systematic, and efficient methodology for the optimization of the cutting parameters. Further S/N ratio analysis for alpha case depth predicts the optimum parameter combination for grit blasting parameters as level 3 for nozzle distance, level 1 of blasting angle, blasting pressure at level 4 and for blasting pressure at level 2 give maximum value of S/N ratio. Thus, ANOVA for
data means of grit blasting with L16 DOE shows that alpha case depth is most significantly affected by the blasting time is the most affecting factor on the alpha case depth with 49.08% followed by nozzle distance, blasting angle and blasting pressure with 25.23%, 18.22% and 5.08%contribution respectively.
ACKNOWLEDGMENT
We thank thanks to Production Engineering Department of VJTI, Mumbai for financial support for this project work and giving us the opportunity to conduct the project in industrial environment. Also, we thank to Mr. S, N. Gawali, Senior Manager Aerospace Department of Bharat Forge Ltd. Pune for giving this opportunity to work in the company and providing me the necessary support.
REFERENCES
-
B. Sefer, Oxidation and AlphaCase Phenomena in Titanium Alloys used in Aerospace Industry: Ti6Al2Sn4Zr2Mo and Ti6Al4V. 2014.
-
B. Sefer, R. Gaddam, J. Josep, A. Mateo, M. Antti, and R. Pederson, Chemical milling effect on the low cycle fatigue properties of cast Ti
6Al 2Sn 4Zr 2Mo alloy, vol. 92, pp. 193202, 2016.
-
T. Kivak, Optimization of surface roughness and flank wear using the Taguchi method in milling of Hadfield steel with PVD and CVD coated inserts, Meas. J. Int. Meas. Confed., vol. 50, no. 1, pp. 1928, 2014.
-
Sawant, P., & Shinde, D. K. Experimental Study of Process Parameters Influencing Powder Coating of EN8 Steel Shaft used for Manual Squeezer off Toolusing Taguchi Approach, International Journal of Engineering Research & Technology, Vol.9 Issue 11, 2020 page 182-186.
-
Chandak, M., Shinde, P. A. N. D. K., & Raut, D. N. Process Parameter Optimization for Laser 2D Barcode Engraving using Taguchi Design of Experiment Technique, International Journal of Engineering Research & Technology, Vol.9 Issue 11, 2020 page 263-267.
-
L. Singh, R. A. Khan, and M. L. Aggarwal, OPTIMIZATION OF SHOT PEENING PROCESS FOR AISI 304 USING GREY RELATIONAL ANALYSIS WITH TAGUCHI METHOD, vol. 2, no. 5, pp. 4558.
-
N. K. R. C, N. K. V, and S. P. Selvan, Optimization of Machining Parameters and Surface Roughness Measurement using Image Processing, vol. 2, no. 1, pp. 26, 2011.
-
Sawant P. U. (2020) Quality Control Of Gas Control Equipment By Taguchi Method (Master of Technology Theis of VJTI, Mumbai).
-
Chandak M. G. (2017) Process Quality Improvement Using Taguchi DoE Method (Master of Technology Theis of VJTI, Mumbai).