
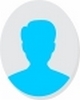
- Open Access
- Authors : B. Anupriya , T. Mohanasankari , B. Saranya
- Paper ID : IJERTV10IS030168
- Volume & Issue : Volume 10, Issue 03 (March 2021)
- Published (First Online): 30-03-2021
- ISSN (Online) : 2278-0181
- Publisher Name : IJERT
- License:
This work is licensed under a Creative Commons Attribution 4.0 International License
Experimental Investigation of Paver Block by using Municipal Solid Waste
B. Anupriya, T. Mohanasankari & B. Saranya
*Associate Professor, Periyar Maniammai Institute of Technology, Thanjavur
*Assistant Professor, Arasu Engineering College, Kumbakonam
*Assistant Professor, Arasu Engineering College, Kumbakonam
Abstract: Now-a-days municipal solid wastes are increased and it causes a great threat to environment and it decomposes very slowly that causing lots of pollutions. One of the global environmental impacts of solid waste is the emission of methane which is regarded as a powerful greenhouse gas, whose impact can be felt within a short period of time. Therefore utilization of these wastes in making building construction materials can reduce the magnitude of the associated problems.
The aim of this project is to reduce environmental pollution by using municipal solid wastes and waste plastic to produce paver blocks. The plastic material is first shredded and melted in a container at a temperature range of 250 ºC – 260 ºC and Municipal solid waste and M-sand was added in the different proportion of 25%,50%,75%. The paver block was prepared and tested and results were compared with cement concrete paver block and fly ash paver block of different proportion.
Keywords:- Paver block, municipal solid waste, M sand, cement concrete paver block, Flyash paver block compressive strength.
-
INTRODUCTION
Plastics are used in day today life. At present nearly 56 lakhs tons of plastic wastes are produced in India per year.
[1] Plastic is one of the daily increasing useful as well as a hazardous material. At the time of need, plastic is found to be very useful but after its use, it is simply thrown away, creating all kinds of hazards. Plastic is non-biodegradable that remains as a hazardous material for more than centuries. The waste plastic will be large in household time.[2]The common and oldest management of plastic waste in the municipality as observed in most parts of the country is through burning and landfilling which are not environmentally friendly and sustainable since these may release smoke, carbon dioxide, carbon monoxide and nitrous oxide, major contributors to global warming (greenhouse gases – GHGs) and methane as leachates that contain pathogens. Moreover, landfilling polymer waste such as plastic waste is not desirable since plastic is non- biodegradable and no economic value would have been derived from the waste in that case. Furthermore, livestock in the municipality may die because they are dieting on plastic waste and being choked [3]
Usually these wastes are either burnt or land filled. This is an approach which could cause various environmental problems like air pollution, emission of greenhouse gases and occupation of useful land. The increasing charges of landfill are further aggravating the problem. Moreover, these methods of disposal are certainly wastage of a
primary resource. In addition, the biodegradation of these wastes in landfills emits methane, a greenhouse gas which has 72 times heating effect relative to that of CO2. Therefore utilization of these wastes in making building construction materials can reduce the magnitude of the associated problems. To reduce use of natural resources, and dumping spaces are being achieved through the use of recycled the solid waste in building materials. Using waste and recycled materials in concrete mixes for paver blocks becoming increasingly important to manage and treat both the solid waste generated by industry and municipal waste
[4] This type of pavement will absorb stress, such as small earthquakes, freezes and thaws, and slight ground erosion, by flexing. Therefore, the pavers do not easily crack, break or buckle like poured asphalt or poured concrete.[5]Thus the results of productive use of waste material represents a means of reducing some of the problems associated with solid waste management; it minimizes the use of natural resources and in some cases results in the production of environmentally friendly products.
Flyash
Flyash is define as the finely divided residue resulting from the combustion powdered coal, which is transported from the firebox through the boiler by flue gases. Flyash is a by- product of coal-fired electric plants. The fly ash used in the work was of class C and the specific gravity was 1.99 g/cm3.
Plastic
Plastic is a material consisting of any of a wide range of synthetic or semi- synthetic organic that are meltable and it can be molded into solid objects. Most of the plastics contain organic polymers. The vast majority of these polymers are formed from chains of carbon atoms or with the addition of oxygen, nitrogen, or sulphur. The chains comprise many repeat units, formed from monomers. But generally the level of plastics in waste composition is high. Polymer modified pavement blocks has applications in road construction and buildings. Hence waste plastic bags can therefore, be mixed in concrete mass in some form, without significant effect on its other properties or slight compromise in strength. [6]
Municipal solid waste
Municipal solid waste, commonly known as trash or garbage is the type of waste consisting of everyday items
we consume and discard. At present, world produces around approximately 2378 Million Tons of Municipal solid waste ash. While India at present uses about 256 Million Tons of as has base material for pavement and used as a replacement in concrete and other application. Also municipal solid waste ash contains less amount of harmful substances and pollutant [7] The required amount of
Block -3
Paver blocks were casted using Mix Proportion =1: 0.5 : 0.5
Plastic = 2 kg
Sieved Municipal Waste : 1Kg M-sand = 1kg
municipal solid waste is collected from the karikulam warehouse storage area which are located at nearby
Block -4
Paver blocks were casted using Mix
Kumbakonam city. The collected municipal waste which are both in solid and semi solid form. It includes both organic and inorganic waste, example of the inorganic waste from residential, commercial, intuitional and industrial source. Example of organic waste are newspaper, clothing, food scrapes etc. The collection is performed by the municipality within a given area.
Proportion =1: 0.75 : 0.25
Plastic = 2 kg
Sieved Municipal Waste : 1.5 Kg M-sand = 500 g
Block -5
Paver blocks were casted using Mix Proportion
=1:1
Plastic = 2 kg
Sieved Municipal Waste : 2 Kg
To compare the strength of Municipal Solid Waste Block (MSWB) with both conventional Fly Ash concrete blocks & Ordinary paver block of M20 grade are casted.
1970)
-
PRELIMINARY INVESTIGATION
A. Sieve Analysis Test (as per IS: 383-
Paver block
Fig.1 Municipal Solid Waste
Sieve analysis helps to determine the particle
Paver block is a paving stone, tile, brick or brick-like piece of concrete commonly used as exterior flooring. In a factory, concrete pavers are made by pouring a mixture of concrete and some type of coloring agent into a mould of some shape and allowing to set. They are applied by pouring a standard concrete foundation, spreading sand on top, and then laying the pavers in the desired pattern. Pavers can be used to make roads, driveways, patios, walkways and other outdoor platforms
In order to determine the increase in compressive strength, various mix proportions are made to find the strength of plastic paver block and municipal solid waste block. They were tested by using compressive testing machine. These are the mix proportion which represent the M-sand, plastics and Sieved Municipal Waste respectively.
Block -1
Paver blocks were casted using Mix
Fig. 2 Sieve Analysis graph
size distribution of the coarse and fine aggregates. This is done by sieving the
aggregates as per IS: 383-1970. The Sieve analysis test which consist of apparatus such as a set of IS Sieves of sizes are 4.75mm, 3.35mm, 2.36mm, 1.18mm, 600µ, 300µ, 150µ and 75µ. Specific Gravity test:
Table 1 Specific gravity test
Proportion = 1: 1
Block -2
Plastic : 2 Kg M-sand = 2 kg
1
Fly ash
2.32
2
M-sand
2.62
3
Municipal Solid waste
2.64
1
Fly ash
2.32
2
M-sand
2.62
3
Municipal Solid waste
2.64
Paver blocks were casted using Mix
Proportion =1: 0.25 : 0.75
Plastic : 2 Kg
Sieved Municipal Waste : 500 M-sand = 1.5 kg
PAVER BLOCK MOULD
V shaped paver block moulds are used for casting paver blocks. The dimension of the paver block is 263.9mm x
-
mm x 88.9 mm and the volume of one mould is 0.0016m3.The height of the mould is to 88.9mm and the distance between the opposite faces shall be specified size of 263.9±0.2mm. The angle between adjacent internal faces and between internal faces and top and bottom planes of the mould shall be 120o ±0.5o C.
Fig.3 Paver Block Mould
CASTING OF PAVER BLOCK PREPARATION OF PLASTIC
When plastic is heated at 120 to 140 oC it is melted into a liquid form and this liquid is calculated into a ml. if 1/2 kg of plastic bags is heated upto a 450ml of liquid is obtained. Similarly the mix proportion of plastic ratio is denoted by liquid form (ml). Then the sieved solid waste is added in different proportion.
Casting Moulds are cleaned and oiled before casting, and then they are put on the level area. The moulds are filled with the melted plastic that consist of m- sand and solid waste at different proportion. Then the specimen surface are leveled by trowel.
Fig.4 Casting of Paver BlockDEMOULDING
After compacting process the blocks are de-moulded and kept for 24 hours in a shelter away from direct sun. The casted paver block was allowed for drying for 24 hours in normal atmospheric temperature.
Fig.5 Demoulding
-
-
RESULTS AND DISCUSSION
-
Compressive Strength Test:
The compressive strength of paver block is one of the most important and useful properties of specimen. In most structural application paver is used primarily to resist compressive stress. In those cases where strength in tension in shear is of primarily, the compressive strength is frequently used as a measure of these properties. Compressive strength is also used as a qualitative for other properties of hardened concrete. For practically there compressive strength increases as the specimen size decrease.
The specimens are kept for one day and then it in tested in saturated conditions. Specimen are placed in such a manner testing machine that the line of loading is perpendicular to the direction it was cast. Constant load is applied on block till it failure.
Conventional Paver Block:
In this study of development of paver blocks from nominal mix design was determined to achieve target strength of M20. Fine aggregate i.e. River sand was replaced completely by M-sand and coarse aggregates less than 12mm were used in mix. The final mix was 1:1.42:2.44 and the compressive strength after 28 days curing was determined.
Conventional block
Conventional block
Convent
Convent
Compressive Strength in N/mm2
Compressive Strength in N/mm2
Table 2 Compressive Strength of Conventional Block
Specimen No.
Load in kN
Compressive Strength in N/mm2
1.
305
15.60
2.
336
16.70
3.
333
16.55
Average
16.28
Compressive Strength of
Compressive Strength of
17
16.5
16
15.5
15
17
16.5
16
15.5
15
16.7
16.7
16.55
16.55
16.28
16.28
15.6
15.6
Specimen Specimen Specimen Average
1 2 3
Specimen Specimen Specimen Average
1 2 3
Specimen
Specimen
Fig.6 Compressive Strength of Conventional Block
Fly ash paver block:
In this process use the partial replacement of Cement with Fly Ash in percentage of 0%, 10%, 20%, and 30% respectively Superplasticizer is used as an admixture which is added 1% by weight of cement constantly in the production of concrete mixture and the compressive strength.
Table 3 Compressive Strength of Fly ash Block
Specimen No.
Replacement of flyash in %
Compressive Strength in N/mm2
1.
0
16.23
2.
10
14.76
3.
20
17.79
4.
30
15.33
20
20
Flyash Paver B17l.o79ck
Flyash Paver B17l.o79ck
16.23
16.23
Compre
Compre
14.76
14.76
15.33
15.33
Compressive Strength in N/mm2
Compressive Strength in N/mm2
10
10
0
0
0%
% o10f%Replace20m%ent of F30l%yash
0%
% o10f%Replace20m%ent of F30l%yash
Fig.7 Compressive Strength of Fly ash Paver Block
20
20
16.2186.23 16.28 16.28
16.2186.23 16.28 16.28
14.76
14.76
15.33
15.33
Compressive Strength in
N/mm2
Compressive Strength in
N/mm2
Fig.8 Comparison of Flyash block with conventional block
Comparison of FlyaCosnhvebntliooncakl block
with conventional
17.79
16.28
Comparison of FlyaCosnhvebntliooncakl block
with conventional
17.79
16.28
15
10
5
0
15
10
5
0
0%
10%
20%
30%
0%
10%
20%
30%
% of replacement of flyash
% of replacement of flyash
Municipal solid waste block:
Specimen for different mix
Mix proportion (plastic+ M- sand+ municipal waste)
Compressive strength (N/ mm2 )
MSWB1(Block)
1:1
9.56
MSWB 2(Block)
1: 0.25: 0.75
12.82
MSWB3(Block)
1: 0.5 : 0.5
13.38
MSWB4(Block)
1: 0.75 : 0.25
7.2
MSWB5(Block)
1: 1
4.5
Specimen for different mix
Mix proportion (plastic+ M- sand+ municipal waste)
Compressive strength (N/ mm2 )
MSWB1(Block)
1:1
9.56
MSWB 2(Block)
1: 0.25: 0.75
12.82
MSWB3(Block)
1: 0.5 : 0.5
13.38
MSWB4(Block)
1: 0.75 : 0.25
7.2
MSWB5(Block)
1: 1
4.5
Table 4 Compressive Strength of Municipal Solid Waste Block
Compressive strength of MSWB
Compressive strength of MSWB
15
10
5
0
15
10
5
0
12.82
12.82
13.38
13.38
9.56
9.56
Compressiv
7.2
4.5
Compressiv
7.2
4.5
MSWB1 MSWB2 MSWB3 MSWB4 MSWB5
MSWB1 MSWB2 MSWB3 MSWB4 MSWB5
Municipal Solid Waste Block Proportion
Municipal Solid Waste Block Proportion
Conventional block
Conventional block
20 16.28 16.28
12.82
20 16.28 16.28
12.82
16.28
13.38
16.28
13.38
10
10
7.2
7.2
Compressive
Strength in N/mm2
Compressive
Strength in N/mm2
Compressive Strength in
N/mm2
Compressive Strength in
N/mm2
Fig. 9 Compressive Strength of Municipal Solid waste block
Comparison of MSW Block with Conventional
Comparison of MSW Block with Conventional
16.28 16.28
9.56
16.28 16.28
9.56
MSWB1 MSWB2 MSWB3 MSWB4 MSBW5
Proportion of MSWB
MSWB1 MSWB2 MSWB3 MSWB4 MSBW5
Proportion of MSWB
4.5
4.5
0
0
S.No
Type of Paver Block
Compressive strength (N/mm2 )
1.
Municipal Solid Waste block 3
(1: 0.5 : 0.5)
13.38
2.
20% replacement of Fly Ash concrete blocks
17.79
3.
Conventional paver block
16.28
S.No
Type of Paver Block
Compressive strength (N/mm2 )
1.
Municipal Solid Waste block 3
(1: 0.5 : 0.5)
13.38
2.
20% replacement of Fly Ash concrete blocks
17.79
3.
Conventional paver block
16.28
Fig. 10 Comparison of MSWB with Conventional block Table 5 Comparison of compressive strength
It is observed that the compressive strength of conventional M20 grade concrete paver block is 16.28 N/mm2, fly ash based M20 grade paver block is 17.79 N/mm2 and paver block made of waste plastic, m- sand and solid waste for proportion of 1: 0.5 : 0.5 is 13.38N/mm2.
The compressive strength of plastic paver block is comparable with ordinary paver block and it is achieved 82% compressive strength nearer to the ordinary paver block and 75% of Fly ash concrete blocks. Hence the addition of 50% of municipal solid waste is effective.
Water absorption test (as per IS 15658: 2006)
The test procedures were followed by IS 15658: 2006. The test specimens were dried in a ventilated oven at 107±70oc for 24 hours. After that the test specimens were completely immersed in water for 24 hours. Then the specimen is taken out from the water and allowed them to dry in room temperature for 2 hours. Then the specimens were wiped
off and weighed immediately. The weight of each specimen was noted. The increase in weight as a percentage of the original weight is expressed as its absorption (in percent). The average absorption of the test samples shall not be greater than 5% with no individual unit greater than 7%.
Table 6 Water Absorption test
Type of Paver Block
Proportion
Water Absorption (%)
Conventional M20 Grade Concrete Paver Block
M20
3.8%
Fly Ash Paver Block
M20
4.2%
Solid Waste Paver Block
1:1
1.4%
1:0.25:0.75
1.2%
1:0.5:0.5
1.04%
1:0.75:0.25
0.8%
The water absorption for conventional concrete block is 3.8% and for fly ash paver block is 4.2%. The water absorption of Solid waste paver block has an average of 1.1%. Hence flyash paver blocks are effective when water absorption is concern.
Cost analysis
Cost of conventional concrete paver block of M20 grade is 12 INR/ block Similarly the cost of fly ash based M20 grade paver block of same size is 10INR/ block. The cost of solid waste paver block is calculated as 6 INR/block.
Table 7 Cost Analysis
S.No.
Types of paver block
Cost of paver block (Rs./piece)
1.
Conventional Concrete Paver block of M20 grade
12
2.
Fly Ash Paver block of M20 grade
10
3.
Solid waste Paver Block
6
Cos
20
Cos
20
0
Conventional Concrete bFlloycaksh block Solid waste block
0
Conventional Concrete bFlloycaksh block Solid waste block
Type of Paver block
Type of Paver block
Cost Analysis
12
Cost Analysis
12
10
10
6
6
Cost in INR
Cost in INR
Fig. 11 Cost Analysis
The cost of solid waste paver block is to be 6 INR /block which is about half of the cost of conventional concrete paver block. Therefore, the cost of paver block made of plastic waste, m-sand and municipal solid waste is less than the conventional M20 grade concrete paver block
and fly ash paver block. Hence, plastic paver block is economical when compared to the other two.
-
-
CONCLUSION
This study was carried out by adding municipal solid waste and M-sand into melted plastic to develop the light weight paver block. Municipal solid waste and M- sand was added in the different proportion of 25%,50%,75%. The result shows that addition of 50% of municipal solid waste and 50% of M-sand with melted plastic shows the good compressive strength.
Based on the experimental investigation, it is found that the compressive strength of plastic paver block is comparable with ordinary paver block and it is achieved 82% compressive strength nearer to the ordinary paver block and 75% of Fly ash concrete blocks. Hence the addition of 50% of municipal solid waste is effective.
The weight of conventional M20 grade concrete paver block is nearly twice than paver block made of plastic waste, m-sand, solid waste. The weight of paver block made of waste plastic, m-sand and solid waste increase with increase in addition of fine aggregate.
Water absorption of conventional M20 grade concrete paver block and flyash paver block is nearly thrice than solid waste paver block. The cost of solid waste paver block is calculated as 6 Rs/block which is about half of the cost of conventional concrete paver block.
Hence the study that conclude addition of 50% of municipal solid waste is effective in account of compressive strength and also economical than the conventional concrete paver block. The utilization of waste plastic in production of paver blocks has productive way of disposal of plastic waste. The recycling of plastic materials will be reduced the environmental degradation.
By adopting precast Paver block made using plastic waste, M-sand and municipal waste have shown better results and benefits.
REFERENCES
-
Sunil Chavan , Shubham Tamhane , Mukesh Chavan , Rushikesh Phuge , Prof.Mayur Tanpure , Prof. Manoj Deosarkar, Manufacturing of Pavement Block by Using Waste Plastic and Sa Sand in International Journal of Innovative Research in Science, Engineering and Technology, Vol. 8, Issue 4, April 2019.
-
Ambrish Narayan Pandey, 2Abhishek Yadav, 3Durgesh Chaudhary, 4Nageshwar, 5Vijay Kumar Srivastava, Waste Plastic Used In Paving Block: A Research, International Journal of Scientific Research and Review, Volume 07, Issue 03, March 2019
-
Exploiting recycled plastic waste as an alternative binder for paving blocks production, ELSEVIER, 2019
-
Jeevan Ghuge, Saurabh Surale, Dr. B.M. Patil, S B Bhutekar, Utilization of Waste Plastic in Manufacturing of Paver Blocks, International Research Journal of Engineering and Technology, Volume: 06 Issue: 04 Apr 2019.
-
P. Velumani & S. Senthilkumar, Production of sludge- incorporated paver blocks for efficient waste management, Journal of the Air & Waste Management Association, 2018, VOL. 68, NO. 6, 626636.