
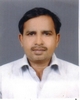
- Open Access
- Authors : S.Selvam , Dr. D. Subramanian
- Paper ID : IJERTV10IS040244
- Volume & Issue : Volume 10, Issue 04 (April 2021)
- Published (First Online): 01-05-2021
- ISSN (Online) : 2278-0181
- Publisher Name : IJERT
- License:
This work is licensed under a Creative Commons Attribution 4.0 International License
Experimental Investigation of Wear Analysis for Aluminum Alloy LM25 Material
S. Selvam
-
E., Computer Aided in Design Department of Computer Aided in Design,
Mahendra Engineering College, Mallasamudram, Tiruchengode, Namakkal District,
Tamil Nadu India.
Dr. D. Subramanian
M.E. Ph. D Assistant Professor Department of Mechanical Engineering,
Mahendra Engineering College, Mallasamudram, Triruchengode, Namakkal District,
Tamil Nadu, India.
Abstract:- Nowadays aluminum alloy materials have become more important for its wide range of applications in design flexibility, most of the automobile industries are conducting various experiments and researches to develop mechanical and chemical properties having less weight material for best cost. In this we are using aluminum alloy LM25 with silicon carbide, alumina and graphite.. These three Nano particles of silicon carbide, alumina and graphite bonded together with aluminum alloy LM25 to form a hard ceramics that are involved for wear test and widely used in applications requiring high resilience, graphite is well known used for thermal conductivity.
Key words: Alumina, Silicon Carbide, Graphite types of aluminum alloy.
-
INTRODUCTION
Silicon carbide is a compound of silicon and carbon with chemical formula Sic of the Nano particles. Molecules of silicon can be bonded with molecules of carbon together by sintering to form very hard ceramics that are widely used in applications requiring high resilience, such as parts of car brakes, clutches and ceramic parts in industries.
Silicon carbide is a refractory material, it has good thermal conductivity and low coefficient of thermal expansion. 4.0 × 106/K. Sic is used for abrasive machining processes such as grinding, honing, and electronic components.
Its hardness suitable to make for small disk, chip and circuit boards in the computer manufacturing industry.
-
Aluminum oxide or alumina
Aluminum oxide Al2O3 is the combination of a chemical compound of aluminum and oxygen. It contains of Nano particles and It is commonly called alumina.
Al 2 O 3 is an electrical insulator but has a relatively high thermal conductivity 30 W m -1 K-1 like ceramic material. Its hardness was suitable for use as an abrasive.
-
Graphite
Graphite is the powdered form of Nano particles. Therefore, it is used in thermochemistry as the standard state for defining the formation of carbon molecules.. Graphite may be powdered from the highest grade of coal. If further heated of graphite it changed anthracite and meta-anthracite in its state.
Grapheme polystyrene materials to process of an industrial processes in hot pressing. It is possible to produce
grapheme from graphite. Graphite may support with Sic by giving hardness between the contact surfaces resulting in increase of wear resistance.
-
-
NEED OF STUDY OBJECTIVES OF STUDY
-
Various methods for the fabrication of aluminum alloy such as stir casting, sand die casting and plaster mold are used. In stir casting, different process parameters wear, coefficient of friction, temperature, load, sliding velocity, lifecycle and impact strength were studied. In the castings of LM25 aluminum alloy .strength and the hardness of the castings while it increases with higher graininess number and moisture content of the molds results in lower impact strength of the castings.
A large number of fabrication techniques are currently used to manufacture the materials used like stir casting. It has been observed a rapid increasing utilization of aluminum alloys, in the automobile and automotive industry due to low weight, density, high hardness and good thermal conductivity.
2.1 REVIEW OF LITERATURE
Wear was occurred on a soft metal surface abraded by hard and sharp abrasive particles. It has found that 50% of all wear in tyre industry are due to abrasion, and as such, much work has examined and tested to the abrasive wear behavior of materials.
There are in several areas where abrasive wear occurs such as an automobile, automotive vibratory equipment and conveyors. Any mechanical devices in which involved the motion of solids related to the surfaces in wear problems.
In the present work is the abrasive damage in aluminum alloy sheet used in trucks buckets under the action of sand friction resulting when transporting the sand in these trucks.. This contradiction can be due to differences in contact conditions, parameters and types of test used. In particular, the influence of grain size and shape of abrasive particles on the wear behavior has been studied. .
In addition to bulk shape, can have notable influence on the particles in fine grinding. Wear tests were carried out with the standard three aluminum alloys were tested, namely 5A(69Hv), and 7T6(128 Hv).
A wear was developed to study both the influence of abrasive particles and it was found for LM25 aluminum alloy travels the distance been tested under the aluminum alloy increases. To identify the effect of abrasive particles,
additional wear tests were carried out abrasive sand particles of wear in mass loss against or LM25 It was found that the mass loss with normalized abrasives sand (NAS), for all tested alloys, is increased almost by 35±15% compared to the tests carried out with the standard pit sand (SPS).
A comparative study of wear resistance of the 5xxx family and 7xxx family (7T6 and 7T4) is summarized. 7xxx aluminum alloy (7T6 and 7T4) are lower than the 5xxx aluminum alloy (5H and 5A),
The wear rate of material increased with increasing of load and abrasive size while the rate of wear increases with increase in sliding distance for Sic reinforced composite and decreases with increase of Al2O3 in reinforced composite. .
As the amount of alloying elements is increased, wear resistance as well as hardness are increased with smaller section size better mechanical properties are achieved due to faster cooling rate in the sand, die casting and plaster mold are used for the fabrication of aluminum alloy.
-
Remora and G Padmanabhan(2012) Fabricated aluminum alloy boron carbide composites using liquid metallurgy techniques with particulates weight 2.5, 5 and 7.5% are developed in aluminum matrix. MadevaNagaral (2013) have studied the mechanical behavior Al6061/Al2O/Graphite reinforced MMC liquid metallurgy route .the tensile strength of composite.
-
Raviteja(2014)have developed and evaluated the mechanical properties of Al-Sil2Cu/B4c composite by varying the weight of B4c particulates and it has improved 10% of the hardness value by 6.97%, and tensile strength by 33%, improved when compared to alloy. The chemical composition of Aluminum LM25 Alloy as follows.
Tabl3 2.1
Chemical Composition |
Percentage % |
Copper |
0.1 |
Magnesium |
0. 2 0.6 |
Silicon |
6.5 – 7.5 |
Iron |
0.5 |
Manganese |
0.3 |
Nickel |
0.1 |
Zinc |
0.1 |
Lead |
0..1 |
Tin |
0.05 |
Titanium |
0.2 |
aluminums |
Reminder |
WORKING METHODOLOGY
Advanced processes for producing metal by stir casting mold with discontinuous particulate reinforcment. Among all the processes, stir casting route by producing vortex by means of mechanical stirring in the crucible is the most suitable and cost effective method.
Producing larger components of metal-ceramic particulates with homogeneous mixture in this method. This type of process is cost effective method for producing the mold components.
Stir casting is also one of the liquid metallurgy techniques for producing metal matrix composite. Nano size of Sic particulates ranging from 50m to 100m may give better results.
It was observed that can be limited to the Graphite and Alumina and the Sic can be varied from a step of 0.5%.The resulting composite may show combined results of Sic, Alumina and Graphite. Composites
A hybrid composite is going to be made, composition of reinforcements for getting better composite may differ from the results.
It possess that the of the final composite based on the optimal composition of properties of the Sic, Alumina and Graphite.
Fig 1 STIR CASTING PROCESS SETUP
WORK IN PROGRESS
In the process work, it requires a stir casting furnace with 3 blade graphite stirrer. The stir casting was specially designed casting method for suitable one. Even though some stir casting furnaces are readily available in the market, and best suited for the present work to vary process parameters
Preparation of Furnace
A furnace body was made by different types of materials and sizes depend upon the requirement.
A furnace was fabricated by using a cylindrical heavy thick sheet metal drum. The inner wall of furnace is kept with refractory ceramic material to prevent heat losses and is packed with glass wool material.
In all types of furnaces, body is the main thing, it holds the total set up with the temperature controller. So, it is high expensive and cost. It can withstand the high temperature.
A temperature controller is used to control the temperature of the furnace by the heat sensor Temperature controllers are needed in any situation requiring a given temperature be
A stir casting furnace consists of the following basic components.
-
Furnace
-
Crucible
-
Stirrer
kept stable. The output temperature is constantly measured and kept to maintain a constant output at the desired temperature.
The motor shaft is connected to a stainless steel rod and the other end is coupled to a graphite three-blade stirrer. Stirrer is inserted into the crucible and allowed to rotate the molten metal. Vortex is formed in the crucible due to the rotation of stirrer.
Stir Casting process is a liquid state method to prepare of composite materials for fabrication, in which a discontinuous reinforcement is mixture with a molten matrix metal by means of mechanical stirring effect.
Table 2.2 Ratio of material Sic, Graphite and Alumina with Aluminum alloy LM25
Group1 |
Silicon Carbide 0.5 % |
Alumina 0.5 % |
Graphite 0.5 % |
Group 2 |
Silicon Carbide 1.0 % |
Alumina 1.0 % |
Graphite 1.0 % |
Group 3 |
Silicon Carbide 1.5 % |
Alumina 1.5 % |
Graphite 1.5 % |
-
SAMPLE PREPARATION
At first aluminum of weight 760 gram is taken from 4 kg and fed into the stir casting furnace. The LM 25 aluminum alloy preheated in separate induction furnace containers and then kept into the furnace. Heat is transferred to the stir casting furnace and metal was melted in a separate furnace using a standard ladle which will carry 760g of molten aluminum. The metal was maintained at 770o C temperature in stir casting furnace. When the temperatures in the furnace were settled nearly above 770oC metal was melted the heat is carried out. The measured three Nano particles were added The molten metal was poured into the die cavity using a ladle from the crucible and allowed to cool for about two minutes for solidification and mold component removed from the die. The remaining metal in the crucible was also The same procedure was followed for producing second samples of 1% alumina 1% graphite and 1% Sic and third samples of Silicon carbide 1.5%, alumina1% and 1% graphite All the samples were grouped and marked based on the composition of reinforcements. A standard test bar which produces 30 mm diameter 280 mm cylindrical rod with larger riser on it to avoid shrinkage. It was tested that the 280mm length bar casting consumes 760 g of molten metal. Three mold components made it by using the stir casting process.
-
EXPERIMENTAL PROCEDURE
After made of samples the following operations were performed and specimens were analyzed for variation in
of Sic 0.5%, Alumina 1% and Graphite 1% was separately coverall to the molten metal. Oxides and other impurities are removed from the molten metal.
Stirrer is inserted to rotate and created vortex in the crucible. The speed of the stirrer is controlled using a potentiometer to get desired vortex in the in the crucible. After the reinforcements were added slowly and after completely adding the reinforcements the stirrer is further it rotates for ten more minutes to the vortex for uniform distribution of particulates.
used for taking the another test samples A ceramic liquid mixture of compound was obtained by the swivel of the hard coating of stirrer.
density as per Archimedes principle. Specimens were freed from the risers and turned to required dimensions on a lathe machine. Small section are cut 8mm to 8mm square into 9 pieces. Wear test was conducted on the experimental setup. And the values of each experiment pieces were noted
-
Sliding wear test
The outer surfaces of the subjected to wear test in pin-on- disc tribometer on dry sliding condition. The wear tester composed of the hardened steel EN-32 counter face which has the hardness of 60 HRC.
The specimen is fixed in the holding jaws of the between the n the contact surface of the disc and load is applied continuously through the lever arrangement.
The continuous rotation of the steel disc face and the action of load produces wear on the specimen surface. The steel disc is cleaned with emery sheets regularly to provide fresh surface contact of the specimen with the counter face.
The experiments are performed as per the experimental design obtained. The specimens are measured for its mass before and after each experiment to predict the mass loss and Al-Gr and Sic is, better properties were obtained up to 1%
of Graphite and 1% of Alumina in the Al matrix and the Nano size of Graphite particulates varies from 40 to 100 microns based on process parameters.
from that, the sliding wear rate is computed through the Eqn. (2)
Where W is the wear rate (mm3/m), M is mass loss (g), is density (g/mm3) and D is the sliding distance (m).
W= MD (2)
It was observed that the studies conducted yield better properties of the composite were obtained on Sic in similar ceramic particulates like Sic, Graphite and alumina in various research works.
Fig2 Component produced using stir casting machine
S. No
Parameter
Dimension in mm
1
Disc diameter
200
2
Thickness of disc
7.8
3
Sliding distance
50
S. No
Parameter
Dimension in mm
1
Disc diameter
200
2
Thickness of disc
7.8
3
Sliding distance
50
Fig 3 Sample specimen 8 mm x 8 mm of cross section Table 3.1
Fig 4 Wear test instrumet
Fig 5 Wear test instrument at start position
Fig 6 Wear in micron at max range
7 . EXPERIMENTAL PROCEDURE
After preheating of samples the following operations were performed.
Specimens were analyzed for variation in density as per Archimedes principle.
Specimens were freed from the risers and turned to required dimensions on a lathe machine. riser portions were shaped.
Small section are cut 8mm to 8mm square into 9 pieces.
7.2 Sliding wear test
The outer surfaces of the disc subjected to wear test in pin-on-disc on dry sliding condition. The wear tester composed of the hardened steel EN-32 counter face which has the hardness of 60 HRC.
The specimen is fixed in the holding jaws between the contact surfaces of the tester and load is applied continuously through the lever arrangement.
The continuous rotation of the steel face and the action of load produces wear on the specimen surface. The steel disc is cleaned with emery sheets regularly to provide fresh surface contact of the specimen with the disc face.
The experiments are performed for the different parameters as per the experimental and the values computed. The specimens are measured for its mass before and after each experiment and from that, the sliding wear rate was computed.
Where W is the wear rate (mm3/m), M is mass loss (g), is density (g/mm3) and D is the sliding distance (m). W= MD (2)
EXPERIMENT CONDUCTED IN WEAR TEST SETUP
Table 4.1
S. No
Specimen
Speed
Load kg
Time min
Wear in micron
Coefficient of friction
Before weight
After weight
Weight Loss in gram
1
Group 1 A
500
1
2
180
4.7
6.055
6.050
0.005
2
B
500
2
2
200
7.4
4.985
4.980
0.005
3
C
500
3
2
280
13.1
5.929
5.921
0.008
4
Group 2 A
500
1
2
170
5.1
7.881
7.870
0.011
5
B
500
2
2
180
9.1
6.213
6.211
0.002
6
C
500
3
2
220
11.4
6.221
6.213
0.008
7
Group 3 A
500
1
2
90
4.2
7.349
7.343
0.006
8
B
500
2
2
160
9.3
6.685
6.678
0.007
9
C
500
3
2
243
12.6
6.841
6.827
0.014
Wear test was conducted on the experimental setup. And the values of each experiment pieces were noted
7.4. RESULTS AND DISCUSSIONS
-
The dry sliding wear test results obtained for the different combination of the parameters as per the experimental design are shown in Table. 1
-
The significance test is conducted for the full quadratic and the acquired regression coefficients are shown in table1.
-
It ensures that the specimen model is well adequate in estimating the dry sliding wear behavior of the correlating the parameters such as load, velocity and sliding distance.
-
It is observed from the interaction terms, the term L*V is observed with high significance on the wear rate than the terms L*S and V*S.
-
From the model it is concluded that positive sign of the parameter indicates that it increases the wear rate majorly and negative sign of the parameter indicates that it has decreasing the wear rate.
-
The accuracy of the specimen of the component through resilience coefficients can be evaluated through the observation of experiments.
-
The adequacy of the model can be evaluated by substituting the new parametric values on the model by comparing the experimental values obtained for the same parametric conditions.
-
The error percentage calculated falls within it ensures that the constructed model is well adequate in estimating the dry sliding wear behaviour of the correlating the parameters such as load, velocity and sliding distance.
-
The wear behavior of the composite protects the specimen from the sliding wear and results in decreasing of wear rate.
-
The wear rate of the specimen increased initially with increase in sliding distance and decreases after running for some distance.
-
The hard reinforcement particles protruded over the specimen surface gets contact initially with the counter face steel disc.
-
The non-linear contact of these protruded reinforcement particles with the steel disc results in more material removal.
-
On running for some considerable sliding distance, the smoothening effect of the specimen which produces stabilization on the contact surface and it decreases the wear rate.
-
-
The further increase in sliding distance results in increase of wear rate of the specimen.
-
It is known that in pin-on-disc test, the wear loss from the specimen greatly depends upon the wear track condition during the whole running distance. When running for long distances, the surface roughness of the wear track gets
-
worsened and this damaged wear track intern causes increase in the material removal from the specimen
Coefficient of friction
Coefficient of friction
.
Group Vs Coefficient of friction
Group 1
Group2
Group 3
Group Vs Coefficient of friction
Group 1
Group2
Group 3
14
12
10
8
6
4
2
0
14
12
10
8
6
4
2
0
Group A
Group B
Group C
Group A
Group B
Group C
Wear in micron
Wear in micron
Fig 7 In this graph the group B material gives the low Co efficient of friction the value of 11.4
Group of specimen Vs wear in micron
Group of specimen Vs wear in micron
300
250
200
150
100
50
0
300
250
200
150
100
50
0
Group A
Group B
Group of specimen
Group C
Group A
Group B
Group of specimen
Group C
Fig 8 In this graph the group B material gives the less wear from all these components.
Group fo specimen Vs Mass in gram
Group fo specimen Vs Mass in gram
0.016
0.014
0.012
0.01
0.008
0.006
0.004
0.002
0
0.016
0.014
0.012
0.01
0.008
0.006
0.004
0.002
0
A
Group of speci B
C
A
Group of speci B
C
men
men
Loss of Mass in gram
Loss of Mass in gram
Fig 9 In this graph the weight was measured of the values of group B material gives the minimum loss of mass in gram
From the obtained less wear component in the same ratio again one mold componet made by the Stir casting process.
For composition of Sic, Al2O3 and Graphite of the ratio of equally 1 %. And it has to be cut for the dimension of 8mm x 8mm cross section for three pieces.
HEAT TREATMENT PROCESS
The three specimen was kept in induction furnace for 3 hours of the temperature has maintained at 274°C for constant and after it allowed to gets air cooled.
Fig 10 Induction furnace at constant temperature for 3 hours.
EXPERIMENT CONDUCTED IN WEAR TEST SETUP
Fig 11 Wear test experimental setup
Then the three specimen was taken wear test for the load of 1kg, 2kg and 3kg respectively.
Observation of readings of Coefficient of friction and wear in micron was noted.
Table 4.2
S. No |
Specimen |
Speed |
Load kg |
Time min |
Wear in micron |
Coefficient of Friction. |
1 |
Group 2 A |
500 |
1 |
2 |
145 |
4.3 |
2 |
B |
500 |
2 |
2 |
60 |
9.0 |
3 |
C |
500 |
3 |
2 |
78 |
13.8 |
APPLICATIONS AND ADVANTAGES
Applications
The main application of metal matrix composites are.
i The density of alloy 2.68 g/cm3 hence, it is mainly used in cylinder blocks and cylinder heads in Automobile industry. ii Space research.
-
Electronic component of Electronic and Electrical industries
-
Rotating machines in various industries. v Mobile applications.
vi Transportation Advantages
To increase the wear resistance of the LM 25 aluminum alloy metal..
To obtain good strength of the composites.
It increases the hardness of the MMC composites
ACKNOWLEDGEMENT
The material purchased from Coimbatore metal mart in Coimbatore. I thank to the technician to completion of the work.
CONCLUSIONS
From the experimental and analysis of present work the following conclusions are drawn.
By the addition of Sic in the molten metal it increases the mechanical properties of the component made by the stir casting process.
By comparing with amount of Sic in the composite LM-25with Sic 1%, Alumina 1% and graphite 1% are most suitable and improved the wear resistance of the alloy.
When considering after the heat treatment process of the component which gives the less wear of 60 micron for same time and rotation of speed. .
Addition of graphite in the composite which is having increases the thermal conductivity and hardness
REFERENCES
-
Fractography, fluidity, and tensile properties of aluminum/hematite particulate composites. S. C. Sharma, et al. 3,
s. l. Springer US, June 1999, Journal of Materials Engineering and Performance, Vol. 8, pp. 309-314.
-
Aluminum Metal-Matrix Composites for Automotive Applications: Tribological Considerations. S. V. PRASAD and R.ASTHANA. 3, s. l.: Kluwer Academic Publishers-Plenum Publishers, October 2004, Tribology Letters, Vol. 17, pp. 445-453.
-
Tribological Behavior of Aluminum/Alumina/Graphite Hybrid Metal Matrix Composite Using Taguchis Techniques. R Subramanian, N Radhika and S Venkat Prasat. : Scientific Research Publishing Inc., 20 April 2011, Journal of Minerals & Materials Characterization & Engineering, Vol. 10, pp. 427-443.
-
GyanendraSingh et al, Fabrication and Characterization of Aluminum-Graphite Composite Material, International Journal of Mechanical and Production Engineering Research and Development (IJMPERD) , Volume 7, Issue 4, July August 2013,pp. 313-320
-
Secrets of Yamaha Technology India YAMAHA Motor Pvt. Ltd.www.yamahamotorindia.com/16secrets/cylinder/index.html.
-
Manufacturing od a MMCS using stir casting processes and testing its mechanical properties Kandpal, Bhaskar Chandra, et al. III, s. l.
: Technical journals online, July-Sept. 2013, International Journal of Advanced Engineering Technology, Vol. IV, pp. 26-29. E-ISSN 0976-3945.
-
Rama Rao, S. and Padmanabhan, G., Fabrication and mechanical properties of aluminum-boron carbide composites, Int. J. Mater. Biomater. Appl, 2/3 (2012), 15-18.
-
Rocha, L.A., Wear mechanisms in functionally graded aluminum matrix composites: effect of the lubrication by an aqueous solution, Mater. Sci. Eng., 492-493 (2005), 33-38.
-
Rajan.T. P.D. Pillai, R.M. and Pai. B.C., Characterization of centrifugal cast functionally graded aluminum-silicon carbide metal matrix composites, Mater. Charact, 61 (2010), 923-928.
-
Vettivel S.C. Selvakumar, N., Narayanasamy. R. and Leema. N., Numerical modelling, prediction of Cu-W Nano powder composite in dry sliding wear condition using response surface methodology, Mater. Des, 50 (2013), 977-986.
-
Naravade R.H. and Belkar R.K., Statistical analysis of factors affecting the dry sliding wear behavior of Al/ Sic on automobile friction material, Int. J. Eng. Sic, 3/12 (2014), 05-3.
-
High strength, and wear resistance Venkatesh.D and. Dinesh Kumar fabricated aluminum 6063 based alloy.
-
B. Vijay Ramnath (2014) have fabricated had investigated are mechanical properties and inner structure of aluminum ally, alumina (Al2O3), and boron carbide metal matrix composite.
-
K.R. Padmavathi (2014) have studied the wear and friction behavior of Al-6061 with various percentages volumes of multiwall carbon Nano tube and silicon carbide reinforcement.
-
N.G. Siddesh kumar (2014) have developed reinforced with B4C & MoS2 using stir casting technique and conducted experiment to evaluated microstructure, density, micro hardness, tensile dry sliding wear test. P.B. Pawar (2014)
-
Baradeswaran and Elaya Perumal, A., Study on mechanical and wear properties of Al 7075/Al2O3/graphite hybrid composites, Compos. Part B, 56 (2014), 464-471.
-
Niranjan, K and Lakshminarayanan, P. R. Optimization of process parameters for in situ casting of Al/TiB2 composites through response surface methodology, Trans. Nonferrous Met. Soc. China, 23 (2013), 1269-1274.
-
Viswanatha, B.M. Kumar. M.P. Basavarajappa, S. and Kiran, T.S., Effect of ageing on dry sliding wear behaviour of Al-MMC for disc brake, Tribol. Ind, 36/1 (2014), 40-48.
-
Naravade, R.H. and Belkar, R.K., Statistical analysis of factors affecting the dry sliding wear behaviour of Al/ Sic on automobile friction material, Int. J. Eng. Sic, 3/12 (2014), 05-13.
-
Yang, L. J., Determination of steady-state adhesive wear rate, J. Tribol, 128 (2006), 725-734.