
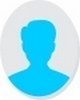
- Open Access
- Authors : Thamil Selvan A
- Paper ID : IJERTV11IS050186
- Volume & Issue : Volume 11, Issue 05 (May 2022)
- Published (First Online): 30-05-2022
- ISSN (Online) : 2278-0181
- Publisher Name : IJERT
- License:
This work is licensed under a Creative Commons Attribution 4.0 International License
Experimental Investigation on Incorporation of Plastic Waste (LDPE) on Durability of Concrete
Thamil Selvan A
S K P Engineering College Tiruvannamalai
Tamil Nadu
Abstract The use of concrete increasing annually due its favorable properties and readily availability. When the concrete exposed to environment it starts to disintegrate due to chemical attack. The majority of chemical attacks on concrete are in the form of a reaction between aggressive agents and the cement matrix, although reactions can also happen with the aggregate. However, the use of Portland cement concrete has an impact on the environmental due to the emission of CO2 in the atmosphere. On the other side handling of plastic waste was a major problem all over the world. So, to solve these problems the investigation had been established as the use of rice husk ash and silica fume as partial replacement of Portland cement to increase strength at early and later age and exhibit considerable enhancement in durability due to its micro structure thereby reducing the permeability of concrete, also the plastic waste (LDPE) obtained from industry was used as a replacement for fine aggregate.
From the literature study the addition of 20% of RHA and 10% SF, gave a better strength, and the addition of plastic waste in the proportion of 5, 10, 15 and 20%, plastic waste decreases the compressive strength the addition of RHA and SF compensate those losses. The concrete is casted at different mix proportion of with and without LDPE waste so as to compare the strength. With the addition of additives at different ratios, the different specimen of concrete cubes was casted and the optimum mix strength of concrete specimen (compression) was checked, for the optimum mix, the performance over the durability was carried (magnesium sulphate, sodium sulphate and sulphuric acid) under the ASTM standards. To analyze the deterioration and homogeneity of concrete cement paste SEM analysis is carried. At final, the of the ordinary Portland cement concrete and the concrete made with different additives.
Keywords: Rice husk ash, Silica fume, LDPE.
INTRODUCTION
-
GENERAL
Concrete is one of the most widely used construction material in the world wide because of its ability to get cast on any form or shape. Concrete is a very durable material needs to maintenance. Due to the effects of environmental and acidic attack, the concrete starts deteriorate in long term behavior, to make the concrete more strong and durable we need to care about its durability. In a mild environment with proper design and production, concrete made with ordinary Portland cement (OPC) can be a durable material. However, it has been long recognized that traditional concrete can suffer from deterioration due to the attack from aggressive agents such as chloride, sulphate, and acid. The
majority of chemical attacks on concrete are in the form of a reaction between aggressive agents and the cement matrix, although reactions can also happen with the aggregate, on the other hand disposal of wastes obtained from many industries is still a challenge for mankind, so the concept incorporation of waste plastic into the concrete which obtained from the industries was developed. To enhance the physical, chemical and durability of concrete, the properties of waste material is analyzed and incorporated into concrete, thus leads to cost effective and durable material.
-
CONCRETE USING ADMIXTURES
To enhance the durability of concrete, the RHA is partially replaced with the cement content and SF is partially replaced with the cement content to enhance the mechanical properties of concrete by weight of the cement, and for the disposal of plastic waste, and to enhance the flexural behavior, the waste powder which is obtained from Tuticorin plastic industries it is being replaced with the fine aggregate in different percentage, and the optimum amount of plastic wastes in strength aspects will be found out by trial and error method.
-
1.3 RICE HUSK ASH
Burning of rice husk at controlled burning temperatures below 700oC, formless silica in RHA is formed which is very reactive by nature. The result showed that the highest amount of formless silica occur in rice husk burnt in the range of 500-700oC. High amounts (up to 30%) of RHA could be blended with cement without adversely affecting the mechanical (strength) and durability (permeability) of concrete. For durability, RHA often improves the concretes resistance to deterioration from sulphate and chlorides, and also lowers the temperature of fresh concrete. RHA, as a partial replacement for cement could contribute to a series of advantageous performances by demonstrating economical, environmental, and technical advantages because it provides a new use for waste materials, produces cheaper concrete for low cost construction, and reduce of carbon emissions. The utilization of RHA as a pozzolanic material in cement and concrete provides several advantages, such as improved strength and durability properties, reduced materials cost due to less usage of cement, and environmental benefits related to the disposal of waste materials. The effectiveness of rice husk ash to serve as a pozzolan in Portland cement concrete is primarily dependent on its silica content and the nature of silica present in RHA. For instance, the concretes containing RHA with high amorphous silica content showed
higher compressive strength and lower permeability than those RHAs containingcrystalline silica. This may be because the high amount of amorphous silica in RHA attributes to quicker depletion of calcium hydroxide especially at early ages, thereby in result enhanced strength and reduced Permeability, and several investigations suggest the beneficial use of low-carbon RHA with amorphous silica to significantly improve specific durability property of Portland cement concrete.
-
1.4 SILICA FUME
-
Silica fume (SF) is a by-product obtained after the smelting process in the silicon and ferrosilicon industry. It is also known as micro silica or silica dust. The American concrete institute (ACI) defines silica fume as a very fine non crystalline silica produced in electric arc furnaces as a by- product of production of elemental silicon or alloys containing silicon. The reduction of high-purity quartz to silicon at temperatures up to 2,000oC produces SiO2 vapours, which oxidizes and condense in the low temperature zone to tiny particles consisting of non-crystalline silica. By- products of the production of silicon metal and the ferrosilicon alloys having silicon contents of 75% or more contain 8595% non- crystalline micro silica. The by-product of the production of ferrosilicon alloy having 50% silicon has lower silica content and is less pozzolanic. It is usually in the form of grey coloured powder, somewhat similar to Portland cement or fly ashes. It can exhibit both pozzolanic and cementitious properties. Because of its extreme fineness and high amorphous silica content, it enhances the pozzolanic reaction by reacting with calcium hydroxide resulting from primary hydration. Silica fume has been recognized as a pozzolanic admixture that is effectively enhancing the mechanical properties to a great extent. By using silica fume along with super plasticizers, it is easier to obtain compressive strengths. Addition of silica fume to concrete improves the durability of concrete due to reduction in the permeability, refined pore structure, leading to a reduction in the diffusion of harmful ions, reduces calcium hydroxide content which significantly resultsin a higher resistance to sulphate attack.
PLASTIC WASTE (LDPE)
Also Environmental impact of dredging, excavating and processing natural aggregate such as threat to river ecosystems, As a result of these environmental concerns, authorities in some parts of the world have imposed restrictions on miningof aggregate through taxation as well as banning of mining on some sites. Environmentalism is a basic principle of sustainable development which aims atprotecting the environment and conserving the earths natural resources. Trends in concrete technology are currently directed towards sourcing alternative sustainable materials for concrete in order to minimize over-reliance on natural resources. Many of the substitute materials used for producing green concrete are recycled materials obtained from industrial wastes and by- products. Plastic is one of the most relevant innovations of the twenty first century. This material has been widely used as a raw material in the manufacture of packaging, electrical and household appliances, toys and various other goods. Total
plastic consumption has been increasing in recent yearsand so contributing to growing volume in the plastic waste stream. This is considered a serious environmental threat, especially in Asia. The use of plastic waste as a substitute for natural aggregate in concrete is a relatively recent concept. One of the first significant reviews on the use of waste plastic in concrete focused on the advantages and economical benefits of such use, besides their physical and mechanical properties. There was common base in that the use of plastic waste aggregate is viable, even though the performance of most properties declined. The plastic wastes can beneficially be incorporated in concrete, as fine aggregates or as supplementary cementitious materials, it is important to notice that not all type of materials wastes are suitable for such use, A decrease in slump value with increase in PET waste as partial aggregate replacement. At 20% replacement the slump decreasedby 2058 mm.
-
AIM OF THE PROJECT
The aim of this experimental program is to compare the efficiency of concrete made of waste plastics and different mineral admixtures, for this study things to be find are as follows,
-
Optimum percentages of plastic waste (LDPE) used
-
Variation of strength b/w admixtures and plastic waste used
-
Volume changes w/r to chemical attack
-
Mechanical behavior w/r to chemical attack
-
-
OBJECTIVE OF THE PROJECT
The main objective of this project was,
-
To study the properties of various additives and plastic waste (LDPE) and to incorporate in the durability study
-
To check the mechanical behavior for different mix proportion
-
To investigate the various durability properties of concrete to the optimum mix proportion (ASTM Stands)
-
To validate the result of normal concrete with the concrete made of different additives.
1.8. SIGNIFICANCE
Concrete which made of waste plastics is a cost effective construction material, and addition of available mineral additives enhance the physical and mechanical behavior of concrete, use of plastic waste is a cost effective in mean time give good resistance to flexural behavior of concrete, use of rice husk ash enhance the durability of concrete due to micro fine structure and silica fume enhance the durability of concrete to a greater extent.
MATERIALS AND THEIR PROPERTIES
-
MATERIALS USED
The following are the materials which are chosen to incorporate in my project, and their properties are listed below,
-
CEMENT
The cement used in all mixture was commercially available Ordinary Portland Cement (OPC) of 53 graded confirmed to IS: 8112-1989. The initial and final setting times were found as 32 & 130 minutes respectively. Specific gravity of cement is 3.15.
-
FINE AGGREGATE
Locally available M sand of size below 4.75 mm conforming to Zone II of IS 383-1970 is used as fine aggregate. The Laboratory tests were conducted for fine aggregate to determine its physical properties as IS: 2386 (Part III). Specific gravity of fine aggregate is 2.78.
-
COARSE AGGREGATE
Coarse aggregate used in this study consist of size 20 mm. Laboratory tests were conducted on coarse aggregate to determine the different physical properties as per IS: 383-1970. Specific gravity of coarse aggregate 20 mm is 2.8 and 12.5 mm is 2.78.
-
SILICA FUME
Silica fume (very non crystalline silicon dioxide) is a by-product of the manufacture of silicon, ferrosilicon etc. According to IS: 456 silica fume is usually used in proportion of 5 to 10 percent of the cement content of a mix. In this study commercially available silica fume is used, Specific gravity of silica fume is 2.2.
-
RICE HUSK ASH
Rice husk is an agricultural residue obtained from the outer covering of rice grains during milling process. The ash produced by controlled burning of the rice husk between 550°C and 700°C incinerating temperature for 1 hour to transforms the silica content of the ash into amorphous phase. Specific gravity of rice husk ash is 2.10.
-
PLASTIC WASTES (LDPE)
LDPE which is low density polyethylene, used for the manufacturing bottles plastic cover and surgical glove e.t.c, these wastes was grinded into powder form to micro fine structure and it can be used as a replacement in concrete which is a best disposal method. The LDPE wastes are obtained from nearby plastic industry at Sivakasi.
-
-
MATERIAL PROPERTIES
-
SPECIFIC GRAVITY OF CEMENT
The specific gravity of cement is determined by Le Chatelier Flask or Specific gravity bottle and details shown in Table 4.2. Weigh a clean and dry bottle and is taken as W1. Place a sample of cement up to half of the bottle and is taken as W2. Kerosene is added to cement in the bottle and is
taken as W3. Finally, the weight of bottle and kerosene is taken as W4.
-
SPECIFIC GRAVITY OF THE FINE AGGREGATE
-
The specific gravity of fine aggregate (M sand) is determined by using a pycnometer and details shown in Table
4.3. Take a clean pycnometer with its cap and weight it W1. Take dry sand in the pycnometer W2. Fill the pycnometer with water up to the hole in the vertical cap and shake it to remove the air then take the weight of pycnometer with sand and water W3. Empty the pycnometer and clean it through then fill it with water up to the hole in conical cap and take the weight W4.
SPECIFIC GRAVITY OF THE COARSE AGGREGATE
The specific gravity of coarse aggregate is determined by using a pycnometer and details shown in Table
-
& 4.5. Take a clean pycnometer with its cap and weight it W1. Take dry sand in the pycnometer W2. Fill the pycnometer with water up to the hole in the vertical cap and shake it to remove the air then take the weight of pycnometer with sand and water W3. Empty the pycnometer and clean it through then fill it with water up to the hole in conical cap and take the weight W4.
-
CHAPTER 5
-
MIX DESIGN
-
5.1. CONCRETE MIX DESIGN
-
One of the ultimate aims of studying the various properties of the materials of concrete, plastic concrete and hardened concrete is to enable a concrete technologist to design a concrete mix for a particular strength and durability. The design of concrete mix is not a simple task on account of the widely varying properties of the constituent materials, the conditions that prevail at the site of work, in particular the exposure condition, and the conditions that are demanded for a particular work for which the mix is designed. Mix design can be defined as the process of selecting suitable ingredients of concrete and determining their relative proportios with the object of producing concrete of certain minimum strength and durability as economically as possible. The purpose of designing as can be seen is to achieve the stipulated strength and durability.
-
MIX DESIGN FOR M 35 GRADE OF CONCRETE Design stipulations
-
Characteristic compressive strength Required in the field at 28 days – 35 N/mm2
-
Maximum size of aggregate – 20 mm
-
Method of concrete placing – Manual
-
Degree of workability – 100 ± 25 mmSlump.
-
Degree of quality control – Good
-
Type of exposure – severe
Test data for materials
-
Cement used Ordinary Portland Cement 53 grade
Estimated water content for 125 mm slump
186+ (9/100) x186= 203 kg/m3
Admixture dosage 0.8% , reduce water content 20% Water content = 203 x 0.8 = 162 kg/m3
Step 4 Calculation of Cement content
= 162 / 0.39
-
Specific gravity of cement – 3.15
= 415.38 kg/m3
-
Specific gravity of coarse aggregate20 mm – 2.80
= 415 kg/m3
-
Specific gravity of coarse aggregate12.5 mm
Add Si-li2c.a78Fume @10% = 415 x 0.1 = 41.5 = 42
3
-
Specific gravity of fine aggregate(M sand)
kg/m
– 2.72
-
Specific gravity of Admixture (Sika Viscocrete 1062 NS) – 1.09
-
Specific gravity of silica fume
Add Rice Husk Ash @20% = 415 x 0.2 = 83
kg/m3
Cement Content = 415- 42 – 83 = 290 kg/m3
Step 5 Proportion of volume of Coarse aggregate and Fine
– 2.2
aggregate
-
Specific gravity of rice husk ash – 2.10
From table 3 (IS 10262 2019)
-
Water absorption of coarse aggregate 20mm
– 0.3%
-
Water absorption of coarse aggregate12.5mm
– 0.4%
-
Water absorption of Fine aggregate( M sand)
-
-
– 2.88%
DESIGN
Step 1 Target Mean Strength of Concrete:
fck = fck + t × s
fck = 35 + (1.65×5)
= 43.25 N/mm2
Step 2 Selection of W/C ratio:
From the figure -1 of IS 10262-2019
Grade |
Target |
W/C ratio |
M35 |
43.25 N/mm2 |
From the Table 5 of IS 456 for severe Exposure maximum Water Cement Ratio is0.45,
0.39 < 0.45 Hence ok.
Step 3 Selection of Water content
From table-4 of IS 10262-2019 Size of aggregate = 20mm
Water cement per cubic meter of cement = 186 kg/m3
Approximate sand and water content per cubic meter of concrete
W/C ratio = 0.39
W/C ratio 0.5 = 0.62, zone II, 20mm coarse aggregate
For every ±0.05 change in w/c, the coarse aggregate proportion is to be changed by 0.01. If the w/c is less than
-
(standard value), volume of coarse aggregate is required to be increased to reduce the fine aggregate content. If the w/c is more than 0.5, volume of coarse aggregate is to be reduced to increase the fine aggregatecontent. If coarse aggregate is not angular, volume of coarse aggregate may be required to be increased suitably, based on experience.
W/C ratio 0.45 = 0.64
For pump able concrete or congested reinforcement, the coarse aggregate proportionmay be reduced up to 6%
Volume of coarse aggregate = 0.64 x 0.94 = 0.60 Volume of fine aggregate = 1-0.60 = 0.40
Step 6 Estimation of the mix ingredients:
-
Volume of concrete = 1 m3
-
Volume of entrapped air 0.5% = 0.005 m3
-
Volume of cement = (Mass of cement / Specific gravity of cement) x(1/1000)
= (290/3.15) x (1/1000) = 0.092 m3.
-
Volume of SF = (Mass of SF / Specific gravity of SF) x(1/1000)
= (42/2.20) x (1/1000) = 0.019 m3.
-
Volume of RHA = (Mass of RHA / Specific gravity of RHA) x(1/1000)
= (83/2.10) x (1/1000) = 0.040 m3.
-
Volume of water = (Mass of water / Specific gravity of water) x (1/1000)
= (162/1) x (1/1000) = 0.162 m3
-
Volume of Admixture= (Mass of Admix. / Specific gravity of Admixture) x (1/1000)
= ((415 * .8%)/1.09) x (1/1000) = 0.003 m3
-
Volume of total aggregates = a (b + c + d + e + f+ g )
=1(0.005+0.092+ 0.019+0.040+0.162+0.003)
= 0.679 m3.
-
Volume of coarse aggregates = 0.679 x 0.60
= 0.407 m3.
-
Volume of coarse aggregates 20mm = 0.407 x 0.60
= 0.244 m3.
-
Volume of coarse aggregates 12.5mm = 0.407x 0.40 = 0.163 m3.
-
Volume of Fine aggregate = 0.679 x 0.40 =
0.272 m3
-
Mass of coarse aggregates 20mm = 0.244x
2.80 x 10
= 683.20 kg/m3
= 683 kg/m3
-
Mass of coarse aggregates 12.5mm = 0.163 x 2.78 x 1000
= 453.14 kg/m3
= 453 kg/m3
-
Mass of fine aggregates = 0.272 x 2.72 x 1000
-
= 739.84 kg/m3
= 740 kg/m3
Total quantities of ingredients and mix proportion for 1m3:
Grade of Concrete: M35
Material |
Quantity (kg) |
OPC-53 |
290 |
Silica Fume |
42 |
Rice Husk ash |
83 |
20mm |
683 |
12.5mm |
453 |
M Sand (ZONE II) |
740 |
Water |
162 |
Admixture |
3.32 |
MIX RATIO: 1:1.78:2.73
-
Volume of cube = 150mm x 150mm x 150mm
= 0.00338 m3
-
Volume of cylinder Ø 150mm, Height 300 mm = 0.0053 m3
CHAPTER 6 EXPERIMENTAL WORK
-
CONCRETE
Concrete is the most widely used man made construction material. It is obtained by mixing cement, water and aggregates in required proportions. The mixture when placed in the forms and allowed to cure becomes hard like stone. The hardening is caused by chemical action between water and cement and it continues for a long time, and consequently the concrete grows stronger with age.
The strength, durability and other characteristics of concrete depend upon the properties of its ingredients, on the proportions of mix, the method of compaction and other control during placing, compaction, and curing. The popularity of the concrete is due to the fact that from the common ingredients, it is possible to tailor the properties of the concrete to meet the demands of any particular situation. The various aspects covered in the following titles are the materials, mix proportioning, elements of workmanship e.g. placing, compaction and curing, method of testing etc.
-
PROCESS OF CONCRETING
Batching:
The measurement of materials for making concrete is known as batching
Mixing:
Mixing of concrete is almost invariably carried out by machine, for reinforced concrete work. Machine mixing is not only efficient, but also economical, when the quality of concrete to be produced is large. Many types of mixes are available they are batch mixes and continuous mixers. Concrete mixers are often used for mixing of concrete.
Moulds
Metal moulds, preferably steel or cast iron, thick enough to prevent distortion is required. The height of mould and distance between the opposite faces are of the specified size ± 0.2mm. The interior faces of the mould are plane surface with permissible vibration of 0.03 mm. Cube mold size 150x150x150 mm and cylinder 150 mm diameter & height 300 mm.
-
TESTING OF HARDENED CONCRETE
Testing of Hardened concrete plays an important role in controlling and confirming the quality of cement concrete works. The test methods should be simple, direct and convenient to apply.
The following tests has been conducted are given below.
-
Test for Compressive strngth
-
-
-
CUBE SPECIMEN DETAILS
6.3.2.
Cube of size 150x150x150mm is used to determine the compressive strength of concrete M35 and number of cube specimen used is shown in Table 6.1
Table.6.1. Number of cubes specimen
Cube specification 150x150x150 mm |
Percentage |
Number of specimens |
Conventional concrete |
– |
3 |
LDPE Waste |
05 |
3 |
10 |
3 |
|
15 |
3 |
|
20 |
3 |
|
30 |
3 |
|
40 |
3 |
|
50 |
3 |
|
RHA 20%, SF10% LDPE (optimum%) |
20:10:05 |
3 |
20:10:10 |
3 |
|
20:10:15 |
3 |
|
20:10:20 |
3 |
|
20:10:30 |
3 |
|
20:10:40 |
3 |
|
20:10:50 |
3 |
CYLINDER SPECIMEN DETAILS
Cylinder specification 150mm dia and 300 mm height |
Percentage |
number of specimen |
Conventional concrete |
– |
3 |
LDPE Waste |
05 |
3 |
10 |
3 |
|
15 |
3 |
|
20 |
3 |
|
30 |
3 |
|
40 |
3 |
|
50 |
3 |
|
RHA 20%, SF10% LDPE (optimum %) |
20:10:05 |
3 |
20:10:10 |
3 |
|
20:10:15 |
3 |
|
20:10:20 |
3 |
|
20:10:0 |
3 |
|
20:10:40 |
3 |
|
20:10:50 |
3 |
Cylinder of size 150mm diameter and 300mm height is used to determine the spilt tensile strength of the concrete M35 and number of cylinder specimen used is shown in Table 6.2.
CASTING OF SPECIMENS
Steel mould was used for casting the cubes, cylinders and beams. Before casting, machine oil was applied on the inner surface of the mould. Concrete was mixed using both Hand mix and Machine mix (tilting type laboratory mixer) and was poured into the moulds in layers. Compaction of concrete was done using a needle vibrator and also using damping rod. After 24 hours from casting, all the specimens were dmoulded and placed in a curing tank under water for a period of 28 days.
-
TESTING OF HARDENED CONCRETE Testing of Hardened concrete plays an important role
in controlling and confirming the quality of cement concrete works. The test methods should be simple, direct and convenient to apply.
The following tests has been conducted are given below.
-
Test for Compressive strength
-
-
TESTING
-
COMPRESSTION TEST
Compressive strength or compression strength is the capacity of a material or structure to withstand loads tending to reduce size, as opposed to tensile strength, which withstands loads tending to elongate. All the cubes were tested under Compression Testing Machine (CTM). For loading the Cubes 3000 kN capacity hydraulic compression testing machine was used. The load was measured using load cell of 500kN capacity. The loading on cube increased gradually and the Ultimate load was obtained and the Load value was measured using Digital display gauge. The specimens shall be tested in accordance with IS: 516-1959.
-
Concrete Permeability
One of the main characteristics influencing the durability of any concrete is its permeability. Three specimen of concrete each of 200mm dia and 120mm height are cast. 2. After 24 hours, the middle portion of 100mm dia is roughened and the remaining portion is sealed with cement paste. 3. The specimen are cured for 28 days and then water pressure is applied on the middle roughened portion so that water can penetrate inside the concrete. The water pressure is maintained as 1 bar for 48 hours, 3 bars for next 24 hours, 7 bars for next 24 hours. The specimen are split in compression machine by applying concentrated load at two diagonally opposite points slightly away from central axis. The Observed average water penetration value is 5mm.
6.5.1 WATER ABSORPTION
After 28 days of water curing the concrete cube is kept at oven for105o c for 24 hours, and then dry weight of cube should be noted. Then the concrete cube should immerse on water for 24 hours and then the wet weight of cube should be noted the difference among which called as the percentage of water absorption.
CHAPTER 7 RESULTS AND DISCUSSION
The representation of the results in graph helps in better understanding of the Strength variations by adding Copper Slag and Styrene Butadiene Rubber under reduced water cement ratio. From the results, we can conclude the percentage of Copper Slag and Styrene Butadiene Rubber (SBR) to be added to get better performance in all the mechanical and thermal aspects. The results of the various tests conducted are discussed as follows.
7.1 COMPRESSIVE STRENGTH
The Concrete cubes are manufactured with various proportions of Low density polyethylene. Fig. 7.1 shows compressive strength testing and reading respectively.
Specimen / Strength |
7 Day (N/mm2) |
28 Day (N/mm2) |
A |
31.25 |
44.32 |
B |
29.40 |
41.23 |
C |
28.12 |
39.02 |
D |
27.02 |
37.12 |
E |
26.15 |
34.02 |
F |
25.25 |
32.10 |
The optimum percentage of LDPE is at 30% and hence to improve theperformance RHA and SF are added
The compressive strength of concrete with the Rice husk ash, Silica fume and LDPE waste are listed below in the table 7.2
Specimen / Strength |
7 Day (N/mm2) |
28 Day (N/mm2) |
A |
38.82 |
51.57 |
B |
36.87 |
48.95 |
C |
34.05 |
46.01 |
D |
33.58 |
43.19 |
E |
32.98 |
40.07 |
F |
31.59 |
38.52 |
Table 7.2 compressive strength of cubes (RHA,SF,LDPE)
REFERENCES
[1] ASTM (2008) ASTM C642-97: Standard test method for density, absorption and voids in hardened concrete. ASTM International, West Conshohocken, PA, USA. [2] IS 456:2000 Indian Standard Code of Practice for Plain and Reinforced Concrete. [3] IS12269 (1987) – "Indian standard for specification for 53 grade OPC", reaffirmed january 1999. [4] IS 10262:2009 Concrete mix proportioning-guidelines. [5] IS 2386:part 3:1963 -"Methods of test for aggregate for concrete". [6] IS 383:1970 – "Specification from fine and coarse aggregate fromnatural source for concrete".
[7] AS 1012.10, Method of testing concrete – Determination of indirect tensile strength of concrete cylinders (Brazil or Splitting Test), Ausralian Standards, 2000. [8] B.Chatveera, P.Lertwattanaruk, Durability of conventional concretes containing black rice husk ash, Journal of Environmental Management 92, 59-66 (Elsevier), September 2010. [9] K.E.Hassan, J.G.Cabrera, R.S.Maliehe, The effect of mineral admixtures on the properties of high-performance concrete, cement and concrete composites 22, 267-271 (Elsevier), 2000. [10] B.V.Bahoriaa, D.K.Parbatb, P.B.Nagarnaik, XRD Analysis of Natural sand, Quarry dust, waste plastic (ldpe) to be used as a fine aggregate in concrete, Materials today 5, 1432-1438 (Elsevier) 2018. [11] Harshad G Patel, Sejal P Dalal, An experimental investigation on physical and mechanical properties of concrete with the replacement of fine aggregate by poly vinyl chloride and glass waste, 11th International symposium on plasticity and impact mechanics 173, 1666-1671 (Elsevier) 2017. [12] Zainab Z. Ismail, Enas A. AL-Hashmi, Use of waste plastic in concrete mixture as aggregate replacement, Waste Management 28, 2041-22047 (Elsevier) October 2007. [13] Sheelan M. Hama, Nahla N. Hilal, Fresh properties of self- compacting concrete with plastic waste as partial replacement of sand, International Journal of Sustainable Built Environment 6, 299-308 (Elsevier) January2017. [14] A.N.Swaminathen, Indian Rice Husk Ash Improving The Strength And Durability Of Concrete: A Review, International Conference on Current Trends in Engineering and Technology, (IEEE) July 2013. [15] Vigneshwari, K. Arunachalam, A. Angayarkanni, Replacement of silica fume with thermally treated rice husk ash in Reactive Powder Concrete, Journal of Cleaner Production 188, 264-277, (Elsevier) April 2018.CHAPTER 8 CONCLUSION
-
The reduction in compressive strength is observed for the increase in thepercentage of plastic waste.
-
To compensate the strength loss RHA and SF are
added, both increase the strength to a greater extent due to the micro structure of both the wastes (RHA and SF)
-
The Optimum percentage of plastic waste that can
be incorporated as a replacement for sand is 30%
-
Due to the closely packed micro structure of RHA
and SF, the concrete is closely packed by reducing the porous structure which increases the durability of concrete.
-
In performance with the acid attack the specimen
performs well in all the attack compared with the control mix.
-
The plastic waste has the smooth surface, which is
the main reason for the reduction in both the compressive strength and the tensile strength of theconcrete.