
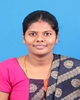
- Open Access
- Authors : S. Deepa
- Paper ID : IJERTV11IS010117
- Volume & Issue : Volume 11, Issue 01 (January 2022)
- Published (First Online): 28-01-2022
- ISSN (Online) : 2278-0181
- Publisher Name : IJERT
- License:
This work is licensed under a Creative Commons Attribution 4.0 International License
Experimental Investigation on Mechanical Properties and Durability of Concrete by Partial Replacement of Fine Aggregate using Copper Slag
S. Deepa
Assistant professor, Department of Civil Engineering,
Ambal Professional Group of Institutions, Tamil Nadu, India
Abstract – Copper slag is a by-product of copper extraction by- smelting. It is mainly used for surface blast-cleaning. Copper slag is used in concrete production as a partial replacement for sand. It act as pozzolanic material. Copper slag is used in concrete to determine the mechanical properties and durability of concrete by the partial replacement of fine aggregate. The fine aggregate (Sand) was replaced with various proportions of 0%, 10%, 20%, 30%, 40% and 50%. The workability of concrete increases with increase in replacement of copper slag. This project helps to determine the compressive strength, flexural strength, split tensile, strength and durability of concrete.
Keywords: Copper Slag, Concrete, Compressive Strength, Flexural Strength, Tensile Strength and Durability
-
INTRODUCTION
Concrete is a composite material of water, granular material (the fine and coarse aggregate or filler ) embedded in a hard matrix of material (the cement or binder) that fills the space among the aggregate particles and glues together. Concrete versatility, durability and economy have made the world most used construction material. In India most of the construction activities are made with concrete as it is easily available and moulding can be done even by unskilled labour. Thus concrete is becoming a very important material for every human. Many environmental phenomena are known significantly the durability of reinforced concrete structure. We build concrete structure in highly polluted urban and industrial area, marine, other environments and many other hostile condition where other material of construction are found to be non- durable. The concrete is used to construct the highway, streets, parking lots, parking garages, bridges, high rise building, dam, homes, floor, sidewalk, driveway and numerous other application.
In the recent revision of IS 456-2000 one of the major point discussed is the durability aspects of concrete is unavoidable. At the same time scarcity of aggregate are also greatly increased nowadays. Therefore nowadays utilization of secondary materials is being encouraged in construction field. So the benefit of by- products in concrete technology has been used in recent projects. Since copper slag is one of the material that considered as a waste material which could have a
promising future in construction industry as partial or full replacement for aggregate. Aggregate are considered one of the main constituents of concrete. Since they occupy more than 70% of the mix whereas copper slag is glassy and granular in nature and has a similar particle size range to sand indicating that it could be used as replacement for the sand. It has a similar properties to the fine aggregate, it can be used as a replacement for this project. Copper slag is currently being used for many purpose ranging from land filling to grit blasting. These application utilize only about 15% to 20% and the remaining damped as a waste material and this cause environmental pollution. In concrete it plays vital role in minimizing the disposal problems, health hazards and aesthetic problems.
Durability of concrete may be defined as the ability of concrete to resist weathering action, chemical attack and abrasion while maintaining its desired engineering properties. When we are dealing with durability of concrete, chemical attack which result in volume change, cracking of concrete and the consequent deterioration of concrete becomes an important part of discussion under chemical attack.
The main objective of the paper identifies the usage of copper slag as sand replacement that improves the strength in concrete production without affecting durability of concrete.
-
MATERIALS USED
-
CEMENT
Selection of cement grade will depends upon the overall requirements of the concrete such as strength, durability etc., in this experimental study OPC (Ordinary Portland Cement) 53 grade is used conforming to IS 12269 (1987). For 53 grade cement the strength is not less than 53N/mm2. Some physical properties of OPC are given below:
Table 1: Test on Cement
S. No
Properties
Values
1
Specific gravity
3.15
2
Standard consistency
31%
3
Fineness of cement
8%
4
Initial setting time
37 min
5
Final setting time
310 min
-
FINE AGGREGATE
Fine aggregate are the materials passing through IS sieve that is less than 4.75 mm sieve. Usually natural sand is used as a fine aggregate due to scarcity crushed stone is used in this project.
Table 2: Test on Fine aggregate
S. No
Properties
Values
1
Specific gravity
2.7
2
Fineness Modulus
2.48
3
Water absorption
1.05%
-
COARSE AGGREGATE
Coarse aggregate are the materials retained on 4.75 mm sieve and the broken stone is generally used. According to IS 383:1970 maximum 20 mm coarse aggregate is suitable for concrete. The nature of work decides the maximum size of coarse aggregate.
Table 3: Test on Coarse Aggregate
S. No
Properties
Values
1
Specific gravity
2.7
2
Water absorption
0.8%
-
COPPER SLAG
Copper slag is the by-product material obtained during smelting and refining of copper. It is the secondary material being encouraged and utilized in construction field. Harmful effects of concrete can be reduced by producing good and durable concrete by using industrial by-product waste. Copper slag is glassy and granular in nature and has a similar particle size range to sand indicating that it could be used as replacement for the sand present in the cementitious mixes. Copper slag is currently being used for many purposes ranging from land filling to grit blasting. This application utilize only about 15% to 20% and the remaining as a waste material and this cause environmental pollution. While using copper slag in concrete it plays vital role in minimizing the
disposal problem, health hazards and aesthetic problems.
Fig. 1 Copper slag
Table 4: Test on Copper Slag
S. No
Properties
Values
1
Specific gravity
3.57
2
Fineness Modulus
3.23
3
Water absorption
1.03%
-
WATER
Water is an important ingredient of concrete, as it actively participates in chemical reaction with cement. The quantity and quality of water is required to be looked very carefully. In the present study tap water is used.
-
-
EXPERIMENTAL INVESTIGATION
In this research work, the concrete strength and replaced concrete strength M30 grade of concrete was found. The properties of concrete materials and strength are determined as per IS 10262-2009. Mix design was designed to 30N/mm2 compressive strength at 28 days using water cement ratio 0.50.
-
MIX DESIGN OF CONCRETE GRADE
Table 5: Mix proportion by weight (kg/m3)
Cement
Fine aggregate
Coarse aggregate
Water
394
732
1139
197
1
1.85
2.89
0.50
Table 6: Replacement of copper slag with fine aggregate
Mix %
Cem ent (kg/ m3)
Fine aggreg ate (kg/m3
)
Coppe r slag (kg/m3
)
Coarse aggregat e (kg/m3)
Wate r (kg/ m3)
0%
394
732
0
1139
197
10%
394
658.8
73.2
1139
197
20%
394
558.6
146.4
1139
197
30%
394
512.4
219.6
1139
197
40%
394
439.2
292.8
1139
197
50%
394
366
366
1139
197
-
PREPARATION OF MOULD SIZE
-
Cube size 150mm x 150mm x 150mm
-
Beam size 1200mm x 150mm x 150mm
-
Cylinder size 150mm (Dia) x 300mm (Height)
-
-
CURING OF CONCRETE
Curing of concrete is a method by which the concrete is protected against loss of moisture required for hydration and kept at recommended temperature. It will increase the strength and decrease the permeability of hardened concrete. It helps to improve the durability of concrete by reducing the cracks. Cubes are cured for and tested at 7 and 28 days. The results from the compressive strength are used to determine the strength of concrete.
-
-
TEST RESULTS
-
TEST ON FRESH CONCRETE
The concrete slump test measures the consistency of fresh concrete before it sets. Workability of fresh concrete is known by slump cone test as per 1199-1959 is followed.
Table 7: Workability of concrete mixture
Mix Identity (Percentage in replacement)
Slump value (mm)
0% CS
25
10% CS
25
20% CS
28
30% CS
30
40% CS
30
50% CS
32
*Whereas, CS – Copper Slag
-
TEST ON HARDENED CONCRETE
Hardened concrete helps to investigate the fundamental physical behaviour of concrete such as elastic properties and strength characteristics.
-
Compressive strength: Compressive strength or Compression strength is the capacity of a material or structure to withstand loads tending to reduce size. Test is done according to code specification IS 516:2959. To determine the compressive strength, cube mould of size 150x150x150 mm were casted. Cubes were prepared and tested at 7 and 28 days of curing in water under laboratory temperature. The compressive strength is calculated using the formula,
Whereas,
T Split tensile strength (N/mm2) P Ultimate load (N)
L Length of the cylinder (mm) D Diameter of Cylinder (mm)
Compressive strength (N/mm2) = P/A
Where,
P Ultimate load (N) A Loaded area (mm2)
Fig. 2 Compressive strength test
Mix Identity (Percentage in replacement)
Compressive strength in 7 days (N/mm2)
Compressive strength in 28 days (N/mm2)
0%
28.48
29.50
10%
28.67
29.20
20%
30.52
34.80
30%
33.20
40.20
40%
38.37
44.73
50%
25.46
37.32
Mix Identity (Percentage in replacement)
Compressive strength in 7 days (N/mm2)
Compressive strength in 28 days (N/mm2)
0%
28.48
29.50
10%
28.67
29.20
20%
30.52
34.80
30%
33.20
40.20
40%
38.37
44.73
50%
25.46
37.32
Table 8: Compressive strength test results (N/mm2)
Fig. 3 Split tensile strength test
Table 9: Split tensile strength result
Mix identity (%)
Split Tensile in 7 days (N/mm2)
Split Tensile in 28 days (N/mm2)
0%
3.78
4.32
10%
3.73
4.46
20%
4.32
4.64
30%
4.48
4.73
40%
4.63
4.86
50%
4.42
4.27
From the table 9, the maximum split tensile strength is obtained at 40% replacement of copper slag in 28 days is
4.86 N/mm2.
From the test result, it can be seen that optimum percentage attained at 40% of replacement using copper slag. Finally, the compressive strength increases with increase in its duration. The maximum percentage of increase in strength is found to be 44.73/N/mm2 at 40% replacement of fine aggregate by copper slag, while comparing to 29.50 N/mm2 for a normal mix.
Compressive strength (N/mm2)
Compressive strength (N/mm2)
7 days 28 days
7 days 28 days
Split tensile strength (N/mm2)
Split tensile strength (N/mm2)
6
5
4
3
2
1
0
0% 10% 20% 30% 40% 50%
Mix identity
50
40
30
20
10
0
0% 10% 20% 30% 40% 50%
Mix identity
Graph 2: Split tensile strength of cylinder in 7 & 28 days
3. Flexural strength: A concrete beam of size 1200 mm x 150 mm x 150 mm where casted with different replacement ranges from 0% to 50%. Beams are cured for 7 and 28 days. Flexural strength test for beams is calculated using the formula,
F=PL/bd2
Whereas,
Graph 1: Compressive strength of cube in 7 & 28 days
-
Split tensile strength: A cylindrical concrete of size 150mm dia x 300mm height placed in longitudinal access is perpendicular to the load. The load shall be applied gradually range from 1.2 (N/mm2/Min) to 2.4 (N/mm2/Min). It can be calculated using the formula,
-
T=2P/LD
F Flexural strength (N/mm2) P Ultimate load (N)
L Length of the beam (mm) b Average width (mm)
d Average depth (mm)
Fig. 4 Flexural strength test
Flexural strength (N/mm2)
Flexural strength (N/mm2)
Table 10: Flexural strength result
Mix Identity (Percentage in replacement)
Flexural strength in days (N/mm2)
Flexural strength in 28 days (N/mm2)
0%
2.95
4.29
10%
3.21
4.17
20%
3.45
4.86
30%
3.86
5.24
40%
4.39
5.47
50%
4.28
4.02
7 days 28 days
6
5
4
3
2
1
0
0% 10% 20% 30% 40% 50%
Mix identity
7 days 28 days
6
5
4
3
2
1
0
0% 10% 20% 30% 40% 50%
Mix identity
Graph 3: Flexural strength of cylinder in 7 & 28 days
4. Durability Test: Durability of concrete is defined as the ability of concrete to resist weathering action, Chemical attack and abrasion while maintaining its desired engineering properties. A total number of 18 cubes of size 150mmx150mmx150mm was casted and stored in a place at a temperature of 27°C for 24 hours and then the demoulded specimens were cured for 28 days. After 28 days of curing cubes were allowed to dry for 1 day. The weight of the concrete cube were taken. The surface of the cubes were cleaned, weighed and then tested in the compression testing machine.
The acid attack test on concrete cube was conducted by immersing the cubes in the acid water for 90 days of curing. HCL, NaOH, Na2SO4 with PH of about to at 5% weight of water is added. After 90 days immersion, concrete cube were taken and tested for compressive strength.
-
Acid attack test: The acid attack of combined admixtures in concrete found to be gain in weight of cube was measured and compared with normal concrete. Table 11 gives the test result obtain from acid attack test where M0, M1, M2, M3, M4 & M5 explains that 0%, 10%, 20%, 30%, 40% & 50% replacement of the mix proportion.
Fig. 5 Acid attack on cubes
Compressive strength (N/mm2)
Compressive strength (N/mm2)
Table 11: Acid attack test
Mix Identity
Compressive strength of cubes in water curing (N/mm2)
Compressive strength of cubes in acid curing (90 days) (N/mm2)
M0
29.50
26.20
M1
29.20
25.73
M2
34.80
30.26
M3
40.20
33.42
M4
44.73
31.30
M5
37.32
28.57
Cubes in water curing Cubes in acid curing 50
40
30
20
10
0
M0 M1 M2 M3 M4 M5
Mix identity
Cubes in water curing Cubes in acid curing 50
40
30
20
10
0
M0 M1 M2 M3 M4 M5
Mix identity
Graph 4: Compressive strength after acid attack
Table 12: Weight loss in acid attack
Mix Identity
Before acid curing (Kg)
After acid curing (Kg) (90 days)
M0
8.500
8.200
M1
8.624
8.282
M2
8.792
8.391
M3
8.851
8.497
M4
8.965
8.612
M5
9.012
8.702
Before acid curing After acid curing
9.5
9
8.5
8
7.5
M0 M1 M2 M3 M4 M5
Mix identity
Before acid curing After acid curing
9.5
9
8.5
8
7.5
M0 M1 M2 M3 M4 M5
Mix identity
Before Sulphate curing After Sulphate curing
9.5
9
8.5
8
7.5
M0 M1 M2 M3 M4 M5
Mix identity
Before Sulphate curing After Sulphate curing
9.5
9
8.5
8
7.5
M0 M1 M2 M3 M4 M5
Mix identity
Cube weight (Kg)
Cube weight (Kg)
Cube weight (Kg)
Cube weight (Kg)
Graph 5: Weight loss of acid attack
-
Sulphate attack: The sulphate attack of combined admixtures in concrete found to be gain in weight of cube was measured and compared with normal concrete. Table 13 gives the test result obtain from Sulphate attack test where M0, M1, M2, M3, M4 & M5 explains that 0%, 10%, 20%, 30%, 40% & 50% replacement of the mix proportion.
Table 13: Sulphate attack test
Graph 7: Weight loss of Sulphate attack
-
Sodium hydroxide attack: The Sodium hydroxide attack of combined admixtures in concrete found to be gain in weight of cube was measured and compared with normal concrete. Table 15 gives the test result obtain from Sodium hydroxide attack test where M0, M1, M2, M3, M4 & M5 explains that 0%, 10%, 20%, 30%, 40% & 50% replacement of the mix proportion.
strength of cubes in water curing (N/mm2)
strength of cubes in sulphate curing (N/mm2) (90 days)
Mix Identity
Compressive strength of cubes in water curing (N/mm2)
Compressive strength of cubes in Sodium hydroxide curing
M0
29.50
25.80
(N/mm2) (90
M1
29.20
24.36
days)
M2
34.80
29.60
M0
29.50
25.60
M3
40.20
31.24
M1
29.20
24.18
M4
44.73
29.32
M2
34.80
30.42
M5
37.32
27.46
M3
40.20
31.26
M4
44.73
29.13
strength of cubes in water curing (N/mm2)
strength of cubes in sulphate curing (N/mm2) (90 days)
Mix Identity
Compressive strength of cubes in water curing (N/mm2)
Compressive strength of cubes in Sodium hydroxide curing
M0
29.50
25.80
(N/mm2) (90
M1
29.20
24.36
days)
M2
34.80
29.60
M0
29.50
25.60
M3
40.20
31.24
M1
29.20
24.18
M4
44.73
29.32
M2
34.80
30.42
M5
37.32
27.46
M3
40.20
31.26
M4
44.73
29.13
Mix Identity Compressive
Compressive
Table 15: Sodium hydroxide attack test
Compressive strength (N/mm2)
Compressive strength (N/mm2)
Cubes in water curing Cubes in sulphate curing 50
40
30
20
10
0
M5 37.32 26.47
M0 M1 M2 M3 M4 M5
Mix identity
Mix Identity
Before Sulphate curing (Kg)
After Sulphate curing weight (Kg) (90 days)
M0
8.500
8.400
M1
8.624
8.521
M2
8.792
8.610
M3
8.851
8.077
M4
8.965
8.882
M5
9.012
8.912
Mix Identity
Before Sulphate curing (Kg)
After Sulphate curing weight (Kg) (90 days)
M0
8.500
8.400
M1
8.624
8.521
M2
8.792
8.610
M3
8.851
8.077
M4
8.965
8.882
M5
9.012
8.912
Graph 6: Compressive strength after Sulphate attack Table 14: Weight loss in Sulphate attack
Cubes in water curing
Cubes in Sodium hydroxide curing
50
40
30
20
10
0
M0 M1 M2 M3 M4 M5
Mix identity
Cubes in water curing
Cubes in Sodium hydroxide curing
50
40
30
20
10
0
M0 M1 M2 M3 M4 M5
Mix identity
Compressive strength (N/mm2)
Compressive strength (N/mm2)
Graph 8: Compressive strength after Sodium hydroxide attack
Table 16: Weight loss in Sodium hydroxide attack
Mix Identity
Before Sodium hydroxide curing (Kg)
After Sodium hydroxide curing weight (Kg) (90 days)
M0
8.500
8.310
M1
8.624
8.412
M2
8.792
8.534
M3
8.851
8.567
M4
8.965
8.682
M5
9.012
8.712
Before Sodium hydroxide curing After Sodium hydroxide curing
9.5
9
8.5
8
7.5
M0 M1 M2 M3 M4 M5
Mix identity
Before Sodium hydroxide curing After Sodium hydroxide curing
9.5
9
8.5
8
7.5
M0 M1 M2 M3 M4 M5
Mix identity
Cube weight (Kg)
Cube weight (Kg)
Graph 9: Weight loss of Sodium hydroxide attack
-
-
CONCLUSION
Based on this experimental study, the following conclusions were made:
-
As per the IS code recommendations the material properties are within the limit and we will be using for our research.
-
The maximum compressive strength is found to be 44.73/N/mm2 at 40% replacement of fine aggregate by copper slag, while comparing to 29.50 N/mm2 for a normal mix.
-
The maximum split tensile strength is obtained at 40% replacement of copper slag in 28 days is 4.86 N/mm2. Beyond 50% of replacement the strength started to reduce.
-
The maximum flexural strength is obtained at 40% replacement of fine aggregate using copper slag is
5.47 N/mm2.
-
Control specimens showed higher resistance to acid attack than copper slag replaced specimens. So the conclusion is made that controlled specimen has higher resistance to acid attack compared to copper slag admixed concrete.
-
In acid attack test result shows that in concrete mix proportion is low resistance to acid solution. Also concrete with copper slag as a partial replacement
of sand shows good to resistance in sulphate attack while comparing to control concrete mix.
-
It can be concluded that, after aging the copper slag can be used as 40% replacement of fine aggregate to produce higher quality concrete.
-
-
REFERENCES
-
Kalaiselvi Subramani, Prabhakaran Subramani (October 2020) An Experimental Investigation on Partial Replacement of Copper Slag as Fine Aggregate in Paver Block International Journal of ChemTech Research.
-
Ms. K. Pandeeswari, J. Kalaignanam and A. Kalithmohammad (May 2019) A Study On Copper Slag As Replacement Of Fine Aggregate With Addition Of Red Soil International Journal of Advanced Research (IJAR)
-
Mr Suhas S. Malkhare, Prof. Atul B. Pujari (May 2018) To Study the Performance of Copper Slag As Partial or Fully Replacement to Fine Aggregates in Concrete International Journal of Research & Review Vol.5; Issue: 5; May 2018.
-
IS: 383-1970 Specification for Coarse and Fine aggregate from natural sources for concrete, (2nd revision), BIS, New Delhi.
-
Anne Mary Janarthanan (December2016) an Experimental investigation on copper slag as replacement of fine aggregate in concrete International Journal of Civil Engineering and Technology (IJCIET) Volume 7.
-
Sabarishri .V, Raguvaran .S and Mohankumar .M (2015) Experimental study on the strength properties of high performance concrete using copper slag as partial replacement of fine aggregate Journal Of Chemical Pharmaceutical Sciences Issue 8, pp-52-56
-
Sushma .V, Suresh Babu. T and Manikanta. V (2015) A Study on the partial Replacement of Fine Aggregate with Copper Slag with Reference to Laboratory Experimental Analysis International Journal of Computational Science, Mathematics and Engineering vol-2, Issue 5, pp-90-95
-
Indian Standard Recommended Guidelines for Concrete Mix Design. IS 10262-2000
-
Deepak Gowda.S and Balakrishna.H (April-2014) Experimental study on flexural behaviour of reinforced concrete beams by replacing copper slag as fine aggregate International Journal of civil and structural engineering, Vol,2 ,
Issue 1, PP- 97-103
-
Alnuaimi .A.S (March 2012) Effect of copper slag as a replacement for fine aggregate on the behaviour and ultimate strength of reinforced concrete slender columns TJER, Vol ,9, No .2, PP 90-102