
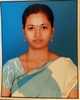
- Open Access
- [post-views]
- Authors : Ezhilarasi. R , Reya George. K
- Paper ID : IJERTV9IS050496
- Volume & Issue : Volume 09, Issue 05 (May 2020)
- Published (First Online): 20-05-2020
- ISSN (Online) : 2278-0181
- Publisher Name : IJERT
- License:
This work is licensed under a Creative Commons Attribution 4.0 International License
Experimental Investigation on Self Compacting Concrete by Replacing Industrial Waste Materials
Ezhilarasi. R1
Assistant Professor Department of Civil Engineering Velammal Engineering College
Chennai, India
Reya George. K2
Assistant Professor Department of Civil Engineering Velammal Engineering College
Chennai, India
AbstractDue to versatility of concrete as a construction material, it is utilized in large quantities over the world. Self- compacting concrete is an innovative concrete which does not require any vibration and gets compacted on its own weight. To check the feasibility of utilizing different waste materials and industrial by products in concrete, extensive research has been carried out to develop high quality and grade of SCC. This paper reviews the influence of utilizing such waste materials as partial replacement of cement and the performance of SCC in both fresh and hardened state. Its durability aspects were also considered
KeywordsSelf compacting Concrete, Nano silica, Micro silica, Acid resistance, Sulphate resistance test, Acid resistance test.
This Self-compacting concrete (SCC) was first developed in Japan (in the mid to late 1980s) as a means to create uniformity in the quality of concrete by controlling the ever present problem of insufficient compaction by a workforce that was losing skilled labor and by the increased complexity of designs and reinforcement details in modern structural members. Durability was the main concern and the purpose was to develop a concrete mix that would reduce or eliminate the need for vibration to achieve consolidation. Self-compacting concrete achieves this by its unique fresh state properties. In the plastic state, it flows under its own weight and maintain homogeneity while completely filling any formwork and passing around congested reinforcement. In the hardened state, it equals or excels standard concrete with respect to strength and durability. The use of SCC concrete has been increasing in the United States also during the last 5 years. Currently the technology is being primarily applied to the precast industry. Other segments being targeted are flatwork, columns and wall construction. The applications of SCC are many, limited only by the industry's knowledge of it, ability to produce it and acceptance of it. The usual self- compacting concretes have compressive strengths in the range of 60-100N/mm². However Ultra High Performance Self-Compacting Concrete (UHPSCC) with strength about 150N/mm² has also been successfully developed. The durability of cement concrete is defined as its ability to resist weathering action, chemical attack, abrasion or any other process of deterioration. Durable concrete will remain its original form, quality and serviceability when exposed to its environment.
-
LITERATURE REVIEW
Ever since the first report of the development of SCC in Japan in 1988 by OZAWA ET AL using super plasticizers and viscosity against and in 1992, they again identified the factors controlling self-compacting namely coarse and fine aggregate content, and presented the paper at CANMET ACI International Conference (1992) which spread the concept of SCC in the world
Ahamad Askari et.al (2011) An experimental investigation into mechanical properties of self-compacting concrete inculpating fly ash and silica fume at different ages of curing. Self-compacting mixtures had a cement replacement of 20, 30 and 40% with class F fly ash and 5,10 and 15% with silica fume. The results show that normal strength self-compacting concrete could be successfully produced using fly ash and silica fume. Compressive strength after 28 days in mixtures containing fly ash is fairly balanced, with the result that specimens containing 30% fly ash along with 5% silica fume content develop compressive strength similar to the control mixture. Mucteba Uysal et.al (2011) has investigated performance of self-compacting concrete containing different mineral admixtures. The influence of mineral admixture on a workability, compressive strength, ultrasonic pulse velocity, density and sulphate resistance of SCC was investigated.
Sulphate resistance tests involved immersion in 10% magnesium sulphate and 10% sodium sulphate solutions for a period of 400 days. Replacing 25% of PC with FA resulted in strength of more than 150 Mpa at 400 days. On the other hand the best resistance to sodium and magnesium sulphate attacks was obtained from a combination of 40% GBFS (granulated blast furnace slag) with 60% PC. The pozzalanic materials FA and GBFS increased the late age compressive strength of SCC mixtures. Replacing 25% of PC with FA resulted in a strength of more than 150Mpa at 400 days. Replacing cement with 40% GBFS can reduce magnesium sulphate attack by one third when compared to control mixture. Kemalettin Yilmaz et.al (2011) has investigated effect of mineral admixtures on properties of self-compacting concrete Limestone powder (LP), Basalt powder (BP) and marble powder (MP) are used directly without attempting any additional processing in the production of SCC. The water to binder ratio is maintained at 30% for all mixtures. The results show that it is possible to successfully utilize waste LP, BP and MP as mineral admixtures in proceeding SCC. The addition of Limestone powder (LP), Basalt powder (BP) and
marble powder (MP) had positive effects on the workability. Static and dynamic elastic moduli also increased and the higher static elastic modulus and dynamic elastic modulus have been obtained for MP20 and MP10. C.Selvamony et.al (2010) has investigation on self-compacted self-curing concrete using limestone powder and clinkers which the use of Silica fume in concrete increased the dosage of super plasticizers. At the same constant sp dosage 0.8% and mineral additive constant 30%, LP can better improve the workability than that of control and fine aggregate by 5% to 45%. A maximum of 8% of lime stone powder with silica fume, 30% of quarry dust and 14% of clinkers was able to be used as mineral admixtures without affecting the self- compatibility. The silica fume was observed to improve the mechanical property of SCC, while limestone powder along with quarry dusts affecting mechanical properties of SCC. S.Venkateswara Rao et.al (2010) has investigation of effect of size of aggregate and fines on standard and high strength self-compacting concrete The mechanical properties viz., compressive strength, flexural strength and split tensile strengths were studied at the end of 3, 7 and 28 days for standard and high strength SCC with different sizes of aggregate. It was noted that with 10mm size aggregate and 52% fly ash in total powder the mechanical properties were superior in standard SCC, while 16 mm size aggregate with a 31% fly ash in total powder improved the properties of high strength SCC. Size of aggregate was 10mm for standard self- compacting concrete (M30), while it is 16mm for high strength self-compacting concrete (M70) though all other sizes. Optimum dosages of fly ash were 52% addition in case of standard grade SCC and it is 31% addition in case of high strength SCC.
-
METHODOLOGY
In this paper Self compacting concrete is made by replacing cement with Micro Silica and Nano silica. These materials were collected and replaced with Ordinary Portland Cement. Basic Physical, Mechanical properties and chemical compositions were tested for the mix design. Mix proportions were designed based on EFNARC guidelines. Fresh concrete and Workability tests were done for SCC as per code guidelines. In order to study about durability properties, few laboratory tests were done like Wter absorption and Acid Resistance.
-
Aggregates
Crushed angular granite metal of 20 mm size from a local source was used as coarse aggregate. River sand was used as fine aggregate and was used in the investigation.
-
Superplasticizer
GLENIUM B233 consists of a carboxylic ether polymer with long side chains. At the beginning of the mixing process it initiates the same electrostatic dispersion mechanism as the traditional superplasticisers, but the side chains linked to the polymer backbone generates a steric hindrance which greatly stabilizes the cement particles ability to separate and disperse. Steric hindrance provides a physical barrier (alongside the electrostatic barrier) between the cement grains. With this process, flow able concrete with greatly reduced water content is obtained. The optimum dosage of SP should be determined with trial mixes.
TABLE 1 PROPERTIES OF MATERIALS
Material Properties
Ranges
Fineness Of Cement
7.5%
Grade Of Cement
53
Specific Gravity
3.15
Initial Setting time
28 min
Final Setting Time
600 min
Specific Gravity of Coarse Aggregate
2.861
Specific Gravity of Fine Aggregate
2.705
Fineness Modulus
2.75
-
Admixtues
The concrete mixtures investigated in this study were prepared with Portland cement type II, Micro silica powder and Nano silica. The specific gravity of micro silica and Nano silica is 2.17 and 1.03, and they are silica particles with a maximum size of 0.2 m and 50 nm, respectively. In addition, Nano silica is a water emulsion with 50 % of dry solid and PH of 10.. The control mix which was exclude of micro silica and Nano silica
TABLE 2 CHEMICAL COMPOSITIONS OF ADMIXTURE
-
-
PROPERTIES OF MATERIALS
-
Portland Cement concrete
The Portland cement usually takes several hours to set, and will harden in a matter of weeks. Cement is a somewhat curious material in that it continues to harden over time as long as there is water available for the components of the cement to form bonds with. One week old Portland cement has strength of around 23 MPa, whereas three month old cement has a strength of 41 MPa. These numbers apply to standard Portland cement which has not had any additives added to it. Various treatments and additives can make cement set and harden at different rates, and various types of Portland cement also possess different properties which affect the rate of setting and hardening.
Materials
Chemical composition
%
Micro Silica
SiO2
85-95
C
0.6 -1.5
Fe2O3
0.4-2
Cao
2-2.3
Al2O3
0.5 1.7
MgO
0.1 0.9
Nano Silica
Solid content (SiO2-
content)
50 wt %
density
1.4 g/cm3
ph
9.5
Viscosity
<15cPS
Materials
Chemical composition
%
Micro Silica
SiO2
85-95
C
0.6 -1.5
Fe2O3
0.4-2
Cao
2-2.3
Al2O3
0.5 1.7
MgO
0.1 0.9
Nano Silica
Solid content (SiO2-
content)
50 wt %
density
1.4 g/cm3
ph
9.5
Viscosity
<15cPS
V MIX PROPORTIONS
Design strength of SCC =50MPa
Aggregate size = 12 mm
Specific gravity of coarse aggregate = 2.86
Bulk density of coarse aggregate =2018 kg/m3
Specific gravity of fine aggregate = 2.703
Bulk density of fine aggregate =1567 kg/m3
Specific gravity of cement = 3.15
Volume ratio of the fine aggregate = 54%
Volume ratio of coarse aggregate = 46% Super plasticizer specific gravity = 1.064 Air content in SCC = 2%
CONVENTIONAL MIX
Cement =485 kg/m3
Fine aggregate = 995 kg/m3
Coarse aggregate = 1114 kg/m3 Super plasticizer (2% of cement) = 9.7 kg/m3 Water = 156 litres
TABLE 3 MIX PROPORTIONS
S.No.
Replacement With Cement
Mix Ratios
1.
20% MS
1 : 2.56 : 2.87 : 0.4
2.
15% MS
1 : 2.39 : 2.68 : 0.37
3.
10% MS
1 : 2.28 : 2.55 : 0.35
4.
5% MS
1 : 2.15 : 2.42 : 0.34
5.
4% NS
1 : 2.14 : 2.39 : 0.33
6.
3% NS
1 : 2.10 : 2.36 : 0.33
7.
2% NS
1 : 2.09 : 2.35 : 0.33
VI EXPERIMENTAL INVESTIGATION
A.FRESH CONCRETE TEST RESULTS
Several test methods have been developed and together with visual inspection are often utilized to verify the performance of fresh SCC. However, none of these methods are standardized as yet, either nationally or internationally.
Some of these test methods include the Slump-ow test, Funnel test, U Type & Box Type tests, T50 Test, J-Ring test
TABLE 4 SCC WITH MICROSILICA TEST RESULTS
TABLE 6 COMPRESSIVE STRENGTH
S.NO.
% Replaced
7th day
28 days
1.
0% MS
24
52
2.
5% MS
26
53.75
3.
10% MS
28.45
56.85
4.
15% MS
31.75
60.50
5.
20% MS
21.65
55.75
6.
0% NS
24
52
7.
2% NS
24.45
52.55
8.
3% NS
26.75
52.90
9.
4% NS
26.65
53.10
TABLE 7 TENSILE STRENGTH
S.NO.
% Replaced
Flexure 28 days
Split Tensile 28 days
1.
0% MS
5.0
3.95
2.
5% MS
5.20
4.10
3.
10% MS
5.68
4.7
4.
15% MS
5.95
4.96
5.
20% MS
5.60
4.92
6.
0% NS
5.0
3.95
7.
2% NS
5.15
3.98
8.
3% NS
5.20
4.15
9.
/td>
4% NS
5.20
4.10
Using Nano silica in SCC individually there is no greater differences in strength gaining as compared to conventional concrete, but it as improve the flexural strength up to 5% using 3% of micro silica. The concrete with addition of 15% micro silica( based on the mass of cement) in SCC, the compressive strength, split tensile strength, flexural strength increased by 22%, 25%, 19% respectively.
S.NO
Micro Silica (%)
Slump flow
(650 mm to 800mm)
V-
funnel (6 -12
sec)
L-box test [(p/p)=
0.8 to 1]
U-Box H2/H1
=30mm (max)
1
0
780 mm
9
0.85
22.24
2
5
785 mm
9.5
0.88
23.50
3
10
700 mm
10
0.95
25.01
4
15
690 mm
10
0.87
28.31
5
20
670 mm
11
0.83
29
S.NO
Micro Silica (%)
Slump flow
(650 mm to 800mm)
V-
funnel (6 -12
sec)
L-box test [(p/p)=
0.8 to 1]
U-Box H2/H1
=30mm (max)
1
0
780 mm
9
0.85
22.24
2
5
785 mm
9.5
0.88
23.50
3
10
700 mm
10
0.95
25.01
4
15
690 mm
10
0.87
28.31
5
20
670 mm
11
0.83
29
The comparison results of micro silica, Nano silica, combination of micro silica and Nano silica specimen indicated that, a more suitable and strength gaining in SCC is combination of micro silica and Nano silica, that is concrete with combination of 15% of micro silica and 3% of Nano silica improve the compressive strength, split tensile strength, flexural strength by 25.61%, 25%, 19% respectively
TABLE 8 COMBINATION OF BOTH ADMIXTURES
TABLE 5 SCC WITH NANO SILICA
SI.
NO.
% of Micro silica
Nano silica (%)
Compressive strength at 28 days (mpa)
Split tensile strength at 28 days(mpa)
Flexural strength at 28 days(mpa)
S.NO.
Nano silica (%)
Slump flow
(650 mm to 800mm)
V-funnel (6 -12
sec)
L-box test [(p/p) =
0.8 to 1]
U-Box (H2/H1
=30mm (max)
1.
0% MS
0
52
3.95
5.0
1.
0
780 mm
9
0.85
22.24
2
52.55
3.98
5.0
2.
2
786 mm
10
0.95
25.65
3
52.90
4.15
5.15
3.
3
790mm
11
0.98
28.50
4
53.10
4.10
5.20
4.
4
791 mm
11
1.0
29.65
B.HARDENED CONCRETE TEST RESULTS
2.
5% MS
0
53.75
4.10
5.25
2
57.50
4.25
5.75
3
63.00
4.80
5.80
4
68.00
4.95
5.90
3.
10%
0
56.85
4.70
5.68
2
61.90
4.95
5.80
MS
3
64.00
5.10
5.90
4
66.00
5.20
5.96
4.
15% MS
0
60.50
4.96
5.95
2
68.00
5.15
5.98
3
76.00
5.20
6.10
4
69.00
5.25
6.25
5.
20% MS
0
55.75
4.92
5.60
2
65.00
4.95
5.70
3
67.00
4.98
5.75
4
66.50
5.00
5.80
MS
3
64.00
5.10
5.90
4
66.00
5.20
5.96
4.
15% MS
0
60.50
4.96
5.95
2
68.00
5.15
5.98
3
76.00
5.20
6.10
4
69.00
5.25
6.25
5.
20% MS
0
55.75
4.92
5.60
2
65.00
4.95
5.70
3
67.00
4.98
5.75
4
66.50
5.00
5.80
3. ACID RESISTANCE Hydrochloric acid (HCL) TABLE 11 Acid Resistance test results
-
DURABILITY TEST ON CONCRETE
The ability of this SCC along with the various admixtures are tested for its ability to resist weathering action, chemical attack and abrasion. The test on durability varies based on its environmental conditions. Here we check with the following tests.
-
SATURATED WATER ABSORPTION TEST
S.No
Mix ID
Initial weight
( Weight after 28 days)
Final weight
( Weight after 72o oven dry)
% of Weight loss
1
SCC
8.344
8.138
2.5
8.862
8.642
2.5
8.756
8.592
1.9
2
SCC+ 15 %
Micro silica with 3% of nano silica
8.454
8.310
1.7
8.348
8.208
1.7
8.353
8.199
1.8
S.No
Mix ID
Initial weight
( Weight after 28 days)
Final weight
( Weight after 72o oven dry)
% of Weight loss
1
SCC
8.344
8.138
2.5
8.862
8.642
2.5
8.756
8.592
1.9
2
SCC+ 15 %
Micro silica with 3% of nano silica
8.454
8.310
1.7
8.348
8.208
1.7
8.353
8.199
1.8
TABLE 9 Saturated water absorption test results
S.No
Mix ID
Initial weight
( Weight after 28 days)
Final weight
( Weight after 72o oven dry)
% of Weight loss
1
SCC
8.474
8.278
2.3
8.138
8.023
1.4
8.458
8.364
1.1
2
SCC+ 15 %
Micro silica with 3% of nano silica
8.480
8.325
1.8
8.391
8.296
1.1
8.248
8.174
0.9
S.No
Mix ID
Initial weight
( Weight after 28 days)
Final weight
( Weight after 72o oven dry)
% of Weight loss
1
SCC
8.474
8.278
2.3
8.138
8.023
1.4
8.458
8.364
1.1
2
SCC+ 15 %
Micro silica with 3% of nano silica
8.480
8.325
1.8
8.391
8.296
1.1
8.248
8.174
0.9
The engineering properties of SCC such as Saturated Water absorption, Sulphate Resistance, Acid Resistance improved while designing 15% of micro silica with 3 % of Nano silica.
-
SULPHATE RESISTANCE TEST
S.No
Mix ID
Initial weight
( Weight after 28 days)
Final weight
( Weight after 72o oven dry)
% of Weight loss
1
SCC
8.678
8.665
0.10
8.646
8.642
0.04
8.652
8.647
0.05
2
SCC+ 15 %
Micro silica with 3% of nano silica
8.435
8.428
0.08
8.457
8.454
0.03
8.402
8.398
0.04
S.No
Mix ID
Initial weight
( Weight after 28 days)
Final weight
( Weight after 72o oven dry)
% of Weight loss
1
SCC
8.678
8.665
0.10
8.646
8.642
0.04
8.652
8.647
0.05
2
SCC+ 15 %
Micro silica with 3% of nano silica
8.435
8.428
0.08
8.457
8.454
0.03
8.402
8.398
0.04
TABLE 10 Sulphate Resistance test results
VII CONCLUSION
Based on experimental research for three self- compacting concrete mixes (only micro silica, Nano silica, combination of micro and Nano silica), the following conclusions can be drawn at 28 days.
-
Due to observed workability and high flow ability of SCC, it can be used in highly congested reinforcement structure as compare to conventional concrete.
-
Using Nano silica in SCC individually there is no greater differences in strength gaining as compared to conventional concrete, but it as improve the flexural strength up to 5% using 3% of micro silica.
-
3.The concrete with addition of 15% micro silica( based on the mass of cement) in SCC, the compressive strength, split tensile strength, flexural strength increased by 22%, 25%, 19% respectively.
-
AS a general conclusion, the comparison results of micro silica, Nano silica, combination of micro silica and Nano silica specimen indicated that, a more suitable and strength gaining in SCC is combination of micro silica and Nano silica, that is concrete with combination of 15% of micro silica and 3% Nano silica improve the compressive strength, split tensile strength, flexural strength by 25.61%, 25%, 19% respectively.
-
5.The engineering properties of SCC such as Saturated Water absorption , Sulphate Resistance , Acid Resistance improved while designing 15% of micro silica with 3 % of Nano silica.
-
-
-
VIII REFERENCES
-
Aaron W.Saak, Hamlin M.Jennings and Srendra P.Shah , New Methodology for Designing SCC, ACI Materials Journal, Title No.98-
M46
-
Dr. Hemant Sood1, Dr.R.K.Khitoliya2 and S. S. Pathak1, Incorporating European Standards for Testing Self Compacting Concrete in Indian Conditions, International Journal of Recent Trends in Engineering, Vol. 1, No. 6, May 2009
-
Manu Santhanam and Subramanian, S. (2004) current developments in Self Compacting Concrete, Indian Concrete Journal, June, Vol., pp. 11-22
-
Jagadish Vengala Sudarsan, M.S., and Ranganath, R.V. (2003), Experimental study for obtaining self-compacting concrete, Indian Concrete Journal, August, pp. 1261- 1266.
-
Mohammed Sonebi, Steffen Grunewald and Joost walraven Filling Ability and Passing Ability of Self-Consolidating concrete, ACI materials Journal (mar/apr-2007),v.104, pp 162-170
-
Mucteba Uysal and Kemalettin Yilmaz Effect of mineral admixtures of self-compacting concrete, Cement and Concrete Composites, Vol 33(2011), pp 771-776
-
Mullick. A.K Cement-superplasticiser compatability and method of evaluation, The Indian Concrete Journal, June (2008), pp 8-15.
-
Parra.C, Valcuende.M, Gomex.F Splitting tensile Strength and modulus of elasticity of self-compacting concrete, Construction and Building materials,Vol 25(2011), pp 201-207.
-
Nagamoto N. and Ozawa K., Mixture properties of Self-Compacting, High-Performance Concrete, Proceedings,Third Canmet/ACI International Conferences on Design and Materials and Recent Advances in Concrete Technology, SP-172, V. M. Malhotra, American Concrete Institute, Farmington Hills, Mich. 623-637 (1997)
-
RavikumarM.S., Selvamony C, Kannan S.U. et al.Behaviour of self compacting self curing kiln ash concretewith various admixtures, ARPN journal of engineering and applied science, 4(8), 25-30 (2009)
-
Frances Yang A report on self consolidating concrete 3-21(2004)
-
IS: 1489 (Part-1), Indian standard specification for Portland Pozzolana cementPart1Fly ash based Bureau ofIndian Standards, New Delhi, India (1991)
-
IS:4031(Part-iv,v), Indian standard code of practice forMethods of tests for Properties of cement Bureau of Indian Standards, New Delhi, India (1988)
-
IS: 383-1970, Specifications for Coarse and Fine aggregates from Natural sources for Concrete, Bureau of Indian Standards, New Delhi, India (1970)
-
Schutter G. DE Guideline for Testing Fresh Self Compacting, 4-19 (2005)
-
EFNARC (European Federation of national tradeassociations representing producers and applicators of specialist building products), Specification and Guidelines for self- compacting concrete, Hampshire,
U.K. (2002)