
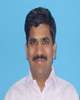
- Open Access
- Authors : Prof. Rahul Kulkarni, Mr. Vijay Machhindra Surwase
- Paper ID : IJERTV12IS050246
- Volume & Issue : Volume 12, Issue 05 (May 2023)
- Published (First Online): 13-06-2023
- ISSN (Online) : 2278-0181
- Publisher Name : IJERT
- License:
This work is licensed under a Creative Commons Attribution 4.0 International License
Experimental Study and Simulation of Test Loop flow characteristics for Vertical Pumps
Prof. Rahul Kulkarni 1, Mr. Vijay Machhindra Surwase2
Mechanical Engineering Dept. Siddhant College of Engineering, Sudumbare, Pune-4121092
ABSTRACT : The efficiency and performance of pump involving multiple pumping units depends not only on the efficiency of the pumping units but also on the proper design of the test loop. Test Loop are designed to provide Air entering, surface vortices, swirl free flow to the pump. The proper design of test Loop is not an easy task because of the various site-specific hydraulic and geometrical constraints. The cost and time involved in sump model design and optimization of Test Loop geometry can be reduced through CFD studies. Swirl degree is measured in physical model tests using swirl meter. Check and remove air when change the wall position. The vortex is called a free surface vortex based on the American National Standard for Pump Intake Design. The vortex starts at the free water surface and is sucked into the pump bell. This vortex is also referred to as a sub- surface vortex, starts at the bottom surface or the sidewalls of the sump, and enters the pump bell. This is a kind of vortex cavitation caused by low pressure at the vortex core
Index Terms Sump Model, swirl ANSYS, CFD
INTRODUCTION
The main aim of Test Loop is to provide water without air entering, uniform velocity, Swirl Free during the pump running, abnormal flow phenomena such as pressure loss, cavitation, flow separation, vibration, noise etc. It is an accepted fact that faulty design of Test Loop is one of the major causes of unsatisfactory operation of pump. The adverse flow conditions at a discharge lead to occurrence of vortices, swirl and air entering, it turn reduce the induce vibrations, pump efficiency and excessive bearing loads. Thus at present model studies are the only tool for developing a satisfactory design of a Test Loop, additional modification such as flow straightener, vortex suppression devices and change the position of wall. The objective of the present work is to close this gap by evolving a method to quantify the Air entering, uniform velocity and swirl angle. CFD helps to simulate the model and gives the design working feasibility and performance and accuracy. There is typical procedure involves in CFD modelling. 1. Modeling a CFD domain (CAD work). 2. Geometry clean up. 3. Meshing. 4. Preprocessing, means applying boundary conditions.
4. Solve. 5. Post processing. 6. Report.
In order to check the suitability of proposed prototype sump at site, a geometrically similar model sump with scale ratio1:8.5 was constructed in Mild steel, marine plywood and acrylic materials and run with scale model pumps to study the flow patterns in the sump. It is always difficult to predict correctly from theoretical aspects, the actual flow conditions in the prototype sump where the flow conditions are complex as maybe normally observed in many sumps. It is advisable to construct a geometrically similar sump model of suitable scale, based on Froude number & Reynolds number similarity criteria. During Sump model studies the nature of flow patterns and likely problems viz. Vortex formation, air entrainment, swirl, etc. in the prototype sump are revealed right in advance. (i.e. before the actual construction of prototype sump is completed).The suitability of the proposed prototype sump shape and dimensions is thus ascertained under various operating conditions i.e., Max. Water Level & Min. Water level with different combinations of pumps in operation, Undesirable flow conditions could be eliminated /reduced to minimum acceptable level incorporating the necessary modification in sump and their effectiveness could be ascertained by studying the flow under modified conditions.
Design criteria
The efficiency and performance of pumping stations involving multiple pumping units depends not only on the efficiency of the pumping units but also on the proper design of the pump sump. The proper design of Test Loop is not an easy task because of the various site-specific geometrical and hydraulic constraints. Hydraulic Test Loop are designed to provide Air entering, surface vortices, swirl free flow to the pump. The degree of swirl is measured in physical model tests using a swirl meter. Remove air entering when change the position of curtain wall. The present paper presents a novel method to compute the bulk swirl angle using the local velocity field obtained from computational fluid dynamics (ANSYS 2021 R2) data. The basis for the present method is the conservation of angular momentum conservation. By carrying out both numerical and experimental studies of air entering, surface vortices, flow pattern, swirl angle calculation method is validated Further the effect of vortex suppression devices (Cruciform) in reducing the swirl angle, air entering is also demonstrated.
A geometric scale, which gives greater confidence in the scaling of vortex effect & model of larger size, is desired. A scale is selected to minimize the viscous and surface tension scale effect and to reproduce the flow pattern near the intake. As per HIS (ANSI/HI 9.8 -2012) the model geometric scale is chosen so that the model bell entrance Reynolds No and Weber No are more than 60000 and 240 respectively for the test conditions based on Froude similarity & the minimum value of 100000 is recommended for Reynolds number at the pump suction. Please refer table given below for cooling water pump Keywords: Pump Sump, Air entering, Swirl Angle, computational fluid dynamics.
Flow wise largest vertical Turbine Pump having Flow of 75000 M3/Hr.
SR. No. |
PARAMETER |
PROTOTYPE PUMP |
MODEL |
1 |
Discharge |
75000 M3/Hr |
98.90 L/S V=0.568 m/s |
2 |
Suction Bell Inlet Dia. |
4000 MM |
471 MM |
3 |
Suction Bell Throat Dia. |
1917 MM |
226 MM |
4 |
Reynolds Number |
– |
331461 Re= vD/ |
5 |
Weber Number |
– |
2124 We= (*v2*D)/ |
SWIRL ANGLE CALCULATION
SWIRL METER DIAMETER (D) mm |
SUCTION PIPE DIAMETER (d) mm |
FLOW CONDITION |
MODEL FLOW LPS |
VELOCITY U M/SEC. (N*A) (A) |
VELOCITY V M/SEC. |
SWIRL RPM AT SWIRL ANGLE OF (VELOCITY VECTOR DIAGRAM tan = U / V |
||||
5° |
4° |
3° |
2° |
1° |
||||||
170 |
226 |
1.0F |
98.9 |
0.01184 |
2.46 |
18.22 |
14.56 |
10.91 |
7.27 |
3.64 |
170 |
226 |
1.5F |
148.35 |
0.01184 |
3.70 |
27.33 |
21.84 |
16.37 |
10.90 |
5.47 |
Geometry of Computational Model
The geometrical Representation in this slide explains the modelling details for CFD analysis. Geometry clean up is the process which involves all unwanted parts of the geometry vz, fillet, champers, extension to be removed. Fluid domain has to be accurate and matching with the actual scenario is something we have to take care of. In order to generate good quality mesh, domain volume should be precise and walls with good smoothness.
Courtesy: Wilo Mather Platt Pumps PVT. LTD
MESHING
Mesh is a part of pre-processing in the CFD modelling technic. In the sump model Tetrahedral meshing is done to cover all complicated regions to covered in the simulation. Orthogonal Quality of the mesh is maintained above 0.4. Boundary layer is maintained on the walls. On the wall of bell mouth 12 layer prism layer is created with 1.2 growth rate.
Courtesy: Wilo Mather Platt Pumps PVT. LTD
FLOW DOMAIN AND BOUNDARY CONDITION
Pre-processings – Realistic and Suitable Boundary conditions will be applied to the ready model in the CFX. The boundary conditions depend upon 1. Single pump capacity 2. Number of working pumps. The domain was specified as a Stationary Fluid domain with working fluid as normal water and reference pressure as 1atm. The turbulence model was selected as SST model. As boundary conditions for the steady state calculation, and isothermal process is considered. Total flow rate and null pressure-inlet condition at the inlet and at the outlet of pipe each pump operating flow rate is applied. considering the equal mass flow condition for similar pump in the suction line. Water level is kept at Defined level. As the wall conditions, free-slip condition is applied to the upper side of pump sump model passage. No-slip condition is applied to side and bottom walls and at pipe outside and inside.
Courtesy: Wilo Mather Platt Pumps PVT. LTD
ANALYSIS OF SIMULATION RESULTS
The results of the computational simulation can be analysed using number of variables. In this study it has been restricted to the comparison of results based on the pattern of streamlines of flow and the velocity profiles. The major problem revealed through the study of the streamlines of flow is the formation of a large rotating fluid mass, in the central bay with the non-working pump. The streamline pattern in the vertical plane parallel to the sump axis shows that a very large rotating mass of fluid is created in the rectangular portion along the centreline of the sump.
Courtesy: Wilo Mather Platt Pumps PVT. LTD
EXPERIMENTAL VALIDATION
WATER LEVEL IN SUMP:- 8500 (1000 MM IN MODEL) Min. Submergence required at 1F flow of VT2 Pump |
TEST RUN CONDITION:- 1.5F |
||||
DISCHARGE PER PUMP. (L/S):- |
DATE:- 04/03/2023 |
||||
VT1 :- 28.7 L/S |
VT2 :- 148.4 L/S |
||||
VT3 :-19.4 L/S |
H.S.C. :-31.7 L/S |
||||
SR NO |
Swirl RPM by Vortometer |
Remarks |
|||
For cooling water pumps |
|||||
VT1 |
VT2 |
VT3 |
VT4 |
||
R.P.M. |
R.P.M. |
R.P.M. |
R.P.M. |
||
1 |
X |
68 |
X |
X |
) Swirl angle for VT02 pump was observed more than 5 Degree.
|
The swirl angle reported in the table show that the maximum swirl angle is 68°. This is close to the maximum swirl angle limit of 5° suggested by Hydraulic Institute [3]. Vortex suppression device can be used to suppress the swirling motion in the pump suction. The vortex breaker designed based on [3] is shown in figure is used in the present work. Experiments and simulations were run with the vortex breaker placed coaxially in the pump centreline. The swirl angles obtained after implementation of the vortex breakers is summarised in below table. It can be seen from table 4 that the vortex breaker has reduced the swirl angles.
WATER LEVEL IN SUMP:-.T.O.W. 11500 (1353MM IN MODEL) |
TEST RUN CONDITION:- 1.5F |
||||
DISCHARGE PER PUMP. (L/S):- |
DATE:- 11/03/2023 |
||||
VT2 :- 148.4 L/S |
|||||
SR NO |
Swirl RPM by Vortometer |
Remarks |
|||
For cooling water pumps |
|||||
VT1 |
VT2 |
VT3 |
VT4 |
||
R.P.M. |
R.P.M. |
R.P.M. |
R.P.M. |
||
1 |
X |
6 |
X |
X |
1) The flow patterns in the fore bay & pump chambers is |
observed to be smooth and satisfactory, without any free air bubbles and vortometer RPM indicating swirl observed readings lie well within acceptable limits. 2) No air bubbles were observed in suction pipe line of HSC pump. 3) No submerged or surface vortex were observed in VT02 pump chamber |
CONCLUSIONS
The commercial CFD package ANSYS CFX-10 was used to predict the three-dimensional flow and vortices in a pump sump model. The CFD model predicts the flow pattern in detail and the location, and nature of the vortices. However, considerable post- processing of the basic data is needed to fully comprehend the details of the flow. Thus CFD model can be used to study the effect of various parameters and hence can become an important tool for optimization of pump sump geometry.
Use of linear grill type floor type splitter as proposed under pump suction bell to eliminate submerged vortex and reduce swirl rpm in VT2 pump. The design as proposed with the above modifications (proven on the model) will work satisfactorily in the prototype test facility at site.
Acknowledgement:
I would like to thanks Wilo Mather and Plat Pumps Pt. Ltd. Pune for allowing me to use ASME standards and Books from technical library.
REFERENCES
[1] Constantinescu G.S., and Patel, V.C. (1998), Numerical model for simulation of pump-intake flow and vortices, ASCE Journal of Hydraulic Engineering, Vol.124, No.2, 123-124. [2] Constantinescu1, G.S. and Patel, V.C. (2000), Role of Turbulence Model In Prediction of Pump-Bay Vortices, ASCE Journal Of Hydraulic Engineering, Vol.126, No.5, 387-390. [3] Hydraulic Institute standards 1975. Centrifugal, Rotary and Reciprocating Pumps. 13th edition, Cleveland, Ohio. [4] Joshi, S.G. and Shukla, S.N. (2000), Experimental and Computational Investigation of Flow through a Sump, Pumps & Systems Asia 2000. Nakato Tatasuaki., Weinberger Marc. and Logden Fred. (1994), A Hydraulic model study of Korea Electric Power Corporation Ulchin Nuclear Units 3 and 4 circulating-water and essential-service-water Intake structure, IIHR Technical Report No 370. [5] Nakato,T. and Darian De Jong (1999), Hydraulic Model study of water-Intake structures for Meizhou Wan Power station, The peoples Republic of China, IIHR Technical Report No 402. [6] Nakato,T., Darian De Jong and Brosow,Volker (1999), Hydraulic Model study of Red Hills generating facility circulating water pumps, IIHR Technical Report No 408. [7] Prosser, M.J 1977. The Hydraulic Design of Pump Sump and Intakes. British Hydromechanics Research Association. [8] Shukla,S.N. and Kshirsagar,J.T. ( 1999), Sump Model simulation using CD tools, International CFX Users Conference, German [9] TanweerS.DeshmukhandV.KGahotSimulationofFlow through a Pump Sump and its Validation, IJRRAS4, July, 2010.pp387-390. [10] Pravin Kumbhar, P.B.Patole., HaribhauMohite CFD ANALYSIS OF FLOW IN PUMP SUMP AND PHYSICAL VALIDATION FOR BETTER PERFORMANCE OF PUMP, IJERTV10N1SPL_132Number 1 (2017)