
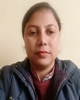
- Open Access
- Authors : Shivali , Ashish Kumar
- Paper ID : IJERTV11IS010097
- Volume & Issue : Volume 11, Issue 01 (January 2022)
- Published (First Online): 26-01-2022
- ISSN (Online) : 2278-0181
- Publisher Name : IJERT
- License:
This work is licensed under a Creative Commons Attribution 4.0 International License
Experimental Study of Non- Autoclaved Concrete Prepared by Bagasse Ash
1 Shivali, 2 Ashish Kumar
1 M.Tech [Ce], Rimt University Mandi Gobindgarh ,India
2 A.P [Ce] Rimt,India
Abstract:- The main focus of this research is on the creation of concrete utilising bagasse ash as a partial replacement for cement in non-autoclaved concrete. The building's dead load also includes a load of partition walls and ordinary mortars. Bagasse ash has a low density, which helps concrete to be lighter. With the addition of bagasse ash, compressive strength increases by 10% and split tensile strength increases by 10.5 percent. It also reduces the price of concrete by 12%. The prepared concrete has a 20% higher water absorption rate but is 5% less dense.
Keywords:- Aluminium powder, Non-autoclaved concrete, bagasse ash.
-
INTRODUCTION
The primary structural material used in Non-autoclaved concrete is used for various structure components, both auxiliary and non-basic, as well as building components. Concrete has several advantages, including its ease of installation, high compressive strength, customizable quality, and local availability. In any case, concrete has a weight limitation as well. When applied to tremor-prone regions like Indonesia, this is a significant burden. frothed concrete is an alternative structure material used to reduce the risk of building damage caused by a seismic tremor disaster. Since the beginning of the twentieth century, non- autoclaved circulated air through cement (AAC) has been mechanically delivered as a structural material. It is a cement obtained by consistently dispersed, closed air bubbles.
Because AAC has one-sixth to one-third the thickness of traditional cement and a similar proportion of compressive quality, it is useful for cladding and infills, as well as forbearing divider segments of low-to-medium-ascent structures. Furthermore, because its warm conductivity is one-sixth or less than that of solid, it can provide cost-effective structure solutions when used in low- vitality structures. The material has incredible fire rating properties, and its fire resistance lasts slightly longer than traditional cement of a similar thickness. It is not susceptible to form development, and due to its inner porosity, it has an extremely low solid transmission and is acoustically extremely powerful for a material of its weight. To control the thickness of the solid, frothed concrete is created by presenting air through the exclusive froth procedure.
The thickness of frothed solid ranges from 300 to 1800 kg/m3, which is significantly less than the thickness of ordinary cement (2400 kg/m3). Invulnerable to disappointment as a result of bacterial, creepy crawly, and fire harms. Cell concrete (also known as circulated air through cement or froth concrete) is made of concrete, lime, silica sand, and occasionally pozzolanic material, in which air-voids are entangled in the mortar lattice by methods for a reasonable frothing specialist. It is classified into three groups based on the pore development strategy: air-entraining technique (gas concrete utilising compound response in glue for gas creation), frothing technique (frothed concrete bringing air into the glue with the addition of bubble stabiliser), and combined strategy (bringing air into the glue utilising concoction response and balancing out it with gas stabilizer).
Because of the relieving temperature, cell cement can be divided into two groups: one that is restored at nearby or marginally raised temperatures, and the other includes precast brickwork items that are not autoclaved at a temperature fundamentally higher than 100 C in a pressurised and steam warmed condition. Because of intentionally entrained air and a lack of compaction, the pore framework in concrete-based material is routinely delegated gel pores, slender pores, and macropores. In comparison to gel pores, fine pores and other large pores are prone to quality decline. Examination techniques such as nitrogen gas assimilation, mercury porosimetry, optical microscopy with image handling, and X-beam registered tomography with image preparation can be used to identify the type of pores.
The pore arrangement of autoclaved circulated air through cement is classified as I fake air pores, intercluster and interparticle pores, (ii) macropores formed by mass development caused by air circulation and micropores that appear in the dividers between the macropores, and (iii) smaller scale vessels (50 nm to 50 lm) and fake air pores (>50 lm). Circulated air through cement is typically made up of lime, concrete, gypsum, and sand (or pozzolanic materials), with traces of aluminium powder added as a pore-shaping specialist. The aluminium reacts with lime, which releases hydrogen gas and forms a large number of small air pockets that are constantly conveyed in the framework [9,10]. After the set, the circulated air through cement was cut into precise dimensional units and then restored in an autoclave with a best fix pressure of 1.01.2 MPa for 58 hours.
In contrast to the traditional autoclaved circulated air through cement (AAC), non-autoclaved circulated air through cement (NAAC) has a significant amount of leeway in encouraging the assembling procedure and decreasing the cost of items. During the NAAC development, steam restoring was directed at temperatures lower than 100 C for 824 hours after being cut. As a result, when compared to AAC, the NAAC has the element of security in the item process with low vitality utilisation. AAC is manufactured and displayed as a brickwork unit in the majority of global markets. It is frequently used to replace various types
of stonework material, but because the material is solid yet , it is frequently used in a thickness that is significantly greater than for other materials.
AAC can also be used to make delicately fortified storey stature components or more intensely fortified components for floorboards, rooftop boards, divider boards, lintels, pillars, and other exceptional shapes. These components have a wide range of applications, including private, commercial, and modern development. Stronger divider boards can be used as cladding frameworks, as well as load-bearing and non-load-bearing outside and inside divider frameworks. Fortified floor and rooftop boards can be used to provide a flat stomach framework while supporting significant gravity loads. One of the key properties of AAC fabrication is the process's adaptability in terms of item attributes and item sizes. As a result, there are numerous different organisations in which the items could be manufactured.
-
METHODOLOGY
For the investigation of Non-autoclaved concrete the different extents of sand and concrete with water concrete proportion of 0.50 is taken for the contemplations. What's more, results are inferred based on compressive strength, split elasticity, water assimilation and cost per cubic meter
td>
1:4
Mix Nomenclature |
Ratio of cement and sand |
Water cement ratio |
Cement Quantity Kg/m3 |
Sand Quantity Kg/m3 |
Water Quantity Kg/m3 |
N01 |
1:1 |
0.50 |
625.000 |
625.000 |
350.97 |
N02 |
1:2 |
0.50 |
416.667 |
833.333 |
233.98 |
N03 |
1:3 |
0.50 |
311.500 |
938.500 |
175.48 |
N04 |
0.50 |
250.000 |
1000.000 |
140.39 |
|
N05 |
1:5 |
0.50 |
209.333 |
1040.667 |
116.99 |
N06 |
1:6 |
0.50 |
177.571 |
1072.429 |
100.28 |
N07 |
2:1 |
0.50 |
834.333 |
415.667 |
467.96 |
N08 |
2:3 |
0.50 |
500.000 |
750.000 |
280.78 |
N09 |
2:5 |
0.50 |
356.143 |
893.857 |
200.55 |
Subsequent to choosing the legitimate proportion, the blend was tried with the water concrete proportion of 0.40, 0.45,0.55 and
-
since light weight substantial necessities more water to respond with alumina Powder to Start the response of the air circulation measure
Mix Nomenclature
Ratio of Cement And Sand
Water – Cement Ratio
Cement Quantity Kg/m3
Sand Quantity Kg/m3
Water Quantity Kg/m3
N03W00
01:03
0.50
311.500
938.500
175.4844
N03W01
01:03
0.40
311.500
938.500
143.5781
N03W02
01:03
0.45
311.500
938.500
159.5313
N03W03
01:03
0.55
311.500
938.500
191.4375
N03W04
01:03
0.60
311.500
938.500
207.3906
For non-autoclaved circulated air through concrete, the plan blend amounts ought to be decreased to 60%, And the measurements of alumina powder is to be tried. The dose of alumina powder is .1%,.2%,.3% and .4%. alumina powder on response with water produces air which assists with creating circulated air through substantial when blended in with water. So the diverse expansion of alumina are tried.
Mix Nomenclature
Ratio of Cement And Sand
Water Cement Ratio
Cement Quantity
Sand Quantity
Water Quantity
Aluminium Dosage Quantity
Kg/m3
Kg/m3
Kg/m3
%
Kg/m3
N03
1:3
0.50
186.500
563.500
103.120
0
0
N03A01
1:3
0.50
186.500
563.500
103.120
.10%
.185
N03A02
1:3
0.50
186.500
563.500
103.120
.20%
.375
N03A03
1:3
0.50
186.500
563.500
103.120
.30%
.560
N03A04
1:3
0.50
186.500
563.500
103.120
.40%
.745
As per the experimental study the bagasse ash to be introduced in the composite mix hence it contents pozzolanic properties it will be helpful in reducing environment waste and emission of CO2 from the concrete.
Mix Nomenclature
Ratio Of Cement And Sand
Water Cement Ratio
CementQuantity
Sand Quantity
Water Quantity
Bagasse Ash Quantity
Kg/m3
Kg/m3
Kg/m3
%
Kg/m3
N03A03
1:3
0.50
186.5
563.500
103.120
00
0
N03B04
1:3
0.50
172.8
563.500
103.120
04
7.2
N03B08
1:3
0.50
158.7
563.500
103.120
08
13.8
N03B12
1:3
0.50
145.2
563.500
103.120
12
19.8
N03B16
1:3
0.50
132.3
563.500
103.120
16
25.2
N03B20
1:3
0.50
120
563.500
103.120
20
30
N03B24
1:3
0.50
106.875
563.500
103.120
24
33.75
Figure 1 Dry mix of Non-autoclaved concrete
-
RESULTS
-
Normal Proportions of Cement And Sand
Mix Nomenclature
Proportion of Cement and Sand
Compression Capacity
Split TensileCapacity
2
=
Water AbsorptionCapacity
Cost
Density
N/mm2
N/mm2
Kg/m3
In Rs
Kg/m3
N01
1:1
4.94
1.56
193.99
6062.19
1435.53
N02
1:2
4.59
1.50
214.41
4679.55
1507.00
N03
1:3
4.09
1.43
229.73
3988.33
1557.03
N04
1:4
3.64
1.34
239.94
3573.50
1602.97
N05
1:5
2.99
1.22
252.19
3297.01
1626.45
N06
1:6
2.47
1.11
268.52
3099.45
1641.77
N07
2:1
5.32
1.63
153.15
7444.83
1684.65
N08
2:3
4.60
1.52
206.24
5232.63
1480.45
N09
2:5
4.34
1.47
221.56
4284.52
1531.50
In the trial investigation of different proportions, 1:3 is observed to be exceptionally viable as far as strength, cost, thickness and water ingestion. The proportion 1:1,1:2,2:and 2:3 have higher concrete substance which has two issues , first is hotness of hydration as higher the concrete substance higher will be the fieriness of hydration .second economy higher concrete substance is anything but a financial agreeable . as the concrete substance expands the thickness of substantial increments. As the concrete substance expands the pores in the substantial fills which increment the strength of ceent yet diminishes the water ingestion.
Strength in N/mm2
Cost in rs
Cost in rs
Strength in N/mm2
Strength Chart for Proposed Aerated Concrete
Strength Chart for Proposed Aerated Concrete
6.000
5.000
4.000
3.000
2.000
1.000
0.000
6.000
5.000
4.000
3.000
2.000
1.000
0.000
N01
N02
N03
N04
N05
N06
N07
N08
N09
N01
N02
N03
N04
N05
N06
N07
N08
N09
Diffrent Light Weigth Concrete
Diffrent Light Weigth Concrete
Comppresive Strength
Split tensile Strength
Comppresive Strength
Split tensile Strength
Cost Analysis of Proposed Concrete
Cost Analysis of Proposed Concrete
8000
7000
6000
5000
4000
3000
2000
1000
0
8000
7000
6000
5000
4000
3000
2000
1000
0
N01
N02
N03
N04
N05
N06
N07
N08
N09
N01
N02
N03
N04
N05
N06
N07
N08
N09
Diffrent Light Weight Ratios
Cost in Rs
Diffrent Light Weight Ratios
Cost in Rs
-
With Different Water Ratios
Mix Nomenclature
Proportion of Cement and Sand
Compression Capacity
Split TensileCapacity
2
=
Water AbsorptionCapacity
Density
N/mm2
N/mm2
Kg/m3
N03W00
0.50
4.17
1.46
234.55
1589.73
N03W01
0.40
3.64
1.37
244.98
1587.63
N03W02
0.45
3.86
1.40
239.76
1584.51
N03W03
0.55
4.06
1.44
234.55
1597.02
N03W04
0.60
3.96
1.42
226.21
1603.28
Strength in N/mm2
Strength in N/mm2
Examination shows that at w/c proportion .50 gives ideal outcomes as far as strength. As the water content in substantial builds the water request insignificantly changes because of less development of hotness of hydration and concrete glue with additional water fills the pores in the substantial so it likewise ingest less water implies changing the water content doesn't influence the water retention of cement. in any case, the water content makes an irrelevant impact on the thickness of cement.
Strength Chart for Proposed Areated Concrete with Varing
w/c ratio
Strength Chart for Proposed Areated Concrete with Varing
w/c ratio
5
4
3
2
1
0
5
4
3
2
1
0
N03W00
N03W01
N03W02
N03W03
N03W04
N03W00
N03W01
N03W02
N03W03
N03W04
Diffrent Light Weight Ratios with varing w/c ratio
Diffrent Light Weight Ratios with varing w/c ratio
Compressive strength
Split tensile Strength
Compressive strength
Split tensile Strength
Water Absorption And Density Chart of different w/c ratio
245 1600 te
Kg/m 240 crn
245 1600 te
Kg/m 240 crn
3
3
250 1605
Water Absorbtion in
Water Absorbtion in
235
230
225
220
215
N03W00 N03W01 N03W02 N03W03 N03W04
Diffrent Light Weight Ratios with varing w/c ratio
1595
Density of Light Weigth Co
in Kg/m3
Density of Light Weigth Co
in Kg/m3
e
e
1590
1585
1580
1575
Water Absorbtion Density
-
With Different Dosage of Alumina Powder
Mix Nomenclature
Alumina powder dosage
Water cement ratio
Dry volume of material taken
Volume after B24 hrs
Increase in cost due to alumina powder
N03
0
0.50
60%
60%
0
N03A01
0.10%
0.50
60%
75%
140.25
N03A02
0.20%
0.50
60%
92%
280.5
N03A03
0.30%
0.50
60%
102%
420.75
N03A04
0.40%
0.50
60%
120%
561
alumina powder on reaction with water forms air bubbles which creates pores in the concrete so different proportions are tried to check the exact dosage of the alumna powder for the formation of light weight concrete.
With Replacement of Cement By Bagasse Ash in Proposed Aerated Concrete
Mix Nomenclature
Ratio of cement and sand
Proportion of Cement and Sand
Compression Capacity
Split Tensile Capacity
2
=
Water Absorption Capacity
cost (Excluding the cost of alumina powder which is 750 rs per kg)
Density
N/mm2
N/mm2
Kg/m3
RS
Kg/m3
N03A03
1:3
0.50
3.34
1.46
234.55
1344.75
1589.73
N03B04
1:3
0.50
3.44
1.50
239.76
1335.37
1587.63
N03B08
1:3
0.50
3.96
1.56
255.40
1303.05
1584.51
N03B12
1:3
0.50
4.27
1.60
274.16
1287.42
1597.02
N03B16
1:3
0.50
4.48
1.61
281.46
1271.78
1603.28
N03B20
1:3
0.50
3.86
1.56
302.31
1198.81
1174.15
N03B24
1:3
0.50
3.75
1.45
364.85
1094.56
1072.05
Expansion in bagasse debris content increment the strength boundaries because of its pozzolanic activities yet it additionally expands water ingestion limit of cement since bagasse debris is water
400
350
300
250
200
150
100
50
0
400
350
300
250
200
150
100
50
0
1800
1600
1400
1200
1000
800
600
400
200
0
1800
1600
1400
1200
1000
800
600
400
200
0
N03A03 N03B04 N03B08 N03B12 N03B16 N03B20 N03B24
Diffrent Light Weight Ratios with Diffrent Bagasse ash Content
N03A03 N03B04 N03B08 N03B12 N03B16 N03B20 N03B24
Diffrent Light Weight Ratios with Diffrent Bagasse ash Content
Water Absorbtion
Water bsorbtion
Density
Density
Strength in N/mm2
Strength in N/mm2
Water Absorbtion in Kg/m3
Water Absorbtion in Kg/m3
Density of Light Weigth Concrete in Kg/m3
Density of Light Weigth Concrete in Kg/m3
restricting debris and it effectively retains water. Utilization of bagasse debris can diminish the thickness of cement for example decrease in weight and utilization of bagasse debris can be result into the decrease in cost too.
Strength Chart for Proposed Aerated Concrete with
Varying Bagasse ash Content
Strength Chart for Proposed Aerated Concrete with
Varying Bagasse ash Content
5
4.5
4
3.5
3
2.5
2
1.5
1
0.5
0
5
4.5
4
3.5
3
2.5
2
1.5
1
0.5
0
N03A03
N03B04
N03B08
N03B12
N03B16
N03B20
N03B24
N03A03
N03B04
N03B08
N03B12
N03B16
N03B20
N03B24
Diffrent Light Weight Ratios with Diffrent Bagasse ash Content
Diffrent Light Weight Ratios with Diffrent Bagasse ash Content
Compressive strength
Split tensile Strength
Compressive strength
Split tensile Strength
Water Absorption And Density Chart of Dfferent Bagasse
ash content
Water Absorption And Density Chart of Dfferent Bagasse
ash content
-
-
CONCLUSION
-
-
Bagasse debris can be effectively supplanting concrete up to 20% because of its pozzolanic activity.
-
For the specific proportion bagasse debris can decrease the expense of light weight concrete up to12%.
-
Bagasse debris additionally decreases the heaviness of cement up to 6%
-
Increase in the strength because of bagasse debris can be seen up to 30%.
-
Due to utilization of bagasse debris water ingestion of substantial increments up to 18%.
5. REFERENCES
-
Apiwaranuwat, A., Kitratporn, P. and Chuangcham, K. (2013) Use of Sugarcane Bagasse Ash as Raw Material in Production of Autoclaved Concrete, Advanced Materials Research, 654, pp. 12421246. doi: 10.4028/www.scientific.net/AMR.652-654.1242.
-
Begum, R., Habib, A. and Mostafa, S. (2014) Effects of Rice Husk Ash on the Non Autoclaved Aerated Concrete Effects of Rice Husk Ash on the Non Autoclaved Aerated Concrete, International Journal of Engineering Innovation & Research, 3(1), pp. 116121.
-
Chen, Y. et al. (2017) A comprehensive study on the production of autoclaved aerated concrete: Effects of silica-lime-cement composition and autoclaving conditions, Construction and Building Materials. Elsevier Ltd, 153, pp. 622629. doi: 10.1016/j.conbuildmat.2017.07.116.
-
Chindaprasirt, P., Sujumnongtokul, P. and Posi, P. (2019) Durability and Mechanical Properties of Pavement Concrete Containing Bagasse Ash,
Materials Today: Proceedings. Elsevier Ltd., 17, pp. 16121626. doi: 10.1016/j.matpr.2019.06.191.
-
Esmaily, H. and Nuranian, H. (2012) Non-autoclaved high strength cellular concrete from alkali activated slag, Construction and Building Materials. Elsevier Ltd, 26(1), pp. 200206. doi: 10.1016/j.conbuildmat.2011.06.010.
-
Fudge, C., Fouad, F. and Klingner, R. (2019) Autoclaved aerated concrete, Developments in the Formulation and Reinforcement of Concrete. Elsevier LTD. doi: 10.1016/B978-0-08-102616-8.00015-0.
-
IS 10262:2019 (2019) Concrete Mix Proportioning Guidelines, Indian Standard, (January).
-
IS 12269:1987 (1999) Specification for 53 grade ordinary portland cement, Indian Standard, (April 1988).
-
IS 383: 2016 (2016) Coarse and fine aggregate for concrete – specification (third revision), Indian Standard, third edit(January).
-
IS 456:2000 (2000) PLAIN AND REINFORCED CONCRETE – CODE OF PRACTICE, Indian Standard, (July).
-
IS 516:1959 (1959) METHODS OF TESTS FOR STRENGTH OF CONCRETE, Indian Standard.
-
IS 5816:1999 (1999) SPLITTING TENSILE STRENGTH OF CONCRETE- METHOD OF TEST, Indian Standard.
-
Kunchariyakun, K., Asavapisit, S. and Sinyoung, S. (2018) Influence of partial sand replacement by black rice husk ash and bagasse ash on properties of autoclaved aerated concrete under different temperatures and times, Construction and Building Materials. Elsevier Ltd, 173, pp. 220227. doi: 10.1016/j.conbuildmat.2018.04.043.
-
Modani, P. O. and Vyawahare, M. R. (2013) Utilization of Bagasse Ash as a Partial Replacement of Fine Aggregate in Concrete, Procedia Engineering. Elsevier B.V., 51(NUiCONE 2012), pp. 2529. doi: 10.1016/j.proeng.2013.01.007.
-
Munir, A. (2015) Utilization of palm oil fuel ash ( POFA ) in producing foamed concrete for non-structural building material, Procedia Engineering. Elsevier B.V., 125, pp. 739746. doi: 10.1016/j.proeng.2015.11.119.
-
Patil, S. C. et al. (2017) Partially Replacement of Cement by Bagasse Ash, International Journal for Research in Applied Science & Engineering Technology, 5(5), pp. 15821587.
-
Pavithra, N. et al. (2019) A Study on Compressive Strength of Concrete with Bagasse Ash as Supplementary Cementitious Material on Various Curing Methods, International Research Journal of Engineering and Technology (IRJET), 06(06), pp. 545548.
-
Shrivastava, A. and Tiwari, P. A. (2017) Non Autoclaved Aerated Concrete ( NAAC ) Blocks: An Alternative Building Construction Material,
International Journal for Research in Applied Science & Engineering Technology (IJRASET), 5(8), pp. 808812.
-
Sood, V., Negi, S. K. and Suman, B. M. (2019) Effect of Admixtures on the Thermo Physical Properties of Non Autoclaved Light Weight Block Using Marble Dust, Key Engineering Materials, 801, pp. 365370. doi: 10.4028/www.scientific.net/KEM.801.365.
-
Sundaravadivel, D. (2018) Recent Studies of Sugarcane Bagasse Ash in Concrete and Mortar- A Review, International Journal of Engineering Research & Technology (IJERT), 7(04), pp. 306312.
-
Ulykbanov, A. et al. (2019) Performance-based model to predict thermal conductivity of non-autoclaved aerated concrete through linearization approach, Construction and Building Materials. Elsevier Ltd, 196, pp. 555563. doi: 10.1016/j.conbuildmat.2018.11.147.
-
Wang, C. et al. (2018) Utilization of oil-based drilling cuttings pyrolysis residues of shale gas for the preparation of non-autoclaved aerated concrete,
Construction and Building Materials. Elsevier Ltd, 162, pp. 359368. doi: 10.1016/j.conbuildmat.2017.11.151.
-
Xia, Y., Yan, Y. and Hu, Z. (2013) Utilization of circulating fluidized bed fly ash in preparing non-autoclaved aerated concrete production,
Construction and Building Materials. Elsevier Ltd, 47, pp. 14611467. doi: 10.1016/j.conbuildmat.2013.06.033.
-
Yang, L., Yan, Y. and Hu, Z. (2013) Utilization of phosphogypsum for the preparation of non-autoclaved aerated concrete, Construction and Building Materials. Elsevier Ltd, 44, pp. 600606. doi: 10.1016/j.conbuildmat.2013.03.070.
-