
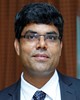
- Open Access
- Authors : Dattaji K. Shinde , Pranav Sawant
- Paper ID : IJERTV9IS110086
- Volume & Issue : Volume 09, Issue 11 (November 2020)
- Published (First Online): 19-11-2020
- ISSN (Online) : 2278-0181
- Publisher Name : IJERT
- License:
This work is licensed under a Creative Commons Attribution 4.0 International License
Experimental Study of Process Parameters Influencing Powder Coating of EN8 Steel Shaft used for Manual Squeezer off Tool using Taguchi Approach
Pranav Sawant 1, Dattaji K. Shinde 2
P.G. Student, Department of Production Engineering, Veermata Jijabai Technological Institute, Mumbai, India1 Associate Professor, Department of Production Engineering, Veermata Jijabai Technological Institute, Mumbai, India2
Abstract In the present situation of surface finishing practices, powder coating is one of the important methods as it protects the components from corrosion and at the same time improves surface appearance. Because of several parameters that are involved in process of powder coating, every time after powder coating has been done, different layer thickness of powder coating material gets deposited on the surface to be powder coated. Because of such different layer thickness deposition of powder coating material, such powder coating methods cannot ensure interchangeability during assembly of such powder coated part with its mating part. So, in case of situations demanding only particular type of fits during assembly of such parts, it becomes necessary to determine influence of individual parameters in powder coating process on the deposited layer thickness in order to design the part prior to powder coating and to eliminate rework after powder coating to get required assembly. In this research the powder coating of EN8 steel shaft was done which is one of the important sub-assembly part of Manual Squeeze off tools that are used for squeezing of HDPE pipes of gas pipeline networks. This paper highlights the effective use of Taguchis Orthogonal Array Approach for predicting the effects of individual process parameters on thickness of deposited layer in powder coating process. An orthogonal array approach and the signal to noise ratio have been used to understand the factor effects in powder coating of EN8 Steel Shaft. Experimental results are also provided to confirm the effectiveness of this approach.
Keywords:) Squeezer off Tool, Surface Coating, Metering devices, S/N ratio, Orthogonal Array.
I. INTRODUCTION
Powder coating is a finishing process in which a coating on a surface is applied electrostatically using a free-floating dry powder and then heat is used to finalize the coating. With lot of scientific research and new technological inventions, scientists have now developed the specialized devices called as Metering devices that can control the thickness of deposited layer in subsequent processes of powder coating. But such systems are very costlier and are suitable to be used only where such a high cost of powder coating is justified by a need of high precision and high performance. So, whatever the powder coating practices that are being followed for general purpose work are not equipped with such costlier Metering devices. So, in these cases, controlling the thickness
of deposited layer is quite a challenging task. Usually, the process parameters for powder coating are chosen based on fixed machine settings, available resources, and experience only. Even with the selected parameter settings, it becomes impossible to predict in advance what would be the layer thickness which is going to be added because of Powder coating.
In general, powder coating is done usually to impart corrosion resistance property and for glossy appearance. So, there is little consideration or value given to thickness of deposited layer. In most of the cases, controlling this thickness of deposited layer is not at all important where intention is to get glossy look or corrosion resistance. But when such a process is employed for parts of subassemblies, it may create problems during assembly. Required interchangeability cannot be achieved in such cases. So, the organizations that are especially doing the assemblies for their own products by using such powder coated parts may face the major problem of non-assembly because of that unpredictable extra added layer thickness. So, it becomes very essential to study process parameters in powder coating process and their individual effects on thickness of deposited layer.
Paper is organized as follows. Section II describes Powder coating methods and related work, how exactly the experimentation has been conducted in sequence is given in Section III. Section IV presents experimental results showing results of final step diameter after powder coating from which thickness of layer deposited for each of eight experiments can be easily calculated. Finally, Section V presents conclusion.
II. LITERATURE REVIEW RELATED WORK
The powder coating process was invented around 1945 by Daniel Gustin and received the US Patent for the same [1]. With this method, a coating of powdered materials is coated electrostatically and cured by heat. Powder coatings contain no solvents and do not release volatile components into atmosphere hence, there is no need to install costly pollution control equipment. Coating thickness is an important parameter as excess deposition of powder will increase material cost and low thickness will lead exposure to
atmosphere and consequently rusting or corrosion. The study of powder properties and spray guns, it was found that adhesion is maximum when nozzle is perpendicular to the part being coated. The correct stand-off distance (Distance between nozzle tip and part) for maximum powder deposition varies with particle velocity as per authors of [2]. It affects coating thickness formed. Thickness of deposited powder layer can be limited by developing analytical expressions for particle size & dielectric constant of powder and for structure and dielectric constant of substrate as per authors of [3]. The powder spray distribution is even for ultrafine powder and concave coarse powder. Coarse powder gives higher coating efficiency than ultrafine powder [4]. Taguchi method is a powerful tool that provides simple, efficient, and systematic approach to optimize process parameters. The method is valuable for qualitative and discrete parameters according to [5]. In the present work, Taguchi method has been introduced first with selection of suitable Orthogonal Array, experiments have been conducted as per Taguchis Orthogonal Array, results have been recorded and analyzed based on signal to noise ratio approach and influence of process parameters have been determined.
The work in this paper is divided in three stages. 1)Selection of Process parameters 2) Experimentation 3) Analysis. By study of actual powder coating method employed and conditions of parts used; selection of process parameters has been done. Experimentation has been done as per Taguchis Orthogonal Array. For analysis of effects of process parameters, signal to noise ratio concept has been utilized to arrive at results.
III. METHODOLOGY
Before you begin to format your paper, first write and save the content as a separate text file. Keep your text and graphic files separate until after the text has been formatted and styled. Do not use hard tabs, and limit use of hard returns to only one return at the end of a paragraph. Do not add any kind of pagination anywhere in the paper. Do not number text heads-the template will do that for you. The presented research work is based on Powder coating of EN8 Steel shaft. The work has been broadly classified into three stages:
A. selection of process parameters:
Based on powder coating method employed; following five factors were chosen with corresponding levels for study as shown in table 1.
B. Experimentation
A) Powder coating Method: Following major steps have been carried ou in powder coating process: i) Part Cleaning: Usually the parts received for powder coating are contaminated with dirt or dust particles, oil or grease. So, parts must be thoroughly cleaned before the actual powder coating process. Parts were cleaned using oil removal chemicals. After cleaning with oil removing chemical, the parts were washed with dilute HCl solution to make it clean and moisture free and after that they were cleaned with fresh hot water and were dried. ii) Phosphating and Passivation: After part cleaning, parts were subjected to phosphating and passivation using the electrical arrangement. iii)Powder spraying: This was done by Electrostatic Spray Gun. Parts were hanged freely in air using electrically conducting wires and were grounded. iv) Baking: Once the complete part coating was accomplished, part was sent to electrically operated and maintained furnace where it was kept for certain fixed duration. v) Drying: The part was dried usually in induction furnace where uniform cooling of part is done for longer duration or convection furnace where part is cooled at non-uniform rate for short duration. vi) Cleaning and touch up: After drying, part was removed from furnace and cleaned with brush. The factors that were kept constant during each experiment are as follows:
Gun air pressure: 1.68 bar, Position of Gun: Normal to surface, Powder: Epoxy thermosetting powder, Powder state: Completely dry, Conditions: Normal atmospheric conditions.
C. Part geometry
The EN8 step shafts with following dimensions have been used for powder coating. The increase in Step dia. because of powder coating on step is of primary interest in this case. Hence, purposely this dimension has not been shown in following figure but for experimentation purpose only its initial diameter before powder coating has been taken constant equal to Ø17.5 mm for all experiments.
Table 1 Selection of process parameters with corresponding levels
C. Analysis:
Fig.1 Dimensions of Step Shaft
Symbol |
Process parameters |
Levels |
|
Level 1 |
Level 2 |
||
A |
Spray voltage |
60 kV |
40 kV |
B |
Part condition |
Preheated |
Cold |
C |
Bake time |
1 hr |
2 hrs |
D |
Curing medium |
Convection Oven |
Induction Oven |
E |
Surface nature of component |
Machined (Smooth) |
Rough |
Symbol |
Process parameters |
Levels |
|
Level 1 |
Level 2 |
||
A |
Spray voltage |
60 kV |
40 kV |
B |
Part condition |
Preheated |
Cold |
C |
Bake time |
1 hr |
2 hrs |
D |
Curing medium |
Convection Oven |
Induction Oven |
E |
Surface nature of component |
Machined (Smooth) |
Rough |
In this section, the use of an orthogonal array to reduce the number of experiments for determining the optimal parameters is reported. Results of the experiments have been studied and analysed using the S/N ratio. Based on the results of the S/N ratio, effects of parameters have been predicted and also confirmed through confirmation experiments. There are three categories of performance characteristics, i.e., the
85 |
8 |
01 |
25.98 |
|||||||||
2 |
1 |
1 |
1 |
2 |
2 |
2 |
2 |
19. 08 |
19.12 |
19.1 4 |
365. 32 |
– 25.62 |
3 |
1 |
2 |
2 |
1 |
1 |
2 |
2 |
19. 4 |
19.3 |
19.2 |
372. 50 |
– 25.71 |
4 |
1 |
2 |
2 |
2 |
2 |
1 |
1 |
19. 42 |
19.36 |
19.4 2 |
376. 36 |
– 25.75 |
5 |
2 |
1 |
2 |
1 |
2 |
1 |
2 |
21. 54 |
21.87 |
21.6 9 |
470. 90 |
– 26.72 |
6 |
2 |
1 |
2 |
2 |
1 |
2 |
1 |
23. 2 |
22.9 |
22.9 |
529. 02 |
– 27.23 |
7 |
2 |
2 |
1 |
1 |
2 |
2 |
1 |
22. 78 |
22.77 |
22.5 5 |
515. 30 |
– 27.12 |
8 |
2 |
2 |
1 |
2 |
1 |
1 |
2 |
22. 3 |
22.4 |
22.5 |
501. 76 |
– 27.00 |
85 |
8 |
01 |
25.98 |
|||||||||
2 |
1 |
1 |
1 |
2 |
2 |
2 |
2 |
19. 08 |
19.12 |
19.1 4 |
365. 32 |
– 25.62 |
3 |
1 |
2 |
2 |
1 |
1 |
2 |
2 |
19. 4 |
19.3 |
19.2 |
372. 50 |
– 25.71 |
4 |
1 |
2 |
2 |
2 |
2 |
1 |
1 |
19. 42 |
19.36 |
19.4 2 |
376. 36 |
– 25.75 |
5 |
2 |
1 |
2 |
1 |
2 |
1 |
2 |
21. 54 |
21.87 |
21.6 9 |
470. 90 |
– 26.72 |
6 |
2 |
1 |
2 |
2 |
1 |
2 |
1 |
23. 2 |
22.9 |
22.9 |
529. 02 |
– 27.23 |
7 |
2 |
2 |
1 |
1 |
2 |
2 |
1 |
22. 78 |
22.77 |
22.5 5 |
515. 30 |
– 27.12 |
8 |
2 |
2 |
1 |
2 |
1 |
1 |
2 |
22. 3 |
22.4 |
22.5 |
501. 76 |
– 27.00 |
lower-the-better, the higher-the-better, and the nominal-the- better. In this research work, the intention is to have lower thickness of layer deposition. Hence, the lower-the-better performance characteristic for layer thickness has been taken. For Lower the better performance characteristic, formula to calculate S/N Ratio is:
=-10log(M.S.D.) (1) where, M.S.D. = , M = no. of tests = 8.
M.S.D. is mean square deviation.
D. Orthogonal Array for experimentation:
In this study, an L8 orthogonal array has been selected as total number of parameters under study are five and each with two levels. Each parameter is assigned to a column and total eight parameter level combinations are available. Therefore, eight experiments are required to study the entire parameter space using L8 orthogonal array. The experimental layout for five parameters using the L8 orthogonal array is shown in Table 2.
Table 4 S/N Response table of S/N Ratio
Symbols |
Factors |
Mean S/N Ratio |
|
Level 1 |
Level 2 |
||
A |
Spray Voltage |
-25.76 |
-27.02 |
B |
part condition |
-26.40 |
-26.3982 |
C |
Bake time |
-26.3852 |
-26.4056 |
D |
Curing medium |
-26.3675 |
-26.4233 |
E |
Surface nature of component |
-26.5225 |
-26.268 |
Symbols |
Factors |
Mean S/N Ratio |
|
Level 1 |
Level 2 |
||
A |
Spray Voltage |
-25.76 |
-27.02 |
B |
part condition |
-26.40 |
-26.3982 |
C |
Bake time |
-26.3852 |
-26.4056 |
D |
Curing medium |
-26.3675 |
-26.4233 |
E |
Surface nature of component |
-26.5225 |
-26.268 |
L8 (27) SERIES |
||||||||
Factors |
Output Paramete r value |
|||||||
Expt. |
A |
B |
A x B |
C |
A x C |
D |
E |
|
1 |
1 |
1 |
1 |
1 |
1 |
1 |
1 |
Y1 |
2 |
1 |
1 |
1 |
2 |
2 |
2 |
2 |
Y2 |
3 |
1 |
2 |
2 |
1 |
1 |
2 |
2 |
Y3 |
4 |
1 |
2 |
2 |
2 |
2 |
1 |
1 |
Y4 |
5 |
2 |
1 |
2 |
1 |
2 |
1 |
2 |
Y5 |
6 |
2 |
1 |
2 |
2 |
1 |
2 |
1 |
Y6 |
7 |
2 |
2 |
1 |
1 |
2 |
2 |
1 |
Y7 |
8 |
2 |
2 |
1 |
2 |
1 |
1 |
2 |
Y8 |
L8 (27) SERIES |
||||||||
Factors |
Output Paramete r value |
|||||||
Expt. |
A |
B |
A x B |
C |
A x C |
D |
E |
|
1 |
1 |
1 |
1 |
1 |
1 |
1 |
1 |
Y1 |
2 |
1 |
1 |
1 |
2 |
2 |
2 |
2 |
Y2 |
3 |
1 |
2 |
2 |
1 |
1 |
2 |
2 |
Y3 |
4 |
1 |
2 |
2 |
2 |
2 |
1 |
1 |
Y4 |
5 |
2 |
1 |
2 |
1 |
2 |
1 |
2 |
Y5 |
6 |
2 |
1 |
2 |
2 |
1 |
2 |
1 |
Y6 |
7 |
2 |
2 |
1 |
1 |
2 |
2 |
1 |
Y7 |
8 |
2 |
2 |
1 |
2 |
1 |
1 |
2 |
Y8 |
Table 2 L8 Orthogonal Array
].
IV. EXPERIMENTAL RESULTS
After the text edit has been completed, the paper is ready for the template. Duplicate the template file by using the Save As command and use the naming convention prescribed by your conference for the name of your paper. In this newly created file, highlight all the contents and import your prepared text file. You are now ready to style your paper; use the scroll down window on the left of the MS Word Formatting toolbar. Table 3 shows the experimental results and S/N ratio values for each parameter for the shaft coating analysis.
Table 3 Experimental Results (Yi) and S/N Ratio()
Even though S/N ratio values for certain factor levels seems to be closer; it is not so, as in calculation logarithmic scale has been used; they are representing relatively larger deviations. In the above Table 4, mean S/N ratio has been calculated by taking average of S/N values corresponding to corresponding factor levels. For example, to determine Mean S/N ratio for bake time at level 1, we need to take average of S/N values of experiments containing bake time parameter at level 1. So, with reference to table 3, average of S/N ratios of experiment nos.1,3,5,7 is taken because for such experiments the bake time parameter is selected at level 1.
(a)
L8 (27) SERIES |
||||||||||||
Factors |
Experiment Outcomes (avg. step dia. in mm) |
M.S .D |
S/N Ratio () |
|||||||||
E X P T S. |
A |
B |
A x B |
C |
A x C |
D |
E |
Y1 |
Y2 |
Y3 |
||
1 |
1 |
1 |
1 |
1 |
1 |
1 |
1 |
19. |
19.87 |
19.9 |
396. |
– |
(b)
(C)
Fig.3. Graph of S/N ratio Vs Factor Levels for all factors
In all the above graphs, variation points of level 1 and 2 have been simply connected using a straight line. It does not mean the variation of process parameters with levels is of linear nature. Variation may be of higher orders also, but prediction of that variation is not of interest for this study. Here, the interest is just to know whether the effect is of increasing, decreasing or of constant nature with respect to level variation. Here research is limited in finding out the most and the least influencing parameter in this powder coating process.
(d)
(e)
Fig. 2. S/N ratio variation with level for selected factors (a) Voltage (b) Part condition (c) Surface nature of part (d) Bake time (e) Curing Medium
V. CONCLUSION
This paper has presented an application of the parameter design approach of the Taguchi method in the optimization of process parameters in Powder coating. We know that, regardless of quality characteristics, a grater S/N ratio corresponds to better quality characteristic. After the analysis of the graphs and values of S/N Ratio the conclusions are as. Most influencing parameter in powder coating process is the spraying voltage. Because it shows large variation in response value if its level is changed from 1 to 2 and its S/N value is coming out highest among all the factors. As Voltage applied increases within the limits of 40-60 kV, the thickness of deposited layer also increases for the said experimental conditions and material of part. The factor part condition has no effect on outcome even if its level is changed from 1 to 2 means that the part is preheated or kept cold before powder coating will not hamper the thickness of powder deposited. Thus, not preheat the part and incur extra time and cost for preheating. Bake time and Curing Medium shows less variation when their levels are changed from 1 to 2. The parameter settings of bake time and curing medium for doing powder coating; Amount of layer deposited on smooth part is less in comparison with that of rough part if all other parameter settings remain unchanged.
Thus, this analysis we cannot predict in advance either accurately or even approximately the thickness of powder that will get deposited because of powder coating. Thus, to select the parameters and their levels that will lead to minimum possible deposition of powder layer thickness. Therefore, the of cost of rework can be saved as it is cheaper to remove relatively thin layer than thick layer from part surface.
ACKNOWLEDGMENT
We thank to S V Gas Solutions Pvt Ltd company for allowing the research activity on their gas pipeline network squeezing tool off development for the oil and gas companies. Also, thanks to Production Engineering Department of VJTI Mumbai for financial support for this project work.
REFERENCES
[1] Gustin, Daniel S, Wainio, Albert W, Electrostatic coating method and apparatus, US Patent, 1945 [2] W.Y. Li, C. Zhang, X.P. Guo, G. zang, H.L. Liao, C.J. Li, C. Coddet, Effect of stand-off distance on coating deposition characteristics in cold spraying, Materials and Design, no. 29, 297-304, 2008 [3] Jacques Cazaux, Critical thickness of electrostatic powder coatings from inside. Journal of Electrostatics, 65, 764-774, 2007. [4] Zhongyan Du, Shaoguo Wen, Jihu Wang, Changle Yin, Dayang Yu, The Review of Powder Coatings, Journal of Materials Science and Chemical Engineering, vol.4, no.4, pp 54-59, 2016 [5] A. Bendell, J. Disney, W.A. pridmore, Taguchi Methods: Applications in World industry, IFS Publications, UK, 1989 [6] M.M. Banubakode, A.C. Gangal, A.D. Shirbhate, Taguchi method for improving powder coating process- a case study, International Journal of Management, Information Technology and Engineering vol. 1, 167-180, 2013 [7] Xiangbo Meng, Influences of different powders on characteristics of charging and deposition in powder coating processes, Journal of Electrostatics, 67, 663-671, 2009