
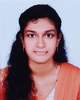
- Open Access
- Authors : Ashiya M Harshad , Salma Saif , Abhinav L R , Neetta S Kumar
- Paper ID : IJERTV11IS070249
- Volume & Issue : Volume 11, Issue 07 (July 2022)
- Published (First Online): 02-08-2022
- ISSN (Online) : 2278-0181
- Publisher Name : IJERT
- License:
This work is licensed under a Creative Commons Attribution 4.0 International License
Experimental Study on Increasing The Strength of Pervious Concrete for its use on Rural Roads
Ashiya M Harshad1, Salma Saif1, Abhinav L R1, Neetta S Kumar2
1Students, Department of Civil Engineering MES Institute of Technology & Management, Chathannoor, Kollam, Kerala, India 2Assistant professor, Department of Civil Engineering MES Institute of Technology & Management, Chathannoor, Kollam, Kerala, India
Abstract Pervious concrete is a paving material that have the ability to allow water to flow through itself to recharge ground water table and minimize storm water runoff. In rural areas costly storm water management practices are not applicable. Permeable concrete pavements is unique and effective way to meet the storm water management of rural roads. But the major problem is that the strength of permeable concrete is less as compared to conventional concrete. Hence its use is limited even though it has a lot of advantages. The objective of this report is to increase the compressive strength and flexural strength of pervious concrete by adding polypropylene fibre and manganese metal powder without compromising with its permeability so that it can be used on rural roads of India. This is done for three different water cement ratios 0.36, 0.38, 0.40 in order to find out the best water cement ratio. It was observed that the compressive strength and flexural strength of modified pervious concrete was more that of conventional pervious concrete. It was found that compressive strength and flexural strength decreases with increase in water cement ratio. Permeability increases with water cement ratio. Considering all the aspects 0.36 w/c ratio can be taken as appropriate one. This modified pervious concrete can be used for rural roads along with reinforced road mesh.
KeywordsPervious concrete, compressive strength and flexural strength, w/c ratio, polypropylene fibre and manganese powder.
-
INTRODUCTION
Pervious surfaces are made of either a permeable material that empowers storm water to course through it or nonporous blocks dispersed so that water can stream between the holes. Porous paving can incorporate a variety of surfacing methods for streets, parking areas, and walker walkways. Pervious pavement surfaces might be made out of; pervious concrete, permeable asphalt, paving stones, or interlocking pavers. Unlike impenetrable surfaces like concrete and asphalt, penetrable clearing frameworks permit storm water to permeate and penetrate through the pavement and into the total layers and additionally soil underneath. Apart from decreasing surface spillover, porous clearing frameworks can trap suspended solids, accordingly separating pollutants from storm water.
Pervious pavements are generally utilized on streets, paths and parking garages subjected to light vehicular traffic, for example, cycle-ways, administration or crisis access paths, street and air terminal shoulders, and private walkways and carports. It is a significant application for economic development and is one of many low effect advancement procedures utilized by builders to safeguard water quality. Pervious concrete is likewise an exceptional and successful means to resolve significant natural issues and to ensure
sustainable development. When it rains, pervious concrete naturally act as a drainage framework, in this manner returning water where it should be. Pervious concrete is rough finished, and has a honeycombed surface, with moderate measure of surface raveling which happens on vigorously travelled streets. Pervious concrete can be utilized in many applications, despite the fact that its essential use is in roads such as private streets, rear entryways and carports, walkways and pathways, sub-base for traditional concrete pavement and so on.
-
Advantages of permeable pavements
Permeable concrete framework has upper hand over impenetrable concrete pavements in that it is excellent in maintaining run-off from surfaces, forestall defilement in run- off water, and re-energize spring, repulsing salt water interruption, control contamination by water leakage to ground water accordingly, forestalling storm water sewer channels, assimilates less intensity than standard concrete and black-top, diminishes the requirement for cooling. By utilizing pervious concrete, the encompassing air temperature will be diminished, requiring less energy to cool the structure. Also, costly storm water designs, for example, funneling, ponds and inlets can be avoided. Construction procedure will likewise be improved as the stone re-energize bed will be introduced toward the start of development, improving erosion control measures and forestalling precipitation delays because of harsh site conditions.
-
Limitations of permeable pavements
Porous concrete isn't great for high traffic regions since it has lower load-bearing limit than ordinary pavements. Starting establishment can be somewhat more costly than conventional strategies. Maintenance necessities are unique, and may require some assessment. They can't hold heavy vehicles for extensive stretches of time, making them unsatisfactory for air terminals and highways. It is moderately low strength and requires standard maintenances.
-
Polypropylene fibre and manganese metal powder for permeable pavements
Polypropylene fibre (PP) fibre and Manganese powder (Mn) powder can be added to increase the strength of permeable pavements. The fibres limit crack propagation and positively influence several concrete parameters. PP fibre possesses high flexural strength because of its semi- crystalline nature. It has good impact strength. Manganese powder is an economic alloying component with a high hardenability. Mn powder is a steel alloy which can be used to increase strength of permeable pavements.
-
Need for study
Impermeable surfaces are increasing day by day as part of development. Thus storm water after rainfall is causing overland flow which in turn causing flooding in many areas. Permeable pavements can be one of the solutions to reduce storm water runoff. The biggest challenge restricting its use in wide scale is its low strength. In our project we try to find a solution for this by using polypropylene fibre and manganese powder to increase strength of pervious concrete so that it can be used for low volume roads in India.
-
Objectives of study
-
To prepare pervious concrete specimen.
-
To prepare pervious concrete specimen added with polypropylene fibre and manganese powder.
-
To compare the strength of conventional pervious concrete and modified pervious concrete.
-
To compare permeability of conventional pervious concrete and modified pervious concrete.
-
-
-
MATERIALS AND PROPERTIES
The crushing valve obtained for coarse aggregate was 28.04% and the impact value obtained was 20.9 %. As per IS 383-1970, the impact value and crushing value must be less that 45 %. The coarse aggregate used in the study confirms to IS 383-1970.
C. Polypropylene fibre
Polypropylene fibre was used for increasing the strength in porous concrete. Polypropylene Fibre with 12mm size was used. It was added in 0.6%. Polypropylene is a 100% synthetic fibre which is transformed from 85% propylene.
-
Cement
Ordinary Portland Cement (OPC) conforming to IS 12269-1987 was used in the study. Laboratory tests were conducted to determine the various properties like standard consistency, fineness, specific gravity, initial and final setting time. Table 2.1 shows the properties of cement ested.
Table 2.1 Properties of cement
Properties
Results
Standard Consistency
32 %
Fineness
6 %
Specific Gravity
3.09 g/cc
Initial Setting Time
35 minutes
Final Setting Time
580 minutes
-
Coarse Aggregate
Crushed rock stones got from neighbourhood quarries were utilized as coarse aggregate. The greatest size of coarse aggregate utilized was 16 mm. Laboratory tests were conducted on coarse aggregate to determine various physical properties as per IS 2386 (Prat III)-1970. Details of sieve analysis are presented in Table 2.2. The properties of coarse aggregate are given in Table 2.3.
Sieve size
Weight retained in each sieve (kg)
% Weight retained
Cumulativ e % weight
Percentage weight passing
80
0
0
0
100
40
0
0
0
100
16
2290
45.8
45.8
54.2
10
2070
41.4
87.2
12.8
4.75
510
10.2
97.4
2.6
pan
130
2.6
100
0
Table 2.2 Sieve analysis results of coarse aggregate
Fineness modulus of coarse aggregate = (Sum of cumulative
% weight retained)/100
Fig 2.1 Polypropylene Fibre
Table 2.4 Properties of polypropylene fibre
Property
Value
Specific Gravity
0.9 g/cc
Length (mm)
12
-
Manganese powder
Manganese powder was used for increasing the strength in porous concrete. It was added in 0.5%. It is a paramagnetic metal that oxidized easily in addition to being very hard and brittle.
Fig 2.2 Manganese powder
Property
Value
Specific Gravity
4.6
Table 2.5 Property of manganese powder
= 330.4/100
= 3.30
Table 2.3 Properties of coarse aggregate
-
Water
Sl.No.
Property
Value
1
Fineness modulus
3.30
2
Specific gravity
2.76
3
Bulk density (g/cc)
1.437
4
Water absorption
0.554
Water is a significant element of concrete as it effectively participates in the chemical reaction with concrete. Water used should be free from acids, oils, salts, vegetables or other organic impurities. pH of water should be between 67.
Potable water free from sulphates and chlorides were used for mixing and curing of concrete.
-
-
EXPERIMENTAL METHODOLOGY
This chapter deals with methodology, mix design and the various experimental tests adopted in the present study.
-
Methodology
-
Materials collection
-
Assessment of physical properties of materials used
-
Tests to determine the fresh and hardened properties of conventional and modified pervious concrete.
-
Tests to determine the permeability of conventional and modified pervious concrete.
-
Analysis of results.
-
-
Mix Design
The mix design here used is of M25 grade concrete. References were taken from IS 10262: 1982, IS 10262:2009 & various papers of mix design of pervious concrete. The details of mix design are given in the table 3.1, 3.2 and 3.3.
Table 3.1 Mix design of M25 grade concrete, w/c ratio 0.36
SI.No
Materials
Proportions
1
Cement (kg)
32.2
2
Coarse aggregate (kg)
64.38
3
Water (L)
11
4
Polypropylene fibre (%) Length = 12mm
0.6
5
Manganese powder
0.5
Table 3.2 Mix design of M25 grade concrete, w/c ratio 0.38
SI.No
Materials
Proportions
1
Cement (kg)
31.76
2
Coarse aggregate (kg)
63.52
3
Water (L)
12
4
Polypropylene fibre (%) Length = 12mm
0.6
5
Manganese powder
0.5
Table 3.3 Mix design of M25 grade concrete, w/c ratio 0.40
SI.No
Materials
Proportions
1
Cement (kg)
31.35
2
Coarse aggregate (kg)
62.7
3
Water (L)
12.54
4
Polypropylene fibre (%) Length = 12mm
0.6
5
Manganese powder
0.5
-
Preparation of specimen
Specimens were casted for both conventional and modified pervious concrete at three different water cement ratios. For finding out compressive strength, cubes of size 100x100x100 mm were casted and were remolded after 24 hours and were put for curing. The specimens were then tested on compressive strength testing machine at 7, 14 and 28 days. For flexural strength, beams of size 100x100x500 mm specimens were casted. The Specimens were remoulded after 24hrs and are immersed in water for curing. The specimens were then tested in universal testing machine at 28 days. For permeability, cylindrical specimens were casted on PVC pipes of 9 cm diameter. The casted specimens were remoulded after 24 hours and were tested using constant head permeability test principle.
-
Tests Conducted
Slump test was conducted on fresh concrete. Compressive strength test, flexural strength test and permeability test were conducted on hardened concrete.
-
Slump Test
Slump test is the most common test used for finding the workability of the concrete. Concrete workability can be characterized as the easiness with which it can be mixed, placed, consolidated and finished. The apparatus used consists of Abrams cone, which is a truncated cone having a base diameter of 200 mm, top diameter of 100 mm and a height of 300 mm, a base plate, measuring scale and a trowel. The procedure is that firstly the inside portion of the cone is made wet and is placed at the centre of base plate. Then the concrete is filled inside using a trowel. Concrete is filled in 4 layers. As we are dealing with pervious concrete compaction given should be less to maintain the permeability of concrete. When the concrete is fully filled the cone is vertically lifted up. If there is no deformation the slump value will be zero. The schematic diagram of slump obtained shown in fig 3.1.
Fig 3.1 Slump test
-
Compressive Strength
Compression strength test is the most common test conducted on hardened concrete because t is easy to perform. Compressive strength of concrete is a measure of its ability to resist static load, which tends to crush it. As per IS: 516- 1959, the compression test can be carried out on cube of size 100 mm x 100 mm x 100 mm using compressive testing machine. The ultimate load divided by the area gives the cube compressive strength. The setup for test is shown in Fig.3.2.
Fig 3.2 Compressive strength testing on compression testing machine
-
Flexural strength
Flexural strength is a measure of tensile strength of concrete. It is the measure of an unreinforced concrete beam to resist failure in bending. Flexural strength can be indicated as the modulus of rupture. Flexural strength test was carried out as per IS 516: 1959 in beam specimen having dimension 100 mm x 100 mm x 500 mm. The test was carried out in universal testing on a third point loading arrangement. The test setup for flexural strength test is shown in fig 3.3.
Fig 3.3 Flexural strength testing on UTM
-
Permeability test
Permeability test was done on the basis of constant head permeability principle.We used PVC pipe of 9cm diameter, 2 litre and 1 litre measuring beaker, and a funnel. We casted cylindrical specimen on PVC pipe for 3 different water cement ratio for both conventional and modified pervious concrete. After 24 hours we took the specimen for testing. The test procedure consist of first take 2 litre beaker and put funnel on top of it. Then place the sealed specimen in funnel and pour 1 litre of water for pre wetting the specimen. Pour the water out of the 2 litre beaker after pre wetting. Then pour 2 litre of water by maintaining the head 15 25 mm. Start watch when water touches the specimen and stop it when there is no water Weigh the water collected in 2 litre jar. Use the formula
K = W / (A×T) to find coefficient of permeability.
Where k = Coefficient of permeability
W = Weight of water collected in jar A = Area of specimen
T = time for which water is left at top
Fig 3.4 Permeability test apparatus setup
-
-
RESULTS AND DISCUSSIONS
-
Slump Test
In pervious concrete fine aggregate is absent. Hence it is highly workable. Pervious concrete have zero slump. Thus it can also be called as zero slump concrete. The result of slump test is given in Table 4.1.
Table 4.1 Slump test results
Sample
Slump (mm)
Normal pervious concrete with w/c ratio 0.36
00
PP fibre and Mn powder added pervious concrete with w/c ratio 0.36
00
Normal pervious concrete with w/c ratio 0.38
00
PP fibre and Mn powder added pervious concrete with w/c ratio 0.38
00
Normal pervious concrete with w/c ratio 0.40
00
PP fibre and Mn powder added pervious concrete with w/c ratio 0.40
00
-
Compressive Strength Test
The compressive strength of 7, 14 and 28 days conventional and modified ( PP fibre and Mn powder added) pervious concrete were found out for three different water cement ratios of 0.36, 0.38 and 0.40 and the results are given in tables 4.2, 4.3 and 4.4 respectively. It was observed that compressive strength decreases with w/c ratio. 0.36 w/c ratio has highest compressive strength for both conventional and modified pervious concrete.
Table 4.2 Compressive strength test results of normal and modified pervious concrete with w/c ratio 0.36
Batch
7 days (N/mm2)
14 days (N/mm2)
28 days (N/mm2)
Normal pervious concrete
5
8
13
PP fibre and Mn powder added pervious concrete
7
12
16
Fig4.1 Comparison of 7, 14 and 28 days compressive strength of conventional and modified pervious concrete with w/c ratio 0.36
Table 4.3 Compressive strength test results of normal and modified pervious concrete with w/c ratio 0.38
Table 4.5 Flexural strength of pervious concrete specimens at 28 days
Batch
7 days (N/mm2)
14 days (N/mm2)
28 days (N/mm2)
Normal pervious concrete
5
7
11
PP fibre and Mn powder added pervious concrete
5
8
12
Fig4.2 Comparison of 7, 14 and 28 days compressive strength of conventional and modified pervious concrete with w/c ratio 0.38
Table 4.4 Compressive strength test results of normal and modified pervious concrete with w/c ratio 0.40
Batch
7 days (N/mm2)
14 days (N/mm2)
28 days (N/mm2)
Normal pervious concrete
6
7
10
PP fibre and Mn powder added pervious concrete
5
9
8
Fig4.3 Comparison of 7, 14 and 28 days compressive strength of conventional and modified pervious concrete with w/c ratio 0.40
-
Flexural Strength Test
The flexural strength was found out at 28th day for normal and modified pervious concrete. This was done for three water cement ratios of 0.36, 0.38 and 0.40. The result is given in table 4.5. It was observed that flexural strength decreases with increase in w/c ratio. It was higher for w/c ratio 0.36 for both normal and modified pervious concrete.
Sample
28 days (N/mm2)
Normal pervious concrete with w/c ratio 0.36
2.4
PP fibre and Mn powder added pervious concrete with w/c ratio 0.36
2.5
Normal pervious concrete with w/c ratio 0.38
2.24
PP fibre and Mn powder added pervious concrete with w/c ratio 0.38
2.38
Normal pervious concrete with w/c ratio 0.40
2.08
PP fibre and Mn powder added pervious concrete with w/c ratio 0.40
2.16
Fig 4.4 Comparison of flexural strength of normal and modified pervious concrete at 28 days
Fig 4.5 Flexural strength variation of normal pervious concrete with different w/c ratios
Fig 4.6 Flexural strength variation of modified pervious concrete with different w/c ratios
Fig 4.8 Permeability variation of normal pervious concrete with w/c ratios
-
Permeability Test
Permeability test was conducted on conventional and modified porous concrete of 0.36, 0.38 and 0.40 w/c ratios. The results are summarized in below table. Permeability test was done on the principle of constant head permeability test. It was observed that permeability was more for conventional pervious concrete than modified pervious concrete. Also permeability was found to be increasing with water cement ratio. From analysis permeability Vs w/c ratio graphs we can conclude that permeability increases with w/c ratio.
Sample
Coefficient of permeability,k (cm/s)
Normal pervious concrete with w/c ratio 0.36
1.16
PP fibre and Mn powder added pervious concrete with w/c ratio 0.36
0.79
Normal pervious concrete with w/c ratio 0.38
1.26
PP fibre and Mn powder added pervious concrete with w/c ratio 0.38
0.89
Normal pervious concrete with w/c ratio 0.40
1.40
<>PP fibre and Mn powder added pervious concrete with w/c ratio 0.40 1.07
Table 4.6 Coefficient of permeability values of different concrete specimens
Fig 4.7 Coefficient of permeability for different concrete specimens
Fig 4.9 Permeability variation of modified pervious concrete with w/c ratios
-
Evaluation of PP fibre and Mn powder added pervious concrete pavement for low volume roads in India
IRC SP:62-2004 deals with design of concrete pavements for low volume roads with average daily traffic less than 450 commercial vehicles per day. For pavement construction of rural roads, it is recommended that the characteristic 28 day compressive strength should be at least 30Mpa and corresponding flexural strength ( third point loading ) shall not be less than 3.8 MPa. Also permeability of conventional pavements is very low. This is for M 30 grade. From our study we have obtained 28 days compressive and flexural strength of PP fibre and Mn powder added Pervious concrete of M25 grade concrete with w/c ratio 0.36 as 16MPa and 2.5MPa. Also permeability of this modified concrete is
-
cm/s which is considerably good. But the strength is less than the desired strength. But by using reinforced road mesh the strength of pervious concrete can be further increased and can be used for rural roads.
-
-
CONCLUSION
In our study we investigated the use of polypropylene fibre and manganese powder in pervious concrete and found out its compressive strength, flexural strength and permeability. We also made a study on using this modified pervious concrete for low volume roads. The result obtained from investigation can be concluded as follows:
-
The use of polypropylene fibre and manganese powder in pervious concrete enhance the bonding between the coarse aggregate and cement paste.
-
The content of polypropylene fibre and manganese powder in pervious concrete decreases workability of concrete.
-
The compressive strength and flexural strength of modified pervious concrete was more than that of conventional pervious concrete.
-
It was observed that there was decrease in compressive strength with increase in water cement ratio.
-
It was observed that there was decrease in flexural strength with increase in w/c ratio.
-
Permeability was found to be increased with increase in water cement ratio.
-
Permeability was less for fibre added pervious concrete than conventional concrete.
-
The w/c ratio 0.36 can be taken as appropriate since it gave a good compressive strength, flexural strength and permeability.
-
Polypropylene fibre and manganese powder added pervious concrete cannot be used alone for rural roads. It can be used by providing additional reinforced road mesh.
-
Scope for further study
-
Same kind of studies can be done for using pervious concrete for high volume roads.
-
Studies can be done to reduce clogging of pervious concrete pavements.
-
Detailed studies of using reinforced road meshes for pervious concrete can be made.
-
Cost effective techniques for employing pervious concrete pavement can be done.
-
REFERENCES
[1] Ankit N Pansuriya & Praful A Shankar ( 2016 ) Use of polypropylene fibre in rigid pavement International Journal of advanced engineering and research development. [2] Bimal Kumar, Sanjeev Sinha, Hilol Chakravarthy ( 2019 ) Study on effect of Nano silica on Strength and Durability characteristics of High Volume Fly Ash Concrete for pavement construction Civil Engineering Journal. [3] Deepkumar K Ashish, S M ASCE and Sunderk Verma (2018) Effect on permeability of concrete made with successive recycled aggregate and silica fumes American Society of Civil Engineers. [4] Felipe Dias Coasla and Brunno Gouveia (2020) Characterization of silicon manganese iron slag for employment in base and sub-base layers for highways International Journal of Advanced Engineering Research and Science. [5] Mariana Marchioni and Gianfranco Becciu ( 2015 ) Expermental results on permeable pavement in urban areas International Journal of Sustainable Development and Planning. [6] Masoud Kayhanian, John T Harvey and Xiao Hiang ( 2019) Application of permeable pavement in highways for stormwater runoff amangement and pollution prevention: California research experience International Journal of Transportation Science and Technology. [7] Pankaj Joon (2017) Permeable pavement system International Journal for Engineering Science and management. [8] P Navyasri and DR, V Srinivasa Rao ( 2016 ) Rainwater harvestment by using pervious permeable system International Journal of Innovative Research in Science Engineering and Technology. [9] Pradip Shanker Shinde and Shrikant Shubash Ingale ( 2017) Experimental Evaluation of Compressive and Flexural Strength of Pervious Concrete by using Polypropylene Fiber International Journals of Engineering Research and Technology. [10] Saurabh y kali, Amit P Halweli, karthik K Rathode and Mayur A Jinapuri (2017) Permeable pavement A step towards sustainable urban drainage system International Advanced Research Journal in Science Engineering and Technology. [11] Singh Hirendra Pratap, Sakale Rakesh, Sharma Kapil, Kushwah Satish Kumar (2016) Enhancement of strength of pervious concrete with different water cement ratio and admixtures International Journal of Engineering Research & Technology.