
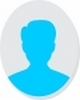
- Open Access
- Authors : Iberahin Jusoh
- Paper ID : IJERTV10IS080240
- Volume & Issue : Volume 10, Issue 08 (August 2021)
- Published (First Online): 14-09-2021
- ISSN (Online) : 2278-0181
- Publisher Name : IJERT
- License:
This work is licensed under a Creative Commons Attribution 4.0 International License
External Loading on the Leg of Jack-up Structure
Iberahin Jusoh
Mechanical Engineering Department, College of Engineering and Islamic Architecture Umm Al-Qura Univerrsity.
Makkah, Kingdom of Saudi Arabia
Abstract The jack-up rig is a unique type of offshore structure where it can self-elevating its main hull clear from the sea-water surface during its operation. This is possible by lowering down its legs reaching the seabed thus supporting the hull clear. In this condition, the legs are susceptible to external load from the environment, mainly wave and current. This paper focuses on external loading induced by wave and current interaction with the legs of the rig. The jack-up structure was first modeled using finite element software and later utilized for wave-structure interaction. The results are presented in tabulated form as well as plotted in graphical form. It is found that the maximum magnitude of the horizontal hydrodynamic load is 29.1 kN experienced by the element at level 20 (at 3.4 m below Mean Water Level, (MWL)) of the aft leg, and associated base shear and overturning moment (OTM) are 2.623 MN and 9.942 MNm respectively. The structure is operating in the safe stress region since the stress utilization is found to be 0.45.
Keywords Structural design, wave loading, Morison equation, jack-up rig, leg structure.
-
INTRODUCTION
There are several types of structures usually employed in the offshore oil and gas industry. One of the most important structures used at the early stage of oil recovery is a jack-up structure. This mobile structure is usually used for exploration and operation of offshore oil and gas fields, as well as for servicing offshore structures. The main feature of a typical jack-up structure is a self-floating body with three or four retractable legs at its corners to support the body during the operation. During its service life, the jack-up structure experience several types of loading mainly from the environment. This paper is focused on the environmental loading encountered by the structure, particularly loading on its legs. It discusses the basic modeling of the legs, loading parameters, and subsequent results derived from the analysis.
-
BACKGROUND
The jack-up structure is a simple floating and mobile unit that is usually employed at an early stage of offshore oil and gas exploration and production. Due to its operational limitation and the challenges in environmental loading as well as its technical capacity, the jack-up structure become suitable to be used in the region of shallow and medium water depth. The technical problems associated with their safety and economic operation become very significant as the waters become more hostile as the depth increased [1]. A special feature of this type of structure is that the legs are lowered to stand on the seafloor then the hull is elevated clear from the sea surface. Operations of the structure will take place in this condition at a water depth of up to about 100 m. Jack-ups spend part of their life as floating structures. This is when such units are towed to a new location using
oceangoing tugs. In this mode, the legs are lifted and extend upwards over the platform [2]. Some typical size jack-ups can have legs of more than 130 m long, accommodate more than
100 personnel, with the capability to drill to subsurface depths of up to 9,144 m. [3]. One of the biggest jack-up structures known as the CJ80 rig was designed for deep drilling. It is capable to operate at a maximum water depth of 175 m with a 25 m air gap [4]. The jack-up legs are usually an assembly of lattice tubular members. This is normally adopted for the leg structure in deep waters for reducing wave forces and current forces on the structure to a minimum, whereas a pure cylindrical pile structure may be considered for areas with comparatively shallow water depth [5].
-
STRUCTURAL MODELLING AND LOADING FORMULATION
The jack-up structure considered in this study is an independent 3-leg self-elevating jack-up. The main dimensions are adopted from an earlier study by Frieze [6]. The legs are modeled using finite element software to represent it with lattice legs elements selected as shown in Fig.1. The rig dimensions are given in Table 1. The rigs layout is presented in Fig. 2.
TABLE 1: Jack-up rigs dimensions.
Features
Dimension
Hull length
74.1 m
Hull width
62.8 m
Hull depth
7.9 m
Forward-aft leg spacing
39. m
Port-starboard leg spacing
43.3 m
Leg length
104.632 m
The retractable jack-up legs are assembled from tubular members as shown in Fig. 3 using similar dimensions as appeared in a previous study [6]. The outer tubular has a diameter of 324 mm and wall thickness of 19.1 mm while the inner bracing has a diameter of 224 mm and wall thickness of
9.5 mm. The total length of each leg is 104.632 m. Fig. 4 shows reference nodal numbers that were assigned as referring to the tabulated results presented in Tables 3 and 4.
The structure is analyzed for the loading conditions at a water depth of 70 m. The wave height is adopted in the investigation is 13 m and associated parameters presented in Table 2. The outcome of the study is the response of the jack- up legs to the external loading from the environment, i.e., wave and current.
Fig.1. Three legs jack-up structural model.
Fig. 2. Jack-up rig layout [6]
Fig.3. Horizontal leg bracing layout [6]
Fig. 4. Assigned reference numbers and levels
TABLE 2. The wave parameters
Wave Parameters
Water Depth, h (m)
70
Wave Height, H (m)
13
Wave Length, (m)
229.04
Wavenumber, k (m-1)
0.0274
Frequency, (rad)
0.4473
Period, T (sec)
14.05
The Airy wave theory was adopted and wave loads on submerged section of the jack-up legs are estimated using Morison equation [7], [8].
(1)
Water particles velocities in x-direction, u and z-direction, v
at any point of time, t is given as:
(2)
(3)
The associated acceleration of water particles, and, at any point of time, t is defined as:
(4)
(5)
Sea driven current velocity that accompanied the wave particle motion is estimated using the following relationship;
(6)
where is current velocity at mean sea level, z is distance from the surface and d is water depth.
Hydrodynamic coefficients adopted in the study is as referred to Det-norske-Varitas recommendation, where drag
coefficient, CD, for clean and rough surfaces are 1.0 and 1.5 respectively, while the inertia coefficient, CM, is 1.8 for both clean and rough surfaces [9].
-
RESULTS AND DISCUSSION
Results from this study are presented in Tables 3 and 4. Table 3 shows the load distribution due to wave and current effects during interaction with the fore leg of the structure while Table 4 gives the load distribution due to wave and current interaction with the aft legs. The presentation of load distribution is referred to points of reference as shown in Figure 4 for each level from 1 to 21. The level has repesented the location on the submerged jack-ups legs which is 3.4 m vertically apart with level 1 is on the seabed and level 21 is at the mean sea level. The plots of the resulting force on each node of the jack-up leg below water level are shown in Fig. 5 to Fig. 8.
Fig. 5 shows the magnitude of horizontal forces on the front leg while Fig. 7 shows the horizontal forces on aft legs. Each Level has a vertical distance of 3.4 m with an exception of the lowest bay where it is the spud-can, the vertical length is 6.032 m. For each point at submerged art of the leg, it would have received a direct load from the wave and current plus transferred load from adjacent members, below and above it. However, for elements at level 21, its nodes would receive direct load plus transfer load from the lower positioned elements but not from the higher-level elements, since elements above level 21 do not interact with wave and current. That is why there is a sudden reduction in load at level 21. A similar trend also happens to vertical forces in the y-direction as shown in Fig. 6 and Fig. 8.
TABLE 3. Load distribution on the Fore Leg (in N)
TABLE 4. Load distribution on the Aft Legs (in N)
Tabulated results are then presented in graphical form as shown in Fig. 5 to Fig. 8, showing the distribution of hydrodynamic loads due to wave and current on the jack-up legs. Fig. 5 shows the horizontal load on the fore leg increases with the increment of water level from the seabed. Maximum load in the x-direction with a magnitude of 27.7 kN occurred on the front leg at level 20 (i.e. at 3.4 m below mean water level). The graph shows a steep dip to a magnitude of 12.6 kN x-direction load due to the water kinematic circulation at reference points as well as no contribution of transferred load from the above elevation. Load distribution in vertical y-direction on the fore leg is plotted in Fig. 6. The loading magnitude as expected is low with a maximum value of about 4 kN at level 20 (at MWL) which could significantly affect the maximum load on the jack-ups leg.
Fig. 5. Horizontal load in x-direction of the fore leg.
Fig. 6. Vertical load in the y-direction of the fore leg.
Fig. 7 and Fig. 8 show the variation of hydrodynamic loading on the aft legs of the structure. The magnitude of loads increases steadily from lower near the seabed to the maximum near the MWL. This trend is due to the speed of water particle circulation in relation to wave motion. The maximum value of hydrodynamic load acting on the aft jack- up leg is found to be 29.1 kN at level 20 (at 3.4 below MWL), which is slightly higher than the load on the fore leg. Its lowest magnitude is found to be about 8 kN at level 1 (seabed). The higher loading magnitude on the aft leg is attributed to the orientation of the aft legs that are diagonal to the direction of wave incident as compared to parallel orientation for the fore leg (refer to Figure 2). A similar trend to the fore leg for the y-direction loads, the maximum magnitude is 4.3 kN at MWL, while the minimum value is zero on the seabed. The trend of lower vertical load magnitude was anticipated because the vertical water particles motion is smaller compared to horizontal motion.
Fig. 7. Horizontal load in x-direction on the aft Leg
Fig. 8. Vertical load in the y-direction of the aft leg.
Overall loading on the jack-up leg at a wave height of 13 m is presented by the magnitude of base shear and overturning moment (OTM) acting along the whole length of the leg. Table 5 shows the magnitude of these loadings. The loading magnitude on the aft legs is slightly higher than the magnitude on the fore leg due to its diagonal orientation facing the incoming wave and current.
TABLE 5. Base Shear and OTM at H = 13m
Fore Leg
Aft Legs, 1 & 2
Base Shear
2.588 MN
2.623 MN
Overturning Moment
9.809 MNm
9.942 MNm
-
CONCLUSOINS
The outcome of the study observed in this paper where the effects of wave loading on typical jack-up structure legs may be summarized as the following;
-
Load analysis of wave interaction with lattice type jack- up legs for a jack-up structure operates at 70 m water depth. Related wave heights considered in the study are 13 m.
-
Maximum loads due to wave and current interaction with jack-up legs are 27.7 kN for the fore leg and 29.1 kN for the aft legs.
-
The highest magnitude of base shear and overturning moment are 2.623 MN and 9.942 MNm on the aft legs.
-
The jack-up leg structure is within the safety limit as the stress utilization factor is found to be 0.45.
REFERENCES
-
Boswell, L.F., DMello, C.A. and Edwards, A.J. (1987). Mobile Offshore Structures. Elsevier, London. 1987
-
WARTSILA: Encyclopedia of Marine Technology, 2021, https://www.wartsila.com/encyclopedia/term/mobile-offshore- drilling-unit-(modus); July 2021.
-
Offshore, 2013; Aramco state-of-the-art jackup drilling rig.
Offshore, Issue Jan 2013.
-
Offshore Technology, 2014; Green machine inside the worlds biggest jack-up drill rig. Offshore Technology March 2014.
-
Ohta, T., Yamauchi H., and Toriumi, M., (1991), Design Method of Leg Structure of Jack-up Rig, The First International Offshore and Polar Engineering Conference (ISOPE), Edinburgh, UK., August 1991.
-
Frieze, T. (2001). SNAME 5-5B WSD 0: Comparison with SNAME 5-5A LRFD and the SNAME 5-5A North Sea Annex. OTR 2001/001; Health and Safety Executive, U.K. 2001.
-
Chakrabarty, S.K. (ed.), 2005; Handbook of Offshore Engineering, San Francisco, Elsevier, 2005.
-
Jusoh, I., 2018; Base shear and overturning moment on jacket structure with marine growth, Intl Jour of Engineering Trend and Technology (IJETT), Vol. 58. Issue 1, April 2018.
-
Det Norske Veritas (2001), Structural design of self-elevating units (LRFD method). Det Norske Veritas, Norway.
-