
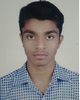
- Open Access
- Authors : Jitesh Singh Rajput , Bhavya Besre , Manish Sahu , Manish R. K. Sahu
- Paper ID : IJERTV11IS010126
- Volume & Issue : Volume 11, Issue 01 (January 2022)
- Published (First Online): 29-01-2022
- ISSN (Online) : 2278-0181
- Publisher Name : IJERT
- License:
This work is licensed under a Creative Commons Attribution 4.0 International License
Fabrication of All-Terrain Vehicle
Jitesh Singh Rajput, Bhavya Besre, Manish Sahu
Department of Mechanical Engineering
Shri Shankaracharya Institute of Professional Management and Technology, Raipur, Chhattisgarh, India
Mr. Manish R. K. Sahu
Department of Mechanical Engineering
Shri Shankaracharya Institute of Professional Management and Technology, Raipur, Chhattisgarh, India
Abstract- The objective of our project is to fabricate an All-Terrain Vehicle. The main purpose is to fabricate a single sitter high- performance and safe vehicle that will take the ruggedness of rough roads with maximum safety and driver comfort. This paper provides an in-detail description of the fabrication of an ATV vehicle. Components used in fabrication are chosen according to their availability and reliability. This report aims to fabricate an ALL-TERRAIN vehicle (ATV) by the SAE BAJA 2021 rulebook.
Keywords Roll cage, Steering system, Suspension system, wheel assembly, and transmission.
-
INTRODUCTION
An All-Terrain Vehicle (ATV) is specially fabricated for off-road driving. ATV is fabricated for very rough terrain, jumps, maneuverability, and endurance. The single sitter, an off-road vehicle is designed and fabricated in several engineering and reversed engineering processes. Usually, ATVs were solely used for transportation through inaccessible areas, but now these vehicles have found their application in different areas, for example In Defence services like the army and air force, etc. to carry and transport guns, ammunition, and other supplies to remote areas of rough and varied terrain.
-
LITERATURE REVIEW
In FABRICATION OF THE BUGGY CAR, D. Rahul Raj, Padma Mahesh Kumar, Sarala Bharath, N. Goutham, N. Nikhitha,
-
Abhilash stated their purpose is to fabricate a buggy car and said that buggy depends on the chassis. A detailed fabrication of components was carried out by them like Roll cage, Suspensions, wheel assembly, transmission & Braking mechanism. In this report, the bending of the pipes is performed at CNC machines and also stated that we can reduce the weight of a vehicle by considering fewer weight materials. It may increase more cost of the vehicle.
In Stress Analysis of Roll Cage for an All-Terrain Vehicle Denish S. Mevawala, Mahesh P. Sharma, Devendra A. Patel, Darshan A. Kapadia studied the design of roll cage for an ATV and Various loading tests like Front Impact, Side Impact, and rear impact have been conducted. The modeling and stress analysis is done by ANSYS software. We have focused on every point of the roll cage to improve the performance of the vehicle without the failure of the roll cage. successfully analyzed the roll cage structure for its strength against the collision from the front, rear, as well as side. A factor of safety is under the safe limit. The roll cage is sustained 4G force from the front as well as the rear & 2G force from the side. Hence, deformation & stresses are under the limit.
In Design Analysis and Fabrication of M-BAJA ATV 2020 Sandeep Chaudhary, Ganesh Kumar Kantak, Priyanka Sharma, Harshita Mathur stated their report gives a brief process to finalize the design of ATV. This report mentions specifications of roll cage, suspension system, steering system, braking system, and transmission system. They tried to obtain the best output of manufacturing, cost, weight, and overall aesthetics and performance by meeting the guidelines and rules by SAE. This report is created keeping in mind the drivers safety, cost-effectiveness, and durability of the vehicle. The team has selected material as their priority to reduce the vehicles overall weight, cost and to maintain the strength of every component. Before the actual fabrication of the vehicle, engineering design and their application is used to design and simulate the vehicle with real-time condition on software like Solidworks, lotus shark, etc.
In FABRICATION OF ALL-TERRAIN VEHICLE BY USING CONTINUOUSLY VARIABLE TRANSMISSION
SYSTEM Kesarinath N. S, Pradeep. M, Senthamilarasu. S, Vijayaprapakar. L. stated that the design and analysis of an ATV is fun to drive, versatile, safe, durable, and high-performance off-road vehicle. This report tried to design an all-terrain vehicle that meets international standards and is also cost-effective at the same time and focused on every single system to improve the performance of each component. The objective of designing a single-passenger off-road race vehicle with high safety and low production costs seems to be accomplished. The design process included using Solid Works, CATIA, and ANSYS software packages to model, simulate and assist in the analysis of the completed vehicle.
-
-
FABRICATION
In fabrication, all the parts have been assembled.
-
ROLL CAGE
The roll cage has been designed by considering BAJA SAE 2021 RULEBOOK. The purpose of the roll cage is to maintain a minimum space surrounding the driver. For the fabrication of the frame, we used lightweight and safe frame steel. For frame making, we considered the material of AISI1018 & AISI4130.
Properties
AISI 1018
AISI 4130
Density
7.87 g/cm3
7.85 g/cm3
Yield Strength
417 MPa
638 MPa
Tensile Strength
440 MPa
560 MPa
Ultimate Strength
473 MPa
810 MPa
Bending Strength
402.9 MPa
415 MPa
Preferred Welding Type
MIG
TIG
Availability
Easily Available
Not easily available
Cost
Cheap
Expensive
Table: Specifications of the material
According to the data shown above, AISI 4130 has a substantially higher strength-to-weight ratio. In addition, by adopting AISI 4130, we may achieve a straight weight reduction of 17% per tube length without sacrificing strength. The following table shows the chemical composition of AISI 4130:
Element
Content (%)
Iron, Fe
97.03-98.22
Chromium, Cr
0.80-1.10
Manganese, Mn
0.40-0.60
Carbon, C
0.280-0.330
Silicon, Si
0.15-0.30
Molybdenum, Mo
0.15-0.25
Sulfur, S
0.040
Phosphorus, P
0.035
Table: Chemical composition of AISI 4130
The chemical composition of AISI 1018 carbon steel is outlined in the following table.
Element
Content (%)
Manganese, Mn
0.60-0.90
Carbon, C
0.15-0.20
Sulfur, S
0.05 (max)
Phosphorus, P
0.04 (max)
Iron, Fe
Balance
Table: Chemical composition of AISI 1018
For our design, we have selected a rod of exterior diameter of 25.4 mm (1 inch) and a wall thickness of 3 mm (0.120 in) Primary member
DLC SIM lateral cross member FBM Front Bracing meber ALC Aft lateral cross member CLC Upper lateral cross member FLC Front lateral cross member
BLC Overhead lateral cross member RHO Roll hoop overhead members LFS Lower frame side members RRH Real roll hoop
Figure (1) primary member of the roll cage
Secondary members
LDB Lateral Diagonal Bracing SIM Side Impact Members
FAB Fore/Aft Bracing Members USM Under Seat Member
RLC Rear Lateral Cross Member
Figure (2) secondary members of the roll cage
Welding electrode E 7018
The "E" in the E7018 electrode indicates a tool used for an arc-welding process. The 70 means it makes welds that are very strong (70,000 psi). The 18 means two things: The "1" means the electrode can be used in any position, and the "18" means low hydrogen and usually DC.
-
STEERING
This vehicle is fabricated keeping in mind that it will go through sharp turns and bumpy roads, so the systems stability and the time of response are vital factors in deciding the vehicles run. We prefer rack and pinion because its a simple system, simple construction, immediate response. It is the interface between the driver and the vehicle so it plays an important role for the vehicle. The driver turns the steering wheel which will rotate the steering column and give further movement in the steering rack. The motion is then transmitted to the wheels by the tie rods. The steering system will depend on the inner and outer angles of the vehicle, the factors like kingpin inclinations, the center of gravity, and scrub radius.
-
SUSPENSION SYSTEM
An ATV is supposed to have a reliable & efficient suspension system because of the unpredictable nature of off-road conditions like it will go through sharp turns and bumpy roads. suspensions were chosen based on their degree of freedom, roll-center adjustability, ease in wheel alignment parameters, etc. We used MONO SHOCK SUSPENSION SYSTEM.
-
ENGINE
-
BRAKING
ENGINE TYPE:
4 STROKE, SOHC 2-VALVE, AIR-COOLED, COMPLAINT DTS-i Fi ENGINE
EMISSION TYPE: 178.6 CC MAX POWER:
17.02 PS @85OO RPM MAX TORQUE:
14.52 NM 6500 RPM FUEL: PETROL
For safety purposes, an excellent braking system is the most important. It must be capable of locking all four wheels on a dry surface. The braking system is chosen based on ease of manufacturability, performance, and simplicity. We used a disc brake. In a disc brake, the fluid from the master cylinder is forced into a caliper where it presses against a piston. The piston, in turn, squeezes two brake pads against the disc (rotor), which is attached to the wheel, forcing it to slow down or stop.
Figure (3) disc brake
-
Brake pads: metal plates bonded with material that provides stopping friction.
-
One or two pistons push the brake pads against the rotor when you brake.
-
A bleeder screw to allow for servicing the brakes and replacing the fluid.
-
A rubber piston seal that prevents brake fluid leakage and retracts the piston when the brakes are released.
-
A dust boot to keep contaminants out of the cylinder.
-
Anti-rattle clips that keep the brake pads stable.
-
-
TRANSMISSION
The transmission system is one of the most important systems in every automobile because it has a significant impact on their efficiency. The transmission allows the variation of torque between the engine and gearbox.
-
WHEEL ASSEMBLY
Components of wheel assembly are spindle, knuckle, hub, wheels, and tires. The selection of tires is based on the traction required for the vehicle.
-
-
CONCLUSION
The design, development and fabrication of the roll cage is carried out successfully. The roll cage is used to build an ATV by integrating all the other automotive systems like transmission, suspension, steering, brakes and other miscellaneous elements.
Results from these tests are shown in the table:
Type of impacts |
Loading Force (N) |
Maximum Deformation (mm) |
Rear |
18000 |
6.232 |
Front |
18000 |
0.83 |
Rollover |
15000 |
7.452 |
Torsion |
15000 |
8.322 |
Table: Test results
Analysis |
Result |
||
Vertical loading |
safe |
||
Front-impact |
safe |
||
Rear impact |
safe |
||
Side impact |
safe |
||
Four-sided impact |
safe |
Table: Result & Discussion
We selected material as their priority to reduce the vehicles overall weight, cost and to maintain the strength of every component. Before the actual fabrication of the vehicle, engineering design, analysis, and application are used to design and simulate the vehicle with the real-time condition on the software like Solidworks, Creo, etc. If The project aimed at fabrication of roll cage, steering, and braking system for a student Baja car. The car has been fabricated to the best of possible. This project helped us to study and to analyze the procedure of vehicle steering, frame, and braking system fabrication and to identify the performance affecting parameters. This study helped us to understand and overcome the theoretical difficulties of vehicle design. Further improvements and a detailed design of all other systems of the vehicle will lead to a competitive vehicle. We hope to come with the best possible final product.
REFERENCES
-
BAJA SAE RULEBOOK INDIA 2021
-
www.wikipedia.com
-
DESIGN AND ANALYSIS OF AN ALL-TERRAIN VEHICLE 1. GAURAV S. CHIMOTE, 2. KARTIK P. RAJAS, 3. ALOK KUMAR MISHRA
-
Design and Fabrication of Steering and Braking System for All-Terrain Vehicle Boby George, Akhil T Benny, Albert John, Aswin Jose, Denny Francis
-
Design Analysis and Fabrication of M-BAJA ATV 2020 Sandeep Chaudhary, Ganesh Kumar Kantak, Priyanka Sharma, Harshita Mathur
-
FABRICATION OF THE BUGGY CAR D. Rahul raj, Padma Mahesh Kumar, Sarala Bharath, N. Goutham, N. NIkhitha, P. Abhilash.
-
OPTIMIZATION AND IMPACT ANALYSIS OF A ROLL CAGE MODEL Panthapilli Karishma, K.Vamssi Venugopal, I.R.K Raju
-
Innovative Design of an All-Terrain Vehicle (ATV) Harsh Raghuvanshi, N.S. Ramnaveen, Puneet Malhotra, Rakshit, Anurag Khatri
-
Stress Analysis of Roll Cage for an All-Terrain Vehicle Denish S. Mevawala, Mahesh P. Sharma, Devendra A. Patel, Darshan A. Kapadia
-
Static Analysis and Optimisation of Chassis and Suspension of an All-Terrain Vehicle Thanneru Raghu Krishna Prasad, Goutham Solasa, Nariganani SD Satyadeep, G.Suresh Babu
-
DESIGN AND DEVELOPMENT OF ROLL CAGE FOR ALL-TERRAIN VEHICLES S. Ramasubramanian, L.Karikalan, C.V. Dhananjayan Rao,
K. Ahalyan, and S. Kamesh
-
Design And Development of Roll Cage for An All-Terrain Vehicle Khelan Chaudhari, Amogh Joshi, Ranjit Kunte, Kushal Nair
-
Design & Manufacturing of All-Terrain Vehicle (ATV)- Selection, Modification, Static & Dynamic Analysis of ATV Vehicle Upendra S. Gupta,
Sumit Chandak, Devashish Dixit
-
FABRICATION OF ALL-TERRAIN VEHICLE BY USING CONTINUOUSLY VARIABLE TRANSMISSION SYSTEM Kesarinath N.S, Pradeep.M, Senthamilarasu.S, Vijayaprapakar. L