
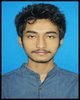
- Open Access
- Authors : Debanga Jyoti Baruah , Saurav Dey , Padmini Neog , Kritika Taniya Saharia, Rahul Raman
- Paper ID : IJERTV9IS110261
- Volume & Issue : Volume 09, Issue 11 (November 2020)
- Published (First Online): 05-12-2020
- ISSN (Online) : 2278-0181
- Publisher Name : IJERT
- License:
This work is licensed under a Creative Commons Attribution 4.0 International License
Feasible Evaluation of a Full-Bridge Resonant Inverter for Induction Heating Appliances with Vienna Rectifier for EMI-RFI Suppression
Debanga Jyoti Baruah
Department of Electrical Engineering
Jorhat Engineering College, Jorhat, India
Saurav Dey
Department of Electrical Engineering
Jorhat Engineering College, Jorhat, India
Padmini Neog
Department of Electrical Engineering
Kritika Taniya Saharia
Department of Electrical Engineering
Jorhat Engineering College, Jorhat, India
Rahul Raman
Department of Electrical Engineering
Indian Institute of Technology (ISM), Dhanbad, India
Jorhat Engineering College, Jorhat, India
Abstract—The present work propound the incorporation of Vienna rectifier (VR) as an integral part of the induction heating (IH) system for vanquishing of electromagnetic interference (EMI) and radio frequency interference (RFI). The IH system employs high frequency switching in the resonant inverter which results in the production of high frequency harmonics. The latter has an ingrained proclivity to flow towards the power supply which in turn the results in the exacerbation of power quality. To overcome this problem, a VR has been proposed at the input of the IH system. The former is based on waveform shaping to obtain a completely sinusoidal nature and thus, it offers a better THD than the other existing techniques using active and passive filters. Moreover, in the present work, priority has been given to the design of an optimized controller for VR for its use as an imperative and amalgamated past of the IH system. Keywords—Vienna rectifier; EMI; RFI; induction heating; PISM; resonant inverter I. INTRODUCTIONThe power electronic devices are very essential in our daily life applications. One of the most common fields is in the Induction Heating Technique. The IH technique is the most favourable mechanism of heating as they are faster, cleaner and more efficient as compared to the conventional heating systems [1-7]. This heating technology without contact finds its approach in domestic, industrial and medical fields. Forming the backbone of many industries and also acting as a predominant in the domestic cooking, it has proved to be the most adoring device for the future [4-7]. However, its complications at high frequency cannot be neglected. The high frequency current results in the formation of harmonics which flows to the mains and cause deterioration of power quality. This has led to the articulation of trendy guidelines by regulatory electrical physique. In the electrical system the vital source of unfruitful power factor and harmonics are non-linear loads and electronic converters. The non-linear load deteriorate the mains or supply side by drawing non-sinusoidal current [8]. They also have interconnection with other power system devices like transformers, capacitors and motors that causes more losses. Therefore, solving these issues of harmonics have grabbed great attention. Thus, various propositions have been established so as to put a constraint on the formation of these harmonics. Also, some new solutions are developed so that the power supply of IH System is feasible [6]. To reduce or mitigate these harmonics and poor power factor issue, passive filters were used earlier. But in present day, with the improvement of power electronic techniques, the passive filters are replaced by some advanced active harmonic filters [7-8]. The active filter circuits steadily use the Boost rectifiers which pull continual current from the input side. By performing switching pattern modulation there could be a chance of getting better power factor and harmonic reduction. The uses of active, passive filters as well as the CRS are the frequently used schemes to overcome the problem of harmonics. These approaches have their own advantages but their disadvantages are also a matter of concern [1-4]. The most conventional and popular methods among these are the passive filters as they are quite cheap. But these filters are suitable for RF range operations and not at low frequencies. Also, they are able to filter only those frequency components that were previously tuned. These factors restrict its use for very specific type of loads. The active filters also face many shortcomings. They have complex design and also their high initial and running cost worse and the situation more. The weekly damped resonant circuit of the CSR also causes great difficulties as the stability of the system is disturbed and so it requires some particular control methods for its enhancement [5-10]. To get rid of these problems VR is used as the fundamental part of IHE.
II. BASIC STRUCTURE OF IHE
Fig.1. Basic circuit diagram of IHE using VR Induction HeatingSystem(IIn)(I0)S1S3S2S4 Vienna RectifierControllerSwitching signals for Vienna RectifierSourceEoutRLC
The IH process works on the basic principle of Electromagnetic induction and Joule Heating. By using electromagnetic induction principle, a contactless process of heating takes place by generation of eddy current within the metal. An IH system consist of a power supply, a work head which receive the alternating current from the supply, the work coil which generates an electromagnetic field inside the coil and work piece. This Electromagnetic field induces current in the work piece so as to produce the heat. The coil is placed around or bordering the work piece. The coil is not placed in proximity with the work piece but it encircle the work piece. The materials generally used for making work piece are metals like aluminium, copper, steel, or brass and also some semiconductors like graphite, carbon or silicon carbide. The heat in the coil is produced by the induced current of alternating nature and of high frequency, and is transmitted through the work piece. Therefore, three physical phenomenon occurs namely eddy current loss, hysteresis loss and skin effect. The eddy current flows against the resistivity of the work piece’s material, and so heat is produced by the principle of Joules heating. Also, some additional heat is produced due to hysteresis internal friction that causes heating of ferromagnetic material. Electrical resistance is offered to this promptly changing magnetic field within the inductor. Another factor that is responsible for heat generation is the skin effect. Due to this effect the high frequency ac from the supply flows only through a thin layer towards the surface of work piece which increases the resistance of conductor. In the present time, the semiconductor technology has come up with new components that are able to operate at high frequency at high power like the MOSFET and IGBT. Due to these advancements, the IH technology is now used in a wide number of applications. The figure 1 shows the basic circuit diagram of an IHE which uses a Vienna Rectifier (VR). The VR restricts the harmonic components of high frequency to flow towards the input side and hence acts as an EMC filter. The next part has the ac-dc converter, i.e. a rectifier circuit which changes the ac to dc. This is followed by an inverter or the dc-ac block. The rectifiers used here can be either a controlled one, comprising of thyristors and other control switches, or uncontrolled one, consisting of only diodes. The former is of outmost importance as it can control the output power with the help of feedback loop control techniques. This dc-ac converter serves as input to the load of the IHE where it supplies the high frequency current. The operating frequency can be adjusted from kHz to as high as MHz based on the type and its need in certain applications. In the present work, the load in the system is a combination of resistor, inductor and capacitor connected in series so as to complete the resonant tank.
III. HARMONIC ELEMINATION BY USING VIENNA RECTIFIER (VR)
The Vienna rectifier is more efficient, nowadays due to its applications in modifying or improvement of power quality. The Vienna rectifier has its unidirectional nature, and for this VR defends the induction heating system from the high frequency harmonics. Over the past few decade, the large industries need various power converters to nullify their loss, for this reason they found that the Vienna rectifier (VR) is the most advisable and profitable consideration due to its power quality improvement and more advantageous over their reliability. For several high power industrial application and unidirectional power conversion aptitude is very advantageous in power converters. Along with the harmonics the VR also increases the power factor quality of the mains. Considering the several important advantages, the VR becomes the most fore choosed option. Lesser number of active switches can produce equal number of voltage level. In the control circuit VR offers very low complexity and device voltage stress. Because of the trivial sensing of various parameter the design and controller implementation is very perspicuous. Moreover, VR offers a highly flexible design for enhancement of power standard at a much lower cost. Several kind of control procedure is effectual for VR. In the present controller attention has been paid off to minimize the number of components and also eliminate the problem due to harmonics.
IV. OPERATING MODE OF VIENNA RECTIFIER (VR)
For achieving better performance it is mandatory to design an idealized circuit. For enacting the mathematical model of the VR, voltage waveforms should be symmetrical at the input side of VR, all switching device components should be ideal in nature. At the input side of VR it is necessary that the switching frequency is higher than fundamental frequency. Moreover, on the DC bus side the capacitance parameter of both the upper and lower should be same. According to the topology of three phase Vienna Rectifier, V(1,2,3)N are the diode switch voltages and E(1,2,3) are source voltage from the mains or input side. VN is the neutral voltage. R and L indicate the value of resistance and inductance respectively at the input side. Beside this Ir and Ir/ are the current flowing under the diode bridge respectively.
)(dtdIL)3,2,1(3,2,13,2,11,2,3NNvvIRE+−−=
() LrccrrRvvI+−=dtdvCcrr
  LrccrrRvvI+−=dtdvCrcr
For the input stage, the active switch unit is forced for commutated current. So, switch voltages are resolved both by the polarity of the AC phase current and the uniform switch state that flows due to inductance. Therefore, the equation for phase 1 is shown in eq. (2) –
; When Sw1 is turned on 01=NV
; When Sw1 is turned off and i1 > 0 (2) crNVV=1
; When Sw1 is turned off and i1 < 0 rcNVV=1
Correspondingly, for the other two phases the equations are procured and switch voltages of these phases are expressed in only one equation as follows:-
(3) rcrcrrwvSvS−=)3,2,1()3,2,1((1,2,3)Nv
Where Sw(1,2,3) and Sw(1,2,3)/ are defined by equation (4) as follows:
, if Sw(1,2,3) is turn on 0)3,2,1(=wS
, if Sw(1,2,3) is turn off and i1,2,3 > 0 (4) 1)3,2,1(=rwS
, if Sw(1,2,3) is turn off and i1,2,3 < 0 1)3,2,1(=rwS
It is considered that the grid is robust and so is a symmetrically balanced 3-phase system. Using equation (3) and (4), it is found that-
3v321NONNNvvv++−=
(5) rcnrncrvSv==+=33S-3,2,11,2,3nnr
The output equations for Ir and Ir/ are represented in equation (6), with the help of equation (4) as follows:-
332211riiSiSiSrwrwrw++=
(6)
332211riiSiSiSrwrwrw−−−=
Switching variables with switching function concluded from straight forward equation which expresses the other system variables (1,2,3)r Sw, (1,2,3)o Sw, and (1,2,3)r/ Sw are functions describing the precise dynamics of the switching state, so the state space equation is neither constant nor variable.
V. SIMULATION DIAGRAM AND THEIR RESULT
The presented paper shows the circuit diagram of IHE along with its corresponding circuit parameter. The simulation of circuit diagram is analyzed by PSIM software. At first, simulation of input phase current of IHE is done in the absence of VR. The simulation is again done by installing a VR in the input side of IHE. The input phase current waveforms are examined and then compared by employing FFT approach. By this approach the effect of harmonics the distortion of input phase current is studied.
The input phase current waveform corresponding to both the cases are shown. The equivalent simulation diagram of IHE in the absence of VR is represented in fig.2. It consists of an AC source (Three phase) which is connected to a three phase (star/delta) step down transformer, whose secondary side is connected to a three phase diode bridge rectifier. Now the IH coil consists of series combination of RLC. This combination behaves like a load of the resonant inverter. The simulation diagram has other voltage and current measuring devices such as ammeter which measures the input phase current of IHE. It is connected to observe the FFT analysis which shows the various high frequency harmonic current. The simulation diagram of IHE having a VR is represented in Fig.5 and its controller is shown in fig.6 which forms the part of the same simulation diagram. The waveforms of the input phase current of IHE without and with the execution of VR are shown in fig.3 and fig.7 respectively. The corresponding FFT analysis of these waveforms is also shown in fig.4 and fig.8 respectively.
Fig.2: IHE in the absence of VR
Fig.3. Waveform of input phase current of IHE in the absence of VR
Fig.4. FFT analysis of input phase current of IHE in the absence of VR
Fig.5. IHE with the application of VR
Fig.6. Controller of VR as presented in fig.5
Fig.7. Input phase current waveform of IHE with application of VR
Fig.8. FFT analysis of input phase current of IHE with the application of VR
VI. TOTAL HARMONIC DISTORTION (THD) CALCULATION OF THE INPUT PHASE CURRENT WAVEFORM-
A. Without the application of VR:
In fig.4, the FFT analysis of current waveform in the supply side shows harmonic deformity due to the appearance of principal harmonic components. With the help of THD calculation the harmonic distortion are examined. The magnitudes of these harmonic components are calculated through PSIM software and are presented in the FFT.
rmsrmsnII,12,2n =THD =
%65.38828.17 1.0231.1233.2314.119193.4=THD 22222=++++
B. With Vienna Rectifier
To reduce the THD, it is necessary to introduce a Vienna rectifier. With VR, it is shown in the FFT that the harmonic distortion due to appearance of existing harmonic components is quite reduced. With the help of THD calculation the harmonic distortions are examined.
2.952% 100%× 31.2310.141+0.246+0.245+0.357+0.763= THD22222=
TABLE I. COMPARISION BETWEEN WITH AND WITHOUT THE APPLICATION OF VR
THD
Without the application of VR
38.65%
With the application of VR
2.952%
VII. CONCLUSION
In the proposed paper, an IHE consisting of VR is studied. The simulation circuit parameter of the IHE is also depicted so as to illustrate the capability of VR to eliminate the harmonic components of high frequency presenting the input phase current waveform. The simulation diagram and FFT analysis are executed in the PSIM software.
Here VR resists the high frequency harmonics which flows back to supply side and hence it works as EMC filter. From the simulation diagram and the FFT analysis of the input phase current waveform has a THD of 38.65% without the application of VR that indicates a very high value. So these harmonics flow back to the supply side and cause deterioration of power standard. On the other hand THD is 2.952% with the application of VR. This value shows that the harmonics in the system with VR is quite minimized as well as the power quality is increased as compared to that of the system without a VR.
These THD value shows the essentiality and significant of VR to minimize the harmonics and increase the power standard. It also shows the importance of VR in IHE which is cost reliable in many senses for practical implementation.
REFERENCES
[1] W. Han, K.T. Chau, R.Y. Zhang, “Flexible induction heating using magnetic resonant coupling”, IEEE Trans. Ind. Electron., vol. 64, no. 3, pp. 1982-1992, March 2017.