
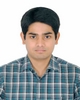
- Open Access
- Authors : Chowdarpally Srinath , Kamal Kumar Ojha
- Paper ID : IJERTV10IS080177
- Volume & Issue : Volume 10, Issue 08 (August 2021)
- Published (First Online): 31-08-2021
- ISSN (Online) : 2278-0181
- Publisher Name : IJERT
- License:
This work is licensed under a Creative Commons Attribution 4.0 International License
Finite Element Analysis of Bullet Impact on Kevlar Fiber Reinforced Composite using Autodyn
1 Chowdarpally Srinath, 2Kamal Kumar Ojha, 1st Mechanical M.C.E.T. Osmania University Hyd 2nd Mechanical M.C.E.T. Osmania University Hyd
Abstract:- The penetration and perforation behavior of Kevlar Fiber Reinforced composite (KFRCP) plate under impact is investigated numerically in this paper. The described numerical analysis was carried out with the AUTODYN hydro code, which included the shock effect due to impact in the modelling. The focus of this research was on the progressive damage behavior and modalities of damage evolution in laminated materials.
The three-dimensional (3D) progressive damage patterns and perforation behavior of 3D Printed plates under impact are highlighted in a number of novel results. For the design and analysis of KFRCP, a few critical parameters such as material, thickness, and impact condition will be explored to improve the crashworthiness design in low-velocity impacts. Determining the maximal deformation, von Mises stress, and energy absorption behavior by modelling.
Keywords: Kevlar fiber reinforced composite, Three dimensional
-
INTRODUCTION
During the last decade, substantial research has focused on experimental and computational simulations of KFRCP under ballistic impact to better understand the target material's post-impact behavior. Nomex and Kevlar aramid fibers were used to make several types of body armor (Jassal & Ghosh, 2002). Experiments, analytical formulations, and numerical simulations were used to carry out these investigations. These CLs' ballistic response was measured in terms of ballistic limit, damage patterns, and energy absorbed by the target when they collided with various projectiles.
Hydrocode simulations have been used to validate the damage patterns observed from experimentation.AUTODYN-3D was used, and a good comparison was found.Several researchers looked at the ballistic impact.by performing on a Kevlar composite target Hydrocode simulations are used to do parametric investigations. These researches advocate for the use of hydrocode simulations to create a ballistic model (Anderson, 1987).
Fiber-reinforced polymer-matrix composites are currently one of the most advanced commercially available materials. Theyre commonly used in aerospace and defense-related industries. Industries, as well as their use in building, automobile, and other fields Sports-goods manufacturing is also very common. The most important the rationale for the composite's broad adoption, as previously stated (Grujicic et al., 2009)
Finite Element Analysis (FEA) is a method of analyzing a material or design using a computer model. It's utilised to improve existing or new products. A corporation can verify that a suggested design meets the client's specifications if certain conditions are met. Manufacturing or construction are two options. It is possible to improve an existing product or building by modifying it.If the model fails, FEA can assist the designer in modifying the design to obtain the desired outcome. By displaying trouble areas on a model, FEA assists analysts in predicting failure due to unknown stresses. Designers will be able to visualize all of the theoretical tensions within an object. Rather than creating and assembling, this strategy can assist cut production costs and time. One of the aspects of Finite Element Analysis is explicit dynamics. The ANSYS explicit dynamics product set assists users in achieving their goals insight into the physics of short-duration events for items that are subjected to extreme temperatures dynamic events that are nonlinear and transitory. The explicit dynamics products from ANSYS (Graça & Vincze, 2021).
-
METHODOLOGY
The endeavor begins with preliminary study on the issue in the form of articles and research papers.. After gaining a sufficient level of comprehension of the subject, software will be employed to complete the remaining tasks. Explicit dynamics will be used to build a rudimentary model with basic bit and formation design. Explicit dynamics will be used to build a rudimentary model with basic bit and formation design. This is where all of the essential parameters will be specified. After that, the model will be imported into AUTODYN, (Fedorova et al., 2016)a different solver. After that, AUTODYN simulations will be run with this model. The success of the Autodyn simulation will be critical to the project's success. Explicit dynamics will be used to build a rudimentary model with basic bit and formation design. This is where all of the essential parameters will be specified. After that, the model will be imported into AUTODYN, a different solver. After that,
Autodyn simulations will be run with this model. The success of the AUTODYN simulation will be critical to the project's success (Maitama et al., 2020).
-
Preliminary Model
A preliminary model is built to familiarize yourself with the software, and then it is run for simulation. This prototype model consists of only two cylinders: one that represents a bit, and another that depicts the formation itself. The model's setup is broken down into a few steps, which are outlined in fig1. Drop tests, collisions between colliding objects, and penetration are all examples of scenarios where explicit dynamics is employed to research or mimic. The materials are chosen and imported here in order to eventually fill up the gaps
Fig 1:- The flowchart of Simulation Process.
Table 1 Showing Mechanical properties of fiber reinforced composite
Material property Value
Longitudinal elastic modulus – 1(GPa) 79.8
Transverse elastic modulus –
2(GPa)
2.59
In-Plane 12 (GPa)
2.1
In-Plane 23 (GPa)
1.17
Poissons ratio – 12
0.33
Poissons ratio – 23
0.1
9. RESULTS OF NUMERICAL SIMULATION
-
(b)
-
(c) (d)
(e) (f)
Fig 2 Showing (a) Dimension of the simulation (b)Meshed file (c) total deformation (d) voi mess
-
Material status (f) Pressure Generated
Total number of nodes and elements generated was 7974, 6517.Physcial preference was explicit .And element order was kept linear.The sides of the plate was fixed and velocity of 100m/s was given to the bullet .Total deformation was 1.5009 e5m and voi mess stress was found to be 1.88 e8 Pa
-
(b)
-
(c) (d)
(e) (f)
Fig3 Showing (a) Material Summary (b)Part summary (c) Energy Summary (d) X Momentum (e) Y Momentum (f) Z Mom
CONCLUSION
In this paper, a numerical simulation of the ballistic impact of a steel projectile on an armour steel plate using a 3-D nonlinear explicit finite element formulation available in ANSYS/AUTO-DYNA is conducted using a rate dependent, simplistic material model of plasticity coupled with a failure criteria. The ability to comprehend the material model, failure criteria, and ballis mechanism In penetration simulations, the impact is amplified. Impact studies on Glass/epoxy laminates revealed that the results varied due on slanted impact rather than regular impact. When a bullet impacts the laminate in a regular direction, it absorbs less energy. The type of impact determines whether a plug or a petal forms. Experiments revealed that crack propagation under the caastrophic situation
REFERENCES
-
Anderson, C. E. (1987). An overview of the theory of hydrocodes. International Journal of Impact Engineering, 5(14), 3359. https://doi.org/10.1016/0734-743X(87)90029-7
-
Fedorova, N. N., Valger, S. A., & Fedorov, A. V. (2016). Simulation of blast action on civil structures using ANSYS Autodyn. AIP Conference Proceedings, 1770(April 2020). https://doi.org/10.1063/1.4963939
-
Graça, A., & Vincze, G. (2021). A short review on the finite element method for asymmetric rolling processes. Metals, 11(5). https://doi.org/10.3390/met11050762
-
Grujicic, M., Glomski, P. S., He, T., Arakere, G., Bell, W. C., & Cheeseman, B. A. (2009). Material modeling and ballistic-resistance analysis of armor-grade composites reinforced with high-performance fibers. Journal of Materials Engineering and Performance, 18(9), 11691182. https://doi.org/10.1007/s11665-009-9370-5
-
Jassal, M., & Ghosh, S. (2002). Aramid fibres – An overview. Indian Journal of Fibre and Textile Research, 27(3), 290306.
-
Maitama, J. Z., Idris, N., Abdi, A., Shuib, L., & Fauzi, R. (2020). A systematic review on implicit and explicit aspect extraction in sentiment analysis. IEEE Access, 8(October), 194166194191. https://doi.org/10.1109/ACCESS.2020.3031217
-
Anderson, C. E. (1987). An overview of the theory of hydrocodes. International Journal of Impact Engineering, 5(14), 3359. https://doi.org/10.1016/0734-743X(87)90029-7
-
Fedorova, N. N., Valger, S. A., & Fedorov, A. V. (2016). Simulation of blast action on civil structures using ANSYS Autodyn. AIP Conference Proceedings, 1770(April 2020). https://doi.org/10.1063/1.4963939
-
Graça, A., & Vincze, G. (2021). A short review on the finite element method for asymmetric rolling processes. Metals, 11(5). https://doi.org/10.3390/met11050762
-
Grujicic, M., Glomski, P. S., He, T., Arakere, G., Bell, W. C., & Cheeseman, B. A. (2009). Material modeling and ballistic-resistance analysis of armor-grade composites reinforced with high-performance fibers. Journal of Materials Engineering and Performance, 18(9), 11691182. https://doi.org/10.1007/s11665-009-9370-5
-
Jassal, M., & Ghosh, S. (2002). Aramid fibres – An overview. Indian Journal of Fibre and Textile Research, 27(3), 290306.
-
Maitama, J. Z., Idris, N., Abdi, A., Shuib, L., & Fauzi, R. (2020). A systematic review on implicit and explicit aspect extraction in sentiment analysis. IEEE Access, 8(October), 194166194191. https://doi.org/10.1109/ACCESS.2020.3031217
AUTHORS
Chowdarpally Srinath
is currently pursuing masters of engineering in Methodist college of Enginee and Technology in the field of mechanical engineering with computer aided design and manufacturing as specialization, he has successfully completed hi bachelors degree from Osmania Univeristy
Kamal Kumar Ojha,
is currently working as Assistant Professor in Methodist College of Enginee and Technology, the author is carrying his doctorate research in the field of additive manufacturing, he has 7 years of teaching experience and has publis more than 20 papers in international journals, the author is expert in dealing the subjects like Finite element analysis, Additive Manufacturing, Fluid Mechanics, Thermodynamics. The author is currently working as a mentor in making an Electric vehicle.