
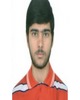
- Open Access
- Authors : Yajnik Dhanvin , Raval Kaushal , Shah Karan , Trivedi Jignesh
- Paper ID : IJERTV10IS110042
- Volume & Issue : Volume 10, Issue 11 (November 2021)
- Published (First Online): 15-11-2021
- ISSN (Online) : 2278-0181
- Publisher Name : IJERT
- License:
This work is licensed under a Creative Commons Attribution 4.0 International License
Finite Element Analysis of Mixing Blade of Stir Casting Machine
Yajnik Dhanvin1, Raval Kaushal2, Shah Karan3, Trivedi Jignesh4
Final year, Mechanical Engineering,
G H Patel College of Engineering and Technology Vidyanagar, Anand, Gujarat, India
Abstract – In this work the aim is to study the effects on blade of stir casting machine used in stirring of Aluminium composite by subjecting it to different conditions like varying rotational speed and blade angle. Varying rotating speed causes changes in the overall torque acting on the shaft and by varying blade angle information related to optimum design is obtained. Finite Element Analysis (FEA) was conducted using commercial ANSYS software and results were derived which consisted of different stress formations on the structure when subjected to different conditions. Two different density materials Aluminium-Silicon Carbide and Aluminium- Graphite were chosen owing to their massive industry usage for analysis. The mixing blade failed when subjected to rotation speeds of 600 and 700 RPM and this is essential to ensure proper functioning of the machine.
Keywords: Aluminium-Graphite, Aluminium-Silicon Carbide, Finite Element Analysis, Mixing Blade, Stir casting machine
-
INTRODUCTION
Stir casting is economical and a widely technique. Its best for mass production due to that it is used widely in industry. In a stir casting process, the reinforcing phases are distributed into molten matrix by mechanical stirrer. Mechanical stirring in the furnace is a key element of this process. The resultant molten alloy, with ceramic particles, can then be used for die casting, permanent mould casting, or sand casting. Stir casting is an economical process for the fabrication of Aluminium matrix composites. There are many parameters in this process, which affect the final micro structure and mechanical properties of the composites. In this method mostly, Aluminium matrix composite (AMCs) is used because of its large availability, flexibility & cost effectiveness, too. AMCs have very high strength to weight ratio, superior wear resistance, greater stiffness, better fatigue resistance, controlled co-efficient of thermal expansion and good stability at elevated temperature therefore AMCs are widely used in Aerospace, Automotive and Construction industries.
Finite Element Analysis was carried out using commercial ANSYS software for understanding the stress limit in the stir casting machine and to understand the effect of blade angle on stresses generated on the mixing blades. This study is important to prevent failure of the blades and ultimately help in preventing industrial accidents. Use of software is more important over here because of the heavy cost involved in finding out the stresses experimentally, time consumed in the process and overall threat to life when attempting to understand the behaviour of fluid and angle of
blade when the machine is in running conditions. Aluminium Graphite (95%Al and 5% Graphite) and Aluminium Silicon Carbide (66% Al and 37% SiC) were chosen for the study due to their massive industrial usage. The mixing blade of the stir casting machine was kept at 30°and 45° with respect to shaft in for a comparative analysis. The shaft connected to the mixing blade was subjected to moment, varying rotational speed and constant downward gravitational acceleration and the mixing blades were primarily subjected to high temperature environment (572°Celsius) and hydrostatic pressure. [1,2,3]
-
METHOD
A. Design and construction
Here we have made a stir casting setup with two mixing blades and have performed FEA on it in order to obtain more information about the working conditions of the machine, Components were designed separately in Solidworks software and the final design was generated using the Assembly function of the Solidworks software. In order to perform Finite Element Analysis (FEA) on the mixing blades, the design was imported into ANSYS software.The mixing blades are made of stainless steel (304) which has ultimate tensile strength of 586 MPa. Stainless Steel is used because it ensures that the mixing blade does not corrode due to high temperature conditions. It turns at high speed on a shaft mounted centrally in the vessel. Principle currents are generated in the liquid due to mixing and this causes high turbulence to be developed in the area surrounding the mixing blade. Mixing Blade has been positioned in a way that vortex formation is less in order to ensure proper mixing The currents generated are radial and tangential. Mixing blades are enclosed in a tank with flat bottom and are connected to the shaft or the tool rod which is made of structural steel having ultimate tensile strength of
460 MPa. Power required to ensure that mixing blades move through the solution was supplied using a motor. [4,5]
Stress, Maximum Principal Elastic Strain, Von Mises Stress and Equivalent Strain. These results were chosen to check the operational capability of the plant. The results were tabulated and graphical charts were made to understand the process better. [6,7]
IV. CALCULATION
Reynolds number (NR) was found out for the molten composite and was used to obtain Power Number Np by using a graph made for Np vs NR which came around 0.3. Power number was used to find the power required to move
the blade by using the formula NP = P×gc
N3 ×D5×
. Power
Figure 1-Design of Setup
-
SIMULATION
Named selection was applied to the model and 3 parts were mainly classified as Mixing Blade, Inlet used to define the upper part of the shaft) and Outlet which is used to define lower part of the shaft. This demarcation is done to apply forces to the selected regions. The model was given a mesh size of 0.0012m and Automatic method was used to generate the shape of the mesh. Meshing is a process of dividing the complex geometrical structure into very small elements for easy calculations. Post meshing, the tool rod or the shaft (Inlet)was given moment and rotational speed in clockwise direction, was subjected to constant gravitational acceleration in downwards (negative y) direction and was allowed displacement in X and Z directions but not in Y direction according to Cartesian Plane system by fixing it. This was done to ensure that the blade does not oscillate vertically due to the resistive force applied by the liquid. The mixing blades were subjected to a hydrostatic pressure caused due to the composite and the entire setup which is inside the crucible was subjected to a temperature of 572° Celsius. The results obtained were Maximum Principal
number is considered similar to friction factor or drag coefficient. It is proportional to the ratio of the drag force acting on the unit area of the impeller and inertial stress. Inertial stress is dependent upon the momentum of the bulk mass of the liquid.
The terms used are listed in the Table 1
Table 1: Terminology used in calculations
Unit |
Description |
g c |
Dimensional Constant with value 1 |
Density of composite (Kg/m3) |
|
D |
Diameter of entire mixing blade (m) |
N |
Rotating speed (RPM) |
T |
Torque acting on the shaft is obtained from power by using formula of P= 2××N×T (N.m) 60000 |
-
RESULTS AND DISCUSSION
The results obtained were tabulated and graphs were plotted to understand the reslts in a better way. Graphs reveal a trend which must be understood when using the machine for better results.
Results obtained for curved mixing blade inclined at 30° to the shaft.
Table 2: FEA of Mixing Blade of 30° angle when using Aluminium-Graphite composite
Power, kWh
Np
Density, Kg/m3
RPM
Diameter,m
Torque, N- m
Maximum Principal Stress, MPa
Maximum Principal Elastic Strain, m/m
Von Mises Stress, MPa
Equivalent Strain, m/m
1.76
0.3
2700
100
0.2159
0.17
0.839
5.34*10-6
1.056
6.8316*10-6
14.07
0.3
2700
200
0.2159
0.67
0.702
6.92*10-6
1.372
8.8719*10-6
47.50
0.3
2700
300
0.2159
1.51
1.580
1.55*10-5
3.059
1.9704*10-6
112.58
0.3
2700
400
0.2159
2.69
2.790
2.74*10-5
5.425
3.4753*10-5
219.89
0.3
2700
500
0.2159
4.20
4.360
4.29*10-5
8.496
5.4352*10-5
379.97
0.3
2700
600
0.2159
6.05
6.280
6.17*10-5
12.230
7.8385*10-5
603.38
0.3
2700
700
0.2159
8.24
8.540
8.39*10-5
16.575
1.065*10-4
Table 3: FEA of Mixing Blade of 30° angle when using Aluminium-Silicon Carbide
Power, kWh
Np
Density, Kg/m3
RPM
Diameter, m
Torque, N- m
Maximum Principal Stress, MPa
Maximum Principal Elastic Strain . m/m
Von Mises Stress, MPa
Equivalent Strain m/m
1.89
0.3
2900
100
0.2159
0.18
0.549
7.62*10-6
1.13
7.13*10-6
15.12
0.3
2900
200
0.2159
0.72
0.757
7.42*10-6
1.47
9.52*10-6
51.01
0.3
2900
300
0.2159
1.62
1.690
1.66*10-5
3.29
2.12*10-5
120.92
0.3
2900
400
0.2159
2.89
3.000
2.95*10-5
5.83
3.73*10-5
236.18
0.3
2900
500
0.2159
4.51
4.870
4.61*10-5
9.13
5.48*10-5
408.11
0.3
2900
600
0.2159
6.50
6.740
6.62*10-5
13.1
8.41*10-5
648.07
0.3
2900
700
0.2159
8.85
7.340
9.01*10-5
17.8
1.14*10-4
Figure 2-Maximum Principal Stress vs Maximum Principal Strain
Figure 3-Von Mises Stress vs Equivalent Strain
Results obtained for flat mixing blade inclined at 45° to the shaft.
Table 4: FEA of Mixing Blade of 45°angle when using Aluminium-Graphite
Power, kWh
Np
Density, Kg/m3
RPM
Diameter, meter
Torque, N- m
Maximum Principal Stress, MPa
Maximum Principal Elastic Strain, m/m
Von Mises Stress, MPa
Equivalent Strain, m/m
1.76
0.3
2700
100
0.2159
0.17
518.71
0.0021036
417.77
0.0021822
14.07
0.3
2700
200
0.2159
0.67
519.30
0.0021994
416.12
0.0021741
47.50
0.3
2700
300
0.2159
1.51
520.86
0.0021962
418.22
0.0021628
112.58
0.3
2700
400
0.2159
2.69
528.29
0.0022036
423.98
0.0021304
219.89
0.3
2700
500
0.2159
4.20
550.86
0.0022222
463.31
0.0026636
379.97
0.3
2700
600
0.2159
6.05
650.94
0.0022701
641.07
0.0037067
603.38
0.3
2700
700
0.2159
8.24
1189.00
0.0031088
853.86
0.0454341
Table 5: FEA of Mixing Blade of 45°angle when using Aluminium-Silicon Carbide
Power, kWh
Np
Density, Kg/m3
RPM
Diameter, meter
Torque, N- m
Maximum Principal Stress, MPa
Maximum Principal Elastic Strain, m/m
Von Mises Stress, MPa
Equivalent Strain, m/m
1.89
0.3
2900
100
0.2159
0.18
518.00
0.0021917
417.77
0.0021822
15.12
0.3
2900
200
0.2159
0.72
520.00
0.0021994
416.11
0.0021741
51.01
0.3
2900
300
0.2159
1.62
525.80
0.0021962
418.23
0.0021928
120.92
0.3
2900
400
0.2159
2.89
528.45
0.0022036
424.00
0.0022305
236.18
0.3
2900
500
0.2159
4.51
551.07
0.0022223
463.81
0.0026665
408.11
0.3
2900
600
0.2159
6.50
651.42
0.0022730
641.80
0.0037111
648.07
0.3
2900
700
0.2159
8.85
679.45
0.0031127
854.86
0.0049634
Figure 4-Maximum Principal Stress vs Maximum Principal Strain
Figure 5- Von Mises Stress vs Equivalent Strain
We observe from the results section that as the torque applied to the shaft increases there is an increase in Maximum Principal Stress, Maximum Principal Elastic Strain, Von Mises Stress and Equivalent Strain for both the composites. Stresses induced in blade with Al-SiC composite is more as compared to stresses induced in blade due to Al-Graphite which is mainly because of the fact that Al-SiC has got greater density than Al-Graphite. As the torque applied increases, there is an increase in stresses as torque causes distribution of stresses around the circular shaft. Therefore, increase in stresses is seen when the speed of rotation of the shaft is increases. This is evident from the following equations:
Von Mises stress is used to determine if the material will fracture or yield. When its value is more than or equal to the yield limit of the same material under tension, the material will yield. Here, we can see that it occurs at 600 RPM and 700 RPM. As the value of torque increases, shear stress increases as given in equation (2) and therefore, value of Von Mises stress and strain also increases. This is evident from the Distortion Energy Theory equation.
(1 2)2+ (2 3)2 + (3 1)2 Syt
2 Nf
Here, represents principal stress, Syt represents yield strength of material and Nf represents the safety factor.
Shear Stress is directly proportional to the yield strength Syt hence, when there is an increase in shear stress it causes
= ( x+ y)
2
+ [
(x+y) 2
]
2
+ xy2
(1)
the yield strength to increase which increases Von Mises stress and Equivalent Strain.
As shown in Table 4, when 45° flat blade is rotated at
where represents maximum principal stress, x and y are components of maximum principal stress and xy represents shear stress.
= `16
3
(2)
where T represents Torque and d represents diameter of blade.
Now according to Hooks Law (=k), as the stress() increases the strain () increases which can be seen in the table.
600 and 700 RPM in Al-Graphite composite, it tends to fail due to high stress induced in it. Similarly, as shown in Table 5, when 45° flat blade is rotated at 600 and 700 RPM in Al- SiC composite, it tends to fail due to high stress induced in it. As seen in Table 2 and 3 we see that mixing blade fails at 600 and 700 RPM for both the composites. This gives us a very important result which will help in preventing machine failure.
We observe from the results that the stresses obtained when blade is kept flat and at 45° are approximately 102 times more than the stresses induced in the curved blade
kept at 30°. This is because when rotated greater face area is exposed to the viscous forces generated due to mixing.
-
CONCLUSION
Here we have subjected mixing blades of stir casting machine to diverse conditions to get more information on its operation capabilities. From this detailed FEA of the mixing blade of stir casting machine we obtain necessary information on operation of this machine which will help us optimize production and avoid failure. As discussed above, when blade is kept at 30° and 45° for speeds of 600 and 700 RPM failure occurs. This result must be kept in mind while operating the machine.
ACKNOWLEDGEMENT
We would like to thank Dr. Darshak Desai, Head of Department, G. H. Patel College of Engineering and Technology for giving us resources to complete the project. We thank our guide Mr. Purnank Bhatt, Assistant Professor,
G. H. Patel College of Engineering and Technology for scientific guidance.
REFERENCES
-
Suman Kant and Ajay Singh Verma, Stir Casting Process in Particulate Aluminium Metal Matrix Composite: A Review, International Journal of Mechanics and Solids, ISSN 09731881 Vol.12, No.1(2017)
-
Nagaral, M., Attar, S., Reddappa, H. N., & Auradi, V. (2015, February). A Review on Particulate Reinforced Aluminium Metal Matrix Composites. In Journal of Emerging Technologies and Innovative Research (Vol. 2, No. 2 (February-2015)). JETIR.
-
Yasmin Begum & Saleemsab Doddamani and Nagesh N, Mechanical Properties of Aluminium Graphite Particulate Composites, International Journal of Engineering Research & Technology (IJERT), Vol.7, Issue 17, ISSN(Online): 22780181
-
Mohit Kumar Sahu and Raj Kumar Sahu, Fabrication of Aluminium Matrix Composites by Stir Casting Technique and Stirring Process Parameters Optimization, Advanced Casting Technologies, InTech Open, 2018, 111-126
-
Ramesh B, Vinayak Koppad, Hemanth Raju Fabrication of Stir casting Setup for Metal Matrix Composite, Fabrication of Stir casting Setup for Metal Matrix Composite, IJSRD – International Journal for Scientific Research & Development| Vol. 5, Issue 06, 2017 | ISSN (online): 2321-0613
-
K Rajendra, MV Sekhar Babu and P Srinivas, Stir Casting Process Simulation by Computational Fluid Dynamics for uniform Nano particles distribution in Al Semi Solid Metal
-
Joseph George, Sheeja Janardhanan, Sijo M T, A Numerical Study on Stir Casting Process in A Metal Matrix Composite Using CFD Approach