
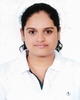
- Open Access
- Authors : Aishwarya B , Geethapriya S , Dr. C. R. Suribabu
- Paper ID : IJERTV10IS040173
- Volume & Issue : Volume 10, Issue 04 (April 2021)
- Published (First Online): 24-04-2021
- ISSN (Online) : 2278-0181
- Publisher Name : IJERT
- License:
This work is licensed under a Creative Commons Attribution 4.0 International License
Flow Analysis in Water Distribution Network under Throttle State of Valves
Aishwarya B SASTRA Deemed University |
Geethapriya S SASTRA Deemed University |
Dr. C R Suribabu SASTRA Deemed University |
Abstract:- The main objective of a water distribution network is to supply water at a sufficient pressure level and quantity to all its users. One of the crucial components is throttle or control valves, which play a critical role in a water distribution system for subsystem isolation and flow or pressure control. Water supply rates from the reservoir(s) which is the source can fluctuate from time to time based on water availability. Therefore, percentage of valve openings has to be adjusted corresponding to the supply rate to maintain the efficacy of the distribution system and to prevent water losses and breakage of apparatuses. The most proficient grouping of valve openings has to be set up for various supply quantities from the reservoirs to maintain the resourcefulness of the network system, keeping equitable distribution among demand nodes as to be satisfied criterion. In addition to adjust valve settings, upholding the economical network configuration, number and position of valves has to be customized on the basis of source connectivity and path of expected higher flow rate and head loss. This paper focuses on obtaining near-Pareto-optimal solution of valve settings to be changed according to the degree of water supply from the reservoirs using differential evolution algorithm with the help of EPANET, Visual Basic embedded in MS Excel. Resilience and reliability parameters are taken as decisive factors for this procedure. This methodology can be used to derive the best set of valve operating conditions for different rates of water supply for every major water distribution network in India to prevent wastage and to reduce water scarcity.
Keywords Differential Evolution Algorithm, Resilience, Reliability, Pareto-optimal solution, Simulation
-
INTRODUCTION
Administering adequate amount of water of applicable quality and quantity has been one of the most important predicaments in human history. Today, a water supply system consists of infrastructure that collects, treats, stores, and distributes apposite amount of sanitary water between water sources and consumers with sufficient pressure. Curtailed natural water sources and booming population has led to the need for innovative methods to efficiently manage a water supply system. Many exertions on the development of a water supply system have been made through for sustainable water supply. As demand of water raise increasingly on the existing water supply system, many studies are attempted to develop a general water supply system to assist decision makers to design more reliable system for a long-range operation period. These attempts also include the optimization of total system construction and operation cost under intricate circumstances. This study concentrates on flow analysis of water in distribution network for varying degrees of supply range from
reservoirs by manoeuvring settings of valves. The main objective is to combine the concept of equitable distribution of available water and the ability of the system to overcome failures to a single parameter. This parameter is termed as common factor and is optimized using Differential Evolution. EPANET2 and macro enabled Microsoft Excel are linked together to search out of optimal valve operations for different percentage of water supply.
The distribution network includes all parts of the water system past treatment. Typical components of the distribution network are storage tanks, reservoirs, pipes, valves, and hydrants. Generally, valves are used to isolate equipment, buildings, and other areas of the water system for repair as well as to control the direction and rate of flow. They are used to drain the system for seasonal shutdown. There are mainly three kinds of valves used. Start/Stop valve only starts or stops the flow of water without controlling/guiding/directing the water flow to any particular direction. Throttle or control valve controls the flow through the supply/distribution system. Check valve checks on the direction of flow. It allows the flow of water through them only in one direction. Mainly, used for preventing backflow to the system. Most valves serve two purposes namely, flow and pressure control and isolating subsystems due to breakage or contaminant containment. In this paper, valves are considered from the point of view of pressure head and controlling water supply. A common practice is to have minimum number of valves in a network as unity less than number of links. This necessitates for every cross-intersection there should be three valves and at every T-section there should be two valves in a network. However, valves suffer more from lack of use than from frequent use. Therefore, placement and configuration of valves is figured out based on source connectivity.
In a water distribution network, the hydraulic parameters, pressure (h) and demand (Q) at the nodes are essential for hydraulic analysis. Equations of Q and h are obtained from conservation of mass or continuity equation and Work- energy principle based either on Darcy-Weisbach or Hazen-Williams equation. Analytical method of solving a network involves complexity because the equations are non-linear in nature. Therefore, several numerical methods such as Hardy – Cross Method, Newton- Raphson Method etc., were used in hydraulics to solve such equations in 19th century. The Evolution of computers had accomplished the task of doing large number of iterations with high speed and accuracy. This paved the way to hydraulic simulation of WDS. One of the approaches of hydraulic simulation is Demand-Driven Analysis (DDA). DDA is carried out by assuming demand on each node in the network is always satisfied without
considering the variation of flow with respect to nodal pressure. This drawback was overcome in Pressure-Driven Analysis (PDA) proposed first by Bhave [1]. Later several relations of nodal pressure and nodal flow were proposed.
EPANET2 is open software used for hydraulic simulations developed by Rossman [2] based on the global gradient algorithm of DDA suggested by Todini and Pilati [3]. One of the techniques to perform PDA model in EPANET2 is to insert artificial elements to all demand nodes. It does not require the need to use of programmers toolkit. Series of
Artificial Elements, suggested by Paez et al. [4], containing FCV-TCV-CV-RES arrangement with has been employed. Parameters of all elements are fixed as suggested. Wagners [5] relationship of flow-pressure is the key principle adopted. Flow Control Valve (FCV) is placed to make sure that flow is not exceeding demand of node. Adding Throttle Control Valve (TCV) is to determine the flow when the nodal pressure is less than minimum pressure. It is achieved by adjusting Minor loss coefficient (k) of TCV. k is calculated based on the following formula.
(1)
Where, A is area of cross section of TCV, hmin is minimum required pressure at each node, Q is discharge through TCV, g is acceleration due to gravity. Reservoir in the series is to quantify flow. When nodal pressure is a negative real number or zero then flow may occur from artificial reservoir (RES) to the node in simulation. Hence TCV and RES are connected via a Check Valve (CV). The arrangement encompasses of two dummy nodes to link the valves and reservoir. Elevation of dummy nodes and reservoir head are kept as same as the demand node to whch they are affixed.
Fig. 1 Alignment of Artificial elements
The term Resilience Index, coined by Todini [6], relates nodal pressure and demand to address the intrinsic capacity of system to overcome failures.
Differential Evolution (DE), a meta-heuristics optimization method, is deployed here to maximize Common Factor for various percentages of water supplies. In general, any evolutionary method mimics the process of gene formation in nature. It is an iterative procedure involving crossover and mutation. DE, is one such method, applies crossover and mutation by means of factors to the generated matrix pool in consecutive sets.
Microsoft Excel is a spreadsheet which features calculation, graphing tools, pivot tables and a macro-enabled programming language called Visual Basic for Applications having an Integrated Development Environment (IDE). This utility can be used to incorporate the EPANET Toolkit. Its library has many functions that help us to retrieve and modify certain parameters of a network model before and after carrying out a hydraulic simulation. This permits us step-by-step control of its simulation process. Visual Basic module (epanet2.bas) and application extension file known as dynamic link library (epanet2.dll) are supplemented to enable access to the header file containing definitions of EPANET in-built functions.
-
LITERATURE REVIEW
This section presents the background to the methodology adopted and source for deciding on analysing dynamics of water flow in distribution network.
Suribabu [7] used Differential evolution algorithm for optimal design of water distribution networks. This paper deals with the application of one of the evolutionary methods to solve non- linear problems which is differential evolution algorithm. This paper gives an insight on how a simulation model of DE is created with the help of VISUAL BASICS to optimize the cost of network by selecting suitable measure for pipe diameter. The simulation is carried out for different sets of weightage factors and crossover probabilities and the results are compared to get best optimized value. Then model is illustrated with Hanoi network. Paez et al. [4] developed a Method for Extended Period Simulation of Water Distribution Networks with Pressure Driven Demands. This paper illustrates a simple way to carry out Pressure-Driven Analysis in EPANET-2 by introducing artificial elements in all demand nodes of the network. These artificial elements are created based on the Wagners relationship between the flow and pressure. The method works both for single period simulation and extended period simulation.
-
METHODOLOGY
-
General
(2)
Where, Qi is the demand at each node, pmin is the minimum pressure required at each node, QResi is the quantity of water supplied from reservoir. pi is pressure at each demand node.
Reliability of a water distribution network can be defined as the probability that the given demand nodes in the distribution system receive sufficient supply with satisfactory pressure head. Proper usage of weightage has made it easier to merge Resilience Index and Reliability into a sole element called common factor (CF).
This paper presents a procedure to generate percentage opening of valves in a water distribution network for varying degrees of supply range from reservoirs without compromising resilience of the system. The simulation model can be applied to any water distribution network.
The method proposed here adds,
-
Selection of a water distribution network, develop it as a prototype and benchmark it under generic conditions.
-
Fixation of Position and number of throttle control valves based on source connectivity. Extraction of
Loss coefficient of values for different percentage openings of the valve from the designer of valve.
-
Insertion of artificial elements to all demand nodes in the network to carry out PDA in EPANET.
Parameters of artificial elements to be entered are as follows,
-
For FCV: Diameter = 1000mm, Setting = Demand of node
-
For TCV: minor loss coefficient = k
-
For CV: Diameter =1000 mm and Length = 0.001mm
-
Addition of connection of flow control valve to all reservoirs to control the supply of water to the network.
-
Incorporation of EPANET2.0, VISUAL BASIC FOR APPLICATIONS, AND MS EXCEL to compute desired values for different degrees of water supply.
-
Application of Differential Evolution Algorithm. Set mutation factor (mf), cross-over probability (cr), number of trials and population size.
-
Calculation of resilience, reliability of each demand node, percentage of total water supply and their ratio M.
-
Allocation of suitable weightages to different M values to achieve equitable distribution of the supplied quantity of water to all demand.
-
Obtaining the product of sum of weightages and resilience as corresponding Common Factor for each set of valves operations.
-
Finding the near-Pareto-optimal common factor for the given percentage of water supply from reservoirs.
-
-
Equations involved in calculating common factor
(3)
Where, Q is the actual quantity of water supplied to the node. QD is theoretical design demand of the node.
(4)
(5)
Where, Qi is designed supply of water supplied from ith Reservoir. xi is the percentage of supply of water from the respective Reservoir. Qtotal is the total designed supply of water from all the reservoirs.
(6)
Weightages for categorizing M factor is used to make the ratio to approach unity so that equitable distribution is mathematically achieved. For example, maximum weightage is given to unity and the weightage value decreases as M factor moves away from unity.
(7)
Where, CF is Common Factor used to compile W factor and resilience.
3.2 Differential Evolution Algorithm 4. Case Study
Input the value of q1, q2 – degree of water supply rate from reservoirs
Input the value of q1, q2 – degree of water supply rate from reservoirs
A benchmark Network with two reservoirs (Fig.2) is selected to perform desired experimentation. This particular network has 21 pipes linking and 13 nodes. Basic inputs such as properties of links, nodes are assigned as given in Table 2 and Table 3. Here gate valve is used as TCV and its loss coefficient
Set mutation factor (mf) and cross- over probability (cr)
Set mutation factor (mf) and cross- over probability (cr)
corresponding to percentage opening is provided in Table 4. Allocation of weightages to M factor is done as
Randomly generate 1000 sets of restricted valve settings for initiating matrix pool
Randomly generate 1000 sets of restricted valve settings for initiating matrix pool
Set target set by random selection from the matrix pool (i)
Set target set by random selection from the matrix pool (i)
100 try outs
100 try outs
demonstrated in Table 1. Minor loss coefficients of TCV in series of artificial elements are calculated and the values with corresponding valve ID are listed in Table 7. To alter the supply from reservoirs percentage openings of FCV are discretized from a range of values to list of numbers. It is illustrated in Table 5 and 6. Mutation factor (mf) and cross- over probability (cr) are taken as 0.8 and 0.4 respectively. Differential Evolution is carried out by keeping 100 as the number of trials and 1000 as population size. . These data are fed to the program and near-Pareto-optimal CF is obtained. Table 8 is formatted to show optimized setting of valves for different combinations of degree of supply and corresponding CF.
Add trial set to matrix pool
Add trial set to matrix pool
Add target set to matrix pool
Add target set to matrix pool
Select randomly three solution sets A, , C (A B C i)
Noisy set = {(A B) * mf} + C
Noisy set = {(A B) * mf} + C
Random generation of indices for each valve – Rdm[9]
Random generation of indices for each valve – Rdm[9]
If cr>=rdm(j),
Trial set (j) =Noisy set (j) Else,
Trial set (j) =Target set (j)
Fig .2 Benchmark Network
WEIGHTAGE ASSIGNED ' W' |
RANGE OF M |
0 |
0 |
(17-37] |
|
0.5 |
(10-17] |
0.75 |
(8-10] |
1 |
(6-8] |
1.2 |
(4-6] |
1.5 |
(2-4] |
2 |
(0-0.2] |
(1.8-2] |
|
3 |
(0.2-0.4] |
(1.6-1.8] |
|
4 |
(0.4-0.6] |
(1.4-1.6] |
|
5 |
(0.6-0.9] |
(1.1-1.4] |
|
6 |
(0.9-1.1] |
(1-1.1] |
|
7 |
1 |
WEIGHTAGE ASSIGNED ' W' |
RANGE OF M |
0 |
0 |
(17-37] |
|
0.5 |
(10-17] |
0.75 |
(8-10] |
1 |
(6-8] |
1.2 |
(4-6] |
1.5 |
(2-4] |
2 |
(0-0.2] |
(1.8-2] |
|
3 |
(0.2-0.4] |
(1.6-1.8] |
|
4 |
(0.4-0.6] |
(1.4-1.6] |
|
5 |
(0.6-0.9] |
(1.1-1.4] |
|
6 |
(0.9-1.1] |
(1-1.1] |
|
7 |
1 |
Table-1: Weightage Value corresponding to the range of M factor
Compute common factors of trial and target sets- CF1 and CF2
Compute common factors of trial and target sets- CF1 and CF2
NO
YES
CF1>CF
Find the set having highest CF and add to maxicf matrix pool
Find the set having highest CF and add to maxicf matrix pool
Set having maximum CF among maxicf matrix pool = near- pareto-optimal
Set having maximum CF among maxicf matrix pool = near- pareto-optimal
Table 2: Pipe Characteristics
Pipe ID |
Length, m |
Diameter, mm |
Roughness Coefficient, H-W |
1 |
609.60 |
762 |
130 |
2 |
243.80 |
762 |
128 |
3 |
1524.00 |
609 |
126 |
4 |
1127.76 |
609 |
124 |
5 |
1188.72 |
406 |
122 |
6 |
640.08 |
406 |
120 |
7 |
762.00 |
254 |
118 |
8 |
944.88 |
254 |
116 |
9 |
1676.40 |
381 |
114 |
10 |
883.92 |
305 |
112 |
11 |
883.92 |
305 |
110 |
12 |
1371.60 |
381 |
108 |
13 |
762.00 |
254 |
106 |
14 |
822.96 |
254 |
104 |
15 |
944.88 |
305 |
102 |
16 |
579.00 |
305 |
100 |
17 |
487.68 |
203 |
98 |
18 |
457.20 |
152 |
96 |
19 |
502.92 |
203 |
94 |
20 |
883.92 |
203 |
92 |
21 |
944.88 |
305 |
90 |
Node ID |
Elevation, m |
Demand, CMH |
1 |
27.43 |
0.0 |
2 |
33.53 |
212.4 |
3 |
28.96 |
212.4 |
4 |
32.00 |
640.8 |
5 |
30.48 |
212.4 |
6 |
31.39 |
684.0 |
7 |
29.56 |
640.8 |
8 |
31.39 |
327.6 |
9 |
32.61 |
0.0 |
10 |
34.14 |
0.0 |
11 |
35.05 |
108.0 |
12 |
36.58 |
108.0 |
13 |
33.53 |
0.0 |
RES1 |
60.96 |
NA |
RES2 |
60.96 |
NA |
Node ID |
Elevation, m |
Demand, CMH |
1 |
27.43 |
0.0 |
2 |
33.53 |
212.4 |
3 |
28.96 |
212.4 |
4 |
32.00 |
640.8 |
5 |
30.48 |
212.4 |
6 |
31.39 |
684.0 |
7 |
29.56 |
640.8 |
8 |
31.39 |
327.6 |
9 |
32.61 |
0.0 |
10 |
34.14 |
0.0 |
11 |
35.05 |
108.0 |
12 |
36.58 |
108.0 |
13 |
33.53 |
0.0 |
RES1 |
60.96 |
NA |
RES2 |
60.96 |
NA |
Table 3: Node Characteristics
Table -4: Loss coefficient value VS valve opening
4
% Opening |
Loss Coeffficient |
0 |
CLOSED |
5 |
120 |
10 |
100 |
15 |
50 |
20 |
26 |
25 |
15 |
30 |
12 |
35 |
9 |
40 |
7 |
45 |
6 |
50 |
5.5 |
55 |
5 |
60 |
4.5 |
65 |
4 |
70 |
4 |
75 |
4 |
80 |
4 |
85 |
4 |
90 |
4 |
95 |
|
100 |
4 |
Table – 5: Discharge of water from Reservoir 1 per % of supply
% of Water Supply |
Discharge, CMH |
0 |
0 |
10 |
224.49 |
20 |
448.98 |
30 |
673.47 |
40 |
897.96 |
50 |
1122.45 |
60 |
1346.94 |
70 |
1571.43 |
80 |
1795.92 |
90 |
202.41 |
100 |
2244.9 |
Table 6: Discharge of water from Reservoir 2 per % of supply
% of Water Supply |
Discharge, CMH |
0 |
0 |
10 |
89.177 |
20 |
178.354 |
30 |
267.531 |
40 |
356.708 |
50 |
445.885 |
60 |
535.062 |
70 |
624.239 |
80 |
713.416 |
90 |
802.593 |
100 |
891.77 |
Table 7: Head loss coefficient values corresponding to Demand
Valve ID |
Demand, CMH |
K value |
23 |
212.4 |
26 |
25 |
212.4 |
26 |
27 |
640.8 |
2 |
29 |
212.4 |
26 |
31 |
684.0 |
2 |
33 |
640.8 |
2 |
35 |
327.6 |
11 |
37 |
108.0 |
102 |
39 |
108.0 |
102 |
-
RESULTS AND DISCUSSION
Proper working of Differential Evolution algorithm is verified by plotting graph between trial number and highest value of Common Factor of the set among 1000 sets in the matrix pool for 20-30 combo (20% supply from Reservoir 1 and 30% supply from reservoir 2). The profile of obtained graph was a reasonable increasing curve. This also proves that the program set for running is working properly according to the formulated procedure.
Fig 3 Graph between iteration number and Common Factor
for 20-30 combination
Table 8: Near-Pareto-optimal solutions for different combinations of degree of supply
Reservoir 1
Reservoir 2
Valve 1
Valve 2
Valve 3
Valve 4
Valve 5
Valve6
Valve 7
Valve 8
Valve 9
CF
0
10
30
100
100
50
30
10
100
60
100
37.852
0
20
50
40
70
100
90
50
50
50
40
41.235
0
30
70
90
100
70
50
50
20
0
10
8.800
0
40
90
90
90
90
100
70
60
50
80
52.676
0
50
90
30
90
30
90
100
30
80
60
47.176
0
60
80
60
80
80
20
0
30
10
90
42.727
0
70
50
60
20
20
70
40
100
60
20
38.497
0
80
70
90
100
70
50
50
20
0
10
44.000
0
90
50
90
40
100
30
50
20
0
100
39.759
0
100
50
40
70
100
90
50
50
50
40
45.817
10
0
20
70
90
20
50
30
60
90
60
2.635
10
10
70
50
10
0
30
20
30
40
90
16.036
10
20
90
30
90
30
90
100
30
80
60
47.176
10
30
80
60
80
80
20
0
30
10
90
42.727
10
40
40
30
50
70
70
70
80
20
40
38.072
10
50
50
60
20
20
70
40
100
60
20
38.497
10
60
70
90
100
70
50
50
20
0
10
44.000
10
70
50
90
40
100
30
50
20
0
100
39.759
10
80
50
40
70
100
90
50
50
50
40
45.817
10
90
100
90
30
80
60
20
10
80
70
45.604
10
100
10
100
70
0
60
10
10
80
30
25.250
20
0
70
50
10
0
30
20
30
40
90
40.090
20
10
10
100
70
0
60
10
10
80
30
25.250
20
20
70
50
10
0
30
20
30
40
90
40.090
20
30
90
90
90
90
100
70
60
50
80
52.676
20
40
90
30
90
30
90
100
30
80
60
47.176
20
50
40
60
70
40
90
80
50
60
80
44.713
20
60
80
60
80
80
20
0
30
10
90
42.727
20
70
70
90
100
70
50
50
20
0
10
44.000
20
80
50
40
70
100
90
50
50
50
40
45.817
20
90
100
90
30
80
60
20
10
80
70
45.604
20
100
70
50
10
0
30
20
30
40
90
40.090
30
0
70
50
10
0
30
20
30
40
90
40.090
30
10
90
90
90
90
100
70
60
50
80
52.676
30
20
90
30
90
30
90
100
30
80
60
47.176
30
30
90
90
90
90
100
70
60
50
80
52.676
30
40
90
30
90
30
90
100
30
80
60
47.176
30
50
70
90
100
70
50
50
20
0
10
44.000
30
60
50
40
70
100
90
50
50
50
40
45.817
30
70
100
90
30
80
60
20
10
80
70
45.604
30
80
90
90
90
90
100
70
60
50
80
52.676
30
90
90
30
90
30
90
100
30
80
60
47.176
30
100
80
60
80
80
20
0
30
10
90
42.727
40
0
70
90
100
70
50
50
20
0
10
44.000
40
10
50
40
70
100
90
50
50
50
40
45.817
40
20
100
90
30
80
60
20
10
80
70
45.604
40
30
90
90
90
90
100
70
60
50
80
52.676
40
40
90
30
90
30
90
100
30
80
60
47.176
40
50
40
60
70
40
90
80
50
60
80
44.713
40
60
70
90
100
70
50
50
20
0
10
44.000
40
70
50
40
70
100
90
50
50
50
40
45.817
40
80
100
90
30
80
60
20
10
80
70
45.604
40
90
70
50
10
0
30
20
30
40
90
40.090
40
100
90
30
90
30
90
100
30
80
60
47.176
50
0
40
60
70
40
90
80
50
60
80
44.713
50
10
80
60
80
80
20
0
30
10
90
42.727
50
20
70
90
100
70
50
50
20
0
10
44.000
50
30
50
40
70
100
90
50
50
50
40
45.817
50
40
100
90
30
80
60
20
10
80
70
45.604
50
50
70
50
10
0
30
20
30
40
90
40.090
50
60
90
90
90
90
100
70
60
50
80
52.676
50
70
90
30
90
30
90
100
30
80
60
47.176
50
80
40
60
70
40
90
80
50
60
80
44.713
50
90
80
60
80
80
20
0
30
10
90
42.727
50
100
50
60
20
20
70
40
100
60
20
38.497
60
0
30
100
100
50
30
10
100
60
100
37.852
60
10
50
40
70
100
90
50
50
50
40
45.817
60
20
100
90
30
80
60
20
10
80
70
45.604
60
30
90
90
90
90
100
70
60
50
80
52.676
60
40
40
30
40
90
100
50
90
80
80
37.590
60
50
90
30
90
30
90
100
30
80
60
47.176
60
60
40
60
70
40
90
80
50
60
80
44.713
60
70
40
30
50
70
70
70
80
20
40
38.072
60
80
50
60
20
20
70
40
100
60
20
38.497
60
90
50
40
70
100
90
50
50
50
40
40.726
60
100
90
90
90
90
100
70
60
50
80
40.970
70
0
90
30
90
30
90
100
30
80
60
47.176
70
10
40
60
70
40
90
80
50
60
80
44.713
70
20
40
30
50
70
70
70
80
20
40
38.072
70
30
50
60
20
20
70
40
100
60
20
38.497
70
40
30
100
100
50
30
10
100
60
100
37.852
70
50
50
40
70
100
90
50
50
50
40
45.817
70
60
100
90
30
80
60
20
10
80
70
40.537
70
70
90
90
90
90
100
70
60
50
80
46.823
70
80
10
40
30
30
10
90
90
60
90
0.000
70
90
40
90
70
90
70
50
80
60
40
0.000
70
100
10
20
10
60
60
60
80
70
60
0.724
80
0
40
30
50
70
70
70
80
20
40
38.072
80
10
50
60
20
20
70
40
100
60
20
38.497
80
20
30
100
100
50
30
10
100
60
100
37.852
80
30
50
40
70
100
90
50
50
50
40
40.726
80
40
100
90
30
80
60
20
10
80
70
40.537
80
50
10
70
80
10
40
20
90
60
50
0.000
80
60
40
90
70
90
70
50
80
60
40
0.000
80
70
90
90
90
90
100
70
60
50
80
0.000
80
80
40
30
40
90
100
50
90
80
80
0.000
80
90
90
30
90
30
90
100
30
80
60
0.000
80
100
40
60
70
40
90
80
50
60
80
5.962
90
0
40
30
50
70
70
70
80
20
40
3.807
90
10
10
40
70
60
60
40
90
30
40
5.580
90
20
50
60
20
20
70
40
100
60
20
38.497
90
30
40
60
10
20
50
20
60
30
100
32.652
90
40
30
100
100
50
30
10
100
60
100
37.852
90
50
50
40
70
100
90
50
50
50
40
45.817
90
60
100
90
30
80
60
20
10
80
70
45.604
90
70
90
90
90
90
100
70
60
50
80
52.676
90
80
40
30
40
90
100
50
90
80
80
37.590
90
90
90
30
90
30
90
100
30
80
60
47.176
90
100
40
60
70
40
90
80
50
60
80
44.713
100
0
90
50
30
40
60
70
10
30
20
0.000
100
10
30
70
60
70
20
20
70
60
80
0.000
100
20
50
60
90
90
50
90
50
60
20
0.000
100
30
50
90
40
100
30
50
20
0
100
4.418
100
40
40
30
40
90
100
50
90
80
80
5.012
100
50
40
80
40
30
20
20
50
40
10
5.506
100
60
90
50
30
40
60
70
10
30
20
6.029
100
70
10
40
70
60
60
40
90
30
40
22.322
100
80
50
60
20
20
70
40
100
60
20
46.196
100
90
30
70
60
70
20
20
70
60
80
43.995
100
100
40
60
10
20
50
20
60
30
100
39.908
-
CONCLUSION
This paper gave an insight on how to deal with managing steady and convenient flow of water in water distribution network. Whenever there is a fluctuation in the water supply rates from the reservoir. This approach can be used to determine the value adjusting to be made for every prominent
change in the water supply for water distribution networks. This ensures reduction in leakages and increase in the durability of apparatuses in the network as the resilience factor is controlled. Also, as the reliability factor is taken into account for justifiable distribution of water among all demand nodes, consumer satisfaction is enhanced. If the prevailing handlings such as gauge measurements and controls, valve/pump operations, of WDN are completely digitalized, manoeuvring
of WDN can be done remotely monitored and controlled. Internet of Things (IOT) can be incorporated in the digitized system. This paves way for quick and smart response by the system itself. This reduces human error and their involvement in regulating water supply in distribution network. By these tactics, sustainable and effectual usages of withstanding water resources can be done to ensure their future availability. For further study and exploration, by the domain of Computational Engineering, multiple simulation models can be explored using different software tools, apt methodologies, complex WDN benchmark layouts and setup configurations. In this research article, combination of streams of water resource engineering and software programming was used which further denotes that mathematical models can be incorporated for numerical analysis of structures and design layouts with the help of software tools.
-
REFERENCES
-
Bhave, P. R. (1981). Node flow analysis of water distribution systems. J. Transp. Eng., 107(4), 457-467.
-
Rossman, L. A. (2000). EPANET 2 users manual, Water Supply and Water Resources Division, National Risk Management Research Laboratory, U.S. Environmental Protection Agency, Cincinnati, OH.
-
Todini, E., and Pilati, S. (1988). A gradient algorithm for the analysis of pipe networks, Wiley, London, 1-20.
-
Paez, D., Suribabu, C.R., and Filion, Y. (2018) Method for Extended Period Simulation of Water Distribution Networks with Pressure Driven Demands, Water Resources Management 32:2837-2846
-
Wagner, J. M., Shamir, U., and Marks, D. H. (1988). Water distribution reliability: simulation methods. J. Water Resour. Plann. Manage., 114(3), 276294.
-
Todini, E. 2000 Looped water distribution networks design using a resilience index based heuristic approach, Urban Water, 2(2), 115122.
-
Suribabu, C.R., 2010. Differential evolution algorithm for optimal design of water distribution networks J. Hydroinf., 12(1), 66-82