
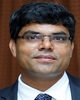
- Open Access
- Authors : D. K Shinde , Dipesh Patil , Pramod A Naik , D N Raut
- Paper ID : IJERTV10IS050224
- Volume & Issue : Volume 10, Issue 05 (May 2021)
- Published (First Online): 25-05-2021
- ISSN (Online) : 2278-0181
- Publisher Name : IJERT
- License:
This work is licensed under a Creative Commons Attribution 4.0 International License
Framework for Implementing Quality Management System for Heavy Construction Equipment Manufacturing Industry
Dipesh Patil1
1PG Student, Department Production Engineering,
Veermata Jijabai Technological Institute Mumbai India 400019
Pramod A. Naik2
2Ph D Scholar, Department Production Engineering,
Veermata Jijabai Technological Institute Mumbai India 400019
D. K Shinde3
3Associate Professor, Department Production Engineering,
Veermata Jijabai Technological Institute Mumbai India 400019
D N Raut4
4Professor,
Department Production Engineering, Veermata Jijabai Technological Institute Mumbai India 400019
Abstract The present Quality Management (QMS) System certification standard or to be specific ISO 9001:2008 has been revised recently to ISO 9001:2015 version. The study examines the future conversion, primary causes, and its impacts on the various domains of business. The complete concept is explained with the help of case study in heavy construction equipment manufacturing industry. The revision will bring some benefits viz. greater emphasis on involvement of top management in the process, address risks and opportunities in a structured manner, use simplified language and a common structure and terms for multiple management systems, address supply chain management more effectively, more user-friendly for service and knowledge-based organizations, less emphasis on documentation. The organizations aspire to implement and upgrade QMS as per ISO 9001:2015 will be benefited from the information given in this research paper. Also, the organizations which seeks the improvement by implementing QMS are also gets benefited by the information available in this report. The standard is being used by the organizations to demonstrate constantly, the capability to supply products and services that satisfy customer and regulatory requirements. The previous version of the standard ISO 9001:2008 has been replaced by a new version of the standard i.e., ISO 9001:2015 which is released in September 2015. The main areas of concern for the organizations are the steps to be taken to achieve the new version and become compliant with it. This research explains the framework for implementation of new revision of ISO in manufacturing industry. Also, explains the concept of ISO 9001:2015 in details and also, helpful for industries seeking for upgraded quality management system and understand its impact on businesses to assess their performance. The interested organization in the quality management system can refer this report to enhance their understanding towards quality QMS.
Keywords: Quality Management System, Risk Management, ISO 9001:2015, PDCA Cycle, QMS Principles, Risk-based Thinking, Business Performance.
-
INTRODUCTION
ISO 9001 is a quality management standard that sets out requirements for organizations quality management systems.
In 1987 the first edition of ISO 9001 standard was formulated. It got the name ISO 9001:1987. Since then four more editions have been released and named after the releasing year; 1994, 2000, 2008 and the latest version, which this project will concern, 2015. The 2015 version emphasizes stronger focus on the organizations stakeholders, its context and has another high-level structure. This aims business organizations to be more efficient in their operations and improve the customer satisfaction. The approach to the research work is sequential. It includes the exploration of transition from ISO 9001:2008 to ISO 9001:2015 with focus on risk-based thinking and, to assess the impact of QMS on the effectiveness of performance of the organization.
A. Case Company
The case company is one of the most renowned construction equipment manufacturing industry in the world. It is an ISO 9001:2008 certified industry. It offers unique technology applies into road construction industry viz. highways & airports, road widening & development projects. The organization has strong quality policy which reflects top management commitment towards quality of the products & delivery processes.
-
ISO 9001:2015 QUALITY MANAGEMENT SYSTEM
-
Quality Management Principles
The quality management principle is explained in the Fig. 1 as below.
Figure 1. Quality Principles for ISO 9001:2015 [10]
-
P-D-C-A Cycle
PDCA cycle remained unchanged in the revised standards. The cycle operates at both a process level & an overall level too it is shown in the Fig.2.
.
Figure 2. P-D-C-A Cycle for ISO 9001:2015 [12]
-
Risk-Based Thinking is at the Core of ISO 9001:2015
Risk-based thinking has a very important place in ISO 9001:2015. To emphasize their dominance, the concept of risk occurs forty-eight times in ISO 9001:2015, compared with only three times in ISO 9001:2008. The addition of risk- based thinking has made the preventive measures of ISO 9001:2008 redundant. These preventive measures no longer appear in ISO 9001:2015. [1]
-
Analyis of ISO 9001:2008 vs ISO 9001:2015
The comparison of the ISO standards are noted in the Table 1 with parameters to be considers for QMS for ISO. Thus, the planning for the implementation of the ISO 2015 is made for the parameters revised in ISO.
Table 1. ISO 9001:2008 vs ISO 9001:2015 [11]
The main causes of delay and cost overruns in such projects
included: monthly payment difficulties; poor contractor management; delay in material procurement; poor technical performances; and escalation of material prices, etc. Hence, effective project planning, controlling and monitoring should be established to enhance project performance in order to minimize or avoid delay and cost overrun in gas pipeline laying projects. If implemented by employees within organization, it can be used for the performance evaluation of overall project and for the contractors working for the company[13].
The project schedule should reflect all the work associated with delivering the project on time. Without a full and complete schedule, the project manager will be unable to communicate the complete effort, in terms of cost and resources, necessary to deliver the project [14]. The industry experts and criteria for the AHP method were determined based upon three mostly used project management software are selected for this study. AHP method is applied with five different experts opinion on the selection vectors are used to reach a subjective conclusion [15].
By implementing lean manufacturing principle, the unnecessary time for performing the fabrication operation were reduce by 120 hours, which leads to cycle time reduction of the above fabrication process and productivity increased by 7.6%. This reduction in the cycle time has significant impact on companys productivity. The value stream map developed gave a good idea of the process and the changes to be done [16].
Manufacturing execution system is a technological advancement which provides a competitive edge to manufacturing organization by promising 43.48% reduction in low efficiency downtime and 18.07% reduction in injection molding machine breakdown [17].
The criteria for selection any project based upon Time elapsed, economic feasibility, issues related to get permissions for carrying out work. To get more understanding surveys was conducted by floating a questionnaire to managers of different offices, the responses were then fed into model prepared on AHP software to derive the sequence of working on projects with above criteria. The inconsistency obtained after the analysis of 2.93% that is acceptale as maximum acceptable inconsistency not more than 10%. More over the activities involved in different projects can be sequenced and a holistic project model can be made by clubbing activities of all available projects in a multi-project environment[18].
-
-
RESEARCH DESIGN
-
Hypothesis Model
To study the impact of implementation of QMS on business performance factors, a hypothesis model has to be considered as shown in the Fig.3. The research model gives the impact of implementation of QMS on business performance, through improvement in mediator factors such as information quality, operating performance, design performance, supplier and customer relationships, product and service quality and business performance. These parameters as discussed as below [1], [2].
Figure 3. Hypothesis Model [1]
H1: Implementation of QMS Improves Information Quality. H2: Information Quality Improves Design Performance.
H3: Information Quality Improves Operating Performance. H4: Information Quality Improves Supplier Relationship. H5: Information Quality Improves Customer Relationship.
H6: Design Performance and Operating Performance Improves Product Quality.
H7: Supplier Relationship & Customer Relationship Improves Service Quality.
H8: Product Quality and Service Quality Improves Business Performance.
-
Selection of Respondents
The respondents are needed to verify the above-mentioned hypothesis model. So, it has been decided to consider all the employees of case company to incorporate in the survey.
-
Data Collection Technique
In this research the used methodology is questionnaire design. So, questionnaires have prepared on the various factors explained in hypothesis model & these are circulated in the respondents to collect the data.
-
Data Analysis Methodology
-
The data is analyzed with the help of statistical software, IBM SPSS Statistics 21 and Microsoft office EXCEL as shown in the Table 2. This section discusses about the tests used in our data analysis approach.
Table 2. Data Analysis Techniques
Sr.
Steps to Perform
Method Used
1
Validity Test
Pilot Survey
2
Reliability Test
Cronbachs alpha Method
3
Descriptive Statistics
Mean & Percentage
4
Measure of Correlation
Correlation Analysis
-
-
DATA ANALYSIS & RESULTS
-
Validity Test
Content validity is the extent to which a measuring instrument provides adequate coverage of the topic under study. It determines the primarily judgmental and intuitive. It can also be determined by using a panel of persons who shall judge how well the measuring instrument meets the standards, but there is no numerical way to express it. Pilot survey has been conducted in order to understand the content validity for the questionnaire.
-
Reliability Analysis
A measuring instrument is reliable if it provides consistent results. It is measured by calculating reliability coefficient, Cronbach alpha () value for each factor. In our analysis it is
calculated by using IBM SPSS statistical software. Cronbach alpha () values greater than 0.7 generally acceptable according to the literature. The Cronbach alpha value found to be lie in between 0.715 (Service Quality) to 0.942 (Customer Relationship). Table 3 show the Cronbach Alpha values
Table 3. Cronbach Alpha () Values
-
Correlation Analysis
All the correlations are found to be positive. Pearsons correlation coefficient is used to evaluate the relationship is noted in the Table 4.
Table 4. Correlation Analysis
Correlation is significant at the 0.01 level
Correlation is significant at the 0.05 level
-
Descriptive Statistical Analysis
From the descriptive analysis using SPSS tool following relationship analysis are obtained and noted for implementation of QMS.
-
Implementation of QMS
Figure 4. Mean Values- Implementation of QMS as Catalyst for Change
From the survey analysis, it is found that the major reason for implementing QMS as a catalyst to bring change are base point for quality improvement & to introduce new practices. Also, the value shows that QMS practices are the part of regular routine & also emphasize on the documents created are used in daily practices for improvements is plotted and is shown in Fig 4.
Figure 5. Mean Values- Use of QMS in Daily Practices
The survey also reflects reasons for implementation of QMS as to establish long term relationship with customers & create discipline in organization is plotted and shown the Fig. 5 and Fig. 6. Also, customer pressure has very less impact on the reason for implementation.
Figure 6. Mean Values- Reasons for Implementing QMS
-
-
Information Quality
According to survey, QMS affected Information quality a lot. The major factors under information quality are: Info in record is complete & accurate, Info is useful in daily practices [15-17] Fig. 6 showed are the maintenance are posted on the shop floor, Quality data is recorded & use to communicate the changes. The mean values for the improvement in information quality is shown in the Table 5.
Table 5. Mean Values- Improvement in Information Quality
-
Design Performance
Some respondent thinks it improved overall product design performance while some thinks it improved design durability. The most significant item that found in analysis is continuous improvement are made in product design are plotted for analysis and is shown in the Fig.7.
Figure 7. Mean Values- Improvement in Design Performance
-
Operating Performance
Fig. 8 showed the significant impact that found are improved manufacturing quality & reduced cost of quality. While the values for mean lies in between 3.33 to 4.
Figure 8. Mean Values- Improvement in Operating Performance
-
Supplier Relationship
Survey analysis emphasizes long term relationship existing with supplier & Suppliers are selected on the basis of quality of their product is plotted and noted the significance and is shown in the Fig. 9. The mean value varies from 3.42 to 4.
Figure 9. Mean Values- Improvement in Supplier Relationship
-
Customer Relationship
The major factor improved due to customer relationship is performance feedback data is collected from customers and plotted the relationship for the analysis and is shown in the Fig 10.
Figure 10. Mean Values- Improvement in Customer Relationship
-
Product Quality
The mean values of measurement variables of product
quality factor lie between 3.67 and 4.08 is obtained after the SPSS analysis in descriptive statistics and is shown the Fig.11.
Figure 11. Mean Values- Improvement in Product Quality
-
Service Quality
The value improvement in the service quality of items lie between 3.25 and 3.83 is shown in the Fig. 12 with a positive response for most of the items.
Figure 12. Mean Values- Improvement in Service Quality
-
Business Performance
Figure 13. Mean Values- Improvement in Business Performance
Figure 13 showed the lists mean values of items of business performance factor. All the values are around 3.8, which means organizations agree with items of business performance factor.
In summary, implemented thought the manufacturing processes. The assessment of impact of ISO 9001:2015 shows positive impact on case company. The analysis of the SPSS on the quality management system showed that QMS is implemented as a base point for improving quality processes in the organization and, it has been used in dily practices. Almost all respondent thinks there is positive relationship between implementation of QMS in organization and business performance. Information quality improved after implementation of standard. The implementation improved the design, operational performance of the organization which in turns led to high product quality.
-
-
CONCLUSION
The case company has successfully implemented new QMS ISO 9001:2015. Risk based thinking is involves in each of the processes. Risk management plan is developed and implemented thought the manufacturing processes.
The assessment of impact of ISO 9001:2015 shows positive impact on case company. The result shows that QMS is implemented as a base point for improving quality processes in the organization and, it has been used in daily practices. Almost all respondent thinks there is positive relationship between implementation of QMS in organization and business performance. Information quality improved after implementation of standard. The implementation improved the design, operational performance of the organization which in turns led to high product quality.
There is significant information sharing between organization and the supplier or customer which helps to develop more significant customer and supplier relationship. The good customer and supplier relationship led to provide good service to the end users. All proposed hypothesis is found to have positive significance. The correlation between operational performance and product quality is highly significant. However, there is not enough statistical significance found between the product quality and business performance.
It is recommended for future researcher to collect more data or to test the relationship between product quality and business performance. Based on the research, it can be concluded that the implementation of QMS helps the case company on multiple aspects, but the major significance is found on information quality and product quality of the organization. Finally, the organization successfully change the QMS to ISO 9001:2015 standard.
ACKNOWLEDGMENT
We thankful to Production Engineering Department, VJTI, Mumbai 400019 for financial support for this project work and giving us the opportunity to conduct the project in industrial environment.
REFERENCES
-
Berglund, Magnus & Jönsson, Anna, ISO 9001:2015 implementation at a manufacturing company, Halmstad 2016-06-02.
-
Waqar Ahmed in his paper titled, ISO 9001 Transition and its Impact on the Organizational Performance: Evidence from Service Industries of Pakistan, International Journal of Research in Business Studies and Management Volume 4, Issue 3, March 2017, 39-54.
-
Glaucia Aparecida Prates & José Claudio Caraschi in their paper titled, Organizational Impacts due to ISO 9001 Certified Implementation on Brazilians Cardboard Companies, International Journal of Academic Research in Business and Social Sciences May 2014, Vol. 4, No. 5.
-
A.Yahia-Berrouiguet, I. Mankouri & N. Benarbia in their paper titled, Impact of ISO 9001 Certification on Firm Performance: Case Study of Beni Saf Cement Company, Journal of Economics and Business Research, Year XXI, No.1, 2015, pp. 158-165.
-
Dr. Omer Abdel Aziz El Tigani in his paper titled, The Impact of the Implementation of the ISO 9000 Quality Management System upon the Perception of the Performance of the Organization's Worker, Global Journal of Management and Business Research Volume 11 Issue 8 Version 1.0 August 2011.
-
Basak Manders in his thesis titled, Implementation and Impact of ISO 9001, Erasmus Research Institute of Management ERIM.
-
Pandi Selvi D in his paper titled, Study on the Impact of ISO Certification on the Quality Culture of Construction Companies International Research Journal of Engineering and Technology (IRJET), Volume: 04 Issue: 09 | Sep -2017.
-
Raju Roy & Dr. Debomalya Ghose in their paper titled, Changeover from ISO 9001: 2008 to the Revised Standard ISO 9001:2015, Journal of Research in Business and Management, Volume 4 ~ Issue 10 (2016) pp: 89-93.
-
https://www.slideshare.net/learnsigma/ISO90002000 [10]http://isoconsultantpune.com/apb-consultant-iso-90012015-quality-
management system/apb-consultant-seven-principles-quality- management-per-iso-90012015/
-
https://www.pauwelsconsulting.com/blog/iso-9001-2015/
-
https://www.iso.org/obp/ui/#iso:std:iso:9001:ed-5:v1:en
-
Zende, T., & Shinde, D. K. Causes of Delay and Cost Overruns in A Domestic and Commercial Natural Gas Supplying Company and Its Analysis Using Research Methodology. International Journal of Scientific and Research Publications, Volume 7, Issue 6, June 2017 page 173-177.
-
Kambli, Pritesh V., and D. K. Shinde. "Project Planning for Installation and Commissioning of Odorization Unit for CGD Projects." International Journal of Innovative Research in Science, Engineering and Technology, Volume 9, Issue 11, November 2020 page 10384-10391.
-
Harsha Gyamalni D. K. Shinde Application of Project Management Processes for Construction of Gas Pipeline Projects, International Journal of Innovative Research in Science, Engineering and Technology, Volume 9, Issue 11, November 2020 page 10384-10388.
-
Ranjan, S. K., & Shinde, D. K. (2018). Implementing Lean Manufacturing Technique in Fabrication Process PlanningA Case Study. International Research Journal of Engineering and Technology Volume: 05 Issue: 07 | July 2018 page 2600-2606.
-
Sachin P. Ghongade, D. K. Shinde, Manufacturing Execution System implementing approach to achieve operational excellence for pipes &fittings manufacturing industry, Proceeding of International Conference on Manufacturing Excellence-ICMAX-2017 March 3-4, 2017 Nashik.