
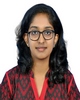
- Open Access
- Authors : Nikhil Binoy C , Abhinand G K , Kavya Rajesh , Syamdas A, Treesa Saji
- Paper ID : IJERTV10IS120182
- Volume & Issue : Volume 10, Issue 12 (December 2021)
- Published (First Online): 20-01-2022
- ISSN (Online) : 2278-0181
- Publisher Name : IJERT
- License:
This work is licensed under a Creative Commons Attribution 4.0 International License
Gas Leakage Monitoring and HVAC Automation System
Nikhil Binoy C
Instrumentation and Control Engineering Department NSS College of Engineering
Palakkad, India
Abhinand G K
Instrumentation and Control Engineering Department NSS College of Engineering
Palakkad, India
Syamdas A
Instrumentation and Control Engineering Department NSS College of Engineering
Palakkad, India
Treesa Saji
Instrumentation and Control Engineering Department NSS College of Engineering
Palakkad, India
Kavya Rajesh
Instrumentation and Control Engineering Department NSS College of Engineering
Palakkad, India
AbstractHazards due to gas leakage are a constant part of industries where storage and transportation facilities of flammable and toxic gases are involved. These include the oil and gas industries, petro-chemical industries and even plants which have toxic and flammable by-products. These leakages can cause serious losses to life and transportation in plants. In this paper a gas leakage monitoring system consisting of a rover which moves outside the pipeline to measure leaked gases and continuously send the monitored data to a local server using an IoT platform is discussed. This allows continuous monitoring of the plant conditions and provides a quick alert when situations go out of hand.
Keywords: Gas leak, Hydrogen sulphide, Carbon monoxide, combustible gas, line follower, rover, IoT
I. INTRODUCTION
Oil refiners, processing plants, storage farms, offshore platforms and many other industries which deal with chemicals either use utilities or make use of a wide range of hazardous, flammable or toxic gases .These gases are in most of the cases unavoidable part of the plants process. Thus storage, usage and transportation of these gases are given extreme care in industries to avoid hazards caused due to their leakage. Leakages can occur in storage places as well as in transportation pipelines. Some of the reasons may be poor maintenance, low quality of vessel material which are used to store corrosive and toxic substances and can also be due to human errors that is due to negligence. One of the biggest example for this is the Bhopal Gas tragedy. So when troublesome gases are involved, either the plant should be well maintained or a proper system for a quick leak detection has to be these so that fast safety action can be taken as soon as possible. In this paper a primary leak detection system is explained which utilizes a mobile gas monitoring rover outside the pipeline and also includes the use of IoT for learning the occurred leak by continuous monitoring of the gas concentration outside the vessel and pipelines. The monitoring is done for toxic gases which are hydrogen sulphide, carbon monoxide, and combustible gases like methane, propane etc.
Hydrogen sulphide when present above 130 ppb is both toxic as well as flammable and causes major health and infrastructure risks. Carbon monoxide when present above 1000ppm, if inhaled for more than ten minutes can cause respiratory and neurological problems in humans while methane being a combustible gas, when present above 50,000ppm can cause exploitation and fire.
II LITERATURE SURVEY
A system was designed to identify and measure methane gas in the zones of flammable gas stockpile sites. The device measures the air and water quality, including every parameter that can have deviation as the result of gas leakage in the water or air. The sensors measure the amount of CH4 and CO2 gas in the air while the temperature, pH, and electrical conductivity of the water are monitored. The device is controlled by an Arduino UNO microcontroller that transmits measured data to the database on Raspberry Pi 3.[2]
Different advancements in pipeline leakage detection were put forward. This includes acoustic emission, optic fiber sensor, ground penetrating radar, Vapour sampling and infrared thermography [5]. A system with sensors are connected to arduino for data collection and it uses LabVIEW as the GUI (graphical user interface).[6]
A detailed sensor list for flammable toxic and combustible gases and their possible advantages and disadvantages has been compared. One such example is the SB-95 sensor, which detects sequentially the variation on the methane and carbon monoxide gas concentration and modifies its resistance accordingly. The variation in the filament resistivity is transmitted as a voltage variation on the load resistor[7]. At the same time, metal oxide sensors have a long response time and even longer recovery time. These sensors need to extract the gas by making a hole into the pipe for the gas concentration measurement. Making holes can cause danger such as leakage or explosion of the toxic gas[9].
On the other hand, ultrasonic sensors are free from the above disadvantages for the measurement of gas concentration with fast response time and the device is compact and inexpensive too[9].
A detailed study of health issues related to gases like hydrogen sulphide, Carbon monoxide and methane has been done[3,7]. Activation of optical alarms and buzzers when the sensed values of SB-95 sensor goes above the threshold along with the working of the sensor is explained in detail[7]. Table.2.1 gives a reference about the sources and flammable limits of Hydrocarbons and Hydrogen Sulphide gas[3].Even though the sources of leaks of both the types of gases are common, the lower range of flammability of hydrocarbons are less than hydrogen sulphide which makes their leaks vulnerable to explosions. At the same time the toxicity of hydrogen sulphide is seen as 50ppm which can really cause lots of health issues in humans and continuous exposure may even lead to death[3].
III DESIGN OF THE ROVER
The rover is basically square shaped which consists of two main wheels at its back and a free wheel at the front portion. The body of the rover, which has the dimensions of 27*27*6 cm are well supported by these wheels. Together they provide a smooth movement for the system. The rover body is designed in such a way so that it could hold the components mounted on it without failure.A hand down sketch of the rover is given in figure 1.
Fig.1 : Rover Design
IV ROVER MOVEMENT
Fig.2 : Path design
The movement of the rover is exactly like a line follower which follows a black path on a white surface. There are no speed controllers for the movement and the line follower works only by the sensing action of two infrared sensor modules which are attached on the front side of the rover.
The infrared module contains a transmitter (photodiode) and a detector (photodetector).When the rover is moving in a straight line the module only comes in contact with the white surface and has no contact with the black path.Thus the IR radiation send by the transmitter gets reflected back by the white surface and is thereby detected by the IR detector. In this state both the wheels rotate in the same direction.The areas where the rover needs to make a turn while following the path, the black path crosses one of the IR modules thus absorbing the IR emitted by the transmitter. At this condition the output of the IR detector turns low and the corresponding wheel rotates in the opposite direction while the other wheel rotates in the same direction as before.This helps the rover to divert to the desired direction.
The main wheels are controlled by two 5V DC motors which in turn are controlled by L293D motor driver. These are coded in embedded C and controlled by the arduino UNO which is an open source microcontroller.
IV GAS MONITORING
The monitoring f gases in the plant is done by three gas sensors namely MQ136, MQ135 and MQ2 for hydrogen sulphide, methane and carbon monoxide respectively. The MQ series of sensors have a wide detecting scope so that the sensing element of these sensors also has affinity to other common gases present in the petroleum industries. The operating voltage of the MQ136 gas sensor is 5V and its sensing material is tin oxide. Its electrode material and electrode lining material is gold and platinum respectively, thus making it one of the expensive MQ series sensors. The MQ2 gas sensor is used specifically for the detection of gases like methane, butane, LPG, smoke, etc. Its digital pin helps us to use this sensor even without a microcontroller.
These gas sensors are mounted on the top of the rover body and they sense the gas as the rover moves its prescribed path. The gas concentrations are displayed in the 16*2 display in millivolts(mv) continuously and when a threshold is crossed an alarm is activated. The monitored gas values are also continuously sent to a local server.
V. ROVER CIRCUIT
Fig.3 : Circuit diagram
From Fig.3 : Circuit diagram the overall working of the system is understood. The LM358 comparator IC along with the L293D motor driver and two 5V DC motors control the movement of the rover with the help of an arduino board and the power supply of 12V. The gas sensors are connected to the analog pins of the Arduino for continuous monitoring.ESP8266 Node MCU wifi module is connected to TX and RX pins (serial communication pins) for data transfer. An encoder with a transmitter is used for the transfer of data from the rover to the system where the control action is taken when the gas level exceeds the threshold value.
VI .DATA TRANSFER AND HVAC AUTOMATION
The data obtained from the gas sensors along with the fire and temperature sensors are continuously sent to a local server using an IoT platform which is ESP8266 Node MCU, which is a wifi module. This provides the interface between the arduino microcontroller and the web. The values of the sensors are sent to the plant control room so that an operator can easily access the condition of the plant. The ESP8266 Node MCU provides a coverage of about 400 m without any router and the antenna, this is very effective for data transfer with reasonable cost.
The HVAC system in the plan deals with the heating, ventilation and air conditioning system of a plant. Here we use a three speed fan and a pump which works under relay logic and is always at the on state, which is the normal speed. There are two extra speeds for the fan which will be activated once the gas level and temperature goes beyond the threshold accordingly. This way the temperature is brought back to normal and thus the fan returns back to its normal speed. Fig.4 : 4 Circuit diagram shows the receiver circuit of the Wi-Fi module.
Fig.4 : Circuit diagram
Here we have given 900mV as the threshold value manually. Before 900mV reached the HVAC system was in OFF condition, that is, it was not activated. But after 900mV the HVAC system in both cases was activated automatically. Methane gas can cause fire due to the leakage therefore a pump is used to drive down the fire and bring the plant back to its normal condition. Fan is used in the case of the carbon monoxide as higher concentration of carbon monoxide may be the cause of the respiratory health issues so proper ventilation should be provided when the concentration of the gas goes higher inside the room. So a proper ventilator or a fan is used in the case of carbon monoxide.
VII COMPLETED SYSTEM
The figure 5 and figure 6 shows completed hardware assembly of the gas leakage monitoring system. series of sensors have a wide detecting scope so that the sensing element.
Fig.5: Top View
Fig.6 : Side View
VIII OBSERVATIONS AND DISCUSSIONS
This primary gas leakage system can only be used for leakage monitoring inside a building as laying the path and detection of gas leaks outside can be very troublesome for this design. As the rover moves on ground, the high pipelines outside the plants makes the gas sensing really inaccurate.Thus indoors are preferred for monitoring.
Table 9.1 Table 9.2
Table 9.1 contains the sensor outputs in millivolts of carbon monoxide, while table 9.2 contains sensor outputs in millivolts of methane. If 900mV is given as threshold value manually, the system is only turned ON or activated by only a value above or equal to 900mV. This activation is done automatically. Methane gas can cause fire due to leakage, therefore a pump is used to drive down the fire and bring the plant back to its normal condition. Fan is used in the case of the carbon monoxide as higher concentration of carbon monoxide may be the cause of respiratory health issues so proper ventilation should be provided when the concentration of the gas goes higher inside the room.
The MQ sensor series are a primary gas sensing device, where sensitive materials are SnO2 (Tin oxide) for almost all sensors. Here sensors when checked on it sensitivity is comparatively low, thus affects the systems overall accuracy.Also speed control for the rover is employed when it encounters small slopes, the paths obstructed. Thus the path should be designed in a manner such that it causes no obstacles for the rover movement.
The graph 9.3 shows the sensor characteristics of carbon monoxide sensor and graph 9.4 shows the sensor characteristics of methane sensor. MQ135 and MQ2 are the sensors used for measuring methane and carbon monoxide respectively.
IX CONCLUSION
The system can be taken as a small attempt in connecting the existing primary gas detection methods to a mobile platform integrated with IoT platforms. The gases are sensed in an area of 1m radius of the rover and the sensor output datas are continuously transferred to the local server. The accuracy of MQ sensors are not upto the mark thus stray gases are also detected which creates an amount of error in the outputs of the sensors, especially in case of methane. Further the availability and storage of toxic gases like hydrogen sulphide also creates problems for testing the assembled hardware. As the system operates outside the pipeline, the complication of system maintenance and material selection of the system in case of corrosive gases is reduced. Thus the system at this stage can only be used as a primary indicator of leakage inside a plant.
X FUTURE SCOPE
Future scope includes the upgradation of the system to a prediction level using Big Data analytics. This can also help in predicting the location of the leak with the analysed values, which in turn will be much useful to avoid hazards caused due to leaks. Further development can be made in the part of improving the accuracy of the gas sensing, speed control of the rover and can also give some control actions when detected with a leak, like automation of the plant's HVAC system.
REFERENCES
-
Meer Shadman Saeed, Nusrat Alim, "Design and Implementation of a Dual Mode Autonomous Gas Leakage Detecting Robot", RoboticsElectrical and Signal Processing Techniques (ICREST) 2019 International Conference on, pp. 79-84, 2019.
-
Adekitan, A. I., Matthews, V. O., & Olasunkanmi, O. (2018). A microcontroller based gas leakage detection and evacuation system. IOP Conference Series: Materials Science and Engineering, 413, 012008. doi: 10.1088/1757-899x/413/1/012008.
-
F. I. M. Ali, F. Awwad, Y. E. Greish and S. T. Mahmoud, "Hydrogen Sulfide (H2S) Gas Sensor: A Review," in IEEE Sensors Journal, vol. 19, no. 7, pp. 2394-2407, 1 April1, 2019.doi: 10.1109/JSEN.2018.2886131.
-
Tissot, J., Trouilleau, C., Fieque, B., Crastes, A., & Legras, O. (2006).Uncooled microbolometer detector: recent developments at ULIS. Opto-Electronics Review, 14(1). doi: 10.2478/s11772-006- 0004-2.
-
Adegboye, M. A., Fung, W.-K., & Karnik, A. (2019). Recent Advances in Pipelines Monitoring and il Leakage Detection Technologies: Principles and Approaches. doi:10.20944/preprints201905.0041.v1.
-
Khera, N., Sharma, P., Shukla, D., & Dar, I. G. (2017). Development of a web based gas monitoring system using LabVIEW. 2017 Recent Developments in Control, Automation & Power Engineering (RDCAPE). doi: 10.1109/rdcape.2017.8358311.
-
M. Chintoanu et al., "Methane and Carbon Monoxide Gas Detection system based on semiconductor sensor," 2006 IEEE International Conference on Automation, Quality and Testing, Robotics, Cluj- Napoca, 2006, pp. 208-211.doi: 10.1109/AQTR.2006.254633.
-
El-Zahab, S., & Zayed, T. (2019). Leak detection in water distribution networks: an introductory overview. Smart Water, 4(1). doi: 10.1186/s40713-019-0017-x.
-
M. Taskin and Y. Kato, "Instant Gas Concentration Measurement Using Ultrasound From Exterior of a Pipe," in IEEE Sensors Journal, vol. 19, no. 11, pp. 4017-4024, 1 June1, 2019.doi: 10.1109/JSEN.2019.2897736.
-
G. Dvajasvie, B. P. Farisha, S. N. Babu, K. P. Saheen and N. C. Binoy, "Leak Detection in Water-Distribution Pipe System," 2018 Second International Conference on Intelligent Computing and Control Systems (ICICCS), Madurai, India, 2018, pp. 1-4.