
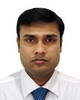
- Open Access
- Authors : Vivekanandan T
- Paper ID : IJERTV13IS090023
- Volume & Issue : Volume 13, Issue 09 (September 2024)
- Published (First Online): 12-09-2024
- ISSN (Online) : 2278-0181
- Publisher Name : IJERT
- License:
This work is licensed under a Creative Commons Attribution 4.0 International License
High Speed Electrical Drives Harmonic Impact and Mitigation in Induction Motor Winding Insulation: A Perspective of VFD
Vivekanandan T M Tech – Power system Electrical Engineering
Shri Venkateshwara University, India
ABSTRACT
Variable Frequency Drives (VFDs) are becoming more commonplace for controlling the speed and torque of induction motors. This has enhanced process control and resulted in significant energy savings in many industrial applications. Still, there have been a few issues with VFDs, such as the production of harmonics that have a negative impact online side power quality and the insulation of induction motor windings. This article provides a comprehensive analysis of the effects of variable frequency drives (VFDs) on induction motor winding insulation, harmonic analysis and mitigation in grid and load side. We look at how harmonics may accelerate insulation deterioration and induce motor failures via voltage stress, extra heating, vibration, and resonance. Among the many mitigation strategies examined in this work are the following: the use of Active harmonic filters, shielded cables with proper grounding techniques; the selection of inverter duty-insulated motors; the implementation of output filters like dV/dt and sine-wave filters; the use of multi- pulse converters at the drive end or active front-end configurations; and other advanced VFD technologies. In addition, losses caused by insulation wearing out may be prevented with frequent inspections.
Keywords: variable frequency drive; Active harmonic filter: interharmonics; induction motors; power quality; subharmonics; ac drives; Voltage harmonics; Current harmonics; Oscillation
-
INTRODUCTION
A growing number of sectors are realizing the benefits of variable frequency drives (VFD). Ultralow-speed machines, like huge mills in the mining and minerals industry, low-speed rolling mills in the metals industry, medium-speed pumps and fans, and high- speed turbomachinery in the oil and gas sector, are just a few examples of the extremely varied speed ranges encountered in various applications. A gear or direct connection links the motor to the load machine. A gas turbine or steam turbine is an alternative technology in turbomachinery to VFD. A gearless direct coupling allows the turbine's high-speed rotation to power the load machine, which is most often a compressor. There is a growing movement to switch out these turbines for ones with an electric drive system for a variety of reasons, including those related to the environment, improved controllability, less maintenance, and others. It is possible to use both traditional and high-speed technologies in some situations.
On the other hand, rapid technology may be the sole option in cases where weight and space constraints are significant. You might also see a gas turbine serving as the primary driver and an electric motor acting as a starter or assister. Increases to the stator frequency made possible by VFD technology also make it possible to use 4-pole machines at faster speeds. The standard VFD design is very similar to a VFD designed for a high-speed application. In one case, it is an identical product with minor tweaks, and in the other, it is unchanged.
In contrast, the electric motor is the most intricate part. A motor with higher speed and "standard" bearings is an improvement over a regular motor. An additional layer of intricacy is introduced if the speed range necessitates magnetic bearings.
-
LITERATURE REVIEW
Current and voltage waveform distortions have been on the rise due to the expansion and integration of contemporary power networks and advances in renewable energy. Interharmonics are distortions that degrade power quality (PQ) in future electrical networks. They are composed of nonmultiplex components of the fundamental frequency [1, 2]. Therefore, the relevant limitations must be revised. Loads in non-steady states and control techniques that modulate amplitude primarily produce nonperiodic fluctuations in current and voltage, which in turn create inter harmonics [3]. A number of factors influence their production. These include the utilization of nonlinear loads, cascaded sub synchronous converters, asymmetric induction motors, and AC/DC and DC/AC conversions in renewable energy sources like wind turbines and photovoltaic systems. Another major source of interharmonics is the double-stage system, which is made up of two AC systems with different frequencies that are linked by a DC connection [4,5]. Static compensators (STATCOMs) and high voltage direct current (HVDC) applications rely on inverters based on integrated gate bipolar transistors (IGBTs) [6, 7]. Other notable devices include cycloconverters, electric arc furnaces, and power communication lines.
Equipment heating, mechanical system vibrations, auditory disturbances, and interference with power transmission lines are all negative outcomes of interharmonics, which can cause energy losses and distortions. A notable impact is the flicker effect, which is defined as the noticeable variation in light intensity in light-emitting diode and fluorescent bulb sources. Interharmonics and voltage fluctuations are directly correlated with this effect, which is induced by changes in the magnitude of the voltage.
Published by : http://www.ijert.org
International Journal of Engineering Research & Technology (IJERT)
ISSN: 2278-0181
Vol. 13 Issue 9, September 2024
When it comes to industrial operations, induction motors, and AC drives are crucial for enabling the interchange of motion. On the other hand, power quality evaluations have shown that harmonic distortion and voltage imbalance are electrical disturbances that lower torque and power performance, which in turn affects how motors and other equipment work [8, 9].
Several reports indicate that these disruptions have detrimental impacts on electrical equipment. In induction motors, for example, variations in voltage may cause saturation of the magnetic circuit [10], which in turn increases ohmic losses in the rotor and stator windings, which leads to overheating [11] and a noticeable decrease in efficiency [12,13]. Voltage subharmonics and interharmonics create speed variations, which in turn cause torque pulsations that correspond with the first elastic mode's inherent frequency [14, 15]. In medium- and high-power motors, this may cause torsional resonance, which can destroy the powertrain [16].
There is a direct link between induction motors and AC drives in terms of PQ and this relationship has the potential to cause grid disruptions.
AC choppers, a kind of soft starting control system for alternating current machines based on thyristors (SCR), reduce startup currents by regulating the voltage supply during startup. On the other hand, torque is shown to be decreasing since it is directly proportional to the square of the current. Some have hypothesized that this architecture causes quite high degrees of interharmonic distortion [17]. Harmonics with resonances and nonstationary properties may be produced by soft starters and amplifiers, according to previous research [18, 19].
However, VFDs are becoming more popular in industrial settings as an alternative to soft starts due to their ability to manage numerous machines simultaneously while using less energy. Interharmonic distortions may be caused by VFDs, albeit [20]. A variable frequency drive (VFD) is an energy storage device that uses a huge capacitor in the connection between two AC-DC-AC conversion stages. Afterard, the DC link voltage is transformed into a three-phase AC voltage with changeable frequency and magnitude by means of a pulse width modulation (PWM) inverter, which allows for the control of the motor speed. But there's no such thing as perfect filtering and interharmonic distortion could still get in via the two AC networks. VFDs can show subpar performance when everything is in equilibrium.
Altering the current's interharmonics at the VFD's input is possible using modulation methods. The VFD system's power level dictates the proper selection of the drive's switching frequency. While DC link small capacitors have a long lifetime, they aren't energy storage devices and may cause distortions between harmonics. Electronic inductor (EI) front-end rectifiers mitigate load- side low-frequency oscillations, according to the research. It is also not possible to reduce interharmonic distortions using standard filters that include AC and DC side chokes and DC link capacitors. Interharmonics of current are known to occur in supply systems in certain situations, such as inverters operating in overmodulation or loads that are imbalanced. A number of variables, including motor operating conditions, imbalances in currents and supply voltage (including switching angles), and varying mechanical loads may affect the magnitudes, frequencies, and phase sequence of these inter harmonics. Variations in torque oscillations and different quantities of the load may also cause Interharmonics.
In a perfect world, the amplitudes of the interharmonic currents would be small if the inverter operated in the linear modulation zone with a constant torque load. Acoustic noise and mechanical vibrations are produced by AC motors that are operated by a variable frequency drive (VFD) [21]. When the machines' inherent frequencies interact, excessive torsional vibrations () become very noticeable. "In high-power induction motors, locomotives, drilling rigs, and big drives in turbomachinery
applications, these vibrations might produce torque pulsation multiplication if the inverter's control mechanism is not appropriately adjusted. The amplitude and frequency of the interharmonics in a motor-mechanical system are affected by the currents produced in the stator and rotor when the VFD is controlled in an open-loop manner [22, 23].
Interharmonic production in the grid and low-power induction motors controlled by various AC drive topologies (e.g., VFDs and soft starts) has yet to be addressed in prior research due to the loads' and machines' inertial qualities. The only thing that has been shown is that at lower load torque levels, the distortions in the drive input current are bigger.
On the other hand, research has shown that in induction motors, undesirable disturbances like torque pulsations, currents, and vibrations can be caused by the machine's inertia characteristics and the load, particularly in the positive sequence, when interharmonic and subharmonic voltage effects are at play [24]. Problems become more severe when the load's moment of inertia (NMI) is less than the motor's moment of inertia in this case [17]. Evidently, substantial inter harmonics may be produced in the grid and inverter output when motors operated by soft starts and VFDs are started.
-
VFD TECHNOLOGY
There is little difference between a standard variable frequency drive (VFD) and a high-speed VFD today. Although there are now easier solutions, the drive arrangement proposed in [25] with a so-called dual inverter layout and an open winding stator design is still essentially feasible. The power hardware is either the same as or slightly modified from standard VFD. There may be variations in the inverter modulation strategy. Presently, two primary technologies are available for high-speed conventional drives: voltage source inverters (VSI) and current source inverters (CSI).
-
Load-commutated inverter (LCI)
One subset of current source inverters is the LCI. The traditional thyristors that make converters on both the line side and the motor side are commutated by voltages applied from outside the device. The terms "load commutated" and the requirement that LCI be used in conjunction with synchronous machines are both clarified by this. Since its introduction in the 1970s, LCI has been accessible to the public as a mature and dependable technology. A very powerful drive may be implemented with little complexity and component count because of the simple scaling of power and voltage. With little tweaking, the LCI drive can achieve an output frequency of up to 100120 Hz, even though most of its uses have rated frequencies between 40 and 60 Hz. The use of a 2-pole turbo-motor allows for direct driving at speeds of up to 7,200 rpm [26]. Some installations of the first semi-high-speed
Vol. 13 Issue 9, September 2024
LCI-driven motors have been in service for more than 30 years, proving their dependability and availability. This technology was accomplished in the early 1980s.
-
Voltage source inverter (VSI)
The development of self-commutated power electronic switches (IGCT thyristors, GTO thyristors, and IGBT transistors) in the 1990s propelled VSI technology to the forefront. These days, most new electric drive installations are VSI drives. Mult winding multicell, modular multilevel converters, 3-level neutral point clamped inverters, 5-level neutral point clamped inverters, and M2Cs are the most popular in the medium voltage range. The 5-L NPC inverter, which is further characterized as a topology, is really composed of 3-L-NPC modules connected in an H-bridge configuration. The rated output voltage may be adjusted between
5.5 kV and 7.2 kV, making it a "6.6 kV class" variable frequency drive. The liquid-cooled version is available in single-unit power capacities ranging from around 6 MW to over 40 MW. Multiple units may be paralleled to produce more power.
In most cases, the maximum allowable output frequency is 66 Hz. Field references [26] up to 260 Hz and technically feasible up to 400 Hz are all readily attainable in a high-speed setup, allowing for an output frequency of more than 250 Hz. True high-speed applications usually include cage induction machines and active magnetic bearings (AMB), and VSI kind of converters may power both synchronous and induction machines.
-
-
OVERVIEW OF HARMONICS IMPACTS ON ELECTRICAL MOTORS
The purpose of this thesis is to examine and address harmonics impact on induction motor winding insulation due to variable frequency drive in industrial application and improve power quality. While analysing the model and compare the input current of VFDs (Variable Frequency Drives) with and without an active power filter, current distortion at linear and non-linear load, measurement of harmonic mitigation at different harmonic current, as well as enhancing the overall system efficiency and reliability. In this paper, information relating to facets of harmonics that include causes, implications, and possible approaches to dealing with the vice are discussed. In this work, our main target will be to perform a comprehensive study of the impact of harmonics and try to mitigate the results.
Insulation breakdown is the result of voltage pulse interaction between VFD and motor stator coil, Inductive reactance property of motor coil causes coils to react to a change in the current by producing voltage which oppose current flow, this is called back- voltage.
Fig 4.1 Induction Motor current lags voltage Fig 4.2 Overshoot voltage and Oscillation
If sine wave voltage is applied to the motor, the change in current flow is gradual and reaction is also gradual, in this case current lags the voltage due the inductive reactance.
When motor is supplied power through variable frequency drives, fast rising voltage pulse is applied to the otor stator winding coils, the back voltage produced by the motor coils can develop voltage to overshoot the voltage supplied by the VFD. This overshoot interacts with the motor inductance, motor cable inductance, capacitance of the motor cable. Motor cause the voltage to oscillate and the peak voltage of the oscillation is the serious concern, if this voltage increases and it is above the insulation value of motor winding insulation withstanding capability, it can break motor winding insulation and cause winding short circuit.
-
Current Harmonics
The current in an AC power system fluctuates smoothly in analog with sinusoidal function at a frequency of 50 or 60 Hz. Linear loads are voltages and currents that are in phase with each other as well as having the same frequency. The waveform problems and, in general, resonance is an outcome of nonlinear loads that distort the waveform while creating a current harmonic. Third, harmonics are the third multiple of the fundamental frequency, and harmonics are positive integer multiples of the fundamental frequency in power systems. Commonplace office equipment like printers, battery chargers, compact fluorescent lights, and computers are examples of non-linear loads. Non-linear loads also include variable frequency drives (VFDs), semiconductor devices, IGBTs, transistors and rectifiers [26].
-
Voltage Harmonics
Vol. 13 Issue 9, September 2024
The most common source of voltage harmonics is harmonics in the current. Because of the source's impedance, current harmonics affected the voltage it supplied. Voltage harmonics are much less than current harmonics when the source impedance is small. Therefore, while the fundamental frequency is a good approximation for the voltage waveform, current harmonics have little influence on the actual power sent to the load. This is because current harmonics have very little impact on actual power consumption. However, current harmonics start to affect the actual power when higher voltage harmonics are taken into account. There can be no line voltages or currents in balanced three-phase power systems with harmonics with frequencies that are integer multiples of the third harmonic's frequency, according to Kirchhoff's voltage law. On the other hand, neutral currents could be augmented by triple harmonics in four-wire systems [26].
-
-
HIGH-SPEED ELECTRICAL MACHINES
Among the machine types recommended for high-speed operations in literature and subsequently used by industry, the one chosen will largely rely on the details of the job at hand [27]. When it comes to traditional machines, those that can handle high speeds include induction (IM), switching reluctance (SR), and surface-mounted permanent magnet synchronous machines (SPMSM). Due to the resilience of these constructions, the first topology may be readily used for high-speed applications in both laminated and solid rotor variants even more so, demagnetization is not an issue since the spinning component does not include any permanent magnets. Because retaining sleeves is unnecessary with the less complicated rotor design, the approach is more economical. Low power factor and excessive rotor losses contribute to inefficient operation. Therefore, this machine type could be better for uses that need a lot of power and efficiency. The absence of active components and a rotor containment mechanism makes SR machines well-suited for high-speed applications, and the rotor design is both simple and sturdy. High fault tolerance and resistance to extreme conditions are two of the topology's main benefits. However, the high magnetizing current has a negative impact on both the power factor and efficiency.
What's more, when the speed is high, the windage losses are amplified by the double salient arrangement, further reducing efficiency. Power factor, torque density, and efficiency are three metrics where SPMSMs excel. Using materials with a high energy density, such as rare-earth permanent magnets, improves efficiency, power density, and power factor while removing the requirement for magnetizing current. At high speed, the enormous forces acting on the rotor are the greatest obstacle for this machine structure. Consequently, a retention system that can ensure the rotor's integrity must be designed and manufactured [28]. To keep the machine's various parts from overheating, it's important to estimate the extra high-frequency losses that the laminated iron, magnets, and retaining sleeve will experience carefully [29].
Several criteria were considered while designing the machine to ensure optimal performance; specifically, power factor, efficiency, and power density were given weight, an ideal distribution of losses has been determined by considering various slot/pole and winding configurations to get the highest performance, all while meeting the necessary limitations and criteria. Meeting the criteria above, particularly in terms of loss distribution, led to the selection of a distributed winding structure with 24 slots and 4 poles. As a result, it is possible to create a machine with iron stator and rotor losses as the primary heat transfer medium, achieving a medium between the two extremes and making thermal management a breeze. A mechanical trade-off analysis is required the rotor design in order to ascertain the material and thickness of the retaining sleeves, among other attributes. The working maximum speed is greater than the first critical frequency, which is deliberate from a rotor-dynamics perspective. Develop a quasi-Halbach array of samarium-cobalt magnets to increase the power density by increasing the fundamental flux density at the airgap, and to make the rotor assembly more manufacturable compared to a complete Halbach structure. The goal of minimizing iron losses led to the selection of a 0.17 mm lamination material thickness. Machine design, which was fine-tuned to operate with low iron flux densities, is another contributor to the decrease in iron losses. After the rated voltage has been used to determine the number of turns in series per phase, the number of strands that make up each conductor is specified with the goal of lowering AC copper losses at both the strand and bundle levels. A single-channel water jacket encircling the stator laminations and a coolant flow rate of 15 l/m make up the cooling system, which was engineered to keep the maximum winding temperature increase within the bounds of the chosen insulation class. Reducing rotor lossesthe eddy current losses caused by harmonic fields that rotate at different speedswas an explicit design objective to be considered.
-
EFFECT OF HARMONIC DISTORTION
When compared to mechanical and pneumatic systems, electrical motors (EMs) need to have their performance enhanced via sophisticated engineering and design for use in commercial and industrial settings. When it comes to maintaining high-efficiency operations while lowering operating costs and energy usage, variable frequency drive (VFD) supplied EMs are crucial [30]. On the other hand, using a VFD at low speed for an extended period may drastically reduce EM performance and even cause the stator windings' insulation to break prematurely [31]. In order to determine the state of the stator insulation in an Ems, a widely used diagnostic tool is the partial discharges (PD) approach. Laboratory testing typically presumes a test voltage that is a pure sine wave. However, the sinusoidal test voltage waveform has harmonics when EMs run on VFD power. It is more noticeable in the test voltage waveform when the VFD is operating at low speeds due to harmonic distortion. A more severe PD in the stator insulation of EMs may be brought about by the waveform of the test voltage by harmonic content. Any phenomenon that affects the lack of harmonic concentration in the measured test voltage waveform might lead to the receipt of only false reports on the conditon of PD, which, in actual fact, would not be conducive to an accurate measurement of when the equipment is in critical need of maintenance. Hence, proper knowledge of how a distorted voltage waveform influences PD diagnostics in VFD-fed EMs is vital in giving a better assessment of the levels of deterioration in the stator insulation.
Some researchers have devoted their efforts to identifying how the Electromagnetic fields generated by power electronic drives affect stator insulation durability. For instance, the issues related to reliability and power quality (PQ) of EM applications fed from
VFD sources were also described in the work [32]. Research by Refs found that in inverter-fed EMs, insulation fails prematurely due to PD occurrence in the stator winding. In addition, the authors put up a method for determining the stator insulation lifespan under PD conditions. The time-domain and frequency-domain PD properties affected by the repeating impulse voltage in inverter- driven EMs were investigated in Refs [33]. In addition, they have investigated the insulating lifespan behaviour and PD phase distribution. The impact of test voltage harmonics on PD pattern analysis was examined in Ref [34]. Research comparing the effects of a sine wave test voltage and a multilevel inverter voltage on PD behaviour and insulation deterioration in twisted wire pairs was described in reference [35]. we learn that epoxy resin's insulating properties are affected by harmonic pollution in the test voltage. In addition, the authors have looked into the fact that the insulation's lifespan was ultimately lowered as a result of electric tree formation caused by the distorted voltage waveform.
In conclusion, prior research has looked at how certain harmonic components of the voltage waveform affect PD activity. Unfortunately, no study has yet shown how PD behaviour is affected by the real harmonic distortion that occurs in the applied voltage waveform when VFD-fed EMs are operated at variable speed (VS). Also, using experimental data, we need to determine how likely it is that VFD-fed EMs will exhibit PD activity as a result of voltage harmonic distortion.
The motor power supplied through pulse with modulation VFD overshoot the dc bus voltage which generated the pulse, so the motor should have the sufficient insulation to ensure motor reliable operation. The peak voltage can raise up to two times of the dc bus voltage of VFD. The VFD compatible motor winding insulation should withstand voltage as provided in the following calculation.
1.1*2* 2 * V rated
1.1 – Safety factor
2- Max voltage overshoot.
2 * V rated – DC bus voltage.
Motor peak voltage does not correlate with insulation class of motor, Class F or H class insulation is for temperature withstanding capability of insulation, it is not the ability to withstand peak voltage. It is important to identify the motor peak voltage at motor terminal and specify the same in motor technical specification for reliable operation.
There are some factors which determines the amount of overshoot, if the peak voltage at the motor is kept under below 1000 V, general purpose motor can be used, otherwise special insulation motors shall be considered.
VFDs use high PWM pulse switching frequencies are required to operate at high switching frequency, those pulses combined with impedance of motor and cable can produce repetitive over voltage in the motor terminals. These overshoots cause damage to the winding interturn insulation, and the severity of the effect is depending on various factors like rise time of voltage pulse, cable length, time difference between pulses, switching frequency and motor operation.
If VFD is designed to operate at lower switching frequency, PWM pulses are produced with longer rise time and value of dv/dt is lower, so the peak voltage motor is lower [36].
Fig 6.1 PWM with high dv/dt Fig 6.2 PWM with low dv/dt
PWM with high dv/dt result larger overshoot voltage PWM with low dv/dt result lesser overshoot voltage Length of cable between motor and VFD drive influence the peak voltage at motor terminal, mostly the calculation of dv/dt and rise time is considered at VFD terminal point, rise time definition specified in NEMA and IEC is different, hence often misunderstanding happen when calculating voltage gradient ( dv/dt ). The motor high frequency impedance is higher than cable impedance, so the excessive cable length increases the overshoot at motor terminals.
Fig 6.3 3-meter cable length causes low peak voltage. Fig 6.4 70- meter cable length causes higher peak voltage
-
MODEL AND SIMULATION USING AHF FOR HARMONIC MITIGATION
Active Power Filter (AHF) provides an active compensation result using power electronics technology. Compared with conventional passive harmonic filter compensation solutions such as inductor and capacitor banks, an active compensation method support to improve the reliability and quality of the power distribution system.
AHF is connected in parallel with non-linear loads and uses one set of current transformers (CT) to measure the load current. It calculates each order harmonic current by algorithms as defined in the microchips of controller, and then produce a compensating current with the same amplitude but opposite phase angles to the detected harmonic current, which cancels out the original load harmonics.
The AHF not only eliminates harmonic current from the load side, but it also mitigates harmonic voltage caused by harmonic currents. The AHF system can also improve power factor (PF) and correct load imbalances in the power system.
Fig 7.1. AHF Schematic diagram circuit with linear and nonlinear load
Fig 7.2 MATLAB Model with Active Power filter and Linear and Non-Liner loads
Figure 7.3 a Source current without APF Figure 7.3 b Source voltage without APF
Figure 7.4 a Linear load current Figure 7.4 b Non-Linear load current
Figure 7.5 a Source current with APF Figure 7.5 b Source voltage with APF
Active Power filter model developed using MATLAB (2023a) covering power source from transformer and linear and non-liner load with switching devices. Source current and voltage distortions measured and after using APF, distortions found mitigated and waveforms quality improved. Current distortions observed with linear load and non linear load, more distortions observed in non- linear load.
AHF can perfectly mitigate harmonic current, and suppress harmonic voltage caused by the harmonic current, when the AHF capacity is sufficient and background harmonic voltage is low, the AHF ensures excellent compensation performance at full load condition, below 200 Amps AHF analysed with VFD load at 100 %, 75 % and 50 % load condition, IRF is the actual harmonic current at various load condition of VFD, SHD is source harmonic distortion value, harmonic mitigation at source observed that performance of AHF harmonic filtering is better when operated near to AHF rated current capacity.
Fig 7.6 a VFD LOAD CURRENT Fig 7.6 b SOURCE HARMONIC DISTORITION 5.1 %
at 93 % AHF RATING (186.1 A)
Published by : http://www.ijert.org
International Journal of Engineering Research & Technology (IJERT)
ISSN: 2278-0181
Vol. 13 Issue 9, September 2024
Fig 7.7 a Source Harmonic distortion 7.8% Fig 7.7 b Source Harmonic distortion -13.6 %
IRF VS SHD
200
150
100
50
0
1
2
3
IRF
SHD
at 76.5 % AHF rating ( 153 A) at 50 % AHF ration ( 99.2 A)
Figure 7.8 AHF current Vs Source Harmonic Distortion
Fig 7.9 a Voltage and Current wavforms 7.9 b Voltage and Current waveforms Under AHF OFF condition Under AHF ON condition,
200 A AHF Filter actual test result at various harmonic current loads illustrated above.
-
CONCLUSION
Induction motors have seen significant improvements in energy efficiencyand process control because of Variable Frequency Drives (VFDs), which change the way the motors operate. However, VFD harmonics pose a significant danger to motor winding insulation because they may increase voltage stress, accelerate insulation degradation, and produce resonance, all of which shorten a motor's lifespan.
To address such unintended consequences, a combination of methods is necessary. Selecting the correct motors with inverter duty insulation is a good starting point for achieving an effective inverter installation process. VFD dv/dt at terminal value, overshoot calculated value at motor terminal to be determined before motor insulation voltage. Motor manufacturers have different dv/dt value design for 415 V LT motors such as 1.6 kV/ s, 2.2 kV/ s., 3.6 kV/ s. So appropriate calculation and selection of dv/dt value plays a vital role. It is observed from the simulated results from MATLAB model that impact of non-linear load harmonic is more severe in source current and voltage distortion and suitable rating selection of active power filter can improve power quality. Reduction of overshoot voltage is possible through output dv/dt filter and sine wave filters. These output filters may significantly
decrease the harmonic content and related dv/dt values in the voltage waveforms. Other metrics to minimize electromagnetic interference and high-frequency noise include maintaining insulated cables and proper grounding.
Some of the latest technologies in VFDs include multi-pulse converters and advancing front-end architectures which help to control the harmonic current distortion in order to enhance overall system performances. It also makes it easier to undertake constant monitoring and maintenance processes to identify a breakdown in insulation when it occurs. Promising results have also been attained in terms of energy savings, as well as control of induction motors through the use of VFDs that alter the usage of these motors.
To counter such adverse effects, more than one approach is required since one solution will not solve the problem altogether. The first consideration is selecting a motor with the proper rating of inverter duty insulation based on overshoot voltage stress on winding interturn insulation, because dv/dt value specified by manufacturer is a at VFD output terminal, impact on dv/dt at motor terminal to be identified for suitable insulation selection of motor winding. Two output filters include a sine wave filter or dV/dt filter, both of which can significantly diminish harmonic content and accompanying voltage leaps. Other mitigation measures in fighting electromagnetic interference and high-frequency noise include proper wiring with insulated wires and good grounding.
Implementing advanced forms of VFD technologies like multi-pulse converters with passive harmonic filters, active harmonic front-end drive designs, Active harmonic filter with proper current rating selection to mitigate harmonic effect in point of common common coupling and so on helps in better control of the harmonic current distortions as well as enhanced system performances. While selecting AHF, harmonic spectrum range of VFD drives to be obtained from VFD manufacturer to ensure that AHF design is suitable to cover complete harmonic distorting range. Management procedures also assist in frequent monitoring, and this makes it easier to identify insulation breakdown once it occurs.
-
REFERENCES
2007, 22, 23352348. [Google Scholar] [CrossRef] [4]. Monteiro, H.L.; Camponogara, Â.; Ribeiro, M.V.; Duque, C.A.; Poor, H.V. A DFT-based method for estimating interharmonics in wind power generation. IET Smart Grid 2022, 5, 332346. [Google Scholar] [CrossRef] [5]. Hou, J.; Ding, G.; Wu, C.; Pan, Z.; Wang, J. An Interharmonic Suppression Control Scheme in PV System Based on DC-Link Voltage Perturbation Reduction. In Proceedings of the 2021 IEEE 5th Conference on Energy Internet and Energy System Integration (EI2), Taiyuan, China, 2224 October 2021; pp. 26952700. [Google Scholar] [6]. Mao, M.; Xu, Z.; Li, J.; Li, H. A Phase-shifting DC-link Voltage Control Strategy for Parallel Inverters to Suppress Interharmonics in PV Systems.
IEEE J. Emerg. Sel. Top. Power Electron. 2023, 11, 31633172. [Google Scholar] [CrossRef] [7]. Feola, L.; Langella, R.; Papi, I.; Testa, A. Selective interharmonic compensation to improve statcom performance for light flicker mitigation. IEEE Trans. Power Deliv. 2018, 33, 24422451. [Google Scholar] [CrossRef] [8]. Donolo, P.; Bossio, G.; De Angelo, C.; GarcÃa, G.; Donolo, M. Voltage unbalance and harmonic distortion effects on induction motor power, torque and vibrations. Electr. Power Syst. Res. 2016, 140, 866873. [Google Scholar] [CrossRef] [9]. Riaz, M.T.; Afzal, M.M.; Aaqib, S.M.; Ali, H. Analysis and evaluating the effect of harmonic distortion levels in industry. In Proceedings of the 2021 4th International Conference on Energy Conservation and Efficiency (ICECE), Lahore, Pakistan, 1617 March 2021; pp. 17. [Google Scholar] [10]. Ghaseminezhad, M.; Doroudi, A.; Hosseinian, S.H.; Jalilian, A. Analysis of voltage fluctuation impact on induction motors by an innovative equivalent circuit considering the speed changes. IET Gener. Transm. Distrib. 2017, 11, 512519. [Google Scholar] [CrossRef] [11]. Gnaciski, P.; Pepliski, M.; Hallmann, D. Thermal transients of induction machine under changeable voltage unbalance. In Proceedings of the 2018 XIII International Conference on Electrical Machines (ICEM), Alexandroupoli, Greece, 36 September 2018; pp. 13381343. [Google Scholar] [12]. Ghaseminezhad, M.; Doroudi, A.; Hosseinian, S.H.; Jalilian, A. An investigation of induction motor saturation under voltage fluctuation conditions. J. Magn. 2017, 22, 306314. [Google Scholar] [CrossRef] [13]. Ghaseminezhad, M.; Doroudi, A.; Hosseinian, S.H.; Jalilian, A. Investigation of increased ohmic and core losses in induction motors under voltage fluctuation conditions. Iran. J. Sci. Technol. Trans. Electr. Eng. 2019, 43, 373382. [Google Scholar] [CrossRef] [14]. Gnaciski, P.; Pepliski, M.; Murawski, L.; Szeleziski, A. Vibration of induction machine supplied with voltage containing subharmonics and interharmonics. IEEE Trans. Energy Convers. 2019, 34, 19281937. [Google Scholar] [CrossRef] [15]. Gnaciski, P.; Hallmann, D.; Muc, A.; Klimczak, P.; Pepliski, M. Induction Motor Supplied with Voltage Containing Symmetrical Subharmonics and Interharmonics. Energies 2022, 15, 7712. [Google Scholar] [CrossRef] [16]. Gnaciski, P.; Klimczak, P. High-Power induction motors supplied with voltage containing subharmonics. Energies 2020, 13, 5894. [Google Scholar] [CrossRef] [17]. Gnaciski, P.; Hallmann, D.; Klimczak, P.; Muc, A.; Pepliski, M. Effects of voltage interharmonics on cage induction motors. Energies 2021, 14, 1218. [Google Scholar] [CrossRef] [18]. Gonzalez-Abreu, A.D.; Osornio-Rios, R.A.; Jaen-Cuellar, A.Y.; Delgado-Prieto, M.; Antonino-Daviu, J.A.; Karlis, A. Advances in power quality analysis techniques for electrical machines and drives: A review. Energies 2022, 15, 1909. [Google Scholar] [CrossRef] [19]. Riyaz, A.; Iqbal, A.; Moinoddin, S.; MoinAhmed, S.K.; Abu-Rub, H. Comparative performance analysis of Thyristor and IGBT based induction motor soft starters. Int. J. Eng. Sci. Technol. 2009, 1, 90105. [Google Schola] [CrossRef] [20]. De Rosa, F.; Langella, R.; Sollazzo, A.; Testa, A. On the interharmonic components generated by adjustable speed drives. IEEE Trans. Power Deliv.
2005, 20, 25352543. [Google Scholar] [CrossRef] [21]. Delgado-Arredondo, P.A.; Romero-Troncoso, R.J.; Duque-Pérez, O.; Morinigo-Sotelo, D.; Osornio-Rios, R.A. Vibration, Acoustic Noise Generation and Power Quality in Inverter-Fed Induction Motors. In Proceedings of the 2019 IEEE 12th International Symposium on Diagnostics for Electrical Machines, Power Electronics and Drives (SDEMPED), Toulouse, France, 2730 August 2019; pp. 412418. [Google Scholar] [22]. Bruha, M. Importance of control engineering to minimize torsional vibration in variable speed drive systems. In Proceedings of the 2016 Petroleum and Chemical Industry Conference Europe (PCIC Europe), Berlin, Germany, 1416 June 2016; pp. 18. [Google Scholar] [23]. Mishra, S.; Palazzolo, A.B.; Han, X.; Li, Y.; Kulhanek, C. Torsional vibrations in open loop volts hertz variable frequency drive induction motor driven mechanical systems. In Proceedings of the 2020 IEEE Texas Power and Energy Conference (TPEC), College Station, TX, USA, 67 February 2020;
pp. 16. [Google Scholar] [24]. Gnaciski, P.; Hallmann, D.; Pepliski, M.; Jankowski, P. The effects of voltage subharmonics on cage induction machine. Int. J. Electr. Power Energy Syst. 2019, 111, 125131. [Google Scholar] [CrossRef] [25]. Ahrens, U. Bikle, R. Gottkehaskamp, H. Prenner, M. Electrical Design of High-Speed Induction Motors of up to 15 MW and 20000 rpm, IEE Conf. on Power Electronics, Machines and Drives, 487, 381386 (2002)
[26]. Neidhöfer, A.G. Troedson, G.J. Large converterfed synchronous motors for high speeds and adjustable speed operation: Design features and experience, IEEE Trans. on Energy Conversion 14, 3 (September 1999) [27]. Bartolo, H. Zhang, D. Gerada, L. D. Lillo, J. B. and C. Gerada, High speed electrical generators, application, materials and design, in Proc. IEEEWorkshop Elect. Mach. Des., Control Diagnosis, Mar. 2013, pp. 4759.
[28]. Binder, T. Schneider, A. and M. Klohr, Fixation of buried and surfacemounted magnets in high-speed permanent-magnet synchronous machines,IEEE Trans. Ind. Appl., vol. 42, no. 4, pp. 10311037, Jul./Aug. 2006
[29]. Jumayev, M. Merdzan, K. O. Boynov, J. J. H. Paulides, J. Pyrhönen, S. and E. A. Lomonova, The effect of PWM on rotor eddy-current losses in high-speed permanent magnet machines, IEEE Trans. Magn., vol. 51, no. 11, Nov. 2015, Art. no. 8109204
[30]. Stone, H. G. Sedding, G. C. and C. Chan, "Experience With Online Partial-Discharge Measurement in High-Voltage Inverter-Fed Motors," IEEE Transactions on Industry Applications, vol. 54, pp. 866-872, 2018. [31]. Li, M. Liu, J. Lau, Y. and B. Zhang, "A novel method to determine the motor efficiency under variable speed operations and partial load conditions,"Applied Energy, vol. 144, pp. 234-240, 2015
[32]. de Almeida, F. J. Ferreira, A. T. and D. Both, "Technical and economical considerations in the application of variable-speed drives with electric motor systems," IEEE Transactions on Industry Applications, vol. 41, pp. 188-199, 2005 [33]. Madonna, P. Giangrande, G. Migliazza, G. Buticchi, V. and M. Galea, "A Time-Saving Approach for the Thermal Lifetime Evaluation of Low-Voltage Electrical Machines," IEEE Transactions on Industrial Electronics, vol. 67, pp. 9195-9205, 2019. [34]. Wang, G. C. Montanari, P. and A. Cavallini, "Partial discharge phenomenology and induced aging behavior in rotating machines controlled by power electronics," IEEE Transactions on Industrial Electronics, vol. 61, pp. 7105-7112, 2014. [35]. Bahadoorsingh, S. and S. Rowland, "Investigating the impact of harmonics on the breakdown of epoxy resin through electrical tree growth," IEEE Transactions on Dielectrics and Electrical Insulation, vol. 17, pp. 1576-1584, 2010. [36]. Variable Frequency Drives and Motor Insulation Stress by Ken Fonstad, HVAC Application Engineering Manager August 3, 2011.