
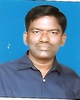
- Open Access
- Authors : T P Sasidharan , D. P. Girish
- Paper ID : IJERTV10IS030227
- Volume & Issue : Volume 10, Issue 03 (March 2021)
- Published (First Online): 07-04-2021
- ISSN (Online) : 2278-0181
- Publisher Name : IJERT
- License:
This work is licensed under a Creative Commons Attribution 4.0 International License
Implementation of Lean Tools in Aircraft Industries: A Review
-
P. Sasidharan
1Research Scholar, Department of Mechanical Engineering,
Government Engineering College, Ramanagar, Karnataka India
-
P. Girish
2Professor,
Department of Mechanical Engineering, Government Engineering College, Ramanagar, Karnataka India
Abstract:- In order to contend with many small as well as medium manufacturers the lean manufacturing technique provides a brand new approach. Some of the aspects which are concerned with processdurations, quality as well as client responsiveness might witness a remarkable improvement in results. It's considered to be beyond a lot of techniques and tools plus by several manufacturing organizations it has been generally received. In the current scenario, it's been a trend in the modern world wherein all representatives inevitably look for approaches to enhance forms. Within the manufacturing process in order to achieve the end of waste lean is an efficient technique. In workloads because of unevenness and overburden the lean considers squandering. Lean creates more value for clients with very few resources. Essentially, lean methods making more incentive for clients with fewer assets. Although for aerospace manufacturing companies and for the automotive industry the lean manufacturing was literally developed but have discovered that these concepts could be used for the industry which is high-precision in order to make a major difference in the efficiency of the production. The lean concepts have been reviewed in this paper as well as for lean implementation summarizes the lean cycle, lean production model as well as practice to enhance the determination in the aerospace sector.
Keywords: Lean Manufacturing, Aviation Industry, Lean Tools, Lean Concept, Lean Cycle.
-
INTRODUCTION
-
-
In the production process, a strategy of lean manufacturing is utilized to lower the waste, the consumption of the product by the form view of a customer, and moreover, the "value" is some activity that the client will be ready to spend for. As a result, the supreme goal of lean companies is to provide the best value to the customer through an ideal value development process with zero waste. A set of goals of eliminating activities in this what the lean manufacturing is based on, plus it doesn't maximize any sort of values to the production system particularly those regarding with processes, elapsed time, methods, people and movements as well as places. In large organizations it's been found that enactment of lean manufacturing is accomplished favorably but it is extremely much less recorded proofs of the implementation of its medium as well as small sized enterprises (SME), to handle competitors in this particular business community and in this way the lean implementation is important with increasing need for superior quality products[1- 2].
Compared to the mass production the lean manufacturing methodology varies considerably, and particularly in the terminology of customer satisfaction, quality and volume the lean production has accomplished a remarkable success in the twentieth century's final decades. Some of the aspects like reduction in cost and cut in development time can be accomplished in the industry of automobile by the techniques of lean manufacturing and also create a much better solution that much more exactly meets buyer needs. All those businesses with effectively implemented lean generation, mainly owned and handled by the 'Japanese, in a competitive market they have done quite well, at the same time those who have followed conventional mass production techniques had a competing problem. On the aerospace defense industry, the lean manufacturing techniques plays a vital impact because it has a potential advantage like affordability, increased quality, flexibility. Nevertheless, the aerospace defense business is just currently starting to completely implement these brand new strategies.
The scope of military aircraft, civil aircraft as well as aircraft maintenance has been covered by the aircraft industry. Primarily the aerospace production community maintain the technicalintensive tasks as well as excessive value added in home, like flying tests, marketing, final assembly and design etc. And blow away the labor-intensive and low value-added production movements to aerospace manufacturing suppliers such as aero-structure assembly as well as detail part fabrication etc. The universal aerospace supply chain is then built and systemized. Customers are provided with the software (NC program, design, logistics, and service etc.) and hardware (component, AOG (aircraft on the ground) parts, aircraft, spare, etc.) by aerospace manufacturing vendors. As a result of the presenting the merchandise by aerospace manufacturing suppliers to meet the needs of primary aerospace manufacturing firms, as a consequence, customer loyalty is an absolute prerequisite for manufacturers to maintain a stable and long-term relationship., and sufficient business from primary aerospace manufacturing [3-5].
In aircraft companies, the cycle time that is time required to accomplish a job completely is significantly imperative as it determines the efficiency levels of an organization. It also determines the time frame required by one organization in comparison to the other to accomplish same tasks thus making it possible to comparatively analyse organizational performance with other in the league and take measures to overcome inefficiencies if any[6-8].
Though extensive research has been undertaken in the sphere of lean manufacturing, but yet there dearth of studies that focus on aircraft industry. Aircraft is one of the most critical industries for an industry due to its expansive scale of operations as
well as revenue earned by the same. Companies operating in this aircraft industry either indulging in manufacturing of parts or assembly of the same or delivering air transportation services need to abide by a number of steps for successfully accomplishing their tasks thus fulfilling objectives. In such a scenario keeping a track of cycle time in order to optimize the same is critically essential which can provide organizations with competitive edge. The goal of this particular paper is to review the lean ideas and for lean implementation summarize the lean cycle, lean production model and practice to enhance the competitiveness in the aerospace manufacturing sector.
-
Basics of Lean Manufacturing
Lean Manufacturing, also known as lean business or lean production, is a production method that considers resource investment for each and every target, ranging from the creation of value for the end user to the reduction of waste. The value is defined as any process or operation that an individual is willing to pay for. The consumer who consumes a service or product and works according to their point of view. [9]. The customer's worth is recognized by a lean business as well as concentrates on its major processes to continuously increase. The main objective is lending best value to the buyer through an ideal value process of creation which has null waste [10]. The lean definition is versatile. It usually associates to those finest practices and processes, in which increases resources as well as produce the most effective merchandise in the speedy way and at probably the cheaper cost. It's a guardian for zero defects, continuous improvement, Total quality management, and most of additional terms that we have utilized as well as heard describing the things irst time rightly, as well as also performing it correctly at all time. It's not a quick transition neither could it be an extension of regular techniques or thinking. Actually, it's a groundbreaking process of thought which necessitates abandonment of several old models. Just to imagine that lean is switching from thinking from internally concentrated to thinking about externally focused [11]. The adjustments to the particular customer's requirements is the key of effective LEAN implementation. Consider a low-volume, high-mix producer attempting to implement lean Assume they produce highly complex electro-mechanical assemblies every other day, with demand for around one unit every other day across all varieties. On lean manufacturing they may read several books as well as make an effort to enact the principles as well as tools in the organization. They may attempt to produce one piece flow cells and incorrectly determine they perform task just only for increased volume and low-mix situations. This is due to they may have read they've computing takt time, finished products are taken out of the cellular every thirty to sixty minutes, design the cellular so that areas are shipped to the cell every thirty to sixty minutes, etc. These lean essentials are definitely not needing but for a high-volume producer they are particular uses of the idea of one-piece flow. As presented, these basics will not serve for a low-volume manufacturer. For instance, they will not have to deliver components to the cellular every thirty to sixty minutes, in case they have to produce one finished device each day. In reality, they may think about kitting areas (or at least the components that aren't common to the product of each) as well as delivering those parts to the cell on a regular basis based on customer requirements [12]. According to Jones and Womack, lean thinking will be the antidote to waste. In the most effective sequence, It helps you to specify value aa well as sequence value-creating activities, with no interruption perform these activities anytime somebody demand them, and does them increasingly effectively [13]. While minimizing waste, the customer value is to be maximized and this is mainly the core idea. Just simply, with fewer resources the lean suggests producing much more value for customer. For the general success of LEAN taking little but sustainable steps is likewise essential.
-
Five LEAN principles [5-10]
-
Identify the importance of
-
Indicating value from the viewpoint of the buyer
-
Make the value creating steps flow
-
Produce on a pull principle
-
Eliminate defects
-
-
Seven types of waster[10-14]
Reducing waste is one of the most important ways to maximize a company's profitability. Processes either add waste or add value on the production of a very good or service. It's quite essential to know precisely what waste is and exactly where it exits in order to eliminate waste. While products between factories significantly differ, the conventional wastes seen in environments of manufacturing are alike. Each waste has a strategy to eliminate or reduce its impact on a business, therefore improving general quality and performance. The term' Muda' is a standard Japanese term for a workout which is careless which doesn't optimize worth or maybe is inadequate, etymologically trivia+ none or maybe not handy in practice or others. In the Toyota Production System (TPS) it is also a key concept and it is among the 3 kinds of waste (muda, mura, muri) it recognizes. Waste reduction is an important way to increase profitability. A process requires energy, and waste occurs when more resources are used than are necessary to produce the goods or provide the service that the customer needs. The TPS's tools and behaviors increase awareness while also offering entirely new perspectives on finding waste as well as, as a result, untapped waste- reduction opportunities.
By Taiichi Ohno the 7 perilous wastes have been recognized together with the Toyotamanufacturing System. The normal categorization of the sorts of waste is:
Transport
To conduct the processing, moving products are not truly required.
Whenever a product is moved it appears to get into trouble of becoming harmed, lost, delayed, etc. along with being a cost for no additional value. Especially to the product, the transportation doesn't make any transformation when the consumer really should spend on. Among processes, the transporting product is said to be an attack of cost wherein to the product it doesn't maximize any value. It's said to be an opportunity for quality to decline when excessive movement and handling cause damage. To supply the materials the material handlers must be utilized, that will lead to cause the organization in terms of expense and moreover it doesn't maximize the value of customer. Transportation can be difficult to mitigate due to the perceived costs of bringing machinery and processes closer together. Additionally, it's generally difficult to make out that which processes must be alongside one another. Visualization is made much easier by mapping product flows.
Inventory
Entire components, finished items as well as work in progress which aren't been processed. Inventory, whether it is work-in- progress (WIP) or maybe finished goods, whether in the type of raw materials, signifies a capital expenditure that hasn't yet generated money for the customer or even for the producer. It's found to be a waste when all of these 3 things not been actively processed to maximize value. Waiting as well as overproduction are the immediate consequences of Work in Progress (WIP). On the plant floor, the excessive inventory tends to remain unseen that should be determined as well as solved in an effort to boost working efficiency. It takes up floor space, inhibits communication, and prevents the detection of problems, as well as lead times are increased as the consequences of excessive inventory.
Between work centers by accomplishing a seamless flow, numerous companies are equipped toenhance support of customer as well as slice inventories and costs related to them.
Motion
To conduct the processing, it is necessary to even walk much more or equipment moving or people. The motion refers to the producer, equipment, or worker as compared to transportation. This has greater importance to injury, safety as well as wear. Additionally, it involves the stagnant expenses and assets that obtained in the production. This waste is related to ergonomics, as well as it can be seen in all instances of stretching, walking, stretching, lifting, bending and reaching. These're additionally safety and health issues, which in the current belligerent society are getting to be much more of a concern for organizations. Tasks with too much movement must be examined as well as redesigned for enhancement with the participation of plant personnel.
Waiting
When goods aren't in transit or being processed, they're sitting around waiting. In traditional systems, a significant portion of an individual product's life is spent waiting to be worked on. When products are not moving or being handled, then the waste of waiting occurs. Traditionally, over 99 percent of a product's life is spent waiting to be manufactured in batch- and-queue manufacturing. A large portion of a product's lead time is spent waiting for the next operation; this is generally due to the production runs are too long, the material flow is poor as well as the ranges between work centers are extremely brilliant. The Theory of Constraints (Goldratt) has also stated that one hour spent in a congested process is only one hour wasted in total factory production, that can't ever be recovered. Connecting together the processes therefore one feeds straightly to the following that can considerably decrease waiting.
Overproduction
The Production leading in front of demand.
The overflow of output occurs when more goods are produced than are needed by consumers at the time. One common practice that contributes to this muda' is large batch manufacturing, as market demand often shifts over long periods of time, necessitating large batches. The production which is done excessively is deemed the worst muda since it generates or hides all of the others. Excessive inventory occurs by overproduction, which in turn demands the resources expenditure on preservation and storage space, and the state of being active that don't profit the customer. To put it simply, a product manufacturing before its actually required is overproduction. Overproduction is extremely expensive to a production plant since it interdicts the substances smooth flow as well as also devalue productivity and quality. Due to each product is created only as it's required so the Toyota Production System is also referred to as Just in Time (JIT). As "Just found Case" the Overproduction manufacturing is described. It generates extreme lead times that leads in increased storage expenses, and also causes it to be hard to identify defects. Switching off the tap is the simple strategy to overproduction; this calls for a great deal of braveness because the troubles which overproduction is concealing is exposed. The idea is scheduling as well as create just what can be instantly shipped/sold as well as improvise machine set-up capability/changeover.
Over Processing
The result of product design or poor tool generating activity. Sometime over-processing occurs much more job is completed on a slice compared to what's needed by the buyer. It involves utilizing tools that happen to be much more accurate, complex, or costly than unconditionally necessary. Using a sledgehammer to crack a nut, which is frequently stated, numerous businesses
work with costly superior precision equipments where easier equipment will be enough. Since the preceding or subsequent operations are separated by a large distance, this usually leads to a terrible plant layout. They promote high asset usage in order to recover the high cost of this equipment). 'Toyota' is well-known for integrating low-cost automation with immaculately operated, often older equipment. By investing in smaller, more flexible equipment where possible, creating manufacturing cells and combining steps helps to greatly reduce the inappropriate processing waste's.
Defects
The exertion needed in examining for and mending defects. If anytime defects happen, additional expenses are attracted rescheduling production, reworking the part etc. When it comes to making a direct effect on the bottom line, product deficiencies that result in scrap or rework are a major cost for companies. Costs that are associated incorporate rescheduling, re- inspecting, quarantining inventory as well as capacity loss. In most companies, the overall cost of defects accounts for a large portion of the total cost of production. There's an enormous chance to decrease defects at numerous facilities through Continuous Improvement Process (CIP) and employee involvement.
Hidden wastes
At a later point, the waste of human creativity is applied to the original seven wastes. It's essentially expressed as the attempt a struggle to generate services or goods the customer isn't urging or maybe the specifications of theirs don't match the expectations of the customers. Organizations use the staff of theirs for the nimble fingers of theirs as well as strong muscles but forget they turn up at the task every day with an entirely open mind. Organization are able to get rid of the additional 7 wastes as well as constantly improve the performance of theirs only by capitalizing on employees' creativity. Brief description and a summary of all of the waste materials from LEAN perspective might be observed in the below Figure:1.
Figure 1. LEAN wastes summary
2.0 LEAN CYCLE [12-14]
The continuous improvement is the concept of lean production. It is a journey of long term as well as efforts. Blend as well as relate the Plan-Do-Check-Action (PDCA) cycle by the leancycle (Fig.2).
Fig.2 PDCA cycle
A. Plan Aspect Mindset change
For the lean implement the most important thing is the company awareness as well as mindset change. Production management, design engineering, parts fabrication, production engineering as well as system assembly are only a few of the functional groups found in aerospace manufacturing suppliers. To remove interface barrier within the organization those functional groups should change their stereotype as well as mindset. To achieve the enterprise's ultimate gain, all departments must work towards the same aim and target.
5S/TPM
The machine/facility, as well as manpower, are critical elements on the shop floor of aerospace manufacturing suppliers. The employees disciplines as well as accountability is guaranteed by the 5S. The 'TPM' is able to ensure the device availability and utility. Particularly in the shop floor those 2 factors can assist the smooth as well as steady production.
The following are the main points of 5S/TPM:
Visual management: Adds color code control, supermarket, and Kanban system. These
tools assist to find the bottleneck as well as critical area to improvement for the first linesupervisor as well as manager.
Autonomous Maintenance.
-
Focused Improvement
-
Administrative and office TPM.
-
Initial Flow Control and Early Management
-
Tracking and evaluation mechanism
-
Overall equipment efficient (OEE)/Machine availability as well as utility
-
Safety and Pollution control
-
Education and training
-
Quality Maintenance
-
Planned Maintenance
The original intention had been to patch the breakdown of the machine. The current principle isthat operators are responsible for performing routine maintenance on their own equipment;
regularly keep an eye on the noise of the spindle as well as vibration. Moreover, assess the dimension or key attributes from the parts of production. After they discovered abnormal message or any error, then pass a message to the division of maintenance for fixing. Additionally, the engineer of maintenance audits the machine accuracy as well as spindle life. And provides the primary key spare parts for the machines. Consequently, improves the machine availability and utility, by helping to decrease the machine down time.
Do aspect
-
Stream flow line/ tested assembly line
The key products of aerospace manufacturing suppliers are component assembly and detail components. The facility/machine of components fabrication direction to create the stream flow line must follow the procedure sequence. To coordinate the number of laborers as well as the assembly jig, the assembly and rhythm creation must be focused on the requirement of manufacturing rate as well as takt time. Metal sheet, tube, plate and composites preprag are the raw materials has been released by the warehouse setup the supermarket to sheet metal, part fabrication, composite shop as well as tubing sequentially and uniformly includes machine. These stream of line of components fabrication retailer drag and create the raw material in needed size, contour and function, further then move to painting as well as coating. These components pass through the kitting center as well as they are ready to be shipped to the assembly line in accordance with the production schedule and takt period. Drill, seal and rivet are the assembly activities which are included. In order to combine as well as link those operations together a moving line is designed.
-
Operation standardization
Following lean/improvement practices, it's vital to standardize the operation/process. Therefore, the imroved outcome could be held and embedded in the product. Vendors of aerospaceproduction must consider how to apply such innovation suggestions to new/broader fields in order to maximize profits.
The following are the most important aspects of operation standardization:
-
Material, male, method, and machine, are the 4M establish the products quality as well asprocesses. If perhaps we are able to discover the right/better progression or maybe manufacturing details of 4M as well as firm repair those blends, then we are able to get thedependable products.
-
Standard work combination table
-
Process capability
-
Work instruction as well as visual aid is able to assist the operator while producing intricatedcomponents in an effective path.
Check Aspect
1) Aligning the IT system
Production cost management is important for assessing the benefit or loss of various programs. The functioning hour collection of every shipset aircraft element quantity is going to be administered as well as in contrast to the worth originate from learning curve. The improved results came after the machine or process's working-hour was increased, the enhance outcomes (Space, lead time, down time, transportation, standard working-houretc.) It is essential to revise within the 'IT' framework. Furthermore, the lean implement workplace is going to regulate the long term trends of implements to make certain the lean activities were flow down follow up.
The idea of production scheduling method shows as Fig.3. The device is going to compare the need as well as supply and come out the achievable information routine of every detail components as well as conclusion product. Schedule parameters (include working hour, lead timeetc.) will enter after verification into the creation scheduling method. Hence the IT system is able to give back and maintain the latest and current competence.
Fig.3 Concept of Production scheduling system
Action Aspect
1) Strategic / system transformation
Following the completion of lean tasks by the workers, each purposeful team's job description, process, and interface will be updated. Following value stream mapping and shop floor simulation, the task flow/layout could change. Following the staff brainstorming as well as many times simulation, the management philosophy can improve. As a consequence, management should think about the transformation of the Strategic or System, after the lean cycle:
On the demand of next process/customer in the kitting cart base the production control prepares the work-in-process. The multiple-skill operator picks up the component, presses it, seals it, and places it in the oven to cure it using seven different methods of analysis and simulation. The working space, transportation distance, production lead time and manpower could be decreased.
3.0 REVIEW OF LITERATURES:
Industry has supported a wave of research into the spot of manufacturing development within various production businesses over the last 20 years. Lean manufacturing was shown to be the best manufacturing technique in the twenty-first century. In today's market environment, a manufacturing company's success is determined by its ability to meet and respond as quickly as possible to changing environmental conditions, as well as to produce and deliver high-quality products at a lower cost to meet the needs of the customer. Much better, faster, cheaper brand emerged as a new paradigm for aerospace products.
Mourtzis etal[15] have stated that Lean theory, tools, and principles are intended to illustrate the value within a company and fully eradicate waste. No matter the lot of literature task on lean, there is an absence of in depth evaluation for collection as well as categorization of some lean rules due to the manufacturing business. Following a review of academic literature and a mold- making company, the current labor proposes a classification, identification, and formalization of lean regulations in order to create an applicable and systematic library of lean rules. Finally, unveiled the drawer strategy, with the intention of empowering staff at all levels of the hierarchy to advance the lean rule.
Abdullah Alkhoraif [16] has pointed out that there is a dearth of research into the cultural factors as well as organizational culture that are related to Lean implementation (LI). The goal when this particular newspaper divided into 4 stages. For starters, to identify the features of the of Lean Implementation (LI) influence. Secondly, group the elements together into themes. Finally, comparing individuals current perceptions to the themes. Finally, a lifestyle role that manufacturing SMEs would desire to achieve the best Lean Implementation was identified. In order to handle the need for Organizational Culture to help promote Lean as well as propel the results of its among small along with medium Enterprises (SMEs) in Saudi Arabia as a circumstance, grounded principle, action exploration plus an inductive strategy is selected. Because of the complexities of the topic, which necessitates the cultures exploration, qualitative research that is based on a well-established concept is advantageous. Consequently, sticking with the grounded theory process using a problem focused solution. Twenty-nine semi- structured interviews, as well as 2 focus groups, have been decided to perform this exploratory research along with a questionnaire that is produced to determine the OC themes within SMEs from the next target group, Seventy-one responses were refunded in total. An analysis of the literature to determine the best location for the themes. Inter-rater reliability is used to check the accuracy of the results. The semi structured interview concluded with 37 factors that affect the Lean implementation in Saudi Arabian manufacturing SMEs. In addition, in the first target category, the 37 elements were grouped into seven themes. Furthermore, the questionnaire's final result shows that many problems were found, with all of the findings falling into the frustration group. Change control and conduct trends were probably the lowest scoring themes. This particular paper plays a role in the perfect placement where the manufacturing SMEs exactly where they ought to be aspiring the best Lean.
Rojo Abollado etal [17] Companies that operate in highly controlled industries face additional challenges beyond traditional competition, product development challenges, and continuous cost reduction, according to studies. To meet these requirements, companies must simplify their business processes and update their applications and information systems to accommodate their changing business strategies. Workflow control engineering makes it easier to achieve these goals through methodologies, tools, and software to allow for company procedure modeling, reengineering plus workflow automation. Company procedure mapping is necessary to be able to record company tasks as workflow specifications. Then, these techniques allow organization procedure reengineering, helping the optimization of workflow automation as well as specified techniques and to create a lean electric workflow from the specs. In aerospace programmes, there are several advantages to be obtained from this technology, although, these generate a slew of implementation problems for major multinational companies operating in multiple markets, all of which must be tackled thoroughly. This particular research offers an overview of the advantages that electronic workflow implementation could possibly bring to aerospace makers, jointly with a comprehensive explanation of substantial complications, concerning both the introduction of automated workflows and the risks associated with human elements. The analysis raises business understanding on the benefits of turning an electronic transformation demonstrating the success factors through the application of electronic workflows and where to begin this implementationat a manufacturing cmpany.
As reported by Johan Vallhagen etal [18] The aerospace industry's competitiveness is gradually improving, while new technology for future decades of jet engines is rapidly emerging. Fabrication of structural elements is one process used by many aerospace firms to accomplish one of the most significant targets, eliminating excess fat. Nonetheless, as time goes by engineering work becomes more complex, necessitating new knowledge. As the demand for different manufacturing processes rises, as does the complexity of certain other production- related activities, production becomes even more complicated. Definitions of producibility and manufacturability are listed in the newspaper, along with related metrics for measuring the effect of the product look while keeping a generation phone. The result is a set of tools that is highly recommended as well as methodologies to control as well as assess the manufacturing passions and goals, and also exactly how they should be covered as well as in order to maximize producibility, the product production process must be balanced. The job also defined improvement opportunities and gaps, as well as a plan for the next step in improving producibility in the development of aerospace motor components.
Konstantions [19] etal have looked into quantifying the robustness of manufacturing methods. After reviewing the definition of robustness, a robustness explanation and metric is released. For robustness analysis, a methodology that incorporates discrete event simulation and statistical analysis is recommended. A case study of a low-volume mixed model creation line from the aerospace industry illustrates the effectiveness of the metric and the framework. The effect of various energy sources of disturbances on flowtime as well as tardiness robustness has been quantified in a couple of scenarios.
Rocio etal [20] have examined the connection as well as links between lean, resilient, as well as green supply chain (SC) methods as well as the impact theirs on the green performance of the aerospace sector. To evaluate the relationships' map involving methods and performance measures, a hybrid strategy of Significance Performance Analysis (IPA) as well as Interpretive Structural Modeling (ISM) is used. Lean SC practices show up as drivers for resilient and green SC methods as well as the impact of theirs on green efficiency is above that among the resilient SC habits. Furthermore, reviewing the results is particularly useful for practitioners who can learn more about the relationships between activities and their effect on environmental performance measures.
Fernando etal [21] have stated that when an aerospace assembly line is in the conceptual design stage, the design solutions that will satisfy the industrial and practical needs are recognized. As a consequence, a simple conceptual look of the assembly line and its basic parameters can be explained. ALB (Assembly Line Balancing) is the process of purchasing tasks from different stations in order to meet priority constraints. Because of the particular options that come with an aircraft, these methods aren't suitable for an aerospace assembly line, where the number of stations is determined by technological criteria rather than an
estimate aimed at lowering a certain parameter. Using the Model for Manufacturing (MfM) strategy, this paper offers a preliminary ontology characterization for aerospace assembly lines in the Airbus context. A brand-new method of characterizing mono configured aerospace solutions has been implemented by the authors. This brand-new technique gives the shop floor the most flexibility possible when using the adherence function, as well as it was created using a novel methodology called MfM.
Parthasarathy Garre [22] etal have claimed that for most little and medium-sized companies the lean manufacturing provides a brand new management approach, particularly used firms organized and also managed by under conventional push methods. In terms of efficiency, cycle times, and client responsiveness, advancement benefits can be impressive. It is much more than a collection of techniques and equipment, and it is commonly used by many manufacturing firms. All workers in Lean manufacturing are actively searching for ways to develop processes. Inside a production operation only lean is a comprehensive approach to reducing waste. Furthermore, by overburden also as via unevenness of workloads the waste which is produced it takes considers. The key principle is to maximize customer importance while reducing waste. For those with less resources, lean simply adds more value. This concept has the advantage of lowering non-value- added online services, tooling, content, labor cost and including space. In order to improve, it employs principles like misuse minimization, responsiveness and freedom.; these are dependent on attempts to enhance the flow of information and material and also to attain exceptional quality to be able to eliminate scrap and also rework.
Crute etal [23] They've advertised that lean manufacturing seems to hold a lot of promise for dealing with an extent of simultaneous, naturally competitive needs such as excessive amounts of progression as well as quality of the product, in addition with a drop in lead times and cost that is low. These needs are recognized in the aerospace market work are well established to apply Lean methods. Within the automobile sector the lean manufacturing was initiated. Nonetheless, even after the publication of the seminal book, The Machine That Changed the World, there are numerous known instances of Lean implementation in a variety of industries. Despite this evidence, the belief persists that Lean manufacturing is primarily a "automotive concept" that is difficult to transfer to other industries, especially when there are significant differences between them. We discuss the primary main drivers for Lean in aerospace in this paper, as well as the assumption that cross-sector transition can be difficult. A review of Lean implementation case studies looks at how issues that occur can have much more to do with the particular plant contextand control than with industry-specific factors.
Nikhil etal [24] have reviewed the lean manufacturing approach in aerospace industries. They say that lean manufacturing offers a brand-new management strategy for most medium and small-sized companies. In terms of efficiency, customer responsiveness, and cycle times, the changes may be remarkable. It's much more than a set of techniques as well as tools and has been generally adopted by a lot of manufacturing organizations. It's a custom where all employees constantly search for solutions to enhance procedures. Only lean is a systematic approach to reducing waste in a production line. Also, waste caused by overburden and uneven workloads is taken into account by lean. The central concept is to increase consumer value while reducing waste. Simply put, lean means generating a lot of value for people with less resources. The advantage of this concept is that it seeks to eliminate unnecessary or non-value-added online resources, space, tooling, labor, and materials, among other things. It applies such concepts as misuse minimization, responsiveness, and freedom, in order to change; these are dependent on attempts to enhance the flow of information and material and also to attain exceptional quality to be able to remove scrap plus also rework. Although lean manufacturing was initially produced for aerospace manufacturing, automobile industry businesses have discovered that these principles may also be applied to this high-precision industry to produce significant improvements in production efficiency. Our goal is typically to find bottlenecks in a respectable manufacturing market's production line. The main aim is to provide background on lean manufacturing, provide a summary of manufacturing waste products, and explain the equipment as well as processes that are used to transform a company into a well-functioning lean enterprise.
Allen Haggerty [25] has claimed that within the past ten years, the lean has been adopted by the aerospace industry, 6 Sigma, along with associated efficiency advancement techniques to boost the quality, and minimize the expense of the products of theirs throughout all life cycle works and also shorten the delivery times. 'Engineering' is especially the area of high leverage for implementing lean thinking as sixty to eighty percent of the life cycle expenses are locked in place by upfront engineering choices. Depending on 9 case studies carried out by students of MIT, this particular paper will elaborate on the components of Lean Engineering that happen to be utilized properly in different ways in programs that are many for more than 50 ages. A lot of the components are tried and true methods of great aircraft engineering, while a few tend to be more recent additions. The primary challenge of Lean Engineering lies in using the different components in an integrated alternative method. Only some programs have accomplished this state.
4.0 CONCLUSIONS
The basic concept of lean, lean cycles and implementation activities in aerospace sector is discussed in this paper. The application of lean techniques are beneficial in aerospace domain not only for engineering applications, it is also useful for business uses. Lean concept can offer nonstop improvement in the aerospace industries. The scope of lean topics as well as environment turns into better than earlier than through the continuous lean cycle. Application of lean ideas in aerospace sectors engineering techniques is viable, delivers real benefits for both small scale and large industries.
REFERENCES:
-
Henderson, B.A., Larco, J.L., Womack, J.P. (2010) Lean Transformation: How to Change Your Business into a Lean Enterprise. Oaklea Press, ISBN: 978-0964660120.
-
LHT LEAN Academy, Lufthansa Technik LEAN Basics Fast track. Company TrainingDocument, Rev. 2.0 – 2011
-
http://en.wikipedia.org/wiki/Muda_(Japanese_term)
-
EMS Consulting Group, Developing foundation for LEAN Implementation.http://www.emsstrategies.com/dd073103 article.html
-
EMS Consulting Group, The 7 Manufacturing Wastes.http://www.emsstrategies.com/dm090203article2.html.
-
LEAN Manufacturing. http://en.wikipedia.org/wiki/ Lean_manufacturing
-
Womack, J.P., Jones, D.T. (1996) Lean Thinking. Second Edition, Simon & SchusterInc., ISBN: 9780684810355
-
EMS Consulting Group, Lean Overview. http://www.emsstrategies.com/dm090203article1.html
-
EMS Consulting Group, Lean Works for Every Organization.http://www.emsstrategies.com/dd040106article.html
-
EMS Consulting Group, Does Lean Work for any Industry.http://www.emsstrategies.com/dd070108article.html
-
Henderson, B.A., Larco, J.L., Womack, J.P. (2010) Lean Transformation: How to Change Your Business into a Lean Enterprise. Oaklea Press, ISBN: 978-0964660120
-
LHT LEAN Academy, Lufthansa Technik LEAN Basics Fast track. Company Training Document, Rev. 2.0 2011, http://en.wikipedia.org/wiki/Muda_(Japanese_term)
-
EMS Consulting Group, Developing foundation for LEAN Implementation.http://www.emsstrategies.com/dd073103 article.html
-
EMS Consulting Group, The 7 Manufacturing Wastes.http://www.emsstrategies.com/dm090203article2.html.
-
D. Mourtzis, P. Papathanasiou, S. Fotia Lean Rules Identification and Classification forManufacturing Industry Procedia CIRP 50 ( 2016 ) 198 203.
-
Abdullah Alkhoraif Patrick McLaughlin Lean implementation within manufacturing SMEs in Saudi Arabia: Organizational culture aspects Journal of King Saud University Engineering Sciences 30 (2018) 232242.
-
J. Rojo Abollado, E. Shehab, P. Bamforth "Challenges and Benefits of Digital Workflow Implementation in Aerospace Manufacturing Engineering
Procedia CIRP 60 ( 2017 ) 80 85
-
Johan Vallhagen, Julia Madrid, Rikard Söderbergb, Kristina Wärmefjord An approach for producibility and DFM-methodology in aerospace engine component development 2nd International Through-life Engineering Services Conference, Procedia CIRP 11 ( 2013 ) 151-156.
-
Konstantions efthymiou, Michael greenhough, Cameron turner Evaluating manufacturing systems robustness: an aerospace case study Procedia CIRP 72 (2018) 653 658.
-
Rocio Ruiz-Benitez, Juan C. Real, Environmental benefits of lean, green and resilient supply chain management: the case of the aerospace sector
-
Fernando Masa , Jesus Racero , Manuel Oliva, Domingo Morales-Palma Preliminary ontology definition for aerospace assembly lines in Airbus using Models for Manufacturing methodology Procedia Manufacturing 28 (2019) 207213.
-
Parthasarathy Garre , V.V.S. Nikhil Bharadwaj, P. Shiva Shashank , Munigala Harish , M. Sai Dheeraj Applying lean in aerospace manufacturing Materials Today: Proceedings 4(2017) 84398446.
-
V. Crute, Y. Ward, S. Brown , A. Graves Implementing Lean in aerospace challenging the assumptions and understanding the challenges Technovation 23 (2003) 917928.
-
V. V. S. Nikhil Bharadwaj , P. Shiva Shashank , Munigala Harish , Parthasarathy Garre A Review On Lean Manufacturing to Aerospace Industry International Journal of Engineering Research and General Science Volume 3, Issue 4.
-
Allen Haggerty EVIDENCE OF LEAN ENGINEERING IN AIRCRAFT PROGRAMS 25th international congress of the aeronautical sciences.