
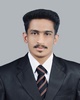
- Open Access
- Authors : Chetan B. Warvante
- Paper ID : IJERTV12IS030037
- Volume & Issue : Volume 12, Issue 03 (March 2023)
- Published (First Online): 15-03-2023
- ISSN (Online) : 2278-0181
- Publisher Name : IJERT
- License:
This work is licensed under a Creative Commons Attribution 4.0 International License
Implementation of Quick Changeover and Analysis of Its Impact on Production
Chetan B. Warvante
Studied Mechanical Engineering,
Tatyasaheb Kore Institute of Engineering and Technology, Warananagar.
Kolhapur, Maharashtra, India.
Abstract- For developing countries like India, it is vital to understand what it takes for a small industry to survive in a global economy. To gain profit and to increase productivity as well as to minimize waste, it is necessary to adopt new manufacturing concepts like lean manufacturing. This paper addresses the application of lean manufacturing concepts to the mass production sector with focus on the automotive manufacturing industry. The objective of this research work is to investigate how the lean manufacturing tools can be adopted to the discrete manufacturing system and to evaluate their benefits on the specific application instance. In this concern observation of changeover activities, time study has been done in this research work. The basic idea behind the lean manufacturing is to increase the productivity by eliminating waste. Waste is defined as anything that does not add value to the end product. The goal of lean manufacturing is to assist the manufacturers to improve their competitiveness through the implementation on lean manufacturing tools to the continuous production process. This research paper tries to analyse present changeover process and extract the common scenario for the changeover process in continuous production systems in automotive industries.
Keywords- Lean Manufacturing; Quick Changeover (QCO); Automotive; Mass Production.
-
INTRODUCTION
The automotive sector in India is playing crucial role in the growth of the national economy. To be in the market and gain the competitiveness in the market it is important for the automotive firm to deliver quality products in time with reasonable price to the customer. The automotive production sector in India which includes continuous production processes such as assembly and testing of different vehicles as well as vehicle parts. Now with highly increasing customer demand it is necessary for the automotive firm to produce quality products within time. The production processes are continuous and the industry runs 24×7 that is throughout the week. In order to manufacture different types of a vehicles as well as vehicle parts having different size and shape it is required to take changeover on the assembly lines as well as test lines whenever there is a type change. Changeover is the processes of converting one system to another, which is nothing but technical and organizational preparation of workstation or work system to produce another part/ product. To maximize the profit, it is necessary to minimize or eliminate all types of waste. In manufacturing industry two important wastes are material waste and time waste. Lead time is one of the important factors. Lead time
is the time requires for product to go through complete process, that is from raw material to finished good. Shorter the lead time higher will be the production. Shorter lead time can be achieved by reducing and eliminating the time required for non-value adding activities.
Lean manufacturing is the concept that focus on the cost reduction by eliminating non value adding activities. The changeover activities for the selected automotive industry includes online and offline activities. For minimizing the changeover losses, it is necessary to make changes in the present changeover process and implement new changeover process in the production. The details regarding the present scenario and the improved scenario, we will see in this research work or case study.
Figure 1: Changeover Process
Figure 2: Benefits of Quick Changeover
-
METHODOLOGY
This is a case study of the present changeover process and the improved changeover process after the implementation of the lean concepts in the selected manufacturing industry. this study gives the idea about the quick changeover and its important outcomes to minimize the waste that is time waste in the continuous production system. The necessary steps required for the case study are,
-
Finding literature/ review
As there were not enough books are available on the selected topics, so the extensive research is carried out with the help of the data available on the internet.
-
Investigation through literature
After reviewing the research work as well as information on internet, concepts and theories related to lean tools are analysed and the present changeover process is compared.
-
Analysis of the present changeover process
In this phase, after the investigation through the literatures the current changeover process is analysed and the various activities takes place during the changeover are noted.
-
Time study
In the time study phase, time required for the changeover is noted along with the detailed step by step process and the on line and off line activities.
-
Scope of improvements and Implementation
After the analysis of the present changeover process necessary improvements are recorded based on time study and activities. Certain changes were made like involvement of the employees in the changeover activities. Newly implemented process of QCO (Quick Changeover) is monitored for certain period of time.
-
Results
In the final phase, the outcome of the newly implemented changeover process is observed.
-
-
ANALYSIS
Changeover Activities
Changeover is the technical and organizational preparation of workstation/ a work system to produce another part/ product. It is one of the important activities in the continuous mass production systems. To produce different type of products as per customer demand, frequent changeovers are necessary in the production process. The selected automotive firm produces automotive parts for its customers. since the products are being assembled on the same assembly line and tested on the same test line it is required to take changeover whenever there is type change. There are total of 85 different types of parts are being assembled and tested on single assembly and test line. The changeover process basically includes the following activities,
-
Internal Activities
-
Tooling change
Tooling change is the major activity in the changeover process. As per the new part/ product
type tools are changed on each workstation of the assembly line. Tools are the fixtures which holds the part/ product during assembly, need to change as per requirement for the new part/ product type.
-
Program change
Now as per the type of the part/ product, there are different programs on the console panel. The program is basically prepared with the process parameters as per the requirement of the customer for the particular part/ product.
-
Calibration and stability
Calibration is the process of checking the accuracy of the system and stability is the process of checking the consistency of the system to give the accurate reading within specified tolerance limit.
-
-
External Activities
-
Pre-adjustment
Pre-adjustment is necessary before taking the changeover. It includes adjustment of the fixtures.
-
Tool supply
Tools need to be taken from the tooling rack to the respective workstation of assembly and test line at the time of the changeover.
-
Check/ Measure
It includes ensuring proper oil pressure, air pressure. If it is not within tolerance limit then it needs to be adjusted as per the requirement.
-
Information transfer
-
Information needs to be provided to the associates regarding the special customer requirement. Before starting production associates present on that respective workstation must be aware of specific customer requirements for the particular part/ product being produced to avoid customer complaints. Such kind of information must be given to the associates before the production starts.
Time study (Before QCO Implementation)
Key factors need to be taken into consideration before doing time study are,
-
In the present scenario of changeover process, process expert is the only person responsible to take the changeover of all the workstations.
-
Toolings are not provided on the station and need to be taken from the tooling rack. (External activity)
-
Calibration is the process of checking the accuracy of the system and stability is the process of checking the consistency of the system to give the accurate reading within specified tolerance limit. Three conjugative readings are taken in the stability process. If the stability readings vary from the tolerance limit, then the entire calibration and stability process needs to be repeated. In the selected automotive firm for the assembly and
testing the calibration and stability requires on the specific workstations like 3.1, 4, 7, 8, and 9.
-
To take calibration and stability on the specified station it is required to have the partial product on the workstation. Since the product is being assembled on the station the time required for the part to move to the next station is not taken into the consideration. Total time required for the assembled part to go through complete process is approximately 18 minutes.
Time required for the changeover on each workstation of the assembly line for different activities is observed and mentioned below in table 1,
Sr. No.
Station
Activity
Idle Time
Process Time
Minutes
Seconds
Minutes
Seconds
1
1
Tooling Change
0
0
4
15
Program Change
2
45
2
2
Tooling Change
5
0
1
30
Program Change
0
30
3
3.1
Tooling Change
5
0
2
0
Program Change
1
15
Calibration and Stability
3
15
4
3.2
Tooling Change
9
30
3
0
Program Change
2
0
5
4
Tooling Change
12
30
1
0
Program Change
1
15
Calibration and Stability
2
30
6
5
Tooling Change
15
15
2
0
Program Change
1
45
7
6
Tooling Change
17
0
2
30
Program Change
2
40
8
7
Tooling Change
20
10
1
20
Program Change
0
45
Calibration and Stability
1
30
9
8
Tooling Change
21
45
2
10
Program Change
1
50
Calibration and Stability
8
40
10
9
Tooling Change
32
25
1
30
Program Change
0
45
Calibration and Stability
3
0
Table 1: Station-wise Changeover activities with time study before QCO implementation
Day
Sr. No.
Changeover (Product types)
Time required (Minutes)
1
1
415 to 510
45
2
510 to 205
40
3
205 to 401
42
2
1
401 to 602
35
2
602 to 508
38
3
1
508 to 18A
39
2
18A to 489
38
4
1
489 to 13D
40
2
13D to 153
39
3
153 to 12S
32
5
1
12S to 489
38
2
489 to 113
42
Average
39
Table 2: Changeover time duration before QCO implementation
From the above collected data it is found that the total idle time on all stations is 32 minutes and 25 seconds. And the set-up time required on the last station that is for station 9 is 5 minutes and 15 seconds. Hence total changeover time is 37 minutes and 40 seconds. Moreover, if we consider the external activities which includes tooling supply, pre- adjustment then the total changeover time is almost 45 minutes. From this time study it is found that in order to minimize the changeover losses we have to work on the idle time and the time required for the external activities.
Investigations from the study
The present scenario of the changeover is observed for 5 days and time required for the same is noted below in table 2,
From the collected data it is found that the average time required for changeover is 39 minutes. Now for the study we consider the maximum time required for the changeover process that is changeover from part/ product type 415 to part/ product type 510, which is 45 minutes. The changeover time which is 45 minutes also incldes time required for internal and external activities. The changeover activity tends to reduce the daily rate of production. While observing the changeover activity few things are noticed, which are as follows,
-
Responsibility- From the observation it is found that process expert is the only person who take set-up change. During set-up change or changeover all the associates working on the respective workstations remains idle.
-
Tooling supply- At the time of changeover the toolings are required to be taken from the tooling rack which is time consuming activity.
-
Components availability- There is delay in the availability of the child components for the assembly.
-
Calibration and stability processes on the respective stations can be done by the associates working on the station.
-
-
SCOPE OF IMPROVEMENTS AND
IMPLEMENTATION
As per investigations and time study which we have seen earlier, some improvements are possible in the present changeover process. Now we will see the factors considered for the improvement in present changeover process,
-
In the present scenario process expert takes the changeover of the entire assembly line that is all the workstations. And it is also observed that associates remain idle during the changeover process. Now it is decided to involve all the associates in the changeover process. That is the associate present on the workstation will take the set-up change of that respective workstation. For this the associates must be trained to take the changeover. Hence learn stat needs to be provided to the associates in all three shifts. Shift
foreman and process expert will provide the learn stat to the associates.
-
It is also found that the tool supply is also time- consuming activity. Sometimes the toolings are not available at the racks and usually misplaced, so it takes more time in search of the toolings which results in larger down times. The solution of this issue is provision of small tool keeping racks on each of the workstations. Process expert will put required tooling in the racks 10- 20 minutes before changeover.
-
Components availability also plays crucial role in the changeover activity. Calibration and stability processes are only possible if the child components available on time. Just in time delivery is necessary for such condition. It is also important to prepare kitting area near assembly lines. Kitting area is used to store multiple components required for the manufacturing assembly. It helps to reduce waiting time for the components during actual time of changeover.
-
Calibration and stability are necessary tasks. It is important in the manufacturing process to check the stability of the system after every two hours or 200 parts to avoid deviations and rejections. It is time consuming activity. In current scenario it is the responsibility of process expert to take calibration and stability of the workstations at the time of changeover. To avoid the time consumption this activity must be done by the associates on the respective workstations. It can be possible by providing learn stat to the associates/ employees.
these are the point of improvements made from the investigation results and time study, now by considering the factors of improvement new changeover process is developed and implemented on the assembly line. Some of the important changes made in the existing changeover process are as follows,
-
Learn stat is provided to all associates/ employees and for few days, assistance is provided to avoid mistakes and to help them understand the changeover procedure. After 10-15 days it is observed that associates are trained to take the changeover on their own.
-
For tooling supply, small rack is provided on each of the workstation to put all required toolings 10-15 minutes before changeover. Process expert will be the responsible person to ensure that required toolings are available on the workstation. also, a small space is provided on the same rack to place Allen keys.
-
Kitting area is built near assembly line to make required components available on right time at right place.
-
Detailed step by step changeover procedure is included in the work instructions and updated work instructions kept on each workstation. Such that whenever problem occurs associate can use the work instructions instead of calling process expert.
Time study (After QCO Implementation)
After successful implementation of new changeover process, time study report is made and results are mentioned below in table 3,
Table 3: Station-wise Changeover activities with time study after QCO implementation
Sr. No.
Station
Activity
Idle Time
Process Time
Minutes
Seconds
Minutes
Seconds
1
1
Tooling Change
0
0
4
15
Program Change
2
45
2
2
Tooling Change
3
0
1
30
Program Change
0
30
3
3.1
Tooling Change
0
0
2
0
Program Change
1
15
Calibration and Stability
3
15
4
3.2
Tooling Change
0
0
3
0
Program Change
2
0
5
4
Tooling Change
0
0
1
0
Program Change
1
15
Calibration and Stability
2
30
6
5
Tooling Change
0
0
2
0
Program Change
1
45
7
6
Tooling Change
0
0
2
30
Program Change
2
40
8
7
Tooling Change
0
25
1
20
Program Change
0
45
Calibration and Stability
1
30
9
8
Tooling Change
0
0
2
10
Program Change
1
50
Calibration and Stability
8
40
10
9
Tooling Change
5
25
1
30
Program Change
0
45
Calibration and Stability
3
0
From above results it is found that the time required for the changeover is reduced to 13-14 minutes.
-
-
RESULTS
After implementation of the Quick changeover, it is observed that the time required for the changeover activity is greatly reduced and the observations are as follows,
Day
Sr. No.
Changeover (Product types)
Time required (Minutes)
1
1
508-401
10
2
401-522
14
2
1
522-415
15
2
415-208
13
3
208-13D
14
3
1
13D-489
16
2
489-18A
10
3
18A-508
14
4
1
508-522
14
2
522-12S
10
5
1
12S-153
14
2
153-508
12
Average
13
Table 4: Changeover time duration after QCO implementation
It is clear that after QCO implementation the changeover time is reduced to 13 minutes. Which will have greater impact on the production of the automotive firm. To check the impact on the production, observations are recorded before and after QCO Implementation,
Sr. No.
Day
Number of Changeovers
Daily Production (No. of Parts)
Daily Production Before QCO Implementation
1
1
3
2386
2
2
2
2508
3
3
2
2428
4
4
1
2645
5
5
1
2800
Total Production
12767
Daily Production After QCO Implementation
1
1
3
2590
2
2
2
2887
3
3
2
2854
4
4
1
2954
5
5
1
3025
Total Production
14310
Table 5: Production before and after QCO implementation
Impact of QCO on changeover time
(Time required in minutes)
50
40
30
20
10
0
415 to 510 205 to 401 13D to 153 602 to 508
Before QCO After QCO
Figure 4: Impact of QCO on changeover time
Note- Downtime due to organizational loss, technical loss, quality loss and performance loss is not taken into consideration.
3500
3000
2500
2000
1500
1000
500
0
Impact of QCO on Production
(Number of parts per day)
Day 1 Day 2 Day 3 Day 4 Day 5 Before QCO After QCO
Figure 3: Impact of QCO on production
-
CONCLUSION
Form the above discussion it is clear that the average production rate which was 2553 parts per day has been increased to 2862 parts per day that is the rate of production is increased by 12%. It is concluded that Quick Changeover has a positive impact on the production of the firm. The result of this study indicates the effectiveness of Quick changeover in the mass production companies. For small firms having higher customer demand for their products, must implement Quick Changeover concept in the production to achieve required daily production rate.
REFERENCES
[1] Shingo, A Revolution in Manufacturing: The SMED System, Productivity Press, Portland, 1985. [2] Jamie W. Flinchbaugh, Implementing Lean Manufacturing Through Factory Design, Massachusetts Institute of Technology, 1998. [3] Miltenburg J, One-piece flow manufacturing on U-shaped production lines: a tutorial source. IIE Transactions 33 (2001) 303–21. 2001 [4] D. Severson, The SMED system for reducing changeover times: an exciting catalyst for companywide improvement and profits, P&IM Review with APICS News, 1988. [5] A. Mileham, S. Culley, G. Owen, and R. McIntosh, "Rapid changeover-a pre-requisite for responsive manufacture," 1998. [6] The Productivity Press Development Team, Quick Changeover for Operators, Productivity Press, Portland, 1996.From the collected 10 days data before and after
implementation of QCO it is clear that the production is increased by 12%.
Changeover time tracking results for some of the major part/ product type changes is mentioned in the figure 4, below,
[7] Sekine, Kenichi, and Keisuke Arai. Kaizen for Quick Changeover.Cambridge, Massachusetts: Productivity Press, 1992.
[8] International Journal of Lean Thinking Volume 3 Issue 2 (December 2015) Single Minute Exchange of Dies: Literature Review by Yash Dave and Nagendra Sohani [9] Pablo Guzmán Ferradás, Konstantinos Salonitis., Improving changeover time: a tailored SMED approach for welding Cells. CIRP,PP 598-603,2013
[10] Reduction in Setup Time by SMED Methodology: A Case Study by Prof. Nagaraj A Raikar (Assistant Professor Dept of Mechanical Engineering AITD, Assagao GOA) volume 5 of International Journal of Latest Trends in Engineering and Technology (IJLTET) issued on 4 July 2015. [11] The Implementation of Single Minute Exchange of Die with 5S in Machining Processes for reduction of Setup Time by Vipin Kumar and Amit Bajaj (Assistant Professor, ME Department, GTB Group of Institutions, Malout) in International Journal on Recent Technologies in Mechanical and Electrical Engineering (IJRMEE) ISSN: 2349- 7947 032 039 Volume: 2 Issue: 2 [12] R. R. Joshi and G. Naik, "Reduction in setup time by SMED a literature review," International Journal of Modern Engineering Research (IJMER), vol. 2, pp. 442-444, 2012. [13] S. Jain and R. O. Vaishya, "Case study: application of SMED in SIM card manufacturing company," International Journal of Productivity and Quality Management, vol. 32, pp. 109-128, 2021. [14] D. Sabadka, V. Molnar, and G. Fedorko, "The use of lean manufacturing techniquesSMED analysis to optimization of the production process," Advances in Science and Technology Research Journal, vol. 11, 2017. [15] K. Arai and K. Sekine, Kaizen for quick changeover: Going beyond SMED: CRC Press, 2006.