
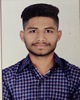
- Open Access
- Authors : Ravi Patel , Rahul Patel
- Paper ID : IJERTV9IS100018
- Volume & Issue : Volume 09, Issue 10 (October 2020)
- Published (First Online): 07-10-2020
- ISSN (Online) : 2278-0181
- Publisher Name : IJERT
- License:
This work is licensed under a Creative Commons Attribution 4.0 International License
Improve Performance Cooling of Clutch by using Fins Around Clutch Surface
Ravi Patel, Rahul Patel
Corresponding Author and Assistant Professor, Department of Automobile Engineering, UG Student, Department of Automobile Engineering,
Sal Institute of Technology and Engineering Research, Ahmedabad-380060, India.
Abstract:- The temperature rise in a car dry single-plate clutch during engagement and disengagement is very crucial because it is one of the parameters which have a direct influence on the clutch life. The slipping of the clutch happens during engagement and disengagement where the friction material on the plates will undergo a change of state from solid to semi-solid state and the friction material properties start to deteriorate. In order to optimize the clutch life it is very important to identify the parameters affecting temperature rise. The temperature measurement setup was developed during the Internship program. Mathematical modeling would help in developing the equation for predicting the temperature rise. The project involves combining equations of different physical phenomena like heat conduction in the plates, convective heat transfer by the cooling fins, torque transfer by the clutch and energy balance equations. Mathematical modeling using ordinary differential equation was determined to calculate the temperature rise. The mathematical model was analyzed using tables and graphs were generated. The generated graphs were compared and validated by the experimental results obtained from Internship program. The cooling system of clutch was designed, analyzed and fabricated by providing cooling fins to the existing clutch cover for improving the cooling for the existing system.
Key words: Clutch plate, clutch cover, cooling, fins, heat generation
1.INTRODUCTION
A Clutch is a mechanism used to connect or disconnect the engine from the rest of the transmission elements. When the clutch is engaged, the engine will be connected to the transmission, and power flows from engine to rear wheels through a transmission system. Clutches allow a high inertia load to be stated with a small power and due to this it produce large amount of heat in itself. When engine started that time this heat do not affect the friction ling material but when engine runs at high rpm then coefficient of friction material lost their thermal properties this causes overall performance of clutch. So , we think to reduce heat from clutch case by putting fins on periphery of clutch.
Here, we have used theory of heat transfer. Heat transfer is a thermal energy which occurs in transits due to temperature difference. Cooling system is one of the important system among all of the systems in automobile. Fins are responsible to carry out the produced heat inside the clutch, for the heat transfer there are various modes like conduction , convection and radiation are taken place. From these modes conduction is carried out in engine cooling fins. There are two different types of cooling system that are used in the automobiles, they are:
1.Air cooling 2.water cooling
-
Air-Cooling : Mostly automobile bikes using direct air cooling (without an intermediate liquid) were built over a long period beginning with the advent of mass produced passenger cars and ending with a small and generally unrecognized technical change.
-
Liquid Cooling: Liquid cooling is also employed in maritime vehicles. For vessels, the seawater itself is mostly used for cooling. In some cases, chemical coolants are also employed (in closed systems) or they are mixed with seawater cooling.
Here, for our project we use air cooling by using fins because liquid cooing have high maintenance and Clutch Case is placed under the engine compartment and there is no large space to mountain water cooling system. Under the engine compartment air is easily can contact with fins which are placed around the clutch case, and in this way we will reduce heat from clutch case by using air cooling system.
Purpose:
The clutch fins is a device that is frequently used in a vehicles cooling system. Thus, when clutch generate heat by engaging or disengaging that time this cooing fins will take heat from clutch and dissipate that heat to surrounding by using cooing fins that we placed on clutch cover in this way our purpose is that to dissipate heat from cultch and improve clutch efficiency.
-
METHODOLOGY
Mostly in automobile for air cooling aluminum is used as a fins material so, here we used aluminum as base material because it is light weight and heat dissipation properties is higher than other material.
System design :
Elevation Plan
Two dimensional sketch of clutch plate drawn from given dimension is showed in fig. fins used for this type of clutch surface is aluminum. Specification of cooling fins and standard data of clutch are mentioned below
Calculation: Calculation of Fins: Data of clutch:
Parameter
Values (mm)
Inner radius of the friction plate and racial cushion (ri)
62.98 mm
Outer radius of the friction plate and axial cushion (ro)
87.21 mm
Thickness of friction plate (tP) and axial cushion
5 mm
Inner radius of the pressure plate (ri)p
58.14 mm
Outer radius of the pressure plate (ro)p
92.05 mm
Thickness of the pressure plate (tp)
9.69 mm
Inner radius of flywheel (rif)
48.45 mm
Outer radius of flywheel (rof)
96.9 mm
Thickness of the flywheel (tp)
19.38 mm
Co-efficient of friction µ
0.3
Torque , T (NM)
432 nm
Initial temperature, Ti(k)
300 k
Final temperature , To(k) at a one second
520 k
(Table 2: Data of clutch)
-
Data of fins: Length: 7mm Width: 7mm Hight: 7mm
Volume of fins = 21mm3
-
Area of fins surface: 7 * 7 = 49 mm3
Total surface of fins: 5
Area of fins each surface = 49*5
=245mm2
-
Gap between each fins = 41.172 mm So, total number of fins are 12
-
The fins are implemented on pressure plate Without fins area of surface = 5601.537 mm2
With fins area of surface = area of fins * number of fins
= 245*12
= 2940mm2
Design of pressure plate: (ro)p = 92.05 mm = 0.09205m (ri)p = 58.14mm = 0.05814m (t)p = 9.69mm = 0.00969m
-
Periphery surface of pressure plate = 2(ro)p
= 2*3.14*0.09205
= 0.578074m
= 578.074mm
-
Area of periphery surface of pressure plate
= periphery of outer surface * Thickness of pressure plate
= (sp) * ( tp)
= 2r * tp
= 578.074*9.69
= 5601.5370 mm
-
Using the fins on the pressure plate Volume fins = l*b*h
= 7*7*7
= 343mm2
So, finally increase the area of surface and increase the area of contact to direct air
-
The law of heat convection Q = h*A* T
Q A
Heat transfer area of surface
-
The free convection of heat transfer so, convective heat transfer co-efficient of air is (h)air = 30 (w/m2 K) The heat transfer co-efficient and air velocity relation graph.
(Graph 2: Air- Heat Transfer co-efficient)
Because the ca running condition speed, Velocity above the 2.5 m/s so, the assume (h)air = 30 (w/m2 K)
-
Data of pressure plate and design
Pressure plate material
Steel
Thermal conductivity (K)
42 w/mk
Specific heat (c)
450 J/Kg*k
(Table 2.1: Data of pressure plate and design)
Heat losses from the rotating clutch the heat losses is from of energy and the unit of energy is (watt).
-
The heat losses threw the Newtons cooling law of convection,
Q = h *A * T
h= heat transfer co-efficient A= Area of surface
T = Temperature difference
-
The heat release without fins on surface of pressure plate, Q = h *A * T
= h*A* (T2-T1)
= 30*5.60153 (520-300) Q = 36,970.098 watt
= 36.970098 kilo watt
-
The heat losses with fins on the surface total area of surface
= only surface area + with fins area
= 5601.53 + 2352
= 7.953.53 m2
Q = h *A * T
= 30*7.95353*220
= 52,493.298 watt
= 52.493,298 kilo watt
So, Q = Q with fins Q without fins
= 52.493298 36.970098
= 15.5232 kilo watt
So, finally it release heat energy and clutch plate cooled by the fins of the pressure plate.
-
-
CONCLUSION
The amount of heat generation is not change but the cooling is increased in short time, it also improves life of clutch plate, lining material, friction plate, compression spring and many other parts which are used in clutch assembly. most of literature has recently focused on improving friction lining material and decreasing heat which is produced by clutch but there are few which has think about cooling of clutch by air cooling and here, by working on this project we solve many problems which are caused by heat generation of clutch assembly. if we apply this system in present automobile sector then it will become very helpful for both customer as well as manufacture.
-
REFERENCES
-
-
28, 1954 were Clutch plate with grovesfor lubricant R coolant Charlrs J. McDowall, New Augusta, Ind., assignor to General Motors.
-
Hiroshi Yabe, Yubo Yang, Robert C. Lam and Yih Fang ChenModeling of Heat Transfer and Fluid Hydrodynamics for a Multidisc Wet Clutch SAE Series 950898
-
David A Pacey and Ralph 0 Turnquist. Modeling Heat Transfer in a Wet Clutch SAE Series 901655
-
Rajasekar, palanisamy, Design and analysis of trible tube heat exchangers with fins. IOSR journal of mechanical and civil engineering ISSN: 2278- 1684, PP 01-05
-
Mooyeon Lee, Air-side heat transfer characteristics of spiral-type circular fin-tube heat exchangers, Oct– 2009, PP 313-320