
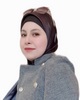
- Open Access
- Authors : Asmaa Shahate Sofy , A. Serag Faried , W. H. Sofi , Magdy A. Abd El-Aziz
- Paper ID : IJERTV12IS030228
- Volume & Issue : Volume 12, Issue 03 (March 2023)
- Published (First Online): 07-04-2023
- ISSN (Online) : 2278-0181
- Publisher Name : IJERT
- License:
This work is licensed under a Creative Commons Attribution 4.0 International License
Influence of Reuse of Drinking Water Treatment Plants Sludge in Concrete
Asmaa Shahate Sofy 1
1 MSC Candidate, Civil engineering Department, Faculty of Engineering, Fayoum University, Fayoum, Egypt
A. Serag Faried 2
2 Professor, Civil engineering Department, Faculty of
W. H. Sofi3
3 Professor, Housing and Building National Research Center (HBRC), Giza, Cairo, Egypt
Magdy A. Abd El-Aziz4
Engineering, Fayoum University, Fayoum, Egypt
Abstract This investigation addresses the effect of sludge from water treatment plants as partially replacing cement on the mechanical properties. Various mixtures of sludge powder (SL)
after heated treatment at 200, 300, and 500 are produced
by partially replacing cement with 0%, 5%, 10%, 15%, 20%, and
25 wt%. SL after heated treatment at 200 with 0%, 5%, 10%,
15%, 20%, and 25 wt% was replaced with 10% liquid sodium
silicate. The program includes the substitution of cement with 5% un-hydrated lime and 10% silica fume at sludge powder after
heated treatment at 200 with 0%, 5%, 10%, 15%, 20%, and 25
wt%. A series of laboratory tests were performed to investigate
the mechanization of strength development which included compressive strength, splitting tensile, flexural strength, SEM, EDX, and mapping. Generally, the results showed that using 5%, 10% sludge in concrete increased the strength and then decreased at 15-25% of sludge. The use of silica fume improved the strength the most and also increase heated treatment of Sludge increased the strength.
Keywords Drinking water treatment plant sludge; sodium silicate; Un-hydrated lime; silica fume
-
INTRODUCTION
The rapid population growth translates into increased demand for drinking water which results in water treatment plants are produced more drinking water than in the last decades [1]. Conventional processes for drinking water treatment involve coagulation-flocculation, sedimentation, and filtration, which produced more precipitates or wastes referred to term drinking water treatment sludge [2]. The process of coagulants for water purification is used chemical materials to separate the solid- liquid in the treatment process [3, 4]. The materials are used in the coagulant process as Aluminium salts (e.g., Al2 (SO4)3.18H2O, Poly-aluminum chloride) or Fe salts (e.g., FeCl3.6H2O, FeCl2, FeSO4.7H2O) [5, 6]. The disposal sludge method has become most common in landfills, which is more expensive, and is against environmental laws [1, 7]. Therefore,
4 Professor, Civil engineering Department, Faculty of Engineering, Fayoum University, Fayoum, Egypt
the efforts for the utilization of sludge strategies would supply a safe and sustainable solution to sludge [3]. THE development of strategies for sludge reconnoitered the potential of using sludge as an ingredient construction material in preparing concrete and mortar, instead of disposal in landfills [8]. The sludge has been applied as filler material to ceramic and bricks products [9-11]. Besides, the feasibility of applying sludge to produce lightweight aggregates [12, 13], sand substitute supplementary cementitious material containing organic matter and heavy metals as alumina-siliceous [14,15 ]. Authors reported that the
use of sludge was treated at 105 for 2h [16, 17]. This
treatment method was more friendly and environmentally and
saved energy due to low-temperature requirements and no emission of greenhouse gas [2, 18]. However, most of the studies demonstrated the addition of sludge content could decrease the strength [19]. It is worth mentioning that sodium silicate, limestone powder, and silica fume improved the mechanical characteristics of concrete [20-22].This paper, therefore, aims to study the mechanical properties, scanning electron microscopy (SEM), energy dispersive X-ray (EDX), and mapping of concrete. This paper also aims to study the
effect of using sludge after heated treatment at200, 300, and 500 as partially replacing cement with 0%, 5%, 10%,
15%, 20%, and 25 wt%. The influence of sodium silicate, un- hydrated lime and silica fume with a ratio of 10%, 5% and 10%, respectively, on using sludge after heated treatment at
200 as partially replacing cement with 0%, 5%, 10%, 15%,
20%, and 25 wt%.
-
MATERIALS
A. Ordinary Portland cement (OPC)
Cement was produced with CEM I 52.5N according to ASTM
G. Fine aggregate
Fine aggregate was river sand. According to ASTM C128, it was 4.75 mm nominal maximum size, 2.65 specific weights,
3
C150 by Misr Beni Suef Company (MBSC), Egypt. The
1.85 t/m
bulk density, and 2.4 fineness modulus.
specific gravity, fineness, and surface area of OPC were 3.15, 3500 Cm2/g, and 3210 cm2/g. The chemical properties of cement are in Table (1).
Oxide
SiO2
Fe2O3
K2O
Na2O
CaO
Al2O3
TiO2
MnO
P2O5
SO3
MgO
CL
H2O
LOI
Cement
20.55
3.62
0.23
0.52
60.95
5.35
–
–
–
2.81
1.03
0.08
–
–
sludge
42.4
10.97
0.73
0.54
4.91
14.57
1.21
0.45
0.72
2.75
1.61
0.24
–
18.62
lime
1.62
0.2
0.03
16
70.9
0.4
0.1
–
0.09
1.05
0.23
–
–
25.14
silica fume
96
1.44
1.2
0.46
1.2
1.1
–
–
–
0.23
0.18
–
0.87
–
TABLE (1): THE CHEMICAL OXIDE ANALYSIS OF CEMENT, SLUDGE, LIME AND SILICA FUME BY XRF (WT %).
-
Sludge (SL)
Sludge was obtained from the drinking and wastewater treatment plants in Egypt. SL was crushed into powders and was sieved through cement sieve #200. The specific gravity and surface area of SL were 2.22, and 756 Cm2/g. Sludge powder was heated treatment at various temperatures of 200°C, 300°C, and 500°C for 2 hours. The chemical compositions of sludge are in Table (1), according to ASTM C150.
-
Un-hydrated lime stone (LS)
The hydrated lime was obtained from a lime production plant in Cairo, Egypt. The specific gravity of lime was 2.24. The chemical compositions of lime are provided in Table (1).
-
Silica fume (SF)
Silica fume was supplied by Sika Egypt Company with a particle size was 0.1 µm. The specific weight of SF was 2.64. The Chemical oxide analysis of silica fume is in Table (1).
-
Sodium silicate solution (S.S)
Sodium Silicate (Na2SiO3) was bought in the liquid state. The chemical composition included 32% SiO2, 16% Na2O, and 62% H2O.
-
Coarse aggregate
Coarse aggregate was basalt from the Eastern Desert of Egypt. According to ASTMC127, Basalt was 22.50 mm the nominal maximum size, 2.65 specific weights, 1.6 t/m3 bulk density, and 1.8% absorption.
H. Water
The casting and curing process used freshwater.
-
-
MIX PROPORTIONS
-
Mix preparation
Table (2) presents the mix proportions. Six different mixtures in each phase were produced according to ECP 203.
-
Phase (1): The partial replacement cement with sludge
after heat treatment at 200 at 0%, 5%, 10%, 15%, 20%,
and 25 wt%.
-
Phase (2): The partial replacement cement with sludge
after heat treatment at 200 at 0%, 5%, 10%, 15%, 20%, and 25 wt% with 10%sodium Silicate by weight of sludge
as a replacemnt.
-
Phase (3): The partial replacement cement with sludge
after heat treatment at 200 at 0%, 5%, 10%, 15%, 20%, and 25 wt% with 5% lime by weight as a replacement of
cement.
-
Phase (4): The partial replacement cement with sludge
after heat treatment at 200 at 0%, 5%, 10%, 15%, 20%, and 25 wt% with 10% silica fume by the weight as a
replacement of cement.
-
Phase (5): The partial replacement cement with sludge
-
after heat treatment at 300 at 0%, 5%, 10%, 15%, 20%, and
25 wt.%6.
Phase (6): The partial replacement cement with sludge after
heat treatment at 500 at 0%, 5%, 10%, 15%, 20%, and 25 wt%. Fig.1. presents the flow chart of experimental work .
TALE (2): THE MIX PROPORTIONS.
100
Phase
Mix Type
Cement (kg/ m3)
Sand (kg/m3)
Basalt (kg/m3)
Water (kg/m3)
SL
(kg/m3)
S S
(kg/m3)
lime (kg/m3)
S F
(kg/m3)
Control
A0
400
836.84
906.9
200
0
0
0
0
Phase (1)
Sludge after heat treatment at
200
A1
380
829.80
906.9
200
20
0
0
0
A2
360
822.77
906.9
200
40
0
0
0
A3
340
815.70
906.9
200
60
0
0
0
A4
320
808.65
906.9
200
80
0
0
0
A5
300
801.60
906.9
200
100
0
0
0
Phase (2)
Sludge after heat treatment at
200
B1
380
828.53
906.9
200
18
2
0
0
B2
360
820.21
906.9
200
36
4
0
0
B3
340
811.89
906.9
200
54
6
0
0
B4
320
803.58
906.9
200
72
8
0
0
B5
300
795.26
906.9
200
90
10
0
0
Phase
)3)
Sludge after heat treatment at
200
C0
380
830
906.9
200
0
0
20
0
C1
360
822.96
906.9
200
20
0
20
0
C2
340
815.91
906.9
200
40
0
20
0
C3
320
808.86
906.9
200
60
0
20
0
C4
300
801.81
906.9
200
80
0
20
0
C5
280
794.76
906.9
200
100
0
20
0
Phase (4)
Sludge after heat treatment at
200
D0
360
830.34
906.9
200
0
0
0
40
D1
340
823.29
906.9
200
20
0
0
40
D2
320
816.24
906.9
200
40
0
0
40
D3
300
809.2
906.9
200
60
0
0
40
D4
280
802.15
906.9
200
80
0
0
40
D5
260
795.1
906.9
200
100
0
0
40
Phase (5)
Sludge after heat treatment at
300
E1
380
829.8
906.9
200
20
0
0
0
E2
360
822.77
906.9
200
40
0
0
0
E3
340
815.7
906.9
200
60
0
0
0
E4
320
808.65
906.9
200
80
0
0
0
E5
300
801.6
906.9
200
100
0
0
0
Phase (6)
Sludge after heat treatment at
500
F1
380
829.8
906.9
200
20
0
0
0
F2
360
822.77
906.9
200
40
0
0
0
F3
340
815.7
906.9
200
60
0
0
0
F4
320
808.65
906.9
200
80
0
0
0
F5
300
801.6
906.9
200
0
0
0
-
Mixing and casting procedures
Fig. 2. presents the mixing and casting procedures. Mixing was performed in the mixer concrete in the laboratory. First, basalt and sand were put inside the mixer and mixed for 120 sec. Then, Portland cement and sludge were mixed with the mixture for 120 sec. The supplementary materials such as sodium silicate solution or lime or silica fume were added to the mixture for 180 sec. Finally, the water was added to the mixture for 240 sec until became a completely homogeneous mixture. The mixes were cast in special molds and were removed from the molds 24 h after casting. The specimens were moved to a moist curing tank in the lab that meets the ASTM C511.
FIG.1: THE FLOW CHART OF EXPERIMENTAL WORK.
FIG. 2: THE MIXING AND CASTING PROCEDURES.
-
A. Experimental Procedure
All specimens were measured for compressive strength, splitting strength, and flexural strength. According to ASTM C39, The compressive strength was conducted with six cubes (0.1×0.1×0.1) m. According to ASTM C496, the split tensile strength was measured with three cylinders (0.1×0.2) m at 28 days. The two point load flexural strength test was performed at 28 days on three beams with (0.1×0.1×0.5) m. In addition to SEM, EDX, mapping for mixture of 10% SL after heat treated at 500°C, 10% sludge after heat treated at 200°C, 10% sludge after heat treated at 300°C and 10% sludge after heat treated at 200°C and 10% S.F.
-
-
RESULTS AND DISCUSSION
-
Compressive strength
The compressive strength of sludge mixtures at 7 and 28 days is presented in Table (3) and Fig.3 (a) and (b). Overall, the compressive strength increases with an increase of sludge replacement up to 10% and then decreases with its increase up to 25% by weight. The compressive strength of samples
containing 10% sludge after heated treatment 200 was
330.21 kg/cm2 compared with 302.02 kg/cm2 for control at 28
days and the strength after curing for 7 days was more than that of the control. The increase in compressive strength is attributed to the formation of more hydrated products with curing ages, the accumulation of these hydrated products within the available pore spaces giving higher strength values
[14].5% and 10% sludge can act as a nucleating factor, which gives higher compressive strength at different curing ages; this is due to the formation of additional hydrated products such as that CSH and C-A-S-H created the reaction between liberated free portlandite, active silica Si+, and alumina- containing sludge. These hydrates improved compressive strength values [14]. The compressive strength of samplescontaining 10% sludge after heated treatment 300 and 500
were 490.11 kg/cm2 and 545.02 kg/cm2 compared with 330.02
kg/cm2 for 10% sludge after heated treatment 200. The results indicate that 5% and 10% sludge contents are the
optimum replacement ratios in all phases. Thus, the results of compressive strength stated that the percentages of the sludge at 7 and 28 days mixed with 10% sodium silicate, 5% un-
(A2). On the other hand, the results exhibited an improvement in compressive strength for the percentages of the sludge mixed with 10% silica fume about their peer with 10% sodium silicate and 5% un-hydrated lime. Silica fume promotes the hydration of cement, which increases the amount of CSH gel, thus improving the microstructure of pastes [29-31]. SF enhanced compressive strength due to the smaller size of SF particles than cement, which is 0.10.5 nm [32-32]. Thus, SF can fill the void between cement grains, leading to micro- filling which increases of compressive strength.
Compressive strength (Kg/cm2)
500
450
400
0%
350
hydrated lime, and 10% silica fume improved compressive
300
5%
strength compared with that the percentages of the sludge after
250
10%
heated treatment at 200. The results introduced that 10%
sodium silicate improved the compressive strength compared
with the mixtures of 0% sodium silicate at 7 and 28 days. Hou et al. [23] stated that Silicate Sodium formed sodium
200
150
100
50
0
Phase Phase Phase Phase Phase Phase
15%
20%
25%
aluminosilicate hydrate (NASH gel), which improved
1 2 3
4 5 6
mechanical properties. For instance, 5% sludge after heated
treatment at 200 with 10% sodium silicate (B1) was increased by 11.76% compared with 5% sludge after heated
treatment at 200 with 0% sodium silicate (A1) at 28 days.
treatment at 200 with 5% lime improved the strength relative
400
5%
to the mixtures of 0% lime. Besides, the lime powder
300
10%
The results also exhibited that the ratios of sludge after heated
FIG.3 (A): COMPRESSIVE STRENGTH AT 7 DAYS.
Compressive strength (Kg/cm2)
600
500
0%
contained CaO, SiO2, Al2O3, MgO, and Fe3O4, thus, lime powder created Ca (OH)2 and CSH gel, which is beneficial to the hydration of calcium silicates [2427]. For instance,
10% sludge after heated treatment at 200 with 5% lime (C2)
was increased by 11.15% compared with 10% sludge after
heated treatment at 200 with 0% lime (A2), at 28 days. In
200
100
0
Phase 1
Phase 2
Phase 3
Phase 4
Phase 5
Phase 6
15%
20%
25%
addition, the results shown that the ratios of sludge after heated
treatment at 200 with 10% silica fume enhanced the strength relative to the mixtures of 0% silica fume. For instance, 10%
sludge after heated treatment at 200 with 10% silica fume
(D2) was increased by 29.98% at 28 days compared with 10%
sludge after heated treatment at 200 with 0% silica fume
FIG.3.) B): COMPRESSIVE STRENGTH AT 28 DAYS.
-
Splitting tensile strength.
The splitting tensile strength of sludge mixtures at 28 days is presented in Table (3) and Fig.4. Obviously, the split tensile strength increases at 5% and 10% sludge and decreases with the increase of sludge up to 1525% by weight. On the other
hand, the results exhibited an improvement in split tensile strength for the percentages of the sludge mixed with 10% silica fume about their peer with 10% sodium silicate and 5%
lime. For instance, 5% sludge after heated treatment at 200
with 10% SS (B1) was increased by 11.14% compared with
5% sludge after heated treatment at 200 (A1) and 10% sludge after heated treatment at 200 with 5% lime (C2) and
10% SF (D2) was increased by 11.24% and 30%, respectively,
compared with 10% sludge after heated treatment at 200 (A2). The results exhibited an improvement in split tensile
strength for the percentages of the sludge after heated
treatment at 300 and 500 about their peer with the sludge after heated treatment at 200. For instance, 10% sludge after heated treatment at 300 (E2) and 500 (F2) was increased
by 48.52%, and 51.11%, respectively, compared with 10%
60
50
40
30
20
10
0
Splitting tensile strength
(Kg/cm2)
sludge after heated treatment at 200 (A2).
0%
5%
10%
15%
20%
25%
Phase Phase Phase Phase Phase Phase
1 2 3 4 5 6
FIG.4: SPLITTING TENSILE STRENGTH AT 28 DAYS.
-
Flexural strength.
Table.3 and Fig.5 show the flexural strength of sludge mixtures at 28 days. It was known that the Flexural strength increases at 5% and 10% sludge and decreases with the increase of sludge up to 1525% by weight. The results showedthat the flexural strength was improved by 5, 10, 15,
20 and 25% sludge at 200 with 10% silica fume about their
peer with 10% sodium silicate and 5% lime. For instance, 5%
sludge after heated treatment at 200 with 10% SS (B1) was
increased by 10.69% compared with 5% sludge after heated
treatment at 200 (A1) and 10% sludge after heated treatment at 200 with 5% lime (C2), and 10% SF (D2) was increased
by 11.21% and 29.99%, respectively, compared with 10%
sludge after heated treatment at 200 (A2) . On other hands,
the results of flexural strength for the percentages of the sludge
after heated treatment at 300 and 500 were improved compared with the percentages of the sludge at 200. For instance, 10% sludge after heated treatment at 300 (E2) and 500 (F2) was increased by 36.04%, and 54.34%,
respectively, compared with 10% sludge after heated treatment
60
50
40
10%
15%
Flexural strength (Kg/cm2)
at 200 (A2).
0%
5%
30
10
0
Phase 1 Phase 2 Phase 3 Phase 4 Phase 5 Phase 6
20
20%
25%
FIG.5: FLEXURAL STRENGTH AT 28 DAYS.
-
SEM& EDX& Mapping
The specified specimens of micrographs A2 (10% sludge after heat treated at 200°C), F2 (10% sludge after heat treated at 500°C), E2 (10% sludge after heat treated at 300°C), and D2 (10% sludge after heat treated at 200°C and 10% S.F) at 28 days by ZEISS apparatus for SEM, EDX, and mapping. Fig.6 exhibits large amounts of C-S-H and C-H gels that revealed homogeneity and bond strength. Fig. 6 (a) reveals the reason reduce of strength with increasing in the sludge ratios due to the presence of unreacted sludge at 10% sludge. In Fig.6 (b) presents the inner product (IP) that C-(A)-S-H gel. Fig.6 (c) exhibits large amounts of C-S-H gels that referred to the strong reaction between 10% sludge and SF. Fig.6 (d) and (e) shows that sludge after heat treatment at 500°C has hydration products(C-S-H ) more than sludge after heat treatment at 300°C, as shown in Fig.6 (f). The chemical analysis of EDS and mapping present large amounts of the main elements Ca,
Si, and Al in the binder matrix, as shown in Fig.7,8 and Table
(4) .
TABLE (3): THE RESULTS OF COMPRESSIVE STRENGTH, SPLITTING TENSILE STRENGTH, AND FLEXURAL TENSILE STRENGTH.
6000
O A2
5000 Si
Counts
4000
3000
Ca
2000
Phase
Mix Type
Compressive strength at
7 days (Kg/cm2)
Compressive strength at 28 days (Kg/cm2)
Splitting tensile strength at 28 days (Kg/cm2)
Flexural tensile strength at 28 days (Kg/cm2)
Control
Cont..
263.06
302.02
30.1
35.1
Phase (1)
Sludge after heat treatment
at 200
A1
265.6
305.31
30.6
35.34
A2
287.4
330.21
33.1
38.24
A3
239.5
275.45
27.6
31.87
A4
210.71
245.03
24.6
28.39
A5
202.13
231.91
23.3
26.88
Phase (2)
Sludge after heat treatment
at 200
B1
297.13
341.23
34.01
39.12
B2
274.6
315.32
31.42
36.54
B3
247.32
284.55
27.99
32.82
B4
217.58
250.12
24.92
28.21
B5
208.86
238.42
23.85
27.11
Phase
)3)
Sludge after heat treatment
at 200
C0
290.21
333.06
33.24
37.9
C1
297.81
342.21
34.31
39.63
C2
319.35
367.05
36.82
42.53
C3
275.35
316.11
31.70
36.62
C4
262.13
301.02
30.19
34.88
C5
228.12
262.21
26.29
30.36
Phase (4)
Sludge after heat treatment
at 200
D0
325.36
378.35
37.92
42.88
D1
343.91
395.11
39.63
45.77
D2
413.21
429.21
43.04
49.71
D3
313.62
359.22
36.01
41.6
D4
284.12
328.54
32.9
38.01
D5
261.23
300.41
30.09
34.76
Phase (5)
Sludge after heat treatment
at 300
E1
322.21
370.10
37.12
42.88
E2
426.71
490.11
49.16
52.02
E3
262.23
301.01
30.19
34.88
E4
261.2
300.41
30.09
34.76
E5
256.9
295.01
29.59
34.18
Phase (6)
Sludge after heat treatment
at 500
F1
361.35
417.11
41.83
47.3
F2
472.13
545.02
50.02
59.02
F3
337.21
387.22
38.82
44.85
F4
313.35
360.21
36.11
41.72
F5
287.38
330.15
33.10
38.24
1000 Fe Al
Mg
Ti Na
0
0.0 1.5 3.0 4.5 6.0 7.5 9.0 10.5
Energy [keV]
D2
o
6000
5000
ca
Counts
4000 si
3000
2000
Al
Fe
1000 Na
Mg
P Ti Mn
0
0 2 4 6 8 10
Energy [kev]
6000 E2
o
5000
4000 Si ca
Counts
3000
2000
1000 Na Fe Al
Mg
P
0
Mn Ti
0 2 4 6 8 10
Energy [kev]
6000
5000
Counts
4000
3000
2000
F2
O Ca
Si
1000 Al
Na Fe Mg
Ti P Mn
0
0 1 2 3 4 5 6 7 8 9 10
Energy [kev]
FIG. 7: EDS [A2 (10% SLUDGE AFTER HEAT TREATED AT 200°C),(2) D2 (10% SLUDGE AFTER HEAT TREATED AT 200°C AND 10% S.F,(3) E2 (10% SLUDGE AFTER HEAT TREATED AT 300°C),(4) F2 (10% SLUDGE AFTER HEAT TREATED AT 500°C)].
TABLE (4) :EDS OF SPECIMENS MATRIX.
Element
A2
D2
E2
F2
Weight
%
Atomic
%
Weight
%
Atomic
%
Weight
%
Atomic
%
Weight
%
Atomic
%
Oxygen
41.01
59.65
23.80
40.67
37.25
56.79
38.78
58.02
Aluminium
2.52
2.17
3.17
3.21
2.99
2.71
2.43
2.16
Silicon
21.53
17.84
21.07
20.51
14.21
12.34
17.42
14.84
Calcium
30.33
17.61
46.09
31.44
39.32
23.93
36.56
21.83
Sodium
0.63
0.64
1.06
1.26
1.54
1.63
1.01
1.05
Iron
2.70
1.12
3.38
1.65
3.08
1.34
2.55
1.09
Titanium
0.41
0.20
0.23
0.13
0.27
0.14
0.31
0.16
Magnesium
0.67
0.64
0.76
0.86
0.84
0.84
0.73
0.72
Potassium
0.21
0.13
0.23
0.16
0.31
0.19
0.18
0.11
Manganese
0.00
0.00
0.21
0.10
0.20
0.09
0.03
0.01
FIG. 8: MAPPING [(1) A2 (10% SLUDGE AFTER HEAT TREATED AT 200°C),(2) D2 (10% SLUDGE AFTER HEAT TREATED AT 200°C AND 10% S.F,(3) E2 (10% SLUDGE AFTER HEAT TREATED AT 300°C),(4) F2 (10% SLUDGE AFTER HEAT TREATED AT 500°C)].
FIG. 6: SEM[ (A,B): A2 (10% SLUDGE AFTER HEAT TREATED AT 200°C),( C):
ISSN: 2278-0181
Vol. 12 Issue 03, March-2023
-
(b)
(c) (d)
(e) (f)
FIG. 6: SEM[ (A,B): A2 (10% SLUDGE AFTER HEAT TREATED AT 200°C),( C): D2 (10% SLUDGE AFTER HEAT), (D,E): E2 (10% SLUDGE AFTER HEAT TREATED AT 300°C),(F): F2 (10% SLUDGE AFTER HEAT TREATED AT 500°C)].
-
-
CONCLUSION
The mechanical properties, SEM, EDX, and mapping were studied for drinking water treatment plant sludge powder after heated treatment at
200, 300, and 500 were partially replaced cement with 0%, 5%, 10%, 15%, 20%, and 25 wt%. SL after heated treatment at 200 with
0%, 5%, 10%, 15%, 20%, and 25 wt% was also replaced with 10% liquid sodium silicate. In addition, the substitution of cement with 5% un- hydrated lime and 10% silica fume at Sludge powder after heated
treatment at 200 with 0%, 5%, 10%, 15%, 20%, and 25 wt%. The
results can be concluded that:
-
Sludge is a Pozzolanic material can be used as partial replacement of cement.
-
The compressive, tensile, and flexural strength of concrete is improved by the incorporation of 5 % Sludge powder after heat
treatment at 200 and replaced with 10% SS. As sludge powder
increases up to 5% by weight, then the strength decreases.
-
The incorporation of 5% un-hydrated lime or 10% silica fume with
sludge powder after heat treatment at 200 can let the development of mechanical properties. However, with the increase in SL powder
at 10%, the mechanical properties are increased, but up to 10% SL powder by weight, the strength decreases.
-
The treatment of SL powder with increased heat has a positive
effect on its strength. The treatment of SL powder at 500 improved the strength compared with SL powder after heating at
200 and 300. However, 10 % SL powder after heated treatment at 500 increased by 80% the strength compared with 0%SL
powder and the strength decreased with the increase of sludge up to 1025% by weight.
-
The microstructure analysis revealed that 10% SL after heat treatment at 500°C tends to have a higher hardness.
REFERENCES
[1] L. Bernardo et al. Métodos e técnicas de tratamento dos resÃduos gerados em estações de tratamento de água,2012. [2] T. Ahmad, K. Ahmad, M. AlamSustainable management of water treatment sludge through 3 Rconcept. Journal of Cleaner Production,2016, 124: 1-13. [3] Y. Liu a et al. Utilization of drinking water treatment sludge in concrete paving blocks: Microstructural analysis, durability and leaching properties. Journal of environmental management, 2020, 262, 110352. [4] T. Ahmad et al. Sludge quantification at water treatment plant and its management scenario. Environmental monitoring and assessment,,2017,189(9), 1-10
[5] A. Sales et al. Mechanical properties of concrete produced with a composite of water treatment sludge and sawdust. Construction and Building Materials, 2011,25(6), 2793-2798 [6] A. O. Babatunde et al. Constructive approaches toward water treatment works sludge management: an international review of beneficial reuses. Critical Reviews in Environmental Science and Technology, 2007, 37(2), 129-164. [7] C. Suksiripattanapong et al. Compressive strength development in fly ash geopolymer masonry units manufactured from water treatment sludge. Construction and Building Materials, 2015, 82, 20-30. [8] A. Sarabia et al. Effect of the incorporation of residual sludge from water treatment on the technological properties of ceramic bodies: a review. J. Phys. Conf. , 2019, 1388. [9] A. Benlalla, et al. Utilization of water treatment plant sludge in structural ceramics bricks. Applied Clay Science, 2015,118, 171-177. [10] Y. P. Ling et al. Evaluation and reutilization of water sludge from fresh water processing plant as a green clay substituent. Applied Clay Science, 2017.143, 300-306. [11] J. Mañosa, et al. Valorisation of water treatment sludge for lightweight aggregate production. Construction and Building Materials, 2021,269, 121335. [12] C. H. Huang et al. Application of water treatment sludge in the manufacturing of lightweight aggregate. Construction and Building Materials, 2013, 43, 174-183. [13] S. E.Hagemann, A. L. G. Gastaldini, Synergic effects of the substitution of Portland cement for water treatment plant sludge ash and ground limestone: Technical and economic evaluation. Journal of Cleaner Production, 2019,214, 916-926. [14] H.El-Didamony, K.. A. Khalil, M. Heikal, Physico-chemical and surface characteristics of some granulated slagfired drinking water sludge composite cement pastes. HBRC journal, 2014,10(1), 73-81. [15] Z . Tang, W. Li, Y. Hu, J. L. Zhou, , V. W. Tam Review on designs and properties of multifunctional alkali-activated materials (AAMs). Construction and Building Materials, 2019,200, 474-489. [16] X. Fang, L.Wang, C. S. Poon, K. Baek, D. C.Tsang, S. K Kwok, Transforming waterworks sludge into controlled low-strength material: Bench-scale optimization and field test validation. Journal of environmental management, 2019,232, 254-263. [17] L. Wang, L.Chen, D. C. Tsang, J. S Li, , K Baek, D.Hou, C. S. Poon, Recycling dredged sediment into fill materials, partition blocks, and paving blocks: Technical and economic assessment. Jounal of Cleaner Production, 2018,199, 69-76. [18] R. H.Geraldo, L. F Fernandes, G.Camarini, Water treatment sludge and rice husk ash to sustainable geopolymer production. Journal of cleaner production, 2017,149, 146-155. [19] E.Nimwinya, W. Arjharn, S. Horpibulsuk, T.Phoo-Ngernkham, A.Poowancum, A sustainable calcined water treatment sludge and rice husk ash geopolymer. Journal of cleaner production, 2016 119, 128- 134. [20] D.Wang, C. Shi, N. Farzadnia, Z., Shi, H. Jia, A review on effects of limestone powder on the properties of concrete. Construction and building materials, 2018,192, 153-166. [21] M. A.Abd-ElAziz, , A. S. Faried, M. M. Kamel, Influence of silica fume incorporation on the fresh, thermal and mechanical properties of expanded polystyrene (EPS) foamed concrete. American Journal of Civil Engineering, 2017, 5(3), 188-195. [22] Fernández A Jiménez, T.Vázquez, A.Palomo, Effect of sodium silicate on calcium aluminate cement hydration in highly alkaline media: a microstructural characterization. Journal of the American Ceramic Society, 2011 94(4), 1297-1303. [23] D. Hou, Y. Zhang, , T.Yang, , J. Zhang, H. Pei, J. Zhang, T. Li, Molecular structure, dynamics, and mechanical behavior of sodium aluminosilicate hydrate (NASH) gel at elevated temperature: a molecular dynamics study. Physical Chemistry Chemical Physics, 2018 20(31), 20695-20711. [24] P . Lawrence, M .Cyr, E .Ringot, Mineral admixtures in mortars effect of type, amount and fineness of fine constituents on compressive strength. Cem Concr Res, 2005 35(6):10921105. [25] O . Mikhailova, G . Yakovlev, I .Maeva, S. Senkov , Effect of dolomite limestone powder on the compressive strength of concrete. Proc Eng , 2013,57(1):775780. [26] A . Nonat, Interactions between chemical evolution (hydration) and physical evolution (setting) in the case of tricalcium silicate. Mater Struct, 1994,27(4):187195. [27] G .Sezer, C. opuroglu O, K. Ramyar , Microstructure of 2 and 28-day cured Portland limestone cement pastes. Indian J Eng Mater Sci, 2010,17(4):289294. [28] Z.Zhang, B.Zhang, , P. Yan, Comparative study of effect of raw and densified silica fume in the paste, mortar and concrete. Construction and Building Materials, 2016,105, 82-93. [29] I.P. Sfikas, K.G. Trezos, Effect of composition variations on bond properties of self-compacting concrete specimens, Constr. Build. Mater, 2013,41,252262. [30] M. Khan, M. Cao, A. Hussain, S. H. Chu, Effect of silica-fume content on performance of CaCO3 whisker and basalt fiber at matrix interface in cement-based composites. Construction and Building Materials, 2021,300, 124046. [31] W.Xu, Y. Zhang, , B. Liu, Influence of silica fume and low curing temperature on mechanical property of cemented paste backfill. Construction and Building Materials, 2020, 254, 119305. [32] X.Wang, C. Gong, J. Lei, J. Dai, L. Lu, X. Cheng, Effect of silica fume and nano-silica on hydration behavior and mechanism of high sulfate resistance Portland cement. Construction and Building Materials, 2021 279, 122481.