
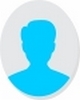
- Open Access
- Authors : Biljana Kostadinoska , Svetlana Risteska , Blagoja Samakoski
- Paper ID : IJERTV10IS010194
- Volume & Issue : Volume 10, Issue 01 (January 2021)
- Published (First Online): 11-02-2021
- ISSN (Online) : 2278-0181
- Publisher Name : IJERT
- License:
This work is licensed under a Creative Commons Attribution 4.0 International License
Influence of the Process Parameters on Manufactured Prepregs by Solvent Impregnation
Biljana Kostadinoska, M.Sc1, Svetlana Risteska, Ph.D1, Blagoja Samakoski, Ph.D1
1Institute of Advanced Composites and Robotics-Krusevski pat bb Prilep, Republic of North Macedonia
Abstract – The properties of prepregs are characterized in terms of their volatile content, resin content, the degree of pre- cure, void content, tack and flow ability. The most important properties of prepregs are resin content and volatile content. In order to monitor the resin content, a quantitative relation to the processing parameters such as line speed, viscosity and gap distance between the resin up taking rollers have to be determined.
In this study, a plain E-glass fabric with the areal weight of 300 g/m2 and an epoxy resin (CHS-EPOXY B200 M80/DCDA/2- MEI) were used to produce the prepreg by the dipping method.
The experimental results and showed that the resin content increased linearly with increasing the distance between rollers. In contrast, the resin content decreased with increasing the resin viscosity. According to our calculations, the effect of the line speed variation on the resin content was negligibly small. According to DoE calculations, the effect of the line speed variation and distance between rollers on the content of volatile was negligibly small, but the content of volatile decreased with increasing the resin viscosity (decreased the percent solvent in resin).
Keywords Prepreg; impregnation; DoE;
-
INTRODUCTION
Prepreg is the common term for a reinforcing fabric which has been pre-impregnated with a resin system. This resin system (typically epoxy/phenol) already includes the proper curing agent. There is a trend towards more extensive use of pre-impregnated or prepreg unidirectional and woven materials for the fabrication of larger composite component parts in the aerospace, sports and marine industries [3,4]. The use of prepregs has increased significantly in the last few decades. Thermoset prepregs with desirable tack and drape properties enable manufacturers to produce composites with complex shapes [1-20].
In the case of a solvent-type prepregs, the impregnated reinforcement usually passes through a heating oven to reduce the solvent content. The mixture would continue to react and lose solvent to a degree determined by the storage and handling environments. It is suggested that, to a certain degree, tack can be adjusted by controlling the volatile content of a prepreg. Though, a higher volatile content can increase the tackiness, it may also affect the viscosity profile during curing process and resulting in development of pores in the laminates [6,7]. The theory of deposition of a viscous liquid onto a moving substrate was first investigated in detail by Deryagin et all. [17] It was shown that, depending upon the influence of capillary effect, the maximum possible
thickness of a coating is proportional to a one-half or two- thirds power of the impregnation velocity.
J. Liu et all [10,18] studied that increasing the impregnation velocity is less effective than increasing the viscosity in achieving a higher resin content of prepregs for impregnation. Also, Liu at all. [10] studied that volatile content of prepregs is obtained as a function of the impregnation velocity and the heating length is also derived to give a possible combination of impregnation velocity and heating length to obtain a specific volatile content.
Prepregs manufactured by solvent coating often exhibit higher tack than comparable hot melt prepregs. Their tack is determined by parameters such as residual solvent content in the prepreg, temperature load in the tower, the resin system itself, and the fiber/fabric type [11].
Although the resin and volatile contents are very important in determining the quality of prepregs from one batch to another, very little has been said regarding the factors that are crucial in controlling quality during the impregnation process. In order to produce a prepreg material that possesses the desired specifications, knowledge of the machine design and operating procedures is required. The objective of the present work was to model a vertical impregnation process and to develop a relationship between the impregnation velocity,
resin content and volatile content.
-
EKSPERIMENT
-
Materials and equipment
For the manufacture of glass fabric prepreg were used following materials:
-
Glass fabric – UTE 280P glass fabric plain, 300gsm, wide 2000mm,
-
Epoxy resin type CHS-EPOXY B200 M80/DCDA/2-MEI – The dynamic viscosity of the resin mix, including solvent at the room temperature is in the range of 200-250 mPas.
In this study, samples were obtained by using an equipment for manufacture prepreg (direct film coat from resin), manufactured with machine from Mikrosam, Macedonia. Vertical Impregnation machine is designed as single step process for manufacturing of glass fabric prepreg materials as primary process.
The basic image of the process is presented on the following Fig 1 and Fig 2.
Fig. 1 Vertical impregnation lines.
-
-
Prepreg making equipment.
The Station is Equipped with single-shaft un-winder for unwinding the glass fabric. Impregnation Unit. For better impregnation there are several web guiding passages, allowing dwelling time adaptation to the required technology. Bath also has temperature regulating unit allowing it to maintain constant resin temperature.
Metering Unit equipped with two steel grounded and hard chromium plated rolls with micrometer accuracy and automatic gap adjustment. This unit is driven by AC servomotor, assuring high – control of resin pick-up. The coating unit is working on room temperature. The Curing Unit is consisted of single vertical drying channel with Heating Zone and temperature range from 60-150oC. The total length of the Curing Oven is 4m. The Cooling Unit is equipped with cooling table that is connected to the chilled water supply. The chilled water temperature range is 12- 16oC. Prepreg Rewinding Station unit is equipped with single
– shaft rewinder.
The drive system of the machine is consisted of AC servo motors equipped with gearboxes. This special selection of the servo system gives possibility of very fine controlling and regulation of the line speed into the required range of 1-10 m/min.
The whole process for producing this prepreg is given by Fig. 2 (a, b, c, d and e).
-
Unit for unwinding glass fabric (cloth)
-
Resin with deep impregnation resin and dosing rollers
-
Transport of the fabric with the resin (dressing) in the heating
tower
-
Weight measurement (surface weight or thickness) of inlet fabric and prepregs
-
Finished manufactured glass woven cloth
Figure 2. Manufacture of glass fabric prepreg with Li3000 machine manufactured by Mikrosam D.O.O
-
-
Design of experiment (DoE)
More and more factors have an influence on effectiveness and efficiency in the industrial processes and systems. To find the optimum in control of the processes there are often a lot of experiments to realize practical and theoretical ones. The preparation of the experiment was conducted in accordance with the 23 full factorial experimental design (DoE) by using of three parameters and two levels of variation. In the DoE, the gap roller was taken to be the first factor, the second factor was speed of tape, and the third factor percent of solvent in resin. The experimental designwas made on the Impregnation processes for obtaining of the determination of the factor levels and coding of the variables is conducted in accordance with Table I. Namely, for the first factor, the low and high levels are set at 0.35mm and 0.45mm, respectively, for the second factor at 1 and 6m/min, respectively, and for the third factor at 20% and 25%. Each factor has two factor levels, a low one and a high one. The low one has the value of (-1), the high one has a value of (+1). There are two factor levels with p = 2 and eight combinations (N= 8, Table II and III):
N = pk = 23 = 8 (1)
where: N = combinations; k = number of factors; p = number of factor levels.
They were made 8 combinations and each combination with 5 samples was tested as shown in Table IV.
TABLE I. CODING CONVENTION OF VARIABLES FOR ALL SAMPLES
Sample designation
Code
Coating unit (roller gap), mm X1
Speed, m/min X2
Solvent,
% X3
Zero level, xi = 0
0.4
3.75
22.5
High level, xi = +1
0.45
6
25
Lower level, xi = -1
0.35
1.5
20
TABLE II. FACTORIAL DESIGN 23
N
Experimental matrix
X0
X1
X2
X3
X1 X2
X1 X3
X2 X3
X1 X2X3
1
+1
+1
+1
+1
+1
+1
+1
+1
2
1
-1
+1
+1
-1
-1
+1
-1
3
+1
+1
-1
+1
-1
+1
-1
-1
4
+1
-1
-1
+1
+1
-1
-1
+1
5
+1
+1
+1
-1
+1
-1
-1
-1
6
+1
-1
+1
-1
-1
+1
-1
+1
7
+1
+1
-1
-1
-1
-1
+1
+1
8
+1
-1
-1
-1
+1
+1
+1
-1
The DoE allows making mathematical modeling of the investigated process in the vicinity of a chosen experimental point within the study domain. In order to include the whole study domain, we have chosen the central points (zero level, xi = 0) of both ranges to be experimental points (Table I). For the statistical analysis five tests of each combination were realized so the number of replications is five. An investigation of the effect of technological parameters on content of resin and volatile content in final material – glass fabric prepreg was performed (Table II and Table III).
During manufacture of prepregs, the resin solution temperature in the dip tank, squeezing rollers pressure in the
soaking zone and consecutive drying chambers temperatures were constants.
TABLE III. CONDITIONS OF THE EXPERIMENT
N
Factors
1 (mm)
2 (m/min)
3(%)
1
0.45
6
25
2
0.35
6
25
3
0.45
1.5
25
4
0.35
1.5
25
5
0.45
6
20
6
0.35
6
20
7
0.45
1.5
20
8
0.35
1.5
20
-
-
RESULTS AND DISSCUSION
A. Tests of prepregs- specimens with DoE
The resin content and volatile content of sample prepregs, were measured according to the ASTM D3529 and D3530 standard test methods [20,21,22]. Two square shape (10x10cm2) samples named A and B, were cut and weighed separately to the nearest 0.0001g to obtain the initial weight MA and MB. Part A was placed in the oven at 160°C for 10 min, cooled in desiccator and immediately weighed to obtain the weight MA1 Part B was dissolved in acetone for 10min, placed in the oven at 160°C for 10 min and weighed to obtain the weight MB1. Then it was placed in a muffle furnace at 600°C for 10 min and weighed to obtain the weight MB2. The volatile content (V%) and resin content (R%) of the prepreg were calculated by using Eq.:
V%=((MA-MA1)/MA)
x100…..(1) R%=(((MB(1-V)-MB2)/(MB(1-
V)))100…(2)
The results for volatile content (V%) and resin content (R%) of the prepreg, dispersion and minimal value of parameters final coefficients for factorial design 23 in this research are shown in Table IV and Table V.
y
y
The test results with five replications of each combination are presented in Table IV and Table V. The statistical parameters: the arithmetic means of the results and S 2 – the variance of the results was calculated at first. By implementing the 23 factorial experimental design we found out that the response function in coded variables, for resin content Y(R%) and volatile content Y(V%) of sample prepregs, is:
Y(V%) = 1.765+0.173X1+0.165X2+0.85X3+0.06X13
…(3)
Y(R%) =34.12+3.59X1+1.52X2-1.39X3+0.449X12- 0.36X13+0.59X23(4)
In the experimental design the terms X1X2, X1X3 and X2X3 are the interaction between the factors which might also have the influence on the response, but only in content resin in prepreg (Y R%).
TABLE IV. RESULTS OF THE EXPERIMENTS (DOE FOR R%)
Y exp R% |
Y cal R% |
Sy2 |
2 Sy sum |
2 Sy sum mid |
S2bi |
bi |
38.79 |
38.58 |
0.14 |
6.89 |
0.86 |
0.02 |
0.29 |
31.00 |
31.21 |
1.7 |
||||
33.14 |
33.35 |
0.293 |
||||
27.98 |
27.77 |
1.452 |
||||
40.68 |
40.89 |
1.39 |
||||
32.30 |
32.09 |
0.7 |
||||
38.24 |
38.03 |
0.2 |
||||
30.82 |
31.03 |
1.01 |
Y exp V% |
Y cal V% |
Sy2 |
S 2 y sum |
S 2 y sum mid |
S2bi |
bi |
3.02 |
2.85 |
0.026 |
0.23 |
0.03 |
0.001 |
0.05 |
2.59 |
2.38 |
0.004 |
||||
2.58 |
2.3 |
0.152 |
||||
2.26 |
2.50 |
0.013 |
||||
1.12 |
1.03 |
0.007 |
||||
0.99 |
0.81 |
0.009 |
||||
1.03 |
1.15 |
0.006 |
||||
0.53 |
0.69 |
0.0095 |
Y exp V% |
Y cal V% |
Sy2 |
S 2 y sum |
S 2 y sum mid |
S2bi |
bi |
3.02 |
2.85 |
0.026 |
0.23 |
0.03 |
0.001 |
0.05 |
2.59 |
2.38 |
0.004 |
||||
2.58 |
2.73 |
0.152 |
||||
2.26 |
2.50 |
0.013 |
||||
1.12 |
1.03 |
0.007 |
||||
0.99 |
0.81 |
0.009 |
||||
1.03 |
1.15 |
0.006 |
||||
0.53 |
0.69 |
0.0095 |
TABLE V. RESULTS FROM DESIGN OF EXPERIMENT (DOE FOR V%)
From design 23 were calculated Cochran criteria (Gcal) and Fisher criteria (Fcal), which fulfill the rule Gcal < Gtab and Fcal < Ftab for R% and V% with eq. from [19]. According to this, the hypothesis for model 23 is acceptable with 5% mistake for equation 3 and 4. By analyzing the regression equation (4), it should be noted that the main positive contribution to the Y(R%) is given by the coating – roller gap and the speed. The influence of the solvent % has a negative effect on the R%. The results by analyzing the regression equation (3) have conrmed the success of our approach of successive decreases volatile in prepreg.
The data from Larson et all. [23] suggests that resin content, similar to volatile content, is greater on the edges, with a lower average value in the center. It would seem appropriate that these two tests show the same trend such that if there is more resin on the edges of the fabric the volatile content should be higher as well. This phenomenon did not occur in the experiments during the production of this research. which means our machine design is well defined even though it was not the subject of this test. In liter [25] the number of impregnation rollers was found to affect only the characteristics of the prepregs manufactured with no tension. The experimental procedure described in liter. [27] and the obtained function of the factorial design leads to the conclusion that the parameter gap is very important for on content of resin in final product – prepreg, same as in this analysis.
V CONCLUSION
The experimental procedure described in the present work is suitable to study the influence of parameters on content resin and volatile content of thermoset prepreg by Impregnation process. It can conclude that high quality of prepregs made by Impregnation process depends on the processing parameters fed to the system.
A prepreging design of experiments (DoE) was utilized to fundamentally understand the effects that prepreg processing parameters and operation conditions have on prepreg impregnation. The prepreg was characterized by resin content and solvent content. From these characterization techniques, it became apparent that a relatively high gap, relatively low persectage of solvent in resin and medium web speed furnished the best results. A relatively high percent solvent of the resin solution in the dip bath reduces the viscosity.
An impregnation procedure was developed for E-glass bric cloth and epoxy resin which ensures the large-scale quality production of E-glass/epoxy prepregs. The results could be applied effectively to large scale production.
However, precise control of all process variables will add reliability in consistency of results.
ACKNOWLEDGMENT
The authors would like to acknowledge the support of the research team from Institute for advanced composites and robotics- Prilep and engineering team from Mikrosam D.O.O. Prilep (N. R. Macedonia).
REFERENCES
-
M.Rajaei, M. H. Beheshty and M. Hayaty Preparation and Processing Characterization of Glass/Phenolic Prepregs Polymers & Polymer Composites, Vol. 19, No. 9, pp. 789-796, 2011
-
S. Akbar, C. Yan Ding a , Irfan Yousaf b and Hayat M. Khan E- glass/Phenolic Prepreg Processing by Solvent Impregnation, Polymers & Polymer Composites, Vol. 16, No. 1, pp: 19-26, 2008 https://doi.org/10.1177/096739110801600103
-
Hayaty M, Beheshty MH, Esfandeh M, Cure kinetics of a glass/epoxy prepreg by dynamic differential scanning calorimetry, J Appl Polym Sci, 120, 62-69, 2011.
-
Hayaty M, Beheshty MH, Esfandeh M, A new approach for determination of gel time of a glass/epoxy prepreg, J Appl Polym Sci, 120, 1483-1489, 2011.
-
Gillanders AM, Kerr S, Martin TJ, Determination of prepreg tack, Int J Adhes Adhes, 1, 125-134, 1981.
-
K.J. Ahn, J.C. Seferis, T. Pelton, M. Wilhelm, Analysis and characterization of prepreg tack, Polym Compos, 13, 197-206, 1992.
-
K.J. Ahn, L.Peterson, J.C. Seferis, D.Nowacki, H.G. Zachmann, Prepreg aging in relation to tack, J Appl Polym Sci, 45, 399-406, 1992.
-
S.PanSart, L.Germanische, Advanced fibre-reinforced polymer (FRP)composites for structural applications: Prepreg processing of advanced fibre-reinforced polymer (FRP) composites, Industrial Services GmbH, Germany: Woodhead Publishing Series in Civil and Structural Engineering: Number 46, 2013, Part II pp. 125-154.
DOI: 10.1533/9780857098641.2.125
-
F.Wolff-Fabris,HLengsfeld, J. Krämer, Composite Technology Prepregs and Monolithic Part Fabrication Technologies: Prepregs and Their Precursors Composite Technology, Publisher: Carl Hanser Verlag GmbH & Co. KG, 2015, pp 11-25. https://doi.org/10.3139/9781569906002
-
J. Liu, D.G. Hwang, J.C. Chen, Development of a theoretical model for a solvent-type prepreg manufacturing process, Composite Science and Technology 51 Elsevier Science Limited (1994), pp- 359-366.
-
H. Lengsfeld and M.Turner Composite Technology Prepregs and Monolithic Part Fabrication Technologies: Prepreg Technology, Publisher: Carl Hanser Verlag GmbH & Co. KG, 2015, pp 27-45. https://doi.org/10.3139/9781569906002
-
M. Molyneux, Prepreg, tape and fabric technology for advanced composites, Composites. vol 14. No.2. pp.87-91, April 1983.
-
K.J.Ahn and J.C.Seferis, Prepreg Processing Science and Engineering, Polymer Engineering and Science, 1993, vol 33, No. 18, pp. 1177-1188.
-
Gruit, Epoxy prepreg Processing, 23 Nov. 2018, Available: https://www.gurit.com/-/media/Gurit/Datasheets/Prepreg-Processing-
Guide.pdf
-
T. A. Cender, P. Simacek, S. G. Advani, Resin Film Impregnation in Fabric Prepregs with Dual Length Scale Permeability, J. Comp.: Part A Vol.53,2013,pp.118-128.
http://dx.doi.org/10.1016/j.compositesa.2013.05.013
-
HexPly Prepreg Technology. Publication No. FGU 017. Hexcel Registered Trademark, Hexcel Corporation, 2013. http://www.hexcel.com
-
S. Shaghaghi, M. H. Beheshty and H.Rahimi,Preparation and Rheological Characterization of Phenolic/Glass Prepregs Iranian Polymer Journal pp. 20 (12), 2011, 969-977 http://journal.ippi.ac.ir
-
B.S.Hayes, Simulation Engineering of Polimeric Prepreg Composite Systems doctor dissertation, University of Washington, 1997.
-
. . and .. . . , ,1980.
-
Standard Test Method for Volatiles Content of Composite Material Prepreg, An American National Std. ASTM D3530, 2003.
- p>Standard Test Method for Matrix Solids Content and Matrix Content of Composite Prepreg, An American National Std. ASTM D 3529, 2003.
-
Standard Test Methods for Constituent Content of Composite Materials, An American National Std. ASTM D3171, 2003.
-
N. Larson, T. S. Chawla, Development of a Solvent-Based Prepreg Treater American Society for Engineering Education, 2015, Paper ID
#11329
-
B.S.Hayes and J.C.Seferis, The effect of fabric tension and the number of impregnation rollers on woven fabric prepreg quality and cured
laminates, Elsevier Science Limited Composite Part A28A, 1997, pp.791-799.
-
S. Capeska, S. Risteska, S. Samak, B. Kostadinoska, Impact of the technological parameters for the production of UD prepreg , KNOWLEDGE International Journal, Vol. 20.5 Bansko, December 2017, ISSN 2545-4439, pp 2319-2325
-
B. Kostadinoska, S. Risteska, B. Samakoski, S. Samak, N. Romevski Influence of process parameters in production of resin film on Kevlar fabric prepreg – ICAT'19 8th International Conference on Advanced Technologies, Bosnia and Herzegovina August 26-30, 2019 Sarajevo. Web proceedings E-ISBN: 978-605-68537-4-6,pp-309-315(2019).