
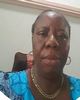
- Open Access
- Authors : Okiemute Grace Erhimona
- Paper ID : IJERTV12IS050002
- Volume & Issue : Volume 12, Issue 05 (May 2023)
- Published (First Online): 06-05-2023
- ISSN (Online) : 2278-0181
- Publisher Name : IJERT
- License:
This work is licensed under a Creative Commons Attribution 4.0 International License
Influence of Welding Processes on the Exposure of Duplex Stainless Steel Alloy 2205 Using Gas Tungsten Arc Welding and Gas Manual Arc Welding
Okiemute Grace Erhimona
Department of Welding Engineering and Offshore Technology, Petroleum Training Institute, Effurun Warri – Nigeria
Abstract – In this work, an investigation on the influences of welding processes on the exposure of Duplex stainless steel (DSS) Alloy 2205 using Gas Tungsten Arc Welding and Gas Manual Arc Welding was carried out. The Duplex stainless steel (DSS) Alloy 2205 containing 22%Cr, 5%Ni, ferritic-austenitic material is an emerging class of stainless steel currently being selected for a variety of applications especially where corrosion is of major concern. It have good mechanical properties and high resistance to all forms of corrosion combined with its high strength-to-mass ratio. These properties allow for savings both in terms of structural weight and maintenance costs. In this work, the Gas Tungsten Arc (GTAW) and the Shielded Metal Arc (SMAW) welding processes were used to weld a 200mm x 16.53mm thick duplex alloy 2205 stainless steel pipe to determine which of the processes will cause susceptibility of the alloy to intergranular corrosion at the grain boundaries. Various tests were carried out on transverse specimens cut out from the welds made with both processes. These tests included metallurgical, compositional analysis across the weld profiles, hardness, and tensile test. The test results for the compositional analysis showed an insignificant depletion of chromium from 22.06 at the weld cap to 19.96 at the root of the TIG weld. This depletion is not enough to cause sensitization although there were likely precipitates in the weld and HAZ from the Microstructural analysis. The hardness across the welds profile revealed that there was a uniform distribution of hardness across the MMA weldment when compared to the TIG weld which dropped drastically at the weld metal region from 337.2 and 328.7 to 256.5 and 252.0 at the face and root respectively. The mechanical properties of both welds have not shown any major deviations from the standard Alloy SAF 2205 properties. They are within the acceptable range. The test results obtained indicated that with proper control and monitoring of the welding parameters, the SMAW can be effectively used to weld the Alloy 2205 with comparable high quality of properties.
Index Terms Stainless, Gas tungsten arc welding, duplex stainless steel, Gas manual arc welding
-
INTRODUCTION
Duplex stainless steels (DSS) are used in applications where their superior corrosion resistance, strength, or both are advantageous. They provide a broad range of corrosion resistance in various environments. They are the prime candidate for sour service application and as such, are now being used increasingly, especially in chloride or sulphide environment as an alternative to austenitic stainless steels. Their typical application is in the oil, gas and petrochemical industries. Due to their duplex microstructure and low carbon content, the wrought alloys have very excellent resistance to intergranular corrosion. Duplex stainless steels (DSS) are the preferred material for the petroleum and refining industry. They combine the characteristics of both ferritic and austenitic stainless steel SS. When properly welded, their composition ensures that austenite get reformed in the heat- affected zone (HAZ) after welding.
Weldments exhibit distinctive microstructural features that need to be identified and understood to be able to predict acceptable corrosion behavior during the service life of welded structures. The role of macro compositional and micro compositional variations, a feature common to weldments, will be examined. The results will be used in the comparative analysis of Duplex stainless steel welds made with the Gas Metal Arc Welding (GMAW) or Manual Metal Arc welding (MMA) and the Gas Tungsten Arc Welding (GTAW) or Tungsten Inert Gas (TIG) processes. The microstructures and micro compositions will be used to demonstrate how the sensitization due to heat effect can accelerate weldment corrosion in general and intergranular corrosion in particular in comparison to that of the wrought material.
Stainless Steel Weldment can be affected by all the classical forms of corrosion but are particularly susceptible to those affected by variations in microstructure and composition. The forms of corrosion include galvanic corrosion, pitting, stress corrosion, intergranular corrosion, hydrogen cracking and microbiologically influenced corrosion. The most common are localize corrosion since locally sensitized zones (i.e., regions susceptible to corrosion) often develop during the welding process. The local sensitization is due to the formation of chromium carbide along grain boundaries which can result in depletion of chromium in the area adjacent to the grain boundaries. This chromium depletion produces localized galvanic cells which if the reduction drops
the chromium content below 12 % wt. required in maintaining a protective passive film, the region becomes sensitized to corrosion. This is the initiation of intergranular corrosion that most often occurs in the HAZ and results in metal loss in the region parallel to the weld deposit. Intergranular corrosion is referred to as weld decay and is a common corrosion problem in stainless steel welds since chromium is one of the major alloying elements which help to prevent corrosion. Weld decay is characterized by a localized attack at an adjacent to grain boundaries with relatively little corrosion of the grains themselves and causes alloy disintegration (grains fall out) and consequent loss of strength. Intergranular corrosion can also be caused by the segregation of impurities at the grain boundaries and the enrichment or depletion of one of the alloying elements in the grain boundary areas. When such a material is exposed to a corrosive environment, the grain interfaces of the sensitized alloy become very reactive compared to the grains themselves resulting in intergranular corrosion.
-
BACKGROUND
Welding is an important fabrication technique for stainless steels and various guidelines have been provided by Patterson and Fager, (1995), Davison (2000), Avesta Welding (2004) and Messer, et al, (2007) for the welding of duplex stainless steel. These guidelines provide insights into the techniques and precautions needed to weld these materials successfully. Davison (2000) affirmed that the Duplex Stainless Steel and the Alloy 2205 are generally considered weldable due to their low carbon content although their successful welding depends on many rules and precautions that must be followed to ensure that the welds maintain the wrought microstructure as much as possible and are free of defects. Problems are common during fabrication and eventually in service when the proper procedures are not followed. According to Lippold and Kotecki (2005), the problems often encountered in welding these steels are associated with improper control of the weld microstructure and related properties. Therefore the aim in welding the Duplex stainless Steel (DSS) is to achieve a weld metal and heat-affected zone (HAZ) that retain the corrosion resistance, strength, and toughness of the base metal. The design of welding procedures are for the welding to lead to a favourable phase balance after welding in the weld and Heat Affected Zone (HAZ) and to prevent the precipitation of detrimental intermetallic or nonmetallic phases. Maximum corrosion resistance and mechanical properties in a Duplex Stainless Steel (DSS) weldment are acheved when the phase balance of ferrite to austenite is 50:50 but this is in most cases difficult to achieve in practice. The difficulty could be traced to the many variables such as metal chemistry, welding processes, and thermal history of the steel but the study of Lippold and Kotecki, (2005) have shown that Duplex Stainless Steel (DSS) will have optimal corrosion resistance and mechanical properties when 35 to 60% ferrite content is maintained throughout the weldment. The microstructure and properties of the Heat Affected Zone (HAZ) which is altered by inducing intensive heat into the parent metal during welding is expected to have comparable corrosion resistance and impact toughness of the base material minimum requirements. The low heat input welding processes and high thermal conductivity of Duplex Stainless Steel (DSS) and Super Duplex Stainless Steel (SDSS) make them to exhibit a narrow-HAZ, in comparison to Austenitic Stainless Steel. Typically an austenitic-SSs HAZ is shown to be in the order of 500 µm in width (approximately 20 grains) but a DSS HAZ is often as small as 50 µm in width (2 grains).
The morphology of a DSS HAZ is therefore more important than estimating (- values). Their research have also illustrated that a low heat input welding process has sufficient heat to promote the transformation of discontinuous ferrite in the HAZ. This structure contributes to the fine grain size responsible for an increase in the toughness of the region therefore, warned that caution is necessary when using too low a heat input associated with rapid cooling as this will produce a narrow and predominantly ferritic HAZ. Having sufficient micrographs demonstrating the presence of discontinuous ferrite in the HAZ may be required to ensure a robust welding process.
Although Duplex steels have good weldability and can be welded using many of the welding methods used for austenitic stainless steel, they are more prone to the precipitation of sigma phase, nitrides, and carbides resulting in embrittlement and reduced corrosion resistance. Limitations are therefore associated with their welding which is on how to control the weld microstructure, associated properties and understanding how the weld metallurgy may influence the susceptibility to intergranular corrosion (IGC). The low carbon content in this alloy helps to avoid sensitization, while the addition of nitrogen helps to slow down the precipitation kinetics associated with the segregation of chromium and molybdenum during the welding process.
Welding with the Gas Tungsten Arc Welding (GTAW) or Tungsten Inert Gas (TIG) and the Gas Manual Arc Welding (GMAW) or Manual Metal Arc (MMA) involve different characteristics and also the welding techniques. Welding with the GTAW process affords greater control over the weld area than the GMAW process. The TIG process produces high-quality welds when performed correctly by a skilled welder, but it is more complicated and challenging to perform. The process is significantly slower than most other welding processes and uneconomical for many indigenous industries but it is mostly specified for quality welds. The SMAW is the most popular welding process Worldwide due to its versatility and simplicity. The process is associated with quality problems such as weld spatter, porosity, poor fusion, shallow penetration and cracking although these problems can be minimized through the use of a proper welding procedure and stiff process control.
-
RESEARCH PROBLEM
Although Gas Tungsten Arc Welding (GTAW) is frequently advised for all stainless steels and high-quality welds, it is very expensive, more difficult to perform, and difficult to learn. In order to save operating costs, the oil and gas industry needs high- quality welded joints. Apart from the purchase price, the DSS, a newly developed material, can be made available to most industries that want to reduce the cost of corrosion in their operations if it can be easily welded without issues of sensitization at the grain boundary that will result in intergranular corrosion in service by the more affordable SMAW process. Despite their numerous cost-saving benefits, the Duplex grade of stainless steel is only widely used by large multinational corporations in local businesses.
-
AIM AND OBJECTIVES OF THE STUDY
This work aims at the determination of the effect of the TIG and MMA welding processes on the susceptibility of duplex stainless steel alloy 2205 to sensitization at the weld Heat Affected Zone (HAZ) resulting in intergranular corrosion. The specific objectives include:
-
To weld a duplex stainless steel alloy 2205 pipe using the GTAW and GMAW welding processes with a standard welding procedure specification.
-
To conduct an assessment of the various weld sections within the duplex stainless steel weldment through mechanical and metallurgical test. The metallurgical structure, composition and mechanical properties will be assessed.
-
To evaluate the various test results and determine if any of the processes has caused Susceptibility to Intergranular corrosion as a result of sensitization at the grain boundaries of the Heat Affected Zones (HAZ).
-
-
METHODOLOGY
After etching with colloidal suspension of a 0.04um silicon diode, the parent material was first characterized by compositional analysis utilizing a Direct Optical Light Emission Polyvac Spectrometer (E980C). proving that the substance is duplex stainless steel, type Al 2205.
Specimen Preparation and Welding
The pipe was beveled as indicated above in the joint design of Fig 1. The preparation was done by machining and fitting carried out by tack welding in accordance with the WPS. The fitted pipes were welded together with both the Gas Tungsten Arc Welding (GTAW) and the Manual Metal Arc Welding (MMAW) processes. The ESAB AB multipurpose welding machine was used to weld following the welding Technique and parameters described in the WPS.
Figure 1: Sample of the specimen
Back gouging was carried out in the case of the GTAW during the root pass using argon gas to enhance root penetration. In each case, proper cleaning was carried out after each pass before subsequent beads were deposited. The weld temperature was allowed to cool to between 125oc and150oc for both processes before carrying the deposition of another bead since the recommended maximum interpass temperature is 150oc. The weld deposits comprise a root run, hot pass, filling and capping in both cases. The actual welding of the pipes and equipment are illustrated in appendix A. The ESAB AB machine is a multi-process welding machine that can be used to carry out three different welding processes depending on the equipment setup.
After the root run, the weld was allowed to cool to below 150oC before the next run was deposited. It was ensured that there was proper penetration at the root before the subsequent deposition. Cleaning was carried out using a stainless steel grinding disc and wire brush. The weld area temperature was measured using an industrial type thermometer to determine when to commence the next weld deposition (when the weld temperature drops below 150oC).
After the capping, the pipe was allowed to cool naturally and then visually inspected to see if there were any surface flaws. Once certain that there were no serious discontinuities or defects, the welded pipe was parted into smaller stripes transversely for further preparation for the various tests.
TESTS CARRIED OUT
The material was first prepared by parting the pipe into small pieces. This was done by machining the pipe followed by milling the surface of the pipe. Further polishing was done before etching was carried out for some of the specific test specimen.
Metallographic Testing
This was done across the weldment to ascertain if there are precipitates or abnormal structures generated in any portion of the weldment as a result of a particular process.
A metallographic cutting machine was used tocut the test piece to the require size by parting from both ends and leaving the welded portion at the centre. The surface to be tested was ground with a grinding machine using a stainless steel grinding disc. Rotopol polishing machine was then used to polish the ground surface using grit papers: 80, 100, 220, 400, 600, 1000 and 1200. The grinding particles were removed using emery paper to be able to obtain a true microstructure that will aid accurate interpretation. Polishing was carefully done to ensure that no scratches of any form was introduced and left on the surface of the test piece. Two different microscopes were used; The ordinary microscope and the light optical microscope. Etching was also carried in two media.
-
Etching in ETHANOL, Hcl and CuCl and Colloidal suspension of 0.04 silicon dioxide and polishing with diamond suspension.
-
Etching using an etchant solution made up of; CuC12-2.5 grams, HCl-300ml, Distilled water-500ml, HNO3- 200ml, Saturated iron- III-chloride solution- 50ml. The etchant was applied by swabbing method for several seconds after which the sample was transferred to the microscope for snapping.
After etching, snapping was done using the two types of microscope after selecting the required magnification. Proper focus was ensured at the required specific test positions before the snapping was carried.
Hardness Testing
Vickers hardness testing was carried out across the weldment profile; i.e. Parent material, HAZ, Weld Cap, and Weld Root regions. For the various positions to be clearly visible, etching was carried out before the actual test. A ten kgf load was applied using 136o Diamond Pyramid at the test positions.
The test specimen was place with focus at a required position. The capstan nut was then used to raise or lower the table anvil to ensure that the specimen was placed centrally under the indenter. The test specimen was placed with focus at a required position. The capstan nut was then used to raise or lower the table anvil to ensure that the specimen was placed centrally under the indenter.
Tensile Testing
Transverse specimens prepared from the two processes were subjected to tensile load until fracture occurred with a UTM, Model- 602 Tensile Testing Equipment. The specimen were prepare in accordance with ASME IX test requirement.
Compositional Analysis
Compositional analysis was carried out to detect if there was depletion of any of the alloying elements in the course of welding with any of the welding processes across the weldment profile. The Direct Optical Light Emission Polyvac Spectrometer E980C Equipment was used. The samples were analyzed under High Chromium Program with 22 analytical channels. The setting standard used was SUS-Al with HCR12 standard.
-
-
RESULT AND ANALYSIS
Macro Analysis
The macrographs of the welds made with both process are shown in Figure 2.
Fig. 2: Macro Structures of MMA and GTAW welds respectively
The MMA macrograph showed a non-uniform bead and a crack. The weld profile confirms to the various quality problems associated with the process such as weld spatter, porosity, poor fusion, shallow penetration and cracking. These problems can be associated with the direct current characteristics of the electric arc which is usually deflected away from the weld pool by magnetic forces.
On the other hand, the macrograph of the GTAW showed good penetration and uniform bead profile. The uniform bead is an indication of an adequate heat input since the level of heat input affects weld quality. Low welding current and high speed will result in poor root penetration and also cause lack of side wall fusion. The lack of side wall fusion is caused by the weld bead lifting away from the surface of the metal. Excessive heat input will cause the weld bead to grow in width resulting in excessive penetration, and excessive weld width.
Microstructure Analysis
Two sets of micrographs were carried out using two different microscopes and etchants. The micrographs in Table 1 were done using ethanol, HCl, and CuCl. The parent material, weld metal, fusion line, and heat affected zone areas were examined to determine if there was microstructural variations across the typical weld profile for the welds made with the two processes. These set of micrographs show the basic structure of the duplex across the weldment.
Table 1: the results using the ordinary microscope at a magnification of 50um.
ZONES
PARENT MATERIAL
ROOT
HAZ
WELD CENTRE
GTAW
MMA
GTAW
MMA
GTAW
MMA
MICROGRAPHS
The weld roots structures are closer to the ones of the parent metal, but the GTAW weld shows a clearer duplex pattern. The weld root is assumed to be purely the filler metal as it had better penetration, but the Weld metal and HAZ either have micro-segregation or the patches seen are due to improper removal of etchant. The unclear nature of the micrographs could be due to improper focus.
Table 2: the micrographs taken with the light optical microscope after etching in colloidal suspension of 0.04 silicon diode.
ZONES
WELD INTERFACE
WELD METAL
GTAW
MMA
GTAW
MMA
MICROGRAGHS
The table shows the transitions between the welds and their heat affected zones. The change was more drastic for the MMA weld, moving from a fine grain structure at the weld to a very coarse grain structure at the HAZ. There are flakes/ dendritic structure at the weld portion of the GTAW weld which could be the formation of micro segregation or high-temperature intermetallic phases in the weld and heat affected zones regions according to Alvarez-Amas (2007). The occurrences of these structures can affect both the mechanical and corrosion properties of the weldment.
Hardness Test result
Table 3 shows the hardness test results for GTAW and MMA weld profile. It shows that the hardness value across GTAW weld is less at the weld region than any part of the weldment and also for the MMA weldment generally. The MMA weld hardness only dropped at the HAZ and generally has a more uniform distribution of hardness values across weld profile when compared to the TIG weld. The results indicatd that there was a more uniform heat distribution across the MMA weld during the process. The GTAW weld had a non-uniform hardness across the weld profile. The lower hardness at the weld region of the GTAW could mean more cumulative heat input was involved because interpass temperature for both processes was in the range of 120 to 150oC. The hardness value could be due to the effect of the multi-run weld and the deep penetration associated with the process. All hardness values for both processes are within the expected range since the expected hardness value for the alloy is 260HV although the hardness of the GTAW weld region were 256.5 for the face and 252.3 at the root.
Table 3: hardness result for both processes
MATERIAL TYPE
Parent Metal
Heat Affected Zone
Weld Metal
Heat Affected Zone
Parent Metal
WELD FACE
GTAW
337.2
286.2
256.5
340.0
337.0
MMA
330.8
312.6
306.2
303.5
342.7
WELD ROOT
GTAW
328.7
290.5
252.0
343.3
348.2
MMA
333.7
288.5
286.3
268.8
291.8
Tensile test
Tensile test was carried out on transverse specimen of weldment. Table 4. Shows the results of the tensile specimens. Both tensile test specimens fractured at the weld centre. The fracture load for the GTAW welded specimen is 821Mpa while that for the MMA
is 819Mpa. The elongations the specimens for both processes are lower than the 25 mm for the standard alloy 2205. The minimum expected Tensile strength of the alloy is between 680Mpa and yield strength 450MPA for the Sandvik duplex stainless steel.
Table 4: Tensile test result
Material Type
Yield Load (KN)
Yield Stress (MPa)
Tensile Load (KN)
Tensile Strength (MPa)
(%) Elongation
GTAW
129.8
805.7
132.3
821.2
21.1
MMA
125.4
726.9
132.0
819.4
20.5
SAF 2205
450-500
680-880
Compositional Analysis
The composition analysis of the weld profiles as shown in Table 5 indicated that the root of both welds maintained the carbon content of the filler material but chromium was depleted from 22.06 at the cap to 19.96 at the root of the GTAW weld. There was also the depletion of N from 0.13 at the cap to 0.107 and 0.123 at the cap to 0 0.09 at the root of the GTAW and MMA respectively. The depletion of Chromium and nitrogen at the root of the GTAW weld could result in the formation of chromium nitride in the weld root. The higher depletion of nitrogen at the root of the MMA weld can be attributed to lack of shielding with shielding gas which can lead to volatilization occur . Normally even with shielding gasses, loss are expected and 2% Nitrogen is added to the argon to compensate for the expected loss. This can be attributed to the reduction in loss of N in the GTAW weld that was back gouge with argon gas. There was depletion of Nickel from 8.79 at the weld cap of the MMA to 5.96 and 5.50 at the weld interface and HAZ respectively. The depletion is expected and is provided for in the filler metal having more Nickel than the parent metal but this will amount to the formation of more Ferrite at those regions. The Nickel has not depleted lower than the 5.5 of the parent metal. There was no appreciable depletion of molybdenum except at the root of the GTAW Weld. The depletions at the root of the GTAW weld indicates that the process experienced more heat and could affect the mechanical properties of the weldment.
Table 5: Result of compositional analysis
Comparative Analysis of GTAW and MMA welding processes
Table 6: Comparison of both processes on 2205 duplex Stainless steel
PARAMETERS
PROCESS
REMARKS
MMA
GTAW
Macro Structure
Possible Crater Crack and uneven weld profile
Good root penetration and even weld bead demonstrates greater control over the weld area.
GTAW is preferably used in the industry for rooting and the MMA for filling since it affords better root penetration. Inconsistencies in the MMA weld can accelerate corrosion in a corrosive environment.
Microstructure
Sharper structural transition at the fusion line (HAZ and Weld)
Possible presence of micro segregation/precipitates and flake like/dendritic structures at HAZ and Weld Metal.
The GTAW process may require lower interpass temperatures to avoid prolonged periods of high temperatures due to it being a slower process
Composition
Nitrogen depletion at Root (0.090) and Interface (1.00) from1.23 at Weld Cap.
Chromium depletion to 19.96 at the root. Slight depletion of molybdenum at root.
Nitrogen depletion in MMA root can be avoided by using shielding gases with 2% Nitrogen inclusion. There is the possibility of volatilization.
Tensile Strength
Fracture at center of the weld.
Fracture at centre of weld.
Comparable strength.
Hardness
Even distribution of hardness values across weld profile.
Uneven distribution of hardness values across weld profile and significantly low value at weld and HAZ.
MMA afforded better heat distribution around weld profile
Comparing both processes, the depletions of elements especially chromium is not sufficient to cause weld decay as could happen in austenitic stainless steel. Sensitization caused by the formation of chromium carbide along grain boundaries of stainless steel weld occurs when chromium is depleted from the region adjacent to the grain boundary that result in localized galvanic cells. The sensitization resulting in intergranular attack (preferential corrosion along the grain boundaries) will occur when the depletion drops the chromium content below 12 percent by weight (wt.) % required to maintain a protective passive film (Davis 2006).
-
CONCLUSION
-
The micrographs and compositional analysis of welds made with both welding processes (MMA and GTAW) have not shown any significant sensitization at grain boundaries of the HAZ.
-
The results of all mechanical test carried out are within the acceptable properties of the Duplex Alloy 2205. There were no major variations as a result of a process.
-
Effective monitoring of heat levels is necessary when using the GTAW process since it is a slower process to prevent
leaving the material at high temperature for more than necessary. A lower maximum interpass temperature than the recommended 150oc should be used especially for multipass welds.
-
The Duplex Stainless Steel can be effectively welded with the Shielded Metal Arc Welding process but needs stringent control of the welding parameters. The GTAW process achieved a better root penetration.
-
-
RECOMMENDATION
Based on the findings of the research work, the following recommendations are hereby made:
-
The use of the Duplex Stainless Steel DSS Alloy 2205 which is regarded as the workhorse of the Duplex class of stainless steel should be encouraged by making it available in the country. This will enable the indigenous oil and gas industry to take advantage of its numerous distinctive properties since it can be readily welded with the more affordable SMAW process without sensitization at the grain boundary that will result in intergranular corrosion while in service.
-
Further investigation needed to be carried out on the effect of dual process characteristics on weldment properties to justify its usage i.e. GTAW for Rooting and MMA for Filling and Capping since the GTAW process afforded a better root penetration.
-
The type of micro-segregations formed as a result of the use of either of the processes in welding the alloy needs to be understood to be able to identify the process characteristics that can lead to the formation of those inclusions and the factors responsible for their formation.
-
The weldments need to be subjected to a corrosive environment to further ascertain the process variation on the corrosion properties of the material since service characteristics can alter material conditions.
-
-
ACKNOWLEDGMENT
My sincere gratitude goes to my Supervisor Professor A.O.A. Ibhadode for his understanding, patient and seeing to it that this work got concluded. The efforts of technical staff of Standard Organization of Nigeria, Enugu State is also acknowledged.
REFERENCES
[1] American Welding Society (2004), Welding Handbook, welding processes Part 1. Miami Florida: [2] API Technical Report 938-C. (2005). Use of Duplex Stainless Steels in the Oil Refining Industry: American Petroleum Institute: First Edition. Washington, D.C. [3] ASM International® Corrosion (2000) Understanding the Basics, editor, p427-474DOI: 1361/cutb2000p427Copyright © All rights reserved. www.asminternational.org [4] Avesta Welding A B Outokumpu Stainless (2004) Welding Parameters for Duplex Stainless Steels AB, Avesta Research Centre Box 74, SE-774 22 Avesta,Sweden
[5] Barry Messer, Vasile Oprea, Andrew Wright (2007) Duplex stainless steel welding: best practices Fluor Canada Ltd. www.stainless steel world .net [6] Cassagne T, Busschaert F. (2007). Experience in duplex stainless steel in oil and gas production. In: Proc. 7th Duplex 2007 Int. Conf. & Expo, Grado, Italy. [7] Charles J (1991), super duplex stainless steels: Structure and properties. In: Proc. Duplex [8] Charles J (2000) 10 years later, obviously duplex grades in industrial applications look like a success store. In: Proc 6th Duplex 2000 Int. Conf. & Expo, Venice, Italy. AIM p. 1, [9] Claes-Ove Patterson and Sven-Åke Fager (1995) Welding practice for the Sandvik duplex 181s191s 81Sandviken, Sweden [10] Corrosion Resistance, Duplex Stainless Steel, ASM International, p 169189 [11] Davis, J R (2006), Corrosion of Weldments: ASM International® Materials Park, OH 44073-002. [12] DeBold TA, Martin J W, and Tverberg J C (1983) Duplex Stainless Offers Strength and [13] Fanica A, Bonnefois B, Gagnepain J C (2007). Welding duplex stainless steels: recent improvements. In: Proc. 7th Duplex 2007 Int. Conf & Expo, Grado,Italy. AIM
[14] Gideon B, Ward L and Biddle G (2008) Duplex Stainless Steel Welds and their susceptibility to Intergranular Corrosion. Journal of Minerals & Materials Characterization & Engineering, Vol. 7, No.3, pp 247-263, jmmce.org Printed in the USA. [15] Gooch T G (1983) Weldability of Duplex Ferritic-Austenitic Stainless Steels, Duplex Stainless Steels, ASM, p 573602 [16] Jacques S, Peultier J, Soulignac P (2007). Desalination plants: why using duplex stainless steels. In: Proc. 7th Duplex Int. Conf. & Expo, Grado, Italy. AIM [17] Kotecki D J (1993) Welding of Stainless Steels, Welding, Brazing, and Soldering, Vol. 6, ASM Handbook, ASM International [18] Lin, W. Lippold, J. C., and Baeslack, W. A. 1993. An investigation of heat-aected zone liquation cracking, 1: a methodology for quantication, WeldingJournal, 71(4): 135s153s
[19] Menendez H and T M. Devine, Weldability of Duplex Ferritic-Austenitic Stainless Steels, ASM, 1983, p 573602 [20] Menendez H and T.M. Devine (1990), the Influence of Microstructure on the Sensitization Behavior of Duplex Stainless Steel Welds, Corrosion, Vol. 46 (No.5), p 410417
[21] Mishra B, Olson D L and Lensing C (1998) The Influence of Weld Microstructural Features on Corrosion Behavior, The Third Pacific Rim International Conference on Advanced Materials and Processing (PRICM 3), TMS, 1998, p 23032308 [22] Nowacki J, Lukojc A (2005). Structure and properties of the heat-affected zone of duplex steels welded joints. J Mater Proc Tech 164-165: 1074-1081. [23] Nowacki J, Lukojc A (2006) Microstructural transformations of heat affected zones in duplex steel welded joints. Mater Charact; 56, 4-5: 436-441. [24] Ralph Davison (2000), Practical Guidelines for the Fabrication of Duplex Stainless Steel, International. Technical Marketing Resources, USA TAPPI journal 2000, volume 83, No.9. New York. [25] Ramirez, A J, Brandi S D, Lippold J C (2004) Secondary austenite and chromium nitride precipitation in a simulated heat affected zone of duplex stainless steels. Journal of Science and Technology of Welding and Joining Vol. 9 Issue 4, pp301-313 [26] Stainless steels SAF 2304, SAF 2205 and SAF 2507 AB Sandvik Steel, S-811, [27] Steklov (1972) Method of Evaluating the Influence of Non-Uniformity of Welded Joint Properties on Corrosion, Svar Proiz., Vol. 19 (No. 9), p 3436 Sweden (Revised August 1995) [28] Weman, Klas (2003). Welding processes handbook CRC Press LLC Pearson Education New York [29] www.astm.org January 2001 news letter [30] www.Shimadzu Corporation