
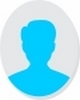
- Open Access
- Authors : Jinhai Jiang , Sen Xing
- Paper ID : IJERTV10IS110066
- Volume & Issue : Volume 10, Issue 11 (November 2021)
- Published (First Online): 17-11-2021
- ISSN (Online) : 2278-0181
- Publisher Name : IJERT
- License:
This work is licensed under a Creative Commons Attribution 4.0 International License
Intelligent Control System of IoT Production Line Based on Niagara
Jinhai Jiang, Sen Xing
School of Mechanical Engineering Tianjin University of Technology and Education
Tianjin, 300222, China
AbstractSmart factory is an important carrier for implementing smart manufacturing, among which production line intelligence is a necessary path for developing smart factory. This paper proposes a Niagara-based intelligent control system for IoT production line with IoT as the core, which combines expert PID control algorithm and stacked sparse self-coding to implement secondary development for automated production line, and achieves intelligent control of production environment temperature and humidity and fault prediction of production line under the premise of satisfying normal production of the production line. Based on the three-layer system architecture of IoT, it is supplemented by software for secondary development to make various module protocols perfectly compatible with each other and realize the production line intelligence.
KeywordsIntelligent control; Niagara; IoT; expert PID control algorithm; stacked sparse self-encoding
-
INTRODUCTION
Since the 21st century, new information technology has promoted innovation in the knowledge society; and knowledge innovation in turn will promote new technological development and transformation, which is the creation of "Internet+". The "Internet + manufacturing" is Industry 4.0, the essence of which is intelligent manufacturing, a concept proposed by Germany, known as "Industrial Internet" in the United States, and "Made in China 2025" in China. It is called "Made in China 2025"[1]. This also accelerates the intelligent transformation of China's traditional manufacturing industry.
The Internet of Things (IoT), as one of the fundamental technologies enabling smart manufacturing, has the characteristics of thorough perception, extensive interconnection and intelligent application [2]. Its various devices and technologies, such as various types of information sensors, RFID (radio frequency identification technology), and infrared sensing, can obtain the required information in real time. Through various types of network access, a ubiquitous connection is established between people, machines, and things to achieve interconnection. Thus, the goal of intelligent sensing, identification and management of the object process is achieved .
The automation line interconnects the machinery of traditional industrial production lines to form a production line that implements all processes of a product through automatic control, measurement and continuity. Using an industrial IoT platform, the line can collect up to tens of millions of
manufacturing data on time, thus monitoring and warning the operation of the equipment in real time. Currently, automated production lines have gained popularity because of their suitability for high-volume production and the stability and consistency of the production process. However, automated production lines are highly technical and require a specific level of expertise and specially trained personnel to operate and maintain them. Moreover, problems arising from the operation of automated production lines still need to be detected by professional technicians.
This paper proposes an intelligent control system for production lines based on the Niagara application framework development platform of Honeywell's subsidiary Tridium. The system combines expert PID control algorithms and stacked sparse self-coding to implement secondary development for automated production lines, which improves the above problems and realizes intelligent control of production environment temperature and humidity and fault prediction for production lines while satisfying the normal production of production lines.
-
OVERALL SYSTEM ARCHITECTURE
The system is an intelligent control system based on the Internet of Things, which realizes local intelligent control through Niagara application framework development platform and secondary development of the automated production line combined with expert system analysis method; and realizes remote real-time monitoring and remote control management through Niagara access to the cloud platform. The overall architecture of the system is shown in Figure 1.
Fig.1. The overall architecture of the system
This system has a simple operation page and a more intuitive data view, which allows managers to understand more clearly the operation status and overall running time of the production line and to adjust the production line according to the actual situation. The three-layer architecture of the IoT, consisting of the perception layer, the network layer and the
application layer, is the basis for realizing the intelligent control system of the production line [3]. The technical architecture of the IoT is shown in Figure 2.
-
Perception Layer
Perception recognition is the foundation and key technology of IoT, and the perception layer includes data acquisition sub-layer and sensor network networking. The data collection sub-layer realizes intelligent sensing recognition, information collection and intelligent control of the physical world, and is the link between the real world and the information world. The sensor network completes the communication and control of sensing nodes, routing nodes and network gateways.
Fig.2. The technical architecture of the IoT
The data acquisition sub-layer includes QR code tags and readers, RFID tags and readers, cameras, GPS, sensors, M2M terminals, sensor gateways, etc. The main function is to identify objects and collect information (such as temperature and humidity, item characteristics, equipment working parameters, geographical information, etc.), similar to the role of skin and five senses in the human body structure. The perception layer solves the problem of data acquisition in the human world and the physical world. Data from the external real world are collected through sensors, industrial cameras and other devices.
The sensor network networking and collaborative information processing sub-layer includes low and medium to high-speed proximity transmission technologies (ZigBee, WiFi, WSN, Bluetooth, infrared, industrial fieldbus, etc.), self- organization technologies, collaborative information processing technologies, and sensor middleware technologies to deliver data through short-distance transmission technologies.
In order to achieve the function of intelligent control of the production line, the system must obtain accurate real-time data. Sensors such as temperature and humidity, pressure, displacement, speed, etc. are used to accurately capture the working conditions around the production line as well as the operating parameters of industrial robots, machine tools and conveyors during the manufacturing process. Comprehensive monitoring and measurement not only expands the amount of data, but also makes the subsequent data analysis and processing more comprehensive and correspondingly more fault-tolerant. In addition to the sensors commonly used in
industry, vision sensors have been added that can be used for visual inspection. Vision sensors can acquire richer data simultaneously and perform multiple tasks simultaneously, while vision sensors also have extremely high sensitivity and a large dynamic range.
-
Network Layer
The network layer solves the problem of transmitting the data obtained by the sensing layer within a certain range, usually long distance, and mainly comletes the access and transmission functions, which is the data pathway for information exchange and transmission, and can rely on various existing communication networks, including public telecommunication networks and the Internet, and also industry-specific communication networks. Data communication is the core function of the network layer, which needs to ensure the lossless and efficient transmission of data, including communication protocols such as ZigBee, SigFox and Wi-Fi and other communication support functions of the layer. In addition, the network layer includes access to devices such as IoT gateways leave, device authentication and other device management and security management functions.
The network input layer of this system uses the Internet as a wide area communication network, Modbus, ZigBee, MQTT and other communication protocols access and bearer technology to realize the equipment and sensors, PLC, AP (wireless access point) and the upper computer software in turn connected. The PLC not only accesses data acquisition devices but also accesses production line execution end components, and adopts a short-range communication protocol such as ZigBee and MQTT. The PLC not only accesses the data acquisition equipment but also accesses the executive end of the production line, and uses Zigbee communication technology with short range, low speed, low power consumption and short delay to transmit to the AP to send and receive data to the server through the Internet to achieve two- way communication. The host computer achieves remote query and management functions through the MQTT protocol based on information distribution and subscription transmission between the client and the server [4].
-
Application Layer
Application layer is the interface between IoT and users, including application support sub-layer and IoT application sub-layer, which solves the problems of information processing and human-machine interface. The data transmitted from the network layer enters various information systems for processing in this layer and interacts with people through various devices. The processing layer consists of business support platform (middleware platform), network management platform (e.g. M2M management platform), information processing platform, information security platform, service support platform, etc. It completes the functions of collaboration, management, computing, storage, analysis, mining, and providing services for industry and public users. Typical technologies include middleware technology, virtual technology, highly trusted technology, cloud computing service model, SOA system architecture method and other advanced technologies. The application layer can provide
industrial control, smart city, telemedicine, intelligent transportation, smart home and other applications.
The large equipment, systems and instruments used in automated production lines are manufactured by different manufacturers and use different protocols, making data collection and transmission difficult. This increases the workload of production, management and operation and maintenance departments, and raises the cost of management and operation and maintenance. The system solves these problems with Niagara, an IoT middleware technology used to solve device connectivity problems. At the same time, the system implements data mining on the collected data to achieve intelligent control of production, and is privately customized to meet user needs, deeply integrating equipment operation environment monitoring, site monitoring, personnel and raw material management, etc., so that all departments in the factory reach data interconnection. Improve production and management efficiency and reduce the cost of operation and maintenance.
-
-
SYSTEM SOFTWARE FUNCTION IMPLEMENTATION
Niagara Framework is an open software framework platform developed by Tridium, a subsidiary of Honeywell Group. The platform seamlessly integrates devices with enterprise-class applications, enabling the integration, connection, management, and development of various protocols, various networks, and intelligent devices and systems on a unified platform [5]. This allows developers to connect with various embedded devices and systems without worrying about compatibility between communication protocols during application development, converting data and attributes of devices and systems into standard controls for information visualization and analysis. Niagara provides customers with a more practical because it allows pre-built standardized templates and then add modules on top of the standardized templates according to their needs. solution and also reduces the time for secondary development [6]. Likewise, Niagara makes it easier for developers to develop diverse application features through its open API library and other supporting tools.
In this system, some functions of the software are handled and processed outside the Niagara development platform, and the data results are transferred to the Niagara platform for secondary processing through the MQTT communication protocol.
-
Expert PID Algorithm Temperature and Humidity Control
This system adopts expert PID control algorithm for certain situations where the temperature and humidity of the production environment are required and the temperature and humidity control has characteristics such as hysteresis, nonlinearity and time-variability. This temperature and humidity control situation using conventional PID control can not guarantee the control accuracy and stability, the expected effect is not ideal. The introduction of expert control rules in the conventional PID rules makes this system have a certain degree of self-adaptability, which makes the system can regulate temperature and humidity more timely and accurately.
t, d are the middle value of the allowable fluctuation range of temperature and humidity set by the system; tc, dc are the actual greenhouse degree of the workshop; e(t),e(d) are the temperature and humidity errors. According to the actual error value, the system controls the output frequency of fan and pump through expert PID algorithm to control the temperature and humidity of the workshop independently. The following gives the control rules of a workshop temperature control when using an expert PID control algorithm.
-
When |e(t)|>M1, and e(t)e(t)>0, the
The absolute value of the temperature error is changing in the direction of increasing, when the error is relatively large, the controller should implement a stronger control role, when the PLC controller output as shown in equation (1).
() = ( 1) + 1{[() ( 1)] + () +
[() 2( 1) + ( 2)]} (1)In the formula (1): e(t) is the current sampling moment workshop temperature error; e(t-1) and e(t-2) are the previous and the first two sampling moments workshop temperature error; e(t)=e(t)-e(t-1) is the current sampling moment workshop temperature error change amount; f(k) is the current PLC controller output frequency; f(k-1) is the previous moment PLC controller output frequency ; M1 is the set error limit; k1 is the gain amplification coefficient (>1); k2 is the rejection coefficient (<1); kp is the proportionality coefficient; ki is the integral gain; kd is the differential gain.
-
When |e(t)|>M1, and e(t)e(t)<0, the absolute value of the temperature error is changing in the direction of reduction, and the control role of the controller should be reduced, at which time the PLC controller output is shown in equation (2).
() = ( 1) + 2{[() ( 1)] + () +
[() 2( 1) + ( 2)]} (2) -
When |e(t)|<M1, it means that the absolute value of the temperature error in the textile workshop has been small, in order to make the system have good steady-state performance to reduce the steady-state error, PI control should be used, at this time the PLC controller output as shown in the formula (3).
) = ( 1) + [() ( 1)] + ()
(3)
-
-
Production Line Equipment Failure Prediction
The system has real-time fault alarm and fault prediction functions. For the real-time alarm function, when the data collected by the sensors are transmitted to Niagara, an alarm message will be issued quickly when an abnormality is detected; the fault prediction is to predict the potential failure of the production line in advance. Before some regular failures
occur, the parameters of some key components of the production line often undergo important changes, and continuous collection of these data to build models can effectively carry out failure prediction.
This paper introduces a fault prediction algorithm using a variable speed gearbox in a production line as an example. Gearboxes are key components of production lines and are widely used in machine tools and industrial robots. At the beginning of a gearbox problem, it is often accompanied by mechanical shaft vibration, oscillation contact positioning accuracy degradation and other phenomena. For this reason, gearbox failure prediction can be achieved by analyzing data such as gearbox vibration and torque.
Stacked sparse self-coding is chosen to build the model in this system. Sparse self-coding is an unsupervised learning algorithm that does not require human extraction of data features. The autoencoder is a three-layer symmetric neural network consisting of input layer, implicit layer, and output layer[7], and its structure is shown in Figure 3. For a single- layer sparse self-coding network, with (W,b) and (W´, b´) denoting the weights and biases of the encoding and decoding layers, the encoding process is as follows:
(1) = ( + ) (4)
The decoding process is as follows:
= [´(1) + ´] (5)
In formula (5): f is the implied layer activation function, which is generally as follows
Fig.3. Structure of autoencoder
-
Niagara IoT Framework Development Platform
In the Niagara IoT framework development platform, data is integrated into the logic view developed within the workstation by creating different types of data nodes and interconnecting the human-machine interface with the production line equipment. In addition, the Palette library in the
=
=
1 1+
(6)
Niagara development platform provides a large number of
For the objective function a penalty term is introduced to achieve the sparse restriction with the following equation.
development components, and the required logic and function components can be directly dragged and dropped into the logic
1
() = {
1
2
=1
()
(,)
[()]2} +view. This graphical development mode not only reduces the difficulty of system development, but also shortens the system development cycle, so that developers can focus more on the
1
2 =1 =1
+1 () 2
[ ] +
[ ] +
=1
optimization of the system logic structure design. Part of the
logical view is shown in Figure 4.
=1
(||)
(7)
The parameters of the network are obtained by feeding the training data to minimize J(W, b) at this time. Multiple single-layer sparse self-coding networks are connected in the first place, and the output layer of the former layer is the input layer of the latter layer, which constitutes a stacked sparse self- coding network. The parameters of stacked sparse self-coding are trained in a layer-by-layer manner. We replace the decoding part of the trained network with a softmax layer to achieve fault prediction.
Fig.4. Production line part logic schematic
The Niagara development platform comes with a human- computer interaction development module, which can display the production line operation data in a simple and effective way. In order to monitor the operation status of the production line in real time, the main interface of the intelligent production line control system and the sub-pages of the equipment operation status are designed. As shown in Figure 5, you can clearly see the real-time temperature and humidity data in the production environment interface, as well as the operation
status of fans and pumps when the conditions are met. By clicking the button of the production line operation schedule, you can enter the production line operation time management interface as shown in Figure 6, through which you can confirm and adjust the production line operation time in real time. At the same time, when the production line fails, the equipment failure warning light will light up. By clicking the warning light icon, you can jump to the fault problem interface to view the fault status description. Similarly, when the fault prediction shows abnormal, you can click on the icon to jump to the fault prediction sub-interface to see which key components will fail, so that you can overhaul in advance to prevent the problem from occurring, The fault prediction interface is shown in Figure 7.The system has the traditional historical data curve and Alarm screen, and also supports the Internet web access, so you can easily access the production line intelligent control system through the common browser of cell phones and computers, and monitor the production line operation status in real time.
Fig.5. Production line working environment interface
Fig.6. Production line operation time management interface
Fig.7. Production line fault prediction interface
-
-
CONCLUSION
This paper proposes a Niagara-based intelligent control system for IoT production lines. Compared with the traditional automated production line, the proposed system is designed around the framework of IoT technology, collecting a large amount of data during the operation of the production line, combining the analysis method of expert system, and using expert PID control to make the production environment of the production line achieve intelligent control. The introduction of production line equipment fault prediction enables real-time prediction of key production line components in the production process, which can detect and eliminate faults in advance and reduce maintenance costs. Through the system's simple human-machine interface, production, maintenance and sales departments can easily and effectively monitor and manage the production process, improve efficiency and reduce operation and maintenance costs.
REFERENCES
-
Zhong, R. Y., Xu, X., Klotz, E., & Newman, S. T. (2017). Intelligent manufacturing in the context of industry 4.0: a review. Engineering, 3(5), 616-630.
-
Lee, In, and Kyoochun Lee. "The Internet of Things (IoT): Applications, investments, and challenges for enterprises." Business Horizons 58.4 (2015): 431-440.
-
Ngu, A. H., Gutierrez, M., Metsis, V., Nepal, S., & Sheng, Q. Z. (2016). IoT middleware: A survey on issues and enabling technologies. IEEE Internet of Things Journal, 4(1), 1-20.
-
Light, R. A. (2017). Mosquitto: server and client implementation of the MQTT protocol. Journal of Open Source Software, 2(13), 265.
-
Mehrotra, S., Kobsa, A., Venkatasubramanian, N., & Rajagopalan, S. R. (2016, March). TIPPERS: A privacy cognizant IoT environment. In 2016 IEEE International Conference on Pervasive Computing and Communication Workshops (PerCom Workshops) (pp. 1-6). IEEE
-
Li, F., Vögler, M., Claeßens, M., & Dustdar, S. (2013, June). Efficient and scalable IoT service delivery on cloud. In 2013 IEEE sixth international conference on cloud computing (pp. 740-747). IEEE.
-
Yin, Q., Duan, B., Shen, M., & Qu, X. (2017). Stacked sparse autoencoder based fault detection and location method for modular five- level converters. In IECON 2017-43rd Annual Conference of the IEEE Industrial Electronics Society (pp. 158-1585). IEEE.