
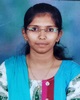
- Open Access
- Authors : Dhivyadharshini. V , Sri Krishna. R , Kamaleshwari. V
- Paper ID : IJERTV10IS090243
- Volume & Issue : Volume 10, Issue 09 (September 2021)
- Published (First Online): 08-10-2021
- ISSN (Online) : 2278-0181
- Publisher Name : IJERT
- License:
This work is licensed under a Creative Commons Attribution 4.0 International License
Investigation of Aerodynamic Efficiency on NACA 2412 Airfoil
1Dhivyadharshini.V, 2Sri Krishna.R, 3Kamaleshwari. V
Department of Aeronautical Engineering
1,2,3 UG Scholar
Nehru Institute of Engineering and Technology, Coimbatore.
Abstract:- Numerous researches are going on about drag reduction and improving the aerodynamic efficiency of flight vehicles, wind turbines automotive vehicles, etc., by adopting various methods. One of the basic reasons of drag is the formation of turbulent nature in the rear side of the airfoil and in turn creates pressure drag. The aim of this research paper is to choose best aerodynamically efficient airfoil. Smooth profile of an airfoil is altered by applying certain surface roughness in transition and turbulent boundary layer regions. This alters flow properties and results in reduced drag and increases aerodynamic efficiency. NACA 2412 airfoil in subsonic condition is considered. Airfoil with and without roughness are generated using modeling software. Surface roughness are created for two different shapes at two different positions on the upper surface of the airfoil. The models are then subjected to CFD analysis.
-
INTRODUCTION
-
AEROFOIL
An airfoil is the cross -sectional shape of a wing, blade or sail. An airfoil -shaped body moved through a fluid produces an aerodynamic force. The component of this force perpendicular to the direction of motion called lift. The component parallel to the direction of motion is called drag. Subsonic flight airfoils have a characteristic shape with a rounded leading edge, followed by a sharp with a trailing edge, often with a symmetric curvature of upper and lower surfaces. Foils of similar function designed with water as the working fluid are called AEROFOIL. The lift on an airfoil is primarily the result of its angle of attack and shape. When oriented at a suitable angle, the airfoil deflects the oncoming air, resulting in a force on the airfoil in the direction opposite and deflection. This force is known as AERODYNAMIC FORCE and can be resolved in to two components: LIFT and DRAG.
-
TYPES OF NACA SERIES
The NACA aerofoils are air foil shapes for aircraft wings developed by the NATIONAL ADDVISORY COMMITTEE FOR AERONAUTICS (NACA). The shape
of the NACA air foils is described using a series of digits following the word NACA.
1.2.1 FOUR DIGIT SERIES
The NACA four-digit wing sections define the profile by, 1.First digit describing maximum camber as
percentage of the chord.
-
-
Second digit describing the distance of maximum camber from the airfoil leading edge in tens of percent of the chord.
-
Last two digits describing maximum thickness of the airfoil as percent of the chord. The NACA 2412 airfoil has a maximum camber of 2% located 40% (0.4 chords) from the leading edge with a maximum thickness of 12% of the chord.
-
IMPACT ON ROUGHNESSFACTORON AEROFOIL
-
ROUGHNESS
Surface roughness often shortened to roughness, is a component of surface texture. It is quantified by the deviations in the direction of the normal vector of a real surface from its ideal form. If these deviations are large, the surface is rough; if they are small, the surface is smooth. In surface metrology, roughness is typically considered to be high frequency ,short wavelength component of a measured surface. However, in practice it is often necessary to know both the amplitude and frequency to ensure that a surface is fit for a purpose. Roughness plays an important role in determining how a real object will interact with its environment. Although a high roughness value is often undesirable, it can be difficult and expensive to control in manufacturing. ROUGHNESS can be measured by manual comparison against a surface roughness comparator, but more generally a surface profile measurement is made with a profilometer.
2.2 ROUGH SURFACE OF AN AEROFOIL
An experimental investigation on the effect of surface roughness on a NACA 2412 airfoils is performed. The experiments include measurements for the pressure distribution, drag co-efficient and lift co-efficient. Two different rough surfaces are analyzed and their data are compared to those over a smooth surface. Measurements are obtained for angle of attack in the range of 0 to 10 degree. Also, measurements of the velocity and turbulence intensity profiles are collected for the flow around the airfoil at various pre- chosen stations.
-
-
DESIGN AND MESHING
3.1 DESIGN
NACA 2412 aerofoil was designed by using CATIA software. CATIA V5 Version has been used for designing. The cord length of our NACA 2412 aerofoil is 15cm.Span
wise length of the aerofoil is 30cm long. Maximum camber thickness of aerofoil is 1.74cm. Then we designed a rough surface on NACA aerofoil at two different positions and two different shapes. The first position of roughness is created at 30% from leading edge shown in figure and second position of roughness is created at 50% from the leading edge shown in figure. Shapes such as rectangular and triangular roughness is created.
4.1 AIRFOIL AT 0o AOA
4.1.1 SMOOTH AIRFOIL AT 0o AOA
The airfoil at 0-degree angle of attack was analyzed by using the above boundary conditions and pressure distribution of an airfoil is shown in fig 4.1.1.1. where the values of CL and Cd are noted.
3.2 MESHING
Fig 3.1.1 NACA 2412 AEROFOIL
Fig 4.1.1.1 Pressure Distribution Over Smooth Surface At 0 AOA
The design of smooth and rough surface airfoil has been analyzed in fluent analyzer. Workbench 14.0 version has been used for analyzing. Rectangular domain is set for 30mm.
Fig 3.2.1 MESH FOR SMOOTH AIRFOIL
Fig 3.2.2 MESH FOR ROUGH AIRFOIL
The boundary conditions such as inlet, outlet, and wall have been set. Fine meshing is done for accurate results. The velocity is given as 32 m/s. The solution is allowed to run for 200 iterations.
-
ANALYSIS
The airfoil is analyzed for various angle of attack resultant pressure and velocity distributions had shown below.
Fig 4.1.1.2Velocity Distribution Over Smooth Surface At 0 AOA
4.1.2 ROUGH AIRFOIL AT 0o AOA
The airfoil at 0-degree angle of attack was analyzed by using the above boundary conditions and velocity distribution of an airfoil is shown in fig 4.1.2.1. where the values of CL and Cd are noted.
Fig:4.1.2.1Pressure Distribution Over Triangular Roughness at 50% of chord from LE At 0 AOA
Fig:4.1.2.2 Velocity Distribution Over Triangular Roughness at 50% of chord from LE At 0 AOA
-
AIRFOIL AT 50 AOA
-
SMOOTH AIRFOIL AT 50 AOA
The airfoil at 5-degree angle of attack was analyzed by using the above boundary conditions and pressure distribution of an airfoil is shown in fig 4.2.1.1. where the values of CL and Cd are noted. The CL and CD values are increased at 5- degree angle of attack.
Fig 4.2.1.1 Pressure Distribution Over Smooth Surface At 50 AOA
Fig 4.2.1.2 Velocity Distribution Over Smooth Surface At 50 AOA
-
ROUGH AIRFOIL AT 50 AOA
The airfoil with roughness at 50% of chord from leading edge at 5-degree angle of attack was analyzed by using the
above boundary conditions and pressure distribution of an airfoil.
Fig 4.2.2.1 Pressure Distribution Over Triangular Rough Surface At 50 AOA
Fig 4.2.2.2 Velocity Distribution Over Triangular Rough Surface At 50 AOA
-
-
-
RESULTS AND DISCUSSION
The CL/CD vs angle of attack shows theaerodynamic efficiency of rough is greater than the smooth airfoil is found using computational fluid analysis. The resultant graph was shown below.
Graph 5.1: CL/CD vs Angle of Attack
-
CONCLUSION
According to the results of Fluent analysis, the addition of surface roughness has proven to be effective in altering the flow properties. With such flow, the resultant lift and drag
force are also altered effectively. The triangular surface roughness on the trailing edge is proved to be the most suitable surface modification. Also, there is a reduction in total drag when the roughness is on the upper surface of the trailing edge (i.e.,) roughness from 50% of chord from leading edge. The graphs are plotted for CL/CD vs angle of attack. Thus, the roughness created on NACA 2412 airfoil shows better aerodynamic efficiency.
REFERENCES
-
Jaiwon Shin Characteristics of Surface Roughness Associated with Leading Edge.
-
Walid Chakroun,Issa Al Mesri Effects Of Surface Roughness On Aerodynamic Characteristics Of A Symmetric Airfoil.
-
R.L. Reuss,G.Mgregorek Effects Of Surface Roughness And Vortex Generators On The Naca 4415 Aerofoil.
-
A.A Abdel RahmenAnd W.M Chakrounin 1997 Surface Roughness Effects on Flow Over Aerofoil.
-
J.M. Janiszewskain 1997 Effects of Grit Roughness and Pitch Oscillations on The Airfoil.
-
D.W Bechart, W. Hage Drag Reduction with Riblets In Nature.
-
Z.Harun,A.A.Abbas,R.Mohammed, M.Ghazali Ordered Roughness Effects On NACA Aerofoil.
-
John A.Zalovolk And Clotaire Wood A Flight Investigation Of The Effect Of Surface Roughness On Wing Profile Drag With Transistion Fixed.
-
John E Matsson Aerodynamics Perfomance Of TheNaca 2412 Airfoil At Low Reynolds Number .