
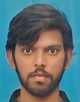
- Open Access
- Authors : Palisetti Sriram, P.Narendra
- Paper ID : IJERTV13IS010037
- Volume & Issue : Volume 13, Issue 01 (January 2024)
- Published (First Online): 21-01-2024
- ISSN (Online) : 2278-0181
- Publisher Name : IJERT
- License:
This work is licensed under a Creative Commons Attribution 4.0 International License
Investigation of The Strength and Durability Characteristics of Fiber-enhanced Ternary Blended Self-compacting Concrete
Abstract-
Palisetti Sriram
Department of Civil Engineering NRI Institute of Technology Vijayawada, A.P, India.
P.Narendra
Department of Civil Engineering NRI Institute of Technology Vijayawada, A.P, India.
used in the site for compaction of the concrete. But, compactions are not done properly in the sites and this affects the strength and durability properties of the concrete. To
The compaction of concrete is one of the prominent factors to be considered to obtain the desired strength of the concrete. The mechanical vibrators are mostly used in the site for compaction of the concrete. But, compactions are not done properly in sites and this affects the strength and durability properties of the concrete. The concrete that flows by its own weight is named as Self-Compacting Concrete (SCC). The flow ability of conventional concrete can be improved by developing or introducing self- compacting concrete. But the cost of SCC is very high due to the high cementitious content and super plasticizer. This high cost can be brought down by using the Supplementary cementitious materials (SCMs). Very fine particle size of these SCMs enables pore refinement in the concrete and subsequently improves both the mechanical and durability properties of the concrete. Various tests were conducted to evaluate the fresh, mechanical anddurability properties of the SCC. Total nine mixes are prepared for optimizing the mix namely (TBC 1 to 9).Ternary blended SCC mix (TBC9) containing 70% of Ordinary Portland Cement, 20% of fly ash, and 10% of silica fume has enhanced the mechanical and durability properties of SCC. Therefore TBC9 mix was considered as the optimized mix. The alkali-resistant glass fibers were added with the optimized mix (TBC9). The increase in the glass fiber content in TBC mixes decreases the compressive strength values. The addition of glass fiber in SCC increases the splitting tensile strength 17 % higher than the splitting tensile strength values of TBC9 mix. The glass fiber reinforced self- compacting concrete mixes increases the energy absorption values more than the optimized mix.
keywords Flyash; Self Compacting Concrete; Silica Fume; Supplementary cementitious materials; Mechanicial Properties.
I.INTRODUCTION
The concrete is one of the broadly used building materials in the world. The casting of concrete is a very simple method by mixing some locally available cement, fine aggregate, coarse aggregate and water which attains some required strength. However, the fresh and the hardened properties of un- designed concrete are unpredictable and it creates considerable issues in all aspects pertaining to the properties of the concrete. The compaction of concrete is one of the prominent factors to be considered to obtain the desired strength of the concrete. The mechanical vibrators are mostly
overcome all these defects due to compaction, a new concrete
is developed which is called as Self-Compacting Concrete (SCC). The concrete that flows by its own weight is named as Self- Compacting Concrete (SCC). The flow ability of conventional concrete can be improved by developing or introducing self-compacting concrete. The SCC has high flow ability and it leads the concrete to flow in any architectural structures and through congested reinforcement elements. The SCC was first developed in Japan to overcome the defects in concrete due to insufficient compaction and lack of skilled laborers. In 1990s, many researches in Japan and Europe countries focused on the field of SCC. The placing of SCC was comparatively easier than that of the conventional concrete. The main difference in the design of SCC is, the content of coarse aggregate is comparatively less than that of the fine aggregate. This reduces the blockage of concrete in the congested reinforcement.
The self-compacting concrete shall satisfy three basic requirements such as, filling ability, passing ability and segregation resistance (Paulo Ricardo et al. 2019) (Rahmat & Yasin 2012). The filling ability shows that the speed of the concrete flow by its own without any external force. The passing ability is an important property of SCC. The concrete can flow easily between the congested reinforcements without any segregation. SCC has to maintain its homogeneity during mixing and placing of the concrete in a structure without segregation and bleeding.
-
Advantages of SCC
-
SCC can flow and fill easily in the formwork by its own weight without any segregation and bleeding.
-
SCC is more suitable for architectural structures, congested reinforced structures, thin walls and deep foundations.
-
SCCdoesnotrequireskilledlaborsandensurefasterpac einconstruction.
-
SCC improves the durability properties of the concrete.
-
SCC reduces noise due to the absence of the vibrator.
-
-
supplementary cementitious materials.
The supplementary cementitious materials are suitable alternative material for the cement. The cost of SCC is very high due to the high cementitious content (300 600 kg/m3) as per EFNARC-2005 and super plasticizer. This high cost can be brought down by using the natural (metakaoline, RHA, etc.,) and artificial (fly ash, silica fume, GGBS etc.,) SCMs. Very fine particle size of these SCMs enables pore refinement in the concrete and subsequently improves both the mechanical and durability properties of the concrete (Kavitha et al. 2015). The addition of water initiates the reaction of SCMs with calcium hydroxide to produce C-S-H (Kavitha et al. 2015). The addition of SCMs decreases the cost of the concrete by reducing the cement content and improves the fresh, mechanical and durability properties of the concrete (Mostafa et al. 2015).
FlyAsh: Fly ash is the by-product of coal-fired power plants (Class F) and combustion of lignite or sub-bituminous coal power plant (Class C). Around 500 million tons of fly ash are produced per year (all over the world) and it is 80% of total ash produced in the world. The disposal of such huge quantity of fly ash creates an environmental harms and issues. Only 80 to 85 million tons of fly ash are utilized for cement manufacturing and other industrial purposes. The remaining quantities are disposed as landfills. The fly ash can be classified as C and F classes. The class C fly ash contains calcium oxide content up to 20% and Class F fly ash contains CaO content less than 5%. The formation of calcium silicate hydrate is high in the fly ash due to the high intensity of alumina and silica (Wgna et al. 2011).The replacement of fly ash in the cement content is effective up to 25% (by weight) (Mostafa et al. 2015). The High Volume of Fly Ash (HVFA) content in the concrete affects the heat of hydration process (Bilodeau & Malhotra 2000).
Silica Fume (SF): Silica fume is one of the by-products from silicon industries which have a high pozzolanic reactivity property. Moreover, the
fineness of SF is 20000 m2/kg which is 100 times smaller than that of the OPC (Samahbhanja & Sengupta 2003). The silica fume contains more than 80% of SiO2 content. The quantity of SF in the concrete is limited to 12.5% of total cement content (Rashid et al. 2002). The appropriate mix proportioning of SF blended concrete can attain extremely high compressive strength at early ages (Ali et al. 2012) and SF improves its durability by reducing the pores size of the concrete (Samahbhanja & Sengupta 2003). The main
disadvantage ofSF blended concrete is the requirement of high-water content due to its fineness and water reducing admixtures which are mandatory to maintain the desired water/cement ratio (Samahbhanja & Sengupta 2003).
-
ternary blended concrete
The ternary blended concrete are produced by combining of two SCMs and substitute in concrete as a partial replacement for the cement. The shortcomings in one of the SCMs can get counteracted by other SCM when they are blended (Deepa et al. 2012) (Murthi & Sivakumar 2008). The ternary blended concrete helps to reduce the environmental impacts by consuming a huge chunk of the waste materials. The ternary blended concrete with limestone (LS) and natural pozzolana / FA decreases the production cost and increases the environmental benefits (Kemal et al. 2015). The ternary blended concrete with SF and low reactivity BFS improves the durability properties of the concrete. The addition of BFS helped in reducing the water demand and hence the required dosage of the superplasticizer (Ali et al. 2012). The self- compacting concrete with PCE based superplasticizer attained robust flow retention at low temperatures (Wgna et al. 2011).
-
Fiber Reinforced scc
The concrete is strong in compression and weak in tension. The shrinkage cracks were developed in the early ages of concrete and this shrinkage cracks decreases the strength of the concrete. The concrete is a brittle material with low tensile stress and impact strength. To overcome these defects, the fibers are added in the concrete. The fibers are the tiny pieces of reinforcing material which in turn can reduce the shrinkage cracks and increases the mechanical properties of the concrete (Siva kumar et al. 2017). The combined effect of self- compacting concrete and fiber reinforced concrete is to form as a fiber reinforced self-compacting concrete. The fiber reinforced self-compacting concrete improves both the mechanical and durability properties of the concrete. The fibers are classified as natural (coir, cotton, jute, etc.,) and artificial fiber (steel, glass, polypropylene, etc.,) with different size and aspect ratio. An alkali-resistant glass fiber in the concrete reduces crack propagation and enhances the durability properties of the concrete (Rao et al. 2012). The addition of glass fiber in the concrete can increase the efficiency up to 0.8% by weight of cement and a large quantity of glass fibers reduces the flow ability of SCC (Manohar et al. 2012).
-
RESEARCH APPROACH
The Figure 1 shows the methodology of the present research work. After review of literatures, the materials were collected and their properties were assessed. The mix proportion of SCC was calculated by using IS: 10262 -2019 and ternary blended SCC mix proportions were arrived. The optimized ternary blended SCC mix was found by the mechanical and durability studies.
Selection of SCM & Determination of Material Properties
Mix Design, Fresh, Mechanical properties of TBC Mixes and Identification of Optimized Blend SCC
Effect of Glass Fibers & Conclusion
Figure-1: Research Approach
-
OVERVIEW OF PREVIOUS STUDIES
Chris & Goodier (2003) discussed the history, development, future scopes of self-compacting concrete in a detailed manner. They stated that the supplementary cementitious materials were suitable for both vibrated and non-vibrated (SCC) concrete. The physical and chemical properties of these SCMs had made some notable difference in the production of SCC. The differences created by SCMs can be adjusted by changing the degree of compaction in the vibrated concrete. They also reported that the practice was not suitable for SCC. It was also observed that the SCC needs high powder content to obtain cohesiveness.
Hajime & Masahiro (2003) investigated the mechanisms of SCC. The rational method of mix design was used in their research work. The coarse and fine aggregate were fixed as 50 and 40% (by volume) respectively. From the results, they observed that the water reducing admixtures (superplasticizer) were mandatory to attain the required SCC properties. The segregation of ingredients shall be avoided when the concrete flows in the congested reinforcement. The properties of self-compacting concrete were affected due to the flow of mortar, coarse aggregate volume, powder content and type of SCMs.
Jones et al. (1997) compared durability performance of ternary blended and normal concrete. From the experimental results they concluded that the ternary blended mixes showed good resistance to chloride ion penetration when compared with that of the normal concrete. The combination of two supplementary cementitious materials blended concrete improved the strength and durability properties of concrete more than that of the binary blended concrete.
Medhat & Michael (2006) studied the durability properties of ternary blended concrete containing fly ash (with different calcium content) and silica fume. The expansion of concrete after alkali-silica reaction was studied with different mix
proportions. The ternary blended concrete with fly ash (low calcium content) + silica fume showed less expansion after alkali- silica reaction when compared with that of the other binary and ternary blended concrete mixes.
Ylmaz et al. (1991) studied the performance of concrete with addition of glass fibers. They analyzed micro structural interface reactions by using EDAX and SEM analysis. From the results they concluded that the glass reinforced concrete increased the tensile strength. However, glass fiber reinforced concrete was not much effective as the normal reinforced concrete.
-
CHARACTERISTICS OF MATERIAL AND MIXING RATIOS
3.1 Properties of Cement and Cementitious Materials
Table 1 Physical properties of OPC 53-grade
Physical properties
Achieved Results
Specific gravity
3.12
Consistency
31%
Initial setting time
42 minutes
final setting time
250 minutes
Table 2 Chemical compositions of OPC 53-
grade
Chemical compositions
Values (%)
SiO2
20.56
Al2O3
5.05
Fe2O3
3.15
CaO
62.54
MgO
2.72
K2O
0.34
Na2O
0.38
Physical properties
Achieved Results
Specific gravity
2.12
Fineness
517 m2/kg
Bulk density
1134 kg/m3
Physical form
Powder
Color
Dark gray
Table 3 Fly Ash Physical Characteristics
Table 4 Chemical compositions of fly ash
Table 5 Physical Attributes of Silica Fume
3.3 Glass Fiber
Chemical compositions
Values (%)
SiO2
58.23
Al2O3
25.35
Fe2O3
6.24
CaO
2.67
MgO
1.36
K2O
0.84
Na2O
0.53
Alkali-resistant glass fiber with the aspect ratio of 857.14 was used in this investigation. The sample of glass fiber are shown in Figure 2 and the properties of glass fiber are tabulated in Table 8.
Fig 2 Glass fiber
Physical properties
Achieved Results
Specific gravity
2.26
Fineness
20000 m2/kg
Bulk density
656 kg/m3
Physical form
Powder
Color
Light gray
Table 8 Attributes of Alkali-Resistant Glass
Fiber
Physical properties
Values
Modulus of elasticity
72 GPa
Specific gravity
2.68
Filament diameter
14 micron
Length
12 mm
Aspect ratio
857.14
Chemical compositions
Values (%)
SiO2
94.4
Al2O3
0.62
Fe2O3
0.15
CaO
1.12
MgO
0.72
K2O
1.15
Na2O
0.22
Table 6 Silica fume Chemical Constituents
Constituent materials
Obtained design
mix value
EFNARC-2005
guidelines
Powder (Cementitious material)
514 kg/m3
380-600 kg/m3
Coarse aggregate
785kg/m3
750-1000 kg/m3
Fine aggregate
908 kg/m3
48-55 %
Properties
Values
Water
204 kg/m3
150-210 kg/m3
Type
Poly-carboxylic ether
Specific gravity
1.22 at 30 0C
Form
Liquid
Color
Light brown
Recommended dosage
0.6-1.5 litres per 100 kg of cement
Chloride content
Nil as per IS: 456-2000
3.2 Chemical Admixture
Poly-carboxylic ether based superplasticizer were used as a chemical admixture to improve the fresh properties of SCC. The properties of superplasticizers are presented in Table 7.
Table 7 Superplasticizer Traits and Attributes
3.4 MIX PROPORTIONS OF SCC
The M30 grade of self-compacting concrete mix was designed as per the guidelines of IS: 10262-2019. To maintain the desired fluidity and segregation resistance, the designed mix proportions were verified with the European Federation of National Associations Representing for Concrete (EFNARC-2005) guidelines. The superplasticizer dosage was determined by trial-and-error process and it is around 2.0% by weight of total powder content for all mixes. The normal SCC design mix (NM) is presented in Table 9.
Table 9 Design mix of SCC
Table 10 Properties of Water
Properties
Obtained values
Limits as per Code
pH Value
7.8
Shall not be less than 6.0
Chloride content
126
500mg/l
Total hardness
96
200mg/l
Total dissolved solids
160
2000mg/l
Table 12 Proportions of Ingredients in Ternary Blended SCC Mix
Mix
Cementitious materials
FA
kg/ m3
CA
kg/ m3
SP
kg/ m3
OPC (%)
F (%)
SF (%)
NM
100
0
0
908
785
10
TBC1
85
10
5
908
785
10
TBC2
82.5
10
7.5
908
785
10
TBC3
80
10
10
908
785
10
TBC4
80
15
5
908
785
10
TBC5
77.5
15
7.5
908
785
10
TBC6
75
15
10
908
785
10
TBC7
75
20
5
908
785
10
TBC8
72.5
20
7.5
908
785
10
TBC9
70
20
10
908
785
10
TBC10
70
25
5
908
785
10
TBC11
67.5
25
7.5
908
785
10
TBC12
65
25
10
908
785
10
TBC13
65
30
5
908
785
10
TBC14
62.5
30
7.5
908
785
10
TBC15
60
30
10
908
785
10
The M30 grade SCC mix proportion is shown in Table 11 and various ternary blended SCC mix proportions (TBC1 to TBC15) are given in Table 12. The total cementitious material content (OPC+ fly ash+ silica fume) was maintained as 514 kg/m3 for all the mixes. TBC 9 is obtained as optimum.
Cement
Fine Aggregate
Coarse Aggregate
Water
Weight (kg/m3)
514
908
785
204
Mix proportion
1
1.76
1.52
0.4
Table 11 Mixing Ratios for Normal Self- Compacting Concrete (NM)
Optimized ternary blended SCC (TBC9) was selected from the mechanical and durability properties. Glass fiber was added (0.2, 0.4, 0.6 and 0.8% weight fractions of total cementitious materials) to the optimized ternary blended SCC mix and Table 13 shows the mix proportions of glass fiber reinforced ternary blended SCC mixes (GFTBC1 to GFTBC4).
Mix
Cement (%)
FA (%)
SF (%)
Glass Fiber (%)
GFTBC1
70
20
10
0.2
GFTBC2
70
20
10
0.4
GFTBC3
70
20
10
0.6
GFTBC4
70
20
10
0.8
Table 13 Mix proportions of GF reinforced ternary blended SCC mixes
GFTBC1- Glass fiber reinforced SCC mix1 GFTBC2- Glass fiber reinforced SCC mix2 GFTBC3- Glass fiber reinforced SCC mix3 GFTBC4- Glass fiber reinforced SCC mix4
-
EXPERIMENTAL INVESTIGATION
1. Normal Consistency & Setting Times
The quantity of water required to make cement paste was determined from the consistency test. The Vicat apparatus was used to find the consistency of cement paste as per the guidelines of IS: 4031(Part4)-1988.
The setting time values are obtained by using Vicat apparatus as per guidelines of IS: 4031(Part5)-1988.
Table 14 Test Results of Consistency and Setting Times of Cement
Table 15 EFNARC-2005 guidelines
Properties of fresh SCC
Name of experiment
EFNARC-2005
guidelines
Filling ability
Slump flow test
550-800 mm
T500 mm Slump
2-5 seconds
Passing ability
L-box test
0.8-1.0
Segregation resistance
V-funnel test
8-12 seconds
V-funnel T5minutes
+3 seconds
Mix Id
Consistency Value (%)
Initial Setting Time (min)
Final Setting Time (min)
NM
31
42
220
TBC1
33
57
237
TBC2
34
57
261
TBC3
35
60
265
TBC4
35
66
287
TBC5
35
72
300
TBC6
37
74
307
TBC7
39
93
313
TBC8
39
99
319
TBC9
39
106
325
TBC10
42
112
341
TBC11
42
112
360
TBC12
43
124
370
TBC13
47
136
372
TBC14
47
148
393
TBC15
49
152
399
5.1 Slump Flow Test and T500 mm Slump Flow Time Test
The consistency value of OPC (NM) mix was 31%. The standard consistency values of TBC mixes were gradually increased with increase in fly ash and silica fume content. The ternary blended mixes required more water for consistency mix than the OPC mix. The high surface area of fly ash and silica fume increases the consistency value.
The initial and final setting time of OPC mix was 42 and 220 minutes respectively. The initial and final setting time of TBC mixes were in the range of 57 to 152 minutes and 237 to
399 minutes respectively. From the results, inclusion of SCMs in OPC increases the initial and final setting time.
-
FRESH PROPERTIES OF TERNARY BLENDED SELF- COMPACTING CONCRETE
A normal workability test was not suitable to study the fresh properties of the Self-Compacting Concrete (SCC). The foremost fresh characteristics of SCC such as passing ability, flow ability and segregation resistance were assessed by using slump flow test, T500 mm slump flow time test, L-box test, V-funnel test and V-funnel T5 minutes test as per the guidelines of EFNARC-2005. The fresh properties of normal SCC mix (NM), ternary blended SCC mixes (TBC1to TBC15) and glass fiber reinforced SCC (GFTBC1 to GFTBC4) were assessed by slump flow test, T500 mm slump flow time test, L- box test, V-funnel test and V-funnel T5 minutes test. EFNARC-2005 guidelines are presented in Table 15
Fig-3 Slump flow test
The filling ability of SCC was obtained by using the slump flow test and T500 mm slump flow test. The experiments were performed on the flat horizontal base plate and the base plate with 500 mm diameter circle was marked. The slump cone with 200 mm bottom diameter, 100 mm top diameter and height of 300 mm was placed in the center of the base plate. Approximately six liters of prepared SCC mix was filled in the slump cone up to the top level of the slump cone without any compaction and the excess concrete was removed. The cone was lifted vertically and allow the concrete to subside. At the same time the stop watch was started to measure the time taken by the concrete to cross 500 mm diameter circle (T500 mm slump flow time test). The experimental setup of slump flow test and T500 mm slump flow time test of SCC was shown in the figure 3.
5.2 L-Box Test
L-box is used to find the passing ability of self- compacting concrete. Passing ability of the concrete is measured by indicating the blocking ratio. L-shaped rectangular section with reinforcement bars are placed at the joint of horizontal and vertical sections
Fig 4- L-box test
The movable gate was fixed near the reinforcement bars to separate the sections. Figure 4 shows the experimental setup of L-box test. Around 14 liters of concrete was filled in the vertical section without compaction and allowed the concrete to stay for a minute in the vertical section. Then the gate was opened and the concrete was allowed to flow from the vertical to horizontal section through the reinforcement bars. The height of concrete in both the sections (H1 and H2) was measured. The blocking ratio was obtained from the ratio between H2 (Horizontal section) and H1 (Vertical section).
5.3 V-Funnel Test
The experimental setup for V-funnel test is shown in Figure 5. Twelve liters of concrete was mixed and filled in the V-funnel without any compaction. Then the lock at the bottom of the funnel was opened and the concrete was allowed to flow from the V-funnel under the gravity. The time taken for complete flow of concrete was noted as V-funnel time. The lock was closed immediately and again filled the V-funnel with same the concrete. After 5 minutes, the lock was released and the concrete was allowed to flow down. The time taken for complete flow of concrete was recorded as V-funnel T5minutes time.
Fig 5- V-Funnel test
Table16- Test Result of Fresh Properties
Mix Id
Slump flow (mm)
T500
mm Slump (sec)
Blocking ratio
V-
Funnel (sec)
NM
760
2.6
0.87
8.70
TBC1
772
2.7
0.85
9.20
TBC2
770
2.8
0.90
9.60
TBC3
788
2.5
0.92
9.21
TBC4
780
2.6
0.87
9.42
TBC5
750
3.3
0.85
10.12
TBC6
728
3.5
0.85
10.60
TBC7
720
3.9
0.82
10.80
TBC8
704
4.2
0.84
11.08
TBC9
700
4.3
0.84
11.2
TBC10
680
4.5
0.82
11.42
TBC11
675
4.6
0.80
11.60
TBC12
660
4.9
0.82
11.40
TBC13
642
5.2
0.78
13.16
TBC14
626
5.4
0.76
13.43
TBC15
608
5.9
0.76
14.10
Table 17-Test Result of Fresh Properties of glass fiber reinforced ternary blended SCC mixes
Mix Id
Slump flow (mm)
T500
mm Slump (sec)
Blockin
g ratio (H2/H1)
V-
Funnel (sec)
GFTBC1
640
4.8
0.82
11.6
GFTBC2
610
5.1
0.80
11.8
GFTBC3
580
5.3
0.76
12.1
GFTBC4
560
5.6
0.72
12.4
-
MECHANICAL PROPERTIES OF TBC MIXES
The mechanical characteristics of SCC were evaluated using the compressive strength test, splitting tensile strength test, flexural strength test. As per the guidelines of IS: 5161959, concrete cube specimens of size 150 x 150 x 150 mm were cast and immersed in water for four different curing ages (7 and 28 days
). Cylinders of size 150 mm diameter and 300 mm height were cast and immersed in water for three different curing ages (7 and 28 days). After curing, the cylinders were tested as per the IS: 58161999 guidelines. Prisms of size 100 × 100 × 500 mm were
cast and immersed in water for 28 days. After water curing, prisms were removed from the curing tank and tested in the flexural testing machine under two-point load under the loading rate of 400 kg/min IS: 516 1959.
Table 18 Strength Properties after curing 7 & 28 Days
Mix Id
Flexural strength (Mpa)
NM
5.12
TBC1
5.28
TBC2
5.20
TBC3
5.92
TBC4
6.16
TBC5
5.92
TBC6
6.32
TBC7
6.64
TBC8
6.80
TBC9
6.88
TBC10
5.92
TBC11
5.20
TBC12
4.88
TBC13
4.64
TBC14
4.72
TBC15
4.32
Table 19 Flexural Strength of ternary blended SCC mixes at 28 Days
Mix Id
Compressive Strength (Mpa)
Split Tensile Strength (Mpa)
7
Days
28
Days
7
Days
28 Days
NM
17.78
39.11
2.38
3.62
TBC1
18.13
40.89
2.49
3.74
TBC2
17.78
41.60
2.60
3.74
TBC3
18.84
41.96
2.60
3.96
TBC4
19.20
40.89
2.38
3.85
TBC5
19.20
41.96
2.60
3.96
TBC6
19.91
42.67
2.72
4.08
TBC7
19.91
42.67
2.94
4.19
TBC8
20.27
43.38
3.28
4.30
TBC9
20.98
44.44
3.40
4.64
TBC10
17.42
41.60
3.40
4.76
TBC11
17.42
40.53
2.83
3.85
TBC12
15.29
38.40
2.49
3.74
TBC13
14.58
35.20
1.81
3.28
TBC14
13.16
31.64
1.59
2.94
TBC15
11.02
30.58
1.36
2.49
Table 18 demonstrates the enhancement in the compressive strength (at 7 & 28 Days) of concretes with fly ash replacement level up to 20%. Conversely, there is a reduction in compressive strength when the fly ash substitution levels are 25 and 30%. Among the sixteen mixes, the worst-case scenario was observed in TBC15 in which compressive strength after 7 days of curing reduced to the level of 38 and 31% respectively, when compared with NM.
A marginal increase in splitting tensile strength from
2.49 to 3.40 N/mm2 was observed at the early ages (7 days) up to the mix TBC10. Beyond that from TBC11 to TBC15, the strength showed a decreasing trend and was reported to have 1.36 N/mm2 for TBC15. At 28 days, the splitting tensile strength values of TBC9 and TBC10 were observed to be higher than that of other TBC mixes. TBC10 and TBC9 give 31.25 and 28.13% higher strength than that of the NM.
-
MECHANICAL PROPERTIES OF GFTBC MIXES.
Table 20 Compressive, Split & Flexural strength test results of Glass Fiber reinforced Ternary Blended SCC mixes at 28 days
Mix Id
Average Specimen weight (grams)
Initial Water absorption (%)
Saturated Water absorption
(%)
Wdry
Winit
Wsat
NM
8262
8362
8438
1.21
2.13
TBC1
8275
8427
8476
1.84
2.43
TBC2
8162
8290
8368
1.57
2.52
TBC3
8310
8458
8508
1.78
2.38
TBC4
8254
8414
8491
1.94
2.87
TBC5
8218
8384
8456
2.02
2.90
TBC6
8196
8361
8449
2.01
3.09
TBC7
8322
8502
8628
2.16
3.68
TBC8
8296
8498
8589
2.43
3.53
TBC9
8324
8534
8624
2.52
3.60
TBC10
8302
8522
8613
2.65
3.75
TBC11
8255
<>8488 8561
2.82
3.71
TBC12
8326
8571
8630
2.94
3.65
TBC13
8406
8660
8736
3.02
3.93
TBC14
8356
8618
8697
3.14
4.08
TBC15
8324
8583
8689
3.11
4.38
Table 21- Water absorption test results of ternary blended SCC mixes at 56 days
Mix
Compressive
strength (Mpa)
Split Tensile Strength (Mpa)
Flexural strength (Mpa)
TBC9
44.44
4.64
6.88
GFTBC1
42.67
4.87
7.20
GFTBC2
40.89
5.10
7.44
GFTBC3
39.47
5.21
7.60
GFTBC4
38.76
5.44
7.68
-
DURABILITY STUDIES
-
The study of concrete mixes are not only concentrated on strength aspect, the durability properties are also fulfilled by the concrete to sustain in the various exposure conditions for many years. The life of the structures can be improved by the durable concrete. The penetration of aggressive ions, industrial liquids, water and gases are to be focused in the study of durability properties of concrete. The durability properties have been tested for normal SCC mix (NM), ternary blended SCC mixes (TBC1 to TBC15). Durability characteristics of SCC mixes were determined by conducting the following tests: water absorption test and Rapid Chloride Permeability Test (RCPT).
-
Water Absorption Test
The concrete cube specimens of size 150 x 150 x 150 mm were cast and immersed in water for 56 days curing. After curing, the cube specimens were dried by hot air oven at 1050c for 24 hours. Then the cube specimens were removed from the oven and kept in the room temperature for few hours. The dry weight of the cube was recorded as Wdry.
-
Rapid Chloride Penetration Test
The cylindrical specimens were cast with the diameter and height of 100 and 50 mm respectively. After 28 days of curing, the specimens were coated with epoxy. Then specimen was kept between two halves of the test cell that contained sodium chloride and sodium hydroxide solutions which acted as an electrolyte (ASTM C 1202-2009). The potential of 60 V was applied to the specimen for 6 hours and the charge passed through the concrete was recorded for every 30 minutes.
Table 22- Chloride ion permeability as per (ASTM C 1202-2009)
Charge passed (Coulombs) |
Permeability of chloride ion |
> 4000 |
High |
2000 4000 |
Moderate |
1000 2000 |
Low |
100 1000 |
Very low |
< 100 |
Negligible |
Table 23- Chloride ion penetration test results of ternary blended SCC mixes at 28 days
Mix Id |
Total charge passed (coulombs) |
Chloride ion penetration as per ASTM 1202-2009 criteria |
NM |
1121 |
Low |
TBC1 |
787 |
Very low |
TBC2 |
623 |
Very low |
TBC3 |
642 |
Very low |
TBC4 |
701 |
Very low |
TBC5 |
688 |
Very low |
TBC6 |
654 |
Very low |
TBC7 |
587 |
Very low |
TBC8 |
556 |
Very low |
TBC9 |
539 |
Very low |
TBC10 |
512 |
Very low |
TBC11 |
498 |
Very low |
TBC12 |
483 |
Very low |
TBC13 |
446 |
Very low |
TBC14 |
422 |
Very low |
TBC15 |
438 |
Very low |
CONCLUSION
Summarizing the observations, this section outlines conclusions regarding the influence of Supplementary Cementitious Materials (SCMs) like Fly Ash (FA) and Silica Fume (SF) on the fresh, mechanical, and durability aspects of Self-Compacting Concrete (SCC). Furthermore, it discusses the effects of incorporating glass fibers in the ternary blended SCC.
-
The NM and 10% replacement of fly ash blended concrete mixes can be categorized as SF3 class. From TBC5 to TBC12, the values lie in between 660 and 750 mm, these mixes can be categorized as SF2 class and are desirable for column and wall concrete works EFNARC-2005. Ternary blended SCC mixes with 30% of fly ash (TBC13 to TBC15) can be categorized as SF1 class. TBC3 (F10% + SF10%) exhibited the maximum flow value in comparison with other ternary blends. The slump flow values of glass fiber reinforced SCC mixes (GFTBC1 to GFTBC4) are in the range from 560 to 640 mm, and these mixes can be categorized as SF1 class. The slump flow value of all glass fiber reinforced SCC mixes conforms to EFNARC-2005 limitations.
-
The blocking ratio of all ternary blended SCC mixes is in the range from 0.76 to 0.92 and it is well below the limitation suggested in EFNARC-2005. Cement replacement with fly ash can improve the passing ability of SCC and decreases the blockage of coarse aggregate to some extent. Blocking ratio values all glass fiber reinforced SCC mixes were greater than0.8 except GFTBC3 and GFTBC4 mixes. The result shows that the high dosage glass fiber in SCC decreases the blocking ratio.
-
A marginal increase in the compressive strength was observed at early ages (7 and 14 days) up to a maximum level of 20% fly ash replacement. At higher replacement level of fly ash (say>20%), the desired strength at early ages was not attained.
-
The highest percentage of increase in compressive strength at 28 days test was attained in TBC9 mix as 13.64%. The enhancement in the compressive strength (at all ages) of concretes with fly ash replacement level is up to 20%. Conversely, there is a reduction in the compressive strength when the fly ash substitution levels are 25 and 30%. Among the sixteen mixes, the worst-case scenario was observed in TBC15. The reduction in strength at these later ages (21% at 28 days and 20% at 56 days) is less than that of reduction in strength reported at early ages (say, 7 and 14 days). This could be attributed to the enhancement in the pozzolanic reaction of fly ash at the later ages. Inclusion of glass fiber in the SCC reduces the compressive strength values and the maximum reduction in strength was found in GFTBC4 mix. Small pores on the fracture surface of the concrete may reduce the compressive strength of SCC.
-
The measured modulus of elasticity of NM and few TBC mixes are slightly less than the limiting value proposed in IS 456-2000. This could be attributed to the reduction in coarse aggregate content in the SCC mixes. Among all the SCC mixes, the maximum modulus of elasticity value was observed in TBC9. The elastic modulus value of TBC9 was 17.84% higher than the elastic modulus of normal (NM) SCC mix. Inclusion of glass fibes increases the elastic modulus values of SCC. GFTBC3 mix shows 7.22% high modulus of elasticity value more than the optimized ternary blended SCC mix.
REFERENCES
-
Aarthi, K & Arunachalam, K 2018, Durability studies on fibre reinforced self compacting concrete with sustainable wastes, Journal of Cleaner Production, vol. 174, pp. 247-255.
-
ACI: 318-95 (R), Building code requirements for structural concrete, American Concrete Institute.
-
Ahmaruzzaman, M 2010, A review on the utilization of fly ash,Progress in Energy and Combustion Science, vol. 36, pp. 327-363.
-
ASTM C 1012-2004, Standard test method for length change
ofhydraulic-cement mortars exposed to a sulfate solution, Annual
Book of ASTM Standards
-
ASTM C 1202-2009, Standard test method for electrical indication of concretes ability to resist chloride ion penetration, Annual Book of ASTM Standards.
-
ASTM C 618-92a, Standard specification for fly ash and raw or calcined natural pozzolana for use as mineral admixture in Portland cement concrete, Annual Book of ASTM Standards, vol. 04, 1994.
-
Aydin, AC 2007, Self compactability of high volume hybrid fiber reinforced concrete, Construction and Building Materials, vol. 21, no. 6, pp. 1149-1154.
-
Barluenga G.Javier Puentes&Irene Palomar 2015, Early age monitoring of self-compacting concrete with mineral additions, Construction and Building Materials, vol. 77, pp.
66-73.
-
CEB-1989, Diagnosis and assessment of concrete structures state of art report, CEB Bulletin.
-
Chandramouli, K, Seshadri Sekhar, T, Sravana, P, Pannirselvam,
N & Srinivasa Rao, P 2010, Strength properties of glass fiber
concrete, ARPN Journal of engineering and applied sciences,
vol. 5, no.4, pp. 1-6.
-
Chawla, K & Tekwani, B 2013, 'Studies of glass fiber reinforced concrete composites', Int J Struct Civil Eng Res, vol. 2, no. 3,pp. 176-182.
-
Chindaprasirt, P & Rukzon, S 2008, Strength, porosity and
corrosion resistance of ternary blend Portland cement, rice
husk ash and fly ash mortar, Construction and Building
Materials, vol.22, no.8,pp. 1601- 1606.
-
IS: 12269-2013, Ordinary Portland cement, 53 grade- Specification, Bureau of Indian Standards, New Delhi, India.
-
IS: 2386-1963 part (III), Methods of test for aggregate for concrete, Bureau of Indian Standards, New Delhi, India.
-
IS: 2386-1963 part (IV), Methods of test for aggregate for concrete Mechanical Properties, Bureau of Indian Standards, New Delhi, India.
-
IS: 383-2016, Coarse and fine aggregate for concrete – specification, Bureau of Indian Standards, New Delhi, India.
-
IS: 4031-1988, Methods of physical tests for hydraulic cement: part 04 determination of consistency of standard cement paste, Bureau of Indian Standards, New Delhi, India.
-
IS: 4031-1988, Methods of physical tests for hydraulic cement: part 11 determination of density, Bureau of Indian Standards, New Delhi, India.
-
IS: 4031-1999, Methods of physical tests for hydraulic cement:
-
part 2 determination of fineness by specific surface by Blaine
air permeability method, Bureau of Indian Standards, New Delhi, India.
-
IS: 456-2000, Plain and reinforced concrete-code of practice, Bureau of Indian Standards. New Delhi, India.
-
IS: 516-1959, Methods for test for strength of
concrete, Amendment No. 2, reprint 1993, Bureau of Indian Standards. New Delhi, India.