
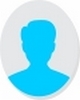
- Open Access
- Authors : Basavaraj H Talikoti , Dr. Girisha H N , Bharath. L
- Paper ID : IJERTV10IS020209
- Volume & Issue : Volume 10, Issue 02 (February 2021)
- Published (First Online): 04-03-2021
- ISSN (Online) : 2278-0181
- Publisher Name : IJERT
- License:
This work is licensed under a Creative Commons Attribution 4.0 International License
Investigation on Hardness of Al7075/Gr./SiCp Hybrid Metal Matrix Composites
Basavaraj H Talikoti
VTU, Research scholar Department of Mechanical Engineering
Government Engineering College Ramanagar, Karnataka, India
Dr. Girisha H N
VTU, Assistant Professor Department of Mechanical Engineering
Government Engineering College Ramanagar, Karnataka, India
Bharath. L
VTU, Assistant Professor Department of Mechanical Engineering
Cambridge Institute of Technology, Bangalore, Karnataka, India
Abstract: In this paper effort have been made to validate the hardness of Al7075 hybrid composite through Taguchi's Techniques. Hybrid composites were prepared by using Al7075 as matrix material and SiC. (0, 2, 4 and 6 wt.%) and graphite
(1, 3, 5 and 7 wt.%) as reinforcement through stir casting technique. Hardness of hybrid composite increased with increase in wt.% of reinforcement in the Al7075 matrix material. In the present study, Taguchis L16 Orthogonal array was used to know the percentage contribution of each factors on hardness by Analysis of Variance (ANOVA). Regression equation have been generated by using design of experiments through Minitab software.
Keywords – Al7075; SiCp; Graphite; Stir casting; Regression Equation.
-
INTRODUCTION
Hybrid composite material plays an important role in industrial application such as automobile sector, aerospace, marine field etc. The useage of these hybrid composites is due to their high strength, low density, high wear and corrosion resistance and good thermal conductivity. Composite material consists of base material know as matrix and secondary material know as reinforcements in order to improve the strength and stiffness of the matrix. The choice of composites in many occurrences will depend on factors which includes number of items to be produced, working lifetime requirements, complexity of the product and skills of the designer in tapping the optimum potential of composites [1]. Aluminum is the most popular matrix for the metal matrix composites. Aluminium alloys are quite attractive due to their capability to be strengthened by precipitation, low density, good corrosion resistance, and high electrical and thermal conductivity. Aluminum Matrix Composites (AMCs) are the class of light weight high performance materials [2,3]. Composite materials are striking since they offer the possibility of attaining property combinations which are not possible to obtain in monolithic materials and which can result in a number of vital service benefits. The key feature of composites is that they generally exhibit the optimum qualities of their constituents and often some attractive qualities that neither of the constituents
possesses [4]. Reinforcing the aluminum alloys with ceramic particles can contribute to activate strengthening mechanisms due to morphological variations such as geometrically increased density of dislocations, grain refinement caused by thermal mismatches of the matrix and reinforcements and load transfer from Al onto reinforcements [6]. Al6061 was reinforced with different reinforcement ratios of SiC by stir casting method to evaluate and compare the results with Al6061 for better improvement in mechanical properties. The results were shown that there was significant improvement in tensile properties and compressive strength and hardness as the wt.% of reinforcement of particles increases as compared to the unreinforced matrix [9].
The literature survey reveals that presently very few research studies are carried out on the mechanical properties of aluminum alloy matrix reinforced with different reinforcing material such as boron carbide, Al2O3, TiB2, fly ash, e-glass fiber, SiC, graphite etc. Therefore, in the present investigation Al6061/Gr./SiCp hybrid composites were prepared by using stir casting process to evaluate the hardness properties. Further, Taguchis Technique was been employed to validate the experimental hardness value.
-
EXPERIMENTAL DETAILS
In this chapter, selection of matrix and reinforcement material, formation of hybrid composites, preparation of hardness specimens and Taguchis Technique have been discussed.
-
Material selection
In this work, Aluminum alloy 6061 is used as a matrix material. The reinforcements are graphite and silicon carbide. The chemical composition of Al7075 alloy is shown in Table 1.
Elemen
t
Cu
Cr
M
n
M
g
Si
Ti
Zn
Fe
Al
Wt. %
1.
8
0.
2
0.4
1.9
0.
5
0.1
5
3.2
5
0.
5
91.
3
Elemen
t
Cu
Cr
M
n
M
g
Si
Ti
Zn
Fe
Al
Wt. %
1.
8
0.
2
0.4
1.9
0.
5
0.1
5
3.2
5
0.
5
91.
3
Table 1: Chemical composition of Al7075 alloy
-
Formation and Machining
Calculated amount of Al6061matrix material were cut and placed in the pre-heated crucible for melting. The pre-heated reinforcements in wt.% were introduced into the molten metal for preparation of Al6061/Gr./SiCp hybrid composite. Proper stirring was employed in order to ensure uniform distribution of reinforcements into the matrix to achieve better mechanical properties.
Vickers Hardness test specimens were prepared as per IS 1501-2011 standard size by using conventional machine tool to evaluate the experimental VHN.
-
Taguchi's Techniques
A Taguchi design or an orthogonal array, is a method of designing experiments that usually requires only a fraction of the full factorial combinations. It is an efficient approach to optimize the process parameter for reducing production cost and improved quality. The three major tools in this process are orthogonal array (OA), Signal to Noise ratio and Analysis of Variance (ANOVA) [17].
-
Process parameter and its levels
In the current research work, two parameters (SiCp and Gr.) have been selected with 4 levels each. These two factors and their level were tabulated in Table 2 (a). Design of L16 (45) Orthogonal array have been consider and shown in Table 2 (b).
Table 2 (a): Process parameter and its level
Sl. No.
Parameter
Level
1
Silicon Carbide (SiC)
0, 2, 4 and 6 (wt.%)
2
Graphite (Gr.)
1, 3, 5 and 7 (wt.%)
Table 2 (b): Taguchi L16 orthogonal array
RUN
Silicon carbide (wt.%)
Graphite (wt.%)
1
0
1
2
0
3
3
0
5
4
0
7
5
2
1
6
2
3
7
2
5
8
2
7
9
4
1
10
4
3
11
4
5
12
4
7
13
6
1
14
6
3
15
6
5
16
6
7
-
-
RESULTS AND DISCUSSION
Vickers hardness number were evaluated for the formed hybrid composite material. The load of 100gm for a period of 10 seconds is applied on specimens. The average of five readings for all 16 specimens was calculated. Table 3 shows the variation of hardness number with respect to different wt.% of reinforcements in Al7075 alloy. As the wt.% of
graphite and SiC particle increased the hardness number has increased [17].
-
Signal to Noise ratio and Optimum process
parameter for hardness.
The response of hardness for each parameter i.e., graphite (wt.%) and SiC (wt.%) at each level was found and its output is plotted in Figure 1. It represents the main effect graph for hardness and its characteristics is based on Larger is better
Table 3: L16 Orthogonal array with response
RUN
Silicon carbide
(wt.%)
Graphite (wt.%)
Vickers Hardness
(VHN)
S/N ratio
1
0
1
124.3
41.89
2
0
3
150
43.52
3
0
5
172.2
44.72
4
0
7
170.8
44.65
5
2
1
131
42.35
6
2
3
160.8
44.13
7
2
5
168.8
44.55
8
2
7
186.4
45.41
9
4
1
139
42.86
10
4
3
163.4
44.27
11
4
5
178.2
45.02
12
4
7
189.2
45.54
13
6
1
136
42.67
14
6
3
164
44.30
15
6
5
182.8
45.24
16
6
7
191
45.62
Figure 1: Main effect plot for SN ratio
Based on the main effect of SN ratio as shown in Figure 1 the optimum process parameter and their levels for obtaining maximum hardness is Graphite at level 4 (7 wt.%) and SiC. at level 4 (6 wt.%). The S/N ratio for each run is tabulated in Table 3. Response table for Signal to Noise ratio is shown in Table 4 which signifies that graphite is the most effective factor for hardness and is designated at rank 1 followed by silicon carbide.
Level
Silicon Carbide
(A)
Graphite
(B)
1
43.7
42.44
2
44.11
44.05
Level
Silicon Carbide
(A)
Graphite
(B)
1
43.7
42.44
2
44.11
44.05
Table 4: Response Table for S/N ratio
3
44.42
44.88 11 4 5 178.2 173.96 2.
4
44.46
45.3 12 4 7 189.2 191.09 0.
Delta
0.76
2.86 13 6 1 136 144.51 6.
Rank
2
1 14 6 3 164 161.64 1.
Optimum
level
4 (6 wt.%)
4 (7 wt.%) 15 6 5 182.8 178.77 2.
16 6 7 191 195.90 2.
3
44.42
44.88 11 4 5 178.2 173.96 2.
4
44.46
45.3 12 4 7 189.2 191.09 0.
Delta
0.76
2.86 13 6 1 136 144.51 6.
Rank
2
1 14 6 3 164 161.64 1.
Optimum
level
4 (6 wt.%)
4 (7 wt.%) 15 6 5 182.8 178.77 2.
16 6 7 191 195.90 2.
37
99
26
43
20
56
-
Analysis of Variance (ANOVA) ANOVA is used to investigate the percentage contribution of each factor on hardness of Al6061/Gr./SiC hybrid composite. It defines the optimum combination of the factors that show the more accurate by observing their comparative significant among them. Table 5 represent the ANOVA for hardness, using Adjusted SS for test. It is observed that wt.% of graphite has highest percentage contribution (90.86%) on hardness followed by wt.% of silicon carbide having (7.4%) and collectively error obtained is 1.72%.
Source
Silicon Carbide (A)
Graphite (B)
Error
Total
DF
3
3
9
15
Seq SS
505.3
6198.6
118
6821.9
Adj SS
505.3
6198.6
118
Adj MS
168.4
2066.2
157.62
F-Value
12.85
157.62
P-Value
0.001
0
% of contribution
7.4
90.86
1.72
Rank
2
1
Source
Silicon Carbide (A)
Graphite (B)
Error
Total
DF
3
3
9
15
Seq SS
505.3
6198.6
118
6821.9
Adj SS
505.3
6198.6
118
Adj MS
168.4
2066.2
157.62
F-Value
12.85
157.62
P-Value
0.001
0
% of contribution
7.4
90.86
1.72
Rank
2
1
Table 5: ANOVA for hardness.
250
200
VHN
VHN
150
100
50
0
1 2 3 4 5 6 7 8 9 10 11 12 13 14 15 16
No. of Trais
Experimental Value Predicted Value
-
Regression Equation
Regression equation is used to validate the experimental hardness number of Al6061/Gr./SiCp hybrid composite by using general linear model through Minitab software. Table 6 shows the validation of experimental hardness value of formed hybrid composites. The general regression equation for hardness is shown in equation (1)
VHN = 121.528 + 2.40375 Silicon Carbide + 8.56375
Graphite (1)
Table 6: Comparison of experimental result and regression
RUN |
Silicon carbide (wt.%) |
Graphite (wt.%) |
Vickers Hardness (Exp.) |
Vickers Hardness from Regression (1) |
% Error |
1 |
0 |
1 |
124.3 |
130.09 |
4.65 |
2 |
0 |
3 |
150 |
147.22 |
1.85 |
3 |
0 |
5 |
172.2 |
164.35 |
4.56 |
4 |
0 |
7 |
170.8 |
181.47 |
6.24 |
5 |
2 |
1 |
131 |
134.90 |
2.97 |
6 |
2 |
3 |
160.8 |
152.03 |
5.45 |
7 |
2 |
5 |
168.8 |
169.15 |
0.20 |
8 |
2 |
7 |
186.4 |
186.28 |
0.06 |
9 |
4 |
1 |
139 |
139.71 |
0.50 |
10 |
4 |
3 |
163.4 |
156.83 |
4.01 |
RUN |
Silicon carbide (wt.%) |
Graphite (wt.%) |
Vickers Hardness (Exp.) |
Vickers Hardness from Regression (1) |
% Error |
1 |
0 |
1 |
124.3 |
130.09 |
4.65 |
2 |
0 |
3 |
150 |
147.22 |
1.85 |
3 |
0 |
5 |
172.2 |
164.35 |
4.56 |
4 |
0 |
7 |
170.8 |
181.47 |
6.24 |
5 |
2 |
1 |
131 |
134.90 |
2.97 |
6 |
2 |
3 |
160.8 |
152.03 |
5.45 |
7 |
2 |
5 |
168.8 |
169.15 |
0.20 |
8 |
2 |
7 |
186.4 |
186.28 |
0.06 |
9 |
4 |
1 |
139 |
139.71 |
0.50 |
10 |
4 |
3 |
163.4 |
156.83 |
4.01 |
equation values for hardness.
Figure 2: Comparison plot of experimental values v/s predicted values for VHN.
Figure 2 shows the plot of experimental values v/s predicted values for two factors at four levels each for hardness. It is clear that the experimental values are very close to the predicted values and hence experimental values of Vickers Hardness Number (VHN) of the formed composites are validated.
III. CONCLUSION
This paper deals with study on Al6061/Gr./SiCp hybrid composite fabricated through stir casting technique. Taguchi technique were employed to know the effect of each factor on hardness behaviour of hybrid composites. It is observed that the method is efficient and economical, to get enough information in a small period of interval with a smaller number of experiments. The results reveal that wt.% graphite is the most dominant factor for hardness followed by wt.% of SiC. particles. The optimum value for hardness is Gr.: 7 wt.% and SiC: 6 wt.% with 90.86% and 7.4% of contribution respectively. Regression analysis shows a good agreement with the experimental results for hardness.
ACKNOWLEDGEMENTS
I wish to convey my truthful thanks to my research supervisor Dr. Girisha H N for the valuable suggestion and inspiration during every stage of my research work.
We gratefully thank to Visvesvaraya Technological University (VTU), Jnana Sangama, Belagavi for the support protracted to this research work.
REFERENCES
-
M Gangadharappa, H N Reddappa, M RaviKumar and R Suresh, Mechanical and Wear Characterization of Al6061 Red Mud Composites Materials Today: Proceedings 5 (2018), 22384 22389.
-
M. Sreenivasa Reddy, Dr. Soma V. Chetty and Dr. Sudheer Premkumar, Influence of reinforcements and heat treatment on Mechanical and Tribological properties of hybrid composite formed by Al 7075 reinforced with fly ash and E-Glass short fibers Volume 3, IJAMS, ISSN 2231-1211, Number 3 (2012), pp. 267-274.
-
M. Sreenivasa Reddy, Soma V. Chetty, Sudheer Premkumar and
A.N. Khaleel Ahemed, Comparative Study on hardness of As- cast and heat-treated Al based hybrid composites IJAIR, Vol. 2 Issue 4, ISSN: 2278-7844, pp. 336-341.
-
M. Sreenivasa Reddy, Soma V. Chetty, Sudheer Premkumar and H N Reddappa, Validation of Hardness and Tensile Strength of Al 7075 Based Hybrid Composites Using Artificial Neural Networks IJMET, Vol.5, Issue 9, September (2014), pp. 280- 285.
-
M. Sreenivasa Reddy, Soma V. Chetty, Sudheer Premkumar and H N Reddappa, Influence of reinforcements and heat treatment on mechanical and wear properties of Al7075 based hybrid composites Procedia Materials Science 5 (2014) 508 516.
-
Y. Pazhouhanfar and B. Eghbali, Microstructural characterization and mechanical properties of TiB2 reinforced Al6061 matrix composites produced using stir casting process Materials Science & Engineering A 710 (2018), pp. 172-180.
-
P. Subramanya Reddy, R. Kesavan and B Vijaya Ramnath, Investigation of Mechanical Properties of Aluminium 6061- Silicon Carbide, Boron Carbide Metal Matrix Composite Silicon, (2016).
-
Balasubramani Subramaniam, Balaji Natarajan, Balasubramanian Kaliyaperumal and Samson Jerold Samuel Chelladurai, Investigation on mechanical properties of aluminium 7075 – boron carbide – coconut shell y ash reinforced hybrid metal matrix composites Overseas Foundry, (2018), Vol.15, No.6, November, pp.449-456.
-
Rajasekhar. Sivapuram, Hariprasad Reddy. Yedulaand Chandra Mohana Reddy Baggidi An experimental investigation on tensile Properties and energy absorption capabilities of Hybrid nano metal matrix (Al6061+B4C +sic) Composites IJAET, (2017), Apr., ISSN: 22311963, pp.210-215.
-
ShipraVerma, P.Sudhakar Rao,Study on mechanical behavior of boron carbide and rice husk ash based aluminium alloy 6061 hybrid composite, IJTIMES, (2018), Volume 4, Issue 10, pp.84- 92.
-
Hosur Nanjireddy Reddappa, Kitakanur Ramareddy Suresh, Hollakere Basavaraj Niranjan and Kestur Gundappa Satyanarayana,Studies on Mechanical and Wear Properties of Al6061/Beryl Composites JMMCE, 2012, Issue 11, pp. 704- 708.
-
N. Ramadoss a, K. Pazhanivel b, G. Anbuchezhiyan, Synthesis of B4C and BN reinforced Al7075 hybrid composites using stir casting method JMR&T, (2020), Elsevier Ltd, pp. 6297-6304.
-
L. Natrayan and M. Senthil Kumar,Optimization of wear behaviour on AA6061/Al2O3/SiC metal matrix composite using squeeze casting techniue Statistical analysis Materials Today: Proceedings, Elsevier Ltd, (2018), pp. 1-5.
-
L. Natrayan, V. Sivaprakash, M.S.Santhosh, Mechanical, Microstructure and wear behavior of the material AA6061 reinforced SiC with different leaf ashes using advanced stir casting method, International Journal of Engineering and Advanced Technology (IJEAT), (2018) ISSN: 2249 8958, Volume-8, Issue-2S, pp. 366-371.
-
David Raja Selvam. J and Robinson Smart. D.S. Dinaharan, Synthesis and characterization of Al6061-Fly Ashp-SiCp composites by stir casting and compo casting methods 10th Eco- Energy and Materials Science and Engineering, SciVerse ScienceDirect, Energy Procedia 34, (2013), pp. 637 646.
-
M. Ravikumar, H. N. Reddappa and R. Suresh,Study on Mechanical and Tribological Characterization of Al2O3/SiCp Reinforced Aluminum Metal Matrix Composite Springer Science Business Media B.V, (2018).
-
M RaviKumar, H N Reddappa, R. Suresh and M. Gangadharappa, Investigation on Hardness of Al 7075/Al2O3/SiCp Hybrid Composite Using Taguchi Technique Materials Today: Proceedings 5, (2018), pp.2244722453.
-
M RaviKumar, Reddappa H N and Suresh R (2018) Mechanical and Wear behaviour of Al7075/Al2O3/SiC Hybrid Composite Materials Today: Proceedings 5, (2018), pp. 55735579.
-
K Sunil Kumar and P L Srinivasa Murthy, Retrogression and re- aging of AL-7075 Microstructure and Corrosion Behaviour Characterization IJEAT, (2019), Vol.9, Issue-1, ISSN: 2249 8958, pp.4377-4383.