
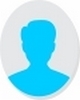
- Open Access
- Authors : Zhiyong Meng
- Paper ID : IJERTV13IS080101
- Volume & Issue : Volume 13, Issue 08 (August 2024)
- Published (First Online): 09-09-2024
- ISSN (Online) : 2278-0181
- Publisher Name : IJERT
- License:
This work is licensed under a Creative Commons Attribution 4.0 International License
Kinematic Analysis of a Double-Layer Parallel Superimposed Mechanism
Zhiyong Meng
Tianjin University of Technology and Education
Tianjin China
Abstract: In order to make the parallel mechanism reach the level of the series mechanism in the working space, a new type of coupling mechanism is proposed, which is coupled in the form of the basic configuration of the parallel mechanism, and then the position positive solution of the double-layer parallel mechanism can be derived. Through the differential mapping relationship of the finite instantaneous spiral theory, the velocity of the mechanism is solved. Finally, through motion simulation, it is verified that the performance of the mechanism is consistent with the theoretical analysis.
Keywords: double-layer parallel mechanism; finite instantaneous spiral theory; differential transformations; positive kinematics
-
INTRODUCTION
Compared with the series mechanism, the parallel mechanism has many advantages such as high stiffness, large bearing capacity, good dynamic performance and high precision, but the disadvantages of the parallel mechanism in the working space are also obvious, so that the application in practice is still very limited, and the parallel machine tool, the parallel attitude adjustment platform and the multi-degree-of-freedom motion simulator are mainly concentrated at present. However, there is still a shortage of parallel mechanisms with large working spaces, especially those with rotational freedom. Therefore, the parallel mechanism with a large working space has high research value and broad application prospects. Li Qinchuan
[3] replaced the mechanism with the equivalent motion pair according to the relationship between the moving platform and the fixed platform, and analyzed the research status and research direction of the two-shift and one-shift parallel mechanism by relevant scholars at home and abroad. Yulin Zhou [4] of Yanshan University proposed a workspace mapping method based on bias output, which changes the institutional workspace by changing the bias angle. Miseabadesu [5] expanded the working space by optimizing the scale parameters of the 3-UPU parallel mechanism and the 3-UPS&S parallel mechanism, and the effect was remarkable. Carol Miller [6] increased the working space of the paralleling mechanism by optimizing the position of the drive unit on the frame. United States scholar Rossheim Mark [7] proposed a variety of large workspace parallel mechanism configurations and applied them to robots. Zhang Yaojun et al. [8] optimized the scale of a class of three- translational degrees of freedom parallel mechanism to increase the working space. Tao Zongjie et al. [9] proposed an effective design method based on theinfluence of member interference on the working space, and verified it in the design of the 3-RRR parallel mechanism. Chen Jianghong [10] used the idea of virtual axis and used the diamond-shaped mechanism as a branch chain to reduce the limitation of rod length on the working space, which not only improved the performance of the working space, but also increased the longitudinal expansion ratio. Bai Zhifu [11] designed a composite spherical pair with three rotating pairs from the perspective of improving the spherical pair of the parallel mechanism, so as to increase the swing angle and then expand the attitude space of the parallel mechanism. Xu Dongguang [12] used the idea of function optimization to obtain the influence of changing the scale parameters on the working space of the 6-UPS parallel mechanism, and gave a solution.
In addition, a new mechanism formed by connecting another mechanism in series on the basis of a parallel mechanism is a hybrid mechanism [13], and this tandem method can also improve the working space. However, it is more difficult to study the hybrid mechanism, and for location analysis, the relationship between input and output is often difficult to determine, so there are multiple solutions, which makes the practicability of the mechanism lacking. The traditional spiral
[14] method is often complex for velocity solving.In order to make the parallel mechanism reach the level of the series mechanism in the working space, a new type of coupling connection mechanism is proposed [15]. This configuration uses a mechanical transmission mode to transmit force and motion between parallel mechanisms, and after the coupling of two parallel mechanisms, the motion characteristics similar to those of the series mechanism are realized, and the important performance of the working space is reached or even better than that of the series mechanism [16]. For the velocity solution, the finite instantaneous spiral theory is used to make the process
rule. Due to the symmetry of the mechanism, points A , B ,
-
DOUBLE-LAYER PAR-ALLEL MECHANISM CONFI G-URATION
and C are all on the Z axis, and points
G1 and Q1
are
symmetric about the origin. Based on this, the coordinates of
points
A1 ,
C1 ,
G1 ,
Q1 can be set as 0 0
a ,
0 0
a
, b
0 c
and b
0 c .
According to the directions of the screws in the figure 1, the motion screw system of this branch can be written as:
$11 0 1 0 ; 0 0 0
$ 0 1 0 ; a 0 0
12
$13 0 1 0 ; a 0 0
$ 1 0 0 ; 0 c 0
14
$
15
0 1 0 ; c
0 b
$16 0 0 1 ; 0 b 0
$17 1 0 0 ; 0 c 0
$ 0 1 0 ; c 0
b
18
Figure 1 Mechanism Configuration
$ 0 0 1 ; 0 b 0
Although the double-layer parallel mechanism appears as a superposition of two 3-RSR parallel mechanisms, it can be
19
1
considered as a 3-RSR parallel mechanism with three coplanar rotational constraints added at the shared linkage, due to the common linkage between the front and rear stages.
The difference between this mechanism and traditional double- layer parallel mechanisms lies in the fact that traditional parallel stacking requires two levels of actuation, which inevitably increases the self-weight of the mechanism and reduces its dynamic performance. By modifying the kinematic pairs at the end of the mechanism to create shared kinematic pairs, the upper and lower stages of the mechanism are connected through these kinematic pairs. The kinematic pairs accurately transmit the motion output of the upper parallel mechanism to the lower mechanism as the motion input of the lower parallel mechanism. This design requires only one set of actuators placed at the base platform, reducing the overall weight of the mechanism and enhancing its stability.
As shown in Figure 1, the origin of the branch coordinate system is selected at the center of the rotational pair of the middle platform. The Z axis is perpendicular to the middle platform and points towards the moving platform, the X axis points positively towards the center of the middle platform, and the Y axis direction is determined according to the right-hand
Since the rank of the aforementioned motion screw system is 6, the constraint screws can only be:
1
$r 0 0 0 ; 0 0 0
2
Therefore, the branch does not impose any constraints on the platform. Additionally, since the mechanism's three branches are of the same type, the moving platform should have 6 degrees of freedom. For a 3-RSR parallel mechanism, in non- singular configurations, the movement of the platform is determined when the inputs are speified, possessing three degrees of freedom: two rotational and one translational. The linkage in the middle layer functions as a single-degree-of- freedom transmission element, which does not increase the degrees of freedom. Consequently, the overall mechanism should also have 3 degrees of freedom.
-
DIRECT KINEMATIC ANALYSIS
the moving platform, the
x2 axis is aligned along vector
2 2 , and the z2 axis is perpendicular to the moving
platform. Define as the angle between the projection of the
moving coordinate system's
z2 axis on the base plane and the
positive direction of the fixed coordinate system's x axis. Let
be the angle between the z2 axis of the moving coordinate
system and the
z2 axis of the fixed coordinate system. The
distance between the centers of the moving and static platforms
is li , and the distance from the platform center to the center of
the rotational pair is R . All link lengths are L . Points
G1 ,
G2 , and
2 , and
G3
3 .
can be expressed in terms of the input angles
1,
R Lc1
G 0
1
Ls1
3
1 (R Lc )
2 2
Figure 2 Schematic Diagram of the Mechanism
G2
3 (R Lc
)
2
2
As shown in Figure 2, the mechanism is composed of three parts: the static platform, the moving platform, and the branches. The branches are distributed in a 360° circular
Ls2
4
2
3
1 (R Lc )
arrangement. Each set of branches includes both active and passive links, where the active links are connected to the moving platform and the passive links are connected to the static platform.
Coordinate systems are established as follows: a fixed coordinate system O xyz on the static platform and a
G3
3
)
2
(R Lc
2
Ls3
5
moving coordinate system
O1 x1 y1z1
on the moving
platform. The origins O O1 and O2
are the centers of the
static and moving platforms, respectively. The x axis is
aligned along vector
OA1 , the z axis is perpendicular to the
static platform and points vertically upwards. The
x1 axis is
aligned along vector
11 , the
z1 axis is perpendicular to
The vectors
G1G2 and
G1G3 are further determined as
arctan k (m 0, k 0)
follows:
1 (3R 2Lc
Lc )
m
arctan k
m
m 0
2 1 2 k
arctan m 0, k 0)
G1G2
3 (R Lc )
2
2
m
10
L(s2 s1)
6
2
m2 k 2
2 arctan
p
1 (3R 2Lc Lc )
11
2 1 3 Where
GG 3 (R Lc )
1 3
2
L(s
3
3 s1)
7
m=3/2(RLs_3+RLs_2-2Rs_1-L^2 c_2 s_3-L^2 c_3 s_2
+Lc_2 s_1+Lc_3 s_1)
k=1/2(3RLs_2-2L^2 c_1 s_2-L^2 c_3 s_2+Lc_3 s_1-3RLs_3
+2L^2 c_1 s_3+L^2 c_2 s_3-Lc_2 s_1))
The cross product of the vectors
G1G2
and
G1G3 yields a
p 3 (6R2 4RLc
-
2RLc
-
4RLc
3L2c c )
vector that is normal to the plane
4
G1G2G3 , with the direction
3 1 2 2 3
pointing from the static platform to the moving platform. Using
The rotation matrix
O R representing the orientation of the
O
1
the coordinates of point
G1 and the normal vector, the point-
moving coordinate system relative to the fixed coordinate
normal form equation of the plane G1G2G3 can be obtained.
system can be expressed as:
s1v1 c1
s1c1v1
c1s1
This allows for the calculation of the distance from point O
O R s c v
c2 v c
s s
O1
1 1 1 1 1 1 1 1
to the plane
G1G2G3 .
m 2 k 2 p 2
1 1 1
d (m1 (R Lc1) pLs1)
c1s1
s1s1
12
c1
s sin , c cos , v 1 cos is the
2
Therefore, the solution parameters are:
8
angle between the
OO2 axis of the moving coordinate
m2 k 2 p2
1
l OO 2d 2 (m(R Lc1 ) pLs1)
system and the z axis of the fixed coordinate system.
The coordinates of Q1 , Q2 and Q3 relative to the fixed
9
coordinate system
O1 are:
R Lc1
18
O1Q 0
1
Therefore, the solution parameters are:
Ls1
13
m 2 k 2 p 2
2 2 2
1 (R Lc )
l2 O1O2
2d2
2 (m2 (R Lc1) p2 Ls1)
2 2
19
m
O1Q 3 (R Lc )
arctan k2
2
2 2
Ls2
2
2
20
14
1
2 2 arctan
m 2 k 2
2 2
p
2
2 (R Lc3)
21
O1Q 3 (R Lc )
Where
m2 , p2 , k2
are all functions of
i and can be
3 2 3
Ls3
15
The vectors are further determined as:
1 3
1 (3R 2Lc Lc )
2
indirectly converted into functions of i . The vector OO1 can be expressed as:
OO1 (l1 sin1 cos1,l1 sin1 sin1,l1 cos1)
22
The vector OO in the O coordinate system can be
1 2 1
Q Q 3 (R Lc ) expressed as:
1 2
2 3
L(s s )
O OO (l sin
cos ,l sin sin ,l cos )
3 1
1
1 2 2 2 2 2 2 2 2 2
23
16
1 (3R 2Lc Lc )
The vector
OO2 can be expressed as:
2 1 3
OO OO OR O O
l ,l ,l
2 1
O1 1 2
x y z
Q Q
3 (R Lc )
24
1 3
2 3
L(s s )
The distance between the centers of the moving platform and
3 1
17
the static platform is:
l 2 l2 l2
x y z
L
25
The distance from point
O1 to the plane Q1Q2Q3 is:
The direct kinematic analysis of the mechanism is validated through simulation, with the link length L 0.07848m
(m (R Lc ) p Ls )
and platform radius r 0.04497m measured. The motion
m 2 k 2 p 2
2 2 2
d2 2 1 2 1
trajectory is described by the following equation:
26
0.8t2 8t 95
p(t)
0
0 t 5
5 t 15
-
-
SPEED ANALYSIS
According to the differential mapping in the finite instantaneous spiral theory, the velocity model can be solved by differential equations
0 0 t 5
St ,i S f ,PM St ,1
St ,2
St ,3 29
(t) 0.32t3 7.4t 2 48t 100 5 t 10
0 10 t 15 5 5
S S
,i 1, 2,3 30
27
k 1
t ,i,k i,k t ,i,k k 1
0 0 t 5
In the structure, the velocity model of the moving platform is:
(t) 0 5 t 10
s s
3.6t 2 72t 360 10 t 15
St ,i
11,i r
1,i
s
12,iT r
1,i
s
11,i
11,i 12,i
1,i
28
The motion trajectory of the center point of the moving
In the structure, the velocity model of the moving platform is:
4
platform is shown in Figure 3, and its positional solution is shown in Figure 4.
St ,i
k 1
qi,k St ,i,k ,i 1,3 32
where St ,i,k
is the unit instantaneous motion i axis of the first
joint in the first rod, and Si,k as its unit direction vector, is its
intensity.
Sw,i f
a,i,3S
wa,i,3
f
2
kc1
S
c,i,kc wc,i,kc
,i 1,3 33
S ri,3 si,3 ,S ri,2 si,2 , S
si,2 si,1 34
wa,i,3 s wc,i,1 s wc,i,2 0
i,3 i,2
S ri,3 si,3 ,S ri,2 si,2 , S
si,2 si,1
wa,i,3 s wc,i,1 s wc,i,2 0
i,3 i,2
34
Figure 3 Motion Trajectory
JwSt Jqq 35
J Jwa ,J
Jqa
,q qa ,q i
t t t T
w J q
o 0 a
1,3 1,3 2,4 3,3
wc
31
36
Jwa
S
wa,1,3
Swa,2,4
T
S
wa,3,3
wc S
wc,1,1
Swc,2,1
T
S
wc,3,1
, J
37
Figure 4 Position Solution
S T S
Jq
wa,1,3
t ,1,3
T
S
wa,2,4
St ,2,4
S
T
wa,3,3
St ,3,3
0
38
REFERENCES
-
Li M, Cao Z, et al. 3-DOF bionic parallel mechanism design and analysis for a snake-like robot[C]//2016 IEEE International Conference on Robotics & Biomimetics. Harbin: IEEE, 2016: 25-30.
-
VERL A, VALENTE A, MELKOTE S, et al. Robots in machining[J]. CIRP Annals,2019,68(2):799-822.
-
BU Y, LIAO W, TIAN W, et al. Stiffness analysis and optimization in robotic drilling application[J]. Precision Engineering,2017(1):388-400
-
S. L. Li, Y. W. Wang, and Z. Wu, Design of a four-degree-of-freedom
5 CONCLUSION
1A configuration idea of connecting the parallel mechanism in series in the form of a mechanism unit is proposed, and the
multi-level coupling connection mechanism with the 3-RSR parallel mechanism as the structural unit is proposed, and the motion space is improved after two superimpositions. This kind of mechanism has both a large working space for a series mechanism and a dynamic performance of a parallel mechanism.
-
The position analysis of the single-layer 3-RSR
mechanism is carried out by using the allocation principle, and the velocity is solved by using the finite instantaneous spiral theory, and the simulation verification is carried out, which lays a foundation for the research of multi-level coupling and linking mechanism.In terms of research content, the neural network model established in this study calculates the mean square error (MSE) to verify the model's reliability. The optimal parameters are found using the Bayesian optimization algorithm. Finally, the reliability of the model is verified through path planning analysis.
-
The configuration proposed in this paper is obviously
different from the previous configuration, and also realizes some motion characteristics that the existing parallel mechanism does not have, and uses the finite instantaneous spiral theory to solve the velocity, which has a certain originality, and the feasibility of the coupling idea of multi- stage parallel mechanism is verified by the position and velocity simulation of the 3-RSR mechanism.
concrete spraying device with tandem and hybrid, Sci. Technol. Innov., vol. 209, no. 17, pp. 6365, 2022.
-
-
Li Z, Feiling J, et al. A Novel Tele-Operated Flexible Robot Targeted for Minimally Invasive Robotic Surgery[J]. Engineering, 2015, 1(1): 073-078.
-
S. L. Li, Y. W. Wang, and Z. Wu, Design of a four-degree-of-freedom concrete spraying device with tandem and hybrid, Sci. Technol. Innov., vol. 209, no. 17, pp. 6365, 2022.
-
M. H. Wang and M. X. Wang, Dynamic modeling and performance evaluation of a new five-degree-of-freedom hybrid robot, CJME, vol. 59, no. 59, pp. 113, 2023.
-
C. D. Zeng, H. P. Ai, and L. Chen, Force/pose impedance control for space manipulator orbit insertion and extraction, CJME, vol. 58, no. 3,
pp. 8494, 2022.
-
J. Peng, H. Wu, T. Liu, and Y. Han, Workspace, stiffness analysis and design optimization of coupled active-passive multilink cable-driven space robots for on-orbit services, Chin. J. Aeronaut., vol. 36, no. 2, pp. 402 416, Feb. 2023.
Position and orientation characteristic equation for topological design of robot mechanisms, J. Mech. Des., vol. 131, no. 2, pp. 021001-1021001- 17, Feb. 2009.
[13]T.-L. Yang, A.-X. Liu, H.-P. Shen, Y.-F. Luo, L.-B. Hang, and Z.-X. Shi,On the correctness and strictness of the position and orientation characteristic equation for topological structure design of robot mechanisms, J. Mech. Robot., vol. 5, no. 2, pp. 021009-1021009-18, May 2013.
[14] Q. Li and J. M. Herve, Type synthesis of 3-DOF RPR-equivalent parallel mechanisms, IEEE Trans. Robot., vol. 30, no. 6, pp. 13331343, Dec. 2014. [15]J. T. Li, H. B. Xu, and X. Y. Zhai, Research on the architecture of in-orbit robot service system based on space station platform, Robot Technique Appl., vol. 200, no. 2, pp. 4548, 2021. [16] Y. Y. Wang, C. W. Hu, Z. X. Tang, and S. Gao, Key technologies development of the space station manipulator system, Spacecraft Eng., vol. 31, no. 6, pp. 147155, 2022.