
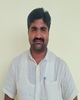
- Open Access
- Authors : Chandrashekar Gowda K N , Naveen G M
- Paper ID : IJERTV10IS100168
- Volume & Issue : Volume 10, Issue 10 (October 2021)
- Published (First Online): 02-11-2021
- ISSN (Online) : 2278-0181
- Publisher Name : IJERT
- License:
This work is licensed under a Creative Commons Attribution 4.0 International License
Laboratory Investigation on Application of Slag in Dense Bituminous Mix
Chandrashekar Gowda K N Department of Civil Engineering MIT Mysore
Mandya, India
Naveen G M
Department of Civil Engineering Government Engineering College Chamarajanagar
Chamarajanagar, India
Abstract Aggregates are significant constituent of any infrastructure building including roads. Advancement and extraction of natural aggregate resources (essentially sand, broken up stone and rock) are increasingly being restricted by zoning regulations, urbanization, environmental concerns and increased costs. For every ton of crude steel produced 400kgs of slag is produced. Considering the Indian scenario, the total steel production is recorded as 110 million tons (2018) leading to generation of 8 million tons of slag by-product. Though the utilization of slag has begun in India, technologies and studies should be advanced to make full utilization of slag. But use of slag aggregates in road construction is least practiced in India. Limited utilization of slag is made in preparation of hot asphalt mixes. Hence there is a need to study the properties of hot asphalt mixes prepared using slag aggregates.
In the present study an effort is made to study the strength properties of hot asphalt mixes prepared using steel slag and blast furnace slag aggregates by conducting laboratory tests. Steel slag and blast furnace slag aggregates were used as partial replacement of conventional coarse and fine aggregates respectively. Dense Bituminous Macadam grade-I as per Ministry of Road Transport and Highways (MORTH) specification is selected for the present study. The conventional aggregates were replaced with varying dosages of 10, 20 and 30% of steel slag and blast furnace slag in the hot asphalt mixes of Dense Bituminous Macadam grade-I. Marshall Stability tests were conducted on Dense Bituminous Macadam grade-I asphalt mix samples prepared using steel and blast furnace slag aggregates.
Marshall Stability test conducted indicated highest stability for mix containing 20% steel slag and 20% blast furnace slag and the increase in Marshall Stability is about 10.5% and 12% respectively compared to conventional mix.
Keywords Aggregates, Bitumen, Steel Slag(LD Slag), Blast Furnace Sla, Marshall Stability, Optimum Binder Content.
-
INTRODUCTION
Demand and extraction of natural materials like sand and aggregates is a great concern in road industry. To prevail over from this crisis, partial or full replacement of both coarser and finer material with slag aggregates may be an economic alternative. Therefore more sustainable practices towards the utilization of marginal materials are gaining importance. Use of marginal/alternative materials, stabilization, recycling, and use of by products are some of the important mitigation options available; Slag is one of the important industrial by product from steel industry. Due to increase in production of steel, the production of slag is also increasing. The demand for good road infrastructure for economical and inclusive growth of country has resulted in massive road development
projects. Majority of our road network warrants rehabilitation or reconstruction. This reconstruction/ rehabilitation of our road network posing several challenges to road industry. Depletion of good natural soil and aggregates, increase in transportation and fuel consumption, strict regulations on utilization of some natural materials are some of the challenges facing by the road construction industry.
Necessity of the Use of Steel Slag
Due to increase in production of steel, the production of slag is also increasing. Steel slag is being used as pavement construction material from several decades. Since it was known that the remains from the production of steel could be crushed and processed into a product that looked like crushed rock. Further studies and tests were performed to find the usefulness of this by product which lead to the conclusion that, the rough textured, vesicular, highly angular, pitted surfaces offer good particle interlock, and if appropriately compacted, the required stability can be achieved for good serviceable pavements.
The key technical index of bituminous concrete containing steel slag is its strength and is due to the reason that steel slag materials are rich in carbon and silicon content and are brittle.
The total estimate of crude steel produced in the whole world is 1200 million tonnes (2018) which leads to a simultaneous production of 300Mt of solid waste. Hence for every ton of crude steel produced 400kgs of solid waste is produced. Considering the Indian scenario, the total steel production is recorded as 110 million tons (2018) further leading to generation of 8 million tons of solid waste. Some developed countries of world are making full utilization of generated waste with technologies developed accordingly. Though the utilization of the generated waste has begun in India, technologies and researches should be emerged to make full utilization of waste generated.
-
OBJECTIVES
In the present study an effort has been made to assess the aptness of steel slag aggregates as a replacement to coarse and fine aggregates. The following are the objectives
-
The physical properties o Conventional aggregates.
-
The physical properties of steel slag.
-
The physical properties of bitumen
-
The Marshall properties of bituminous mix containing conventional aggregate and various percentages of steel slag and blast furnace slag.
-
-
METHODOLOGY
The intention of this course work was to study the likelihood of using slag aggregates in Dense Bituminous Macadam grade-I mix. The necessary basic tests are carried out to check the suitability of the materials such as coarse aggregate, fine aggregate, bitumen and slag. The comparative study on the strength of hot bituminous mixes containing slag and conventional aggregates were carried out. The bituminous mix properties were studied by carrying out Marshall Stability test in the laboratory.
The following material are used for the present
-
Constituents of Hot Bituminous Mix
-
Coarse aggregate: Material retained on 2.36mm IS sieve is considered as coarser fraction. LD slag and blast furnace slag are used as replacement to conventional coarse aggregate in the present study.
-
Fine aggregate: Fractions passing 2.36mm IS sieve and retained on 0.075mm IS sieve is considered as fine fractions. Blast furnace slag is used as partial replacement to conventional fine aggregates in the present study.
-
Filler: Stone dust and cement is used as filler in the present study.
-
Binder: Viscosity Grade-30 (VG-30) has been used as binder in the present study.
-
-
-
RESULTS AND CONCLUSIONS Table I. Results of Basic Tests on Conventional
Aggregates
Sl. No
Aggregate tests
Test result
Requirements as per MoRT&H Specifications
1
Aggregate Crushing Value (%)
26.8
Maximum 30
2
Aggregate Impact Value (%)
14.4
Maximum 27
3
Combined Flakiness and Elongation Index (%)
27.5
Maximum 30
4
Water absorption (%)
0.45
Maximum 2
5
Aggreate Specific gravity Coarse aggregate Fine aggregate
2.6
2.6
2.5-3.0
TABLE II. Basic Properties of Viscosity Grade-30
Bitumen (VG-30)
Sl.
No.
Basic Tests Conducted
Test Results
Specifications as per IRC SP:53-2002
1
Penetration at 25C, 0.1mm, 100g, 5sec
63.5
60-70
2
Softening point (R&B), C
47
55(minimum)
3
Ductility, cm
90
50 (minimum)
4
Specific gravity at 25C
1.01
Min 0.99
TABLE III. Material Properties of Slag Aggregates
Bulk Density (KN/m3)
1.4
–
Specific gravity
3.6
2.8
Water Absorption (%)
1.0
2.6
Combined Flakiness and Elongation Index (%)
24.1
27
TABLE IV. Chemical Composition of Steel Slag Aggregates
Compounds
Steel slag general composition (%)
Steel slag used in present study (%)
CaO
47-55
49
Free CaO
6.50
6.50
SiO2
7.5-15
12.40
Al2O3
1.20-1.70
1.45
MgO
1.30-1.50
1.35
Iron
20-26
23.00
MnO
3.50-5.30
3.60
CaO/SiO2
3.70-6.25
5.35
A. Filler Material
Stone dust and cement is used as filler material in the present study. The specific gravity test results of Stone dust is2.60 and cement 3.02.
TABLE V. Specific Gravity Values of Filler Material
Filler Material
Specific gravity
Stone dust
2.60
Cement
3.02
TABLE VI. Aggregate Gradation for Dense Bituminous Macadam Grade-I Mix According to
MoRT&H (V Revision)
Sieve size, mm
Adopted mid gradation
%
Weight retained
Weight retained, grams
37.5
97.5
2
30
26.5
78
20
246
19
–
0
0
13.2
65
13
162
9.5
–
0
0
4.75
46
19
234
2.36
35
11
138
1.18
–
0
0
0.6
–
0
0
0.3
14
21
258
0.15
–
0
0
0.075
5
9
108
<0.075
0
5
24
TABLE VII. Aggregate Gradation for Dense Bituminous Macadam Grade-I Mix According to
Sl.
No.
Bitumen Content,
%
Bulk density, kN/m3
Air Voids,
%
VMA,
%
VFB,
%
Marshall stability, Kg
Flow, mm
1
4.5
2.40
5.8
15.5
62.1
1916
4.2
2
5.0
2.39
5.4
16.2
66.5
1802
3.1
3
5.5
2.45
2.4
14.7
83.5
2098
4.4
4
6.0
2.41
3.2
16.5
80.4
1909
4.7
5
6.5
2.38
3.6
17.9
80.0
1447
5.1
Sl.
No.
Bitumen Content,
%
Bulk density, kN/m3
Air Voids,
%
VMA,
%
VFB,
%
Marshall stability, Kg
Flow, mm
1
4.5
2.40
5.8
15.5
62.1
1916
4.2
2
5.0
2.39
5.4
16.2
66.5
1802
3.1
3
5.5
2.45
2.4
14.7
83.5
2098
4.4
4
6.0
2.41
3.2
16.5
80.4
1909
4.7
5
6.5
2.38
3.6
17.9
80.0
1447
5.1
MoRT&H (V Revision)
Material Properties
Tests
LD slag
Blast furnace slag
Aggregate Impact Value (%)
19.3
20.2
Aggregate Crushing Value (%)
26.2
25.8
-
Comparison of Marshall Properties Obtained for Steel Slag and Blast Furnace Slag
Table VIII and IX presents the Marshall Test results of specimens casted at OBC for both conventional and mix containing steel slag and blast furnace slag aggregates respectively. Figure 5.1 to Figure 5.10 presents the variation of Marshall Properties with varying bitumen content of both conventional and bituminous mixes containing steel slag and blast furnace slag aggregates.
TABLE VIII. Marshall Test Results for Mixes with Conventional and Steel Slag Aggregates
Parameters
Conventional
10% steel slag
20% steel slag
30% steel slag
Requirements as per MoRT&H
V revision
OBC (%)
5.4
5.8
5.7
5.7
5.00-7.00
Air Voids
3.6
5.2
5.2
6.0
Min. 3.0
Max. 6.0
Bulk density (KN/m3)
2.42
2.38
2.38
2.35
–
Stability (Kg)
1834
1932
2026
1855
900 Kg
Flow (mm)
4.3
2.9
3.4
2.3
<>Minimum 2.0 VMA, %
15.8
17.1
17.1
17.8
Minimum 13
VFB, %
76.6
69.5
69.1
65.7
Minimum 65
TABLE IX. Marshall Test Results for Mixes with Conventional and Blast Furnace Slag Aggregates
P
a r a
m e
C
o n
1
0
%
2
0
%
3
0
%
R
e q u i r
OBC (%)
5.4
5.9
5.5
5.8
5.0-7.0
Air Voids
3.6
6.1
5.4
5.7
Min. 3.0
Max. 6.0
Bulk density (KN/m3)
2.42
2.36
2.37
2.36
–
Stability (Kg)
1834
1926
2049
1955
900 Kg
Flow (mm)
4.3
3.5
3.6
3.3
Minimum 2.0
VMA, %
15.8
17.9
17.3
17.6
Minimum 13
VFB, %
76.6
65.8
68.5
66.9
Minimum 65
From Table VIII and IX, it may be inferred that the stability value for Blast Furnace Slag is 2% higher than the bituminous mix consisting of Steel Slag.
The below are the graphs that are obtained after conducting tests on bituminous mixes.
Fig.1. Relationship between Stability and Binder Content for Conventional and Mix Containing LD Slag
Fig.2. Bulk Density Comparisons of Conventional and Bituminous Mix Containing LD Slag
Fig.03. Air Voids Comparisons of Conventional and Bituminous Mix Containing LD Slag
Fig.4. Flow Comparisons of Conventional and Bituminous Mix Containing LD Slag
Fig.5.Voids Filled with Bitumen Comparisons of Conventional and Bituminous Mix Containing LD Slag
Fig.6. Marshall Stability Comparisons of Conventional and Modified Mixes Containing Blast Furnace Slag
Fig.7. Bulk Density Comparisons of Conventional and Bituminous Mixes Containing Blast Furnace Slag
Fig.8. Air Voids Comparisons of Conventional and Bituminous Mixes Containing Blast Furnace Slag
Fig.9. Flow Comparisons of Conventional and Bituminous Mixes Containing
Blast Furnace Slag
Fig.10. Voids Filled with Bitumen Comparisons of Conventional and Bituminous Mix Containing Blast Furnace Slag
-
-
CONCLUSION
-
Basic tests performed on conventional aggregates, bitumen and slag aggregates (LD slag and Blast Furnace Slag) exhibited satisfactory results and thus satisfying all the requirements conforming to MoRT&H (V revision).
-
Mix containing partially replaced steel slag and blast furnace slag aggregates exhibited maximum stability of 10.5% and 11.5% higher respectively compared to conventional mix. This may be due to slag aggregates possess high specific gravity and contains greater amount of iron.
-
Optimum bitumen content for mixes contaning steel slag and blast furnace slag was 6% and 6.5% more respectively compared to conventional mix. This may be due to the reason that slag possess greater voids on the surface
-
-
ACKNOWLEDGMENT
I Thank my guide for his support in all aspect in preparing this paper. I also thank my institution and my research centre for providing facilities to conduct the experiments. I also thank every one who has involved in this research paper.
REFERENCES
-
A.K. Sinha, V.G. Havanagi, A. Ranjan and S. Mathur, Steel Slag Waste Material for the Construction of Road, Indian Highways A Review Of Road and Road Transport Development, ISSN 0376-7256, Vol.41, 2013.
-
Amir Modarres and Peyman Alinia Bengar, Investigating the indirect tensile stiffness, toughness and fatigue life of hot mix
asphalt containing copper slag powder, International Journal Of Pavement Engineering 2019, VOL. 20, NO. 8, 977985 (2019).
-
Ebenezer AkinOluwasola, MohdRosliHainin and M.M.A. Aziz, Evaluation of Asphalt Mixtures Incorporating Electric Arc Furnace Steel Slag and Copper Mine Tailings For Road Construction, Transportation Geotechnics 2 (2015) 4755, ISSN: 2214-3912, 2014.
-
FaragKhodary, Comparative Study Of Using Steel Slag Aggregate And Crushed Limestone In Asphalt Concrete Mixtures, International Journal of Civil Engineering and Technology (IJCIET), ISSN 0976 6308 (Print), ISSN 0976 6316(Online), Volume 6, Issue 3, March (2015), pp. 73-82 © IAEME.
-
Francesco Preti, Stefano Noto, Corrado Accardo, Elena Romeo, Antonio Montepara and Gabriele Tebaldi, Effect of hyper- modified asphalt binder and steel slags on cracking and rutting behaviour of wearing course mixtures, Taylor and Francis, ISSN: 1468-0629 (Print) 2164-7402 (Online) (2019).
-
Iuri Sidney Bessa, VerônicaTeixeira Franco, CasteloBrancoand, Jorge Barbosa Soares, Evaluation Of Polishing And Degradation Resistance Of Natural Aggregates And Steel Slag Using The Aggregate Image Measurement System, Road Materials and Pavement Design, 2014, Vol. 15, No. 2, 385405.
-
K.Ganesh, D. T. Prajwal Studies on fatigue performance of modified dense bituminous macadam mix using nano silica as an additive, International Journal of Pavement Research and Technology, ISSN: 1997-1400 (2019) DOI: https://doi.org/10.1007/s42947-019-0087-z.
-
Madhu Lisha Pattanaik, Rajan Choudhary, Bimlesh Kumar & Abhinay Kumar, Mechanical properties of open graded friction course mixtures with different contents of electric arc furnace steel slag as an alternative aggregate from steel industries, Taylor and Francis, ISSN: 1468-0629 (Print) 2164-7402 (Online) (2019).
-
P.S.Kothai and R.Malathy, Utilization Of Steel Slag In Concrete As A Partial Replacement Material for Fine Aggregates, International Journal of Innovative Research in Science, Engineering and Technology, ISSN: 2319-8753, Vol. 3, Issue 4, April 2014.